毕业设计77江苏大学基于485总线的PLC控制系统设计.docx
《毕业设计77江苏大学基于485总线的PLC控制系统设计.docx》由会员分享,可在线阅读,更多相关《毕业设计77江苏大学基于485总线的PLC控制系统设计.docx(76页珍藏版)》请在冰豆网上搜索。
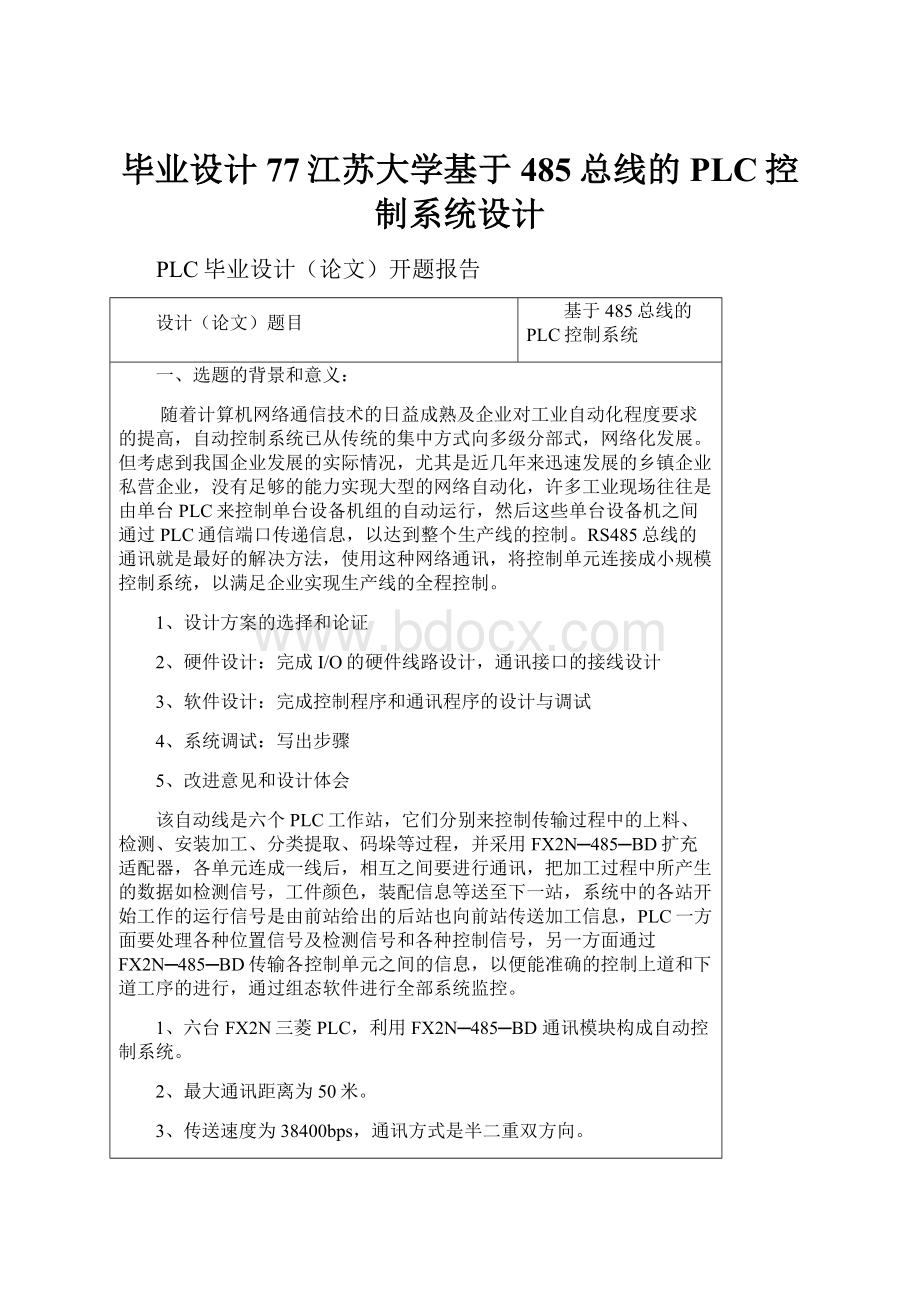
毕业设计77江苏大学基于485总线的PLC控制系统设计
PLC毕业设计(论文)开题报告
设计(论文)题目
基于485总线的PLC控制系统
一、选题的背景和意义:
随着计算机网络通信技术的日益成熟及企业对工业自动化程度要求的提高,自动控制系统已从传统的集中方式向多级分部式,网络化发展。
但考虑到我国企业发展的实际情况,尤其是近几年来迅速发展的乡镇企业私营企业,没有足够的能力实现大型的网络自动化,许多工业现场往往是由单台PLC来控制单台设备机组的自动运行,然后这些单台设备机之间通过PLC通信端口传递信息,以达到整个生产线的控制。
RS485总线的通讯就是最好的解决方法,使用这种网络通讯,将控制单元连接成小规模控制系统,以满足企业实现生产线的全程控制。
1、设计方案的选择和论证
2、硬件设计:
完成I/O的硬件线路设计,通讯接口的接线设计
3、软件设计:
完成控制程序和通讯程序的设计与调试
4、系统调试:
写出步骤
5、改进意见和设计体会
该自动线是六个PLC工作站,它们分别来控制传输过程中的上料、检测、安装加工、分类提取、码垛等过程,并采用FX2N─485─BD扩充适配器,各单元连成一线后,相互之间要进行通讯,把加工过程中所产生的数据如检测信号,工件颜色,装配信息等送至下一站,系统中的各站开始工作的运行信号是由前站给出的后站也向前站传送加工信息,PLC一方面要处理各种位置信号及检测信号和各种控制信号,另一方面通过FX2N─485─BD传输各控制单元之间的信息,以便能准确的控制上道和下道工序的进行,通过组态软件进行全部系统监控。
1、六台FX2N三菱PLC,利用FX2N─485─BD通讯模块构成自动控制系统。
2、最大通讯距离为50米。
3、传送速度为38400bps,通讯方式是半二重双方向。
4、利用组态软件,构成计算机控制系统,动态显示状态变化。
二、课题研究的主要内容:
1、485通讯的原理和程序实现
2、组态软件的应用
3、硬件系统的设计
4、软件系统的设计
5N:
N网络相当于三级总线型结构的中间一级,即控制层,最低一层为远程I/O链路,负责与现场设备通信,收集现场数据,驱动执行器,在远程I/O链路中配置周期I/O通信机制,这一层也可配置AS-I(传感器-执行器接口)链路,除了N:
N网络外,比较通用的有主从总线(1:
N)方式,争用总线方式,令牌环方式,浮动主站(N:
M)方式,目前已存在若干种现场总线,现场总线的体系结构,省略了网络层,传输层,回话层及表示层这四层,包括应用层(APPLICATION),数据链路层(DATALINK),物理层(PHYSICAL),这主要时针对工业过程的特点,使数据在网络流动中尽量减少中间环节,加快数据的传输速度,提高网络通信及数据处理的实时性,他们之间区别最大之处在于数据链路层协议,尤其是这层中的介质访问控制(MAC)子层,MAC协议可分为如下三个类型。
(1)集中式轮询协议1:
N
(2)令牌总线协议N:
N
(3)总线仲裁协议。
SCADA(SupervisoryControlAndDataAcquisition)系统作为生产过程和事物管理自动化最为有效的计算机软硬件系统之一,它包含两个层次的含义:
一是分步式的数据采集系统,即智能数据采集系统,也就是通常所说的下位机;另一个是数据处理和显示系统,即上位机HMI(HumanMachineInterface)系统。
三RS232C和RS422/485串行通信接口介绍
RS232C和RS422/485串行通沤涌冢琑S232C地电气接口电路是单端驱动,单端接收地电路,有公共地线,这种接口电路不能区分有用信号和干扰信号,抗干扰能力差,故其传输速率和传输距离收到很大限制。
RS422/485采用平衡驱动,差分接收电路,取消了信号地地接法,平衡驱动器相当于两个单端驱动器,当输入同意信号时其输出是反相的,如有共模信号干扰时,接收器只接收差分信号电压,从而大大提高了抗共模干扰的能力,并能在较长距离内明显提高传输速率。
其传输距离可达1200M(10KB/S)传输速率可达10MB/S,分别是RS232C的100倍和500倍。
RS485是RS422的变形,二者的区别是RS422为全双工型,RS485为半双工型,在使用RS485互联时,某一时刻只有一个站点可以发送数据,其他站点只能接收,因此,其发送电路必须由使能端加以控制, 用FX2N所组成地N:
N网络地总站点数最大为8个,使用专用协议时,最多16个站,包括A系列的可编程控制器,半双工通讯,38400bps,
N:
N网络RS485连线的选择是一对导线,单对子布线的情况下,在端子RDA和RDB之间连接端子电阻(110欧,1/2瓦棕棕棕),双对子布线的情况下,在端子SDA和SDB之间连接端子电阻,(220欧姆,1/4瓦),而在RDA和RDB之间也是这样。
(橙橙棕),
优点:
1节省配线,2提高处理速度,3实时性好。
四N:
N网络设计
1硬件设计,PLC可选用FX2N,FX2NC,FX1N,FX0N,通讯选用FX2N-485-BD,或者FX1N-485-BD,FX0N-485-BD,在本设计中,选用四个FX2N-485-BD。
2软件设计,由于使用了四个FX2N可编程控制器,在软件设计中,要分别对每个可编程控制器进行编程,选一个PLC为主站,将网络参数写在这个主站中.
