答案管理学原理模拟题.docx
《答案管理学原理模拟题.docx》由会员分享,可在线阅读,更多相关《答案管理学原理模拟题.docx(20页珍藏版)》请在冰豆网上搜索。
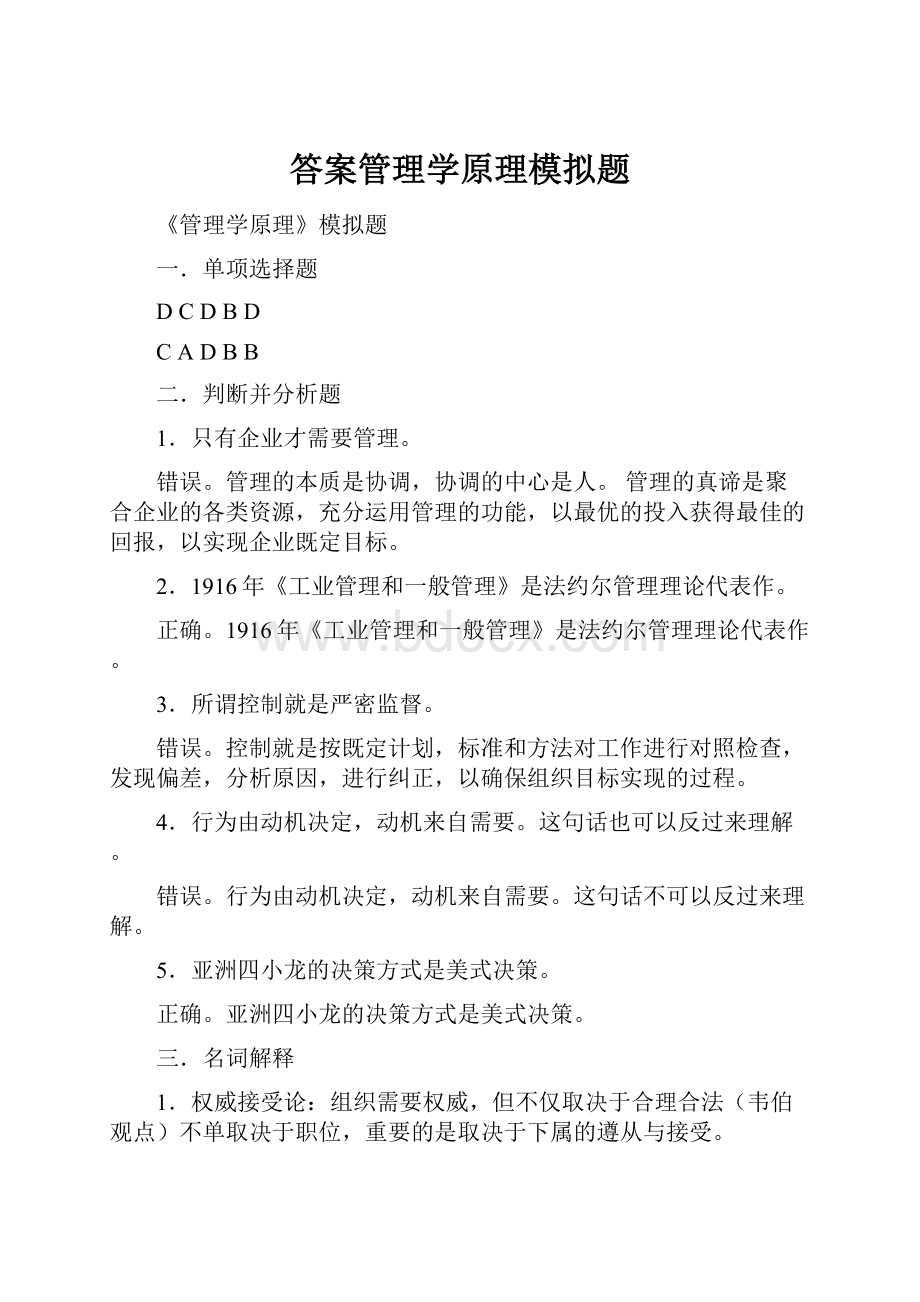
答案管理学原理模拟题
《管理学原理》模拟题
一.单项选择题
DCDBD
CADBB
二.判断并分析题
1.只有企业才需要管理。
错误。
管理的本质是协调,协调的中心是人。
管理的真谛是聚合企业的各类资源,充分运用管理的功能,以最优的投入获得最佳的回报,以实现企业既定目标。
2.1916年《工业管理和一般管理》是法约尔管理理论代表作。
正确。
1916年《工业管理和一般管理》是法约尔管理理论代表作。
3.所谓控制就是严密监督。
错误。
控制就是按既定计划,标准和方法对工作进行对照检查,发现偏差,分析原因,进行纠正,以确保组织目标实现的过程。
4.行为由动机决定,动机来自需要。
这句话也可以反过来理解。
错误。
行为由动机决定,动机来自需要。
这句话不可以反过来理解。
5.亚洲四小龙的决策方式是美式决策。
正确。
亚洲四小龙的决策方式是美式决策。
三.名词解释
1.权威接受论:
组织需要权威,但不仅取决于合理合法(韦伯观点)不单取决于职位,重要的是取决于下属的遵从与接受。
2.滚动计划法:
是一种定期修订未来计划的方法。
根据计划的执行情况和环境变化情况定期修订未来的计划,并逐期向前推移,使短期计划、中期计划有机结合起来。
3.管理跨度和管理层次:
管理跨度就是说一个企业里面从老总到员工有几个级别,讲的是层级的概念;管理层次:
是指公共组织内部划分管理层级的数额。
