数控操作标准.docx
《数控操作标准.docx》由会员分享,可在线阅读,更多相关《数控操作标准.docx(46页珍藏版)》请在冰豆网上搜索。
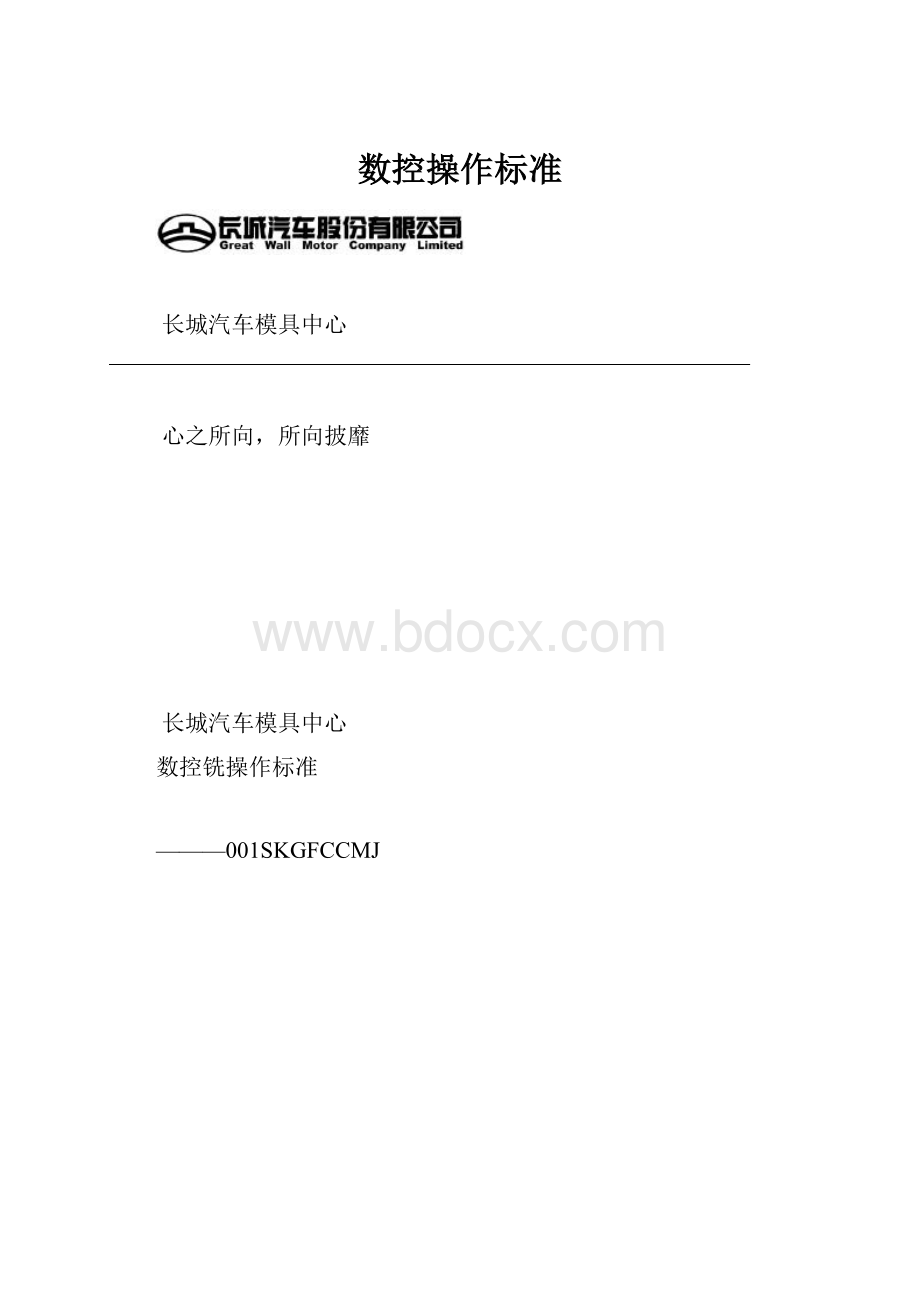
数控操作标准
长城汽车模具中心
心之所向,所向披靡
长城汽车模具中心
数控铣操作标准
———001SKGFCCMJ
编制:
校对:
审核:
批准:
进每步天一
点点
长城汽车模具中心
发布日期实施日期:
:
发布长城汽车股份有限公司模具中心
目的1.
