MG双梁门式起重机制造工艺作业文件.docx
《MG双梁门式起重机制造工艺作业文件.docx》由会员分享,可在线阅读,更多相关《MG双梁门式起重机制造工艺作业文件.docx(17页珍藏版)》请在冰豆网上搜索。
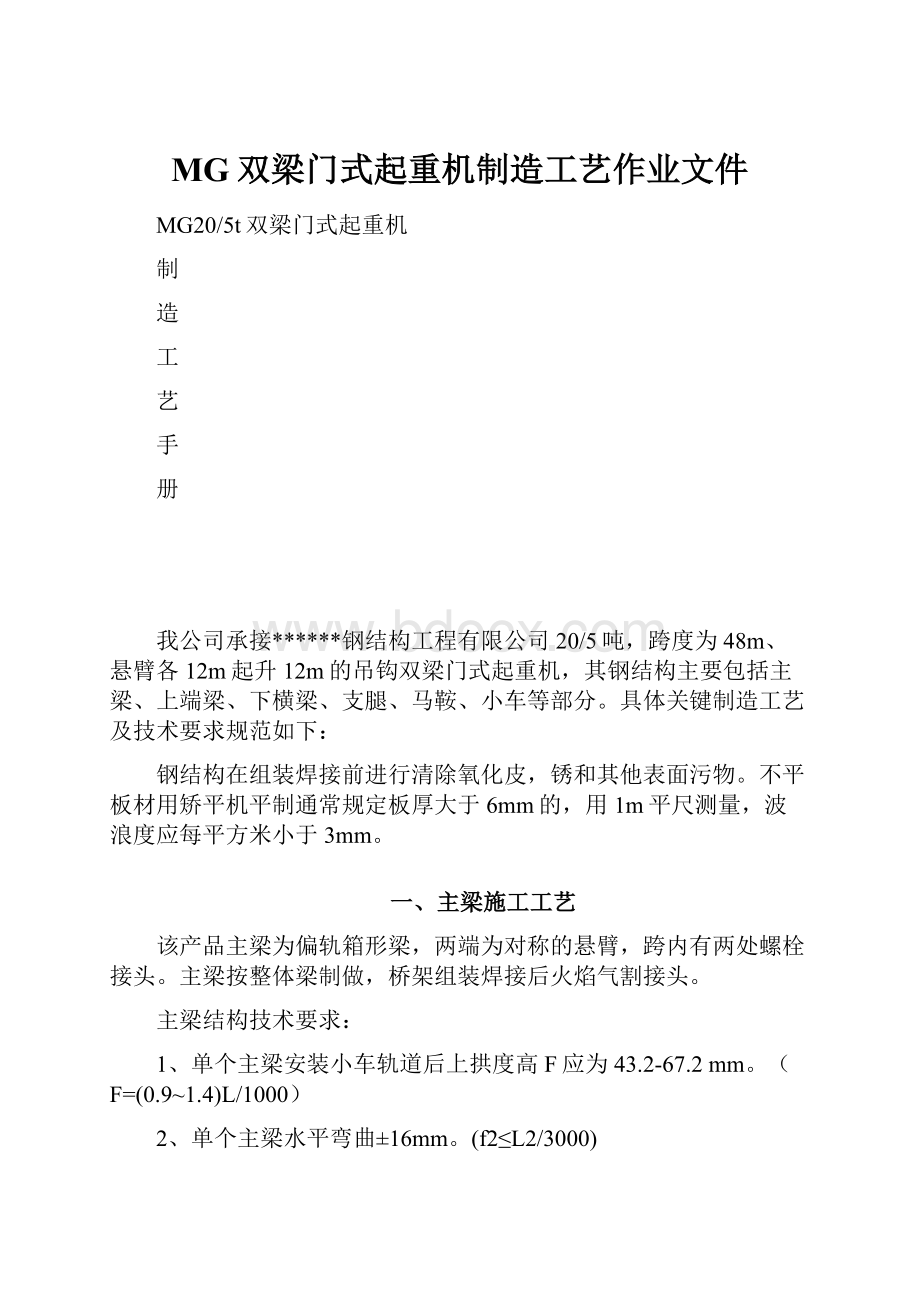
MG双梁门式起重机制造工艺作业文件
MG20/5t双梁门式起重机
制
造
工
艺
手
册
我公司承接******钢结构工程有限公司20/5吨,跨度为48m、悬臂各12m起升12m的吊钩双梁门式起重机,其钢结构主要包括主梁、上端梁、下横梁、支腿、马鞍、小车等部分。
具体关键制造工艺及技术要求规范如下:
钢结构在组装焊接前进行清除氧化皮,锈和其他表面污物。
不平板材用矫平机平制通常规定板厚大于6mm的,用1m平尺测量,波浪度应每平方米小于3mm。
一、主梁施工工艺
该产品主梁为偏轨箱形梁,两端为对称的悬臂,跨内有两处螺栓接头。
主梁按整体梁制做,桥架组装焊接后火焰气割接头。
主梁结构技术要求:
1、单个主梁安装小车轨道后上拱度高F应为43.2-67.2mm。
(F=(0.9~1.4)L/1000)
2、单个主梁水平弯曲±16mm。
(f2≤L2/3000)
3、主梁上盖板水平倾斜b≤B/250=4mm。
4、主梁腹板垂直倾斜h≤H/250=8.4mm。
5、整个主梁的拱度曲线和翘度曲线是园滑的,应基本上符合选定的抛物线。
6、腹板波浪变形,测量长度为1m检测,受压区波浪不得超过3mm;受拉区波浪度不得超过7mm。
7、上盖板波浪变形(两隔板之间)小于或等于3mm
8、主梁上下盖板的横向拼接焊缝与腹板横向拼接焊缝要相互错开200mm以上。
9、主梁上与支腿连接的下座形成的框形对角线差|d1-d2|≤5mm。
10、主梁下盖板和腹板受拉区域的对接焊缝应焊透,并符合JB1152-81《锅炉和钢制压力容器对接焊缝超声波控伤》中1级质量要求或GB3323-87《钢熔化焊对接接头射线照相和质量分级》中的二级质量要求。
(一)备料
1、上盖板
(1)下料加长量按2L/1000计算为140mm。
板宽允许偏差<2mm。
用火焰切割。
(2)上盖板切割后出现波浪变形及水平弯曲,在6m长内变曲量>3mm应采用矫正手段矫平。
(3)上盖板压出反变形。
2、下盖板
(1)下料按L/1000加长72mm。
宽度允许<2mm。
用火焰切割。
(2)下盖板切割后出现波浪变形及水平弯曲,在6m长内变曲量>3mm应采用矫正手段矫平。
3、主(副)腹板
(1)下料按1.5L/1000加长105mm。
(2)用1m平尺复查板材的波浪变形,大于3mm的要重新矫正。
(3)腹板跨中拱度值,主腹板为F=f技-f焊-f自+K(修正值5~10),副腹板f副=f主-b/250,主腹板悬臂端的翘度为F`=f`技-f`焊-f`自+K`(修正值5~10),或按f=L1/350+K``(修正值15~20)。
