《冷冲模毕业设计》doc版.docx
《《冷冲模毕业设计》doc版.docx》由会员分享,可在线阅读,更多相关《《冷冲模毕业设计》doc版.docx(14页珍藏版)》请在冰豆网上搜索。
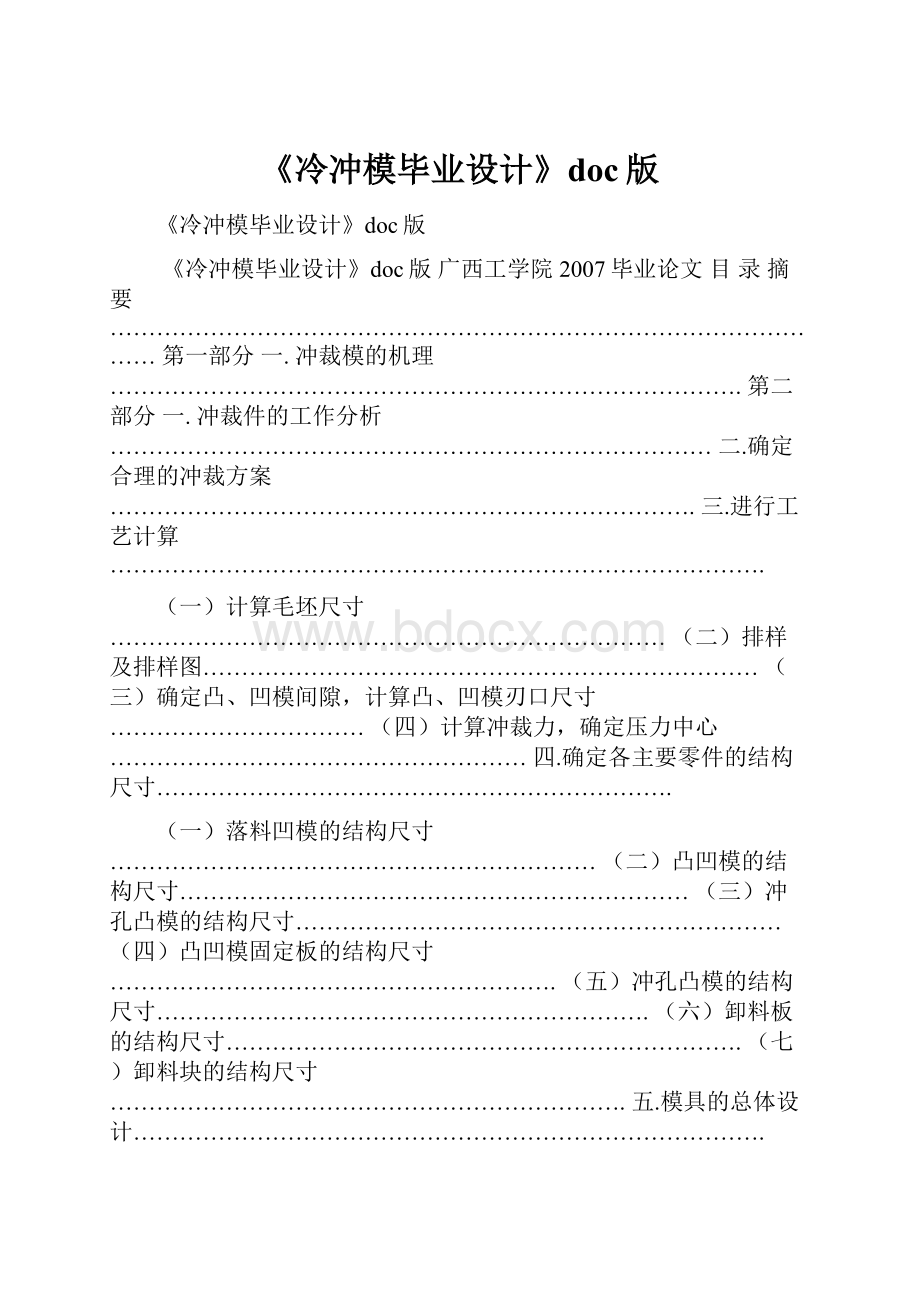
《冷冲模毕业设计》doc版
《冷冲模毕业设计》doc版
《冷冲模毕业设计》doc版广西工学院2007毕业论文目录摘要……………………………………………………………………………………第一部分一.冲裁模的机理……………………………………………………………………….第二部分一.冲裁件的工作分析……………………………………………………………………二.确定合理的冲裁方案………………………………………………………………….三.进行工艺计算………………………………………………………………………….
