第四章印刷工艺与设备.docx
《第四章印刷工艺与设备.docx》由会员分享,可在线阅读,更多相关《第四章印刷工艺与设备.docx(43页珍藏版)》请在冰豆网上搜索。
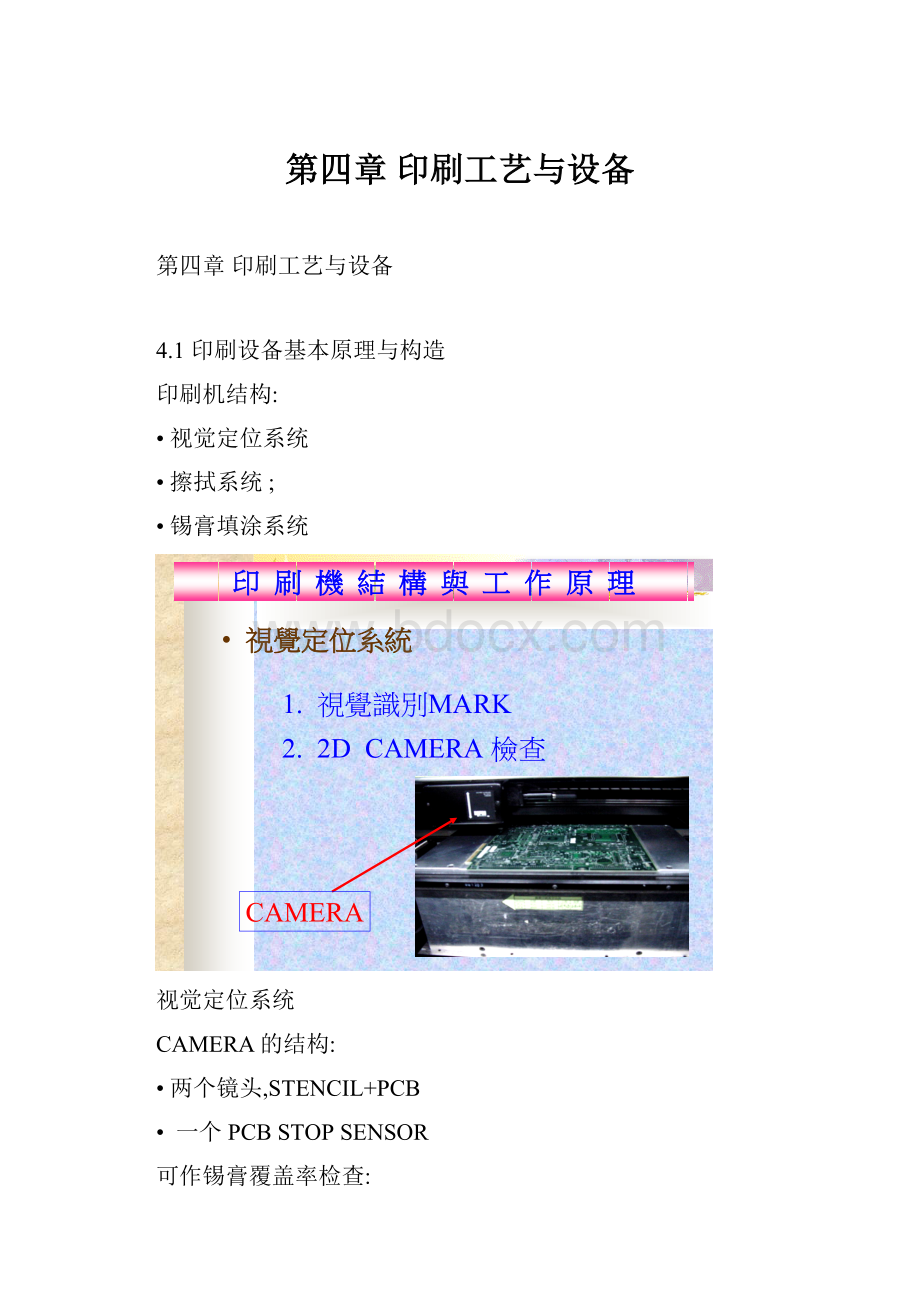
第四章印刷工艺与设备
第四章印刷工艺与设备
4.1印刷设备基本原理与构造
印刷机结构:
•视觉定位系统
•擦拭系统;
•锡膏填涂系统
视觉定位系统
CAMERA的结构:
•两个镜头,STENCIL+PCB
•一个PCBSTOPSENSOR
可作锡膏覆盖率检查:
•用CAMERA的PCB镜头
•可设定覆盖率参数,不合格的机器会自动提示
视觉定位系统
PCBSTOPSENSOR感应到PCB后.PCB停
CAMERA的两个镜头分别识别stencil和PCB上的MARK,以识别的图像完全重合为基准,来完成定位精准度,在校对位置时,PCB不动,只有STENCIL可移动调整.(分X.Y.)