4.激励:
激励是为了特定目的而去影响人们的内在需要或动机,从而强化,引导或改变人们行为的反复过程。
5.职位权力:
由职位赋予的权力,包括奖励权、惩罚权和法制权。
四.简答题
1.管理学的特征有哪些?
综合性、科学与艺术性、不精确性、系统性、软科学、二重性
2.目标管理的过程。
目标的设置:
高阶层领导者预定目标(但这个目标是暂时的、可以改变的)、重新审议组织结构和职责分工、确定下级的目标、上下级达成书面协议,建立目标体系,绘制出目标图
实现目标过程的管理。
总结和评估
3.事业部结构的优点和缺点各是什么?
优点:
更侧重于结果,使企业最高层摆脱了日常行政事务,集中精力决策规划企业的战略问题;既有较高的稳定性,又有较高的适应性;各事业部之间可以相互竞争,提高效率;为企业储备了高级管理人才。
缺点:
增加了管理层次,活动和资源出现重复配置,使管理人员和管理费用大大增加;对事业部管理人员要求较高;各事业部之间的相互交流和支援困难,成为“独立王国”。
4.简述亚当斯的公平理论。
公平理论又称社会比较理论,它是美国行为科学家斯塔西·亚当斯提出的,侧重于研究工资报酬分配的合理性、公平性及其对职工生产积极性的影响。
该理论的基本要点是:
人的工作积极性不仅与个人实际报酬多少有关,而且与人们对报酬的分配是否感到公平更为密切。
人们总会自觉或不自觉地将自己付出的劳动代价及其所得到的报酬与他人进行比较,并对公平与否做出判断。
公平感直接影响职工的工作动机和行为。
因此,从某种意义来讲,动机的激发过程实际上是人与人进行比较,做出公平与否的判断,并据以指导行为的过程。
5.解决冲突的办法有哪些?
