冶炼厂及其周边环境污染数据分析报告.docx
《冶炼厂及其周边环境污染数据分析报告.docx》由会员分享,可在线阅读,更多相关《冶炼厂及其周边环境污染数据分析报告.docx(51页珍藏版)》请在冰豆网上搜索。
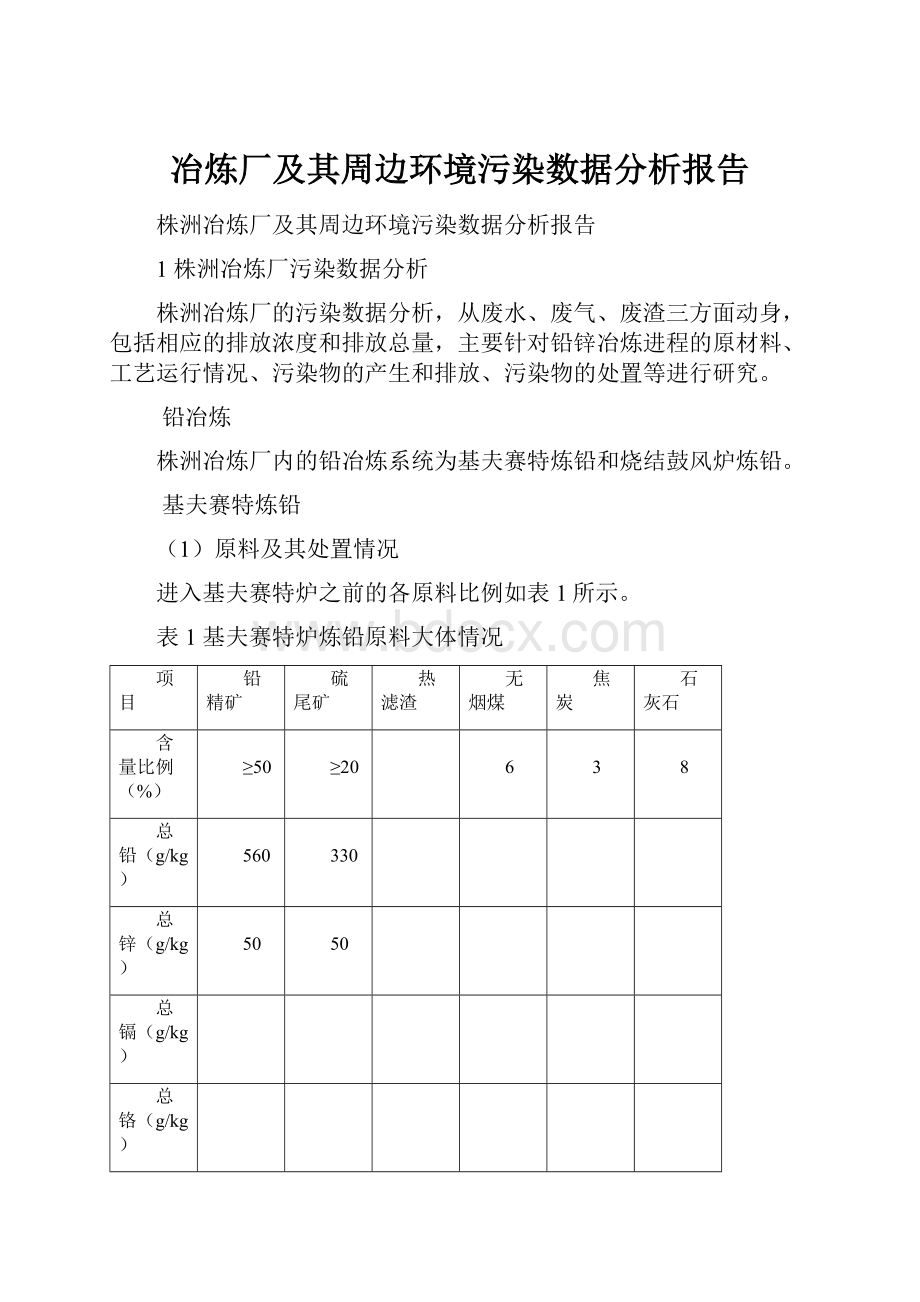
冶炼厂及其周边环境污染数据分析报告
株洲冶炼厂及其周边环境污染数据分析报告
1株洲冶炼厂污染数据分析
株洲冶炼厂的污染数据分析,从废水、废气、废渣三方面动身,包括相应的排放浓度和排放总量,主要针对铅锌冶炼进程的原材料、工艺运行情况、污染物的产生和排放、污染物的处置等进行研究。
铅冶炼
株洲冶炼厂内的铅冶炼系统为基夫赛特炼铅和烧结鼓风炉炼铅。
基夫赛特炼铅
(1)原料及其处置情况
进入基夫赛特炉之前的各原料比例如表1所示。
表1基夫赛特炉炼铅原料大体情况
项目
铅精矿
硫尾矿
热滤渣
无烟煤
焦炭
石灰石
含量比例(%)
≥50
≥20
6
3
8
总铅(g/kg)
560
330
总锌(g/kg)
50
50
总镉(g/kg)
总铬(g/kg)
总砷(g/kg)
3
总汞(g/kg)
总镍(g/kg)
总铜(g/kg)
4
1
总铁(g/kg)
90
80
45
总硫(g/kg)
180
160
8
8
在最初的Kivect炉工艺设计进程中考虑到热滤渣注1的应用,在实际运行进程中,热滤渣的应用较少,主要原料为铅精矿,硫尾矿、粉煤、焦炭、石灰石等。
其中铅精矿和硫尾矿的主要金属成份为铅、锌、铜、铁、砷,含硫量在160g/kg以上,硫尾矿来源于常规法炼锌系统产出的酸浸渣,基质成份硅和钙因在工艺进程中状态稳定,在此再也不进行考虑。
注1:
热滤渣是镍阳极泥经加热过滤硫后的一种含贵金属的冶金中间产品,含硫约50%,(元素硫为主),还有铜、镍、铁的硫化物、硫酸盐、造渣氯化物等,贵金属品位%。
基夫赛特炉入炉物料技术参数见表2。
表2物料技术参数
物料名称
物料含水(%)
粒度(mm)
堆密度(t/m3)
铅精矿
8~10
锌系统硫尾矿
约10(预干燥后)
1~3
石灰石
5
3~5
无烟煤
≤1
焦炭
5~8
0~30
Kivcet炉对还原剂焦炭的入炉要求为:
熔炼区粒度5~15mm,电热区粒度20~30mm,水分小于1%;对铅精矿、硫尾矿渣、烟尘、石灰石、无烟煤等物料的入炉要求为:
混合料粒度≤1mm,水分小于1%。
原料制备流程如图1所示。
图1原料制备流程
炉料粒度的控制是由物料在炉内反映的传热传质要求决定的:
铅精矿的氧化脱硫进程是一种闪速熔炼,在喷枪出口即与氧气混合,在基夫赛特炉反映塔上部迅速反映。
