托板冲裁模具设计说明书.docx
《托板冲裁模具设计说明书.docx》由会员分享,可在线阅读,更多相关《托板冲裁模具设计说明书.docx(23页珍藏版)》请在冰豆网上搜索。
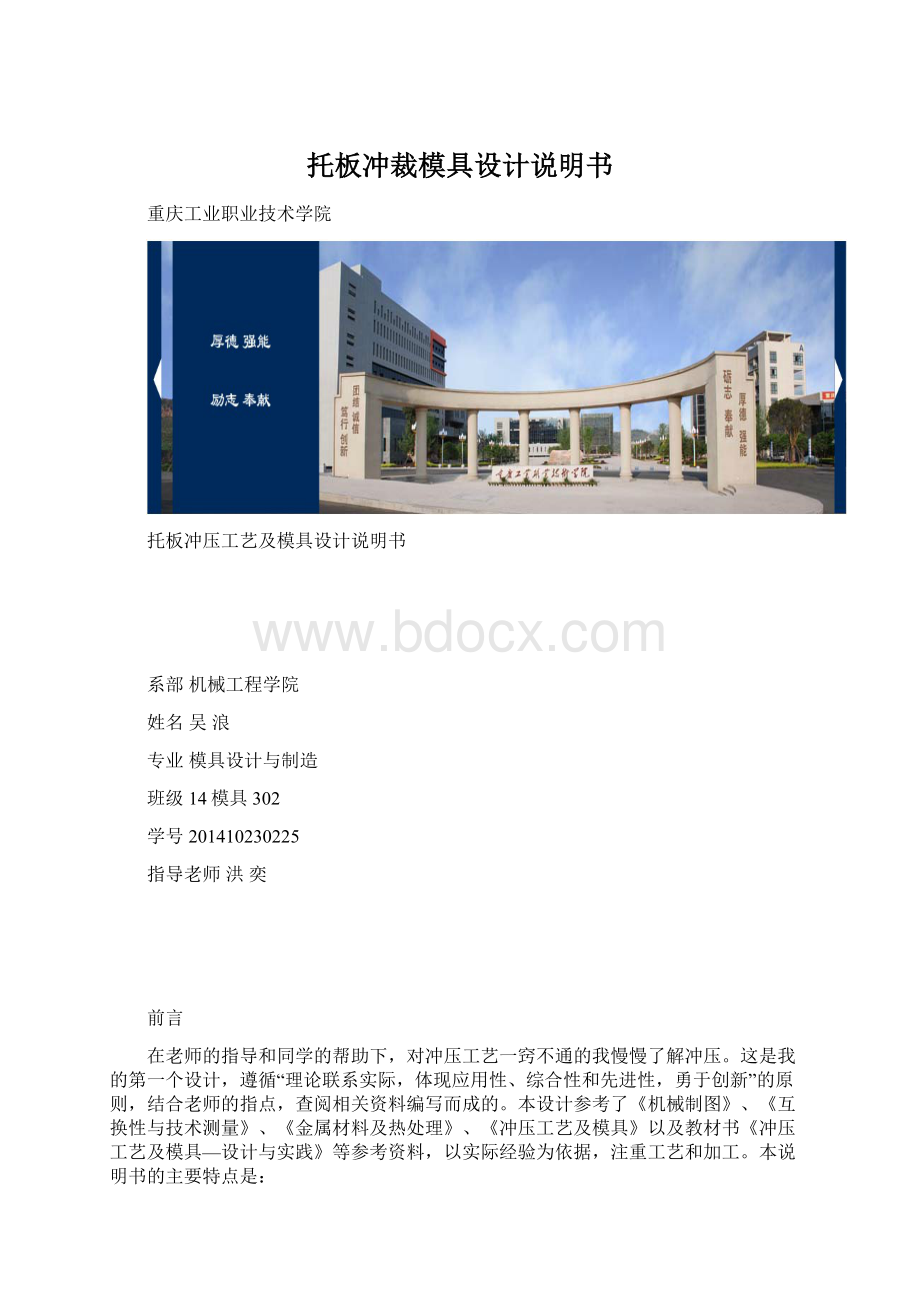
托板冲裁模具设计说明书
重庆工业职业技术学院
托板冲压工艺及模具设计说明书
系部机械工程学院
姓名吴浪
专业模具设计与制造
班级14模具302
学号201410230225
指导老师洪奕
前言
在老师的指导和同学的帮助下,对冲压工艺一窍不通的我慢慢了解冲压。
这是我的第一个设计,遵循“理论联系实际,体现应用性、综合性和先进性,勇于创新”的原则,结合老师的指点,查阅相关资料编写而成的。
本设计参考了《机械制图》、《互换性与技术测量》、《金属材料及热处理》、《冲压工艺及模具》以及教材书《冲压工艺及模具—设计与实践》等参考资料,以实际经验为依据,注重工艺和加工。
本说明书的主要特点是:
1、根据从事成型工艺及模具设计工程应用型人才的实际要求,理论以“必须、够用”为度,着眼于加强专业知识,积极吸纳新技术,体现了应用性、实用性、综合性和先进性。
2、本设计介绍了冲裁模具的设计思路和方法,着重介绍了工艺方案的确定,重要尺寸的计算、主要零件的设计。
3、各部分均选用了较多的应用实例,重点部分精选了综合应用实例,应用性和可操作性强,便于生产和识读。
通过本设计,我深刻体会到了“书到用时方很少”这句话,以前的基础知识没怎么学好,设计时步步艰难。
只要一个数据出错,后面全错,必须认真查阅相关书籍,不能有半点马虎。
不过也扩展了知识面,学到了不少的东西。
由于编者水平有限,错误及不妥之处在所难免,希望老师和广大读者批评指正。
编者
第一章冲裁件的工艺分析···········5
1.1冲裁件的批量和材料
1.2冲裁件的结构和尺寸
1.3冲裁件的精度和粗糙度
第二章冲压工艺流程设计及优化·····8
2.1冲压工艺类型
2.2冲压工艺次数
2.3冲压工艺顺序
2.4冲压工艺组合方式
第三章冲裁件的工艺参数计算······12
3.1排样
3.2定位方式
3.3方案分析
3.4模具中心压力的确定
3.5冲裁力的计算与冲裁设备的确定
第四章冲裁模具参数计算·········22
4.1冲裁模具间隙的选用和确定
4.2冲裁模具刃口尺寸计算
第五章模具总装图··············26
第六章冲裁模具零部件设计·····28
6.1冲裁模具工作零件设计
