大学化工厂实习报告.docx
《大学化工厂实习报告.docx》由会员分享,可在线阅读,更多相关《大学化工厂实习报告.docx(13页珍藏版)》请在冰豆网上搜索。
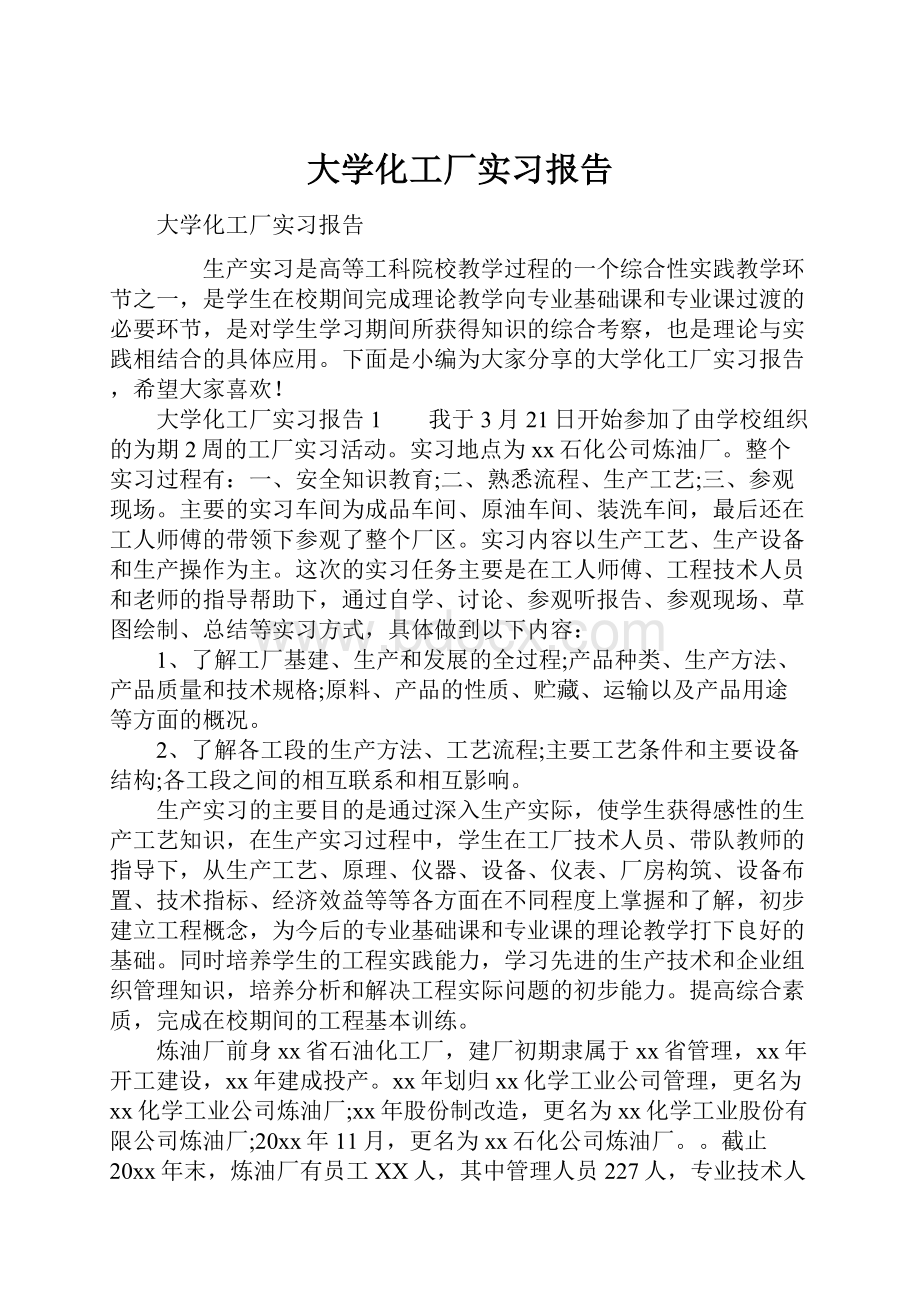
大学化工厂实习报告
大学化工厂实习报告
生产实习是高等工科院校教学过程的一个综合性实践教学环节之一,是学生在校期间完成理论教学向专业基础课和专业课过渡的必要环节,是对学生学习期间所获得知识的综合考察,也是理论与实践相结合的具体应用。
下面是小编为大家分享的大学化工厂实习报告,希望大家喜欢!
