电火花成形加工工具电极的设计与制造概要.docx
《电火花成形加工工具电极的设计与制造概要.docx》由会员分享,可在线阅读,更多相关《电火花成形加工工具电极的设计与制造概要.docx(12页珍藏版)》请在冰豆网上搜索。
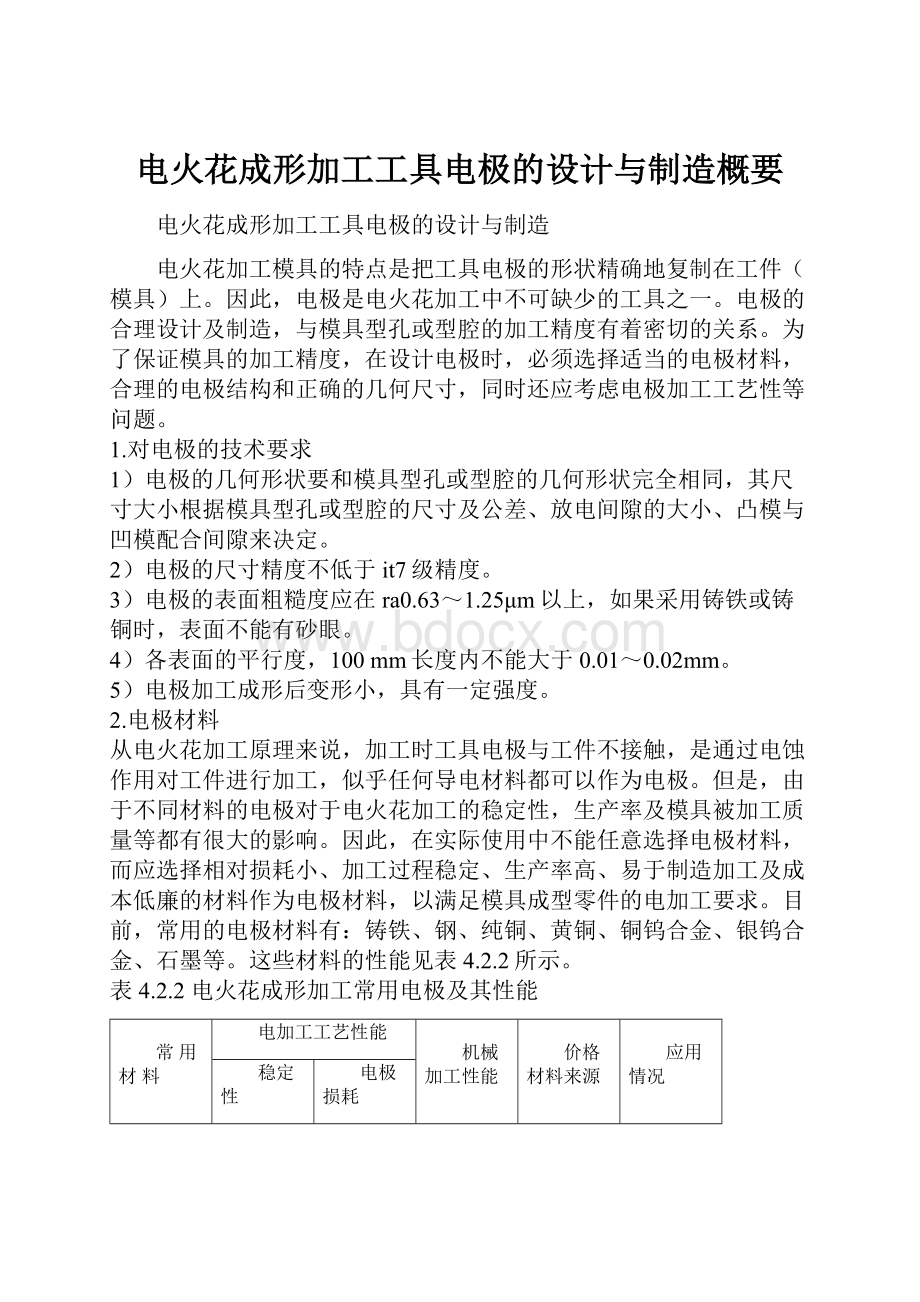
电火花成形加工工具电极的设计与制造概要
电火花成形加工工具电极的设计与制造
电火花加工模具的特点是把工具电极的形状精确地复制在工件(模具)上。
因此,电极是电火花加工中不可缺少的工具之一。
电极的合理设计及制造,与模具型孔或型腔的加工精度有着密切的关系。
为了保证模具的加工精度,在设计电极时,必须选择适当的电极材料,合理的电极结构和正确的几何尺寸,同时还应考虑电极加工工艺性等问题。
1.对电极的技术要求
1)电极的几何形状要和模具型孔或型腔的几何形状完全相同,其尺寸大小根据模具型孔或型腔的尺寸及公差、放电间隙的大小、凸模与凹模配合间隙来决定。
2)电极的尺寸精度不低于it7级精度。
3)电极的表面粗糙度应在ra0.63~1.25μm以上,如果采用铸铁或铸铜时,表面不能有砂眼。
4)各表面的平行度,100mm长度内不能大于0.01~0.02mm。
5)电极加工成形后变形小,具有一定强度。
2.电极材料
从电火花加工原理来说,加工时工具电极与工件不接触,是通过电蚀作用对工件进行加工,似乎任何导电材料都可以作为电极。
但是,由于不同材料的电极对于电火花加工的稳定性,生产率及模具被加工质量等都有很大的影响。
因此,在实际使用中不能任意选择电极材料,而应选择相对损耗小、加工过程稳定、生产率高、易于制造加工及成本低廉的材料作为电极材料,以满足模具成型零件的电加工要求。
目前,常用的电极材料有:
铸铁、钢、纯铜、黄铜、铜钨合金、银钨合金、石墨等。
这些材料的性能见表4.2.2所示。
表4.2.2电火花成形加工常用电极及其性能
常用
材料
电加工工艺性能
机械
加工性能
价格
材料来源
应用情况
稳定性
电极损耗
铸铁
较差
适中
好
低
(常用材料)
主要用于型孔加工,
制造精度高
钢
较差
适中
好
低
(常用材料)
常采用加长凸模,加长部分为加工型孔的电极;可降低制造费用
石墨
较好
较小
(取决于石墨性能)
好
(有粉尘、易崩角、掉渣)
较低
(常用材料)
适用于加工大、中型尺寸的型孔与型腔
纯铜
好
较大
较差
(磨削困难)
较高
(小型电极常用材料)
主要用于加工较小尺寸型腔,精密型腔,表面加工粗糙度可很低
黄铜
好
大
较好
(可磨削)
较高
(小型电极常用材料)
铜钨
合金
好
小
(为纯铜电极损耗的15%~25%)
较好
(可磨削)
高
(高于铜价40倍以上)
主要用于加工精密深孔、直壁孔和硬质合金材料的型孔与型腔
