铜丝与低碳钢焊接组织性能研究初稿.docx
《铜丝与低碳钢焊接组织性能研究初稿.docx》由会员分享,可在线阅读,更多相关《铜丝与低碳钢焊接组织性能研究初稿.docx(27页珍藏版)》请在冰豆网上搜索。
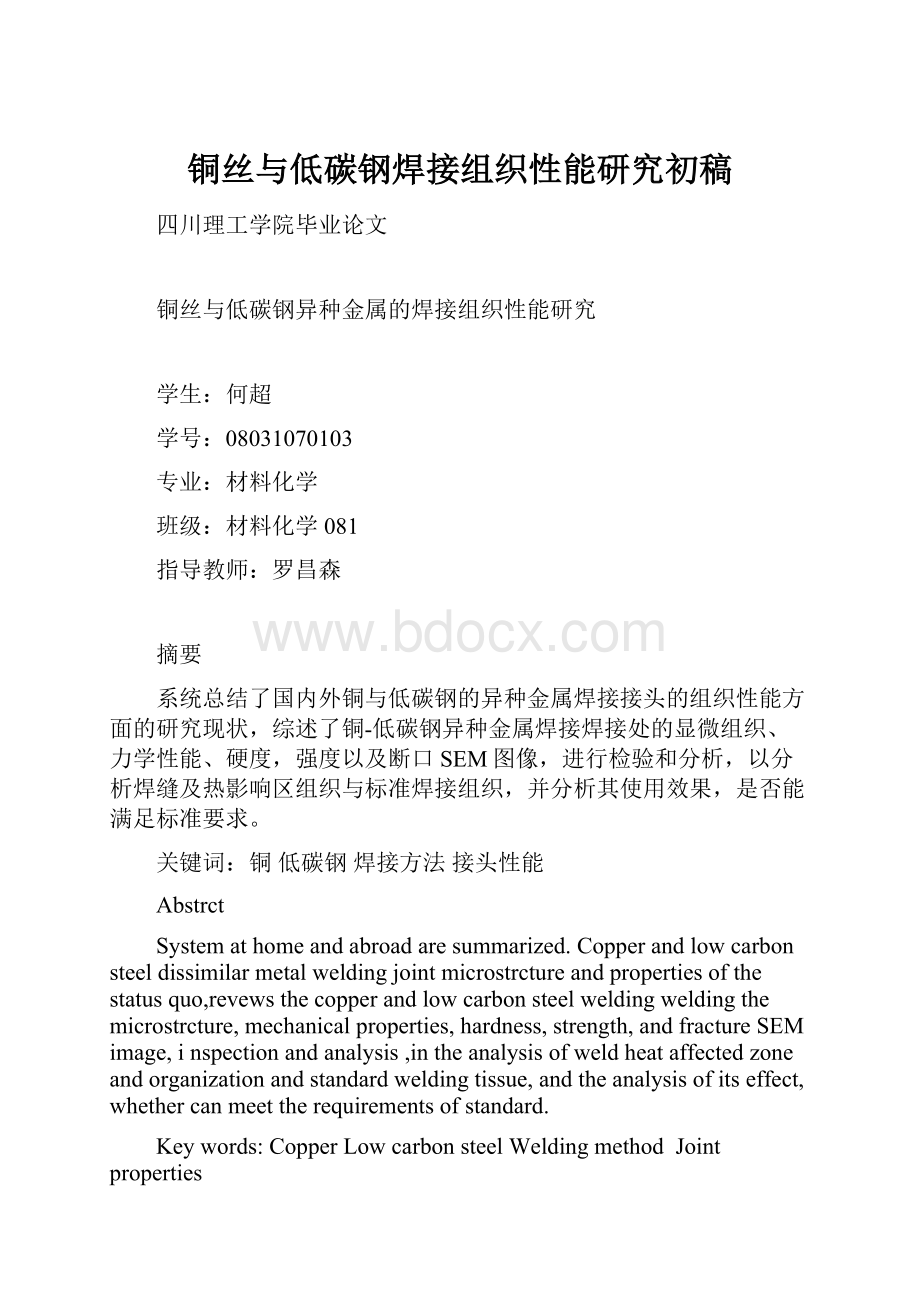
铜丝与低碳钢焊接组织性能研究初稿
四川理工学院毕业论文
铜丝与低碳钢异种金属的焊接组织性能研究
学生:
何超
学号:
08031070103
专业:
材料化学
班级:
材料化学081
指导教师:
罗昌森
摘要
系统总结了国内外铜与低碳钢的异种金属焊接接头的组织性能方面的研究现状,综述了铜-低碳钢异种金属焊接焊接处的显微组织、力学性能、硬度,强度以及断口SEM图像,进行检验和分析,以分析焊缝及热影响区组织与标准焊接组织,并分析其使用效果,是否能满足标准要求。
关键词:
铜低碳钢焊接方法接头性能
Abstrct
Systemathomeandabroadaresummarized.Copperandlowcarbonsteeldissimilarmetalweldingjointmicrostrctureandpropertiesofthestatusquo,revewsthecopperandlowcarbonsteelweldingweldingthemicrostrcture,mechanicalproperties,hardness,strength,andfractureSEMimage,inspectionandanalysis,intheanalysisofweldheataffectedzoneandorganizationandstandardweldingtissue,andtheanalysisofitseffect,whethercanmeettherequirementsofstandard.