粒度减小,反映速度成几何倍数加速,单位质量物料反映面积达105~106cm2/kg,相反,对焦炭的粒度要求则是为了降低其在反映塔上部的反映和燃烧速度,使其在反映塔下部形成焦滤层,对金属氧化物熔体进行捕集并还原。
(2)基夫赛特炉运行
基夫赛特炉依照其功能分成熔炼区和电热区两部份,熔炼区与电热区之间用铜水套隔墙隔开。
熔炼区的顶部安装投料喷嘴,炉料和氧气通过喷嘴喷入反映塔进行氧化反映。
在反映塔内,炉料中的PbS被迅速氧化生成PbO,形成高温熔融物,进入熔炼区熔池,PbO通过漂浮在熔池上的焦炭过滤层时被还原,形成液态金属铅;熔炼进程产生的烟气通过竖烟道余热锅炉和电收尘器进行降温除尘,富集的烟尘返回Kivcet炉,高浓度二氧化硫送往硫酸系统制酸;渣和铅通过隔墙流向电热区。
竖炉烟尘成份(返尘成份)含铅≥50%,含硫≥8%,含锌≥6%。
图2基夫赛特炉电热区烟气处置流程
基夫赛特炉电热区顶部安装有电极,电极插入渣层,为电热区补充热量。
电热区的主要作用是:
使流入电热区的熔体沉淀分离;进一步还原渣中的PbO,使渣含铅降低至3%左右;使渣中的金属氧化物还原挥发。
挥发的金属及金属氧化物以烟尘的形式随烟气从电热区出口排出,烟气先进入电热区余热锅炉降温并沉降部份烟尘,然后通过袋式除尘器捕集细尘,烟气达标后排放。
基夫赛特炉电热区烟气的特点是:
温度高,含尘高,SO2浓度低等,其性质决定了该烟气必需采用先经余热利用降温,再经除尘器收尘,然后放空的处置流程。
基大赛特炉电热区烟气由以下几种气体组成:
①炉顶和电极间隙密封用的氮气。
氮气量大约3000m3/h(标)左右。
②铅锌氧化物的还原产物。
由于还原反映是在1300℃左右的熔体内进行的,被还原出的部份Pb和几乎全数的Zn形成金属蒸气挥发进入烟气中。
③炉外渗入的空气。
由于电热区炉膛是微负压(约-l5Pa左右),故有少量的空气渗入。
④烟气二次燃烧的产物。
电热区的烟气必需进行二次燃烧,通过引人空气,使烟气中CO、铅、锌氧化生成CO2、PbO、ZnO。
电热区最终烟气的主要成份是N2、CO2和O2,烟尘的主要成份是ZnO和PbO。
由于通过二次燃烧,烟气具有很高的温度。
基夫赛特炉设有专门的复燃室,烟气在复燃室二次燃烧后再进入余热锅炉,产出更多的饱和蒸汽,尽可能地利用烟气余热。
电热区烟气和烟尘参数为:
烟气量(标)7800m3/h,烟气温度1350℃,烟气含尘265g/m3。
烟气和烟尘成份见表3和表4。
表3电热区烟气成份(体积分数)%
SO2
CO2
O2
N2
H2O
合计
6~
7~
85~86
100