指导合理顺畅的加工,为下道工序(顾客)提供合格的工序产品,正确的找正定位数据等。
确保产品质量。
适用范围2.
本规范适用于各类冷冲模具数控加工工艺流程,加工部位、加工要求,注意事项等的控制。
作业前准备3.
穿戴好劳保用品,注意自身形象。
3.1
进行设备点检。
~15分钟,检查设备的机、电、润滑情况3.2冷机空运行5
熟悉图纸、程序及工艺,检查刀具、工具、辅具的状况,看清并明白交接班记录的数据和3.3
说明。
”侧非加工区右边用记号笔写明加工件的令号、件号,以3.4根据图纸在铸件毛坯(工件)“F
供转序使用。
结合图纸、程序、工艺,使用可视刀轨信息软件、卷尺等方式,确认加工件的尺寸无大的3.5
出入,程序与加工件的方向一致、形状相似等情况。
工件装夹4.
。
)正方向一致F4.1工件正方向“”面向操作台(冲压上模具指示箭头与机床“Y”轴
”轴平行或垂直。
、工件中心座标轴与机床“XY4.2
工件压紧处应选择较平整处,忌选与压板宽度方向有一较大夹角的斜面,注意产生侧向力。
4.3
工件压紧点下应具备良好的支撑(不采用易受压变形的支撑物)且已受力(用手轻拉动支4.4
。
撑物如垫铁,不动则为已受力)
0.4mm.0.2~4.5压板支撑要求平稳,力求大面积受力。
支撑高度可稍高出压紧处
2:
4.6压紧螺杆应靠近于工件,压板前端与支撑后端距螺杆之比为1
工件压紧应均衡,对角受力,采用预压后再压紧。
一般不使用加力杆(忌用加力杆大力压4.7
紧)
20mm.螺杆旋入螺母和梯形块的长度不得少于4.8
工件的牢固定位不光来自于压板方向压力还可应用快速定位键和侧顶紧装置等加固。
4.9
每天进步一
点点
长城汽车模具中心
使用的工装经常检查,发现开缝等不良现象及时处理以防不测。
4.10
0.02mm.4.11工件垫铁注意磕碰,定期自检,其同一尺寸精度不能超差
压卸工件人员姿势(前蹬后撑)保持正确以防安全事故发生。
4.12
装卡找正工时(包含起吊转工件时间)4.13
)上下模座装卡时有快速定位键的条件下必须要用快速定位键,模座尺寸小于1
的,2000mm*1000mm分钟,找正时间为15分钟;大于2000mm*1000mm的,装卡时间为15
分钟;20装卡时间为25分钟,找正时间为
分钟;大1525分钟,找正时间为)压件芯尺寸小于22000mm*1000mm的,装卡时间为
分钟;2030分钟,找正时间为2000mm*1000mm于的,装卡时间为
分钟;分钟,找正时间为153)装有工艺板的刀块,尺寸小于500*500的,装卡时间为15
分钟;分钟,找正时间为20大于500*500的,装卡时间为25
条,找正时间为)上述三条是指按基准找正的。
按线找正的工件,装卡时间参考上述34
分钟。
10
工件的找正及定位5.
毛坯件粗加工底面时按铸件上“等高线”(等高线高度分为5.1
)找平定出加工余量,依铸件中心线定出加工件200mm100mm、150mm、、20mm、50mm
(如上图)的中心,同时应周全考虑外形和重要轮廓的加工余量等情况。
按快速定位键或预先制作的基准找正定位,加工模具的正面全部。
5.2
型面轮廓和重要加工位置精加工前依图纸尺寸或在下序易找正定位的位置作两个或三个销5.3
孔,并以此孔为最终基准作后序加工。
Z单加工件需在脱离基准体前作两个销孔或直角基准面,并测量此工件安装面在基准体的5.4
向高度以供单加工件后序加工基准使用,记录并画简图标识在交接班记录中。
加工流程6.