大学化工厂实习报告1 我于3月21日开始参加了由学校组织的为期2周的工厂实习活动。
实习地点为xx石化公司炼油厂。
整个实习过程有:
一、安全知识教育;二、熟悉流程、生产工艺;三、参观现场。
主要的实习车间为成品车间、原油车间、装洗车间,最后还在工人师傅的带领下参观了整个厂区。
实习内容以生产工艺、生产设备和生产操作为主。
这次的实习任务主要是在工人师傅、工程技术人员和老师的指导帮助下,通过自学、讨论、参观听报告、参观现场、草图绘制、总结等实习方式,具体做到以下内容:
1、了解工厂基建、生产和发展的全过程;产品种类、生产方法、产品质量和技术规格;原料、产品的性质、贮藏、运输以及产品用途等方面的概况。
2、了解各工段的生产方法、工艺流程;主要工艺条件和主要设备结构;各工段之间的相互联系和相互影响。
生产实习的主要目的是通过深入生产实际,使学生获得感性的生产工艺知识,在生产实习过程中,学生在工厂技术人员、带队教师的指导下,从生产工艺、原理、仪器、设备、仪表、厂房构筑、设备布置、技术指标、经济效益等等各方面在不同程度上掌握和了解,初步建立工程概念,为今后的专业基础课和专业课的理论教学打下良好的基础。
同时培养学生的工程实践能力,学习先进的生产技术和企业组织管理知识,培养分析和解决工程实际问题的初步能力。
提高综合素质,完成在校期间的工程基本训练。
炼油厂前身xx省石油化工厂,建厂初期隶属于xx省管理,xx年开工建设,xx年建成投产。
xx年划归xx化学工业公司管理,更名为xx化学工业公司炼油厂;xx年股份制改造,更名为xx化学工业股份有限公司炼油厂;20xx年11月,更名为xx石化公司炼油厂。
。
截止20xx年末,炼油厂有员工XX人,其中管理人员227人,专业技术人员223人,操作及服务人员15
62;机关设综合办公室、生产科、技术科、机动科、安全环保科、组织人事科、党群工作科等7个科室;下辖常减压一车间、常减压二车间、催化裂化车间、重油催化车间、柴油加氢车间、加氢裂化车间、联合芳烃车间、硫磺回收车间、延迟焦化车间、成品车间、原油车间、装洗车间、分析车间、仪表车间、电气车间、供排水车间、锅炉车间、综合车间等18个生产及辅助车间。
炼油厂厂区占地面积1
55。
42公顷,原油加工能力700万吨/年,有380万吨/年和320万吨/年两套常减压装置、140万吨/年和70万吨/年两套重油催化裂化装置、25万吨/年气体分馏装置、40万吨/年联合芳烃装置、90万吨/年加氢裂化装置、120万吨/年柴油加氢装置、100万吨/年延迟焦化装置、90万吨/年汽油脱硫醇装置、30万吨/年液化气脱硫装置、10万
吨/年催化干气脱硫装置、7万吨/年加氢干气脱硫装置、60万吨/年酸性水汽提体装置、64万吨/年溶剂再生装置、7000吨/年硫磺回收等;套生产装置,以及锅炉、循环水场、污水处理场、原油和成品油罐区、装卸车等辅助设施。
主要产品有汽油、柴油、液化石油气、丙烯、苯、甲苯、邻二甲苯、混苯、化工原料油、石油焦、硫磺等20多个品种。
20xx年,原油加工总量675万吨,商品总量650万吨。
目前,炼油厂正在实施汽柴油质量升级和Ⅱ常减压装置改造项目,项目主要包括:
Ⅱ常减压装置600万吨/年改造、催化裂化装置140万吨/年采用MIP技术改造、建设60万吨/年液化气脱硫及气分装置、新建120万吨/年催化汽油加氢脱硫及烃重组联合装置、;0万吨/年柴油加氢精制装置和2万吨/年硫磺回收装置、以及进行贮运系统、公用工程配套系统的改造。
