汽车左右弯管注塑模设计毕业论文.docx
《汽车左右弯管注塑模设计毕业论文.docx》由会员分享,可在线阅读,更多相关《汽车左右弯管注塑模设计毕业论文.docx(30页珍藏版)》请在冰豆网上搜索。
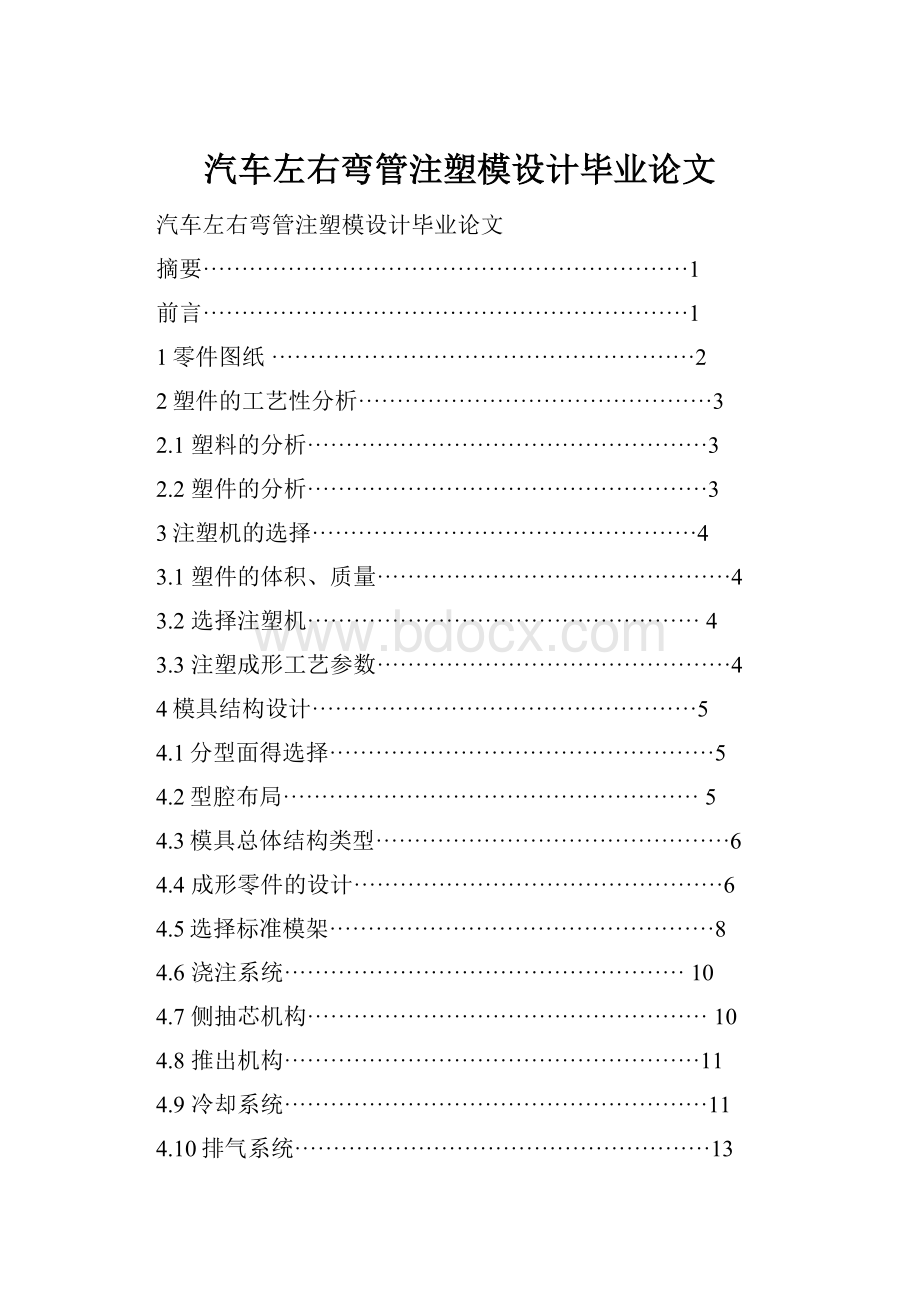
汽车左右弯管注塑模设计毕业论文
汽车左右弯管注塑模设计毕业论文
摘要·······························································1
前言·······························································1
1零件图纸·······················································2
2塑件的工艺性分析··············································3
2.1塑料的分析····················································3
2.2塑件的分析····················································3
3注塑机的选择··················································4
3.1塑件的体积、质量··············································4
3.2选择注塑机···················································4
3.3注塑成形工艺参数··············································4
4模具结构设计··················································5
4.1分型面得选择··················································5
4.2型腔布局······················································5
4.3模具总体结构类型··············································6
4.4成形零件的设计················································6
4.5选择标准模架··················································8
4.6浇注系统····················································10
4.7侧抽芯机构····················································10