加工零件名称7.每天进步一
点点
长城汽车模具中心
加工部位8.
找正及定位9.
加工件余量与信息处理10.
铸件毛坯10.1
,)20mm余量1.5m时为15mm,超大铸件为1′铸铁件加工部位余量一般为10mm(长大于
。
8mm8mm)型面铸钢件底面为5mm(大件为
5mm2′加工导板、型面、轮廓及重要挡墙时应充分考虑这些部分的加工余量,误差在
(如上图)内可以加工。
程序加工10.2
。
1′等高分层加工件首层程序所有角度与实体工件误差为±2mm
。
0.8~1mm0.15~0.2mm,型面粗加工余量为2′半精加工余量为
待处理后再加工余量不够或超大不均时,应立刻向上一层人员反映并填写“异常报告”10.3
加工(期间可先加工与此超差无关的部位)
记录及标识11.
记录内容:
加工工件的名称、制号、导板尺寸、定位销孔位、导柱(衬套)孔的加工公差、11.1
值对刀点及数据等。
Z基准孔基准面、与侧冲或侧整有关的位置、变更的数据、型面加工
′在交接班本上记录111.2记录方式:
′在所加工件上标出2
向对刀点标识。
Z3′中心销孔在孔位处打钢字标识及
工艺平台及孔12.
。
1510H7深1′CH孔为φ
。
,深20mmφ10H7、φ12H7、16H7′中心销孔为2φ
。
30~40mmL形平台有效长为3′中心两销孔做
。
15mm′冲头安装定位孔φ6,深4
。
10mmφ4,深5′防转销孔
刀具选择原则13.
平面加工应根据平面大小选择合适端铣刀,无干涉的平面用下直径大的盘铣刀,有干涉13.1
的区域加工应根据干涉高度选择稍高于干涉物的端铣刀,忌用长刀杆加工无干涉的区域。
立铣刀选择要根据加工深度切忌用长而细的刀杆加工浅部位,轮廓加工中,若因条件限13.2
制,使用了长刃刀具也应力求使用刀刃上部。
大余量的加工部位,应选择锥柄刀具避免刀具爬坡式加工中刀具从刀柄中拉出。
13.3
球头刀具的选择及适用13.4
具有主副刃的间断刃刀具。
、R20R30′大直径刀具适用于粗加工,用于重中度切削1,如、R25
每天进步一
点点
长城汽车模具中心
等等。
R8、R62′小直径球刀一般作为清根使用,如R10、
的不同选择及适用条件R12.5、R103′球头刀具R15、
刀具选择中还应针对不同的切削条件做合适的调整(加沙、气孔、高硬度等)13.5
的导板面可采用立铣刀加工。
导板加工:
小于150mm13.6
刀具的切削参数表14.
加工顺序原则15.
先粗后精的原则可贯穿于整个加工中。
15.1
型面与轮廓:
先加工轮廓后加工型面。
15.2
轮廓粗加工→型面粗加工→轮廓半精加工→型面清根、精加工→轮廓精加工
斜面空位加工:
先用不大于最终孔径的平底刀具窝平斜面再作孔。
15.3
凹模套、防转销孔,一般为先加工防转销孔,再加工凹模套孔。
15.4
提高数控加工效率的方法16.
认真进行交接班,填写每个加工的当班情况,于交接班记录中反映非正常现象,提出合理化17.