项目建成后工厂原油加工量可达1000万吨/年,汽油产品质量全部达到国Ⅲ标准
原油车间:
原油车间是以原油储存为主要任务的车间,车间的主要岗位分别是:
原油罐区、蜡油罐区、原油卸车站、驻寨、计量、调度、办公室等。
现车间共有人员为;2人。
岗位班次的运转方式为两种;一种是四班三倒(原油罐区、蜡油罐区),另一种为运输班(卸车站、调度)。
装置特点
a。
车间大部分原油储罐为浮顶油罐,此种储罐最大限度地减小了原油蒸发损失。
b。
三个原油罐区与卸车站之间流程相连,可以实现最科学的原料平衡。
c。
原油卸车站拥有四个原油上卸鹤位和两个渣油上卸鹤位,可以最快速地处理原油、渣油“瞎子车”。
d。
渣油站台为装卸一体化站台,可以同时实现渣油装车与卸车。
储存原油种类及输送形式
储存原油主要分轻、重两种组分,按来源主要分为大庆原油、xx油田原油、俄罗斯原油、扎赉诺尔原油。
按输送形式主要分为管输原油和铁路槽车原油。
俄油、大庆油两种原油性质的差异。
工艺原理
利用液体油品流动性能,通过不同的管路自压或用泵压进行卸车及输送油品入装置。
成品车间
成品系统于xx年开始长周期的投入使用。
其主要操作是接收、储存、调合、转输半成品油和成品油,并按要求进行加温、脱水及计量。
其最主要特点是罐区分散、战线长且储存介质易燃易爆。
目前的成品车间共设置五个罐区,即:
汽油罐区、柴油罐区、液化气罐区、渣油罐区、芳烃成品罐区,总存储能力19万立。
9个泵房,即:
汽油泵房、汽油消防泵房、汽油加铅泵房、柴油泵房、柴油消防泵房、液化气泵房、液化气消防泵房、渣油泵房、芳烃成品泵房。
共有储罐77台,其中储油罐64台(包括10台球罐),其他储罐13台,冷换设备9台,机泵61台,其中油品转输用泵44台,消防用泵10台,其它机泵7台,以及全部出入该5个
罐区的全部输油管线约35万多延长米。
汽油罐区xx年建成。
目前的汽油罐区共有储罐17台,其中5000立储罐11台,XX立储罐2台,1000立储罐4台,总储存能力63000立,共有离心泵12台,其中加铅泵1台,消防泵3台,消防泡沫罐2座。
总占地面积约为93100米
2。
柴油罐区xx年建成。
最初的柴油罐区共有储罐11台,目前的柴油罐区共有13台储罐,其中5000立储罐9台,10000立储罐2台,XX立的储罐2台,总储存能力69000立。
油品转输泵7台,加降凝剂泵2台,消防水泵3台,消防泡沫罐1座。
总占地面积约为54600M
2。
渣油罐区xx年建成,目前渣油共有储罐7台,其中5000立储罐3台,3000立储罐2台,XX立储罐2台,总储存能力25000立,共有油品转输用泵7台,其中离心泵5台,蒸汽往复泵2台,总占地面积约为2;00米
2。
液化气罐区xx年建成,后有扩建和改建,目前共有球罐13台,总储存能力7200立。
其中1981年建成400立球罐三台,1986年建成400立球罐四台,1992年建成400立球罐一台,随着生产装置的扩建和改造,20xx年增建两台1000立球罐,20xx年增建3台1000立球罐。
共有油品转输用泵10台,消防用水泵4台,另设汽车装车鹤位19个,总占地面积约为58000m
2。
芳烃罐区xx建成,为30万吨乙烯装置配套。
xx年10月投用,共有储罐8台,其中3000立储罐6台,1000立储罐2台,总储存能力XX0立,共有油品转输用泵10台,总占地面积约为8400M