(一)计算毛坯尺寸………………………………………………………………
(二)排样及排样图………………………………………………………………(三)确定凸、凹模间隙,计算凸、凹模刃口尺寸……………………………(四)计算冲裁力,确定压力中心………………………………………………四.确定各主要零件的结构尺寸………………………………………………………….
(一)落料凹模的结构尺寸………………………………………………………
(二)凸凹模的结构尺寸…………………………………………………………(三)冲孔凸模的结构尺寸………………………………………………………(四)凸凹模固定板的结构尺寸………………………………………………….(五)冲孔凸模的结构尺寸……………………………………………………….(六)卸料板的结构尺寸………………………………………………………….(七)卸料块的结构尺寸………………………………………………………….五.模具的总体设计……………………………………………………………………….
(一)工作零件的设计……………………………………………………………
(二)定位零件的设计……………………………………………………………(三)退料零件的设计……………………………………………………………(四)模架零件的设计……………………………………………………………六.模具图样设计………………………………………………………………………….
(一)绘制模具总装配图……………………………………………………………
(二)编写工艺过程卡………………………………………………………………七.选择冲压设备…………………………………………………………………………八.模具装备与调试………………………………………………………………………九.结论…………………………………………………………………………………….十.致谢词………………………………………………………………………………….十一.参考文献…………………………………………………………………………….气筒垫片冲裁模作者:
周兴盛「摘要」冲裁是利用模具使板料产生分离的冲压工序,它包括落料、冲孔、切口、切边、部切、修整、精密冲裁等。
冲裁所得到的工件可以直接为零件使用或用于装备部件或可以作为弯曲、拉深、成形、冷挤压等其他工序毛坯。
冲裁工序是利用凸模与凹模组成上、下刃口,将材料置与凹模上,凸模下降使材料变形,直至全部分离,因凸模与凹模之间存在间隙Z,故凸模与凹模作用于材料的力量不均匀分布,主要集中在凸、凹模刃口。
通过了解冲裁机理以及工作原理,对气筒垫片进行工艺分析,确定合理的冲裁方案,设计出结构合理、经济、实用的冲裁模。
「关键词」工作原理结构设计计算绘图第一部分冲裁是利用模具使板料产生分离的冲压工序,它包括落料、冲孔、切口、切边、部切、修整、精密冲裁等。
冲裁所得到的工件可以直接为零件使用或用于装备部件或可以作为弯曲、拉深、成形、冷挤压等其他工序毛坯。
精密冲裁的机理根据金属塑性变形原理分析可知,塑性金属材料在变形过程中,压应力及应变只能使金属材料产生形态的改变,而不会导致金属材料的断裂破坏,引起变形金属材料断裂破坏的主要因素是拉应力和拉应变,精密冲裁的机理,就是设法使冲裁变形区的金属材料在冲裁模刃口处进行存塑性变形,这样就杜绝了微裂纹的产生及断面撕裂破坏的可能性,从而获得高质量的纯塑性剪分离的冲裁件断面。
第二部分技术要求:
工件名称:
气筒垫片1.工件外观精美无明显毛刺。
材料:
08钢2.工件精度按IT8制作。
数量:
10万件一.工艺分析气筒垫片的材料为08钢,08钢是一种中碳钢,室温下塑性较好。
08钢的抗拉强度:
δb33~45Mpa抗剪强度:
Tb26~36Mpa屈服点:
δs20Mpa以上数据根据《工具钳工工艺学》96新版中国劳动出版社责任编辑万象教材中第233页表15.10黑色金属的力学性能材料名称牌号材料的状态机械性能抗剪强度Tb抗拉强度σb屈服点σ延伸率δ(%)10pa电工用工业纯铁C<0.025%DT1,DT2,DT3已退火的182326电工硅钢D11,D12,D21,D31,D41~48,D310~340,D370已退火的192326普通碳素钢Q21527~3434~422226~31Q235未经退火的31~3844~472421~25Q25534~4249~522619~23二.确定合理的冲裁方案在冲裁工艺分析的基础上,根据冲裁件的特点,确定冲裁工艺方案。