4.8推出机构······················································11
4.9冷却系统·······················································11
4.10排气系统······················································13
5注塑机的校核···················································13
毕业小结··························································14
答谢词····························································14
参考文献··························································14
1、零件图纸
图1-1
图1-2
零件描述:
汽车左/右弯管二维图如图1-1所示,三维图如图1-2所示。
1.1塑件材料为ABS,收缩率为0.5%。
1.2大批量生产,塑件表面不得有飞边毛刺、无银丝、无波浪、熔接痕最小、无缩痕、无气泡、无划伤和白斑等外观缺陷。
1.3未注圆角为R2
1.4表面粗糙度达到Ra1.6
1.5未有尺寸按MT6级精度计算
2、.塑件的工艺性
2.1塑料
品种:
ABS
颜色:
白色
基本特性:
1、ABS是丙烯腈、丁二烯和苯乙烯的三元共聚物,A代表丙烯腈,B代表丁二烯,S代表苯乙烯。
ABS树脂是目前产量最大、应用最广泛的聚合物,它将PS、SAN、BS的各种性能有机地统一起来,兼具韧、硬、刚相均衡的优良力学性能。
ABS工程塑料一般是不透明的,外观呈浅象牙色、无毒、无味,兼有韧、硬、刚的特性,燃烧缓慢,火焰呈黄色,有黑烟,燃烧后塑料软化、烧焦,发出特殊的肉桂气味,但无熔融滴落现象。
2、ABS工程塑料具有优良的综合性能,有极好的冲击强度、尺寸稳定性好、电性能、耐磨性、抗化学药品性、染色性,成型加工和机械加工较好。
3、ABS树脂耐水、无机盐、碱和酸类,不溶于大部分醇类和烃类溶剂,而容易溶于醛、酮、酯和某些氯代烃中。
4、ABS工程塑料的缺点:
热变形温度较低,可燃,耐候性较差。
成形特点:
1、无定形料,流动性中等,吸湿大,必须充分干燥,表面要求光泽的塑件须长时间预热干燥80-90度、3小时。
2、宜取高料温、高模温,但料温过高易分解(分解温度为>270度)。
对精度较高的塑件,模温宜取50 ~60度,对高光泽、耐热塑件,模温宜60~80度
3、如需解决夹水纹,需提高材料的流动性,采取高料温、高模温,或者改变入水位等方法。
4、如成形耐热级或阻燃级材料,生产3~7天后模具表面会残存塑料分解物,导致模具表面发亮,需对模具及时进行清理,同时模具表面需增加排气位置。
2.2塑件
1、尺寸精度:
该塑件未标注公差尺寸,故公差等级取MT6级精度计算.
