基于PLC的啤酒发酵自动控制系统课程设计.docx
《基于PLC的啤酒发酵自动控制系统课程设计.docx》由会员分享,可在线阅读,更多相关《基于PLC的啤酒发酵自动控制系统课程设计.docx(28页珍藏版)》请在冰豆网上搜索。
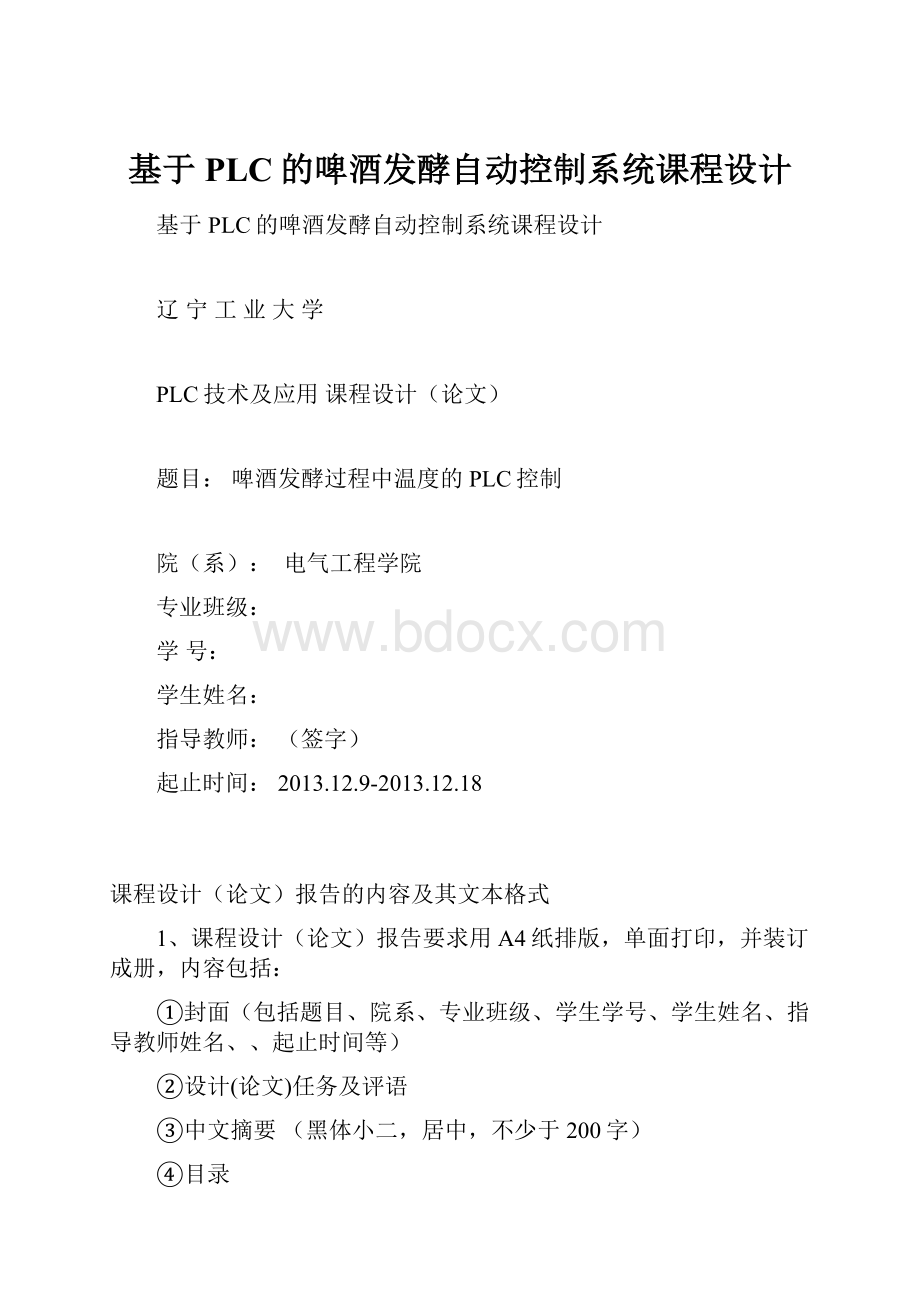
基于PLC的啤酒发酵自动控制系统课程设计
基于PLC的啤酒发酵自动控制系统课程设计
辽宁工业大学
PLC技术及应用课程设计(论文)
题目:
啤酒发酵过程中温度的PLC控制
院(系):
电气工程学院
专业班级:
学号:
学生姓名:
指导教师:
(签字)
起止时间:
2013.12.9-2013.12.18
课程设计(论文)报告的内容及其文本格式
1、课程设计(论文)报告要求用A4纸排版,单面打印,并装订成册,内容包括:
①封面(包括题目、院系、专业班级、学生学号、学生姓名、指导教师姓名、、起止时间等)
②设计(论文)任务及评语
③中文摘要(黑体小二,居中,不少于200字)
④目录
⑤正文(设计计算说明书、研究报告、研究论文等)
⑥参考文献
2、课程设计(论文)正文参考字数:
2000字
周数。
3、封面格式
4、设计(论文)任务及评语格式
5、目录格式
①标题“目录”(小二号、黑体、居中)
②章标题(四号字、黑体、居左)
③节标题(小四号字、宋体)
④页码(小四号字、宋体、居右)
6、正文格式
①页边距:
上2.5cm,下2.5cm,左3cm,右2.5cm,页眉1.5cm,页脚1.75cm,左侧装订;
②字体:
一级标题,小二号字、黑体、居中;二级标题,黑体小三、居左;三级标题,黑体四号;正文文字,小四号字、宋体;
③行距:
20磅行距;
④页码:
底部居中,五号、黑体;
7、参考文献格式
①标题:
“参考文献”,小二,黑体,居中。
②示例:
(五号宋体)
期刊类:
[序号]作者1,作者2,……作者n.文章名.期刊名(版本).出版年,卷次(期次):
页次.
图书类:
[序号]作者1,作者2,……作者n.书名.版本.出版地:
出版社,出版年:
页次.
课程设计(论文)任务及评语
院(系):
电气工程学院教研室:
自动化
学号
学生姓名
专业班级