调解法、互助法、裁决法、改组法、支配法、拖延法。
五.论述题
1.论述科学管理理论的主要内容及评价。
主要内容:
工作定额;能力与工作相适应;标准化;差别计件付酬制;计划与执行分开原理;例外原理。
评价:
两重性。
主要贡献:
科学方法。
局限性:
把工人看做“经济人”,局限在具体工作的作业效率(层次)。
2.结合管理实际,论述领导者应该具备的素质。
一、政治品德素质政治品德素质是确保领导者在政治上合格的要素,是一个领导者在政治问题上的道德品质,是领导者从事领导管理活动必须具备的政治立场、政治观点、政治态度和政治品质等方面的基本素质。
二、文化知识素质具有良好的文化知识素质是现代领导者最起码的要求,也是领导者适应复杂多变和高标准的领导工作要求所应具备的最主要的条件。
三、工作能力素质工作能力是一个人的技能、智能和体能的综合体现。
四、心理素质心理素质是指领导者个人的性格、气质、意识、情感价值观等心理要素。
五、身体素质健康的体魄是领导者必备的素质,是做好领导工作的前提和基础。
核心能力:
开拓创新.行动学习团队协作.科学决策.有效执行。
六.案例分析题
李氏进出口公司的李先生是一家服装生产公司的创立者和执行总裁。
他成立了自己的公司,并在五年内使之从一家一个人经营的小企业发展成一家拥有50名员工,年生产额为300万美元的公司。
尽管企业的规模和赢利水平都发生了变化,但李先生的管理并没有发生太大的变化。
他埋头于企业的日常事务中,总是犹豫不决是否由其下属人员完成某些重要的任务。
当他到国外进行采购而不在公司的时候,公司就会停步不前。
他坚持认为自己是最了解本公司的人,自己有知识和技能制定有关企业利益的所有决策。
李先生制定企业的所有计划,组织各项活动,招募员工,指挥员工的活动,解决员工遇到的问题,解决与人事有关的问题。
他知道他的全部雇员的名字,他的办公室是随时向员工开放的。
企业成长期间,李先生已经不能抽出时间去制定新的策略来应付所发生的变化。
员工发现当他们碰到非常重要的难题时,很难找到李先生。
企业中员工的士气达到了最低点。
随着问题增多,压力增大,李先生正在考虑卖掉公司。
他感觉公司给自己带来了很大麻烦,使他丧失了健康和心灵的平静。
问题:
(1)你如何评价李先生的处境?
(2)在李先生卖掉公司之前,你会给他提出什么样的建议?
答:
(1)李先生的管理精力有限。
(2)在他卖掉公司以前,可以建议他授权,将一部分权力下放,从而提高管理效率,也使他本人从繁忙的工作状态种出来,集中精力处理企业的重大战略决策问题。
1-1试述精密和超精密加工技术对发展国防和尖端技术的重要意义
1-2从机械制造技术发展看,过去和现在达到怎样的精度可被称为精密和超精密加工?
1-3精密和超精密加工现在包括哪些领域?
1)超精密切削,如超精密金刚石刀具切削,可加工各种镜面,它成功地解决了高精度陀螺仪、激光反射镜和某些大型反射镜的加工。
2)精密和超精密磨削研磨,例如解决了大规模集成电路基片的加工和高精度硬磁盘等的加工
3)精密特种加工,如电子束、离子束加工,使美国超大规模集成电路线宽达到0.1um。
1-4试展望精密和超精密加工技术的发展
1-5我国的精密和超精密加工技术和发达国家相比情况如何?
1-6我国要发展精密和超精密加工技术,应重点发展哪些方面内容?
1)超精密切削、磨削的基本理论和工艺
2)超精密设备的关键技术、精度、动特性和热稳定性
3)超精密加工的精度检测、在线检测和误差补偿
4)超精密加工的环境条件
5)超精密加工的材料
2-1金刚石刀具超精密切削有哪些应用范围?
用金刚石刀具进行超精密切削,用于加工铝合金、无氧铜、黄铜、非电解镍等有色金属和某些非金属材料;
现在用于加工陀螺仪、激光反射镜、天文望远镜的反射镜、红外反射镜和红外透镜等。
现在的使用面日益扩大,不仅有为国防尖端技术服务的单件小批生产方式,而且有为民用产品服务的大批量生产方式。
2-2金刚石刀具超精密切削的切削速度应如何选择?
超精密切削实际选择的切削速度,经常是根据所使用的超精密机床的动特性和切削系统的动特性选取,即选择振动最小的转速。
在该转速时表面粗糙度最小,加工质量最高。
2-3试述超精密切削时积削瘤的生成规律和它对切削过程和加工表面粗糙度的影响
一、超精密切削时切削参数对积屑瘤生成的影响
1)切削速度对积屑瘤产生的影响
2)进给量f和背吃刀量ap对积屑瘤生成的影响
二、超精密切削时积屑瘤对切削力和加工表面粗糙度的影响
1)积屑瘤对切削力的影响
2)积屑瘤对加工表面粗糙度的影响
三、使用切削液减小积屑瘤,减小加工表面粗糙度
2-4试述各工艺参数对超精密切削表面质量的影响
一、切削速度的影响
二、进给量和修光刃对加工表面粗糙度的影响
三、切削刃形状对加工表面粗糙度的影响
四、背吃刀量变化对加工表面粗糙度的影响
五、背吃刀量变化对加工表面残留应力的影响
2-5超精密切削时如何才能使加工表面成为优质的镜面
2-6超精密切削时,金刚石刀具切削刃锋锐度对切削形变和加工表面质量的影响如何?