2、表面质量要求:
该塑件为汽车座椅调节器支架,要求表面光滑、完整、厚度均一、无飞边毛刺、无银丝、无波浪、熔接痕数量最少,熔接痕最小、无缩痕、无气泡、无划伤和白斑等外观缺陷,表面粗糙度可取Ra1.6。
3、结构工艺性:
此塑件为壁壳类零件,整体尺寸为135×138,厚度基本均匀为5.07mm,最厚处为10.13mm,属于小型塑件。
塑件一侧有两个较深的孔,无法直接脱模,必须加侧抽机构。
塑件周边有较小的圆角,可以提高模具的强度,改善塑料的流动情况,便于塑件顺利脱模。
4、通过以上分析,此塑件可以采用注塑成形生产,又因为需要模具正常生产,塑件产量要达到100万件,属于大批量生产,采用注塑成形具有较高的经济效益。
3..注射机的选择
3.1.计算塑件的体积、质量
经UG软件测得塑件的体积约为75.22㎝3,塑件密度为0.91g/cm3,则质量M=75.22×0.91=68.45g。
3.2.选择注射机
根据公式Vmax≥(nVs+Vj)/k
Vmax指注射机的最大注射量n指型腔数量
Vs指塑件体积Vj浇注系统凝料体积
K指注射机最大注射量利用系数,一般取K=0.8
已知n=2,Vs=75.22㎝3,Vj=10㎝3,则Vmax≥(2×75.22+10)/0.8=200.55㎝3
查表可选择的注射机型号为XS-ZY-500型卧式注射机,其有关参为:
额定注射量500cm3
注射压力145MPa
锁模力3500KN
最大成形面积1000cm2
模具厚度300~450mm
最大开合模行程500mm
喷嘴圆弧半径18mm
喷嘴孔直径6mm
拉料间距540mm×440mm
顶出形式中心液压顶出,两侧顶杆机械顶出
3.3.制定注射成形工艺参数
⑴温度(℃)
预热温度:
80~85
料筒温度:
前段255~265,
中段260~280,
后段240~250。
喷嘴温度:
250~260
模具温度:
50~80
⑵压力(MPa)
注射压力:
70~90
保压压力:
50~70
⑶时间(S)
成形时间:
预热时间:
2~3,
注射时间:
3~5,
包压时间:
15~30,
冷却时间:
15~30,
成形周期:
40~70。
4.模具结构设计
4.1.分型面的选择
分型面是模具动模和定模的结合处,分型面的选择应以模具结构简单、分型容易,且不破坏已成形的塑件为原则,首先确定模具的开模方向为塑件的轴线方向,根据分型面应选择在塑件外形的最大轮廓处原则,则此塑件的分型面选在塑件的上接面处。
分型面如图4-1所示
图4-1
4.2.型腔布局
方案一:
单型腔模具虽然可使模具结构简单,塑件的精度高,工艺参数易于控制,模具制造成本低、周期短;但塑件成形的生产效率低,塑件的成本高。
适于塑件较大,精度要求较高或者小批量及试生产。
方案二:
多型腔模具虽然使模具结构复杂,塑件精度低,工艺参数难以控制,模具制造成本高、周期长;但塑料成形的生产效率高,塑件成本低。
适于大批量生产或者长期生产的小型塑件。
由于需要100万件的大批量生产,即便塑件精度要求较高,但是为提高效率,综合考虑采用一模两腔结构的型腔布局。
型腔布局如图4-2所示
图4-2
4.3.确定模具总体结构类型
方案一:
普通两板模结构,两板模是注塑模中最简单的一种结构形式,这种模具只有一个分型面。
方案二:
三板模结构,三板模也是注塑模中较为常见的一种结构,但是比较繁琐。
综上所述:
塑件的形状较简单,且比较小,属于小型塑件,而且零件需要加侧抽芯。
表面要求又高,所以综合考虑采用两板模模具。
由于对塑件表面的要求较高,要求表面光滑、完整、厚度均一、无飞边毛刺、无银丝、无波浪、熔接痕数量最少,熔接痕最小、无缩痕、无气泡、无划伤和白斑等外观缺陷,所以使用侧浇口,可以缩短成型周期减少注塑时间和冷却时间,提高效率,还可以减少流道的能量损失,提高成型质量。
