硬质合金插齿刀设计及有限元分析 毕业设计.docx
《硬质合金插齿刀设计及有限元分析 毕业设计.docx》由会员分享,可在线阅读,更多相关《硬质合金插齿刀设计及有限元分析 毕业设计.docx(52页珍藏版)》请在冰豆网上搜索。
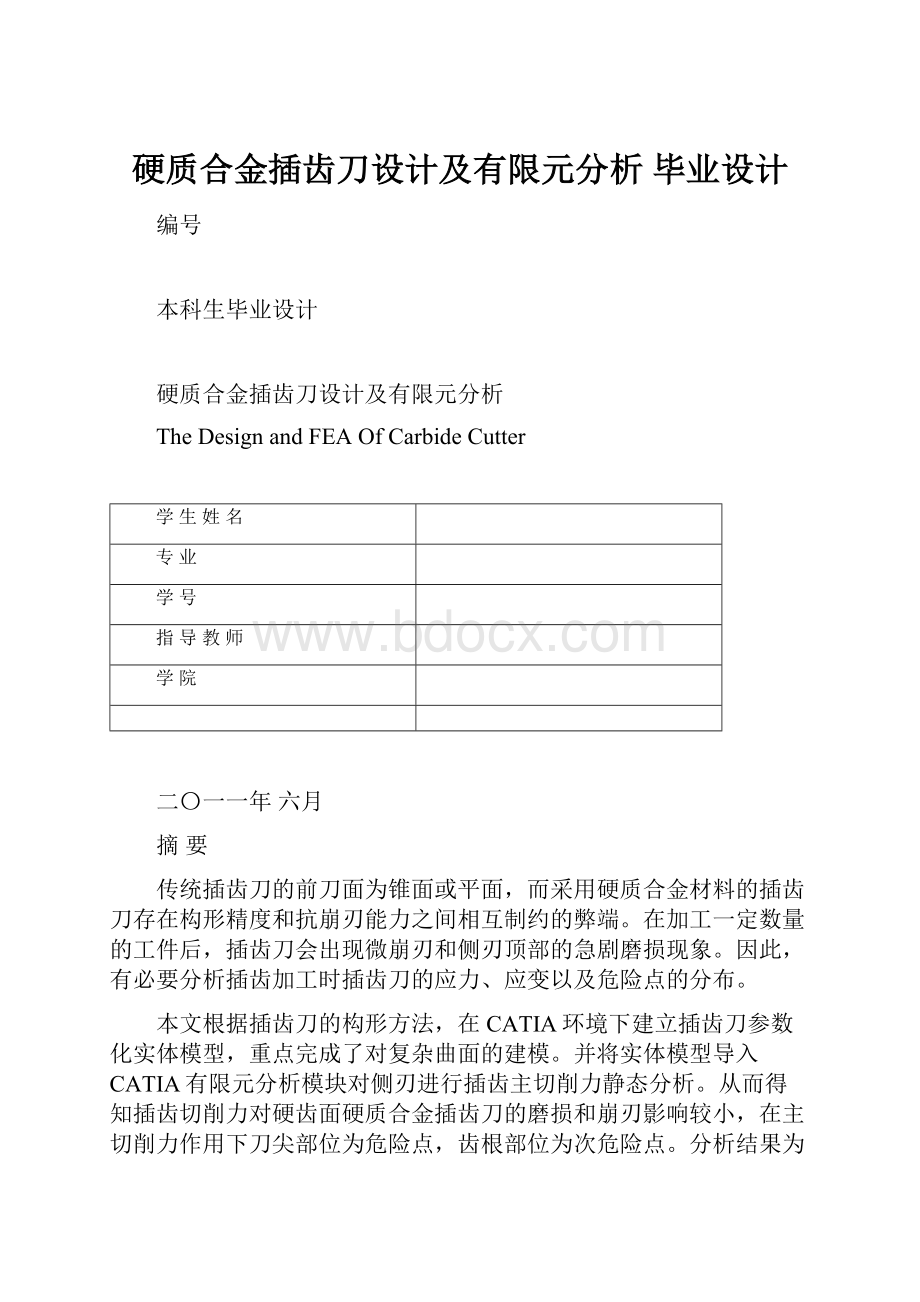
硬质合金插齿刀设计及有限元分析毕业设计
编号
本科生毕业设计
硬质合金插齿刀设计及有限元分析
TheDesignandFEAOfCarbideCutter
学生姓名
专业
学号
指导教师
学院
二〇一一年六月
摘要
传统插齿刀的前刀面为锥面或平面,而采用硬质合金材料的插齿刀存在构形精度和抗崩刃能力之间相互制约的弊端。
在加工一定数量的工件后,插齿刀会出现微崩刃和侧刃顶部的急剧磨损现象。
因此,有必要分析插齿加工时插齿刀的应力、应变以及危险点的分布。
本文根据插齿刀的构形方法,在CATIA环境下建立插齿刀参数化实体模型,重点完成了对复杂曲面的建模。
并将实体模型导入CATIA有限元分析模块对侧刃进行插齿主切削力静态分析。
从而得知插齿切削力对硬齿面硬质合金插齿刀的磨损和崩刃影响较小,在主切削力作用下刀尖部位为危险点,齿根部位为次危险点。
分析结果为继续研究硬质合金插齿刀奠定了理论基础。
同时,为了加工应用,利用AutoCAD软件绘制了二维工程图纸。
关键词:
硬质合金插齿刀CATIA实体建模有限元分析
Abstract
Thetraditionalshapercutter’srakefaceistapersurfaceorflat.Theuseofcarbidematerialleadsadrawbackthattheshapercutter’sconfigurationaccuracyandabilityofanti-chippingrestrictseachother.Aftermachinedacertainnumberofjobs,microchippingwillappearsandthetopofsideedgewillwearrapidly.Therefore,itisnecessarytoanalyzethedistributionofshapercutter’sstress,strainanddangerouspoint.
Thisarticleaccordingtotheshapercutter’sconfigurationmethod,establisheditsparametricsolidmodelsintheCATIAenvironment,focusonthecompletionofthemodelingofcomplexsurface.AndimportsolidmodelsintoCATIAfiniteelementanalysismoduleforthestaticanalysisofthemaincuttingforce.Atlastwegottheresultthatthemaincuttingforcehaslittleeffectoncarbideshapercutter