6.2冲裁模具卸料与出件装置设计
6.3弹簧和橡胶的选用
6.4冲裁模具定位零件设计
6.5标准模架与与导向零件设计
6.6其他支承固定零件
后记···························40
参考文献·······················41
第一章冲裁件的工艺分析
1.1冲裁件的批量和材料
1、批量
由零件图中的相关要求可知:
该零件的生产批量为大批量,所以为提高生产效率,降低生产成本,该零件适合冲压。
2、材料
由零件图中的相关要求可知:
该零件所用材料为08F,
据《金属材料及热处理》P101页可得:
08F为优质碳素钢,其强度低且硬度、塑性、韧性好、易于冲裁、弯曲、拉深,所以该零件适合冲压。
1.2冲裁件的结构和尺寸
1、形状
由零件图分析可知:
该零件形状相对简单,成对称结构。
而冲压要求零件形状相对简单、规则,有利于材料的合理利用,提高模具的使用寿命,所以该零件适合于冲压。
2、尖角
由零件图分析可知:
该零件外形有90度的尖角,为提高模具寿命,便于模具加工,零件的内、外形转角处要尽量避免尖角,应以圆弧过渡,最小圆角半径查教材表4-3,落料时交角大于等于90度的软钢最小圆角半径为0.25t=0.5mm,所以建议将零件所有90度尖角改为R0.5的圆角,并与客户会签。
3、悬臂与凹槽
为提高模具寿命及零件质量,尽量避免零件过于窄长和凸出悬臂和凹槽。
由零件图分析可知:
该零件无过长悬臂和凹槽,所以该零件适用于冲压。
4、冲孔的最小尺寸
冲孔时,因受凸模强度的限制,孔的尺寸不宜太小,冲孔的最小尺寸取决于材料的性能、凸模强度和模具结构等。
有零件图分析可知:
零件只有一个圆形孔,查教材表3-2可知,08F的抗剪强度为230-310Mpa。
再查表4-4得:
无导向凸模冲孔最小尺寸为2.6mm,由零件图可知,零件唯一的最小的孔的直径dmin=10mm>2.6mm,所以零件满足冲压要求。
5、孔间距和孔边距
因为零件只有一个孔,所以不存在孔间距。
由零件图可知,零件为对称结构,其最小边距为10mm,故不影响生产。
1.3冲裁件的精度和粗糙度
1、精度等级
冲裁件的经济公差等级不高于IT11级,一般落料件公差等级最好低于IT9级。
根据零件图查《互换性与技术测量》表2-3,零件长度58-0.74的精度等级为IT14级,零件宽度30-0.52的精度等级为IT14级,外圆尺寸R8-0.22的精度等级为IT13级,