Keywords:
CopperLowcarbonsteelWeldingmethodJointproperties
第一章绪论
1.1课题背景及研究意义
现代机器制造业最迫切的问题之一是在提高结构和设备工作技术性能和可靠性的同时,降低金属消耗量。
随着国民经济的迅速发展和科学技术的不断进步,新结构、新设备、新设备层出不穷,新材料、新工艺的应用日益广泛,对零部件的性能有了更高的要求,如硬度、耐磨性、耐蚀性、低温韧性、高温持久强度、磁性、导电性、导热性、熔点等多方面的性能。
在有些情况下,任何一种金属材料都不可能完全满足使用要求,或者即使某种金属比较理想,也往往由于十分稀贵,不能在工程中普遍应用[1]。
现代焊接技术的发展已经可以将不同性能的材料焊接成复合零件件,既能满足各种性能要求,又可节约各种贵重材料,降低成本。
一方面钢与铜或钢合金连接可以形成能满足各种特殊需求的金属结构,特别是要求既具有高强度,又要有高导电和导热性能的工件;另一方面,在钢上堆焊铜合金可以改善工件表面的性能,如提高耐磨耐蚀性能,增强润滑和密封性能等。
通常需要涉及到铜-钢异种金属的焊接[2]。
因此,采用焊接方法制造异类材料复合零部件受到人们的广泛重视,采用钢-铜复合部零件,在性能和经济上优势互补,因而在航空航天、核电站、机电、化工、冶金等工艺制造中具有广阔的应用前景。
本课题主要针对铜丝与低碳钢异种金属的焊接的组织性能方面的研究。
通过对铜-钢焊接件的镶样磨制,借助于金相显微镜(SEM)和维氏硬度计分别对焊接接头的组织和显微硬度的比较,以分析焊缝及热影响区组织与标准焊接组织,并分析其使用效果,是否能满足标准要求。
1.2铜-钢异种金属焊接的概述
1.2.1焊接母材选用
焊接母材采用的是紫铜T2、低碳钢Q235和新型低合金钢。
母材的化学成分如表1.2.1a、1.2.1b、1.2.1c
表1.2.1a紫铜T2的化学成分
牌号
化学成分(质量分数)(%)
Cu+Ag
Bi
Sb
As
Fe
Pb
Sn
O
Zn
Ni
T2
≥99.90
≤0.001
≤0.002
≤0.002
≤0.005
≤0.005
≤0.002
≤0.006
≤0.005
≤0.005
表1.2.1bQ235的化学成分
牌号
等级
Q235的化学成分(质量分数)(%)
C
Mn
Si
S
P
Q235
A
0.14~0.22
0.30~0.65
≤0.30
≤0.050
≤0.045
B
0.12~0.20
0.30~0.70
≤0.045
C
≤0.18
0.35~0.80
≤0.040
≤0.040
D
≤0.17
≤0.035
≤0.035
表1.2.1c新型低合金钢丝的化学成分
化学元素
化学成分(质量分数)(%)
C
Mn
Si
Ni
Cr
Mo
含量
≤0.010
0.40~0.70
≤0.050
≤0.060
4.5~6.0
0.45~0.65
1.2.2铜-钢焊接特点
铜丝与低碳钢异种金属的焊接属于异种材料之间的焊接。
Fe与Cu在液态时无限互溶,固态时有限互溶,不形成金属间化合物而是以(α+ε)双相固熔体组织存在;当Fe向Cu扩散时,形成有限溶解度得ε固熔体。
铜及铜合金与铁的熔点,热导率,线膨胀系数,力学性能等存在很大的不同,这对焊接是非常不利的。
但Fe与Cu的化学性能如原子序数,晶格类型,点阵常数及最外层电子数等都比较接近,这对铜与钢的焊接来说,又是较为有利的[3]。