表4电热区烟尘成份(质量分数)%
PbO
ZnO
CaO
SiO2
其他
合计
100
由表3可以看出,电热区烟气SO2浓度相对较低,不适宜于制酸(需进行脱硫处置),主要的烟气成份为N2。
由表4中可以看出,烟尘的ZnO质量分数达到了60%以上,PbO的质量分数达到了20%以上,烟尘通过布袋收尘富集以后送往锌系统进行回收。
(3)基夫赛特炉渣及其处置
图3Kivcet炉渣处置进程
基夫赛特炉产生的冶炼渣,进入烟化炉进行吹炼处置,吹炼以后的炉渣进行粒化冲渣和冷却处置,进程中的全数用水进行循环利用,水淬以后的无害渣外卖。
烟化炉吹炼以后的烟气进入余热锅炉进行热量回收利用,以后通过布袋收尘,尾气送脱硫处置,烟尘的主要成份为氧化锌,送锌系统进行冶炼回收利用。
(4)粗铅精炼
通过基夫赛特炉熔炼以后的粗铅,含铅量在95%~97%,一般含有3~5%的杂质成份,如金、银、铜、铋、砷、铁、锡、锑、硫等,见表5:
表5粗铅的化学成份(%)
编号
化学成份(%)
Pb
Cu
As
Sb
Sn
Bi
S
Fe
Au(g/t)
Ag(g/t)
1
2
3
粗铅需通过精炼才能普遍利用。
精炼目的:
一是除去杂质。
由于粗铅含有上述杂质,影响了铅的性质,使铅的硬度增加,韧性降低,对某些试剂的抗蚀性能减弱,使之不适于工业应用,因此降低了铅的利用价值。
因此必需通过精炼,提高铅的纯度。
二是回收贵金属,尤其是银,由表5中可以看出,粗铅中银的质量含量1800g/t,粗铅中所含贵金属价值有时会超过铅的价值,在电解进程中金银等贵金属富集于阳极泥中。
粗铅精炼的方式有两类,第一类为火法精炼,第二类为先用火法除去铜与锡后,再铸成阳极板进行电解精炼,株冶应用的为第二类。
电解精炼的长处是能使铋及贵金属富集于阳极泥中,有利于综合回收,因此金属回收率高、劳动条件好,并产出纯度很高的精铅。
其缺点是基建投资大,且电解精炼仍需要火法精炼除去铜锡等杂质,火法精炼只是初步精炼,其任务是将粗铅中的铜和砷、锑、锡除至必然程度,并调整锑含量,浇注成化学质量和物理规格均知足要求的阳极板,为电解精炼做好准备。
具体的工艺流程图如图4所示:
图4基夫赛特炉粗铅精炼
通过Kivcet炉熔炼以后的取得的粗铅再也不含有硫元素成份,在铅熔锅火法初步精炼时不会产生二氧化硫,初步精炼以后的粗铅进电解车间进行电解精炼,酸解液为硅氟酸注2,电解进程中产生的氧化铅渣与火法初步精炼产生的熔铅浮渣送反射炉再次进行熔炼,产生的烟气通过布袋收尘以后烟尘返回炼铅系统,废气经处置以后达标排放。
电解车间在电解、出槽、搬运、卸皮进程会产生硅氟酸的酸雾。