内孔尺寸的精度等级为IT8级,其余未标注尺寸为自由公差,按IT14级计,所以该零件满足精度要求。
2、粗糙度
冲裁件的断面粗糙度及毛刺高度与材料塑性、材料厚度、冲裁间隙、冲模结构和凹凸模工作部分表面粗糙度有关。
用普通冲裁方式冲裁厚度为2mm以下的金属板料时,其断面粗糙度值Ra一般可达3.2~12.5um,由零件图可知该零件的表面粗糙度为6.3um,满足使用要求。
查教材4-8,毛刺高度在试模时小于等于0.05mm,生产时小于等于0.15mm,故满足使用要求。
综合上述分析,该零件适合冲压。
冲压件图
第二章冲压工艺流程设计及优化
2.1冲压工艺类型
由冲压件图可以看出,该零件所需的基本工序为落料、冲孔。
2.2冲压工艺次数
由冲压件图可以看出,该零件的工艺次数分为落料和冲孔两个工序。
2.3冲压工艺顺序
根据第一章算出零件的孔边距为10mm,如果先冲孔,零件的形状和尺寸很有可能受后续工序的影响,导致变形,所以不宜先冲孔后落料,为减少定位误差和避免尺寸计算,应先落料后冲孔。
故零件的冲压工艺顺序为先落料后冲孔。
2.4冲压工艺组合方式
单工序模方案1:
落料→冲孔
方案2:
冲孔→落料
复合膜方案3:
落料+冲孔
方案4:
冲孔+落料
方案5:
落料、冲孔同时进行
级进模方案6:
落料→冲孔
方案7:
冲孔→落料
组合方式分析
方案1:
采用单工序模,制造成本低,尺寸和冲压件的厚度不受限制,但冲压出来的工件精度低,冲压多工序的冲裁件时,要经过多次定位和变形,产生累积误差大,生产效率低,生产时安全性低,只适合小批量生产。
由冲压件图可以看出,该零件生产批量大,若采用单工序模,增加了生产周期,从冲裁质量、经济性、安全性上看,该零件不适合采用单工序模,故不采用单工序模,否定方案一。
方案2:
采用单工序模,分析同方案1,故不采用方案2。
方案3:
采用复合模,由教材表4-10可知,复合模的加工精度可达IT9-IT8级,孔与外形的位置精度较高,冲压件平整,冲压件厚度在0.05~3mm之间,适合大批量生产,能实现废料重新利用,在调校和试模中虽技术要求高,但难度不大。
但操作性能不方便,需要手动进行卸料,不太安全。
由冲压件图可知,零件加工精度一般,厚度为2mm,结构简单且大批量生产。
从冲裁质量、经济性方面来看,复合模明显优于单工序模,本方案满足其生产要求,故暂时保留方案3.
方案4:
采用复合模,分析如方案三,与方案3工艺顺序相反,一般情况下,有落料和冲孔时,应采取先落料后冲孔以减少定位误差和避免尺寸换算。
故不采用方案4.
