课设说明书.docx
《课设说明书.docx》由会员分享,可在线阅读,更多相关《课设说明书.docx(12页珍藏版)》请在冰豆网上搜索。
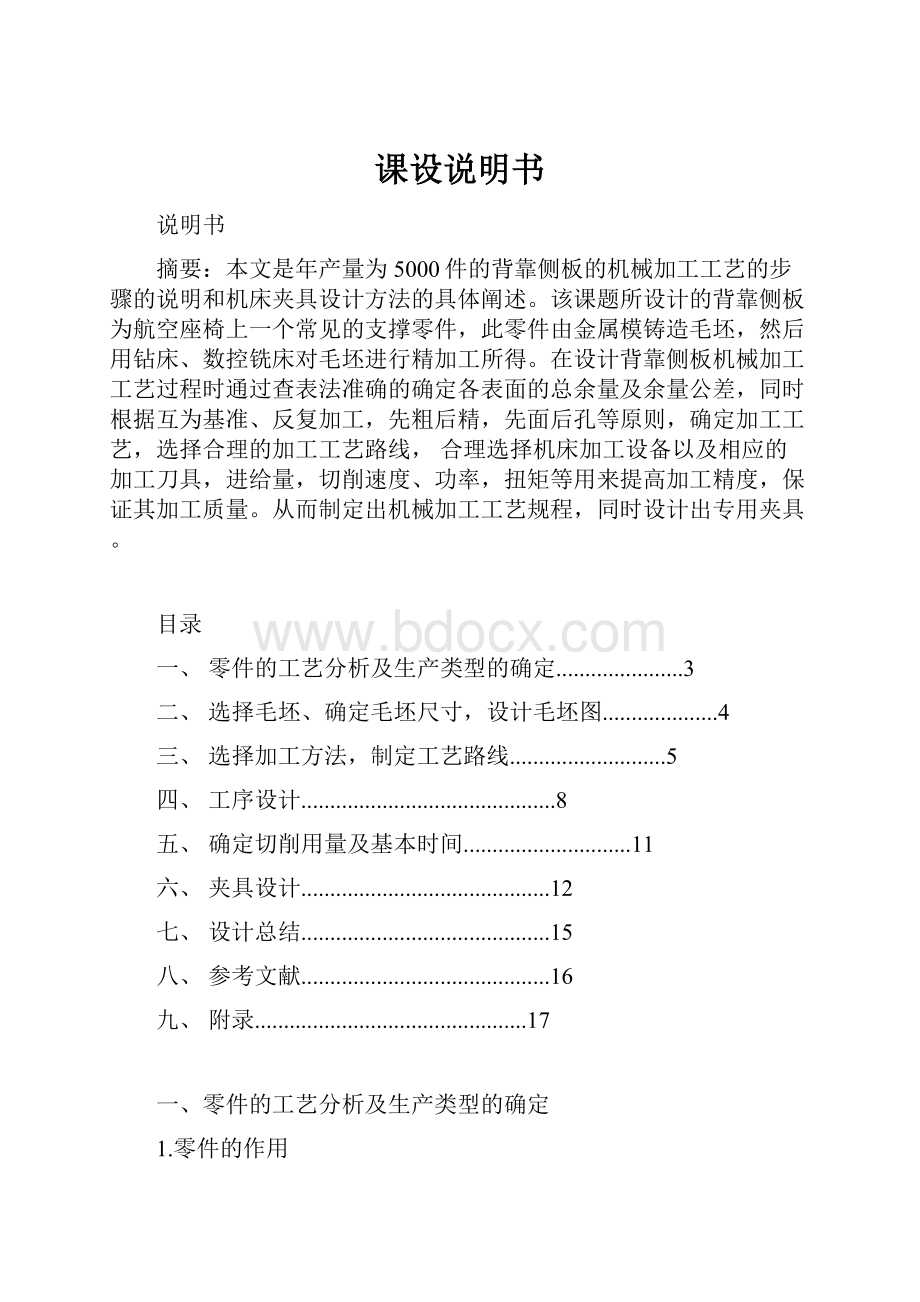
课设说明书
说明书
摘要:
本文是年产量为5000件的背靠侧板的机械加工工艺的步骤的说明和机床夹具设计方法的具体阐述。
该课题所设计的背靠侧板为航空座椅上一个常见的支撑零件,此零件由金属模铸造毛坯,然后用钻床、数控铣床对毛坯进行精加工所得。
在设计背靠侧板机械加工工艺过程时通过查表法准确的确定各表面的总余量及余量公差,同时根据互为基准、反复加工,先粗后精,先面后孔等原则,确定加工工艺,选择合理的加工工艺路线,合理选择机床加工设备以及相应的加工刀具,进给量,切削速度、功率,扭矩等用来提高加工精度,保证其加工质量。
从而制定出机械加工工艺规程,同时设计出专用夹具。
目录
一、零件的工艺分析及生产类型的确定......................3
二、选择毛坯、确定毛坯尺寸,设计毛坯图....................4
三、选择加工方法,制定工艺路线...........................5
四、工序设计............................................8
五、确定切削用量及基本时间.............................11
六、夹具设计...........................................12
七、设计总结...........................................15
八、参考文献...........................................16
九、附录...............................................17
一、零件的工艺分析及生产类型的确定
1.零件的作用
背靠侧板由优质材料ZL401,通过钢模铸造的方法一次性锻造出毛坯,然后经过精加工制造而成。
侧板载荷均匀分布、总体应力水平较低,弹性变形的可能性较小。
侧板无焊缝,完全排除焊接热应力造成侧板变形和开裂的可能。
侧板没有疏松,缩孔及裂纹等缺陷,有较高的强度,能够起到很好的支撑作用。
2.零件的生产类型
为年产量为5000件的大批量生产
3.零件的工艺分析
该零件航空座椅侧板,铸造等级为8级,加工余量等级为F级,精度要求不高,零件主要技术要求分析如下:
由图可知,5个零件内部的尺寸要求只要通过金属模锻造就可达到,而该侧板的五个面精度要求为Ra3.2,经过粗铣、半精铣、精铣即可,用数控铣床铣外形斜面及R18和台阶面就能满足精度要求为Ra3.2技术要求,孔φ30H7只需粗镗、半精镗、精镗即可达到精度要求为Ra0.8,然后用钻床钻四个孔φ10.5和两个腰形孔就能满足精度要求Ra6.3,再钻5个φ5.1的孔,再对其攻丝为5孔M6即可完成整个加工流程.