反射炉产生的冰铜与电解产生的阳极泥送希贵厂提取珍贵金属。
总的来讲,基夫赛特工艺的特点是含铅炉料与工业纯氧一路喷入炉内,同时加入还原用焦炭,在炉内一次冶炼成粗铅并排出弃渣。
经净化后的烟气用于制酸。
生产进程是在单体设备中持续进行,不需烧结给料,不需增加设备就可以够部份地回收炼铅原料中的锌,能够处置低品位物料,烟气量小,烟气SO2浓度高。
(注2:
盐酸和硫酸只能与铅的表面作用,形成几乎不溶解的气化铅和硫酸铅表面薄膜;用硝酸或醋酸溶液进行的铅电解精炼时,不能产出密实块状的铅沉积物,而且采用硝酸电解液电解时,一部份硝酸根会在阴极上还原成氮化物。
硅氟酸对铅的溶解度大,电导率较髙,稳定性也较好,价钱相对较低。
)
(5)废气及相应重金属排放情况
基夫赛特炼铅法每一年生产粗铅12万吨,电铅10万吨,废气及相应重金属排放情况如表6与表7所示。
(数据应历时详细分析)
表6废气及重金属污染物排放强度
冶炼工艺流程
废气排放量(Nm3/t)
粉尘排放强度(kg/t产品)
重金属排放强度(kg/t产品)
Cu
Pb
Zn
Cd
As
基夫赛特炉-烟化炉
-制酸/产出粗铅
40086
电解-铅锅熔铸
-产出电铅
5069
(粗铅+电铅)合计
45155
表7废气及重金属污染物排放总量
废气排放源
废气排放总量
(万Nm3/a)
粉尘排放量(t/a)
污染物排放量(t/a)
Cu
Pb
Zn
Cd
As
基夫赛特炉-烟化炉
-制酸/产出粗铅
481032
电解-铅锅熔铸
-产出电铅
50690
(粗铅+电铅)合计
451550
(6)竖炉二氧化硫WSA制酸(详细WSA工艺流程)
WSA工艺的特点是湿式工艺,即工艺气体不通过干燥,所有进气中的水蒸气及化学反映产生的水蒸气全数保留在气体中,SO3不像传统干法工艺那样被硫酸吸收,而是通过水合反映生成硫酸蒸气,然后在由空气冷却的管式冷凝器中冷凝成浓硫酸。
WSA工艺的能效超级高,因为SO2的氧化热、气态SO3与H2O的反映(形成硫酸蒸气)热、硫酸蒸气冷凝热及工艺气体接近100℃的冷却热都取得了回收,这些能量一部份以高压蒸汽的形式回收,另一部份以热空气(例如作为燃烧空气)的形式回收,只有产品酸的冷却热随冷却水流失于环境。
WSA工艺中气体无需干燥,因此生产中既不会有硫酸损失,也不会产生酸性废水。
(7)废水及废渣
基夫赛特炼铅进程中,烟化炉渣渣水淬进程顶用到必然量的水,在无暴雨的情况下全数回收循环利用,竖炉烟气动力波湿法除尘会产生必然量的污酸废水,全数进污酸处置系统,以后进入污水处置厂(废水大体情况以污水处置厂为主)。
烟化炉渣水淬以后的无害渣外卖,进污酸处置以后产生的污酸渣?
