生产计划课程设计.docx
《生产计划课程设计.docx》由会员分享,可在线阅读,更多相关《生产计划课程设计.docx(36页珍藏版)》请在冰豆网上搜索。
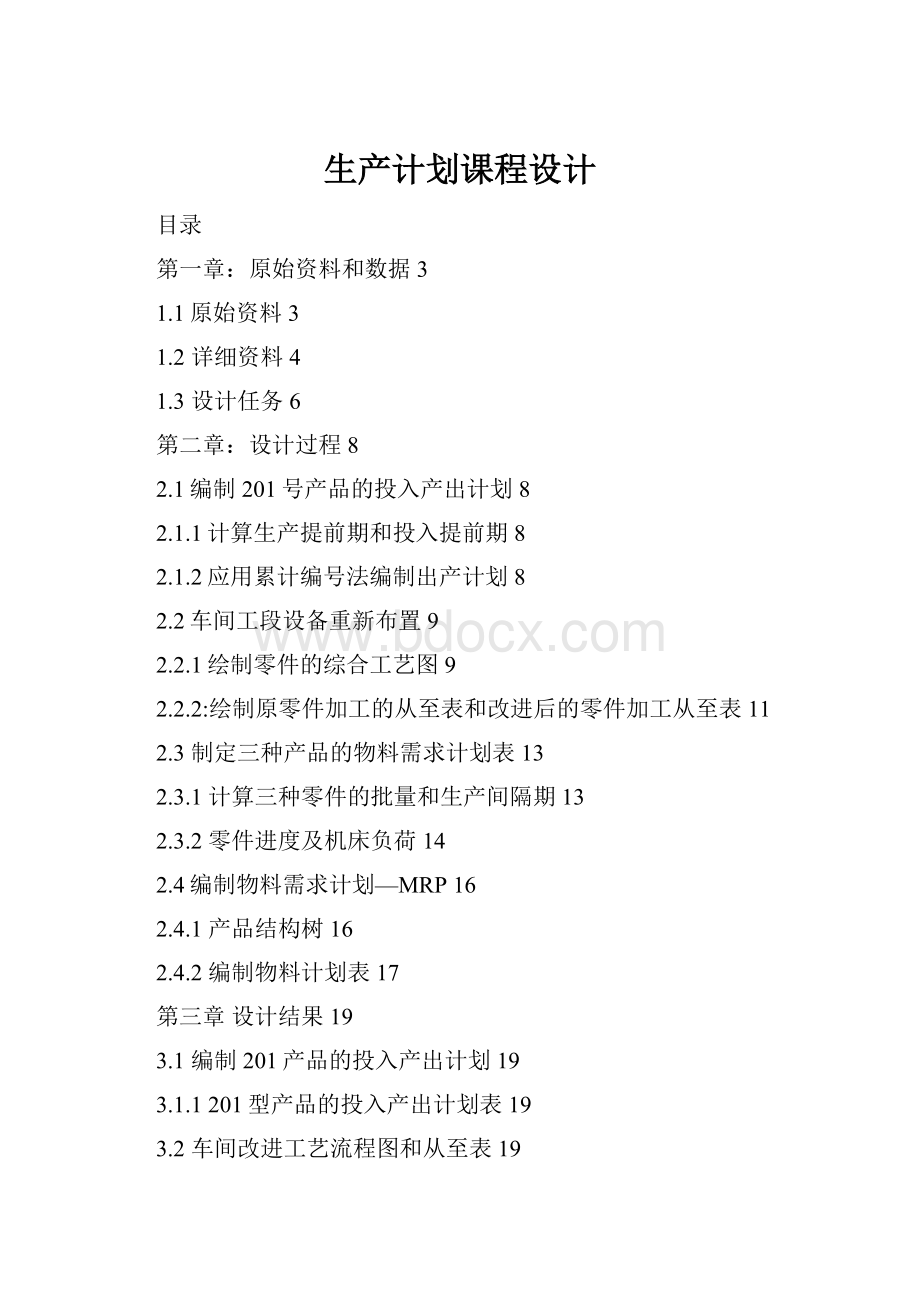
生产计划课程设计
目录
第一章:
原始资料和数据3
1.1原始资料3
1.2详细资料4
1.3设计任务6
第二章:
设计过程8
2.1编制201号产品的投入产出计划8
2.1.1计算生产提前期和投入提前期8
2.1.2应用累计编号法编制出产计划8
2.2车间工段设备重新布置9
2.2.1绘制零件的综合工艺图9
2.2.2:
绘制原零件加工的从至表和改进后的零件加工从至表11
2.3制定三种产品的物料需求计划表13
2.3.1计算三种零件的批量和生产间隔期13
2.3.2零件进度及机床负荷14
2.4编制物料需求计划—MRP16
2.4.1产品结构树16
2.4.2编制物料计划表17
第三章设计结果19
3.1编制201产品的投入产出计划19
3.1.1201型产品的投入产出计划表19
3.2车间改进工艺流程图和从至表19
3.2.1零件移动距离计算表19
3.2.2原始的和改进的从至表20
3.2.3原始的和改进后的工艺流程图21
3.3零件进度和机床负荷表24
3.3.1零件进度和机床符合进度表24
3.4物料需求计划表26
参考文献27
生产计划课程设计
第一章:
原始资料和数据
1.1原始资料
该公司主要产品201型机械的有关资料如下:
⑴该产品2008年度各月出产计划如表1所示:
表1201型产品2008年度各月出产计划
月份
1
2
3
4
5
6
7
8
9
10
11
12
产品出产量
方案1
25
26
19
26
38
29
25
30
30
30
30
29
方案2
25
26
19
26
38
29
25
26
19
26
38
29
方案3
25
30
30
30
30
29
25
30
30
30
30
29
方案4
30
30
30
30
30
30
30
30
30
30
30
30
方案5
30
30
30
30
30
30
25
25
25
25
25
25
方案6
26
30
28
30
30
29
25
26
19
26
38
29
方案7
25
25
25
25
25
25
30
30
30
30
30
30
方案8
26
38
29
25
30
30
25
26
20
26
38
29
方案9
25
25
25
25
25
25
25
25
25
25
25
25
方案10
28
30
30
32
30
29
26
26
19
26
38
29
⑵该产品的加工工艺流程及各环节的生产周期如图1所示:
240
225
210
195
180
165
150
135
120
105
90
75
60
45
30
15
铸
件
90
冷
作
90
装
配
60
锻
件
90
油漆
30
冲
压
90
一
金
工
90
二
金
工
90
图1201型产品加工工艺流程及各环节生产周期
平均日产量的求法可用投入(出产)期起到该批产品出产期为止的各月产量的总和除以投入(出产)提前期。
注:
平均日产量=从投入(出产)期起到该批产品出产期为止的各月产量的总和/投入(出产)提前期
⑶该产品的投入批量为月批,投入间隔期为30天,每月按标准日历时间30天计算,暂不考虑保险期,上年度出产累计编号为2210号。