其他程序见附表,分别为每个可编程控制器写好程序。
其通讯通过以下操作实现:
1)主站点的输入点X000到X003(M1000到M1003)输出到站点号1和2的输出点Y010到Y013。
2)站点1的输入点X000到X003(M1064到M1067)输出到主站点和站点2的输出点Y014到Y017。
3)站点2的输入点X000到X003(M1128到M1131)输出到主站点和站点1的输出点Y020到Y023.
4)主站点中的数据寄存器D1指定为站点1中计数器C1的设定值。
计数器C1的接触(M1070)状态反映在主站点的输出点Y005上。
5)主站点中的数据寄存器D2指定为站点2中计数器C2的设定值。
计数器C2的接触(M1140)状态反映在主站点的输出点Y006上。
6)站点1中数据寄存器D10的值和站点2中数据寄存器D20的值被加入主站点,并被存入数据寄存器D3中。
7)主站点中数据寄存器D0的值和站点2中数据寄存器D20的值被加入站点1,并被存入数据寄存器D11中。
8)主站点中数据寄存器D0的值和站点1中数据寄存器D10的值被加入站点2,并被存入数据寄存器D21中。
五结果分析
在本试验中,N=3,在这个网络中,通过485BD的通讯功能,链接了这个网络中的数据,这种通讯是通过在刷新范围内的字软元件和位软件的数值和状态交换来实现的,可以通过改变一个站点的数值,来改变整个网络的控制状态。
此网络的最大总站点数最大为8个,为半双工通讯,可以根据需要来决定站点数的多少,当增加站点数的时候,可以通过修改N=3的程序,写入增加站点的程序,并在原有的站点进行相应的改变即可实现。
此网络适用于多点分散控制,实时性要求高的场合,且处理速度快。
能节省配线,。
、系统调试
三、主要研究(设计)方法论述:
自动线是由六个PLC工作站相互连接而成的,它们分别来控制传输过程中的上料、检测、安装加工、分类提取、码垛等过程,通讯模块采用FX2N─485─BD扩充适配器,各单元连成一线后,相互之间要进行通讯,把加工过程中所产生的数据如检测信号,工件颜色,装配信息等送至下一站,系统中的各站开始工作的运行信号是由前站给出的后站也向前站传送加工信息,PLC一方面要处理各种位置信号及检测信号和各种控制信号,另一方面通过FX2N─485─BD传输各控制单元之间的信息,以便能准确的控制上道和下道工序的进行,通过组态软件进行全部系统监控。
许多工业现场往往是由单台PLC机来控制单台设备机组的自动运行,然后这些单台设备机组之间通过PLC通信端口传递信息,以达到整个生产线的控制。
N:
N通讯就是最好的解决方法,使用这种网络通讯,将控制单元连接成小规模控制系统,以满足企业实现生产线的全程控制。
四、设计(论文)进度安排:
时间(第周)
工作内容
第一周
熟悉设计任务,查阅资料,构思方案
第二周
硬件系统的设计
第三周
硬件系统的设计
第四周
软件系统的设计
第五周
软件系统的设计
第六周
软件系统的设计
第七周
软件系统的设计
第八周
软件系统的设计
第九周
系统仿真调试,修改,完善
第十周
系统仿真调试,修改,完善
第十一周
系统仿真调试,修改,完善
第十二周
撰写论文
五、指导教师意见:
指导教师签名:
年月日
六、系部意见:
系主任签名:
年月日
摘要
随着计算机网络通讯技术的日益成熟及企业对工业自动化程度要求的提高,自动控制系统已从传统的集中式控制向多级分布式、网络化方向发展,这些技术是工业控制过程智能化的发展方向。
但考虑我国企业的实际情况,尤其是近几年迅速发展的乡镇私营企业,没有足够的能力实现大型的网络自动化,许多工业现场往往是由单台PLC机来控制单台设备机组的自动运行,然后这些单台设备机组之间通过PLC通信端口传递信息,以达到整个生产线的控制。
N:
N通讯就是最好的解决方法,使用这种网络通讯,将控制单元连接成小规模控制系统,以满足企业实现生产线的全程控制。
关键词:
PLC,N:
N通讯
ABSTRACT