1.2.3铜-钢焊接性分析
对比铜-铁元素的各种性能参数(见表1.2.3a和表1.2.3b)
Fe和Cu的物理性能表1.2.3a
化学元素
比重
(g/cm3)
熔点
(℃)
比热
﹝J/(kg.K)﹞
导热系数
﹝W/(m.K)﹞
线膨胀系数(10-6K-1)
电阻系数
(10-6Ω.m)
Fe
7.87
1537
481.5
66.7
11.76
10.1
Cu
8.92
1084
376.8
359.2
16.6
1.67
Fe和Cu的化学性能表1.2.3b
化学元素
原子序数
原子量
原子半径
(nm)
原子外层电子数目
点阵类型
点阵常数
(nm)
Fe
26
55.85
0.127
2
体心立方(α-Fe)
面心立方(γ-Fe)
体心立方(δ-Fe)
aα=0.2860
aγ=0.3668
Cu
29
63.54
0.128
1
面心立方
a=0.365
二元相图(图1.2.2)可以看出,在高温下,他们的原子半径、晶体类型、晶格常数、原子外层电子数等都比较接近。
并且,在液相中能相互无限固溶;在固态下,虽为有限固溶,但并不想成脆性金属间化合物,而是以(α+ε)的双相组织形式存在,其中α相是Cu(<0.3%)在铁中的固溶体,ε相为Fe(<0.2%)在铜中的固溶体。
这些都是实现钢与铜合金之间焊接的有利因素。
但是这两种材料的导热系数、热膨胀系数、熔点等又存在较大的差异,容易在焊接接头中产生应力集中,导致各种焊接裂纹,这又对获得优质接头非常不利,造成焊接困难。
Cu-Fe二元相图图1.2.2
焊接钢与铜或铜合金接头的方法主要有熔化焊和固相压力焊。
当用铜焊丝在钢表面进行熔化堆焊时,由于母材中Fe、Cr、Ni等元素的溶入,以及氧与铜的强烈亲和作用和多种低熔共晶体得存在,常常使焊缝金属区脆化,导致铜未焊透、气孔、夹杂、裂纹和烧穿等,施焊处结晶组织区晶粒粗大。
另外,在焊接过程中,液态铜或铜合金向所接触的近缝区钢表层渗透,即沿微裂纹浸润深入以及沿晶界扩散发展等,形成所谓的“渗透裂纹”,是熔化焊的另一个主要问题[4~10]。
1.2.4铜-钢异种金属焊接存在的主要问题
(1)焊缝易产生热裂纹。
这与低熔共晶、晶界偏析以及铜与钢的线膨胀系数相差较大有关,在焊缝中出现晶界偏析,即低熔点共晶合金或是铜的偏析,因而焊接时,在较大的焊接应力作用下,容易出现宏观裂纹。
(2)热影响区产生铜的渗透裂纹。
铜及铜合金与钢焊接时对铜的渗透裂纹十分敏感。
尤其是焊接融合区和热影响区更容易产生裂纹,甚至发生断裂。
为防止渗透裂纹产生,首先要合理选择焊接工艺,选用小的焊接线能量;其次是选择合适的填充材料,控制易产生低熔共晶的元素(S、P、Cu2O、FeS、FeP、),向焊缝中加入Al、Si、Mn、Ti、V、Mo、Ni等元素[9]。
(3)气孔倾向严重
铜-钢焊接时,容易产生气孔,其主要原因是过量氢的存在导致的。
(4)接头力学性能低。
由于铜与钢的种类不同,焊接接头的组织与性能也不同,在焊接过程中热作用之下,晶粒严重长大,杂质和合金元素的渗入,有用合金元素的氧化,各种脆性的低熔共晶体出现于晶界,或产生脆性相,使接头的塑性、韧性、耐蚀性、导电导热性等大幅下降[10]
1.2.5铜-钢焊接防止裂纹的措施
(1)选用异种铜和钢均具有良好焊接性的金属,如选用镍基焊条或镍铜合金焊丝作为焊接材料。