课程设计(论文)题目
基于Ethernet/IP远程锅炉液位控制系统设计
课程设计(论文)任务
课题完成的功能、设计任务及要求、技术参数
实现功能
以Netlinx网络控制平台为基础,设计锅炉液位控制系统,网络选择Ethernet/IP,通过FlexI/O模块,实现基于Ethernet/IP的液位远程控制。
设计任务及要求
1、确定系统设计方案,画出Ethernet/IP远程FlexI/O的结构图。
2、Ethernet/IP远程FlexI/O液位控制系统硬件设计,包括介质、模块及器件等选择。
3、Ethernet/IP远程FlexI/O硬件组态及软件组态(PID程序)。
4、使用Factorytalkview软件设计显示画面。
5、要求认真独立完成所规定的全部内容;所设计的内容要求正确、合理。
6、按学校规定的格式,撰写、打印设计说明书一份;设计说明书应在4000字以上。
技术参数
1、Ethernet/IP传输速率10Mbps;2、液位高度设定值80cm;3、控制精度
进度计划
1、布置任务,查阅资料,确定系统设计方案(1天)
2、对系统功能进行分析,构建Ethernet/IP远程FlexI/O网络(1天)
3、系统硬件组态及模块选择(3天)
4、系统软件组态及编写功能程序及调试(3天)
5、撰写、打印设计说明书(1天)
6、验收及答辩。
(1天)
指导教师评语及成绩
平时:
论文质量:
答辩:
总成绩:
指导教师签字:
年月日
注:
成绩:
平时20%论文质量60%答辩20%以百分制计算
摘要
啤酒发酵是啤酒生产工艺流程中关键环节之一,本文针对实验室啤酒发酵装置技术装备落后、自动化程度低、产品质量不稳定以及啤酒发酵罐温度所具有的大时滞、强关联、时变、大时间常数和变量的特点,提出了S7-200PLC核心的温度控制系统方案。
在发酵罐中设置上、中和下三个测温点,控制系统对这三个测温点进行循环检测,然后检测到的温度信号送到PLC,由PLC通过具体程序对以上三个信号进行处理,通过本文设定的特殊控制算法决定每层控制阀的开度,从而实现了啤酒发酵罐内部麦汁三层温度的精确控制,进而解决了啤酒发酵罐内部温度控制精度不高的问题,提高了啤酒生产的综合自动化水平.
