数字射线检测焊接缺陷的模式识别算法.docx
《数字射线检测焊接缺陷的模式识别算法.docx》由会员分享,可在线阅读,更多相关《数字射线检测焊接缺陷的模式识别算法.docx(9页珍藏版)》请在冰豆网上搜索。
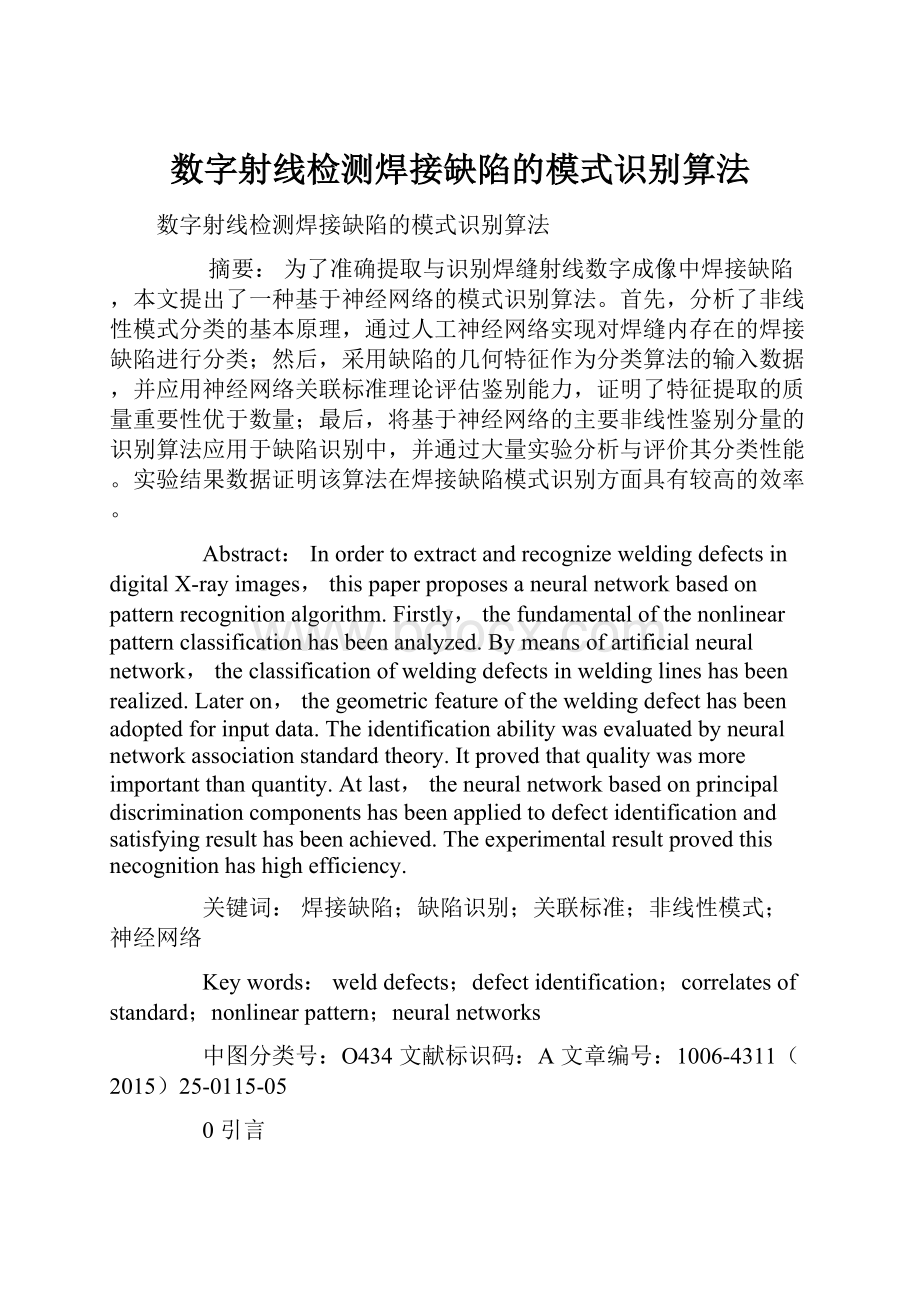
数字射线检测焊接缺陷的模式识别算法
数字射线检测焊接缺陷的模式识别算法
摘要:
为了准确提取与识别焊缝射线数字成像中焊接缺陷,本文提出了一种基于神经网络的模式识别算法。
首先,分析了非线性模式分类的基本原理,通过人工神经网络实现对焊缝内存在的焊接缺陷进行分类;然后,采用缺陷的几何特征作为分类算法的输入数据,并应用神经网络关联标准理论评估鉴别能力,证明了特征提取的质量重要性优于数量;最后,将基于神经网络的主要非线性鉴别分量的识别算法应用于缺陷识别中,并通过大量实验分析与评价其分类性能。
实验结果数据证明该算法在焊接缺陷模式识别方面具有较高的效率。
Abstract:
InordertoextractandrecognizeweldingdefectsindigitalX-rayimages,thispaperproposesaneuralnetworkbasedonpatternrecognitionalgorithm.Firstly,thefundamentalofthenonlinearpatternclassificationhasbeenanalyzed.Bymeansofartificialneuralnetwork,theclassificationofweldingdefectsinweldinglineshasbeenrealized.Lateron,thegeometricfeatureoftheweldingdefecthasbeenadoptedforinputdata.Theidentificationabilitywasevaluatedbyneuralnetworkassociationstandardtheory.Itprovedthatqualitywasmoreimportantthanquantity.Atlast,theneuralnetworkbasedonprincipaldiscriminationcomponentshasbeenappliedtodefectidentificationandsatisfyingresulthasbeenachieved.Theexperimentalresultprovedthisnecognitionhashighefficiency.
关键词:
焊接缺陷;缺陷识别;关联标准;非线性模式;神经网络
Keywords:
welddefects;defectidentification;correlatesofstandard;nonlinearpattern;neuralnetworks
中图分类号:
O434文献标识码:
A文章编号:
1006-4311(2015)25-0115-05
0引言
数字射线检测较其他方法而言具有较高的图像精度。
目前,在对焊接质量进行评价时,尚需采用传统方法,如检验员的目测。
这种方法对经验要求较高,发生错误的概率也较高[1-2]。