擦拭系统
1.擦拭时由气缸将擦拭杆顶起,使擦拭纸与钢板接触.
2.湿擦时的溶剂量要控制在湿擦完毕时,湿的擦拭纸正好被用完.
3.溶剂的喷量可通过调整溶剂泵的频及冲程来进行控制.
锡膏填涂系统
1.刮刀采用钢刮刀.角度标准45~60度,现用60度.
2.印刷时锡膏在钢板上是滚动,一般滚动的直径为1~1.5cm
3.刮刀的压力一般为0.5+0.1kg/inch
锡膏印刷现在被认为是,表面贴装技术中控制最终焊锡节点品质的关键的过程步骤。
印刷是一个建立在流体力学下的制程,它可多次重复地保持,将定量的物料(锡膏或黏胶)涂覆在PCB的表面,一般来讲,印刷制程是非常简单的,PCB的上面与丝网或钢板保持一定距离(非接触式)或完全贴住(接触式),锡膏或黏胶在刮刀的作用下流过丝网或钢板的表面,并将其上的切口填满,于是锡膏或黏胶便贴在PCB的表面,最后,丝网或钢板与PCB分离,于是便留下由锡膏或黏胶组成的图像在PCB上.
在印刷锡膏的过程中,基板放在工作台上,机械地或真空夹紧定位,用定位销或视觉来对准。
或者丝网(screen)或者模板(stencil)用于锡膏印刷。
在手工或半自动印刷机中,锡膏是手工地放在模板/丝网上,这时印刷刮刀(squeegee)处于模板的另一端。
在自动印刷机中,锡膏是自动分配的。
在印刷过程中,印刷刮刀向下压在模板上,使模板底面接触到电路板顶面。
当刮刀走过所腐蚀的整个图形区域长度时,锡膏通过模板/丝网上的开孔印刷到焊盘上。
在锡膏已经沉积之后,丝网在刮刀之后马上脱开(snapoff),回到原地。
这个间隔或脱开距离是设备设计所定的,大约0.020"~0.040"。
脱开距离与刮刀压力是两个达到良好印刷品质的与设备有关的重要变量。
如果没有脱开,这个过程叫接触(on-contact)印刷。
当使用全金属模板和刮刀时,使用接触印刷。
非接触(off-contact)印刷用于柔性的金属丝网。
手工印刷机(MANNALPRINTERS)
手工印刷机是最简单而且最便宜的印刷系统,PCB放置及取出均需人工完成,其刮刀可用手把或附在机台上,印刷动作亦需人手完成,PCB与钢板平行度对准或以板边缘保证位置度均需依靠作业者的技巧,如此将导致每印一块PCB,印刷的参数均需进行调整变化。
半自动印刷机(SEMIANTOMATICPRINTERS)
半自动印刷机是当前使用最为广泛的印刷设备,它们实际上很类似手工印刷机,其PCB的放置及取出仍赖手工操作,与手工机的主要区别是印刷头的发展,它们能够较好地控制印刷速度,刮刀压力、刮刀角度,印刷距离以及非接触间距,工具孔或PCB边缘仍被用来定位,而钢板系统以助人员良好地完成PCB与钢板的平行度调整。
全自动印刷机(AUTOMATICPRINTER)
PCB的置取均是利用边缘承载的输送带完成,制程参数如刮刀速度、刮刀压力、印刷长度、非接触间距均可编程设定。
PCB的定位则是利用定位孔或板边缘,有些设备甚至可利用视觉系统自行将PCB与钢板调成平行,当使用该类视觉系统时,便可免却边缘定位带来的误差,而且令定位变得容易,人工的定位确认为视觉系统所取代。
刮刀
刮刀的磨损、压力和硬度决定印刷质量,应该仔细监测。
对可接受的印刷品质,刮刀边缘应该锋利和直线。
刮刀压力低造成遗漏和粗糙的边缘,而刮刀压力高或很软的刮刀将引起斑点状的(smeared)印刷,甚至可能损坏刮刀和模板或丝网。
过高的压力也倾向于从宽的开孔中挖出锡膏,引起焊锡圆角不够。
常见有两种刮刀类型:
橡胶或聚氨酯(polyurethane)刮刀和金属刮刀.