4.4.成形零件设计
1、结构设计
方案一:
如果采用组合式的型芯型腔,可以减少加工工艺,减少热处理,拼合处有间隙,利于排器,便于模具的维修,节省贵重的模具刚。
方案二:
如果采用整体式的型芯型腔,这种结构加工效率高,拆装方便,可以保证各个型腔型芯的形状尺寸一致。
但是型腔加工困难,热处理不方便。
综上所述:
为便于拆装,型腔采用整体嵌入式的型芯型腔
2、工作尺寸计算(未注公差按MT6计算)
对于标注公差的型芯、型腔尺寸按相应公式进行尺寸计算,其余则按简化公式计算。
查表可知ABS的平均收缩率Scp=0.5%
型芯径向尺寸400+0.46245.6+0.54
LM=(LS+LSScp+3Δ/4)-δz
=(400+400×0.5%+0.46×3/4)-(0.46/4)
=402.345-0.115
LM=(LS+LSScp+3Δ/4)-δz
=(245.6+245.6×0.5%+0.54×3/4)-(0.54/4)
=247.233-0.135
型芯高度尺寸131+0.3290+0.46
HM=(HS+HSScp+2Δ/3)-δz
=(131+131×0.5%+2/3×0.32)-(0.32/4)
=132.021-0.08
HM=(HS+HSScp+2Δ/3)-δz
=(90+90×0.5%+2/3×0.46)-(0.0.46/4)
=90.816-0.115
型腔径向尺寸317-0.80400-0.54
LM=(LS+LSScp-3Δ/4)+δz
=(317+317×0.5%-3/4×0.80)+(0.80/4)
=317.985+0.2
LM=(LS+LSScp-3Δ/4)+δz
=(400+400×0.5%-3/4×0.54)+(0.54/4)
=401.595+0.135
型腔深度尺寸131-0.4641-0.32
HM=(HS+HSScp−2Δ/3)+δz
=131+131×0.5%-2/3×0.46)+(0.46/4)
=131.349+0.115
HM=(HS+HSScp−2Δ/3)+δz
=(41+41×0.5%-2/3×0.32)+(0.32/4)
=40.992+0.08
3、型腔侧壁和底板厚度计算
此模具采用组合式矩形型腔,查表,已知圆形型腔内壁短边为28.83mm,则型腔壁厚S1=9㎜,模套壁厚S2=22㎜。
已知t≥(a`p/[σ])0.5b,则L/b=28.83/28.83=1.0则a`=0.3078,又已知p=40MPa[σ]=300Mpa
带入公式t≥(a`p/[σ])0.5b
=(0.3078×40/300)0.5×28.83=5.8
型腔深度尺寸10.13-0.465.07-0.32
HM=(HS+HSScp−2Δ/3)+δz
=(10.13+10.13×0.5%-2/3×0.46)+(0.46/4)
=8.260.115
HM=(HS+HSScp−2Δ/3)+δz
=(5.07+5.07×0.5%-2/3×0.32)+(0.32/4)
=3.18+0.08
型芯圆角R2
LM=(LS+LSScp)-δz
=(2+2×0.5%)-0.01
=2.01-0.01
型腔圆角R2
LM=(LS+LSScp)+δz
=(2+2×0.5%)+0.01
=2.01+0.01
4.5.选择标准模架
1、确定模架组合形式
采用推杆推出机构,定模和动模均由两块模板组成。
2、斜导柱侧抽芯机构设计与计算
抽芯距与抽芯力的计算:
抽芯距S=S1+(2-3)=(R2-r2)0.5+(2-3)=(292-162)0.5+2=26.19
抽芯力的计算F=chp(ucosa-sina)
C—侧抽芯成形部分的截面平均周长m
h—侧抽芯成形部分高度m