2-7超精密切削时极限最小切削厚度是多少?
2-8试述超精密切削用金刚石刀具的磨损和破损特点
2-9金刚石刀具晶面选择对切削变形和加工表面质量的影响如何?
2-10工件材料的晶体方向对切削变形和加工表面质量的影响如何?
2-11脆性材料用超精密切削如何加工出优质表面?
2-12超精密切削对刀具有哪些要求?
为什么单晶金刚石是被公认为理想的,不能代替超精密切削的刀具材料?
2-13单晶金刚石有哪几个主要晶面
2-14试述金刚石晶体的各向异性和不同晶面研磨时的好磨难磨方向
2-15金刚石晶体有哪些定向方法?
2-16试述金刚石晶体的激光定向原理和方法
2-17如何根据金刚石微观破损强度来选择金刚石刀具的晶面?
2-18比较直线修光刃和圆弧修光刃金刚石刀具的优缺点
2-19单晶金刚石刀具前面应选哪个晶面
2-20试述金刚石刀具的金刚石固定方法
2-21试述单晶金刚石刀具的研磨加工方法
2-22单晶金刚石刀具质量的好坏如何评定?
3-1何谓固结磨料加工?
何谓游离磨料加工?
他们各有何特点?
适用于什么场合?
固结磨料加工:
将磨粒或微粉与结合剂合在一起,形成一定的形状并具有一定强度,再采用烧结、粘结、涂敷等方法形成砂轮、砂条、油石、砂带等磨具。
其中用烧结方法形成砂轮、砂条、油石等称为固结磨具;用涂敷方法形成砂带,称为涂覆磨具或涂敷磨具
特点:
1)精密和超精密砂轮磨削
2)精密和超精密砂带磨削
3)其他加工
游离磨料加工:
在加工时,磨粒或微粉不固结在一起,而是成游离状态,其传统加工方法是研磨和抛光,近年来,在这些传统工艺的基础上,出现了许多新的游离磨料加工方法,如磁性研磨、弹性发射加工、液体动力抛光、液中研抛、磁流体抛光、挤压研抛、喷射加工等。
3-2试述超硬磨料磨具(金刚石砂轮、立方氮化硼砂轮)的特点。
超硬磨料磨具为什么会成为精密加工和超精密加工的主要工具之一?
超硬磨料在当前是指金刚石和立方氮化硼以及以它们为主要成分的复合材料。
特点:
两种材料均属于立方晶系、金刚石:
硬度高、有较高的耐磨性、很高的弹性模量,可以减小加工时工件的内应力、内部裂隙和其他缺陷。
有较大的热容量和良好的热导性,线膨胀系数小,熔点高。
立方氮化硼的硬度略低于金刚石,但内热性比金刚石高,有良好的化学稳定性,于碳在2000摄氏度时才起反应,故适于磨削钢铁材料。
由于它在高温下易与水反应,一次一般多用于干磨。
3-3在表示普通磨料磨具和超硬磨料磨具的技术性能时,有哪些技术性能的表示方法相同?
在哪些技术性能的表示方法不同?
为什么?
3-4为什么在超硬磨料磨具的结构中一般由磨料层、过渡层和基体三个部分组成?
过渡层起什么作用?
普通磨料磨具的结构为什么与超硬磨料磨具的结构不同?
3-5涂覆磨具在制造技术上的质量关键是哪些?
3-6试述近年来涂覆磨具在精密和超精密加工中所占的地位。
3-7试述涂覆磨具制造中三种涂覆方法的特点和应用场合。
3-8试从系统工程的角度分析精密磨削的技术关键
3-9试分析砂轮修整对精密磨削质量的影响
3-10精密磨削能获得高精度和小表面粗糙度表面的主要原因何在?
3-11试分析超硬磨料砂轮的各种修整方法的机理、特点和应用范围
3-12试分析普通磨料砂轮和超硬磨料砂轮在修整机理上的不同
3-13在超硬磨料砂轮磨削时如何选用磨削液
3-14超精密磨削的含义是什么?
