液压系统油缸支架工艺及夹具设计.docx
《液压系统油缸支架工艺及夹具设计.docx》由会员分享,可在线阅读,更多相关《液压系统油缸支架工艺及夹具设计.docx(35页珍藏版)》请在冰豆网上搜索。
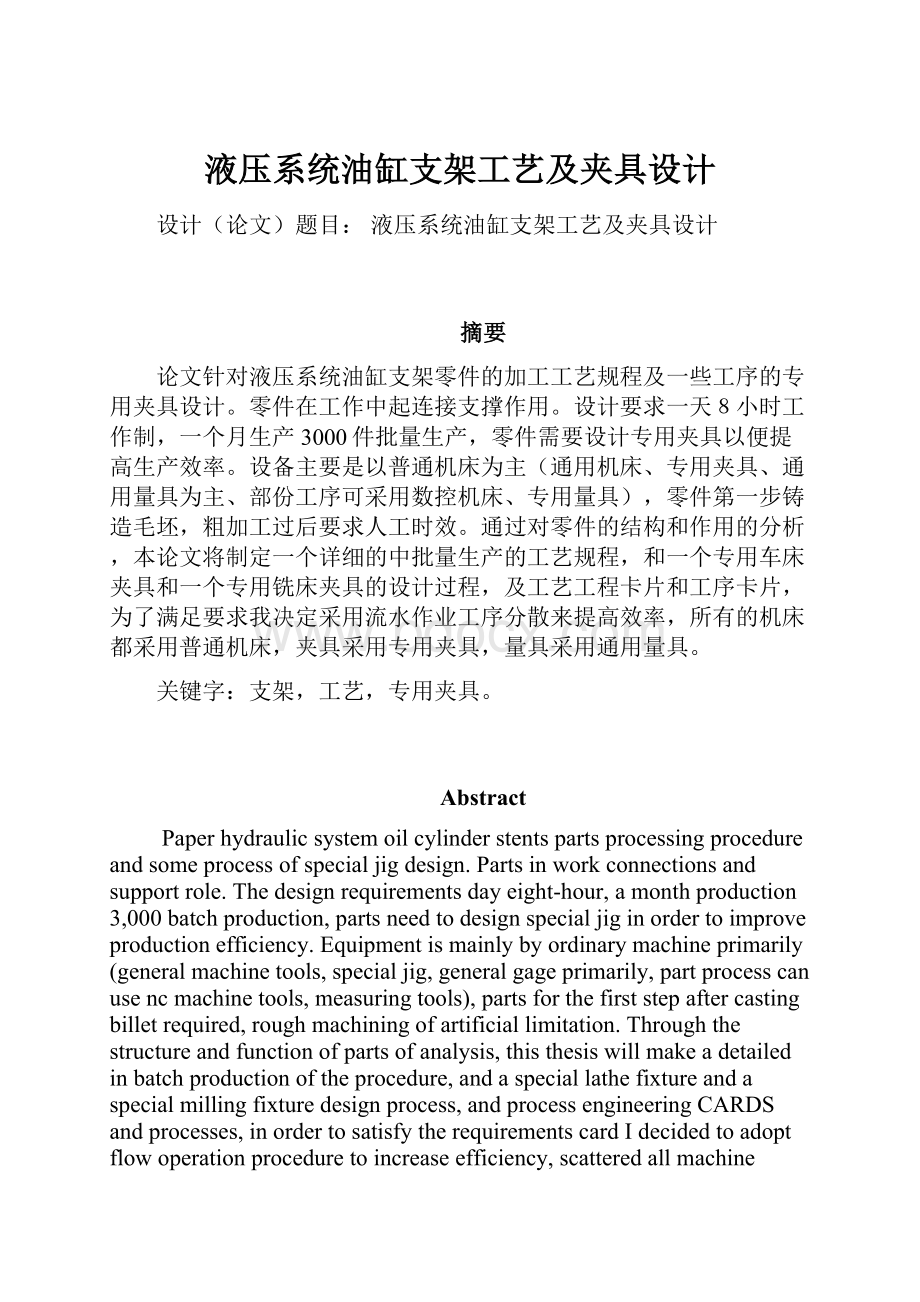
液压系统油缸支架工艺及夹具设计
设计(论文)题目:
液压系统油缸支架工艺及夹具设计
摘要
论文针对液压系统油缸支架零件的加工工艺规程及一些工序的专用夹具设计。
零件在工作中起连接支撑作用。
设计要求一天8小时工作制,一个月生产3000件批量生产,零件需要设计专用夹具以便提高生产效率。
设备主要是以普通机床为主(通用机床、专用夹具、通用量具为主、部份工序可采用数控机床、专用量具),零件第一步铸造毛坯,粗加工过后要求人工时效。
通过对零件的结构和作用的分析,本论文将制定一个详细的中批量生产的工艺规程,和一个专用车床夹具和一个专用铣床夹具的设计过程,及工艺工程卡片和工序卡片,为了满足要求我决定采用流水作业工序分散来提高效率,所有的机床都采用普通机床,夹具采用专用夹具,量具采用通用量具。
关键字:
支架,工艺,专用夹具。
Abstract
Paperhydraulicsystemoilcylinderstentspartsprocessingprocedureandsomeprocessofspecialjigdesign.Partsinworkconnectionsandsupportrole.Thedesignrequirementsdayeight-hour,amonthproduction3,000batchproduction,partsneedtodesignspecialjiginordertoimproveproductionefficiency.Equipmentismainlybyordinarymachineprimarily(generalmachinetools,specialjig,generalgageprimarily,partprocesscanusencmachinetools,measuringtools),partsforthefirststepaftercastingbilletrequired,roughmachiningofartificiallimitation.Throughthestructureandfunctionofpartsofanalysis,thisthesiswillmakeadetailedinbatchproductionoftheprocedure,andaspeciallathefixtureandaspecialmillingfixturedesignprocess,andprocessengineeringCARDSandprocesses,inordertosatisfytherequirementscardIdecidedtoadoptflowoperationproceduretoincreaseefficiency,scatteredallmachineUSESordinarymachine,fixtureusingspecialjig,measuringusinguniversalmeasuringtool.