2。
油品储罐及其附件炼油厂成品车间用于储存油品的设施为油罐,油罐共分三种类型,分别是立式拱顶罐、立式浮顶罐和球罐。
汽油罐区、四苯罐区全部为浮顶罐,柴油罐区为部分浮顶罐和部分拱顶罐。
渣油罐为拱顶罐,液化气罐区储存液态烃,全部为压力球罐油品储存的注意事项
1、易燃性。
燃烧的难易和石油产品的闪点,燃点和自燃点三个指标有密切关系。
石油闪点是鉴定石油产品馏分组成和发生火灾危险程度的重要标准。
油品越轻闪点越低,着火危险性越大,但轻质油自燃点比重质油自燃点高,加此轻质油不会自燃。
对重油来说闪点虽高,但自燃低,着火危险性同样也较大,故罐区不应有油布等垃圾堆放,尤其是夏天,防止自燃起火。
2、易爆性。
石油产品易挥发产生可燃蒸气,这些气体和空气混合达到一定浓度,一遇明火都有发生火灾、爆炸危险。
爆炸的危险性取决于物质的爆炸浓度范围。
3、易挥发、易扩散、易流淌性。
4、易产生静电。
石油及产品本身是绝缘体,当它流经管路进入容器或车辆运油过程中,都有产生静电的特性,为了防止静电引起火灾,在油品储运过程中,设备都应装有导电接地设施;装车要控制流速并防止油料喷溅、冲击,尽量减少静电发生。
装洗车间建于xx年,是我厂生产的最后一道工序,担负着我厂成品油出厂主要任务。
目前车间共有三座装车站台,分别是汽油装车站台,柴油装车一站台,柴油装车二站台;一坐挑车站台,一座洗槽站台。
汽油装车站台于1986年3月建成投用,设有2台浸没式内液压柴油大鹤管,另设有2台浸没式外液压汽油油大鹤管,同采用爬车牵引,双侧轮换液下装车。
(20xx年新建一套膜法油气回收装置与其配套)柴油装车站台于XX年9月建成投用,设有2台浸没式内液压轻油大鹤管,采用爬车牵引,双侧轮换液下装车。
汽油装车站台设计装车能力为130万吨/年。
两坐柴油装车站台设计装车能力为300万吨/年。
汽油装车二站台设计装车能力为130万吨/年,目前正在建设中。
洗槽站共有48个洗车鹤位,采用双侧洗车,可洗汽油、柴油槽车。
工艺原理
1、根据液体油品流动性能,通过不同的管路自压或泵压进行装车。
2、对含污油槽车进行清洗,将清洗后的污油抽至污油罐内,从而达到洗车目的。
在这段短暂的实习时间里,我的收获和感想很多,我觉得这种形式的参观实习非常的有意义,因为这比坐在课堂里听讲来得更为实际、直观。
通过实地参观,我了解了生产的工艺流程,对工业生产的各个环节和主要设备都有了一定认识,并对这个行业有了一定的了解。
我感到自己真的是学到了很多与专业相关的知识,同时也提高了我在生产实践中认识、分析问题的能力。
为日后的实际工作打下了基础。
但同时,也意识到了自己知识是如此匮乏,所以在今后的日子里,我们要更加努力的学习专业知识,填补自己的空白我们通过实习对炼化公司的生产技术了较详细的认识,在此我们不仅加深了对专业知识的认识,也使我们开阔了眼界,也更加让我们感到了学习的重要性。
为进一步学好专业课,从事这方面的研制、设计等打下良好的基础。
在这次生产实习过程中,不但对所学习的知识加深了了解,更加重要的是更正了我们的劳动观点和提高了我们的独立工作能力等。
总之,理论学习是基础,但实际工作与理论的阐述又是多么的不同,在工作的闲暇之间,在同一些工作多年的人员的交谈中,深知,在工作岗位上,有着良好的业务能力是基础能力,是那么的重要。
虽然实习的时间很短,但对我来说,收获是很大的。
我会更加珍惜我的学习,并且用实习的心得时时激励自己!