(2)预先堆焊过渡层把及铜合金母材,钢母材或同时在两母材的坡口平面上预先堆焊过渡层,然后再进行焊接。
这种堆焊的过渡层材料以镍及镍合金为好。
(3)采用铜复合钢作为中间过渡母材以钢为基层,铜及其合金为覆层,用爆炸焊的方法制成铜复合钢,然后将母材与铜钢的基层焊在一起,以及将铜及铜合金与铜复合钢的覆层作为同种材料焊在一起[3]。
1.3铜和钢焊接在国内外的发展状况
铜与钢的异种金属之间的焊接研究一直是国内外学术界和工业界共同关注的热点前缘课题,已做了大量的工作,积累了丰富的理论知识和实践经验。
但由于铜与钢的焊接还存在许多问题没有得到解决或还须进一步的研究。
在铜与钢的的焊接中能否满足工程上复杂工况下的功能要求,关键是要解决他们的焊接性问题,核心其实就是接头熔合区或过渡区得行为和性能,随着现代新材料和新型复合结构的大量出现,研究铜钢异种金属焊接熔合区的显微结构特征及其转变机理就显得尤为突出和重要。
因铜与钢的焊接不仅充分发挥了材料各自的作用和性能,达到了充分利用的目的,而且大大节省了材料,降低了能耗。
利用铜和钢的各自性能特点,通过焊接的方法制造出了许多性能优异的焊接件在航天,核动力,船舶,石油化工等方面已获得了越来越多的应用。
1.3.2铜及铜合金在国内外的发展状况及应用
铜及铜合金是古老而又年轻的有色金属,伴随着中华民族五千多年的历史沧桑,成为了我国古代文明史的重要组成部分,在古代我们的先辈就铸造出了铜刀。
蒸汽时代时,铜产品的加工生产由手工制造转向了半机械化的生产方式。
随着科学技术的进步和发展,铜及铜合金加工技术由半机械化向机械化合自动化发展。
在20世纪80年代,铜及铜合金加工理论取得了很多的新成果的同时,新工艺、新技术和新产品也相继出现了。
纯铜呈紫色又名为紫铜。
纯铜的的密度为8.96,熔点1083℃,具有优良的导电导热性、延伸性及耐蚀性。
主要应用于发电机,电线等带电装置。
本次实验采用的就是紫铜。
常用的铜合金按合金成分分为青铜(Cu-Sn)、黄铜(Cu-Zn)、白铜(Cu-Ni)三大类。
铜及铜合金适用于塑性加工和铸造加工的有色金属。
目前已在航天航空、电子信息、能源化工、建筑和交通方面得到了广泛的应用。
我国的铜及铜合金的加工产业发展速度较快,铜及铜合金的加工产量已居世界首位[]。
1.3.2低碳钢在国内外的发展状况及应用领域
低碳钢的硬度和强度较低,塑性和韧性较好,具有很好塑性加工性能,焊接接头产生裂纹的倾向小,适合制造各类大型结构件和受压容器。
原先由低碳钢固有的特性,使其使用范围大大受限,随着科学技术的不断发展,低碳钢的许多新型用途得到了很好的开发利用。
依据低碳钢的优异性能,在吊索具、汽车制造领域等得到了广泛的应用
1.4焊接方法
铜-钢的焊接方法很多,各种方法都有其各自的特点,在焊接过程中会产生不同的物理化学变化,选择焊接方法的目的之一就是要使其适应这种变化,以获得优质接头。
目前常常的熔化焊中的手工电弧焊,埋弧自动焊,钨极气体保护焊,固相焊中的爆炸焊和扩散焊。
1.4.1熔焊
钢与铜焊接时经常发生铜渗透到钢晶粒之间,产生热应力,使焊缝发生断裂且合金元素易蒸发,烧损等,同时焊缝中的锡、铅等元素的偏析,因此需要熔化焊这种特殊的工艺。
1)电弧焊
电弧焊是利用焊条与工件之间产生的电弧将焊条和工件局部加热到融化状态,焊条端部融化后的熔滴和融化后的母材融合到一起形成熔池。