文中介绍了系统的工艺流程、软件设计。
软件设计包括系统控制的梯形图、温度设定值的计算和电磁阀控制。
该设计编程容易,容易掌握。
该系统满足啤酒生产发酵工艺的技术要求,并兼顾了实用的需求且性能/价格比高、可靠、技术先进,扩展性强,移植性强,具有推广实用价值。
关键词:
啤酒发酵;温度控制;可编程逻辑控制器PLC
第1章绪论1
第2章课程设计的方案2
2.1概述2
2.2控制原理2
2.3啤酒发酵工艺流程3
第3章硬件设计6
3.1PLC的选型6
3.1.1PLC工作原理及功能6
3.1.2PLC的选型6
3.2S7-200主要功能及特点8
3.3控制系统的硬件配置8
3.4文本显示器TD2009
3.5I/O地址分配10
第4章软件设计12
4.1控制系统组成12
4.2程序流程图设计12
4.3PLC功能模块程序设计14
4.4主程序15
4.5模拟量信号采集处理18
4.6温度设定值的计算18
4.7电磁阀控制19
第5章课程设计总结21
参考文献22
第1章绪论
随着我国改革开放现代化建设,人民生活水平不断断提高,啤酒己成为人们的时尚饮品,市场的宠儿,生产直线上升,目前已成为仅次于美国的世界第二大啤酒产销国,令世界啤酒界人士刮目相看。
啤酒生产是一个利用生物加工进行生产的过程,生产周期长,过程参数分散性大,传统操作方式难以保证产品的质量。
近年来,国外的各大啤酒生产厂家纷纷进军中国市场,凭借技术优势与国内的啤酒生产厂家争夺市场份额,虽然我国的啤酒装备配套水平有很大提高,但与国外的主要啤酒生产厂家相比大部分企业技术落后,国内的啤酒行业迫切要求进行技术改造,提高生产率,保证产品质量,以确保在激烈的市场竞争中立于不败之地。
啤酒的发酵过程是在啤酒酵母的参与下,对麦汁的某些组成进行一系列代谢,从而将麦汁风味转变为啤酒风味的过程。
啤酒发酵是啤酒生产工艺流程中关键环节之一,也是一个极其复杂的在发酵罐内发生并释放大量热量的生化放热反应过程。
由于这一过程中麦汁的可酵糖和氨基酸等营养物质被酵母细胞酶分解为乙醇(C2H5OH)和二氧化碳(CO2),同时还产生一系列的发酵副产物,如:
双乙酰、醛、酸、酯等。
这些代谢产物的含量虽然极少,但它们对啤酒质量和口味的影响很大,而这些中间代谢产物的生成取决于发酵温度。
因此发酵过程是否正常和顺利,将直接影响到最终啤酒成品的质量。
比如,发酵过程的温度若发生剧烈变化,不仅会使酵母早期沉淀、衰老、死亡、自溶,造成发酵异常,还直接影响到酵母代谢副产物组成,从而对啤酒酒体与风味,及啤酒胶体稳定性造成危害。
啤酒发酵具有非线性、时间滞后和大惯性等特征,发酵过程的精密控制一直是自动控制领域较难解决的问题之一。
要求发酵液的温度严格按照一定的工艺曲线变化,温度控制精度在±0.5℃范围内,这样的控制精度单凭传统的热工仪表加上手工操作方式是完全不能满足要求的,随着控制领域新技术、新方法的不断涌现,这些问题也在不断地得到改进。
改进啤酒发酵生产过程控制是酿造业技术进步的有效措施,它可以在不增加原材料及动力消耗的前提下,增加产品产量、提高产品质量,同时减轻劳动强度、改善工作条件、提高发酵工艺水平及生产管理水平。
因此,优化啤酒发酵控制应用前景乐观,能产生较大的社会经济效益,具有很大的应用价值。
利用PLC实现啤酒发酵罐温度的自动控制,对提高啤酒发酵温度控制精度,优化啤酒温度控制过程,使用效果好且性能稳定可靠,编程简单,具有非常现实的意义。
第2章
课程设计的方案
2.1概述
啤酒是采用麦芽和水为主要原料,加酒花,经酵母发酵酿制而成的一种含有二氧化碳、气泡的低酒精度饮料。
啤酒生产工艺主要由麦汁制备(俗称糖化)、啤酒发酵、啤酒罐装等工艺流程组成。
发酵过程是啤酒生产中一个非常重要的环节,啤酒发酵是一个复杂的生化过程,这个过程可以理解为把麦汁转化为啤酒的过程,整个发酵过程同样也包含若干个生产工序,如:
麦汁充氧、酵母添加、发酵、过滤、修饰以及酵母扩培等等。
生产周期都在十几天以上,要求发酵液的温度严格按照一定的工艺曲线变化,温度控制精度在±0.5℃范围内如果温度控制偏低,就会使得发酵过程缓慢,影响生产进度;如果温度偏高,又会造成生化参数超出标准,影响啤酒的质量。
啤酒发酵整个过程分为:
麦汁进罐,自然升温,还原双乙酰,降温过程等。
麦汁进料阶段的温度为5~100C,自然升温阶段的温度为20~350C,开始进行主发酵,发酵液直接由糖化车间经管道灌入,初始的温度大约为8摄氏度左右,糖度为10度左右,温度控制开始实施,以保证满罐后发酵液的温度在规定范围内。
发酵液满罐后工人开始测量发酵液的满罐糖度,主发酵阶段结束,发酵进入还原双乙酰阶段,这一阶段要求温度控制在15~200C。
当双乙酰浓度下降到合格标准时,发酵就可以进入降温阶段,分两个阶段按不同的速率降温,此时把所有冷媒阀打开,使发酵液全速降温,降温阶段的温度为-1~120C。
当温度到达1摄氏度以下时发酵进入低温储酒阶段,在低温储酒阶段温度控制在0.5~10摄氏度。
这一阶段主要是让酵母和一些固态物进行充分沉淀并进行回收。
2.2控制原理
啤酒发酵对象的时变性、时滞性及其不确定性,决定了发酵罐控制必须采用特殊的控制算法。
由于每个发酵罐都存在个体的差异,而且在不同的工艺条件下,不同的发酵菌种下,对象特性也不尽相同。
因此很难找到或建立某一确切的数学模型来进行模拟和预测控制。
为节省能源,降低生产成本,并且能够满足控制的要求,发酵罐的温度控制选择了检测发酵罐的上、中、下3段的温度,通过上、中、下3段冷媒进口的两位式电磁阀来实现发酵罐温度控制的方法。
对于采用外部冷媒间接换热方式来控制体积大,惯性大的发酵温度的情况,采用普通的控制方案极易引起大的起调和持续的震荡,很难取得预期的控制效果。
在不同的季节,甚至在不同一季节的不同发酵罐,要求生产不同品种的啤酒,这样就要求每个罐具有各自独立的工艺控制曲线,这不仅要求高精度,高稳定性的控制,还需要控制系统有极大的灵活性。
利用PLC实现发酵罐温度的控制,PLC实现啤酒发酵温度控制的主要任务是接受由发酵罐传来的温度模拟量输入信号,然后与工艺曲线设定温度值进行比较,计算出温度偏差值,再使用简单的PID控制回路计算出电磁阀的开度,对阀门进行控制调节,从而实现对发酵罐温度的控制。
在发酵的过程中,温度在不断的升高,当达到上限温度时,要打开制冷设备,通过酒精在冷却管内循环使罐内的温度降下来。
当发酵温度低于工艺要求的温度时,关闭冷媒,则啤酒按工艺要求继续发酵,发酵罐工艺示意图如图2.1所示:
图2.1啤酒发酵罐工艺示意图
2.3啤酒发酵工艺流程
根据锥形发酵大罐的特性将发酵的全过程分为多个阶段:
麦汁进罐,自然升温,还原双乙酰,一次降温,低温储酒等,各个阶段温度的曲线图如图2.2所示。
oa段为自然升温段,不须外部控制;ab段为主发酵阶段;主酵阶段,典型的控制温度为26℃;bc段为降温逐渐进入后酵,;cd段为后酵阶段,典型控制点16℃;de段为降温进入贮酒阶段,;ef段为贮酒阶段。
啤酒口味和实际要求的不同,啤酒的发酵工艺曲线也就不同,但是对于确定好的啤酒发酵工艺,就应严格按照工艺曲线去控制温度和压力等,这样才能保证啤酒的质量。
发酵温度控制机制
1.自动升温阶段,姜汁满罐酵母自然升温,要控制温度,否则会导致啤酒质量下降。
2.主发酵和双乙酰还原阶段,酵母大量繁殖产生较多热量,当酵母进行无氧呼吸,使罐内中,下部酒液浓度不同,要保持强烈的发酵并均衡的酒液状态,要控制不同部分的温度。
3.降温保温,还原双乙酰后转入降温阶段,将酒均为冷却与贮酒温度。
酒在不同温度选会形成对流的作用。