对于数字射线检测缺陷的分类,也有数字智能化的算法应用。
其自动检测步骤大致如下:
第一,胶片图像数字化或直接进行数字射线图像生成;第二,图像的预处理;第三,焊缝缺陷的识别和分类;最后,检验结果的获取与后处理。
本文使用线性分类算法将神经关联的标准用于研究各种缺陷特征,并证明了特征提取的质量重要性优于数量,以提高分类成功的概率。
主要鉴别分量(PCD:
PrincipalComponentsofDiscrimination)算法在其它研究领域比较常用。
采用此算法,通过神经网络执行,用于减少输入维数,并且对等级分离区的二维性进行可视化。
1模式识别及分类算法
1.1缺陷特征的提取
数字射线图像的噪声一般作为随机分散的像素出现,并且相邻像素值并没有耦合特征。
低通滤波器一般用于降低噪声,采用直方图均衡或拉伸的算法对对比度进行优化。
从而提高图像的对比度,更容易地检测到焊缝和缺陷[3-4]。
图像进行预处理之后,需要提取焊缝的形状和位置特征。
文献[5]提取了10种特征,开发了自动焊缝射线照片检验系统。
文献[6]提出采用10种焊接缺陷特征,将特征用于缺陷识别,需要比分类器图像像素处理更少的信息。
但是需要非常大的输入空间,计算较为复杂。
本文算法采用四种特征形成系列非线性模式分类数据输入,如下:
①位置(P=h/H):
缺陷到焊缝中心的距离(h)之间与发生缺陷的焊缝厚度(H)之比。
H用于求焊缝厚度变化的平均值,此类变化经常出现在焊缝射线照片中。
②长宽比(a=L/e):
小椭圆的长轴(L)与短轴(e)的比率,相当于此缺陷的面积。
③比例e/A:
短轴(e)与缺陷面积(A)之比。
④浑圆度(p2/4πA):
缺陷的周长p的乘方与缺陷面积A的4π倍之比。
采用上述特征,形成用于神经网络(输入矢量)的输入数据集。
1.2基于神经网络的非线性模式分类及关联标准
本文采用双层神经网络模型,分别为中间层和输出层。
通过调整中间层神经元的数量,跟踪输出性能和误差,确定最佳神经元数量。
得到的结果用神经元数量与误差分类性能图进行表示。
在模式分类的一种网络中,输出层中的神经元数量对应进行研究的等级数量。
在此情况下,输出包含四个神经元,考虑只有包含一种级别;若输出包含五个神经元,则考虑只有包含两种级别,并且将此夹渣等级分为两种等级:
线性和非线性夹渣。
所有神经元在一定范围内都是双曲正切型。
输入矢量是一个四维向量,在算法执行中,根据关联标准可降维为3、2或1。
本文采用文献[7]中所述关联标准得到的新结果。
此标准基于对网络回复中的变化进行搜索,此时使用的特征用其平均值进行代替。
网络回复之间的差异越大,特征的关联就越大[7-9]。
将此标准用于评价原来采用的六种特征,由于分类器为线性的,并且只通过双曲正切型神经元执行。
采用方程式对关联的标准进行计算如式
(1)所示。
R(xi)=■■■■(■j)-■(■j,i)■■
(1)
其中,R(xi):
输入矢量■i的分量■的关联;
N:
模式的数量;
■(■j):
神经网络的输出矢量,用于输入的每种模式xi;
■ji:
输入矢量■j,其中第i个分量用其平均值进行代替,并且基于所有输入矢量;
■(■ji):
网络的输出,用于输入■ji。
针对使用的每种特征计算相关参数后,得到的结果如表1所示。
1.3非线性分类的主要分量分析
主要分量分析(PCA:
PrincipalComponentsAnalysis)是一系列多变量数据的有效精简技术之一。
它将多维数据通过线性映射在低维中的一种技术,从而减少信息的损失。
但是,由于它是一种线性映射方法,故并不适用于非线性的工程问题中。
因此,需要借助于主要非线性分量的分析[10-12]。
形成主要分量的方法之一就是采用人工神经网络,可以用于减少表示分量。
本文借助主要分量用于非线性鉴别,通过神经网络执行,并且已通过误差反向传播算法进行开发,步骤如下:
首先,将模为n的矢量■的模式分类系统作为输入,那么为了减少输入矢量的模,用于模m的矢量■,m(2)所示。
■(dimn)→■(dinm),m(2)
第二,考虑模式分类的问题,矢量■包含m个主要区别分量。
假设这些分量通过分层形式出现,第一个分量通过方向w1(w1=1)中的矢量的正交投影形成,此方向表示数据鉴别的主要方向,如图1所示。
然后,求主要分量p1为■1中■的正交投影,如式(3)所示。
p1=■t■1(3)
其中:
■t:
■的转置;
■1:
矢量,表示鉴别的主要方向。
并且,■只有一种主要分量,如式(4)所示。
■≌p1■1(4)
■1的误差如式(5)所示。
■≌p1■+■(5)
矢量■1表示没有投影在■1方向的■的信息。
矢量■在m分量中的细分如式(6)所示。
■=p1■1+p2■2+p3■3+…+pm■m+■(6)
其中■为残留误差矢量,并采用m个主要分量进行表示。
非线性鉴别的第一个分量由在误差反向传播中训练三层网络中得到。
第一层只包括一种线性神经元,并且其余层为双曲正切型神经元,如图2所示。
三层突触矢量的调整通过梯度下降法进行,并且将均方差函数作为目标函数。
训练后,矢量■1表示研究模式等级的非线性鉴别的主要方向。
确定其余分量的特殊情况为使它们垂直,也就是说,■1⊥■2⊥■3⊥…⊥■m。
因此,通过相同方式得到■1后,网络的重新训练,但是使用的新输入为■1,通过式(5)得到,并且连续地进行,直到分量达到m(一般m在此对这些分量进行分类,作为独立起作用的主要分量,因为每种分量与信息的噪声■j一起起作用,此类信息没有被以前的分量使用,如式(7)所示。
■j=■-■pk■k(7)
得到分量的另一种方式就是考虑采用合作行动过程进行分类,即采用正在计算的分量以及以前已提取的所有其它分量进行分类。
I类:
得到■1后,通过将第二种线性神经元增加到第一层上,就得到第二种分量。
但是,在训练期间使■1保持固定,只训练■2以及其它层的重量。
在此情况下,因为这些分量不是独立的,则输入继续为。
在此情况下的目标是找到最与第一种分量相关的第二种鉴别分量。
同理可得到第三种、第四种和第m种分量,使■1,■2,■3…,■m-1保持稳定。
加快此过程的一种方法是将用作第一种神经元的输入,并且将■j-1用作第一层的第j种线性神经元的输入。
在输入第二层的双曲正切型的每种神经元时,激励为输入网络的线性组合。
II类:
两种分量也可以通过同时训练得到,也就是说,这两种分量在网络训练期间在它们之间进行合作。
通过类似方式可以对3,4或m分量进行相同程序。
在此情况下,形成输入空间减少和优化的基础,用于分类。
在有多维度的数据中,很难显示等级分离问题的规模。
但是,通过采用两种主要非线性鉴别分量,可以对模式等级进行较好的区分。