建议,员工相互鞭策,共同上进。
孔
一、基准孔3-5mm,没有铸25mm.。
铸件毛坯实型铸出基准孔平台的,基准平台高度为基准孔最终为D16H7加工,深的见光平台,在平台的中心打出基准孔。
必出平台或自己在合适位置加工基准孔的,要铣出一见方50*50mm须用铅字头打出基准孔的数值。
加工过程的工艺基准孔不要求铣平台和打铅字,但必须在交班本上作好记录。
孔二、CH,拉延模的下模可深一些。
深度:
ф15mm10H7
)2/3H7。
。
2.底部必须具有支撑平面(大于孔底面积的要求:
1.直径公差
到底标记销孔三、)(压印器
直径
公差
深度
备注
孔底部须平面(大)于孔底面积的2/3
ф12
+0.018)(120
11.7
压配
16ф
+0.018)(160
15.7
压配
左右标记销孔(刻印)四.
每天进步一
点点
长城汽车模具中心
直径
公差
深度
备注
孔底部须平面(大)于孔底面积的2/3
ф16
+0.018)(160
19.7
可滑配
20ф
+0.021)(200
19.7
可滑配
中心销孔五、
直径
公差
深度
备注
ф8
+0.015)(80
15
粗加工→精加工依次1.选销孔直径原则:
.先打小直径→稍大直径孔。
增大无辅助平台时需做中心销孔“L”型台。
2.D×30×30
ф10
)(100+0.015
12ф
)(120+0.018
ф16
)(160+0.018
冲头安装定位孔。
六、深(工艺尾孔):
ф15mm60+0.012
七、防转销孔(凹模套)。
ф:
()深10mm40+0.012
位置防转销孔F(凹模套)八、
凹模套孔径
ф10
ф13
ф16
ф20
ф22
ф25
ф32
ф38
ф40
ф45
F值
6
7.2
8
10
11
12.5
16
19
20
22.5
凹模套孔底孔直径备注:
盘起厂家“K41”型九、
每天进步一
点点
长城汽车模具中心
D凹模套尺寸
ф10
1ф3
ф16
ф20
ф22
ф25
ф32
ф38
ф40
ф45
ф50
ф56
6ф3
7ф1
底孔d
6.4
8.4
10.4
12.5
15
17.5
21
27.5
28
37
42
47
52
58
螺钉常用加工参数过孔及沉头深度十、
每天进步一
螺钉直径
底孔直径(d)
)底孔深度(L
)套扣深度(L1
‘螺钉过孔(d)
M5
4.2ф
30
20
5.5
M6
ф5.1
30
20
6.6
M8
ф6.8
40
25
9.5
M10
ф8.5
40
25
11.5
M12
ф10.5
50
30
14
M16
ф14
50
35
17.5
M20
ф17.5
55
45
21.5
M24
ф21.5
65
50
26
M27
ф24
70
55
30
M30
ф27
80
65
33
M36
ф32
90
75
38
点点
长城汽车模具中心
螺钉常用加工参数十一.
销孔直径
销孔预钻
沉孔直径
沉孔深度
本体预钻深度
铰孔深度
(D)
)(D1
)(D2
(H)
)(H1
)(h1
6ф
5.5
6.7
15
35
15
ф8
7.5
10.5
15
35
20
10ф
9.5
10.5
20
40
20
ф12
11.5
14
25
40
25
16ф
15.5
17.5
25
40
25
ф20
19.5
21.5
30
50
25
导柱底孔、导套孔的尺寸公差作出,表如下:
孔的加工公差按H7.十二
导柱(套)孔径D
20
25
32
40
50
63
80
100
120
H7
200+0.021
250+0.021
320+0.025
400+0.025
500+0.025
630+0.030
800+0.030
1000+0.035
1200+0.035
装配式顶出器孔径公差卸料装置导套孔加工公差一般可按注:
导柱孔加工公差一般可按—DD:
十三.D-0.01+0.01+0.01+0.020+0.03
弹顶销合件(外部丝扣固定)孔的制作:
数控作出点位即可。
十四.