二、选择毛坯、确定毛坯尺寸,设计毛坯图
1.选择毛坯
根据零件要求,该零件的材料为ZL401,且为大批量生产,为使零件有较好的力学性能,保证零件工作可靠,故需要采用金属模锻造毛坯,效率高,同时保证了毛坯尺寸,便于加工。
2.确定机械加工余量
①上、下两面和R18的外圆的加工余量分别为
2.2+1.0+0.6=3.8mm(粗铣+半精铣+精铣)
②右端面的加工余量为
2.2+1.5+0.6=4.3mm(粗车+半精车+精车)
③前后两面的加工余量分别为
2.2+1.0+0.8=4mm(粗车+半精车+精车)
④φ30孔的加工余量为
1.5+1.5+1.0=4mm(粗镗+半精镗+精镗)
⑤剖面C-C的加工余量为
2.2+1.0+0.8=4mm(粗铣+半精铣+精铣)
3.毛坯尺寸(mm)
项目
总长度
上下两端面距离
前后面厚度
半圆形孔外端半径
通孔直径
C-C面
毛坯尺寸
444.3
87.6
38
21.8
26
28
4.设计毛坯图
①铸造方法:
金属模铸造
②确定圆角半径
根据零件图纸要求,铸件外轮郭未注圆角半径为7mm,内轮廓未注圆角半径为2mm,其余圆角半径见图纸要求,圆角尺寸能保证各表面的加工余量。
③确定拔模斜度
查表2-8得:
外表面斜度为0°30′,内表面斜度为1°。
④铸件浇铸位置及分型面的选择
为保证铸件没有气孔,砂眼,缩松,裂纹等缺陷,根据简单铸件的分型面应尽量选在铸件的最大端面上原则,选取上下两端面作为分型面
三、选择加工方法,制定工艺路线
1.定位基准的选择
粗基准的选择:
按基准的选择原则,即当零件有不加工表面时,应以这些不加工表面作粗基准;若零件有若干不加工表面时,则应以与加工表面要求相对位置精度高的不加工表面作粗基准。
遵循“基准重合”“互为基准”原则,采用加工表面为精基准。
精基准的选择:
考虑要保证零件的加工精度和装夹准确方便,尽可能地用加工过的表面为精基准,依据“基准重合”原则和“基准统一”原则
2.零件表面加工方法
●上、下端面:
表面粗糙度为Ra3.2,应该采取需要进行粗铣,再进行半精铣,再进行精铣。
●前后端面:
表面粗糙度为Ra3.2,应该采取需要进行粗铣,再进行半精铣,再进行精铣。
●右端面:
表面粗糙度为Ra3.2,应该采取需要进行粗铣,再进行半精铣,再进行精铣。
●斜面及R18:
表面粗糙度为Ra3.2,用数控铣床加工
●1.5的台阶:
用数控铣床加工
●φ30的孔:
表面粗糙度为Ra0.8,用镗床进行粗镗,再进行半精镗,再进行精镗
●4×φ10.5的孔:
表面粗糙度为Ra6.3,用数控钻床钻孔加工
●两个腰形孔:
表面粗糙度为Ra6.3,用数控钻床钻孔加工
●5×M6:
表面粗糙度为Ra6.3,用数控钻床钻孔,然后攻丝
●侧板为R5的圆弧:
表面粗糙度为Ra3.2,用钳工进行加工
●侧板为R50的圆弧:
表面粗糙度为Ra3.2,用钳工进行加工
以上加工工艺路线参考表2-9,2-10
3.制定工艺路线
工序1:
粗铣端面①(前端面)
工序2:
粗铣端面②(后端面)
工序3:
半精铣端面①
工序4:
半精铣端面②
工序5:
精铣端面①
工序6:
精铣端面②
工序7:
粗铣端面③(上端面)
工序8:
粗铣端面④(下端面)
工序9:
半精铣端面③
工序10:
半精铣端面④
工序11:
精铣端面③
工序12:
精铣端面④
工序13:
粗铣端面⑤
工序14:
半精铣端面⑤
工序15:
精铣端面⑤
工序16:
精铣斜面及R18外圆弧
工序17:
精铣1.5的台阶
工序18:
铣C-C面:
工序19:
粗镗孔φ30
工序20:
半精镗孔φ30
工序21:
精镗孔φ30
工序22:
钻两个腰形孔
工序23:
钻4×φ10.5的孔
工序24:
钻5×φ5.1的孔
工序26:
攻丝5-M6
工序27:
钳工对R50和2个R5的圆弧进行打磨加工
工序28:
剔除毛刺
四、工序设计
1.选择加工设备与工艺装备
工序号
设备
工艺装备
工序1
X5032立式铣床
高速钢套式面铣刀、游标卡尺、专用夹具
工序2
X5032立式铣床
高速钢套式面铣刀、游标卡尺、专用夹具
工序3
X5032立式铣床
高速钢套式面铣刀、游标卡尺、专用夹具
工序4
X5032立式铣床
高速钢套式面铣刀、游标卡尺、专用夹具
工序5
X5032立式铣床
高速钢套式面铣刀、游标卡尺、专用夹具
工序6
X5032立式铣床
高速钢套式面铣刀、游标卡尺、专用夹具
工序7
X5032立式铣床
高速钢套式面铣刀、游标卡尺、专用夹具
工序8
X5032立式铣床
高速钢套式面铣刀、游标卡尺、专用夹具
工序9
X5032立式铣床
高速钢套式面铣刀、游标卡尺、专用夹具
工序10
X5032立式铣床
高速钢套式面铣刀、游标卡尺、专用夹具
工序11
X5032立式铣床
高速钢套式面铣刀、游标卡尺、专用夹具
工序12
X5032立式铣床
高速钢套式面铣刀、游标卡尺、专用夹具
工序13
卧式铣床
高速钢套式面铣刀、游标卡尺、专用夹具
工序14
卧式铣床
高速钢套式面铣刀、游标卡尺、专用夹具
工序15
卧式铣床
高速钢套式面铣刀、游标卡尺、专用夹具
工序16
卧式铣床
高速钢套式面铣刀、游标卡尺、专用夹具
工序17
X5032立式铣床
高速钢套式面铣刀、游标卡尺、专用夹具
工序18
X5032立式铣床
高速钢套式面铣刀、游标卡尺、专用夹具
工序19
TK611B立式镗床
镗刀、内径千分尺、专用夹具
工序20
TK611B立式镗床
镗刀、内径千分尺、专用夹具
工序21
TK611B立式镗床
镗刀、内径千分尺、专用夹具
工序22
Z525型立式钻床
麻花钻、游标卡尺、专用夹具
工序23
Z525型立式钻床
麻花钻、游标卡尺、专用夹具
工序24
Z525型立式钻床
麻花钻、游标卡尺、专用夹具
工序25
Z525型立式钻床
麻花钻、游标卡尺、专用夹具
工序26
Z525型立式钻床
麻花钻、游标卡尺、专用夹具
工序27
钳工
圆锉、平挫等
工序28
钳工
圆挫、平挫等
2.确定工序尺寸
①表面工序尺寸
本零件的表面工序尺寸表见下表:
加工表面
工序单边余量
工序尺寸及公差
Ra
粗
半精
精