(4)腹板号料拱度曲线和翘度曲线列表号出基准线。
(5)腹板号料用油笔写出材料排列顺序号码和标记基准。
然后用火焰切割。
4、其他
(1)筋板用剪床切割,要求邻边夹角为90度。
(2)主梁接头。
可预先将连接板的孔在摇臂钻下钻孔。
(二)板件的拼接
1、盖板的拼接。
将盖板放在平台上,边缘拉尼龙丝线为准对齐,接头处间隙小于2mm定位焊,并要求接口两端定位焊引弧和引出板(60*60*6)。
焊接前,两端用螺栓压紧于平台上,用半自动埋弧焊进行焊接,焊接方向,正面焊后清根翻个面反向焊接。
焊接矫平,铲去引弧板和引出板,进行无损探伤,合格后转入下道工序。
2、腹板的拼接
(1)腹板不够宽的板料要预先拼接宽度,拼接间隙<2mm定位焊。
接口两端要定位焊引弧板和引出板(60*60*6),采用半自动埋弧焊,焊完一面翻个身焊接另一面,要求焊透。
焊后要进行矫平,要求波浪度在1m内小于3mm。
铲去引弧板和引出板,(按下料的编号依次将腹板放在平台上或平地上,以号料时的基准线为准,拉尼龙线将各块板料对齐,检查调整拱度和翘度。
然后定产位焊接拼接线。
同样,接缝两端定位焊引弧板和引出板(60*60*6)。
(3)对接焊缝采用气体保护焊,焊接方向,由主梁下盖板向上盖板方向焊接,悬臂梁焊接方向相反,由上盖板向下盖板方向焊接。
(4)焊后修理。
对接焊产生的角变开可采用砣重方法矫正。
然后割掉引弧板和引出板。
(5)拉钢丝线或尼龙线测量必要时进行矫正。
3、大筋板允许用几块板条拼接。
为了保证邻边成90度可采用定位胎组装定位焊。
对接焊缝要求焊透。
如采和用工电弧焊,背面清根后,焊接。
筋板内部镶边。
采用断续焊。
为了防止镶边时筋板产生瓢曲变形,可先将靠近上盖板的镶边焊焊缝焊好,其余三面可先定位焊,待∏形梁焊接内壁焊缝时再焊接镶边焊缝。
筋板焊后,以上盖板接合边为准,两邻边的垂直偏差≤H/1000=2.1mm。
(三)∏形梁组装焊接
1、在腹板上划出大筋板的定位线(筋板间距要加1/1000焊接收缩量)和<90*56*6角钢的定位线,组装定位焊角钢,并完成腹板的垂直焊缝。
2、在腹板上,按定位线组装定位焊大筋板。
3、将上盖板(反变形部分朝下)放在平台上,按筋板间距加焊接收缩量L/1000划出大筋板、跨度中点,支腿零点定位线及腹板和<90*56*6角钢的定位线,组装定位焊角钢,再将上盖板用吊卡吊起与主腹板和大筋板组装定位焊。
4、在已与主腹板组装好的大筋板上组装好的大筋板上组装定位焊副腹板的<90*56*6角钢。
5、在副腹板上,划出大筋板(注意同样要按筋板间距加焊接收缩量),跨中点和支腿零点的位置线。
然后将副腹板用吊具吊起与大筋板和上盖板组装定位焊。
组装时注意,要使副腹板和主腹板,上盖板的跨中点和支腿中心点对准。