Keyword:
stents,craft,specialjig
绪论
毕业设计是每一个学校对学生在学完了大学的全部基础课、技术基础课以及全部专业课之后进行的一次考核,考查学生是否具有能力去完成一项与专业相关或与专业无关的任务,这就要考查学生有没有具备独力学习、合作、独力思考的能力,这也是大学生该具备的能力,所以毕业设计是对学生综合能力的一次大考验,也是学生能否合格拿到毕业证的标准。
机械加工工艺及夹具设计是数控专业非常重要的两们课程,它考查学生对零件从材料到成品全过程的掌握程度,也是对我们在大学所学课程的一次综合性的考核,加工工艺是工人进行加工的一个依据,所有零件只有制定合理的工艺才能加工出合格的零件来,夹具就是让工件在机械加工时和机床保持正确的们位置,我加工的零件是一个液压系统油缸支架,它将用到车、镗、铣,钻床,我将设计出零件的机械加工工艺规程,要打印出机械加工工艺过程卡片、机械加工工序卡片,设计出车和铣专用夹具,写出夹具设计说明书;考虑到是一个中批量生产,毛坯采用砂型机器造型,采用工序分散原则,流水作业提高生产效率。
我希望从这次毕业设计中学到更多专业知识,对自己未来将从事的工作进行一次适应性训练,从中锻炼自己分析问题、解决问题的能力,为今后的工作打下一个好的基础。
由于能力有限,设计尚有许多不足之处,恳请各位老师给予指教。
1.液压系统油缸支架工艺及夹具设计
1.1毕业设计题目及技术要求
毕业设计题目:
液压系统油缸支架工艺及夹具设计;
要求:
要求一天8小时工作制,一个月生产3000件,设备主要是以普通机床为主(通用机床、专用夹具、通用量具为主、部份工序可采用数控机床、专用量具),零件粗加工过后要求人工时效。
题目分析:
要加工的工件是液压系统油缸支架,支架在机床中起支撑作用,材料是HT250,零件的端面Φ150中心线不垂直度允许误差0.04mm,所以必需采用端面和内孔一次性装夹加工,C面粗糙度是1.6要求在钳工台上刮削,其余的表面粗糙度用车床或铣床直接加工。
设计出零件的机械加工工艺规程,要打印出机械加工工艺过程卡片、机械加工工序卡片,设计出两个专用夹具,写出夹具设计说明书;考虑到是一个中批量生产,毛坯采用砂型机器造型,采用工序分散原则,流水作业提高生产效率,通过我对零件的初步分析,加工这人零件需要用到车、镗、铣、钻床,我设计一个车床夹具和一个铣床夹具。
1.2零件的分析
1.2.1零件的作用
题目是液压系统油缸支架,零件在工作中起支撑作用。
1.2.2工艺路线分析