•刮刀刃口的型状:
锋利平整的刃口可获至最佳的印刷。
•刮刀的压力一般为5到30磅,其具体大小应依据刮刀类型及材料,非接触间距,是丝网还是钢板及锡膏状况。
•刮刀的速度,若对于的流动状况而定。
刮刀的压力与速度的关系是非常重要的,在理论上,对于每一种锡膏成份均应有一个最佳的压力与速度与之对应。
但此二参数是互成负面影响,对于任何刮刀压力,每增加一点速度均会令刮刀刃上的压力减小,相反地,刮刀速度的减小将令刮刀刃的压力增大。
刮刀宽度:
应超过PCB宽度大约50MM(2“),(每边大25MM(1”)),这可令钢板受到的力最小,以保持丝网的弹性,请不要偿试对刮刀进行维修。
视觉识别标示的平整度(AlignmentTargets)
如果印刷机未配备视觉系统,将难于找到丝网及钢板与PCB的平行面,人工识别标示将有助于丝网及钢板的水平设置。
识别标示可以是任何型状,一般来说用2.54mm(0.100")的方块就是够了,在丝网或钢板的对角上如PCB一样,有两个识别标示,使用时,将PCB置于印刷机并将PCB及丝网或钢板的识别标识对齐即可,此识别标示亦可作为一个制程控制的工具,例如,将锡膏或黏胶涂在识别标示上可供做平整性,厚度及边界的检查,胜过做整块板的全检。
4.2印刷设备参数设置与实际操作
1.系统简介:
印刷机特性
视觉自动对准装置VisionAlignmentSystem
慢速脱模功能SlowSnap-offFunction
可程序设定刮刀头ProgrammingSqueegee
自动擦拭钢板系统StencilWipper
2.关于印刷周期PrintingCycle
印刷周期包含下列过程
1.基板搬入LoadingBoard
2.基板定位LocatingBoard
3.视觉系统对位VisionAlignment
4.印刷平台上升ZTowerUP
5.刮刀向前后刮印锡膏Printting
6.慢速脱模SlowSnap-Off
7.印刷平台下降ZTowerDown
8.基板搬出UnloadingBoard
4.3钢网
4.3.1钢网制作流程
钢网的主要功能是帮助锡膏的沉积(deposition)。
目的是将准确数量的材料转移到光板(barePCB)上准确的位置。
锡膏阻塞在钢网上越少,沉积在电路板上就越多。
因此,当在印刷过程中某个东西出错的时候,第一个反应是去责备模板。
可是,应该记住,还有比钢网更重要的参数,可影响其性能。
这些变量包括印刷机、锡膏的颗粒大小和黏度、刮刀的类型、材料、硬度、速度和压力、钢网从PCB的分离(密封效果)、阻焊层的平面度、和组件的平面性。
钢板是一种用液体或干膜覆盖于金属薄片并蚀刻制成的金属板,覆盖层除那些需蚀刻成切口的区域外,将金属薄片完全盖住,蚀刻后,再将覆盖层去除,将此金属薄片直接粘接在框架上,称为金属钢板,若是通过金属丝网与框架进行粘接,则称为柔性钢板,一般建议使用柔性钢板的粘接方式,因为金属丝网可令钢板在其牵引下变得平坦无弯曲.