组装时可应用腹板装配上卡具,由跨中向两边组装定位焊。
6、焊接∏形梁内壁焊缝。
首先焊接主腹板侧内壁焊缝(包括主腹板与上盖板焊缝),通常用手工电弧焊,也可采用气体保护焊。
主筋板焊接方向,主梁内跨由下盖板方向朝上盖板方向焊接,悬臂由上盖板向下盖板方向焊接。
然后翻转90度使上盖板朝下,焊接大筋板与上盖板焊缝,仍采用手工电弧焊或气体保护焊。
焊接方向,由主副腹板向主腹板方向焊接。
再翻转90度使副腹板朝下(要沿长度垫平),焊接副腹板内壁焊缝,焊接方法和焊接方向同主腹板内壁焊缝。
(四)∏形梁组装定位焊下盖板
1、将下盖板放在平台上,划出两端折弯定位线,可垫钢轨用重砣压弯。
2、将下盖板垫起,然后将∏形梁吊放在下盖板上,测量∏形梁的上拱度和上翘度。
如拱度和翘度不合适,可采用顶、压方法调整。
应注意每个大筋板在主腹板侧的垂直偏斜≤H/300。
如偏斜超差,应采用反扭方法进行调整,然后定位焊下盖板。
组装下盖板时拱度应控制在54-70mm,悬臂端翘度应控制在34mm。
下盖板组装定位焊应由跨中向两端进行。
用压杠、钢轨起升器和千斤顶等工具使下盖板贴紧腹板,间隙不大于1mm。
定位焊用手工电弧焊,焊条直径4mm,定位焊焊脚<4mm,定位焊焊缝长度30-40mm,间距<400mm。
3、下盖板与∏形梁组装定位焊后卸去螺旋拉紧器、压重和千斤顶。
然后检查拱度、翘度和腹板、盖板倾斜。
4、装配定位焊下盖板上的角钢及大筋板与盖板按图纸需要焊接之焊缝。
5、在主梁跨中用千斤顶将主梁拱度顶起10-20mm焊接下盖板上的角钢焊以及大隔板与下盖板的焊缝。
如主梁外(内)变应由副(主)腹板向主(副)腹板方向焊接。
(五)主梁四条纵向角缝焊接
1、将主梁吊放在不台上,应垫支腿中心,跨中、悬臂位置。
2、焊接方法采用气体保护焊。
焊接次序,原则上是先焊下盖板与腹板的焊缝,后焊上盖板与腹板的焊缝;先焊副腹板侧,后焊主腹板侧。
如若主梁拱度大,翘度小,应先焊上盖板与腹板焊缝,后焊下盖板与腹板的焊缝。
若是主梁内弯,则应先焊主腹板与盖板焊缝。
(六)组装主梁下座框板
1、将主梁倒置(下盖板朝上),支腿中心线垫起,悬臂端悬空。
划主梁两支腿中心线的位置线。
应注意,用钢制盘尺划位置线时应按图纸尺寸减该盘尺在相应拉力下的修正值(偌盘尺截面积10*0.25mm拉力147N,修正值为12mm,则应按刻度值48000-12=47988mm划线。
在下盖板上划出支座框板的位置线。
2、按定位线组装定位焊形成框形,其对角线差要≤3mm。
然后再进行焊接。
3、修正框架的焊接变形。
(七)主梁的调整和验收
1、按技术条件要求逐项进行检查。
2、如不符合要求要进行调整和修理,其矫正方法现场确定。
(八)主梁接头
将连接板和连接角钢按接口位置定位焊于主梁上,可将连接板预先用钻床钻好孔,再定位焊于主梁上,然后用摇臂钻或磁力钻配钻孔。