?
?
。
钠碱脱硫法,布袋除尘、电除尘、动力波除尘等污染物处置方式是统一的,在全数工艺分析完以后详细研究。
烧结鼓风炉炼铅
图5烧结鼓风炼铅
(1)原料及其处置情况
进入烧结炉之前的各原料比例如表7所示。
表7烧结鼓风炼铅原料大体情况
项目
铅精矿
硫精矿
金精矿
铅烟尘
焦粉
氧化锌浸出渣
含量比例(%)
60%
25%
10%
总铅(g/kg)
60%
65%
55%
总锌(g/kg)
7%
总镉(g/kg)
总铬(g/kg)
总砷(g/kg)
总汞(g/kg)
总镍(g/kg)
1%
总铜(g/kg)
5%
1%
5%
总铁(g/kg)
18%
8%
8%
总硫(g/kg)
由表7中可以看出,烧结鼓风炉炼铅的主要原材料为铅精矿、铅烟尘与氧化锌浸出渣,三者的含铅比例都在55%以上,在其他金属元素中,含量最多的为铁,其次含有部份的锌、铜、镍。
烧结前配料技术要求:
主要知足S、Pb和造渣组分的要求,精矿中的硫化物就是焙烧进程的燃料,配料时硫数量的肯定是直接与进程的热平衡和烧结块残硫联系在一路的,太高与太低都会致使进程热制度的破坏和残硫不符合要求。
烧结料适宜的硫量应当是:
脱硫率一般为60%~75%,欲得残硫%~%的烧结块,则料含S应为5%~7%。
若是S>7%时,则烧结块残硫必然升高而不合要求。
为了使鼓风炉熔炼取得高的生产率、金属回收率和低的燃料和熔剂消耗,希望尽可能地提高烧结块的含Pb量,但太高会致使熔炼困难,铅含量一般在45%左右,配渣成份:
SiO220~32,Fe22~30,CaO14~20,Zn8~15。
炉料粒度对鼓风炉冶炼铅的影响,炉料粒度过大,在炉内下降速度加速,影响着冶炼质量,粗铅成份太低,影响下一步的精炼。
按照配料的技术要求,对所有的原材料进行相应的处置,为下一步的粗炼、精炼提供对应的配料。
(2)烧结焙烧
烧结焙烧是硫化物在高温(800℃以上)条件下经氧化脱硫转化为氧化物,并烧结产出具有多孔和必然强度的烧结块的进程。
烧结进程应尽可能提高烟气中SO2浓度,以利于制酸,同时力求富集原料中易挥发的有价金属,以便综合利用。
烧结焙烧采用60m吸风烧结机、返烟烧结方式,控制的主要技术条件为炉料成份、点火温度、料层厚度、鼓风量、车速等。
通常,炉料成份要求是Pb--42%~48%,S--5%~%,点火温度--850~950℃,料层厚度--280~350mm、鼓风量--50000~60000m/h、车速--700~800mm/min。
烧结进程中会产生大量的烟气和烟尘,表8和表9为具体成份含量情况。
表8烧结烟尘化学成份含量比例
化学成分(%)
Pb
Zn
As
Cu
Fe
S
SiO2
CaO
50~70
1~3
~
~
~
7~10
~
~6
表9烧结炉烟气性能参数
烧结机面积(m2)
烟气量
(m3/h)
烟气成分(%)
烟尘量g/m3
烟气温度℃
SO2
CO2
O2
N2
H2O
SO3
70
36630~44640
~
~
~
~
~
~
200~250
烧结产物经单轴破碎及齿辊破碎后,采用双辊筛进行筛分,由链板运输机将烧结块和返粉别离输送到鼓风炉料仓及返粉破碎系统。
图6烧结矿处置进程
烧结炉料技术要求如表8所示:
表8烧结炉料技术要求
块度mm
固定碳%
灰分%
发热值MJ/kg