2.承担该产品生产任务的加工车间设备的有关资料:
⑴该车间一工段原有设备的布置顺序(图2);
⑵该工段生产该产品零件的工艺路线(图3)。
3.机加工车间主要产品甲、乙、丙三种零件的有关资料:
⑴三种零件在主要工序上的加工时间(表2);
⑵三种零件在各道工序的生产周期(表3);
⑶三种零件的月产量分别为2000,3000和1000件,每月工作25天,两班制生产,每班8小时,设备损失系数为0.05。
4.201型产品代表零件的有关资料:
⑴201型系列产品A、B结构层次图(图4);
⑵A、B产品零部件其它有关资料(表4)。
1.2详细资料
该公司某机器厂加工车间一工段承担机加工生产任务,最近由于生产任务的改变,零件在各工序之间的流转也发生了变化,现有设备的平面布置不合理,零件流转路线长,因此决定调整现有设备的平面布置,使零件在各设备之间流转的距离最短,原有设备的布置顺序和工段所生产零件的工艺路线如图2和图3所示:
A
B
C
D
E
F
G
H
I
J
A:
毛坯库;B:
铣床;C:
1号车床;D:
钻床;E:
刨床;F:
磨床;G:
2号车床;H:
锯床;
I:
钳台;J:
检验。
图2原有设备布置
序号
零件号
工艺流程
1
A1008
A—H—C—D—B—I—J
2
A1009
A—G—F—I—J
3
A1203
A—H—C—G—F—I—J
4
A1204
A—H—C—B—D—I—J
5
A1205
A—D—C—D—G—B—G—F—I—J
6
A1310
A—G—F—I—J
7
A1312
A—E—B—I—J
8
A1313
A—G—I—J
9
B2101
A—H—C—D—G—F—B—I—J
10
B2103
A—I—E—B—J
11
B2105
A—C—D—I—J
12
B2106
A—I—C—J
13
C1108
A—C—B—I—J
14
C1109
A—I—C—I—J
图3工艺流程路线图
二、此机加工车间固定生产甲、乙、丙三种零件,该三种零件在主要工序上的工时间如下表2所示:
(δ=0.05)
表2零件在主要工序上的加工时间
零件名称
月产量
主要工序
单件时间
准备与结束时间
甲
2000
3分钟
1小时
乙
3000
4分钟
2小时
丙
1000
3分钟
0.5小时
三种零件各道工序的生产周期如下表3所示:
表3工序生产周期
零件
工序1
工序2
工序3
工序4
工序5
名称
生产周期(天)
名称
生产周期(天)
名称
生产周期(天)
名称
生产周期(天)
名称
生产周期(天)
甲
铣
1.5
车
3
钻
3
磨
1.5
钳
2
乙
车
1
钳
2.5
磨
3.5
铣
2.5
刨
4
丙
铣
1
车
1
钳
1
刨
1
钳
3
三、201型系列产品中,主要生产A产品,A产品分别由C、D、E、F、G、H等零部配件装配而成,目前的存货量、订购时的交货期限如下表4所示:
表4A、B、C、D目前的存货量、订购时的交货期限
项目
存货量
订购交货期
项目
存货量
订购交货期
A
20
2周
F
2000
2周
C
30
1周
G
600
4周
D
40
1周
H
400
3周
E
3000
2周
该产品已与用户签订交货合同。
产品A、B在不同方案下的交货量如下:
方案
1
2
3
4
5
6
7
8
9
10
产品A
第8周
600
400
500
400
300
300
400
200
300
200
第12周
400
600
500