镜面磨削的含义是什么?
3-15试从系统工程的角度来分析超精密磨削能达到高质量的原因。
3-16试分析超硬微粉砂轮超精密磨削的特点
3-17试比较精密砂轮磨削和精密砂带磨削的机理、特点和应用范围
3-18比较闭式砂带磨削和开式砂带磨削的特点和应用场合
3-19论述接触轮外缘截面形状及其结构对砂带磨削的影响
3-20分析接触轮外缘材料的种类及其硬度对砂带磨削的影响
3-21如何处理砂带磨削时的冷润与除尘问题?
4-1试述精密和超精密机床的国内外发展概况
4-2试述我国发展超精密机床概况
4-3以美国为例,说明精密机床的发展过程
4-4能代表超精密机床最高水平的是那几台超精密机床
4-5试述美国LLL实验室生产的DTM-3大型精密车床的主要技术性能
4-6试述美国LLL实验室生产的LODTM大型光学金刚石车床的主要技术性能
4-7试述美国Cranfield公司生产的OAGM2500大型超精密机床的必要性
4-8举例说明发展高效专用多功能超精密机床的必要性
4-9为什么超精密机床大部分都采用空气轴承,它有哪些优缺点
4-10空气主轴轴承有哪些常用的机构形式?
它有哪些优缺点?
4-11超精密主轴有哪些驱动方式?
各自的优缺点是什么?
4-12超精密车床有哪几种总体布局?
各自的优缺点是什么?
4-13简述精密和超精密机床使用的床身和导轨材料,并说明各自的优缺点
4-14简述精密和超精密机床的导轨结构形式,并说明各自的优缺点
4-15试述滚珠丝杠驱动系统的结构和优缺点
4-16试述超精密机床中使用的摩擦驱动机构的原理、结构和优缺点
4-17精密加工对微量进给装置的性能要求是什么?
4-18试述压电和电致伸缩传感器的结构和主要性能
4-19介绍几种典型的压电式或电致伸缩式微进给装置的原理、结构和性能
4-20介绍一种两坐标不见位移的激光在线检测系统
4-21介绍一种三坐标部件位移的激光在线检测系统
4-22提高机床结构的抗振性和减少机床内部振动有哪些办法?
4-23精密和超精密机床的隔振防振措施有哪些?
4-24试述温度变化对精密机床和精密加工误差的影响
4-25减少机床热变形的措施有哪些?
4-26美国LLL实验室对大型超精密车床如何进行恒温控制?
达到什么水平?
5-1试述精密加工中测量技术的新发展
5-2试述精密测量需要的环境条件
5-3怎样选择量具和量仪的材料?
5-4我国采用的长度标准是什么?
现在国际上用的长度基准是什么?
5-5如何正确使用量块以达到较高的测量精度?
5-6精加工工厂如何选用自己的长度基准?
5-7铸铁和花岗岩测量平台比较,各有哪些优缺点?
5-8简述直线度和直线运动精度的检测原理和方法
5-9简述平面度的检测原理和方法
5-10简述零件垂直度的检测方法
5-11试述使用圆光栅和圆感应同步器的静谧测量转台的主要优点和它能达到的测量精度
5-12试述精密多齿分度盘的测角原理,主要优点和能达到的测角精度
5-13试述精密多齿分度盘的小角度分度器的测量原理、结构和测角精度
5-14试述用两个多齿分度盘互检标定的原理和方法
5-15圆度有哪些测量方法
5-16试述圆度误差的评定方法?
5-17圆度仪有哪两种结构形式?
各自的优缺点如何?
5-18试述主轴回转精度的测量原理和方法
5-19试述单频激光测长度的原理
5-20试述双频激光测长度的原理,为何它比单频激光测量的精度高?
5-21试述激光测小角度的原理
5-22试述激光测量中使用空气参数补偿的必要性和家补偿后效果
5-23使用光纤传输的激光测量系统有哪些优点?