着火点℃
孔隙率%
抗压强度MPa
50~100
75~80
<16
25~29
600~800
40~50
>7
(3)鼓风炉还原熔炼
还原熔炼的目的是使铅烧结块中的含铅化合物还原成金属铅,并将金银等贵金属富集在铅中,使铁氧化物从高价变低价,再与其他脉石成份造渣而与铅分离。
鼓风炉中炭质燃料的燃烧,既冶金反映提供必要的热量,又在炉内形成还原气体,还原氧化铅:
C+O2====CO2
CO2+C====2CO
PbO+CO====Pb+CO2
烧结块中的2PbO·SiO2,在有较强碱性氧化物FeO、CaO存在时,可发生置换反映放出PbO,进一步还原为金属铅:
2PbO·SiO2+2FeO+2CO====2Pb+2FeO·SiO2+2CO2
2PbO·SiO2+2CaO+2CO====2Pb+2CaO·SiO2+2CO2
烧结熟料中的三氧化二铁发生以下还原和造渣反映:
3Fe2O3+CO====2Fe3O4+CO2
Fe3O4+CO====3FeO+CO2
2FeO+SiO2====2FeO·SiO2
烧结块中的其他氧化物,如Al2O3、CaO、MgO也都进入炉渣。
PbSO4有部份与CO反映生成PbS和CO2,部份受热分解为PbO和SO2。
含铜、硫高时,可生成梳相,镍、钻砷化物高时,还可形成黄渣。
铅是金和银的优良捕集剂,熔炼时烧结块中的金银大部份富集于粗铅中,少量散布在锍和黄渣内。
鼓风炉产粗铅分析
表9鼓风炉产粗铅成份比例
粗铅成分(%)
Pb
Sb
Sn
Cu
As
Bi
Ag
Au(g/t)
鼓风炉产粗铅,一般品位为95%~98%,其余为铜、砷、锑、铋、金和银等。
粗铅产出率与炉料含铅量和操作制度有关,一般为35%~55%。
粗铅放出时的温度为800~980℃。
鼓风炉烟气分析
铅鼓风炉的烟气成份及烟气量,主要取决于鼓风炉与炉内焦炭的燃烧情况。
为使焦炭燃烧取得较高的热利用率,同时又保障炉内有适当的还原气氛,通常按照炉内料面处烟气中CO2与CO的含量比例来控制。
当采用高料柱操作法时,其比值为2~3:
1,低料柱法时,以1~2:
1为宜。
烟气成份如表10所示:
表10鼓风炉烟气成份
通道面积(m2)
烟气成分
烟气中CO2/CO
烟气(m3/min)
CO2
CO
O2
500
鼓风炉烟尘分析
鼓风炉的烟尘率与操作条件有关,采用高料柱操作法时为~2%,低料柱操作法时为3~5%,烟尘中含有铅、锌外,还含有铟、碲、镉、硫等有价元素。
烟尘产出率与化学成份如表11所示:
表11鼓风炉烟尘产出率与化学成份
产出率
化学成分
Pb
Zn
Cd
Se
Te
Ti
Sb
Sn
In
S
As
鼓风炉炉渣分析
铅鼓风炉还原熔炼所产炉渣的特点是渣含ZnO较高,一般为5~25%。
通常SiO2、FeO、CaO和ZnO之和占渣总量的85~90%。
为了降低渣含铅,可以在必然范围内提高渣中CaO的含量。
当处置高锌炉料时,宜适当提高渣中FeO含量,以利于锌富集在炉渣中。
炉渣产出率及炉渣成份如表12所示:
表12炉渣产出率及炉渣成份
炉渣产出率(%)
炉渣化学成分(%)
Pb
Fe
SiO2
CaO
Zn
Cu
S
Al2O3
50~60
铅鼓风炉熔炼进程中重金属散布