零件机械加工的工艺路线时指零件生产过程中,由毛坯到成品所经过工序的先后顺序。
在拟定工艺路线时,除了首先考虑定位基准的选择外,还应当考虑各表面加工方法的选择,工序集中与分散的过程,加工阶段的划分和工序先后顺序的安排问题。
所需加工的表面的加工方法
端面E:
表面粗糙度值6.3um,采用加工方法,粗车——精车
内孔:
表面粗糙度值6.3um,采用加工方法,粗镗——精镗
支架侧耳:
表面粗糙度值1.6um,采用加工方法,粗铣——半精铣——精铣
Φ16孔:
表面粗糙度值3.2um,但后面需用于定位,所以提高精度,采用加工方法,钻——扩——铰
Φ17孔:
表面粗糙度值12.5um,采用加工方法,钻
螺纹孔:
采用加工方法,钻——攻丝
2.加工零件工艺规程设计
2.1工艺设计基础理论知识
机械加工工艺是指用机械加工的方法改变毛坯的形状、尺寸、相对位置和性质使其成为合格零件的全过程,加工工艺是工人进行加工的一个依据。
机械加工工艺流程是工件或者零件制造加工的步骤,采用机械加工的方法,直接改变毛坯的形状、尺寸和表面质量等,使其成为零件的过程称为机械加工工艺过程。
比如一个普通零件的加工工艺流程是粗加工-精加工-装配-检验-包装,就是个加工的笼统的流程。
机械加工工艺就是在流程的基础上,改变生产对象的形状、尺寸、相对位置和性质等,使其成为成品或半成品,是每个步骤,每个流程的详细说明,比如,上面说的,粗加工可能包括毛坯制造,打磨等等,精加工可能分为车,钳工,铣床,等等,每个步骤就要有详细的数据了,比如粗糙度要达到多少,公差要达到多少。
技术人员根据产品数量、设备条件和工人素质等情况,确定采用的工艺过程,并将有关内容写成工艺文件,这种文件就称工艺规程。
这个就比较有针对性了。
每个厂都可能不太一样,因为实际情况都不一样。
总的来说,工艺流程是纲领,加工工艺是每个步骤的详细参数,工艺规程是某个厂根据实际情况编写的特定的加工工艺。
机械加工工艺规程是规定零件机械加工工艺过程和操作方法等的工艺文件之一,它是在具体的生产条件下,把较为合理的工艺过程和操作方法,按照规定的形式书写成工艺文件,经审批后用来指导生产。
机械加工工艺规程一般包括以下内容:
工件加工的工艺路线、各工序的具体内容及所用的设备和工艺装备、工件的检验项目及检验方法、切削用量、时间定额等。
制订工艺规程的步骤
2.1.1毛坯的选择
在制订机械加工工艺规程时,正确选择合适的毛坯,对零件的加工质量、材料消耗和加工工时都有很大的影响。
显然毛坯的尺寸和形状越接近成品零件,机械加工的劳动量就越少,但毛坯的制造成本就越高,所以应根据生产纲领,综合考虑毛坯制造和机械加工的费用来确定毛坯,以求得最好的经济效益。
毛坯的种类
1)铸件
铸件适用于形状较复杂的零件毛坯。
其铸造方法有砂型铸造、精密铸造、金属型铸造、压力铸造等,较常用的是砂型铸造。
2)锻造
锻件适用于强度要求高、形状比较简单的零件毛坯。