钢板一般由黄铜或不锈钢制成,早期使用黄铜是因其容易取得且易于蚀刻,但是,黄铜因为其抗强度仅为27.0001b,而显得太软,所以,黄铜制成的印刷模板在制程中,取置及贮存时均易变形受损。
而不锈钢,因其抗强度为163.0001b之高,故不易变形受损,因为很耐用,不锈钢的缺点是蚀刻为困难.
模板制造的三个主要技术是,化学蚀刻(chemicaletching)、激光切割(lasercutting)和电铸成形(electroforming)。
每个都有独特的优点与缺点。
化学蚀刻和激光切割是递减(substractive)的工艺、电铸成形是一个递增的工艺。
通常,当用于最紧的间距为0.025"以上的应用时,化学腐蚀(chem-etched)模板和其它技术同样有效。
相反,当处理0.020"以下的间距时,应该考虑激光切割和电铸成形的模板。
虽然后面类型的模板对0.025"以上的间距也很好,但对其价格和周期时间可能就难说了。
化学蚀刻的模板是模板世界的主要类型。
它们成本最低,周转最快。
化学蚀刻的不锈钢模板的制作是通过在金属箔上涂抗蚀保护剂、用销钉定位感光工具将图形曝光在金属箔两面、然后使用双面工艺同时从两面腐蚀金属箔。
由于工艺是双面的,腐蚀剂穿过金属所产生的孔,或开口,不仅从顶面和底面,而且也水平地腐蚀。
该技术的固有特性是形成刀锋、或沙漏形状(图一)。
图一
化学蚀刻的缺点:
这个方法对引脚间距为0.65mm或更大的组件是可接受的。
当在0.020“以下间距时,这种形状产生一个阻碍锡膏的机会,这个缺陷可以用叫做电抛光(electropolishing)的增强工艺来减小。
改进锡膏释放的另一个技术是梯形截面孔(TSA,trapezoidalsectionapertures),可以进一步提高表面光洁度,消除表面不规则.
电铸成形,一种递增而不是递减的工艺,制作出一个镍金属模板,具有独特的密封(gasketing)特性,减少锡桥和对模板底面清洁的需要。
该工艺提供近乎完美的定位,没有几何形状的限制,具有内在梯形的光滑孔壁和低表面张力,改进锡膏释放。
电铸成形的缺点:
因为涉及一个感光工具(虽然单面)可能存在位置不正。
如果电镀工艺不均匀,会失去密封效果。
还有,如果清洗过程太用力,密封“块”可能会去掉.
直接从客户的原始Gerber数据产生,激光切割不锈钢模板的特点是没有摄影步骤。
因此,消除了位置不正的机会。
模板制作有良好的位置精度和可再生产性。
Gerber文件,在作必要修改后,传送到(和直接驱动)激光机。
物理干涉少,意味着出错机会少。
虽然有激光光束产生的金属熔渣(蒸发的熔化金属)的主要问题,但现在的激光切割器产生很少容易清除的熔渣。
激光技术是唯一允许现有的模板进行返工的工艺。
除了激光切割与电铸成形之外,模板制作中的最重要进步是电子数据转移。
近如1995年,提供给模板制造商的多数图片都是胶片正片(filmpositive),一比一地配合光铜上的图形。
组件开孔的修饰涉及重复的摄影技巧和手工操作。
该工艺也决定于所提供胶片正片的质量。
最后,分步重复图片是一项繁重的任务。
胶剂模板(AdhesiveStencil)
电子文件也使计算机辅助设计(CAD)操作员可容易地决定一个焊盘形状的质心点。
有这个能力,设计文件中锡膏层可转换成圆形和椭圆形。
示组件尺寸而定(图七)。
因此,可制作一块模板来“印刷”,而不是滴胶。
印刷比滴胶快,将这种设备让给其它工作上面。
一个比较近期的创新发生在返修(rework)领域。
现在有“小型的”模板,专门设计用来返工或翻修单个组件。