’swearandchipping.Undertheactionofmaincuttingforcethecornerisdangerouspoint,thetoothrootspartistheminordangerouspoint.Theanalysisresultslaidatheoreticalfoundationoffurtherstudyofcarbideshapercutter.Meanwhile,forpracticalapplication,usedAutoCADsoftwaretodrawtwo-dimensionalengineeringdrawings.
Keywords:
Carbidematerial;Shapercutter;CATIAsolidmodeling;Finiteelementanalysis
第1章绪论
1.1硬齿面插齿技术概述
随着机械工业的发展,硬齿面齿轮的应用越来越广泛。
而且现代工业对传动系统和变速系统中齿轮精度和机械性能的要求越来越高,齿轮正朝着高精度、低噪声、高承载、高速度、轻量化及长寿命方向发展。
伴随着高精度硬齿面齿轮的广泛应用,国内外都对硬齿面齿轮的加工进行了大量研究,致力于如何以高效率和低成本来实现硬齿面的精加工。
在齿轮的切削加工方法中,插齿技术是目前高精度硬齿面齿轮加工的一种广泛应用的切齿方法。
1.1.1插齿技术在齿轮加工中的地位
齿轮的切削加工方法按其原理可分为仿形法和展成法两类,其中展成法是目前齿轮加工中应用最普遍的方法,它是利用一对齿轮啮合或齿轮与齿条啮合的工作原理来加工的,如滚齿、插齿、剃齿和梳齿等工艺方法。
硬齿面齿轮的精插削是用硬质合金插齿刀精加工热处理后硬度为HRC45-64硬齿面齿轮。
硬齿面精加工通常采用磨削工艺,即齿轮在淬火前进行粗切齿,淬火后用磨齿的方法精加工。
此工艺的特点是效率低、成本高,其应用受到很大的限制。
20世纪70年代,国内外开始采用硬质合金刀具精加工的研究,相继开发了硬质合金滚刀、硬质合金插齿刀等精切硬齿面齿轮的新技术,均已取得了一定的成效,从工艺上保证了淬硬齿轮的广泛应用的可能性。
但是到目前为止刀具都存在易崩刃、寿命短的问题,使这类刀具即使在稳定的工况上也难于使用。
对于插齿工艺来说,由于插齿时刀具的齿距累积误差和机床传动链误差都将反映到被加工的齿轮上,因此插齿刀不易加工出精度很高的齿轮,其加工效率亦相对低于滚齿工艺。
滚齿生产具有高效率、高精度及加工范围广等特点,因此滚齿工艺是实际生产中应用最为广泛的切齿方法,在齿轮加工中一直居优势地位。
然而有些情况,特别是对内齿轮、阶梯齿轮或多联齿轮、无空刀槽的人字齿轮及某些非标准齿轮的加工,插齿加工方法具有不可替代性,因而插齿工艺在整个齿轮加工业中仍占有很大的比例。
随着工业技术水平的提高,插齿技术也得到很大发展,对插齿机床和插齿刀具的有效改进,使得其生产效率和加工精度与滚齿生产的差距日益缩小,加之其所具有的加工特性,在实际生产中至今仍被广泛采用,因此,它是一种不可取代的齿轮加工技术。
1.1.2硬齿面插齿技术的国内外发展现状