安全侧销公差侧销.:
十五.DH7
侧销.安全侧销D
22
32
42
52
62
72
H7
+0.021220
+0.025320
+0.030420
520+0.030
620+0.030
720+0.030
镗孔规范
一每天进步
点点
长城汽车模具中心
确保孔的准确度
一斜面上孔:
用立铣在其表面先按孔位置铣平斜面(所铣面积要稍小于实际加工
。
~)面积单边0.5mm0.2
二用中心钻打定位孔(所用中心钻直径一般不得超过实际孔的直径)深度应进入
中心钻头锥面处。
三,大孔选大值,小孔选小选用合适的钻头(一般小于实际加工孔直径~5mm1
值)钻底孔。
阶梯孔(如:
凹模套孔)一般采用钻头钻底孔(直接按底孔大小要求
左右镗孔。
,上台阶孔采用立铣加工,留单边钻出)0.5~1mm
四镗孔:
①机床轴向位移需把其反向间隙去除(到达每个孔位机床轴向移动方向
。
相同,特别是加工导向孔时更应如此)
之间。
0.05~0.1mm②最后一刀精镗余量一般单边为
③镗孔直径在没有准确把握的情况下,采用直径少给深度不宜过大的原
以内必须停止、抬刀、量表检测孔径。
确保准确的条件则。
镗入孔的深度在10mm
。
下方可继续加工(按之前所用切削参数加工)
粗糙面孔,④精镗时转速不宜过高,进给也不宜过大,避免出现锥孔.
锥度。
0.02mm大直径深孔可允许有
台阶孔时应特别注意深度控制,过深造成镗刀片损坏,过浅⑤镗盲孔.
以下(在精镗时深度可少进0.3mm易留下较大台阶。
一般可允许留台阶圆角或斜角
。
)0.1mm
⑥调节镗头进刀尺寸若超过所加工孔径需调节缩小(与前调节旋转方向
相反)尺寸时,应把尺寸缩小范围增大,再调节增大至需缩小位置,即可实现较准
确的后退调节尺寸。
⑦在镗孔过程中,应时常检测量表的准确性,避免出现重复测量中量具
的变动造成不合格孔的出现。
毛坯底面加工规范
作底面加工的基准面一.
,力求高度线等高度线检测高度毛坯基准线,也称等高线百位线)(,20mm,50mm
。
大型模若无法一致应取整数差加工标准垫块作为高度补差作到基准面等高),(,
每天进步一
点点
长城汽车模具中心
为底面加工作基准时应考虑正面加工各重要位置的加工余量,板长以上)(3.5m
正面各位置尺寸无法按底面以避免底面加工完后找正试切余量可重设定中心,,,
基准坐标加工出来。
工件翻面加工底面二.
按工件装夹规范和工件找正及定位规范找正定中心A
盘型ф盘型刀具去除大余量筋条部分用山特维克用国产D63CoroMillB125365,
盘刀加工。
刀具加工或用戴杰多功能ф80
立铣精或ф快速定位键加工,用ф钻铣粗铣留余量单边。
ф260.5mm16C20
略。
。
附程序加工,用检棒检测,槽宽公差-32+0.01+0.03
ф(新干线)钻铣开槽,用压板槽加工,未铸出压板槽的采用ф或ф402632D
略。
对应白钢立铣刀具过槽。
附程序或ф-30
压板面加工:
用三面刃铣刀加工(注意刀具刀杆干涉问题)E
正面加工有干涉有难度的再次查看图纸,确认需从底面加工的其它部位如:
1`F
图纸注明须从底面加工的部位(安装面导向装置导向孔,导向面侧销面等。
`,2
。
注意周全考虑不得漏项。
,弹簧孔,侧销面等等)
长两作无法使用快速定位键定位工件的基准面,在长边相隔最远处铣约G40mm
处基准面,再在其垂直边做一基准面,记录所铣基准面的位置尺寸,打钢印标记。
超轻快盘刀精ф松开工件压力点螺母,检查支撑点受力情况,用或ф160125H
以内。
小工件可适当施加工底面,切深在以内,要求平面精度在0.3mm0.05mm
加压板压力和应用侧顶装置,避免工件移动。
三、注意事项:
工件底面加沙,硬度不均等异常切削条件对刀具的影响。
局部问题可采用A
每天进步一
点点
长城汽车模具中心
。
ф钻铣消除异常面,可略低于实际加工面小刀具,如0.1mm30
底面精加工时支撑物必须均衡受力。
B
一次底面精加工若不能达到其精度,应考虑采用:
C
加工。
量表测出表面高度差数值,反向切深为前次高度差值加1.0.05mm
若出现局部偏差,可针对局部去除高度差值部分。
2.