酒液密度温度在直接冷却3℃,要以上带和中带控温为主。
3℃保温稳定酒液流态。
3℃以下控制罐下部为主控温,打破温度梯度,满足控制温度效果
图2.2啤酒发酵工艺曲线
每个发酵罐的上、中、下3个测量点的温度进行检测,实现自动控制,罐内实行压力检测。
整个发酵过程按照发酵机理,根据主酵→双己酰还原→冷却→酵母回收→后贮的阶段,分别设定曲线进行控制,并采用滞后预估等控制方法,使系统控制精度符合工艺要求。
在各个阶段,对象的特性相对稳定,温度的控制存在一定的规律性。
在发酵开始前,根据工艺要求预先设定工艺控制的温度曲线;在发酵工程中,根据发酵进行的程度(发酵时间、糖度、双乙酰含量等),发酵罐上、中、下3段温度的差异,以及3段温度各自的变化趋势,自动正确选择各个阶段相应的控制策略,从而达到预期的控制效果。
在前期的自然升温阶段基本上不需要加以控制,这是由于啤酒罐发酵过程中,升温是靠发酵本身产生的热量进行的,任其自然升温;在恒温阶段,通过控制冷媒开关阀,保持发酵罐内温度恒定;在降温阶段,通过控制冷媒开关阀,以指定速率降温。
主要分为以下阶段:
1.麦汁进料过程:
在这个过程中,由糖化阶段产生的麦汁原料经由连接管道由糖化罐进入发酵罐中。
2.自然升温阶段:
麦汁进料过程中,随着酵母的加入,酵母菌逐渐开始生长和繁殖。
在这个过程中,麦汁在酵母菌的作用下发生化学反应,产生大量二氧化碳和热量,这就使原料的温度逐渐上升。
3.还原双乙酰过程:
在自然升温发酵过程中,化学反应能产生一种学名叫双乙酰的化学物质。
这种物质对人体健康不利而且会降低啤酒的可口程度,所以这个过程需要将其除去,增强啤酒的品质。
4.降温过程:
在1和2过程中啤酒发酵已经完成,降温过程其实属于啤酒发酵的后续过程,其作用是将发酵过程中加入的酵母菌进行沉淀、排出。
5.低温储酒过程:
降温过程完成以后,已经发酵完成的原料继续储存在发酵罐等待过滤、稀释、杀菌等过程的进行。
第3章硬件设计
3.1PLC的选型
3.1.1PLC工作原理及功能
可编程控制器(PLC))工作原理
当PLC投入运行后,其工作过程一般分为三个阶段,即输入采样、用户程序执行和输出刷新三个阶段:
1.输入采样:
即检查各输入的开关状态,将这些状态数据存储起来为下一阶段使用。
2.执行程序:
然后PLC按用户程序中的指令逐条执行,但是把执行结果暂时存储起来。
3.刷新输出:
按第1阶段的输入状态在第2阶段执行程序中确定的结果,在本阶段中对输出予以刷新。
PLC的主要功能:
逻辑控制、定时控制、计数控制、步进(顺序)控制、PID控制、数据处理、通信和联网,还有许多特殊功能模块,适用于各种特殊控制的要求,如定位控制模块,CRT模块。
正是由于PLC具有多种功能,集三电于一体,PLC网络具有优良的性能价格比和PLC具有高可靠性等等,使得PLC在工厂中倍受欢迎,用量高居首位,成为现代工业自动化的支柱。
因此,可编程控制器啤酒发酵过程自动控制系统,可完成啤酒发酵过程控制功能,完成与上位机的通讯,实现啤酒发酵过程的远程监控。
3.1.2PLC的选型
各个种类PLC的容量、结构形式、性能、指令系统、编程方法、价格各不相同,适应的工作场合也有差异。
因此,对于每一个准备使用PLC的用户来说,合理的选择PLC是非常重要的,它直接影响到所设计系统的性能与造价。
据啤酒发酵的工艺流程和需要,PLC的选型需要满足以下条件:
1.有简单回路控制算法。
2.有模拟量的采集、处理过程及开关量的输入/输出功能。
3.有温度显示和用外部按键随时改变内部参数
因此PLC的选择包括机型、容量、I/O模块等几个方面的内容。
1.PLC机型的选择
如今国内使用的PLC以国外产品居多。
美国是PLC的发源地,以大中型机为主,功能完备,单机价格高,GE公司、MODICON公司、AB公司是其代表。