齿轮传动作为机械传动的主要形式和机器结构的基本部件,随着科学技术的发展,齿轮的传动装置朝着大功率、小体积和高寿命方向发展,这就对齿轮的承载能力、使用寿命、制造精度等方面提出了越来越高的要求。
为了满足这些要求,硬齿面齿轮获得越来越广泛的应用。
而硬齿面齿轮的精加工则成为齿轮加工技术发展的重点。
伴随着新型磨料和刀具材料以及相关技术和设备的发展,也随之产生了对硬齿面齿轮精加工的多种方法。
传统上多采用普通磨齿法、珩齿法。
近年来,在汽车行业大量生产中,主要采用蜗杆砂轮磨齿机磨齿,它是磨齿工艺中效率较高的,同时为了提高硬齿面齿轮的加工效率,满足各种硬齿面加工的需要,许多国家致力于各种切削方法的研究以实现硬齿面的高效加工。
迄今为止,用硬质合金刀具进行硬齿面的滚齿、插齿、剃齿等均有了很大的成效,从工艺上保证了淬硬齿轮广泛应用的可能性,尤其适用于中小批生产规模的机械制造工厂,可取得投资小,见效快,获得较高的技术、经济效益的效果。
硬齿面珩齿加工能加工
级精度的齿轮,不仅能加工淬硬的直齿、斜齿、圆柱齿轮,而且能纠正齿轮预加工时的各项误差,常用于精密和高精密齿轮的加工。
硬齿面滚齿加工广泛用于模数为
齿面硬度为
各种硬齿面圆柱齿轮的半精滚和精滚加工,由于滚齿加工能有效的纠正热处理变形,使齿轮恢复到热前精度,因此,可用于加工
级精度齿轮。
目前,标准的插齿刀只能用于加工中硬度齿面的齿轮。
硬齿面插齿刀的研制,国外起步较早,德、日、前苏联等国早在70年代就开始此项目的研究,先已进入应用阶段。
国内开始于80年代中期,目前正处于研制阶段,并已取得了显著成果。
如内蒙古第一机械制造厂采用758刀片制造的压配式插齿刀(采用平前刀面)加工硬度HRC60的齿轮(18CrNi4A)达到8级精度;成都工具研究所用AA级硬质合金插齿刀加工HRC45
62的硬齿面齿轮,加工精度可达6
7级(GB179-83),表达粗糙度达到
Ra0.4;瑞士MAAG公司研究的硬齿面梳齿法,可加工m6
m50,硬齿面硬度小于HRC65的齿轮,精度可达5
6级(DIN3962),与磨齿相比,加工时间可减少30%
40%。
但这些插齿刀突出的问题是极易崩刃,寿命较短,从而导致硬质合金插齿刀难以在生产中推广应用,硬质合金材料效用难以充分发挥。
大圆周进给量插齿方法的开发成功使插齿技术得到了重要进展。
采用大圆周进给插削齿轮时,插齿刀的切削负荷比滚齿加工大的多。
切削速度超过50m/min,圆周进给量增大,插削出的切屑变窄变厚,引起刀具磨损状态的变化。
前刀面上磨损形成的月牙洼的深度减小,月牙洼最深处离刀刃较远,磨损区沿整个刀刃均匀分布。
由于切屑变厚,容易发生磨损,但插齿的啮出侧刃刃部的磨损有所减少;同时由于单个刀刃的切削面积为传统插齿方法的1.5倍以上,切削负荷集中于顶刃,容易发生由热冲击和切削应力集中造成的刀具破损。
前刀面磨损造成的月牙洼虽然变浅,但磨损区的材料软化却深入到刀具材料内部,要注意在刀具重磨时将软化层除去。
采用CAE技术在切削负荷、应力预测、刀具材料选择、热处理方法等方面进行分析,找出对策,就能延长刀具寿命。
CNC技术应用于插齿机后,生产率和质量大大提高,微电子技术的广泛发展使机床在技术上领先于刀具,加工能力超过了原有刀具的承受能力。