在此方式中,借助独立起作用的两种,查看一起处理的四种和五种等级的分离图。
这些分量通过图2中的神经网络得到,并且采用反向传播误差、瞬时和可变的学习速率进行训练。
将分量p1用作非线性分类器输入矢量,以便用于评价性能,同时也可以采用通过合作行动的两类训练得到的(p1+p2)独立值以及两个分量。
2实验结果和讨论
2.1非线性模式分类
为了找到用于非线性分类器中间层的最佳神经元数量,采用在此层中逐渐增加神经元数量的经验标准,然后对分类误差和性能进行观测。
同时考虑将夹杂等级分为线性夹杂和非线性夹杂(总共五种等级)如图3(a)所示,若将夹杂只作这一种等级(总共四种等级)如图3(b)所示。
注意在第一种情况中,有五种等级,分类器到达最高性能(99.2%)和最小误差,其训练数据针对中间层中的17/18种神经元。
对于四种等级,通过10种神经元达到最佳性能(100.0%)。
结果表明,只有一件样品没有明确分类。
因此,所有等级的成功概率都大约为100.0%。
咬边等级得到的分布实例如图4所示。
2.2非线性关联标准
根据上述结果,采用这些特征对输入的不同组合进行试验。
图5为针对这些特征组合得到的各种结果。
通过输入矢量a-e/A-P得到的这些结果,不考虑特征R,在两种情况下(四种和五种等级)都等于通过四种特征得到的结果,从而说明输入矢量的维度仍然可以减少为3维,而不会影响分类器的性能。
也对只采用两种特征的可能性进行研究,如图5所示,虽然与使用四种或三种特征相比,性能降低,但是使用非线性分类器时,此分类中的成功率仍然高于90%。
2.3非线性鉴别的主要分量
图6为独立起作用的两种主要非线性鉴别分量的两个二维图。
图6(a)为四种等级的分离,说明咬边和未焊透等级出现在良好定义的区域,因此很容易通过非线性分离器进行分离。
气孔和夹渣等级在图中出现混乱区域,并且夹渣的有些观测值位于气孔区域中。
这在以前采用线性分类器时已检测到,因为误差分类为这些等级的参考数据。
在图6(b)中可以注意到有五种等级,非线性夹渣、线性夹渣与气孔之间的混乱更大,但是这很容易解释,因为夹渣的两种等级之间的区分比较复杂,这是由于其特征类似[13-16]。
图7中的图表表示只采用第一种分量p1作为分类器的输入矢量时得到的性能结果,同时(p1+p2)为独立的分量(二维矢量),并且(p1+p2)为合作的分量(用于两种类型)。
结果表面只采用第一种分量时,有四种等级的训练数据的成功率达到92.0%,在逻辑上有五种等级的更复杂情况的成功率更低(66.4%)。
采用两种分量时,成功率非常接近采用三种或四种特征时达到的成功率。
这还确定使用的分量类型之间的性能没有显著差。
这些结果证明了主要分量减少原始数据维度的效率,并且保持分类成功的较高能力。
对于进行研究的这种情况,没有对将规模从三维或四维降低为二维进行判定。
但是,这些结果将推动通过更大规模的系统进行类似研究。
3结论
本文采用二层神经网络及主要分量分析法对数字射线图像中的焊接缺陷进行分类,实验结果表明,无论是四种还是五种等级(夹渣是否分为线性和非线性),均取得了较高的分类效率,算法适用性较好,不依赖于大量经验数据,具有较好的应用前景。
参考文献:
[1]孔凡琴,路宏年.采用数字射线DR成像的焊接质量检测[J].无损检测,2008,30
(1):
20-22.