银钨
合金
好
很小
较好
(可磨削)
高
(比铜钨合金高)
(1)铸铁电极的电极损耗和加工稳定性均较一般,容易起弧,生产率不及铜电极。
但是,它的来源丰富、价格低廉、并且机械加工性能好,因此电极的尺寸精度,几何形状精度及表面粗糙度等都容易保证。
因此,铸铁是一种较常用的电极材料,多用于穿孔加工。
(2)钢电极的加工稳定性较差、电极损耗较大、生产率也较低、但是来源丰富、价格便宜、具有良好的机械加工性能。
钢电极还有其独特的优点,即把电极和凸模做成一体,实质上就是将凸模加长,加长的部分就用作电极。
电火花加工后,把损耗部分切除掉,余下部分可做凸模使用。
这种方法使电极的制造工时减少到了最低程度。
所以钢为常用的电极材料之一,多用于一般的穿孔加工。
(3)纯铜电极在加工过程中稳定性好、生产率高、但损耗较大、来源少、价格较贵。
由于其韧性大,机械加工性能差、磨削加工困难,其加工精度较低。
由于磨削困难,使得难以将电极与凸模连接在一起加工,电极与凸模分别制造使凸模与凹模配合间隙不易均匀。
对于电火花型腔加工来说,纯铜电极适用对小型腔及高精度型腔的加工。
纯铜电极与其他材料电极相比,在电火花加工中能使模具达到最细表面粗糙度。
(4)黄铜电极在加工过程中稳定性好、生产率高、与纯铜电极相比价格较低、机械加工性能尚好,但其磨削性能不如钢和铸铁。
而黄铜电极的损耗最大。
因此,黄铜电极一般用在对加工表面粗糙度较低,尺寸、形状精度要求较高及形状复杂的小孔穿孔加工。
(5)石墨电极的电极损耗小、加工稳定性尚好、易于加工、生产率最高、其价格与铜大体相同,但机械强度较差,尖角处易崩裂。
石墨是电火花型腔加工的常用电极材料,适用于大、中、小型腔。
由于石墨的热胀系数小,所以,最适于大电极的穿孔加工。
(6)铜钨合金和银钨合金的加工稳定性均很好,电极损耗也均很小,它们的电加工性能优越,而机械加工性能尚好,其磨削性比铜好。
但其价格较高,比铜的价格高40倍。
因此,主要用于模具中高精度的深孔、直壁孔等的穿孔加工和加工面积小且高精度的型腔加工,以及硬质合金模具的加工。
而银钨合金的价格更高,约为铜的100倍,所以它的使用受到限制,一般只用于硬质合金模具的加工。
当用同一种电极材料加工不同材料的模具时,加工情况也会有一定的差异,即使同是钢件也会因其成分不同而对加工有所影响,在实际生产中应根据具体情况选用电极材料。
3电极的结构形式
电极的结构形式应根据模具型孔或型腔的尺寸大小,复杂程度及电极的加工工艺性等来确定,常用的电极结构有下列几种形式:
(1)整体电极
整体电极就是用一整块电极材料加工出的完整电极,这是型孔或型腔加工中最常用的电极结构形式,图4.2.4所示即为型腔加工用整体电极的结构形式。