因此如何在刀具上进行改革迎头赶上CNC机床的发展,成为齿轮刀具界的一个重要使命。
由于硬齿面插齿工艺在齿轮加工中的独特地位,随着机械工业的发展,硬齿面插齿刀的研制将越来越受到齿轮制造业的重视。
1.2插齿刀技术的发展
近年来,由于机床设计的改进和技术的发展,在生产中采用新型的高速或CNC高速插齿机床己成为一种趋势。
在一些工业发达的国家,如德、美、日、英等国,已得到较为普遍的应用,插齿生产的效率和精度都在逐步提高。
为了充分发挥现代机床的效能,开发和制造与之适应的新型插齿刀具,己成为刀具研究和生产领域面临的重要课题之一。
为了发挥以车削加工中心和镗铣类加工中心为代表的数控加工技术的优势,提高加工效率,对复杂零件的加工要求在一次装夹中进行多工序的集中加工,并淡化传统的车、铣、镗、螺纹加工等不同切削工艺的界限,是当前提高数控机床效率、加快产品开发的有效途径。
为此,这也对刀具提出了多功能的新要求,要求一种刀具能完成零件不同工序的加工,减少换刀次数,节省换刀时间,以减少刀具的数量和库存量,有利于管理和降低制造成本。
较典型的有多功能车刀、铣刀、镗铣刀、钻铣刀、螺纹-倒角等刀具。
与此同时,在批量生产线上,使用针对工艺需要开发的专用刀具或智能刀具,可以提高加工效率和精度,减少投资。
有的专用刀具可将零件的加工时间降至原来的1/10以下,效果十分显著。
插齿刀的发展主要在以下三个方面进行:
刀具材料、刀具结构和刀具几何参数改进。
1.2.1涂层技术的开发应用
刀具涂层技术自从问世以来,对刀具性能的改善和加工技术的进步起着非常重要的作用,涂层刀具已经成为现代刀具的标志,在刀具中的比例已超过50%。
在21世纪初,涂层刀具的比例将进一步增加,有望在技术上突破CBN涂层技术,并且实用化,使CBN的优良性能在更多的刀具和切削加工中得到应用,甚至精密复杂刀具和成形刀具,这将全面提高加工黑色金属的切削水平。
此外,纳米级超薄、超多层涂层和氮化碳等新型涂层材料的开发应用速度将加快,涂层将成为改善刀具性能的主要途径。
1.3插齿刀变位系数的限制因素
设计插齿刀时合理选择变位系数是一项重要工作。
新插齿刀应尽量采用大的变位系数X0,这是因为:
(1)增加X0值使插齿刀可刃磨次数增多,增加插齿刀的使用寿命;
(2)插齿刀X0值大时顶圆出侧刃前角大,加工出的齿轮表面质量好。
但插齿刀变位系数X0的增加也受到限制:
(1)插齿刀齿顶将变尖,而耐用度降低;
(2)用变位量打的插齿刀加工出的齿轮容易发生过度曲线干涉。
设计插齿刀时应在这两限制条件允许的情况下,选用最大的变位系数(X0)max。
使用插齿刀时要求能多磨几次,变位系数达到最小值。
(X0)min受到下列因素的限制:
(1)插齿刀刀齿强度的限制,刀齿刃磨后变薄强度下降;
(2)被切齿轮根切的限制(当被切齿轮较小时);
(3)被切齿轮顶切的限制(当插齿刀齿数较少和齿轮齿数较多时)。
计算时根据插齿刀用到强度极限时的(X0)min校验根切和顶切是否发生。
设计和使用插齿刀时,必须考虑上面几个限制因素,保证加工出合格的齿轮。