其锻造方法有自由锻和模锻两种。
3)型材
型材有热轧和冷拉两种。
热轧适用于尺寸较大、精度较低的毛坯;冷拉适用于尺寸较小、精度较高的毛坯。
4)焊接件
焊接件是根据需要将型材或钢板等焊接而成的毛坯件,它简单方便,生产周期短,但需经时效处理后才能进行机械加工。
5)冷冲压件
冷冲压件毛坯可以非常接近成品要求,在小型机械、仪表、轻工电子产品方面应用广泛。
但因冲压模具昂贵而仅用于大批量生产。
毛坯选择时应考虑的因素
1)零件的材料及机械性能要求
零件材料的工艺特性和力学性能大致决定了毛坯的种类。
例如铸铁零件用铸造毛坯;钢质零件当形状简单且力学性能要求不高时常用棒料,对于重要的钢质零件,为获得良好的力学性能,应用锻件,当形状复杂力学性能要求不高时用铸钢件;有色金属零件常用型材或铸造毛坯。
2)零件的结构形状和外形尺寸
大型且结构较简单的零件毛坯多用砂型铸造或自由锻造;结构复杂的多用铸造;小型零件可用模锻件或压力铸造毛坯;板状钢质零件多用锻件毛坯;轴类零件的毛坯,若台阶直径相差不大,可用棒料;若各台阶尺寸相差较大,则宜选择锻件。
3)生产纲领
大批大量生产中,应采用精度和生产都较高的毛坯制造方法。
铸件采用金属模机器造型和精密铸造,锻件用模锻或精密锻造。
在单件小批生产中用木模手。
工造型或自由锻来制造毛坯。
4)现有生产条件
确定毛坯时,必须结合具体生产条件,如现场毛坯制造的实际水平和能力、外协的可能性等,否则就不现实。
5)充分利用新工艺、新材料
为节约材料和能源,提高机械加工生产率,应充分考虑精密铸造、精锻、冷轧、冷挤压、粉末冶金、异型刚材及工程塑料等在机械中的应用,这样,可大大减少机械加工量,甚至不需要进行加工,经济效益非常显著。
2.1.2定位基准的选择
在制订工艺规程的时候,定位基准选择的正确与否,对能否保证零件的尺寸精度和相互位置精度要求,以及对零件各表面间的加工顺序安排都有很有大影响,当用夹具安装工件时,定位基准的选择还会影响到夹具结构的复杂程度。
精基准的选择原则
1)基准重合原则
2)基准统一原则
3)自为基准原则
4)互为基准原则
5)便于装夹原则
粗基准的选择原则
1)选择重要表面为粗基准
2)选择不加工表面为粗基准
3)选择加工余量最小的表面为粗基准
4)选择较为平整光洁、加工面积较大的表面为粗基准
5)粗基准在同一尺寸方向上只能用一次
2.1.3工艺路线制定
零件机械加工的工艺路线是指零件生产过程中,由毛坯到成品所经过工序先后顺序。
在拟定工艺路线时,除了首先考虑定位基准的选择外,还应当考虑各表面加工方法的选择,工序集中与分散的程度,加工阶段的划分和工序先后顺序的安排问题。
目前还没有一套通用而完整的工芤路线拟定方法,只总结出一些综合性原则,在具体运用这些原则时,要根据具体条件综合分析。
表面加工方法的选择
加工阶段的划分
加工顺序的安排
工序的集中与分散
2.2支架零件工艺设计
2.2.1支架零件毛坯的选择