随着电弧向前移动,熔池逐步冷却结晶形成焊缝金属。
埋弧焊一般分为手工电弧焊、半自动电弧焊和自动电弧焊。
自动电弧焊一般是指埋弧自动焊在焊接部位的焊剂层,有填充金属制成的光焊丝插入焊剂层,与焊接金属材料产生电弧,电弧产生的热量熔化焊丝、焊剂和母材金属形成焊缝,在这一系列的过程是自动进行的。
手工电弧焊使用的设备简单,方法简单灵活,适应性强,应用范围极为广泛,有单层焊、双面焊和多层焊接头,是熔焊中最常见的焊接方法。
但采用手工电弧焊也存在一些问题如易产生裂纹、气孔、偏析等缺陷[7]
2)埋弧焊
埋弧焊也是利用电弧作为热源的焊接方法,但其电弧是在一层颗粒状的可融化焊剂的覆盖下燃烧,电弧光不外漏,所用的金属电极是不间断送进的裸焊丝。
电弧热将焊丝断布及电弧附近的母材和焊剂融化。
融化的金属形成熔池,冷却后成为焊缝,融化的焊剂成为熔渣,凝固后成渣覆盖与焊缝表面。
熔池受熔渣和焊接蒸汽的保护,不会与空气接触。
另外,在焊接过程中,熔渣还与融化金属发生冶金反应,从而影响焊缝金属的化学成分。
埋弧焊的特点是热效率高,熔深大,机械化操作程度高。
焊接质量稳定,在许多机械行业中均有广泛的应用,是当今焊接生产中最普遍使用的焊接方法之一。
3)钨极气体保护焊
钨极气体保护焊是在惰性气体保护下,利用钨电极与工件之间产生的电弧热熔化母材和填充焊丝的异种焊接方法。
焊接时保护气体从焊枪喷嘴中连续喷出,在电弧周围形成气体保护层隔绝空气,以防止其对钨极、熔池及邻近热影响区得有害影响,从而可获得优质接头。
用氩气作保护气体的钨极氩弧焊(TIG)在铜-钢异种焊接中应用最为普遍。
钨极氩弧焊主要分为手工焊、半自动焊和自动焊三类。
在焊接工艺上具有电弧稳定,热输入易调节、焊缝成型美观、容易实现全位置自动化焊接以及焊接易氧化、氮化、化学活性强的有色金属和不锈钢等特点和优越性。
采用钨极氩弧焊(TIG)实现铜-钢之间的焊接,一方面由于氩气是惰性气体,不会和焊接金属起化学反应,同时又不溶于液态的焊接金属,合金元素不会受损,也不容易由氢引起的气孔,而且氩气比空气重,能形成坚实的氩气隔离层,可获得优质的焊接接头;另一方面氩气在弧柱中能产生正离子,使其质量和动能都比较大,在电弧场得作用下,向阴极告诉移动,当工件为负极时,受正离子的撞击,能破坏掉接头表面的氧化膜,起到清理的作用。
1.4.2固相焊
1).爆炸焊
爆炸焊[]是焊接加工领域中的一种特殊加工工艺,在大面积板材的焊接,过渡接头的焊接,管材或管与板得焊接中,具有操作简便,省时省力等优点。
爆炸焊接是利用炸药产生的冲击力造成焊接迅速碰撞,使其两种金属件待焊表面实现连接的方法。
爆炸焊的基本原理是:
将基板放在固定的支座上,覆盖平行或以一定的夹角放在基板上方,覆盖上表面隔橡胶类缓冲层撒敷炸药。
当炸药引爆时,瞬间释放的化学能直接传递到覆盖并转化为冲击波,使其覆盖以极高的速度冲向基板,两金属发生猛烈碰撞,接触界面在碰撞点将产生射流。
射流的冲刷作用,清除了金属表面的氧化膜和吸附层,使两个洁净的金属表面相互接触并在高压下紧密结合形成金属键。
随着炸药的连续爆炸,界面将不断向前移,形成连续的爆炸结合面。
2).摩擦焊
摩擦焊是利用焊接接触端面相对旋转运动互相摩擦产生的热,使端部达到热塑性状态,然后迅速顶锻实现连接的一种焊接方法。
摩擦焊可以分为:
搅动摩擦焊、轨道摩擦焊、线性摩擦焊、旋转摩擦焊。