存在什么问题
5-24试述接触式激光干涉测量表面形貌和表面粗糙度的原理
5-25试述非接触式激光干涉测量表面形貌和表面粗糙度的原理
5-26简述精密自由曲面的测量原理
5-27简述已知设计模型的自由曲面的测量结果评定原理
5-28简述未知设计模型的自由曲面的测量结果评定原理
5-29简述测量精密自由曲面时的粗糙度和评定原理
6-1从提高加工精度的角度来看,试论述误差的隔离和消除、误差的补偿两条途径的实质和特点
6-2试阐述离线检测、在位检测和在线检测的含义,并分析其特点
6-3试论述进行在线检测的条件
6-4试述误差补偿的概念及其各种形式
6-5举例说明误差修正、误差校正、误差均化、误差“纯化”、误差分离等概念
6-6试述软件误差补偿与硬件误差补偿的特点及其相互间的关系
6-7论述综合误差补偿、多维误差补偿、预报型误差补偿的含义和意义
6-8试述误差补偿的过程
6-9试述误差补偿系统的组成及各组成部分的作用
6-10试分析三点法误差分离方法的特点和应用
6-11试分析三点转位误差分离原理及其在误差测量中的应用
6-12平面类形状位置误差的测量中,利用哪些方法来分离误差,它们在原理上有哪些共同点
6-13分析图6-12中车削工件圆度和圆柱度误差补偿的原理和特点
6-14通过在线检测与误差补偿系统应用实例(图6-11、图6-12、图6-13、图6-14、图6-15)总结在线检测与误差补偿的特点
6-15试述微位移系统的作用及其组成
6-16分析各种位移机构和器件的性能、特点及其应用场合
6-17分析平行弹性导轨微位移工作台的特点及其应用
6-18分析电磁控制微位移工作台的特点及其应用
6-19分析电致伸缩位移工作台的特点及其应用
6-20分析压电效应微位移工作台的特点及其应用
6-21试比较电致伸缩材料和压电材料的特点
6-22如何应用柔性铰链形成的连杆结构来获得微位移?
6-23如何应用变形量小的压电陶瓷元件来制作长行程的微位移机构
6-24如何利用3个管状压电器件来实现x、y方向移动和绕z轴转动的微位移。
请参考图6-25布局自行设计。
7-1试述研磨加工的机理和特点
7-2试述抛光加工的机理和特点
7-3试述研磨、抛光时加工表面产生变质层的机理和减少变质层的办法
7-4精密研磨、抛光时主要工艺因素有哪些?
7-5研磨精密平面时,应使用怎样的研磨机床和研具?
应有怎样的研磨运动?
7-6简述无损伤抛光方法
7-7简述弹性发射加工方法
7-8简述化学机械抛光
7-9简述电场和磁场辅助抛光方法的原理及其应用
7-10简述曲面研磨抛光方法、原理及适用范围
8-1试论述微细加工的含义
微细加工技术是指制造微笑尺寸零件的生产加工技术
广义讲,微细加工包含了各种传统精密加工方法和与传统精密加工方法完全不同的新方法,如切削加工、磨料加工、电火花加工、电解加工、化学加工、超声波加工、微波加工、等离子体加工、外延生长、激光加工、电子束加工、离子束加工、光刻加工、电铸加工等
狭义讲,微细加工主要是指半导体集成电路制造技术,因为微细加工和超微细加工时在半导体集成电路制造技术的基础上形成并发展起来的,他们是大规模集成电路和计算机技术的技术基础,是信息时代、微电子时代、光电子时代的关键技术之一。
如化学气相沉积、热氧化、光刻、离子束溅射、真空蒸镀以及整体微细加工技术
整体微细加工技术是指用各种微细加工方法在集成电路基片上制造出各种微型运动机械,即微型机械和微型机电系统
8-2试述微细加工与精密加工的关系
精密加工和微细加工时有着密切联系的,他们都是现代制造技术的前沿,微细加工时属于精密加工范畴内的,现代技术发展的很快,不仅出现了微细加工技术,而且出现了超微细加工技术。
8-3微小尺寸加工和一般尺寸加工有哪些不同?
微细加工主要指1mm以下的维系尺寸零件,加工精度为0.01~的加工,即微细度为级的亚毫米级的微细零件加工;超微细加工主要指1um以下的超微细尺寸零件,加工精度为0.1~0.01um的加工,即微细度为0.1um级的亚微米级的超微细零件加工。
今后的发展是要进行微细度为1nm以下的豪微米级的超微细加工
8-4试分析微细加工中的微切削去除机理
微细切削时,为保证工件尺寸精度要求,最后一次的表面切除层厚度必须小于尺寸精度值。
同时,由于工件尺寸小,从材料的强度和刚度上考虑,切削必须很小,因此迟到两可能小于材料的晶粒大小,切削就在晶粒内进行,这时称之为微切削去除
8-5何谓原子、分子加工单位?