400
600
300
300
300
200
200
产品B
第9周
400
500
400
500
300
400
300
200
300
500
第12周
500
400
400
300
300
300
400
300
200
500
1.3设计任务
1.采用累计编号法编制201型产品的投入产出计划(全年):
⑴计算全年各月份的出产投入累计编号;
⑵计算各车间的出产投入累计编号;
⑶编制各车间投入产出计划表(填入附表1中)。
2.根据现有的任务对加工车间一工段设备重新进行布置:
⑴编制零件的综合工艺路线图;
⑵绘出原零件加工的从至表和改进后零件从至表;
⑶计算并绘制出零件移动总距离计算表;
⑷绘出改进后的设备布置图。
3.编制机加工车间甲、乙、丙三种主要产品(零件)的生产作业计划:
⑴计算出三种零件的标准批量和生产间隔期;
⑵编制三种零件各道工序的标准计划。
要求绘制出零件工序进度表和机床负荷进度表(钳工按两个小组安排,其余工种为一个小组)(附表2)。
4.根据图4和表4的资料,编制产品A的物料需求计划——MRP。
第二章:
设计过程
2.1编制201号产品的投入产出计划
2.1.1计算生产提前期和投入提前期
为了保证生产的顺利进行,在投入生产之前要考虑各个生产车间的需求时间,为了保证每道工序都按时进行,必须保证每个车间需要的半成品或者零部件即使供给,因此需要考虑生产过程中各个零部件的生产提前期和投入提前期。
理论上还应该加上保险期。
本题为了简化工作量不考虑这一因素。
应用以下公式结合图1可以计算出各个工序的生产提前期和投入提前期。
计算公式如下:
某工序投入提前期=某工序出产提前期+该工序生产周期
某工序出产提前期=该工序的下一道投入提前期+该工序生产周期
由于转配工序是整个过程的最后一道工序,所以它的出产提前期是零(因为只要在计划的那一天开始装配就可以了),由图1可以知道装配的生产周期是60天,因此可以计算出装配的投入提前期:
装配工序投入提前期=该工序出产提前期+该工序生产周期
=0+60
=60
同理可以计算出其他工序的投入提前期和出产提前期,汇总结果如下表:
表5生产和投入提前期
车间时间
生产周期
出产提前期
投入提前期
铸件
90
150
240
锻件
90
150
240
油漆
30
150
180
冷作
90
60
150
冲压
90
60
150
一金工
90
60
150
二金工
90
60
150
装配
60
0
60
2.1.2应用累计编号法编制出产计划
由于累计编号法的公式是:
某环节某月的投入(出产)累计编号数目=装配出产累计编号+该环节投入(出产)提前期×平均日产量。
根据以上方法介绍可以计算出各个工序的各个月份的出产计划例如铸件车间一月份的出产计划
出产计划=(2210+25)+(25/30)×0=2235
投入计划=(2210+25)+(25/30)×60
=2285
该方法计算我们可以计算出各个车间工序的投入和产出计划量(用的是累计编号表示),由于每道工序需要生产周期,并且考虑到各个工序的投入提前期和出产提前期,以及它们的生产周期,所以每道工序的计划投入期要比出产期早一个生产周期。
为了保持制定的计划更符合实际,所以采用倒退法,即知道了出产计划,再利用生产周期来推算出投入计划。
这样能够更好的组织生产。
而不利用计算出的投入计划(因为计算出的和实际推算出来的差距比较大)。
最终得到的结果如下表所示:
表6产品投入出产计划表
月份
1
2
3
4
5
6
7
8
9
10
11
12
本月计划任务
2261
2180
2306
2344
2373
2398
2428
2458
2488
2518
2547
本月出产累计
2235
2261
2280
2306
2344
2373
2398
2428
2458
2488
2518
2547
铸件
投入
2405
2431
2469
2498
2523
出产
2360
2386
2405
2431
2469
2498
2523
锻件
投入
2405
2431
2469
2498
2523
出产
2360
2386
2405
2431
2469
2498
2523
冷作
投入
2330
2356
2394
2423
2448
2478
2408
2538
出产
2285
2311
2330
2356
2394
2423
2448
2478
2508
2538
油漆
投入
2360
2386
2405
2431
2469
2498
2523
出产
2360
2386
2405
2431
2469
2498
2523
冲压
投入
2330
2356
2394
2423
2448
2478
2508
2538
出产
2285
2311
2330
2356
2394
2423
2448
2478
2508
2538
1金工
投入
2330
2356
2394
2423
2448
2478
2408
2538
出产
2285
2311
2330
2356
2394
2423
2448
2478
2508
2538
2金工
投入
2330
2356
2394
2423
2448
2478
2408
2538
出产
2285
2311
2330
2356
2394
2423
2448
2478
2508
2538
装配
投入
2280
2306
2344
2373
2398
2428
2458
2488
2518
2547
出产
2235
2261
2280
2306
2344
2373
2398
2428
2458
2488
2518
2547
2.2车间工段设备重新布置
2.2.1绘制零件的综合工艺图
零件的综合工艺图是反映零件的各个工序在车间机床上进行加工的顺序流程,因此我们结合原有设备布局图和工艺流程路线图可以绘制出零件的综合工艺图。
A
B
C
D
E
F
G
H
I
J
A:
毛坯库;B:
铣床;C:
1号车床;D:
钻床;E:
刨床;F:
磨床;G:
2号车床;H:
锯床;I:
钳台;J:
检验
最终绘制出的工艺路线流程图如下所示
零件号
A
毛坯库
B
铣床
C
一号车车
D
钻床
E
刨床
F
磨床
G
二号磨床
H
锯床
I
钳台
J
检查
A1008
A1009
A1203
A1204
A1205
A1310
A1312
A1313
B2101
B2103
B2105
B2106
C1108
C1109
图4原始工艺流程路线图
2.2.2:
绘制原零件加工的从至表和改进后的零件加工从至表
表7从至次数表
从至
次数
从至
次数
A-C
2
C-J
1
A-I
3
C-I
1
A-G
3
D-B
1
A-H
4
D-C
1
A-D
1
D-G
2
A-E
1
D-I
2
B-D
1
E-B
2
B-G
1
F-I
1
B-I
4
F-B
1
B-J
1
G-F
5
C-D
4
G-B
1
C-B
2