p—塑件对侧型芯的收缩应力(包紧力),其值与塑件的几何形状及塑料的品种、成形工艺有关,一般情况下模内冷却的塑件,p=(0.8~1.2)×107模外冷却的塑件,p=(2.4~3.9)×107
a—侧抽芯的脱模斜度或倾斜角
u—塑料在热状态时对刚的摩擦系数,一般取0.15~0.3
则F=chp(ucosa-sina)
=9.1688×10-3×1.46×10-1×0.8×107×(0.3cos13—sin13)
=1007.23N
斜导柱的长度计算L=s/sina=26.19/sin13=119.05
3、计算型芯模板周界
长度L=78.21+423.58+78.21=580
宽度N=80.44+268.56+81.00=430
型芯模板周界如图4-3所示
图4-3
4、选取标准的型芯模板周界尺寸
首先确定模架宽度,N=430最接近于标准尺寸450,则选500×L;然后从L系列标准尺寸中选择接近于L=580的600。
最终确定的模架规格为1400×500。
5、确定模板厚度
A板定模板,本套模具没有定模板,型腔能直接充当定模板,则A板厚度等于型腔厚度,型腔厚度=40,选取标准中A板厚度HA=40mm。
B板动模板,用来固定型芯,采用通孔台肩式,B板厚度=(0.5~1)型芯高度,则B板厚度HB在26~52之间,标准化取HB=40mm。
此设计中模架标准采用龙记(LKM)标准模架。
标准模架如图4-4所示
图4-4
6、检验模架与注射机的关系
1、模具外形尺寸400×400<拉杆空间540mm×440mm,适合。
2、最大模具厚度450>模具厚度400>最小模具厚度300,合理。
3、开模行程<最大开合模行程500,合理。
4.6.浇注系统
浇注系统包括主流道、分流道、浇口和冷料穴。
浇注系统的设计应根据模具的类型、型腔的数目及布置、塑件的原料及尺寸的确定。
浇口分为直浇口、点浇口、潜伏式浇口、侧浇口等等,但是侧浇口由于浇口截面小,减少了浇注系统的消耗量,同时去除浇口容易,不留明显痕迹。
有助于提高模具表面质量。
B=0.6~0.9/30
=4.5
T=(0.6~0.9)g=1.5
浇注系统如图4-5所示
图4-5
4.7.侧抽芯机构
分析塑件汽车左/右弯管的外形特征得出,弯管的内部是空心的,这样单独只靠型芯和型腔不能直接加工生成塑件,必须从三个方向往内部加上侧抽,在塑件成型冷却后先向三个方向移开侧抽,之后再分模,这样就可以得到空心的汽车左/右弯管塑件了。
侧抽芯如图4-6所示
图4-6
4.8.推出机构
常用推出机构有推杆、推板、推管等。
推出机构设计的是否合理直接影响到塑件的质量和外观,因此推出机构应有足够的强度和刚度,推出动作应简单、灵活、可靠。
本套模具较为特殊,由于该塑件的外形特征因此选用了三个方向的滑块侧抽,虽然塑件成形冷却后收缩就连在型芯上,不过可以在滑块移开的时候滑块头连带着碰到塑件,加上塑件又是空心的圆管,因此塑件很容易受到自身重力落下,这样就不用去添加其他推出机构,也不需要推板、推杆固定板以及垫块等零件,大大提高了制造模具和生产的效率。
4.9.冷却系统
模具温度的调节既关系到塑件质量(塑件的尺寸精度、塑件的力学性能和塑件的表面质量),又关系到生产效率。
采用冷却水效果良好的冷却水回路的模具是缩短成型周期、提高生产效率最有效的方法,所以根据塑件的形状、壁厚及塑料的品种,设计与制造出能实现均一、高效的冷却水路。
分析得出,本套模具在型芯和型腔中都加工出了冷却水路,这样冷却的效果更好。
冷却系统如图4-7所示
型芯中冷却水路
型腔中冷却水路
图4-7
4.10.排气系统
由于此模具属于中小型模具,且模具结构较为简单,可利用模具分型面和模具零件间的配合间隙自然地排气,间隙通常为0.02~0.03mm,中间设排气槽。
5.注射机的校核
5.1.最大注射量