以原子、分子为加工单位时的微细加工就是把原子、分子一个一个地去除,这时不管用什么加工方法,其所需临界加工能量密度相当于材料的结合能量与活化能量的总和,大致相等。
8-6论述分离、结合、变形三大类微细加工方法的含义及其常用加工方法的特点和应用范围
分离加工又称去除加工,其机理是从工件上去除一块材料,可以用分解、蒸发、扩散、切削等手段去分离。
结合加工又可称之为附着加工,其机理是在工件表面上附加一层别的材料。
如果这层材料与工件基体材料不发生物理化学作用,只是覆盖在上面,就称之为附着,也可称之为弱结合,典型的加工方法是电镀、蒸镀等。
如果这层材料与工件基体材料发生化学作用,生成新的物质层,则称之为结合,也可称之为强结合,典型的加工方法有氧化、渗碳等
变形加工又可称之为流动加工,其机理是通过材料流动使工件产生变形,其特点是不产生切削,典型的加工方法是压延、拉拔、挤压等
8-7试分析附着加工、注入加工、接合加工3种结合加工方法的含义,他们有哪些共同点与不同点?
对于结合加工,又可分为附着、注入、接合三类
附着指附加一层材料;
注入指表层经处理后产生物理、化学、力学性质变化,可统称为表面改性,或材料化学成分改变,或金相组织变化;
结合指焊接、粘接等
8-8试述电子束加工的原理、加工装置、特点及其应用
原理:
电子束加工是利用电子束的高能量密度进行钻孔、切槽、光刻等工作
加工装置主要由电子枪系统、真空系统、控制系统和电源系统等组成。
特点:
束径小、能量密度高
被加工对象范围广
加工速度快、效率高
控制性能好,易于实现自动化
应用范围很广,可用于打各种孔、切槽、焊接、光刻、表面改性等工件
它既是一种精密加工方法,又是一种重要的微细加工方法。
8-9电子束的热效应和化学效应有何不同?
利用种两种效应分别有哪些主要加工方法
由于电子束的能量密度高、作用时间短,所长生的热量来不及传导扩散就将工件被冲击部分局部融化、气化、蒸发成为雾状粒子而飞散,这时电子束的热效应。
电子束加工就是主要靠电子束的热效应现象
用功率密度相当低的电子束照射高分子材料时,即使几乎不会引起材料表面温度的上升,也会由于入射电子和高分子相碰使其分子链切断或重新聚合,从而使材料的相对分子质量和化学性质产生变化,这就是电子束的化学效应。
8-10试比较电子束光刻中两种曝光方式(扫描曝光、投影曝光)的特点
电子束扫描曝光:
质量、速度均很高*****
投影曝光:
优点是图形精度高、速度快、生产率高、成本低、可在基片或掩膜上复印
8-11试述离子束加工的原理、加工装置、特点及其应用
原理:
离子束加工时在真空条件下,将氩、氪、氙等惰性气体通过例子源产生离子束,经加速、集束、聚焦后,射到被加工表面上以实现各种加工的方法。
装置:
由离子源、真空系统、控制系统、电源等部分组成
特点:
加工精度和表面质量高
加工材料广泛
加工方法丰富多样
控制性能好,易于实现自动化
应用范围广之
应用:
可根据加工要求选择离子束的束径和能量密度,直径小、能量密度大的离子束用于去除加工;直径大、能量密度较低时适于镀膜、刻蚀;直径大、能量强的离子束适于注入加工。
8-12试述离子束的溅射过程模型(即离子碰撞过程)
8-13试论述离子束的几种溅射加工方法。
如何控制离子束去除加工、镀膜加工和注入加工的加工机理转变
离子束溅射去除加工:
离子束溅射去除加工简称为离子束去除加工
其加工原理:
是利用离子溅射,主要是一次溅射和二次溅射,它是一种最典型的原子、分子加工单位的微细加工方法
离子束溅射镀膜加工:
离子束溅