主梁接口等桥架组装焊接后,再号线火焰切割。
注意:
制造主梁时,接头处腹板,盖板的波浪变形应使用1m平尺检查要小于3mm,否则需矫正。
二、下横梁工艺
下横梁技术要求
1、上拱度为5-10mm。
2、旁弯±5mm。
3、上盖板水平倾斜b≤2.5mm。
4、腹板垂直偏斜h≤3mm。
5、两组弯板的高差小于2mm。
6、两组弯板距离Ba的偏差为±5mm。
7、弯板直角偏差,用角尺测量端部折合间隙≤1.5mm。
8、两组弯板中心线与下横梁纵向中心线偏差E≤4mm。
9、弯板的扭曲M≤4mm。
10、一组弯板孔中心距A之偏差±3mm。
11、支腿法兰座板上平面与两组弯板平面平行度偏差C≤3mm。
(一)备料
1、弯板下料后,用压力机压直角,用直尺检查,偏差b≤1.5mm。
2、腹板弯板处采用样板号料,气割,直偏差b≤1.5mm。
3、上盖板和腹板下料加长量均为15mm;下盖板下料加长量10mm。
4、上座板下料后要矫平,平面度2mm。
5、筋板剪切,直角偏差b≤1.5mm。
(二)组装焊接
1、盖板和腹板长度拼接焊缝采用半自动埋弧焊或气体保护焊。
如采用手工电弧焊,为保证焊透,背面采用碳弧气刨清根焊接。
2、将上盖板放在平台上,接尼龙丝线检查水平弯曲,如有变曲要矫正,每块筋板处盖板两边,用压板螺丝压紧在平台上。
3、在上盖板上号出筋板和腹板的定位线,并按定位线组装筋板,要求筋板与上盖板垂直。
焊接筋板与上盖板的焊缝,可采用气体保护焊或手工电弧焊,筋板焊接方向为双面焊接一正下反,往复焊接。
4、在上盖板上组装定位焊两腹板形成∏形梁梁。
5、将同一端的两弯板用定位胎连接起来,一起∏形梁组装定位焊。
注意要控制弯板的不平度,可用水平尺检测。
如不符合要求肆重新研配。
6、烛接∏形梁内壁焊缝。
观察∏形梁旁弯,注意腹板凹向和凸向。
将∏形梁躺放使凸形腹板面朝上,首先焊接凸向腹板与筋板的焊缝。
可采用气体保护焊或手工电弧焊。
焊完一面翻个。
凹形腹板朝上,焊接另一面腹板与筋板焊缝。
7、组装定位焊补强板并进行塞焊。
8、∏形梁内壁要涂刷防锈底漆。
9、将∏形梁倒置放在平台上,以两端弯板平面为基准或水平,检查腹板和盖板的偏斜。
如有扭曲变形可用螺栓接紧器使梁反扭转,然后组装定位焊下盖板。
10、焊接盖板与腹板的纵向角焊缝,采用气体保护焊,焊接次序为先焊下盖板与腹板的焊缝,后焊上盖板与腹板的焊缝。
如下横梁有水平弯曲,应先焊凸向面盖板与腹板的焊缝,后焊凹向面的盖板与腹板的焊缝。
11、焊接弯板与腹板和下盖板的焊缝。
然后焊接补顶板与腹板的焊缝。
12、对下横梁弯板水平面和垂直面进行检测。
如不合要求应进行矫正。
13、将下横梁倒置,组装定位焊。
(三)组装焊接下横梁其他零件
1、将下横梁正立,以两端弯板平面为基准调整腹板偏斜符合要求。