1.3.1内插齿刀的最大变位系数(X0)max的限制因素
(1)刀齿齿顶变尖;
(2)插内齿轮时的切入顶切;
(3)插内齿轮时发生负啮合角;
(4)被加工齿轮的过渡曲线干涉。
对于标准的内插齿刀,确定(X0)max主要是根据齿顶变尖和被加工齿轮过渡曲线干涉的限制。
其他限制条件是使用插齿刀的校验项目。
1.3.2内插齿刀的最小变位系数(X0)min的限制因素
(1)插齿时内齿轮齿顶的干涉顶切;
(2)插齿刀本身的根切;
(3)插齿刀齿形有效渐开线长度的减小。
由于内插齿刀一般齿数都较少,所以插齿刀本身的根切和有效渐开线齿形的长度的减小,常常成为限制插齿刀最小变位系数(X0)min的主要因素。
切齿时的齿顶干涉顶切,可作为验算项目。
插齿刀最小变位系数(X0)min也受到刀齿强度的限制,内插齿刀的允许最小刃磨厚度Bmin可参考外插齿刀的数值。
一般情况因插内齿轮的限制因素较多,往往没有用到强度极限,就受其他条件限制而不能继续使用,特别是在插齿刀齿数较少时。
1.4本课题研究的主要内容
刀具在切削过程中将逐渐产生磨损,当磨损量达到一定程度时,可以明显地发现切削力加大,切削温度上升,切屑颜色改变,甚至产生振动。
同时,工件尺寸可能会超出公差范围,已加工表面质量明显恶化。
有时刀具也可能在切削过程中会突然损坏而失效,造成刀具破损。
刀具的磨损、破损及其使用寿命关系到切削加工的效率、质量和成本,因此它是切削加工中极为重要的问题之一。
因此有必要对插齿刀进行三维参数化实体建模,并在保证一定精度的前提下,对实体模型进行有限元分析以了解刀具切削过程中应力的分布及其对刀具的影响。
本文主要研究内容:
(1)完成m=5mm\α=25°\
=0.0332精插齿直齿硬质合金插齿刀设计;
(2)利用CATIA软件对复杂刀具建模,重点曲面建模;
(3)根据插齿加工切削用量及切削力计算经验公式对切削力进行计算,利用CATIA软件的工程分析模块对硬质合金插齿刀进行有限元分析。
分析刀具切削过程中应力的分布及其对刀具的影响。
第2章硬质合金插齿刀的建模
2.1硬质面插齿刀的构形理论
插齿刀就像一个磨有前、后角而形成切削刃的齿轮,它是根据展成原理与被加工齿轮啮合来插制齿轮的。
标准插齿刀的主要技术特征是其前刀面为圆锥面,使顶刃和侧刃形成径向前角,即切深剖面前角γp。
齿侧表面是渐开螺旋面形成侧刃后角αc,两侧齿面螺旋角相等但螺旋方向相反。
顶刃后刀面亦为一圆锥面,形成顶刃后角αp。
插齿刀切削齿轮时,切削刃运动轨迹形成一个齿轮,称为产形齿轮,直齿插齿刀切削刃在端面的投影就是产形轮的端面齿形。
要加工出正确的渐开线齿形齿轮,和它共轭的产形齿轮齿形必须是渐开线,故插齿刀切削刃在端面的投影必须是渐开线时插齿刀才没有构形误差(也称齿形设计误差)。
但由于插齿刀有前角和后角,这必将引起构形误差。
如果径向前角γp=0,插齿刀端剖面中的齿形是渐开线,没有构形误差。
对于一般的高速钢插齿刀,其前刀面常常设计成γp>0°的圆锥面;对于硬质合金插齿刀,为提高插齿刀的抗崩刃能力,其前刀面须设计成γp<0°的圆锥面,它们和后刀面--渐开螺旋面的交线(即侧刃)在端面中的投影已不是渐开线,即存在构形误差。