方案5:
采用复合模,分析如方案3.但若冲孔与落料同时进行,不但对模具磨损大,而且冲裁时精度互相影响,冲裁质量差,故不采用方案5.
方案6:
采用级进模,由教材表4-10可知,级进模的加工精度可达IT13~IT10级,冲压件料厚为0.6~6mm之间,冲裁时自动送料,冲件和废料从下模漏下,操作方便安全,可采用高生产效率的高速压力机。
在加工形状简单的工件时模具制造成本和工作量低于复合模,适合大批量生产,无论从生产批量、生产效率还是安全性上来看都符合零件的生产要求。
由前面的计算可知,零件内孔精度要求较高,若采用级进模,加工精度达不到要求,需要后期加工,延长生产周期,故不采用级进模。
否定方案6.
方案7:
采用级进模。
分析同方案6,与方案6工艺顺序不同。
故不采用方案7.
综合以上分析,确定采用方案3为宜,即冲压工艺组合方式为采用复合模,落料+冲孔。
第三章冲裁件的工艺参数计算
3.1排样
1.排样方式
①有废料排样
②少废料排样
③无废料排样
由冲压件图可以看出,零件结构简单,尺寸精度不高,可选择无废料排样,但无废料排样难以保证尺寸精度,且难以实现材料完全利用。
故采用少废料排样为宜。
2、排样形式
由教材表4.11分析可知,选择具体形式为直排最佳。
3、板料纵裁和横裁的选择
板料一般都是长方形的,故有纵裁和横裁两种方法。
横裁和纵裁各有横排和竖排两种方式。
3.2定位方式
1.初级定位
初级定位定位不太准确,适用于单工序模或精度不高的复合模。
2.中级定位
中级定位比初级定位准确,适用于复合模。
3.高级定位
高级定位定位最准确,适用于级进模。
综合以上分析,由零件图可知,该零件精度较高,可采用中级定位,导料板且有侧压装置的模具。
3.3工艺参数的计算
根据排样方式可分为四种方案:
方案一:
纵裁→竖排
方案二:
纵裁→横排
方案三:
横裁→竖排
方案四:
横裁→横排
方案分析:
查教材表4-15,C=5mm
由冲压件图可以看出,零件面积A1=38×30+16×2×2+82×π-4×(-π×)=1404.85mm2
方案一
搭边值:
查教材表4-12,a1=2.2mm,a=1.8mm
条料宽度:
查表4-13,△=0.6mm
B0-0.6=(Dmax+2a)0-0.6=61.60-0.6
导料板间距:
A=B+C=66.6mm
条料步距:
S=Dmax+a1=32.2mm
查《冲压模具及设备》表2-5,选择长为2000mm,宽为1000mm的板料
板料条数:
n1=1000÷61.6=16.23取整数16
每条条料上的零件数:
n2==62.03取整数62
一张板料上的零件数:
n=n1×n2=992
材料利用率:
η=×100%=69.68%
方案二
搭边查教材表4-12得,a1=1.5mm,a2=2.2mm
查表4-14△=0.2mm
条料宽度B0-0.2=(Dmax+2a)0-0.2=34.40-0.2
导料板间距离A=B+C=39.4mm
条料步距S=Dmax+a=59.5mm
板料条数n==29.09取整数29
每条板料上零件数n==33.59取整数33
一张板料上的零件数n=957
材料利用率η=×100%=67.22%
方案三
搭边值查表4-12a1=1.5mma2=2.5mm
查表4-14△=0.2
条料宽度B0-0.2=(Dmax+2a+c)0-0.2=350-0.2
导料板间距离A=B+C=40mm
条料步距S=Dmax+a1=59.5mm
板料条数n1==57.14取57
每条板料上的零件数n2==16.76取整数16
一张板料上的零件数n=n1n2=912
材料利用率η=×100%=64.06%
方案四
搭边值查表4-12a1=2.0a=1.8
条料宽度查表4-13△=0.6
B00.6=(Dmax+2a+c)0-0.6=61.60-0.6
导料板间距离A=B+C=66.6mm
条料步距S=Dmax