日本的PLC以中小型机为主,价格便宜,典型代表为OMRON公司、三菱(MITSUBISHI)公司的产品。
德国SIEMENS公司的产品以可靠性高著称,其主要产品有S5、S7两个系列,包括了从大型机到小型机各个型号,在国内使用广泛。
2.选择容量。
PLC的容量包括主机用户存储器的内存容量和I/O控制点数两个方面,选择时应留有适当的裕量做备用。
3.选择I/O模块。
输入模块有直流24VDC和交流220VAC两种。
输出模块有三种形式:
继电器输出,晶体管输出和晶闸管输出。
晶体管输出模块只能带直流负载,是直流输出模块,用于高速小功率负载;晶闸管输出模块是交流输出模块,只用于高速大功率负载;继电器输出模块是交直流输出模块,即可带直流也可带交流,因其有触点,故只能用于低速负载。
上煤系统电控部分控制对象为接触器,属于交流低速负载。
S7-200系列是西门子公司生产的小型可编程程序控制器,结构小巧,可靠性高,运行速度快,有极丰富的指令集,具有强大的多种集成功能和实时特性,配有功能丰富的扩展模块,性能价格比非常高。
S7200四种CPU:
CPU221,CPU222,CPU224,CPU226
CPU226这种模块在CPU224的基础上功能又进一步增强,主机输入输出点数增为40点,具有扩展能力,最大扩展为248点数字量或35点模拟量,增加了通信口的数量,通信能力大大增强,它可用于点数较多、要求较高的小型或中型控制系统。
根据对整个系统的考察,啤酒发酵温度PLC控制系统的I/O点数及类型确定,可知PLC要提供21个开关量输入和15个开关量输出,5个模拟量输入,同时考虑到要留有20%~30%的余量。
通过比较S7200四种CPU的各种技术指标,选定CPU226为啤酒发酵温度PLC控制的控制器。
3.2S7-200主要功能及特点
1.执行指令速度高。
CPU212执行每条二进制指令时间为1.2s,而CPU214-CPU261仅为0.8s。
2.丰富的指令功能。
S7-200PLC几乎包括了一般计算所具有的各种基本操作指令,如变量赋值、数据存位置、传送、比较、子程序调用、循环等。
另外,它还有良好的用户使用功能,如脉宽调制(PWM),位置控制(PTO)、PID等功能。
3.灵活的中断功能,中断触发有几种形式:
可用软件设定为中断输入信号的上升沿式下降沿,以便做出快速响应;可设为时间控制的自动中断;可由内置高数计数器自动触发中断;在与外设通信时可以以中断分式工作。
4.输入和输出的直接查询和赋值。
在扫描周期内,可直接查询当前的输入和输出信号,在必要时,还可以用指令对输入和输出直接赋值或改变其值,这样不仅用户调试程序方便,同时也可使系统对过程事件做出快速响应。
5.严格的口令保护。
S7-200系统有3个不同的口令保护级别,以便用户对程序做有效保护,3级口令分别是自由存取,只读,完全保护。
6.友好的调试和故障诊断功能,包括整个用户程序可在用户规定的同期数内运行和分析,同时可纪录性存储器、定时器、计数器状态。
7.输入或输出的强制功能。
用户调试程序时,可对输入或输出强制接通。
8.通信功能。
通信是S7-200PLC的一个重要功能,它为用户提供了强大,灵活的通信功能。
用户对点接口(PPI)作9.6Kbit/s的数据通信,用RS-485接口实现高速用户可编和接口。
3.3控制系统的硬件配置
S7-200PLC的扩展模块
S7-200PLC可以安装在板上,也可以安装在标准DIN导轨上,利用总线连接电缆,可以很容易的把CPU模块和扩展模块连接在一起。
需要连接的扩展模块较多时,模块连接起来会过长,两组模块之间可使用扩展连接电缆,将模块安装成两排。
信号处理模块主要分为四类:
开关量输入DI、开关量输出DO、模拟量输入AI、模拟量输出AO。