2.2插齿刀的具体设计参数
本课题设计的是直齿插齿刀,根据指导教师所给出的相关数据,根据《复杂刀具设计手册》可算得其它的相关参数。
具体设计参数见表2-1、表2-2、表2-3.表2-4
表2-1热前插齿刀模数M=4
序号
计算项目
符号
计算公式及依据
计算结果
插齿刀基本参数
1
模数
mn
选取齿轮的标准模数
4
2
分圆压力角
α
为被切齿轮的分圆压力角
20°
3
齿数
zo
建议根据模数按标准插齿刀来选取。
如需特殊设计,须保证能在齿轮磨床上磨削,并与被切齿轮齿数无公约数
25
4
侧刃所在圆锥面底角
可取
≤-5°
5°
5
齿顶后角
α
通常取标准值6°
6°
序号
计算项目
符号*
计算公式及依据
计算结果
6
齿高系数
ho
正常齿取1,短齿取0.8
0.8
7
齿顶间隙系数
co′
根据被加工四排齿圈要求,选取co′=0.1368(标准齿轮通常取0.25或0.3)
0.1368
8
齿根间隙系数
co″
根据被加工四排齿圈要求,选取co″=0.3732(标准齿轮通常取co″=co′)
0.3732
9
插齿刀变位系数
根据被加工的四排齿圈的要求,计算得插齿刀变位系数X=0.0332
0.538
10
原始截面到侧刃距离
bb
20.475
11
厚度
B
根据插齿刀的结构工艺取B=39.8mm
40
12
分圆直径
d
d=mzo
100
13
基圆半径
rb
rb=dcosα/2
46.985
原始截面上的齿形尺寸
14
齿顶高
ha
6.22
15
分圆弧齿厚
s
s=πm/2
6.2832
16
分圆齿距
po
po=πm
12.5664
前端面上的齿形尺寸
17
齿顶高
hoa
6.81
18
齿根高
hof
2.85
19
齿顶圆半径
roa
56.81
20
齿根圆半径
rof
47.15
插齿刀其它参数
21
修正后齿形角
αo
20.1707°
22
基圆螺旋角
βob
2.0756°
23
分圆螺旋角
βo
2.2111°
24
基圆半径
rob
rob=dcosα0/2
46.933
25
前端面分圆弧齿厚
so
7.85
序号
计算项目
符号
计算公式及依据
计算结果
26
基圆齿厚
sob
半径ri处的圆弧齿厚公式:
其中:
8.7335
27
顶圆齿厚
soa
其中:
2.3319
28
刀片厚度
C
使胶缝远离切削刃热源,刀片不宜太薄
29
其它结构尺寸
-
按标准插齿刀选取
结果见图纸
在距前端面2.5mm处进行齿形检测,计算检测用参数
30
测量始点压力角
αoi
其中:
hoo*—被切齿轮的原始齿条齿顶高系数,一般取1
12.8644°
31
测量终点压力角
32.2860°
32
测量始点曲率半径
ρmin
12.875
33
测量终点曲率半径
ρmax
31.446
34
前端面公法线长度
Wn
n—测量公法线时的跨齿数,取n=5
32.3787
表2-2热前插齿刀模数M=5
序号
计算项目
符号
计算公式及依据
计算结果
插齿刀基本参数
1
模数
mn
选取齿轮的标准模数
5
2
分圆压力角
α
为被切齿轮的分圆压力角
25°