在摩擦焊的过程中,工件在压力的作用下发生机械接触,由工件的转动或相对运动会产生摩擦热和摩擦面上原子发生塑性位移。
在压力和摩擦热的共同作用下,焊接摩擦面上附近的原子被激活,导致了原子扩散加速,表面污染物和氧化层被排除,进而迁移形成连接。
3).扩散焊
扩散焊是将两被焊工件紧压在一起,置于真空或保护气体中加热,使两焊接表面微观凹凸不平处在高温下产生塑性变形达到紧密接触,再经保温、原子相互扩散而形成牢固的冶金连接的一种焊接方法。
在扩散焊中母材不发生融化和宏观塑性变形,温度和压力的主要作用是使焊接表面微观凸起处产生塑性变形而增加紧密接触的面积以及激活原子促进相互扩散。
在铜-钢扩散焊中通常加一个中间扩散层。
中间层材料有钛、镍、银、含铍合金等【1】,加入中间层得目的主要是为了填充间隙与基体的扩散反应,同时由于两端焊接金属材料存在较大的硬度差,加入中间层后合金元素扩散到非合金的中间层,使其接头两端的祖坟和性能保持在最小的梯度。
1.5本课题研究的主要内容及研究步骤
1.5.1主要内容
1,将铜丝与低碳钢异种金属进行焊接后取样,检验其力学性能。
2,重点对焊接处的显微组织、硬度,进行检验和分析,以分析焊缝及热影响区组织与标准焊接组织,并分析其使用效果,是否能满足标准要求。
1.5.2研究步骤
1.将已焊接好的两个焊接件进行镶样
2.试样编号:
编号
试样名称
A
铜丝与低碳钢的焊接组织试样
B
铜丝与合金钢的焊接组织试样
3.观察试样组织:
分别观察A、B两个试样的焊后组织(融合区、焊缝区、粗晶区、细晶区、基体组织)
4.硬度实验:
铜丝与低碳钢焊接后的样品(A、B),利用维氏硬度计分别做维氏硬度测试,分别记录其测试结果。
[1]潘春旭.异种钢及异种金属焊接(M).北京:
人民交通出版社,2000.
[2]王向斌,赵晓红,周石泉,等.T2紫铜与10#钢异种金属电子束焊接工艺研究[J].电子焊机,2005,35
(1):
42~44.
[4]周振风,金属熔焊原理及工艺(下册)。
北京:
机械工业出版社,1981,228~229.
[5]M.C.Mushala,W.F.SavageandE.F.Nippes.Copper-contaminationcrakingintheweldheat-affectedzone.WeldingJournal,1987,57(5):
145~152.
[6]M.C.Mushala,W.F.Nippes.Liquid-metalembrittlementoftheheat-affectzonebyCopper-contaminationcraking.WeldingJournal,1978,57(8):
237~245.
[7]E.F.NippesandD.J.Ball.Copper-contaminationmechanismandcrackinhibitors.WeldingJournal,1982,61(3):
75~81
[8]高慧玲,安煦,铝青铜的融化极氩弧堆焊,焊接,1986,(12):
15~19
[9]顾德嘉,何世柏,赵立稳,HSn621与1Cr18Ni9Ti钢焊接的铜渗透裂纹,焊接,1986,(8):
6~9
[10]李亚江,王娟,刘强等,有色金属焊接及应用(M)化学工业出版社,2006(3)160~261
[11]D.拉达伊.焊接热效应【M】.北京:
机械工业出版社,1997.