大学化工厂实习报告2 实习目的
本次生产实习,是为了让我们了解社会、工厂、企业,深入了解本专业,并为后续课程的学习提供感性认识;让我们了解化学工业生产过程和状况,了解产品的工艺流程及主要设备、机械的结构原理。
通过将以前学习的基础课程与生产实践相结合,形成初步的专业概念,让我们对现实生活中工厂的工艺流程有所了解。
通过将所学的理论知识与实践结合起来,培养我们勇于探索的创新精神、提高动手能力,加强社会活动能力,与严肃认真的学习态度,为以后专业课的学习和走上工作岗位打下坚实的基础。
通过两个星期的工厂实习让我们对生产工艺流程和相关设备有一定的感性和理性认识,培养我们理论联系实际的能力,提高分析问题和解决问题的能力,增强独立工作的能力。
最主要的是培养了我们与其他同学的团队合作、共同探讨、共同前进的精神。
实习任务
主要内容:
(1)企业组织运行概况
了解现代化工厂企业的生产组织机构、生产企业管理、运行机制,认识企业生产过程,认识企业的研发过程。
(2)了解生产过程,工艺流程。
(3)现代化生产流水线及测控仪表及集散控制系统
认识实际的离散控制系统的实现过程,理解计算机控制系统的核心技术。
认识计算机测控系统的通信方式及协议等。
(4)了解产品检验及质量管理
认识和了解生产企业的产品检测过程和规范,质量管理体系建设。
认识企业建设和维护核心竞争力的措施和方法。
分组及进程安排:
中午从科技学院到川化
日上午:
川化阶梯教室安全教育
下午:
阶梯教室合成氨工艺
日上午:
化肥厂合成氨尿素工艺装置现场
下午:
阶梯教室现场仪表概述
日上午:
检修公司仪表部仪表检修
下午:
硫酸/硝酸工艺
日上午:
三胺厂/制酸厂参观工艺
下午:
阶梯教室调节阀理论
日上午:
检修公司仪表现场仪表
下午:
阶梯教室双氧水工艺
日上午:
气体厂二氧化碳工艺现场
下午:
阶梯教室学习
日上午:
检修公司仪表现场仪表
下午:
阶梯教室,调节阀事故处理
日上午:
检修公司仪表部现场仪表
下午:
技校阶梯教室实习考试
日上午:
技校阶梯教室实习总结/作业
下午:
返回科技学院
川化集团有限责任公司(原四川化工厂)始建于xx年,经过四十多年的发展,已成为一个以生产化肥和化工原料为主的综合性特大型化工企业,是全国18个大型化工基地之一。
公司是于xx年9月经国家经济体制改革委员会"体改生157号"文件批准,根据《中华人民共和国公司法》等有关法规,由川化集团有限责任公司作为独家发起人,以川化集团公司下属的第一化肥厂、第二化肥厂、三聚氰胺厂、硫酸厂、硝酸厂、催化剂厂、气体厂、供应公司、销售公司及相关部门经评估确认的净资产折股,发起设立的股份有限公司;公司于xx年10月20日经四川省工商行政管理局核准登记注册成立。
肥料制造、基础化学原料制造及销售;生产食品添加剂;道路运输经营;专用铁路兼办铁路货物运输(运输品名类按《铁路专用线专用铁路名称表》规定)。
(以上项目及期限以许可证为准)一般经营项目(以下项目不含前置许可项目,后置许可项目凭许可证或审批文件经营):