序号
计算项目
符号
计算公式及依据
计算结果
3
齿数
zo
建议根据模数按标准插齿刀来选取。
如需特殊设计,须保证能在齿轮磨床上磨削,并与被切齿轮齿数无公约数
21
4
侧刃所在圆锥面底角
可取
≤-5°
5°
5
齿顶后角
αp
通常取标准值6°
6°
6
齿高系数
ho*
正常齿取1,短齿取0.8
1
7
齿顶间隙系数
co′
根据被加工四排齿圈要求,选取co′=0.1368(标准齿轮通常取0.25或0.3)
0.1368
8
齿根间隙系数
co″
根据被加工四排齿圈要求,选取co″=0.3732(标准齿轮通常取co″=co′)
0.3732
9
插齿刀变位系数
根据被加工的四排齿圈的要求,计算得插齿刀变位系数X=0.0332
0.0332
10
原始截面到侧刃距离
bb
1.58
11
厚度
B
根据插齿刀的结构工艺取B=39.8mm
17
12
分圆直径
d
d=mzo
105
13
基圆半径
rb
rb=dcosα/2
47.58
原始截面上的齿形尺寸
14
齿顶高
ha
6.2
15
分圆弧齿厚
s
s=πm/2
7.8540
16
分圆齿距
po
po=πm
15.7080
前端面上的齿形尺寸
17
齿顶高
hoa
6.2665
18
齿根高
hof
6.0185
19
齿顶圆半径
roa
58.7
20
齿根圆半径
rof
46.415
插齿刀其它参数
21
修正后齿形角
αo
25.2033°
22
基圆螺旋角
βob
2.5627°
序号
计算项目
符号
计算公式及依据
23
分圆螺旋角
βo
2.7803°
24
基圆半径
rob
rob=dcosα0/2
47.6584
25
前端面分圆弧齿厚
so
8.3923
26
基圆齿厚
sob
半径ri处的圆弧齿厚公式:
其中:
10.3977
27
顶圆齿厚
soa
其中:
1.3502
28
刀片厚度
C
使胶缝远离切削刃热源,刀片不宜太薄
29
其它结构尺寸
按标准插齿刀选取
结果见图纸
在距前端面2.5mm处进行齿形检测,计算检测用参数
30
测量始点压力角
αoi
其中:
hoo*—被切齿轮的原始齿条齿顶高系数,一般取1
12.8396°
31
测量终点压力角
35.4501°
32
测量始点曲率半径
ρmin
10.8623
33
测量终点曲率径
ρmax
33.9318
34
前端面公法线长度
Wn
n—测量公法线时的跨齿数,取n=5
38.9222
表2-3热后插齿刀模数M=4
序号
计算项目
符号
计算公式及依据
计算结果
插齿刀基本参数
1
模数
mn
选取齿轮的标准模数
4
2
分圆压力角
α
为被切齿轮的分圆压力角
20°
3
齿数
zo
建议根据模数按标准插齿刀来选取。
如需特殊设计,须保证能在齿轮磨床上磨削,并与被切齿轮齿数无公约数
25
4
侧刃所在圆锥面底角
可取
≤-5°
-5°
5
齿顶后角
αp
通常取标准值6°
6°
6
齿高系数
ho*
正常齿取1,短齿取0.8
0.8
7
齿顶间隙系数
co′
根据被加工四排齿圈要求,选取co′=0.1368(标准齿轮通常取0.25或0.3)
0.1368
8
齿根