可购买单个组件的模板,如标准的QFP和球栅阵列(BGA)。
当然也有相应的刮板,或小型刮刀。
化学腐蚀模板的价格是有框架尺寸驱使的。
虽然金属箔是模板制作过程中的重点,但框架是单一的、最贵的固定成本。
其尺寸很大程度上由印刷机类型决定。
可是,大多数印刷机可接纳不止一个框架尺寸。
(框架尺寸是工业标准)。
多数模板供应商保持一定库存的标准框架,尺寸范围从5x5"~29x29"。
因为空的金属箔成本没有框架的那么多,金属厚度对价格没有影响。
并且由于所有孔都是同时蚀刻的,其数量也是无关紧要的。
电铸成形模板价格主要是由金属厚度驱使的。
电镀到所希望的厚度是主要的考虑:
厚的模板比薄的模板成本低。
激光切割模板价格是按照设计的孔数.激光一次切割一个孔,即孔越多,成本越高。
还要加上所要求的框架尺寸。
一个用激光切割密间距和化学腐蚀标准间距组件的混合模板,当要求许多开孔时,可能是成本有效的方法。
可是,对于少于2500个孔的设计,完全用激光切割整个模板也许更成本低。
4.3.2钢网检验规范
钢片材质与制作方式选用原则,如:
模板类型
化学蚀刻
普通激光
电铸模板
Polymer(高聚物模板)
复合Polymer
加工方法
蚀刻
YAG热切割
电沉积
YAG冷切割
YAG冷切割
原材料
日本SUS304
日本SUS304
镍合金
环氧树脂
镀镍环氧树脂
所用设备
国产
LPKF
LPKF
LPKF
可加工厚度
0.10~2mm
0.10~0.60mm
0.03~0.20mm
0.02~0.20mm
0.02~0.20mm
可加工间距
P≧0.50mm
P≧0.40mm
P≧0.30mm
P≧0.20mm
P≧0.20mm
开口位置精度
±10um
±3um
±6um
±1um
±1um
孔壁粗糙度
5um
1um
0.4um
0.5um
0.5um
BGA圆孔度
≧95%
≧99%
≧98%
≧99.9%
≧99%
生产使用
通用
通用
通用
要重新试验设定工艺参数,只能用钢刮刀,会产生静电,对印刷机有要求
通用
清洗
酒精
酒精
酒精
酒精
酒精
寿命
1年
1年
1.5年
0.8年
1.7年
模板技术对锡膏释放的百分比也起一个主要作用。
开孔侧壁的几何形状和孔壁光洁度直接与模板技术有关。
经过电解抛光的激光切割模板得到比非电解抛光的激光切割模板更光滑的内孔壁。
在一个给定面积比上,前者比后者释放更高百分比的锡膏。
对于接近1.5的宽深比和接近0.66的面积比,一些模板技术比其它的更好地达到较高百分比的锡膏释放。
使用这种模板的一个例子是,一个两排的连接器,0.10"间距,0.045"直径的通孔和0.035"的引脚直径,0.048"厚度的PCB,在0.150"的通孔开口范围内没有其它的组件和通路孔。
一块0.085"宽,0.170"长的开口,和0.006"厚度的添印模板,可以达到足够的锡膏量,以形成在PCB的两面有焊接圆角的焊接点。
在一些情况中,模板可能要求台阶。
一种情况是对密间距(fine-pitch)组件的向下台阶区域。
有一个例子是,对所有组件为8-mil厚度的模板,20-mil间距的除外,它要求6-mil的厚度。
在模板上朝电路板这一面的陷凹台阶是模板中要求台阶的另一个例子。
在板上有凸起或高点妨碍模板在印刷过程中的密封作用的时候,陷凹台阶是所希望的。
例子有条形码、测试通路孔和增加性的踪迹线。
陷凹台阶的凹穴也用于两次印刷(two-print)模板,它主要用于混合技术要求-或者通孔技术/表面贴装或者表面贴装/倒装芯片。