第二章实验方法设备与材料
2.1实验器材
2.1.1实验材料
厚度为2mm的铜丝和钢丝的双丝焊件(A为低碳钢与铜的双丝焊件,B为合金钢与铜的双丝焊件)。
2.1.2药品
3%酒精硝酸,王水,无水酒精,蒸馏水。
2.1.3实验仪器
本次实验所用的主要仪器及型号如表2.1
表2.1主要仪器及型号
仪器(材料)名称
型号
产地
金相试纸
120、320、600、800等不同号试纸
无锡市港下精密砂纸厂
金相试样镶嵌机
XQ-1
莱州市蔚仪试验器械有限公司
金相试样抛光机
P-2
上海电机专用机械厂
金相显微镜
NIKONEPIPHOT200
莱州华银实验仪器有限公司
显微硬度计
HV-5
日本
逆变直流氩弧焊电焊机
TIG-135A
。
。
。
。
。
2.2实验方法
2.2.1实验流程
实验流程如图2.2
2.2.2检测
(1)金相检测:
借助于金相显微镜分别观察A、B两个试样的焊后组织。
(2)硬度检测:
利用维氏硬度计分别对A、B两个试样做维氏硬度测试,并记录其测试结果。
2.3检测过程及原理
2.3.1试样镶嵌
实验样品为铜-钢异种金属双丝焊接件,焊丝直径为2mm,由于是异种钢焊接接头,两边组织情况不一样,所以制作样品时,只需保证一边截取一半的样品且包含所需的焊接接头组织即可。
截取样品时应保证足够长度,但试样太长将导致试样无法进行镶嵌,故本次实验截取样品长度约为1.5cm。
镶嵌好的试样如图2.3.1
低碳钢+铜丝焊件合金钢+铜丝焊件
镶嵌步骤如下:
1.拧松螺母,打开盖板,转动手柄,使下模上升到放置试样的位置。
用夹子夹住试样,将试样的被观察面朝下,平稳的放在下模的中央位置。
2.转动手柄,使载着试样的下模在模套中下降,用小匙将镶料倒入镶嵌机的加料口。
然后把上模放入镶嵌机的模套,并用手将它全部压入加料口内。
最后推动盖板,盖紧加料口。
3.将定时开关放在ON位置,打开电源开关。
4.温度设定:
按SET键,再∧或者∨键,可以进入SV设定状态,设定温度为145,设定完毕后按SET键。
5.加压,加热。
中途应保持压力灯始终亮起。
到145度左右停止加热,冷却至60度下即可取出试样。
6.将镶嵌机周围打扫清洁,并整理好工具,完成整个镶嵌操作。
注意:
镶嵌过程中不可中途离开,时刻注意镶嵌的温度和压力灯
2.3.2金相试样磨制
金相试样磨制是很关键的步骤,磨制质量的好坏直接决定了金相试样的好坏及后期实验的效果。
粗磨一般是金相试样磨制的第一道工序,将试样的一面用120#粗砂纸磨成平面,磨制时要使试样受力均匀。
将粗磨好的试样用清水冲干,接下来就开始细磨工序。
依次用120#、200#、240#、280#、320#、400#、600#、800#金相砂纸把磨面磨光,磨制过程中用力要均匀、平稳。
注意事项:
①磨制时应把砂纸放在玻璃板上(平整的桌面上),在往返推磨的过程中,应保持正确的手势,并始终保持一个姿势;②在往返推磨过程中用力应均匀,磨制速度要平稳;③下一道的磨痕方向应垂直于上一道的磨痕方向,直到将上一道的磨痕全部磨除;④以铁素体为主的焊接试样或奥氏体不锈钢及有色金属软金属焊接试样,在磨制时用力应更轻,速度应更慢。
2.3.3金相试样抛光
为了尽快的把磨制工序留下的损伤层除去,都要进行抛光阶段。
在经过金相砂纸细磨后的试样表面,仍然存在或多或少的表面磨损层,同时在表面上也存在细磨痕或脏东西。
所以必须对试样表面进行抛光,才能满足显微组织的显示要求,本次实验采用的是机械抛光。
机械抛光分两步进行,一是粗抛,以最大的抛光速率去除表面磨损层;二是精抛,去除粗抛产生的表面损伤,使抛光损伤降至最低。
抛光前要准备抛光所需的抛光粉,本次实验用是Al2O3粉末悬浮水溶液。
抛光操作步骤:
1)开启抛光机,使抛光机转动。
2)与试样磨制时的手抓姿势一样,将磨痕的方向与抛光机的旋转方向垂直,方便抛光操作及质量的检查。
接着把磨面轻压在抛光盘外面除去较粗的磨痕。
3)抛光一定时间后(大约30s)观察抛光面,如果观察到多数的深划痕已经被抛浅,继续抛时,可将试样在盘上按圆形轨迹抛光。
4)当抛光试样只有少量的浅划痕时,将试样移至抛光盘中央,降低抛光速