2、组装定位焊接使盖板平行于弯垂直面。
3、组装焊接上座子。
4、与支腿下底座定位焊在一起,在摇臂钻床下钻铰孔。
5、在下横梁的上盖板上划出上座子的定位线,研配上座子,使两个上座子的上法兰座板在同一水平面内。
然后将上座子定位焊在下横梁上。
并焊接上座子与下横梁盖板的焊缝。
6、下横梁正立,弯板面垫成水平位置。
用经纬仪在下横梁的上、下盖板上划出下横梁的中心线与下横梁纵向中心线重合。
三、支腿工艺
支腿结构技术要求
1、支腿弯曲偏差≤5mm。
2、支腿盖板偏斜为B/200。
3、支腿腹板倾斜偏差为H/200。
4、支腿盖板,腹板波浪度以1m长尺测量不超过6mm。
5、支腿上法兰座板和下法兰座板平行度2mm。
(一)备料
1、腹板和盖板下料宜用数控切割机,也可用样板号料,自动火焰切割器切割。
2、盖板、腹板加焊接收量11mm,两端又各加研配量25mm。
3、盖板钻塞焊孔。
4、下法兰座板定位焊在下横梁上座板上一起配钻铰孔,上法兰座板与马鞍架法兰座板一起配钻铰孔,打上“十”字中心线洋冲眼。
5、筋板采用数控或剪切。
塞焊垫板下料长度比图纸尺寸缩短5mm(工艺要求)。
6、折弯部分划线压弯。
(二)组装焊接
1、将筋板和相应的塞焊垫板组装定位焊并焊接成筋板组合件。
应在胎具上完成此项工作,以保证两件的夹角及焊后总高。
2、将盖板用吊具吊放在平台上,号出筋板的定位线和纵面加劲板与盖板的定角形尺,组装定位焊纵向加劲板。
焊接筋板和纵向加工劲板焊缝,采用手工电弧焊,焊接方向与下横梁相同。
3、压弯后的腹板进行整形,并划线、组装焊接纵向加劲板。
并号出筋板的定位线。
4、组装定位焊两腹板,使腹板对准筋板的定位线,特别要注意例筋板纵使件的垫板与腹板口一平,组成∏形结构。
5、将∏形结构平放,焊接腹板与筋板的焊缝,焊完一面翻个焊另一面。
可采用手工电弧焊或气体保护焊。
焊接方向类似下横梁。
6、将∏形结构盖板贴在平台上(开口朝上),调整腹板倾斜符合要求,再检查支腿水平弯曲。
7、在连接的腹板上组装焊接纵向加劲板,然后再将工件用吊具分别吊放在∏形结构上进行组装定位焊。
注意组装定位焊后应保持弯板90度。
8、焊接盖板与腹板的纵向角焊缝,可采用气体保护焊。
应视旁弯方向确定焊接次序,先焊凸起方向的焊缝。
9、塞焊上的焊缝,可采用气体保护焊或手工电弧焊。
(三)整形并划出中心线
1、支腿按技术条件逐项检测。
2、在支腿盖板上,用水平仪号出盖板的中心线。
并在端头和弯角处打上洋冲眼。
四、马鞍工艺
马鞍结构技术要求
1、箱形截面偏斜≤2.5mm。
2、用1m平尺测量腹板的波浪≤6mm。
3、马鞍梁架座平面度2mm。
4、马鞍梁上部直梁上拱或下挠≤5mm。
(一)备料
1、采用号料自动火焰切割。
2、弯折部分需压弯。
3、马鞍桩面切割应保证垂直。