熔炼进程中重金属的去向分为三种粗铅、炉渣、烟尘,烟尘一般通过各级的收尘装置回收回炉熔炼,炉渣按照转变的情况进行不同的处置处置,粗铅进行精炼。
具体含量比例如表13所示。
表13铅鼓风炉熔炼进程中重金属散布
元素
粗铅
炉渣
烟尘
合计
Pb
95
2
3
100
Cu
79
100
Zn
2
95
3
100
Bi
93
7
100
Cd
10
11
79
100
Sb
96
3
1
100
Sn
80
18
2
100
In
49
49
2
100
Ge
99
1
100
Se
71
16
13
100
Te
75
10
15
100
As
82
17
1
100
图7铅鼓风炉熔炼进程中重金属散布
(4)烧结鼓风炉粗铅精炼(与基夫赛特炼铅粗铅精炼进程大体相符)
(5)废气及相应重金属排放情况
首先分析烧结鼓风炉炼铅系统的粗铅与电铅产量,以后分析各生产工艺进程中污染物的产生情况,并研究彼此之间的内在联系。
表14烧结鼓风炼铅系统主要生产工艺与规模
生产系统
主要工艺设备
产能
2010年产量
铅系统
烧结机—鼓风炉熔炼—电解精炼工艺,主要设备:
烧结机、鼓风炉、烟化炉、反射炉,
WSA制酸,电解车间、熔铸车间
粗铅万t/a,
硫酸13万t/a,
电铅10万t/a
粗铅万t/a
析出铅.8万t/a
电铅及铅合金:
万t/a
硫酸万t/a
烧结鼓风炉炼铅系统主要污染源为铅烧结、铅鼓风炉、熔铅锅、铅烟化炉、铅反射炉、WSA制酸系统等,主要污染物为SO2、粉尘、Pb、Cd等。
烧结鼓风炼铅烟气重金属排放总量与排放强度如表15与表16所示。
表15烧结鼓风炼铅系统废气重金属污染物排放总量
废气排放点
废气排放总量
(万Nm3/a)
粉尘
污染物排放量(t/a)
浓度mg/Nm3
排放量t/a
Cu
Pb
Zn
Cd
As
铅鼓风炉脱硫设施出口
41976
铅烟化炉布袋出口
22428
铅鼓风炉前床布袋出口
20369
铅烧结大布袋1#出口
50147
铅烧结大布袋2#出口
53734
铅烧结大布袋3#出口
47984
熔铅布袋出口
39998
铅浮渣反射炉布袋出口
4848
铅备料干燥窑出口
6536
铅416m2布袋1#出口
15850
鄂式破碎除尘出口
2185
熔剂对锟除尘出口
2962
破碎4000m2
37949
粗铅部份合计
346966
小铅锅布袋出口
6720
铅钙合金收尘出口
55473
电铅部份合计
62193
铅系统总合计
(粗铅+电铅)
389141
表16烧结鼓风炼铅系统废气重金属污染物排放强度
冶炼工艺流程
废气排放量(Nm3/t)
粉尘排放强度(kg/t产品)
重金属排放强度(kg/t产品)
Cu
Pb
Zn
Cd
As
烧结-鼓风炉-烟化炉-WSA制酸-产出粗铅
51786
电解-铅锅熔铸-产出电铅
6038
铅系统总合计
(粗铅+电铅)
57824
(对两表进行细致分析)
对以上数据进行总结,按照工业源污染普查数据对烧结鼓风炼铅系统粗铅生产与电铅生产进程中的废水、废气、废渣进行总结,结果如表17与表18所示。
表17烧结鼓风粗铅生产“三废”产生与排放情况
产品
名称
原材料
工艺名称
产量/万t
污染物指标
单位
产污系数
产污量
排污系数
污染物排放量
粗铅
铅精矿
烧结机-鼓风炉工艺
6
工业废水量
吨/吨-产品
×105t
×105t
化学需氧量