啤酒发酵控制原理可以得出:
每只发酵罐需要有上温、中温、下温、液位四个模拟量需要测量,上温、中温、下温3个温度各需要一个二位式电磁阀进行控制,所以每只发酵罐的I/O点数为4个模拟量、36个开关量,考虑到CPU226主机上的I/O口不够多必须对它进行扩展,在这选用EM221CN数字量输入模块(6ES7211~1BF22~0XA8)、EM222CN数字量输出模块(6ES7222-1HF22-0XA8)、模拟量扩展模块EM231CNAI4X12位。
其扩展图如图3.1所示:
图3.1模块扩展连接图
3.4文本显示器TD200
TD200是TextDisplay200的简写,它是可编程控制器S7-200系列的常用文本显示器。
它可以用来显示信息,在信息中可以内嵌数据,数据既可以显示,也可以由操作人员进行设置。
TD200键盘共有9个键:
5个命令键和4个功能键。
命令键:
ENTER—用写入新数据和确认信息;ESC—用转换DisplayMessage方式和Menu方式,或紧急停止一个编辑;UPARROW—UP箭头用于递增数据和上卷光标到下一个更高优先级的信息;DOWNARROW—DOWN箭头用于递减数据和卷动光标到下一个较低优先级的信息;SHIFT—转换所有功能键的数值。
当按SHIFT键时,在TD200显示区的右下方显示一个闪烁的S。
功能键:
F1—设置标志位Mx.0。
(S7-200M存储区x字节的第0位)如果按SHIFT键的同时(或预先按下SHIFT键)按下功能键F1,则设置标志位Mx.4;
F2—设置标志位Mx.1。
如果按SHIFT键的同时(或预先按下SHIFT键)按下功能键F2,则设置标志位Mx.5;F3—设置标志位Mx.2。
如果按SHIFT键的同时(或预先按下SHIFT键)按下功能键F3,则设置标志位Mx.6;F4—设置标志位Mx.3。
如果按SHIFT键的同时(或预先按下SHIFT键)按下功能键F4,则设置标志位Mx.7。
TD200既可以通过TD/CPU电缆由S7-200CPU供电,也可以由一个外部插入式电源供电,但不能TD/CPU电缆和外部电源同时对TD200供电,这样会损坏设备。
本文只讨论最简单、最常用的方式:
由S7-200通过TD/CPU电缆供电。
TD200只是一个文本显示器,不需对TD200进行组态和编程,所有组态信息全部存在CPUS7-200中。
TD200里只存储TD200的地址、所连接的CPU的地址、通讯波特率和参数块的位置(注意要与CPU中的一致)。
也就是说,TD200的所有组态数据都存储在CPUS7-200可变存储器(V存储器)内,而在TD200中只需通过面板设置TD200的地址、所连接的CPU的地址、通讯波特率和参数块(TD向导中变量的起始地址)的位置。
TD200上电后,按“ESC”键进入“诊断菜单”,接着进入“TD200设置”选项,分别设置“TD200地址”(缺省值为1)、“CPU地址”(缺省值为2)、“参数块地址”(缺省值为0)、“波特率”(缺省值为9.6K)。
本例中,我们使用缺省设置。
在STEP7MicroWINV4.0中,用TD200向导(菜单“Tools>TD200Wizard”)给CPUS7-200编程。
完成编程并下载后,将CPU和TD200通过TD/CPU电缆进行正确连接,正确设置TD200的参数,即可完成TD200的开发使用。
上电后,TD200从CPU读参数块。
对所有参数均进行合法性检查。
如果一切合格,TD200开始主动轮询信息使能位以决定要显示的信息,并从CPU读取信息,然后显示信息。
显示的信息,并从CPU读取信息,然后显示信息。
3.5I/O地址分配
根据啤酒发酵温度控制的工艺流程及实际需求,确定整个系统共有26个输入点,其中5个模拟量;