Withthegrowingofcomputernetworkcommunicationtechnologyandincreasingofindustrialenterprisesautomationrequirements,automaticcontrolsystemdevelopsfromthetraditionalcentralizedcontroltothemultileveldistributednetwork,thesetechnologyisintelligentdirectionofindustrialprocesscontrol.ButconsideringtheactualsituationofChineseenterprises,especiallytherapiddevelopmentofprivateenterprisesinthelastfewyears,insufficientcapacitytoachievelargenetworkautomation,inlotsofindustriallocaleauto-runningofsingleequipmentcomplexisoftencontrolledbysinglePLCset,theninformationistransferredamongallofequipmentcomplexthroughPLC’scommunicationports,inordertoachievethecontroloftheentireproductionline.N:
Ncommunicationisthebestsolution,usingsuchcommunicationnetwork,controlmodulesislinkedintoasmallcontrolsystemtomeetthewholecontrolofenterpriseproductionlines
Keywords:
PLCN:
Ncommunication
引言
目前PLC网络采用分级分布式复合结构时,一般分为三级(层)1管理层(以太网)2控制层(开放式,标准的现场总线)3现场层(部件层)也就是指装置层和传感器层以太网采用CSMA/CD(CarrierSenseMultipleAssesswithCollisionDetection)介质访问控制方式,即载波监听多路访问/冲突检测方式,该方式可以简单通俗地叙述为“先听后讲,边讲边听”。
以太网在工厂管理层、车间监控层将成为主流技术,与互连网技术结合是未来manufactory技术基础;在没有严格时间要求的设备层也将获得一定的发展;但对一般工业网络要求实时性、确定性通信场合,现场总线技术还将处于主导地位;我们必须学会面对一个多种网络技术并存的现实世界。
N:
N网络相当于三级总线型结构的中间一级,即控制层,最低一层为远程I/O链路,负责与现场设备通信,收集现场数据,驱动执行器,在远程I/O链路中配置周期I/O通信机制,这一层也可配置AS-I(传感器-执行器接口)链路,除了N:
N网络外,比较通用的有主从总线(1:
N)方式,争用总线方式,令牌环方式,浮动主站(N:
M)方式,目前已存在若干种现场总线,现场总线的体系结构,省略了网络层,传输层,会话层及表示层这四层,包括应用层(APPLICATION),数据链路层(DATALINK),物理层(PHYSICAL),这主要是针对工业过程的特点,使数据在网络流动中尽量减少中间环节,加快数据的传输速度,提高网络通信及数据处理的实时性,他们之间区别最大之处在于数据链路层协议,尤其是这层中的介质访问控制(MAC)子层,MAC协议可分为如下三个类型
(1)集中式轮询协议。
1:
N
(2)令牌总线协议N:
N(3)总线仲裁协议。
SCADA(SupervisoryControlAndDataAcquisition)系统作为生产过程和事物管理自动化最为有效的计算机软硬件系统之一,它包含两个层次的含义:
一是分步式的数据采集系统,即智能数据采集系统,也就是通常所说的下位机;另一个是数据处理和显示系统,即上位机HMI(HumanMachineInterface)系统。
N:
N网络RS485连线的选择是一对导线,单对子布线的情况下,在端子RDA和RDB之间连接端子电阻(110欧,1/2瓦),双对子布线的情况下,在端子SDA和SDB之间连接端子电阻,(220欧姆,1/4瓦),而在RDA和RDB之间也是这样。
优点:
1节省配线,2提高处理速度,3实时性好。
第一章概述
1.1系统简介
该模拟生产线是由独立的六个工作站相互连接而成。
它们分别是上料检测站、搬运站、加工检测站、安装站,安装搬运站和分类站。