塞焊垫板下料长度比图纸尺寸缩短5mm(工艺要求)。
4、支腿下部与座板的研配余量为20-30mm。
5、钻塞焊孔。
6、与法兰连接部分的四周定位配钻铰孔,划十字线打洋冲眼。
(二)组装焊接
1、盖板允许拼接,采用半自动理弧焊或气体保护焊,如用手工电弧焊,背面要用碳弧气刨清根焊接,要求焊透。
2、组装定位焊筋板与塞焊垫板,并焊成筋板组合件。
注意应保证两板件的垂直和焊后总高。
3、在平台上按图纸放地样,将腹板按地样线摆上,号上述筋板组合件及位置线并组装焊接,特别要注意使筋板组合件的塞焊垫板与腹板口一平。
4、将腹板下面垫起,划出位置线,组成∏形结构。
5、焊接∏形结构内壁焊缝,焊接方法同支腿。
6、将∏形结构重新吊放在地样上检查变形,如有弯形应予以调整。
再将内盖板用吊卡吊起,与∏形结构组装定位焊。
注意应使园角处贴合,间隙不得大于2mm。
7、先按图加焊临时拉筋,然后焊接角焊缝,可采用气体保护焊。
8、塞焊可采用气体保护焊或手工电弧焊。
9、铲掉临时拉筋,磨掉残留的焊肉。
10、在平台上放地样,将马鞍吊地地样上垫平,用水平仪测量,划出盖板的中心线并找上洋冲眼。
调整马鞍符合地样线。
并根据地样线,划出马鞍法兰座的位置线,用火焰切割割去多余部分。
11、将其与支腿法兰座板配钻铰孔后的组合件中心线对准马鞍的中心线,复测两法兰座板的距离符合图纸尺寸要求后定位焊。
为减小焊接法兰座板时的角变形,要号出筋板位置线,在定位焊时先焊出筋板外一小段正规焊缝。
再组装定位焊筋板。
12、焊接与邓鞍体的焊缝和筋板焊缝。
五、门腿研配工艺
技术要求
1、同一下横梁侧两支腿法兰座板间距K±2mm,支腿上水平弯板底座中心间距T±2mm。
2、支腿高度偏差H±4mm,相对差|H1-H2|≤4mm。
3、支腿对角线[D1-D2]≤3mm。
4、以支腿盖板基准线和下横梁上下盖板纵向中心线找成水平为基面上法兰座板偏斜量C1<2mm;下横梁高深莫测板面偏斜量C2<2mm。
5、下横梁法兰座板中心线与支腿法兰板中心线重合偏差a≤2mm。
6、下横梁法兰座板与支腿下法兰座板中心线偏差量b≤2mm。
研配工艺
1、要平台上划地样线,号出支腿、下横梁和马鞍梁的组装位置线,并打上洋冲眼。
2、将下横梁吊放平台上,用水平仪测量调整使下横梁上、下盖板中心线(两端已打洋冲眼)在同一水平面内,两端弯板符合地样线,并将下横梁上的支腿下法兰座板垂直投射到地样线上。
然后将下横梁移开。
3、将二支腿分别吊放到地样线上,同样用水平仪测量调整使支腿的上、下盖板中心线(两端也已打上洋冲眼)在同一水平面内。
吊线锤检查与地样线吻合。
按地样号出支腿两端研配余量,进行火焰切割。
4、将下横梁重新移至原处,并用前述方法找正,按技术要求与支腿研配。
符合要求后将连在下横梁上的支腿下法兰座板定位焊在支腿上。