方案1.采用级进冲裁模。
是压力机在一次行程中,依次在模具多个不同的位置上同时完成多道冲压工序的冲裁模,模具材料比复合模相对较多,具要求送料相对位置精度较高,模具结构复杂。
方案2.采用倒装复合模。
是冲床一次行程中,在模具同一位置上能完成几个不同的冲裁工序。
采用钢性推件的倒装复合模,材料不是处在被压紧的状态下冲裁,因而平面精度不高,这种结构适用于冲裁较硬的或厚度大于0.3mm的板料,如果上模推料块采用弹性推件装置,就可用于冲制材料较软的或板料厚度小于0.3mm且平面度要求较高的冲裁件。
综合以上得:
级进模比倒装复合模的制件精度底,此外,级进模的结构复杂、制造困难,而且不易定位;而倒装复合模模具结构比级进模简单,制造精度易保证,能准确定位。
因此,选用倒装复合模。
三.进行工艺计算
(一)计算毛坯尺寸1.毛坯尺寸:
根据:
《冲压工艺与模具结构》中国劳动社会保障出版出版人:
张梦欣课本教材里的表2—5搭边值数料厚(mm)手工送料自动送料圆形非圆形往复送料abababab~1大于1~2大于2~3大于3~4大于4~5大于5~6大于6~88以上1.522.5345671.51.522.5345622.533.556781.522.53456733.545678922.53.545678345678234567查得出,确定毛坯尺寸如图所示。
(二)排样及排样图①排样是指制件在板料上的布置方法,直接影响材料的利用率、冲模结构、制件质量和生产率等,条料冲裁时,所产生的废料分为两种情况:
1.工艺废料2.结构废料排样方法重要有三种:
A有搭边排样B无搭边排样C少搭边排样气筒垫片形状比较复杂,精度要求较高,适合于采用单边有搭边排样。
有搭边排样是在板料上冲裁轮廓;四周都有搭边,搭边为废料,其特点是材料利用率低,制件的质量和冲模寿命较高。
(三)确定凸、凹模间隙,计算凸、凹模刃口尺寸。
1.凸、凹模之间的间隙:
凸、凹模之间的间隙对冲裁质量、冲裁力模具寿命影响很大,是冲裁工艺与模具设计中的一个积极重要的问题。
凸、凹模间隙的计算:
公式:
Z=mtZ——间隙M——系数,与材料性能及厚度有关,m=8—12%T——材料厚度,t=1.5mm为了保证冲模间隙小于最大合理间隙(Emax),凸模和凹模制造公差必须保证。
│δ凸│+│δ凹│≤Zmax—Zmin经校核,证明所选的δ凸和δ凹均合适。
因是冲裁模,所以间隙取Zmin。
3.凸、凹模刃口尺寸计算:
确定凸、凹模工作部分尺寸及制造精度时必须考虑到冲裁变形规律,冲裁件质量等级,模具磨损和制造的特点:
(1)落料时,先确定凹模工作尺寸,其大小取接近或等于工作的最小极限尺寸,为保证凸模磨损到一定范围内仍能冲出合格工件,凸模公称尺寸应比凹模尺寸小一个最小合理间隙。
(2)冲孔时,先确定凸模工作部分尺寸,其大小应取接近或等于孔的最大极限尺寸,保证凸模磨损到一定范围内仍能冲出合格工件,凹模公称尺寸大一个最小合理间隙。
由于加工模具的方法不同,凸模和凹模刃口部分在尺寸的计算方法和制造公差的标柱上不同,刃口尺寸的计算方法基本上可分为两类:
(1)凸模与凹模分开加工
(2)凸模与凹模配合加工凸、凹模分开加工,是指凸模与凹模分别按图纸加工出合格的尺寸,要分别标柱凸模和凹模的刃口尺寸与制造公差,而且要求较高的制造精度,适用于圆形或简单的(方形或矩形)的工件。
凸、凹模配合加工是指加工凸模(或凹模),然后根据制造好的凸模(或凹模)的实际尺寸,配做凹模(或凸模),在凹模(或凹模)修出最小合理间隙值,其方法是把先加工出的凸模(或凹模)作为基准件,它的工作部分尺寸作为基准尺寸,而与它配做的凹模(或凸模)只需在图纸上标柱相应部分的凸模(或凹模)配做,每边保证最小合理间隙,这种加工方法在工厂中被广泛应用,适合形状复杂的冲裁件.因此,采用分开加工方法.其凸模和凹模刃口尺寸计算如下:
根据《工具钳工工艺学》96新版中国劳动出版社责任编辑万象教材中的第231页公式:
(1)落料设制件尺寸为D,其计算公式如下:
D凹=(D-X△)D凸=(D凹-Zmin)=(D-X△-Zmin)
(2)冲孔设制件孔的尺寸为d,其计算公式如下:
d凸=(d+X△)d凹=(d凸+Zmin)=(d+X△+Zmin)式中:
D凸、D凹——分别为落料凸、凹模基本尺寸,mmD、d——分别为落料件和冲孔件的基本尺寸,mmd凸、d凹——分别为冲孔凸、凹模基本尺寸,mm△——零件的制造公差,mmZmin——最小合理间隙(双边),mmδ凸、δ凹——分别为凸、凹模的制造公差,如图15.8所示X——磨损系数,在0.5—1之间,与制造精度有关,如表15.9所示外形Φ30mm,2个R10mm属落料,Φ18mm和2个Φ10mm属于冲孔,工作无特殊要求,根据《工具钳工工艺学》96新版中国劳动出版社责任编辑万象教材中第230页表15.7冲裁模合理间隙值Z材料厚度0.8、10、35、09Mn、Q23516Mn40、5065MnZminmaxZminmaxZminmaxZminmax小于0.5无间隙0.50.60.70.80.91.01.21.51.752.02.12.52.753.03.54.04.55.56.08.00.0400.0480.0640.0720.0900.1000.1260.1320.2200.2460.2600.3600.4000.4600.5400.6400.7200.9101.0800.0600.0720.0920.1040.1260.1400.1800.2400.3200.3600.3800.5000.5600.6400.7400.8801.0001.2801.4400.0400.0480.0640.0720.0900.1000.1320.1700.2200.2600.2800.3800.4200.4800.5800.6800.6800.7800.8400.9401.2000.0600.0720.0920.1040.1260.1400.1800.2400.3200.0380.4000.5400.6000.6600.7800.9200.9601.1001.2001.3001.6800.0400.0480.0640.0720.0900.1000.1320.1700.2200.2600.2800.3800.4200.4800.5800.6800.7800.9801.1400.0600.0720.0920.1040.1260.1400.1800.2300.3200.3800.4000.5400.6000.6600.7800.9201.0401.3201.5000.0400.0480.0640.0900.0900.0600.0720.0920.0920.1260.126由表查得:
Zmax=0.24mmZmin=0.132mm
(1)落料:
Φ30mm制造公差由图示可知0.05mm根据《工具钳工工艺学》96新版中国劳动出版社责任编辑万象教材中表15.7冲裁模合理间隙值Z材料厚度0.8、10、35、09Mn、Q23516Mn40、5065MnZminmaxZminmaxZminmaxZminmax小于0.5无间隙0.50.60.70.80.91.01.21.51.752.02.12.52.753.03.54.04.55.56.08.00.0400.0480.0640.0720.0900.1000.1260.1320.2200.2460.2600.3600.4000.4600.5400.6400.7200.9101.0800.0600.0720.0920.1040.1260.1400.1800.2400.3200.3600.3800.5000.5600.6400.7400.8801.0001.2801.4400.0400.0480.0640.0720.0900.1000.1320.1700.2200.2600.2800.3800.4200.4800.5800.6800.6800.7800.8400.9401.2000.0600.0720.0920.1040.1260.1400.1800.2400.3200