在通孔技术/表面贴装的情况,第一个模板用正常厚度的模板(6-mil)印刷所有的表面贴装锡膏。
第二个模板印刷所有通孔组件的锡膏。
这个模板通常是15~25-mil厚,为通孔组件提供足够的锡膏。
陷凹台阶(通常10-mil深)是在这个第二次印刷模板的朝板面上,在第一次印刷所有表面贴装锡膏的位置上。
这个台阶防止通孔印刷期间抹掉表面贴装锡膏。
当单一厚度的添印模板不能提供适当的锡膏量来形成一个可接受的焊接点的时候,可使用台阶式添印模板。
台阶式添印模板的应用是,多引脚排的通孔组件(三或更多)或在SMT组件和通孔组件之间具有最小不准入内区域的高密度组装板。
这个模板类型的一个例子如图三所示。
K1和K2是不准入内距离。
K2是通孔开口与台阶边缘之间的距离。
当设计模板开孔时,在长度大于宽度的五倍时考虑宽深比,对所有其它情况考虑面积比。
随着这些比率的减少并分别接近1.5或0.66,对模板孔壁的光洁度就要求更严厉,以保证良好的锡膏释放。
在选择提供光滑孔壁的模板技术时应该小心。
作为一般规则,将模板开孔尺寸比焊盘尺寸减少1~2-mil,特别是如果焊盘开口是阻焊层界定的。
当焊盘是铜箔界定时,与多数微型BGA一样,将模板开孔做得比焊盘大1~2-mil可能是所希望的。
这个方法将增加面积比,有助于微型BGA的锡膏释放。
4.4印刷材料
4.4.1锡膏
焊膏是由合金焊料粉、糊状助焊剂均匀混合而成的浆料或膏状体。
它是SMT工艺中不可缺少的焊接材料,广泛用于再流焊中。
焊膏在常温下具有一定的粘性,可将电子元器件初粘在既定位置,在焊接温度下,随着溶剂和部分添加剂挥发,将被焊元器件互联在一起形成永久连接。
目前涂布焊膏多数采用丝网漏印法,其优点是操作简便、快速、配制后即刻可用。
但该法也有缺点:
(1)难以保证焊点的可靠性,易造成虚焊。
(2)浪费焊膏,成本高。
近年来,用微机控制的自动焊膏点涂机可以克服上述缺点。
4.4.1.1焊膏的化学组成
焊膏主要由合金焊料粉末和助焊剂组成(表4.1)。
其中合金焊料粉占总重量的85%~90%,助焊剂点15%~20%。
1.合金焊料粉末
合金焊料粉末是焊膏的主要成分。
常用的合金焊料粉末有锡-铅(Sn-Pb)、锡-铅-银(Sn-Pb-Ag)、锡-铅-铋(Sn-Pb-Bi)等,常用合金成分为63%Sn/37%Pb以及62%Sn/36%Pb/2%Ag。
不同合金比例有不同的熔化温度,见表4.2。
合金焊料粉末的形状、粒度和表面氧化程度对焊膏性能的影响很大。
合金焊料粉末按形状分成无定形和球形两种。
球形合金粉末的表面积小、氧化程度低、制成的焊膏具有良好的印刷性能。
合金焊料粉末的粒度一般在200~400目。
粒度愈小,粘度愈大;粒度过大,会使焊膏粘接性能变差;粒度太细,则由于表面积增大,会使表面含氧量增高,也不宜采用。
组成
使用的主要材料
功能
合金焊料粉
Sn-Pb
Sn-Pb-Ag等
元器件和电路的机械和电气连接
焊剂系统
焊剂
松香,合成树脂
净化金属表面,提高焊料润湿性
粘接剂
松香,松香脂,聚丁烯
提供贴装元器件所需粘性
活化剂
硬脂酸,盐酸,联氨,三乙醇胺
净化金属表面
溶剂
甘油,乙二醇
调节焊膏特性
触变剂
防止分散,防止塌边
表4.1焊膏组成和功能
合金焊料
熔点/℃
合金焊料
熔点/℃
Sn-Zn
204~371
Sn-Sb
249
Pb-Ag
310~366
Sn-Pb-In
99~216
Sn-Pb
177~327
Sn-Pb-Bi
38~149
表4.2合金焊料温度
2.助焊剂
在焊膏中,糊状助焊剂是合金粉末的载体。