当电极面积较大时,可在电极上开一些孔,或者挖空以减轻重量。
对于穿孔加工,有时为了提高生产率和加工精度,降低表面粗糙度,可以采用阶梯式整体电极。
所谓阶梯式整体电极就是在原有的电极上适当增长,而增长部分的截面尺寸适当均匀减小(f=0.1~0.3mm),呈阶梯形。
如图4.2.5所示,l1为原有电极的长度,l2为增长部分的长度(为型孔深度的1.2~2.4倍)。
加工时利用电极增长部分来粗加工,蚀除掉大部分金属,只留下很少余量,让原有的电极进行精加工。
阶梯电极有许多优点:
能充分发挥粗加工的作用,大幅度提高生产效率,使精加工的加工余量降低到最小,特别适宜小斜度型孔的加工,易保证模具的加工质量,并且可减少电规准的转换次数。
a)无固定板式; b)有固定板式
图4.2.4整体电极结构形式 图4.2.5阶梯式整体电极
1-冲油孔; 2-石墨电极;3-电极固定板
(2)组合电极
在冲模加工中常遇到需要在同一凹模上加工出几个型孔,对于这样的凹模可以用单个电极分别加工各孔,也可以采用组合电极加工,即把多个电极组合装夹在一起。
如图4.2.6所示,一次完成凹模各型孔的电火花穿孔加工。
采用组合电极加工时,生产率高,各型孔间的位置精度也较为准确,但必须保证组合电极各电极间的定位精度,并且每个电极的轴线要垂直于安装表面。
图4.2.6组合电极 图4.2.7分解式电极
1)分解式电极 当工件形状比较复杂,则可将电极分解成简单的几何形状,分别制造成电极,以相应的加工基准,逐步将工件型腔加工成形。
采用分解式电极成形加工,可简化电加工工艺。
但是,必须统一加工基准,否则将增加加工误差,如图4.2.7所示。
分解式电极多用在形状复杂的异型孔和型腔的加工。
2)镶拼式电极 对形状复杂而制造困难的电极,可分解成几块形状简单的电极来加工,加工后镶拼成整体的电极来电加工型孔,该电极即为镶拼式电极。
如图4.2.8所示,是将e字形硅钢片冲模所用的电极分成三块,加工完毕后再镶拼成整体。
这样即可保证电极的制造精度,得到了尖锐的凹角,而且简化了电极的加工,节约了材料,降低了制造成本。
但在制造中应保证各电极分块之间的位置准确,配合要紧密牢固。
图4.2.8镶拼式电极
4电极尺寸的确定
(1)电极横截面尺寸的确定
电极横截面尺寸是根据凹模(或凸模)的尺寸及公差,凸模、凹模配合间隙和放电间隙的大小确定的。
电火花放电间隙的大小与电极材料、模具材料、电规准的选择、设备的精度及工作液等有关。
为了保证模具加工后的表面粗糙度,最后必须用精规准修出,因此在确定电极尺寸时,应先按相应的条件得到放电间隙值。
在凸模、凹模零件图上标注的公差时,根据模具的设计基准不同,有不同的标注方法。
因此,电极截面尺寸的确定也要按以凹模设计为基准,还是凸模设计为基准两种情况来讨论。