5、按地样线吊放马鞍,以马鞍盖板中心线为准找水平,并使马鞍与支腿的中习线生命进行研配,等符合要求后将连在马鞍上的支腿上法兰座板定位焊于支腿上。
6、预先制作支腿水平弯板上的底座。
注意与支腿弯板连接的底座框架要留有10mm研配余量。
底座组装焊好修平,与主梁座板定位焊在一起,号出十字线,打上洋冲眼。
7、按地样线在支腿水平弯板上,研配支腿底座,使底座的十字中心线与支腿水平弯板上定位线重合,并用经纬仪检查调整使两个支腿底座上主梁座板在同一铅锤需内并与地样线重合。
在校检两座板中心距的偏差符合要求,将底座定位焊于弯板上。
8、将主梁座板用工艺型钢定位焊成一体,由支腿法兰座板拆下来,供桥架研配用。
9、焊接所有的焊缝,最好采用气体保护焊,采用手工电弧焊。
减小焊接法兰座板的角变形的方法同前。
10、在各座板的相应部位分别打上产品编号和部件编号的钢印。
六、桥架工艺
技术要求
1、桥架主梁拱度F为43-67mm;桥架主梁悬臂端上翘度F`为31-48mm。
2、桥架水平弯曲f≤8mm。
3、从法兰座板中心量届跨度偏差±5mm,且两侧跨度相对差|l1-l2|≤5mm。
4、主梁腹板波浪,以长度为1m的平尺测量距上盖板H/3以上区域以及两端离地腿中心线l/4范围内距下盖板H/3以内区域;悬臂距下盖板H/3范围内区域)≤0.7б=5mm,其余区域≤1.2б=8mm。
5、主梁上盖板水平偏斜b≤6mm。
6、主梁腹板垂直偏斜h≤9mm。
7、同截面小车轨道差≤3mm。
8、桥架对角线差≤5mm。
9、小车轨距允许偏差±3mm。
10、小车轨道中心线与腹板中心线的位置偏差≤6mm。
11、主梁上盖板波浪度(在两筋板之间)≤3mm。
12、小车轨道接头外的高低差e≤1mm;轨道接头处的侧向错位g≤1mm;轨道接头间隙≤2mm。
(一)主梁与上端梁组装焊接
1、将两主梁分别吊放在垫架上。
注意在测得的马鞍架加上垫架影响值△F=2mm,测得的翘度减去△F=3mm,即为正常支承情况下相应的拱度、翘度值。
2、在主梁上盖板的主腹板中心线上,划出支腿中心和跨度中心。
调整两梁达到:
(1)用水平仪将上述支腿中心(上盖板处)测量调整至同一水平面,误差≤2mm。
(2)调整两梁主腹板中心距,偏差±3mm。
(3)两梁同一截面高低差≤2mm。
(4)两梁上述支腿中心对角线差≤3mm。
(5)主梁上盖板水平偏斜b≤4mm。
(6)主梁腹板垂直偏斜h≤6mm。
符合以上要求后,将两根主梁用工艺型钢在支腿位置上盖板处定位焊。
3、在主梁两端划出上端梁事先用预装螺栓将上端梁用预装螺栓连成整体的组装位置线。
并按定位线定位焊接于主梁上。
4、焊接上端梁与主梁下盖板的焊缝。
先焊接上端梁下盖板与主当做下盖板的焊缝,然后焊接上端梁上盖板与主梁上盖板焊缝,再焊接上端梁腹板与主梁腹板的角焊缝。
采用气体保护焊或手工电弧焊。