G-I
1
C-G
1
H-C
4
H-C
4
I-E
1
I-C
2
I-J
12
对于本题,我们假设车间设备是均匀布局的。
所以我们可以在从至表的表格里用零件在两个设备中移动的间隔数代表其移动距离。
在本题中我们假设每一个单元格距离从至表对角线的距离是一,我们就可以用从至表单元格中的数值与其到对角线的距离相乘即可得到最终移动的总距离。
在改进的过程中应该使从至次数最多的两台机床,应该尽可能的靠近。
有对从至表的分析可以知道这需要从至表中越大的数字应该靠近对象线。
2.2.3绘制改进后的零件工艺流程图及机床布局
优化后的机床布局减小了总的移动距离,所以我们可以依据优化后的机床排布重新绘制零件的工艺流程图,同时给机床以新的布局,如下图所示:
零件号
A
毛坯库
H
锯床
C
一号车车
E
刨床
G
二
号
磨
床
D
钻床
F
磨
床
B
铣
床
I
钳台
J
检查
A1008
A1009
A1203
A1204
A1205
A1310
A1312
A1313
B2101
B2103
B2105
B2106
C1108
C1109
图5重新布置机床后工艺流程路线图
A
H
C
E
G
D
F
B
I
J
A:
毛坯库;B:
铣床;C:
1号车床;D:
钻床;E:
刨床;F:
磨床;G:
2号车床;H:
锯床;I:
钳台;J:
检验。
图6改进后设备布置
2.3制定三种产品的物料需求计划表
2.3.1计算三种零件的批量和生产间隔期
(1)生产批量
计算最小批量的公式是
(δ=0.05)
由原始数据和公式可以得到甲乙丙三种零件的各自最小批量,如下所示:
Q甲=60/(3×0.05)=400件
Q乙=120/(4×0.05)=600件
Q丙=30/(3×0.05)=200件
(2)生产批次
有公式批次N=月产量/批量,结合表中的数据同样可以计算出各自的批次如下:
N甲=月产量/批量=2000/400=5
N甲=月产量/批量=3000/6000=5
N甲=月产量/批量=1000/200=5
(3)生产间隔期
生产间隔期公式如下:
生产间隔期R=批量Q/平均日常量q
平均日常量q=月产量/月工作天数
所以结合数据可以求得三种零件的平均日产量和生产间隔期:
q甲=2000/25=80件R甲=400/80=5天
q乙=3000/25=120q乙=600/120=5
q丙=1000/25=40q丙=200/40=5
2.3.2零件进度及机床负荷
由于车间机床数量有限,为了满足不同零件相同工艺的生产要求,我们必须考虑不同零件间相同工艺的进度,合理安排生产时间,才能保证不同零件的相同工艺不发生冲突。
注:
在本题中由于题中告诉了钳工按两个小组进行安排,我在安排的时候是将甲乙零件的钳工工序安排在一个小组里,所以他们的进度不可重合,但是丙的可以和他们重合,而丙中的两道钻工序是不可以重合的,因为它单作为一个工序。
结合生产批量和生产间隔期可以画出零件进度及机床符合表。
三种零件生产间隔期和生产批量
零件
生产间隔期
生产批量
甲
5
5
乙
5
5
丙
5
5
表8零件工序进度表和机床负荷平衡表
零件
工序
周期
工作日
1
2
3
4
5
6
7
8
9
10
11
12
13
14
15
16
17
18
19
20
21
22
23
24
25
甲
铣
1.5
车
3
钻
3
磨
1.5
钳
2
乙
车
1
钳
2.5
磨
3.5
铣
2.5
刨
4
丙
铣
1
车
1
钳