零件的材料为灰铸铁HT250。
考虑到零件结构简单,工艺性好,在工作过程中受力不大及没有经常承受交变载荷,因此,应该选用铸件。
由于零件年产量为3000件,以达到大批生产的水平,而且首先采用普通机床加工,零件的轮廓尺寸不大,重量在12kg以下,故可采用机械造型中的金属模铸造。
这从提高生产率,保证加工精度上考虑,也是应该的。
2.2.2支架零件定位基准的选择
基面的选择是工艺规程设计中的重要工作之一。
基面选择得正确与合理,可以使加工质量得到保证,生产率得以提高。
否则,加工工艺过程中会问题百出,更有甚者,还会造成零件大批报废,使生产无法正常进行。
粗基准的选择
按照有关粗基准原则:
选择重要表面为粗基准、选择不加工表面为粗基准、选择加工余量小的表面为粗基准等,应以Φ105f6mm圆柱右端面为粗基准面(两个定位板),限制3个自由度,用Φ35H7铸造孔(弹簧销定位)限制两个移动的自由度,再用与Φ125mm相切的面(支撑钉定位)限定一个转动的自由度,达到完全定位。
精基准的选择
精基准选择的原则有:
基准重合原则、基准统一原则、互为基准原则和自为基准原则。
在选择时,主要应考虑基准重合的问题。
当设计基准与工序基准不重合时,应该进行尺寸换算,这在以后还要专门计算,此处不再重复。
2.2.3支架零件工艺路线制定
制定工艺路线的出发点,应该是使零件的几何形状、尺寸精度及位置精度等技术要求能得到合理的保证。
在生产纲领已确定为大批生产的条件下,可以考虑采用万能性机床配以专用夹具,并尽量使工作集中来提高生产率。
除此以外,还应当考虑经济效率,以便使生产成本尽量下降。
工艺路线1
工序号
工序名称
工序内容
0
铸
铸造毛坯
10
漆
涂防锈漆
20
热
人工时效处理
30
车
以外圆、B面定位,两侧耳夹紧。
1.粗车φ200端面E
2.粗镗内孔
40
铣
以E面、内孔、侧耳C定位,端面夹紧。
粗铣D面
50
铣
以D面、端面E、内孔定位,端面夹紧。
粗铣侧耳C面
60
热
人工时效处理
70
铣
以E面、内孔、侧耳C定位,端面夹紧。
精铣D面
80
铣
以D面、端面E、内孔定位,端面夹紧。
精铣侧耳C面
90
钻
以D面、端面E、内孔定位,端面夹紧。
1.钻2-φ16
2.扩2-φ16
3.铰2-φ16
100
车
以侧面C、2-φ16定位,侧耳夹紧。
1.精车φ200端面
2.精镗内孔
3.倒角
110
钻
以D面、端面E、内孔定位,端面夹紧。
钻4-φ17
120
锪
以D面、端面E、内孔定位,端面夹紧。
锪4-φ26
130
钻
以D面、端面E、内孔定位,端面夹紧。
1.钻2-M6中心孔
2.钻2-M6底孔孔
140
攻
以D面、端面E、内孔定位,端面夹紧。
1.倒角
2.攻丝
150
钻
以侧面C、2-φ16定位,侧耳夹紧。
1.钻8-M12中心孔
2.钻8-M12底孔孔
160
攻
以侧面C、2-φ16定位,侧耳夹紧。
1.倒角