.0380.4000.5400.6000.6600.7800.9200.9601.1001.2001.3001.6800.0400.0480.0640.0720.0900.1000.1320.1700.2200.2600.2800.3800.4200.4800.5800.6800.7800.9801.1400.0600.0720.0920.1040.1260.1400.1800.2300.3200.3800.4000.5400.6000.6600.7800.9201.0401.3201.5000.0400.0480.0640.0900.0900.0600.0720.0920.0920.1260.126查得:
Zmx=0.18mmZmin=0.126mm表15.8规则形状(圆形、方形)冲裁凸、凹模的制造公差基本尺寸凸模凹模≤18>18~30>30~800.0200.0200.0250.030>80~1200.0250.035120~180>180~2600.0300.0400.045>260~3600.0350.050>360~5000.0400.060>5000.0500.070查得:
凸、凹模制造公差δ凸=0.02mmδ凹=0.025mm表15.9磨损系数X材料厚度t(mm)非圆形圆形10.750.50.750.5制造公差△(mm)≤1>1~2>4<0.16<0.20<0.24<0.300.16~0.350.20~0.410.24~0.490.30~0.59≥0.36≥0.42≥0.50≥0.60<0.16<0.20<0.24<0.30≥0.16≥0.20≥0.24≥0.30查得:
X=1则Zmax-Zmin=0.18-0.126=0.054mm因为0.02+0.025<0.018-0.126,故能满足δ凸+δ凹≤Zmax-Zmin的条件将已知和查表得到的数值代入公式,即得D凹=(D-X△)=(30-1X0.05)=29.95mmD凸=(D凹-Zmin)=(D-X△-Zmin)=(30-1X0.05-0.126)=29.824mm
(2)落料:
R10mm查表15.8得凸、凹制造公差δ凸=0.02mmδ凹=0.02mm查表15.9得磨损系数X=1因为0.02+0.025<0.18-0.126,故能满足│δ凸│+│δ凹│≤Zmax—Zmin的条件将已知和查表得到的数值代入公式,得:
D凹=(D-X△)=(10-1X0.05)=9.95mmD凸=(D凹-Zmin)=(D-X△-Zmin)=(10-1X0.05-0.126)=9.824mm(3)冲孔制造公差由图示可知0.05mm查表15.7得合理间隙值Zmax=0.18mmZmin=0.126mm查表15.8得凸、凹制造公差δ凸=0.02mmδ凹=0.02mm查表15.9得磨损系数X=0.75=(18+0.75X0.05)=18.038d凹=(d凸+Zmin)=(d+X△+Zmin)=(18+0.75X0.5+0.126)=18.164mm(4)冲孔Φ10查表15.7得合理间隙值Zmax=0.18mmZmin=0.126mm查表15.8得凸、凹制造公差δ凸=0.02mmδ凹=0.02mm查表15.9得磨损系数X=0.75d凸=(d+X△)=(10+0.75X0.05)=10.038mmd凹=(d凸+Zmin)=(d+X△+Zmin)=(10+0.75X0.05+0.126)=10.164mm(四)计算冲裁力及总压力,确定压力中心。
1.计算冲裁力P=LxTxδb式中P——冲裁力(N)L——冲裁线长度(mm)T——制件厚度(mm)δb——材料抗拉强度(pa),可从有关手则中查得,08钢δb=330-450Mpa根据公式得:
δb=390X107且L=0.2636X2+0.1936X4+0.0758X2+0.0314X10X2+0.0314X18=2.6464(m)P=LxTxδb=2.6464X0.015X390X107=1.548144X108N1.总压力P总=p+Q顶+Q卸式中P总——压力机所需总压力P——冲裁力Q顶——顶件力Q卸——卸料力而Q顶=K顶p=0.06X1.548144X108=9.288864X106Q卸=K卸p=0.06X1.548144X108=9.288864X106式中Q顶、Q卸——分别为顶件力、卸料力(N)K顶、K卸——分别为顶件力系数、卸料力系数,一般取0.05-0.08P——冲裁力因此:
P总=p+Q顶+Q卸=1.548144X108+9.288864X106X2=1.73392128X1082.确定压力中心3.冲压力合力的作用点称为压力中心。
在设计冲裁模时,应尽量使模具压力中心与压力机滑块中心相重合,否则会产生偏心裁荷,使模具倾斜,间隙不均匀,严重时会啃刃口,加速压力机和模具等导向部分及刃口磨损。
在模具设计中,使柄的轴线通过压力中心,在安装模具时,便能实现压力中心与滑块中心重合。
由于此制件为对称的制件,所以压力中心为几何中心。
四.确定各主要零件的结构尺寸五.模具的总体设计
(一)工作零件的设计
(1)凸模设计凸模材料:
凸模的结构形式,根据冲孔尺寸的大小分三种:
1.标准圆形凸模2.冲大孔凸模3.带护套的小孔凸模凸模冲件形状已决定了横向尺寸和形状,所以在一般情况下,凸模的强度是足够的,但是,对于特制细长的凸模和板料厚度大的情况下,才需进行压应力和弯曲应力的校核,检查其危险面尺寸和自由长度是否满足强度要求。
压应力校核公式:
圆形凸模Dmin≥4T\「δ压」非圆形凸模Amin≥F\「δ压」弯曲应力的校核圆形凸模非圆形凸模无导向装置Lmax≥95d2/Lmax≤425带导向装置Lmax≥270d2/Lmax≤1200冲孔凸模直径Φ18和Φ10的圆形凸模参照GB2863.2—81选取凸模,凸模基本尺寸分别为Φ18和Φ10。
冲孔凸模的固定方式:
采用凸模固定板固定,凸模与固定板是紧配合(H7/m6),上端带台阶,预防脱落。
(3)凹模设计:
凹模结构:
分为整体式和镶拼式两种。
镶拼结构常用于大型冲裁模,冲件形状不易制造及有易损部分的级进模。
凹模刃口形式:
有两大类,分别是直壁式和锥形式,锥形刃口凹模,冲裁件或废料容易通过,修磨量较小,刃口强度低,修磨后刃口增大,适合于形状简单、精度要求又高、材料厚度较薄工件的冲裁,而直壁式刃口凹模,刃口强度较高修磨后刃口尺寸不变,但孔口容易积有工件和废料,推件力大且磨损大,适合于形状复杂且加工精度要求较高的冲裁。
凹模的固定形式:
本模具是小型模具,而且气筒垫片形状较复杂且加工精度要求较高,因此,凹模采用直壁式刃口、整体式结构。
采用销钉定位、螺钉紧固方法。
(4)凸凹模设计:
凸凹模材料:
凸凹模是复合模的主要特点,凸凹模内外边缘均为刃口,内外壁之间的厚度决定了冲件的尺寸,不象凹模那样可以将外边缘尺寸扩大,所以从强度考虑,壁厚受最小限制。
凸凹模的最小壁厚受冲裁结构影响,凸凹模装在上模时,内孔不积存废料,胀力可以小于等于最小壁厚;凸凹模装在下模时,内孔有积存废料,胀力要大于最小壁厚。
目前,凸凹模的最小壁厚值一般按经验数据决定:
不只集废料的凸凹模的最小壁厚:
1)对黑色金属硬材料约为工件料厚的1.5倍,但不小于0.7mm2)对有色金属和软材料的工件约等于工件料厚,但不小于0.5mm
(二)定位零件的设计1.导尺导尺是保证材料在冲裁模中具有准确位置的零件。
导尺的宽度由板料的宽度来确定。
2.定位销按实际要求来加工。
(三)退料零件1.卸料零件是将材料从凸模或凸凹模上的料卸下来,包括钢性卸料装置和弹性卸料装置。
钢性卸料常用于较硬、较厚且精度要求不高的工件冲裁后卸料,而弹性卸料即起到卸料又起到压料的双作用。
冲裁件较为平整,适于精密冲裁。
所以用弹性卸料装置。
1.顶件装置顶件装置是将卡在凹模中的料顶出来。
分弹性顶件装置和钢性顶件装置两种。
钢性顶件装置,其特点是顶件力大,工作可靠,但要求顶杆长短一致,分布均匀。
所以难于加工,不易保证。
而弹性顶件装置,没有那么严格的要求它的长短一致性,而还起到压料的作用,制件平整度较高。
因此,采用弹性顶件装置(四)模架零件的设计1.导柱、导套模具中导向副的作用是保证上模相对于下模有一定位置关系,分为滑动导向副和滚动导向副两类。
滚动导向副磨损系数小,提高模具导向副的使用寿命,但是滚动导向副的价格高,难于制造,而滑动导向副价格