(二)组装轨道,焊接轨道压板
1、小车轨道装配前,底部要刷防锈漆。
2、按技术条件对桥架复测主梁水平弯曲、拱翘度、主梁两主腹板中心线距离和同一截面两梁的主腹板高低差等项符合要求。
将两主梁在跨中用型钢固定。
3、组装小车轨道。
注意保证小车轨距,且要保证轨道中心线对主腹板中心线的偏差。
用轨道安装夹具将轨道压紧在上盖板上,定位焊轨道压板。
4、焊接轨道压板。
对拱度较小的主梁,在焊接轨道压板时跨中应用千斤顶顶起焊接。
采用气体保护焊或手工电弧焊,焊工较多时应沿梁长均布同时焊接。
5、焊接轨道压板后,卸掉千斤顶,铲掉跨中的固定型钢及焊留。
(三)组装焊接主梁下法兰座板(在安装现场完成)
1、按技术条件要求对桥架进行整体检查矫正,安全达到要求后再组装焊接下法兰座板。
2、用水平仪测量,在主梁支座框板上划出主梁法兰座板的水平位置线,火焰切割多余的部分。
3、将主梁上已有的支腿中心线引到支座框板侧面上,再用钢制盘尺在框板下端测量桥架跨度,应满足跨度<±5mm,且∣L1-L2∣≤2mm的要求。
在另两块框板侧面上划中心线。
4、将支腿研配后从支腿弯板上拆下来的连成一体的法兰座板组合体,吊放在专用拖车上推到主梁支座框板底下,再用吊车吊起与支座框板研配,使法兰座板的十字中心线,与框板四面的中心线重合,然后定位焊。
焊前要用水平仪重新检查一下:
(1)桥架主梁四个法兰座板的水平差△h≤2mm。
(2)拉钢丝检测纵横两个法兰座板中心连线与座板十字中心线的偏差e≤2mm。
(3)测量法兰座板中心对角线差∣D1-D2∣≤5mm
如不符合要求,要铲开调整达到要求后再定位焊。
5、焊接法兰座板。
应先焊接横向焊缝,后焊纵向焊缝。
(四)检查验收及接头处理
1、按技术条件逐项检测,达不到要求的项目要进行调整或矫正。
2、对连接部件,包括连接板和连接角钢要打产品编号和零件连接序号的钢印。
3、主梁接头处理。
(1)铲掉连接板,划出主梁活接口位置线。
利用靠尺火焰切割。
(2)火焰切割后将两主梁移开一段距离,铲掉切割熔渣,磨掉定位焊的残留焊肉。
对火焰切割后的腹板,盖板波浪变形进行矫平。
目录
一、主梁施工工艺1
(一)备料1
(二)板件的拼接2
(三)∏形梁组装焊接2
(四)∏形梁组装定位焊下盖板3
(五)主梁四条纵向角缝焊接3
(六)组装主梁下座框板3
(七)主梁的调整和验收3
(八)主梁接头4
二、下横梁工艺4
(一)备料4
(二)组装焊接4
(三)组装焊接下横梁其他零件5
三、支腿工艺5
(一)备料5
(二)组装焊接5
(三)整形并划出中心线6
四、马鞍工艺6
(一)备料6
(二)组装焊接6
五、门腿研配工艺7
研配工艺7
六、桥架工艺7
(一)主梁与上端梁组装焊接8
(二)组装轨道,焊接轨道压板9
(三)组装焊接主梁下法兰座板(在安装现场完成)9
(四)检查验收及接头处理9