2.攻丝
170
钳
去毛刺
180
洗
清洗
190
油
涂防锈油
200
终检
终检
工艺路线2
工序号
工序名称
工序内容
0
铸
铸造毛坯
10
漆
涂防锈漆
20
热
人工时效处理
30
车
以外圆、B面定位,两侧耳夹紧。
1.粗车φ200端面E
2.粗镗内孔
3.精车φ200端面E
4.精镗内孔
40
铣
以E面、内孔、侧耳C定位,端面夹紧。
1.粗铣D面
2.半精铣D面
3.精铣D面
50
铣
以D面、端面E、内孔定位,端面夹紧。
1.粗铣侧耳C面
2.半精铣侧耳C面
3.精铣侧耳C面
60
钻
以D面、端面E、内孔定位,端面夹紧。
4.钻2-φ16
5.扩2-φ16
6.铰2-φ16
70
车
以侧面C、2-φ16定位,侧耳夹紧。
4.精车φ200端面
5.精镗内孔
6.倒角
80
钻
以D面、端面E、内孔定位,端面夹紧。
1.钻4-φ17
2.锪4-φ26
90
钻
以D面、端面E、内孔定位,端面夹紧。
1.钻2-M6中心孔
2.钻2-M6底孔孔
3.倒角
4.攻丝
100
钻
以侧面C、2-φ16定位,侧耳夹紧。
1.钻8-M12中心孔
2.钻8-M12底孔孔
3.倒角
4.攻丝
110
钳
去毛刺
120
洗
清洗
130
油
涂防锈油
140
终检
终检
、工艺方案的比较与分析
上述两个方案的特点在于:
方案一和方案二在0-2工序相同,方案一采用工序分散了,有利于大批量生产,方案二采用工序集中在位置精度上的要求仍不易保证,在一道工序中同时钻几个孔,只能选用专门设计的组合机床(但在成批生产时,在能保证加工精度的情况下,应尽量不选用专用组合机床)加工,这样便增加了加工设备的要求,经济花费会相应提高,综上所诉我决定采用方案一,设计专用夹具在普通机床上加工,以提高加工效率。
2.3、机械加工余量、工序尺寸及毛坯尺寸的确定
2.3.1、右端面的加工余量
按照《金属机械加工工艺人员手册》,取毛坯的单边加工余量Z=3mm,铸件尺寸精度等级为5,固偏差为±1。
粗车加工余量:
分两次走刀,单边加工余量为Z=3mm,(《简明机械加工工艺手册》),加工精度等级为IT11,所以加工偏差为
(入体方向)
2.3.2、内孔的加工余量
按照《金属机械加工工艺人员手册》,取毛坯的单边加工余量Z=4.5mm,铸件尺寸精度等级为6。
半精镗加工余量:
单边加工余量为0.5见《简明机械加工工艺手册》,加工精度为IT9.
粗镗加工余量:
单边为
=4.5-0.5=4mm,分两次走刀,固每次加工余量为2mm(《简明机械加工工艺手册》),加工精度等级为IT11
2.3.3、侧耳的加工余量
按照《金属机械加工工艺人员手册》,取毛坯的单边加工余量Z=4.5mm,铸件尺寸精度等级为6。
半精铣加工余量:
单边加工余量为0.5见《简明机械加工工艺手册》,加工精度为IT9.
精铣加工余量:
单边加工余量为0.1见《简明机械加工工艺手册》,加工精度为IT7.