这六个站连接成生产线后可完成工件类别的检测、加工、搬运、安装和分类并且可以通过485-BD总线连接PC机对各个工作站进行监测。
1.上料检测站:
回转上料台将工件依次送到检测工位提升装置将工件提升并检测工件颜色搬运站;
2.搬运站:
工件从上站搬运至下一站;
3.加工站:
四个工位转换,钻孔单元打孔,检测单元检测正、次品;
4.安装站:
选择要安装工件的料仓,工件从料仓中推出,将工件安装到位;
5.安装搬运站:
将上站正品工件拿起放入安装工位,将安装工件拿起放下站;将上站次品工件拿起放入堆放次品处
6.分类站:
按工件类型分类,将工件推入库房,统计不同类型工件的类型工件在生产线上从一站到另一站的物流加工的传递过程如下:
上料检测站将大工件按顺序排好后提升传送,搬运站将大工件从上料检测站搬运至加工站,加工站将大工件加工并检测被加工的工件,产生成品或废品信息,通知下站,安装搬运站将成品送至安装工位,安装站再将小工件装入大工件中,最后,由安装搬运站再将安装好的工件送至分类站,分类站将工件按类送入相应的料仓并统计工件的数量和总量,如加工站有废品产生,则安装搬运站将废品直接送入废品收料站。
图1.1站间通讯的实现及框图
各站连成一模拟生产线后,相互之间要进行通讯,把加工过程中所产生的数据如检测信号、工件颜色、装配信息、废品信息等,送至下站,使系统安全、可靠运行。
系统中各站开始工作的运行信号,是由前站给出的,后站也要向前站传送加工信息。
PLC一方面要处理各种位置信号以及检测信号和各种控制信号,另一方面要通过FX2N-485-BD传输各控制单元之间的信息,以便能准确控制上道和下道工序的进行。
通过组态软件进行全面系统控制。
系统配置图1.2。
图1.2系统配置
我们以FX2N为例介绍N:
N通讯硬件配置,系统通讯模块采用FX2N-485-BD扩充适配器或FX2N-CNV-BD机能扩充板,采用FX2N-485-BD时最大通讯距离为50米,采用FX2N-CNV-BD时最大通讯距离为500米,对FX2ND的V2.0以后的产品,网络的站点数最多8个。
传送速度为38400bps,通信方式是半2重双方向。
1.2N:
N通讯的主站点初始化程序(举例)
主站点程序:
图1.3主站点程序
从站点1程序:
图1.4从站点1程序
从站点2的程序:
图1.5从站点2程序
程序分析:
因为D8178的设置为1,所以主站点和其他站点是工作在模式1的状态下,
对于软件的传送指令FNC12,主站点程序的步骤1是主站输入点X000~X1003输出四个检测信号传送给主站M1000~M1003,从站1和从站2的步骤是将M1000~M1003输出到从站1和从站2的输出点Y010~Y013,让从站1和从站2都同时.同样道理,主站步骤2,从站1、从站2的步骤4是将从站2的输入点X000~X003输出到主站点1的输出点Y020~023上。
站步骤3,从站1、从站2的步骤4是将从站2的输入点X000~X003输出到主站点和站点1的输出点Y020~Y023上。
从站1和从站2的步骤1是用来确定本站的信号。
主站步骤6,从站1、从站2的步骤5是将从站点1的数据寄存器D10的值和从站点2中数据寄存器D20的值加起来、并被存入主站的数据寄存器D3中。
主站步骤7,从站1步骤6、从站2的步骤5是将主站点数据寄存器D0的值和从站点2中数据寄存器D20的值加起来、并存入从站1的数据寄存器D3中。
主站步骤7,从站1步骤5、从站2的步骤6是将主站点数据寄存器D0的值和从站点1中数据寄存器D10的值加起来,并被存入从站2的数据寄存器D3中。
系统通过特殊继电器和数据寄存器在PLC之间进行数据传送,达到生产线的控制目的。
1.3小型可编程控制器(PLC)的简介
1.3.1PLC的概述
PLC是一种数字运算操作的电子系统,专为在工业环境下应用而设计。
它采用了可编程的存储器,用来在其内部存储执行逻辑运算、顺序控制、定时、计数和算术运算等操作指令,并通过数字式和模拟式的输入和输出,控制各种类型的机械或生产过程。
PLC内部有许多不同功能的器件,实际上这些器件是由电子电路和存储器组成的,例如输入继电器X是由输入电路和映象输入接点的存储器组成;输出继电器Y是由输出电路和映象输出接点的存储器的组成;定时器T、计时器C、辅助继电器M、状态器S、数据寄存器D、变址寄存器V/Z等都是有存储器组成的。