化学试剂和助剂、塑料制品制造;商品批发与零售;进出口业;仓储业;工程机械租赁;货运代理;国内劳务派遣;房地产经营;建筑装饰装修工程;科技推广和应用服务业;环境治理;专业技术服务业;金属制品、机械和设备修理业;人力资源管理服务。
公司地处四川省成都市青白江区,距成都市区约30公里,距成都双流国际机场约60公里,均高速公路直达。
厂区专用铁道与宝成铁路青白江站接轨,厂区公路与成绵高速公路、川陕公路接道。
公司拥有川化股份有限公司、川化永达建设工程有限责任公司、川化润嘉置业有限责任公司、成都望江化工厂、深圳荣生化工有限公司等5家全资、控股子公司和中外合资企业川化味之素有限公司、川化青上有限公司。
公司现有在册职工7350人(其中各类专业技术人员1020余人),资产总额25亿元,占地220公顷,是我国目前最大的合成氨、氮肥生产企业之一及最大的三聚氰胺和赖氨酸生产企业。
公司以其规模优势、技术优势、管理优势、人才优势和地域优势,在全国化工行业中处于领先水平。
"川化"(scw)这一企业品牌和"天府牌"商标,在国内外享有较好知名度和声誉,产品畅销全国各省、市、自治区,部分产品还远销国外。
公司先后荣获"全国产品质量优秀企业"、"全国环保先进企业"、"全国五一劳动奖状"、"中国企业管理杰出贡献奖"、"全国精神文明建设工作先进单位"、"全国先进基层党组织"等称号。
该公司共生产90个品种200多个型号的产品,主导产品年生产能力为:
合成氨50万吨、尿素62万吨、硝酸铵24万吨、浓硝酸万吨、工业硫酸10万吨、三聚氰胺万吨、催化剂2500吨、双氧水万吨、硫酸钾2万吨、赖氨酸1万吨、皮革化学品8000吨、氨基塑料4500吨。
产品均采用国际标准和国外先进标准组织生产,国家和部级优质产品率达87%以上。
公司拥有进出口权,产品畅销全国各省、市、自治区,部分产品还远销力、韩、俄、美灯二十多个国家和地区
尿素工艺
川化集团股份有限公司化肥厂现有2套尿素生产装置,其中一套尿素装采用传统水溶液全循环法工艺,主要包括合成、两段分解、三段吸收、两段蒸发和自然通风造粒的工序,生产能力为16kt/a;二尿装置采用日本东阳公司(TEC)水溶液循环改良C法,XX年采用该公司的ACES21工艺进行增产、技能技术改造,改造后生产能力为720kt/a。
全循环法存在一次通过的尿素合成率低的诸多缺点,目前大多厂家采用汽提法生产尿素。
其实质是在与合成反应相的压力的条件下,利用一种气体通过反应物系,是反应的氨和二氧化碳通过气提法合成。
(1)工艺流程简介
①原料氨和二氧化碳的压缩
原料液氨由合成氨车间供给,进入尿素车间后,经过氨预热器后进入高压氨泵,为了避免液氨气化需控制液氨的温度比经过氨泵提压后的沸点低10℃。
原料气CO2经过二氧化碳压缩机压缩后送入合成塔和气提塔底部。
②合成与气提
合成氨装置来的原料液氨经过升压和预热后进尿素合成塔,原料CO2经脱氢反应器脱除H2后,再经过压缩,大部分的CO2送汽提塔作汽提介质,其余部分则送尿素塔合成尿素。
在达到高的转化率后,尿素进入汽提塔,通过CO2汽提,将尿素溶液中的未反应的甲铵分解以及过量的氨汽提出来之后进入甲铵冷凝器,经过汽提后的尿素溶液送至提纯工序。