1)按凹模尺寸和公差确定电极横截面尺寸 如图4.2.9所示凹模型孔不同部位的尺寸公差标注。
其相应部位电极横截面尺寸的计算公式如下:
式中s——单面放电间隙;
δ——电极制造公差,通常取模具公差δ的1/2~2/3,并按“入体原则”标注。
2)按凸模尺寸和公差确定电极横截面尺寸 图4.2.10所示为凸模尺寸及公差标注,由于凹模、凸模配合间隙的不同又存在三种情况:
①凸模、凹模单边配合间隙等于放电间隙(z/2=s):
电极横截面尺寸和凸模截面尺寸完全相同,电极公差取凸模公差1/2~3/2。
②凸模、凹模单边配合间隙小于放电间隙(z/2<s):
电极应按凸模四周每边均匀缩小一个值(s-z/2),电极横截面尺寸计算公式如下:
图4.2.9凹模尺寸及公差标注 图4.2.10凸模尺寸及公差标注
③凸模、凹模配合间隙大于放电间隙(z/2>s),电极应按凸模四周每边均匀放大一个值(z/2-s),电极横截面尺寸计算公式如下:
式中s——单面放电间隙;
z/2——凸模、凹模单边间隙;
δ——电极制造公差,取模具公差δ的1/2~2/3。
由以上相应公式设计计算出的电极横截面尺寸适合一般型孔的电火花加工,对加工型腔的电极还应考虑精加工及抛光加工余量。
图4.2.11穿孔加工用电极长度 图4.2.12加工型腔电极纵截面尺寸
1-电极;2-凹模
(2)电极长度的确定
在电极长度确定方面,穿孔加工与型腔加工是不同的,穿孔加工只计算电极长度,而型腔加工还须考虑各纵截面的形状和尺寸。
1)穿孔加工电极长度的确定 图4.2.11所示为穿孔加工用电极长度。
电极长度按下式计算:
式中 l——电极总长度;
l1——精加工用的电极长度;
l2——粗中加工用的电极长度;
t——电极长度损耗(用铸铁电极,当加工钢模具时,t=0.9t1;当加工硬质合金模具时,t=1.7t1。
用钢电极,当加工钢模具时,t=1.1t1;当加工硬质合金模具时,t=2.1t1);
t1——凹模有效刃口厚度;
t2——凹模中有较大斜度的漏料部分厚度;
βt——粗中加工的电极端面损耗比。
当凹模的刃口为全刃口,没有斜度较大的漏料部分时,电极长度仅计算l1部分,即l=l1,但此时凹模有效刃口厚度t1应为t。
以上计算所得的电极长度是电火花穿孔加工时的工作部分长度,需要夹持时,还要加上夹持部分长度。
若采用同一只电极加工几副模具时,其电极的长度应加长,每多加工一副模具应比原来的长度约增加0.4~0.8倍。
但电极总长度一般不应超过110~120mm,否则将会给加工带来困难。
2)型腔加工电极纵截面尺寸的确定 型腔加工电极纵截面的形状和尺寸,应根据型腔底部的形状和尺寸并考虑放电间隙而确定。
对型腔底部不同部位的尺寸,其电极的尺寸计算也有所不同。