一般取K=0.8,已知n=1,Vs=36.1752㎝3,估计Vj=40㎝3,则Vmax≥(4×36.1752+40)/0.8=184.7008㎝3,因为满足KVmax﹥Vs+Vj,适合。
5.2.注射压力
已知P注=80~121MPa,P公=145MPA,
则P公≥P注,适合。
5.3.锁模力
锁模力是4500KN
5.4.安装部分尺寸
喷嘴孔直径φ7.5<主流道小端直径φ8
模具外形尺寸510×450<拉杆空间650mm×550mm
最大模具厚度510>模具厚度400>最小模具厚度300
5.5.开模行程
最大开模行程450
则最大开模行程>开模行程,适合。
5.6.推出机构
中心顶出,顶出距100mm,两侧顶杆机械顶出
毕业设计小结
这次的毕业设计,感受颇深,受益良多。
半个多月的时间,自己一点点的忙碌和老师的悉心指导加上同学的无私帮助,终于顺利完成了本次的毕业设计。
本次对汽车左/右弯管的注塑模设计很好的让我梳理了一遍自己所学的专业知识,其中不乏很多收获,有很多就是平时没注意或是学习得不好复习不到位的,通过这次算是更加了解和掌握了。
这个论文的完成包括从开始利用UG软件设计出整套模具出来,好好分析模架、浇注、推出、冷却四大系统的结构设计,还包括其他许多零部件的设计分析;之后利用UG和CAD绘图软件完成三维与二维的转换导出各个零件图,并且完成好尺寸标注。
这个过程中我很好的又熟练了UG与CAD绘图软件的使用。
在这次完成毕业设计的过程中,遇到的问题其实是不少的,这让我认识到以前所学还是有不少缺陷的,不过通过自己的复习加深巩固和老师同学的悉心指导与帮助,我自己完成了这次汽车左/右弯管的注塑模设计论文。
同时也很好的更透彻的掌握了自己所学的专业知识。
汽车的发展如此之迅速,本次通过对汽车左/右弯管注塑模的设计,不仅仅是更加巩固了所学的专业知识,也是面向现在良好发展趋势的一次很好的认识。
我相信这次的毕业设计让我学到了很多很多,以后在工作中一定能够有很大帮助,使我对所学专业知识和以后工作有更深的认识,争取以后能运用到实践中去,为以后的工作作一个很好的铺垫。
答谢词
我能够完成这次的毕业设计论文,要十分感谢我的指导老师叶峰老师。
因为自己所学知识和能力毕竟有限,多亏了叶老师的悉心指导下得以顺利的完成此次毕业设计论文。
此外,好几位同学的无私帮助也使我更加清晰、明了、深刻的掌握了所学专业知识,并且使得此次毕业设计论文圆满完成。
参考文献
[1].齐卫东.塑料模具设计与制造[M].第二版.北京:
高等教育出版社.2004
[2].陈剑鹤.塑料模具设计图册[M].第三版.北京:
清华大学出版社.2008
[3].史新民.机械设计基础[M].第二版.南京:
东南大学出版社.2007
[4].屈华昌.塑料成形工艺与模具设计[M].第一版.北京:
高等教育出版社.2001
[5].周小玉.实用模具技术手册[M].第二版.北京:
机械工业出版社.2002
附录一:
装配图
附录二:
零件图
毕业设计(论文)成绩评定表
一、指导教师评分表(总分为70分)
序号
考核项目
满分
评分
1
工作态度与纪律
10
2
调研论证
10
3
外文翻译
5
4
设计(论文)报告文字质量
10
5
技术水平与实际能力
15
6
基础理论、专业知识与成果价值
15
7
思想与方法创新
5
合计
70
指导教师综合评语:
指导教师签名:
年月日
二、答辩小组评分表(总分为30分)
序号
考核项目
满分
评分
1
技术水平与实际能力
5
2
基础理论、专业知识与成果价值
5
3
设计思想与实验方法创新
5
4
设计(论文)报告内容的讲述
5
5
回答问题的正确性
10
合计
30
答辩小组评价意见(建议等第):
答辩小组组长教师签名:
年月日
三、系答辩委员会审定表
1.审定意见
2.审定成绩(等第)________系主任签字:
年月日