甲铵冷凝器出来的气体则进一步进入高压吸收塔冷却器进一步回收NH3和CO2,甲铵冷凝器底部出来的甲铵溶液通过高压甲铵喷射器进入尿素合成塔。
③中低压分解和回收工序
从合成工序来的尿素溶液进入一段分解塔,通过尿素自身热量使液相中的一部分NH3和CO2被解吸出来,进而通过中压蒸汽的热量使甲铵分解成气相的NH3和CO2,再进入一段吸收塔冷却器。
从一段分解塔出来的尿素溶液经二段溶液分解塔进一步使尿素溶液中的NH3和CO2降至%和%。
从二段分解塔出来的尿素溶液经冷凝、闪蒸后送至蒸缩工序。
④尿液的蒸发和造粒
从提纯工序来的尿素溶液经预压缩至70%wt左右,再进入蒸发工序,经二段工序蒸发后,送造粒塔生产颗粒尿素产品。
蒸发出来的水蒸汽,进入最终浓缩器表冷器,冷凝后送至工艺冷凝液处理工序。
从蒸发器出来的汽液混合物在分离器中分离,气相经冷凝后送至工艺冷凝液处理工序。
合成氨工艺
合成氨的原料包括氮气、氢气,氮气从空气中获取,氢气的来源较多。
川化合成氨工艺的氢气来源于天然气,这也是世界上80%以上的合成氨采用的原料。
(1)川化的合成氨工艺包括以下四道主要工序:
①原料天然气的压缩和脱硫
硫是天然气带来的主要危害,合成氨生产过程所用的催化剂对硫极为敏感,在转化工序中,平均每一个镍原子中,只要有不到一个硫原子就足以产生严重的硫中毒。
虽然转化催化剂的硫中毒,可以用提高温度将硫驱除,但是硫浓度增加五倍,温度要提高380C才能抵消其影响。
这样就要求炉管在较高的温度下操作,不仅使炉管的寿命缩短,并使每吨氨的燃料消耗大大增加,在变换工序中,低温变换催化剂的硫中、毒是不可逆的,因此必须先除去原料气中的硫化物。
本装置使用的天然气,含硫量设计值不大于35PPm,其中主要是硫化氢和硫醇(硫醇占有机硫的90%),这套装置根据使用的天然气中硫含量不高,而要求的净化程度很高这二个特点,选用了钴钼加氢转化串联氧化锌脱硫。
②粗合成器的制备
本工艺甲烷制氢的方采用蒸汽二段转化法,即将甲烷分两次转化,这是为了减轻一段炉的负荷,使其能在较低的温度下操作。
将一段转化炉内(1000℃)约为90%的甲烷转化为氢气,剩余10%的甲烷与定量的已预热空气一起进入二段转化炉转化,温度1035~1070℃。
将%的CO在高温炉内氧化铁触媒催化下雨水蒸气反应转化为CO2,出口温度为428℃,出口CO含量下降到%。
③合成气的净化
经过变换后的工艺气体中,二氧化碳含量达%,必须清除到%以下,如果有较多的二氧化碳存在,不仅会使氨合成塔催化剂中毒,而且进入甲烷化后,给清除少量的一氧化碳过程带来困难,因为二氧化碳越多,则消耗的氢气越多,同时放出大量的热量,产生很大的温升,可能使甲烷化触媒由于超温所损坏,另一方面,二氧化碳是制造尿素的原料,在脱除二氧化碳过程中,要考虑它的回收以满足尿素生产需要。
本装置脱除CO2采用苯菲尔法,是催化热钾碱法的一种,使用的液相催化剂为二已醇胺,苯菲尔溶液有较高的净化能力,并能副产较纯的CO2尿素生产用,其流程和设备设计为二段吸收,二段加闪蒸再生,吸收塔上段有三层鲍尔环填料(其中碳钢环不锈钢环)塔下段有三层超级拉西环填料,不锈钢环是设置在气液分界处,气液易冲刷处及温度较篙处,以减少腐蚀和克服在这些位置钒化膜不稳定的缺点。