图4.2.12所示为加工型腔时,电极纵截面尺寸,尺寸的计算如下:
式中:
s为单面放电间隙;h、r1、r2、b为型腔要求尺寸;h′、r1′、r2′、b′为电极尺寸。
以上的计算方法仅适合型腔加工中低损耗加工的电极设计,并且精加工或抛光余量应另行考虑。
对于有损耗加工的电极设计在此没有涉及。
5.电极的制造
工具电极是电火花加工中必不可少的工具之一,因此方便而又准确地制造出电极是一个十分重要的问题。
由于电极的材料、类型、几何形状复杂程度及精度要求的不同,则采用的加工方法也各有不同。
(1)机械加工方法
对几何形状比较简单的电极,可用一般的切削方法来进行加工,如圆形电极可直接在车床上一次加工成形。
矩形、多边形等铸铁或钢电极可在刨床、铣床或到插床上加工后,再由平面磨床进行磨削加工,经钳工修整后即可使用。
对形状比较复杂的电极,往往需要经过多道工序才能加工成形,达到图样要求。
机械加工电极除采用一般的加工方法外,已广泛采用成形磨削。
对根据凹模尺寸设计出的电极,最后用成形磨削的方法进行精加工,可以提高电极的尺寸精度、形状精度和降低表面粗糙度,用此电极对凹模进行电火花加工,再由凹模按间隙要求配制凸模,这种方法适合于凸、凹模配合间隙比放电间隙大0.10mm以上,或凸、凹模配合间隙小于0.01mm的场合。
对于纯铜、黄铜一类的电极,由于不能用成形磨削加工,一般可用仿形刨床加工而成,并经钳工锉削进行最后修整。
(2)电极与凸模联合成形磨削
在电极制造中,为了缩短电极和凸模的制造周期,保证电极与凸模的轮廓一致,常采用电极与凸模联合成形磨削。
这种方法的电极材料大多选用铸铁和钢。
当电极材料为铸铁时,电极与凸模常用环氧树脂等胶合在一起,如图4.2.13所示。
但对于截面积较小的工件则不易粘牢,为防止在磨削过程中发生电极或凸模脱落,可采用锡焊或机械方法使电极与凸模连接在一起。
当电极材料为钢时,可把凸模加长些,将其作电极。
即把电极和凸模做成一个整体。
电极与凸模联合成形磨削,其共同截面的公称尺寸应直接按凸模的公称尺寸进行磨削,公差取凸模公差的1/2~1/3。
当凸、凹模的配合间隙等于放电间隙时,正好适用磨削后电极的轮廓尺寸与凸模完全相同的情况。
当凸、凹模的配合间隙小于放电间隙时,电极的轮廓尺寸应小于凸模的轮廓尺寸则可用化学腐蚀法将电极尺寸缩小至设计尺寸。
腐蚀剂可用草酸:
双氧水:
蒸馏水=40:
40:
100的溶液,腐蚀速度为0.04~0.07mm/min。
腐蚀的方法为:
将干净的电极垂直浸人腐蚀剂中,根据其腐蚀速度的大小,每隔一定的时间后取出,测量其尺寸是否符合要求,若尺寸仍偏大时应继续侵入,直到适合为止。
但取出的次数不要太多,否则在电极上会出现斜度,影响电极的加工质量。
当凸、凹模的配合间隙大于放电间隙时,电极的轮廓尺寸应大于凸模的轮廓尺寸,则需用电镀法将电极扩大到设计尺寸。