其组成与通用助焊剂基本相同。
为了改善印刷效果和触变性,有时还需加入触变剂和溶剂。
通过助焊剂中活性剂的作用,能清除被焊材料表面以及合金粉末本身的氧化膜,使焊料迅速扩散并附着在被焊合金属表面。
助焊剂的组成对焊膏的扩展性、润湿性、塌陷、粘度变化、清洗性质、焊珠飞溅及储存寿命均有较大的影响。
4.4.1.2焊膏的分类
焊膏的品种很多,通常可按以下性能分类:
1.按合金焊料粉的熔点分
最常用的焊膏熔点为178~183℃,随着所用金属种类和组成的不同,焊膏的熔点可提高至250℃以上,也可降为150℃以下,可根据焊接所需温度的不同,选择不同熔点的焊膏。
2.按焊剂的活性分
参照通用液体焊剂活性的分类原则,可分为无活性(R),中等活性(RMA)和活性(RA)三个等级(表4.3),根据PCB和元器件的情况及清洗工艺要求进行选择。
类型
焊剂和活化剂
应用范围
R
水白松香,非活性
航天,军事
RMA
松香,非离子性卤化物等
军事和其它高可靠性电路组件
RA
松香,离子性卤化物
消费类电子产品
表4.3焊膏按焊剂的活性分类
3.按焊膏的粘度分
粘度的变化范围很大,通常分100~600Pa’s,最高可达1000Pa’s以上。
依据锡膏工艺手段的不同进行选择。
4.按清洗方式分
按清洗方式分为有机溶剂清洗、水清洗、半水清洗和免清小清洗等方式。
从保护环境的角度考虑,水清洗、半水清洗和免清洗是发展方向。
4.4.1.3表面组装对焊膏的要求
在表面组装的不同工艺或工序中,要求焊膏具有的性能如表4.4所示。
1.焊膏在印刷前应能保持3~6个月。
2.印刷时和再流加热前应具有的性能
(1)印刷时应具有优良的胶模性;
(2)印刷时和印刷后焊膏不易坍塌;
(3)焊膏应具有一定的粘度。
3.再流加热时应具有的性能
(1)应具有良好的润湿性能;
(2)应形成最少量的焊料球;
(3)焊料飞溅要少。
4.再流焊接后应具有的性能
(1)要求焊剂中固体含量越低越好,焊后易清洗干净;
(2)焊接强度高。
材料诸因素
组装要
求的特性
焊料合金
焊剂
焊膏
组
成
不
纯
物
粒
度
颗
粒
形
状
粒度分布
氧
化
状
态
熔
点
沸
点
含
量
成
分
CI
量
氯
素
含
量
触
变
剂
量
溶
剂
量
电
导
率
吸
水
量
粘
度
比
重
印刷前
储存稳定性
△
〇
〇
△
△
〇
印刷到
再流前
印刷脱模性
〇
〇
〇
〇
〇
〇
〇
〇
触变性
〇
△
〇
△
△
〇
〇
〇
△
〇
△
粘性
〇
〇
〇
〇
〇
〇
〇
再流时
润湿性
〇
〇
〇
〇
〇
〇
△
△
〇
焊料球
△
〇
〇
〇
〇
△
〇
△
〇
△
〇
〇
〇
焊剂飞溅
〇
△
〇
△
〇
〇
速干性
△
〇
△
〇
△
△
再流后
洗净性
△
△
〇
〇
〇
△
〇
〇
组件表面美观
△
〇
△
△
〇
〇
〇
△
△
非腐蚀性
△
〇
〇
绝缘电阻
△
△
〇
△
△
△
△
接
合
强
度
张力
蠕变性
弯曲弹性
热冲击性
〇
〇
〇
〇
〇
注:
〇关系大,△有关系
表4.4对焊膏要求的特性和相关因素
4.4.1.4焊膏的选用原则
根据焊膏的性能和使用要求,可参考以下几点选用:
(1)焊膏的活性可根据印制板表面清洁程度来决定,一般采用RMA级,必要时采用RA级。
(2)根据不同的涂覆方法选用不同粘度的焊膏,一般液体分配器用粘度为100~200Pa’s,丝网印刷用粘度为100~300Pa’s,漏模板印刷用粘度为200~600Pa’s。
(3)精细间距印刷时选用球形、细粒度焊膏。
(