再生塔上段有三层超级拉西环填料m3,塔下段有一层填料鲍尔环,其中碳钢环m3,,不锈钢环m3,。
甲烷化的作用是将氢氮混合气中未被完全脱除掉的少量一氧化碳(约%)和二氧化碳(%以下)在一定温度下通过甲烷化催化剂的作用与氢反应生产甲烷,使在氢氮混合气中的CO+CO2降到10PPm以下。
甲烷化操作是否稳定取决于低变触媒的状况或脱碳操作是否稳定,如果低变后的CO或脱碳后的CO2超过了设计数据,进入合成系统的甲烷将会增多,结果不仅增加了驰放损失和功耗,而且甲烷化反应放出的热量增加时(即超温)可能损坏触媒和容器,这是实际操作中必须注意的问题。
④精合成气的压缩和氨的合成
以天然气为原料的大型氨厂使用四台大压缩机,即原料气压缩机将原料天然气送入一段转化炉,空气压缩机将工艺空气送入二段转化炉,合成气压缩机将合格的氢氨气送入合成回路,以及提供冷冻量的氨气压缩机。
硫酸工艺
硫酸,化学式为H2SO4。
是一种无色无味油状液体,是一种高沸点难挥发的强酸,易溶于水,能以任意比与水混溶。
硫酸是基本化学工业中重要产品之一。
它不仅作为许多化工产品的原料,而且还广泛地应用于其他的国民经济部门。
硫酸是化学六大无机强酸(硫酸、硝酸(HNO3)、盐酸(HCl,学名氢氯酸)、氢溴酸(HBr)、氢碘酸(HI)、高氯酸(HClO4)之一,也是所有酸中最常见的强酸之一。
硫酸厂是以硫磺为原料,以五氧化二钒为主体的催化剂催化,通过接触法生产98%的浓硫酸及副产品。
硫酸厂在价格上涨,而硫酸价格持平的情况下,基本处于亏损状态,但是由于硫磺制酸工艺过程会产生大量的能量,除供给自身外,还要供给硝酸车间、合成氨工艺、尿素生产工艺,所以仍在持续生产。
(1)硫酸主要工艺流程
①硫磺熔融及过滤
原料固体硫磺先通过熔硫系统,利用蒸汽熔化成液态,经过利用硅藻土附在叶片上做成的液硫过滤器除去其中的灰分、渣子等。
通过过滤的液硫在泵的压力下进入贮硫罐,流过精硫槽,精硫槽出口处的泵出口呈枪型,对液硫进行物理雾化,使之进入焚硫炉可以更加完全的燃烧。
产生的SO2气体约在400℃进入转化器。
②焚硫转化
转换器内自下而上分成四层,每一层都装满了V2O5,气体从底部进入转换器首先进入的是一层,在这一层的转化率达到60%,气体温度升至600℃,换热后,气体进入二层,在二层的转化率达到80%,反应后的气体温度上升至500多℃,通过热热换热器将温度降至420~440℃。
再进入三层,此时转化率升高不多,仍旧是80%多,温度上升至400多℃(高于440℃)原料固体硫磺先通过熔硫系统,利用蒸汽熔化成液态,经过利用硅藻土附在叶片上做成的液硫过滤器除去其中的灰分、渣子等。
通过过滤的液硫在泵的压力下进入贮硫罐,流过精硫槽,精硫槽出口处的泵出口呈枪型,对液硫进行物理雾化,使之进入焚硫炉可以更加完全的燃烧。
产生的SO2气体约在400℃进入转化器。
反应后的气体经过冷热换热器将温度降至200多℃。
经过三层转化,反应已经基本平衡,很难再提高转化率,此时需要吸收已经生成的SO3使反应继续进行。
③三氧化硫吸收
S