[2]梁丽红,孔凡琴,路宏年.X射线非晶硅面阵探测器B级像质的研究[J].无损检测,2005,27(3):
113-116.
[3]张晓光,高顶.射线检测焊接缺陷的提取和自动识别[M].国防工业出版社,2004.
[4]陶亮,孙同景,李振华,等.基于邻域对比度的X射线数字图像自适应增强法[J].无损检测,2011,33
(1):
20-22.
[5]KatoY,OkumuraT,MatsuiS,etal.Developmentofanautomaticwelddefectidentificationsystemforradiographictesting[J].WeldingWord1992,30(7):
182-195.
[6]AokiK,SugaY.Applicationofartificialneuralnetworktodiscriminationofdefecttypeautomaticradiographictestingofwelds[J].ISIInternational,1999,39(10):
1081-1097.
[7]SilvaRR,SiqueiraMHS,CalobaLP,etal.Radiographicspatternrecognitionofweldingdefectsusinglinearclassifiers[J].Insight,2001,43(10):
669-674.
[8]SilvaRR,SiqueiraMHS,CalobaLP,etal.Evaluationoftherelevantcharacteristicparametersofweldingdefectsandprobabilityofcorrectclassificationusinglinearclassifiers[J].Insight,2002,44(10):
616-622.
[9]SilvaRR,SiqueiraMHS,CalobaLP,etal.Contributiontothedevelopmentofaradiographicinspectionautomatedsystem[C].8thEuropeanConferenceonNon-destructiveTesting,June17-21,Paris,2002.
[10]SeixasJM,CalobaLP,DelpinoI.Relevancecriteriaforvarianceselectioninclassifierdesigns[C].InternationalConferenceonEngineeringApplicationsofNeuralNetworks,April4-6,London,1996.
[11]DongD,McAvoyTJ.Nonlinearprincipalcomponentanalysis-basedonprincipalcurvesandneuralnetworks[J].ComputChemEngng,1996,20
(1):
65-78.
[12]AngAHS,TangWH.Probabilityconceptsinengineeringplanninganddesign[J].Basicprinciples,1975,1(5):
575-579.
[13]MeryD,SilvaRR,CalobaLP,etal.Patternrecognitionintheautomaticinspectionofaluminiumcastings[J].Insight,2003,45(7):
1-9.
[14]MeryD,FilbertD.Classificationofpotentialdefectsintheautomaticinspectionofaluminiumcastingsusingstatisticalpatternrecognition[C].8thEuropeanConferenceonNon-DestructiveTesting,June17-21,Barcelona,2002.
[15]BrittenJ,ZhechuanFENG,GuXU.MagnifiedhardX-rayimageinonedimension[J].AppliedPhysicsLetters,2010,96(26):
261907-261907-3.
[16]HUANGKuidong,ZHANGDinghua,LIMingjun.ScatterdetectionandcorrectionmethodofFPD-basedDR/CTimagingsystems[C]//ProceedingsoftheConferenceonElectronicMeasurement&Instruments2009.Beijing:
[s.n.]:
102-105,2009.