加工余量:
单边为
=4.5-0.5=4mm,分两次走刀,固每次加工余量为2mm(《简明机械加工工艺手册》),加工精度等级为IT11
2.3.4、4-φ17孔的加工余量
孔的精度要求为IT8,《金属机械加工工艺人员手册》表13-14,确定工序尺寸及余量为:
毛坯孔:
φ15mm
钻孔:
φ17mmZ=2mm
2.3.5、2-φ16孔的加工余量
毛坯孔:
φ14mm
钻孔:
φ15.5mmZ=1.5mm
扩孔:
φ15.9mmZ=0.4mm
铰孔:
φ16mmZ=0.1mm
2.3.6、M12螺纹孔的加工余量
孔的精度要求为IT7,《金属机械加工工艺人员手册》表13-14,确定工序尺寸及余量为
钻孔:
φ11.85mm
攻丝:
M12mmZ=0.15mm
2.3.7、M6螺纹孔的加工余量
孔的精度要求为IT7,《金属机械加工工艺人员手册》表13-14,确定工序尺寸及余量为
钻孔:
φ5.85mm
攻丝:
M6mmZ=0.15mm
2.4切削用量选择
工序3、粗车端面E,内孔选用机床:
CA6140车床。
.粗车E端面
零件材料为灰铸铁HT250,故可用90°外圆硬质合金车刀。
查《简明机械加工工艺手册》(简称简明手册)。
查《机械加工工艺人员手册》(简称工艺手册)表11-69可知,
=0.3-0.6mm/r,取fz=0.4mm/r。
查《工艺手册》表14-77,取u=,80m/min则:
=1000u/dπ=200(r/min)
.粗镗内孔
零件材料为灰铸铁HT250,故可用90°镗刀。
查《简明机械加工工艺手册》(简称简明手册)。
查《机械加工工艺人员手册》(简称工艺手册)表11-69可知,
=0.3-0.6mm/r,取fz=0.4mm/r。
查《工艺手册》表14-77,取u=40m/min则:
=1000u/dπ=90(r/min)
工序4粗铣D面,采用卧式铣床X61W
零件材料为灰铸铁HT250,故可用硬质合金圆柱铣刀。
查《简明机械加工工艺手册》(简称简明手册)。
查《机械加工工艺人员手册》(简称工艺手册)表11-69可知,
=0.10-0.25mm/r,取fz=0.2mm/r。
查《工艺手册》表14-77,取u=50m/min则:
=1000u/dπ=600(r/min)
工序5粗铣侧耳C面
零件材料为灰铸铁HT250,故可用硬质合金圆柱铣刀。
查《简明机械加工工艺手册》(简称简明手册)。
查《机械加工工艺人员手册》(简称工艺手册)表11-69可知,
=0.10-0.25mm/r,取fz=0.2mm/r。
查《工艺手册》表14-77,取u=50m/min则:
=1000u/dπ=600(r/min)
工序8精铣D面,采用卧式铣床X61W
零件材料为灰铸铁HT250,故可用硬质合金圆柱铣刀。
查《简明机械加工工艺手册》(简称简明手册)。
查《机械加工工艺人员手册》(简称工艺手册)表11-69可知,
=0.10-0.25mm/r,取fz=0.1mm/r。
查《工艺手册》表14-77,取u=50m/min则:
=1000u/dπ=600(r/min)
工序5粗铣侧耳C面
零件材料为灰铸铁HT250,故可用硬质合金圆柱铣刀。
查《简明机械加工工艺手册》(简称简明手册)。
查《机械加工工艺人员手册》(简称工艺手册)表11-69可知,
=0.10-0.25mm/r,取fz=0.1mm/r。
查《工艺手册》表14-77,取u=50m/min则:
=1000u/dπ=600(r/min)
工序10、钻2Xφ16底孔,选用机床:
Z525型钻床。
.钻φ16的底孔,选用高速钢麻花钻,d=15.5mm。
查《简明手册》表11-10,f=0.18∽0.22mm/r,按机床试用说明书取f=0.2mm/r.
查《简明手册》表11-12,取U=0.2m/s=21m/min,则
n
=1000u/πd=1000×12/(π×5.8)=431.48(r/min)
按机床使用说明书取n
=450r/min,所以实际切削速度为:
U=πdn
/1000=π×5.8×680/1000=21(m/min)
工序11、精车端面E,内孔选用机床:
CA6140车床
1.精车φ200端面E
零件材料为灰铸铁HT250,故可用90°外圆硬质合金车刀。
查《简明机械加工工艺手册》(简称简明手册)。
查《机械加工工艺人员手册》(简称工艺手册)表11-69可知,
=0.3-0.6mm/r,取fz=0.4mm/r。
查《工艺手册》表14-77,取u=,100m/min则:
=1000u/dπ=250(r/min)
.精镗内孔
零件材料为灰铸铁HT250,故可用90°镗刀。
查《简明机械加工工艺手册》(简