为了把他们区分开来,我们通常用把上面的器件称为软器件,是等效概念抽象模拟的器件,并非实际的物理器件。
从工作过程看,我们只注重器件的功能,按器件的功能给名称,例如输入继电器X、输出继电器Y等,而且每个器件都有确定的地址标号,这对编程十分重要。
PLC是面向用户的专用工业控制计算机,具有许多明显的特点:
可靠性高,抗干扰能力强,编程直观,简单,适应性好,功能完善,接口功能强。
目前它所具有的功能有:
顺序控制,过程控制,数据处理,通信联网和显示打印,可编程控制器的更新很快。
1.3.2PLC的工作原理
PLC采用循环扫描的工作方式,这个工作过程分为内部处理、通信操作、程序输入处理、程序执行、程序输出几个阶段。
全过程扫描一次所需的时间称为扫描周期。
内部处理阶段,PLC检查CPU模块的硬件是否正常,复位监视定时器等。
在通信操作服务阶段,PLC与一些智能模块通信、响应编程器键入的命令,更新编程器的显示能容等,当PLC处于停(STOP)状态时,只进行内部处理和通信操作服务等内容。
在PLC处于运行(RUN)状态时,从内部处理、通信操作、程序输入、程序执行、程序输出,一直循环扫描工作。
第二章系统的总体设计
2.1软件设计
本设计中主要用的组态软件是Synall2000监控系统,Synall2000监控系统作为一个实时监视管理和数据采集系统,其软硬件系统的配置直接影响到系统的表现,并直接关系到能否满足其功能。
作为开发这样一个系统的工具软件,应该在考虑到大多数应用所面临的软硬件环境的基础上,尽可能地提高系统各方面的效率,满足应用对系统响应时间和处理能力方面的需要。
2.1.1SCADA与Synal2000系统
Synall2000系统是太力信息产业有限公司(原北京赛诺义科贸有限公司)在总结多年工业生产过程管理和事务处理自动化系统集成经验的基础上,综合研究国内外优秀的组态系统如Intouch、WinCC、FIX、LOGVIEW、CiTech,并应用最新的软硬件技术研制成功的。
它适用于从单一设备的生产运营管理和故障诊断,到网状结构的分布式大型集中监控管理系统的开发。
2.1.2Synall2000系统功能
配合以上特点,Synall2000系统提供能满足通常生产过程管理和事务管理自动化系统所需要的系统功能。
1.Synall2000组态系统提供以下功能:
(1)数据词典定义功能
(2)画面生成功能
(3)动画连接功能
(4)操作连接功能
(5)强劲的后台语言编程功能
(6)其它辅助功能
2.Synall2000运行系统具有以下功能:
(1)生产和管理设备的数据采集功能
(2)多点同时报警处理功能
(3)设备监控参数(变量)的显示、改变、登录和趋势分析
(4)事故追忆功能
(5)安全性管理功能
(6)容错功能
(7)其它功能
2.1.3Synall2000系统一般使用步骤
Synall2000系统作为一个通用的组态系统,它为系统集成商提供了一个方便的生产过程管理和事务管理自动化系统的开发平台,使用Synall2000系统的一般步骤如下:
第一步准备工作,包括:
了解您应用的领域,为组态准备以下初步信息:
1.有哪些变量需要监控?
其对应的逻辑智能数据采集设备包括哪些?
2.怎样用图形元素表达这些监控信息?
怎样有效地组织这些图形元素形成监控显示的基本单位(窗口)?
3.需要哪些辅助变量和辅助信息窗口,以便表达更准确更丰富的信息?
4.应用需要配置在不同的物理或行政地区吗?
由此确定需要定义属于同一系统的不同监控子系统。
5.确定需要的版本,Synall2000系统包括两个版本:
“单机版”,“网络版和容错版”,分别满足不同的需要。
简单地说,如果您的应用只需在独立的一台计算机上运行Synall2000运行系统即可满足要求,我们建议选择Synall2000运行系统的单机版,否则选择网络版。
第二步系统组态,包括以下步骤:
1.定义设备;
2.编辑变量词典;
3.定义运行系统,为每个运行系统作以下工作:
(1)定义画面窗口(一个或多个);
(2)使用作图工具,构造窗口的画面;
(3)对需要的图形元素,描述其显示属性(静态和动态),即动画连接;
(4)选定在本系统中进行数据采集的设备;
(5)定义后台语言,以完成有关的初始化工作、后台控制操作、系统结束操作等;
(6)配置运行系统