结构面加工
。
按底面定位键槽定位,定中心,装夹工件(无定位键槽者按基准边定中心)一.
平面上的重要加工部位(如:
导板、挡墙等)的加工余量,且加工二.检验XY
以内,如出现严重超差应考虑局部加垫,底面余量应均匀。
可允许最大偏差5mm
压板槽等)重做等异常现象。
(快速定位键加工位置.
盘铣刀对刀后在较宽敞的加工平面(一般在模φ三做向加工基准面:
用.Z63
具限位器安装面,中央调整块等处)上铣出一基准面,作为后序结构面加工的高
。
量)加-留精工余(此面的加工按图纸尺寸抬高度依据。
1mm0.5
导板面加工
为确保导板精确的位置度、垂直度,达到导板的加工要求。
一.导板粗加工
加工范围及选用刀具:
玉φ①无干涉高度在以下的导板面采用大直径粗加工刀具(φ、200mm5063
。
米铣、φ波刃立铣刀)切宽5mm50
新干线层切加工(注意新干φ的,采用②加工导板面刀具悬伸大于63200mm
。
线切深一般不应超过)1.5mm
③狭窄导板面加工
每天进步一
点点
长城汽车模具中心
钻铣层切加工。
钻铣或φ采用φ32a.26
之间。
粗加工留余量在-b.0.3mm0.2
具有挂台的导板面应严格控制挂台高度以备精插加工时使用。
c.
二.加工导板面左右有干涉的部位,防止精加工时对刀具的损坏(特别是精插
。
具)铣刀
三.导板面精加工:
加工范围及选用刀具
硬质合金精加工立铣刀左右可以加工的导板面采用φ①.刀具悬深50150mm
具往复三次走刀即可。
此种刀具应特别注意刀具直径的大小,切削进给速度,主轴
转速加工次数和加工材料的变化,对导板加工精度的影响。
为避免不定因素特定:
刀具专用,进给,转速不易随意更改。
精插铣刀具加工,应特别注φ②.长悬深的导板面加工刀具,采用φ或8063
意到底高度的控制以及结束位置的控制,避免碰撞。
程序不得单使用无限循环,必
须使用调用方式。
镜面直角铣刀横向往复加工。
φ③.狭窄导板面加工采用32
定位,垂直度测量,垂直度要求:
四.导板面位置测量以过切-0.06mm0.03
以内。
长以下导板在以内,其它须控制在0.01mm0.02mm150mm
挡墙安装面加工
安装位置准确无干涉平面度达要求,挡墙垂直度高,为部件装配创造条件。
安装面粗加工:
根据平面大小和干涉高度选用合适盘铣刀具,在良好避让干一.
国产φ涉条件下选配刀具应力求短而粗壮,大平面无高度方向干涉问题的选用125
盘刀开粗盘刀开粗,切深-。
其他可选用山特维克5D637mmCOROMILL390
余量待精加工。
-切深,也可采用多功能盘刀加工,留0.17mm0.5mm
挡墙面粗加工:
根据干涉高度选用合适盘铣刀具刀杆,采用山特维克二.
每天进步一
点点
长城汽车模具中心
余量待,切宽,留-盘刀加工,切深5mm0.5mmCOROMILL390D630.19mm
精加工,注意刀杆悬深长度与切削条件的密切关系。
波刃立铣,小直径钻铣清除,也可预先钻清角三.去除角落加工面:
采用φ50
即可。
孔,孔深为钻肩穿过此加工面1mm
盘刀精加工安装面加四.安装面精加工:
采用山特维克D63290COROMILL
加工底面,。
挡墙处可按挡墙尺寸缩小-工,切深-,切宽5mm0.10.10.5mm0.2mm
。
安装面相对位置精