如单面放大量在0.05mm以下时,可以镀铜。
单面放大量超过0.05mm时,可以镀锌。
4.2.13电极与凸模粘结 4.2.14机械加工与线切割加工电极
l-电极;2-粘结面,3-凸模 a)机械加工;b)线切割加工
(3)电极制造常用工艺
电极制造常用工艺一般可按下述工序进行:
1)刨(或铣):
按图样要求刨或铣所要求的形状的电极毛坯(若是圆形可车削),按最大外形尺寸留1mm左右精加工余量。
2)平磨:
在平面磨床上磨两端面及相邻两侧面(对铜及石墨电极应在小台钳上,用刮研的方法刮平或磨平)。
3)划线:
按图样要求在划线平台上划线。
4)刨(或铣):
按划线轮廓,在刨床或铣床上加工成形,并留有0.2~0.4mm的精加工余量。
形状复杂的可适当加大,但不超过0.8mm。
5)钳工:
钻、攻电极装夹螺孔。
6)热处理:
指采用钢电极时,按图样要求淬火。
7)精加工电极:
对于铸铁或钢电极,在有条件的情况下,可用成形磨削加工成形;而对于铜电极,可在仿形刨床上进行仿刨成形。
8)化学腐蚀或电镀:
指电极与凸模联合加工(或阶梯电极)时,对小间隙模具采用化学腐蚀,对大间隙模具采用电镀。
9)钳工修整:
指对铜电极的精修成形。
(4)由线切割加工电极
除用机械方法制造电极以外,在比较特殊需要的场合下也可用线切割加工电极。
如异形截面和薄片电极,用机械加工方法无法胜任,或很难保证精度的情况。
图4.2.14a)所示的电极,在用机械加工方法制造时,通常是把电极分成四部分来加工,然后再镶拼成一个整体,如图4.2.14b)所示。
由于分块加工中的误差及拼合时的接缝间隙和位置精度的影响,使电极产生一定的形状误差。
如果使用线切割加工机床对电极进行加工,则很容易制作,并能很好地保证其加工精度。
(5)石墨电极的加工
石墨电极是电火花型腔加工中最常用的电极之一。
石墨电极的制作一般是采用传统的机械加工,即车、铣、刨、磨、手工修磨,样板检验等方法。
但在加工时,石墨材料易碎裂、粉末飞扬、劳动条件差,最好采用湿式加工(把石墨先在机油中浸泡)对精度高和形状复杂的电极较难制造。
且加工电极的重复精度差。
适用于单件或少量电极的加工。
当要批量生产石墨电极时,可采用压力振动加工方法方便地将石墨制成各种所需的电极形状。
压力振动加工石墨电极的方法,需要制造钢质母模,并需配有专用的压力振动加工机床,制作的石墨电极与母模的仿形性较好,加工重复精度较高。
不论是整体式和拼合式的石墨电极,都应使石墨压制时的施压方向与电火花加工时的进给方向垂直(图4.2.15),且拼合的石墨电极应采用同一牌号石墨。
a) 石墨压制时的施压方向 b) 拼合不合理 c)拼合合理
图4.2.15石墨电极方向性和拼合方向