粗
半精
精
精
前后两端面
2.2
1.0
0.8
38±0.25
33.6±0.1
31.6±0.2
3.2
右端面
2.2
1.5
0.6
84.3±0.25
82.1±0.1
80.6±0.1
3.2
上下端面
2.2
1.0
0.6
87.6±0.25
83.2±0.1
81.2±0.1
3.2
②本零件各圆柱表面的工序加工余量,工序尺寸及公差,表面粗糙度见下表
加工表面
工序余量
工序尺寸及公差
Ra
粗
半精
精
粗
半精
精
精
R18外圆弧
2.2
1.0
0.6
21.8±0.25
19.6±0.1
18.6±0.1
3.2
φ30H7孔
1.5
1.5
1.0
26±0.25
27.5±0.1
29±0.1
0.8
1.5的台阶
3.2
两个腰形孔
6.3
4-φ10.5四个孔
φ10.5±0.25
6.3
5-M6孔
φ5.1±0.25
6.3
五、确定切削用量及基本时间
切削用量包括背吃刀量
、进给量
和切削速度
。
专用夹具用于钻5-φ5.1的通孔,如下为钻φ5.1通孔的基本时间的确定
1.切削用量及基本时间的确定
(1)切削用量工序为钻五个φ5.1的通孔。
已知加工材料为ZL401,机床为Z525立式钻床,工件装卡在专用夹具中,所选刀具为标准高速钢直柄长麻花钻。
钻φ5.1通孔
1确定背吃刀量
由于加工余量为5.1mm,故背吃刀量
=2.55mm。
②确定进给量
根据《机械制造技术基础课程设计》表5-64,查得本工序进给量
=0.27~0.33,由Z5125A立式钻床的进给量,选择
=0.27mm/r。
③切削速度
根据表5-66,当用标准高速钢直柄长麻花钻加工ZL401,
=2.55mm、
=0.27mm/r时,切削速度
=75m/min。
故
n=1000v/πd=1000×75/π/5.1=4683r/min
(2)基本时间
根据公式
确定工件的工时定额。
其中l为孔深,l1=(D/2)cotKr+(1~2),l2=1~4,D为孔径,Kr为主偏角(标准麻花钻Kr=59°)。
由此可确定l=30mm,l1=(5.1/2)cot59°+1.5=3mm,l2=2mm
=(30+3+2)mm/(0.27mm/r×4683r/min)×60s=1.66s
计算出基本时间,然后根据一定的比例,分别计算出
、
、
各个参数,其中
单件钻φ15通孔工时为:
=2
+
+
+
=3.654s~3.8346s
六、夹具设计
七、设计总结
通过两周紧张而充实的课程设计,我们在宋老师的指导下,完成了年产量为5000件的靠背侧板的机械加工工艺规程及典型夹具的设计,绘制出了毛坯图、机械加工工艺过程卡、所设计夹具对应工序的机械加工工序卡以及总装配图等,基本掌握了一个零件由设计到生产的基本流程,实现了由理论到实践的过渡。
在这两周里我学到了很多东西,学会了使用机械加工工艺手册,对一些基本夹具也有所理解,对一些新型的夹具有了一些认识,当最终完成全部设计时,体会到了作为设计者的那种快乐,在整整两周的课程设计中,宋老师每天早上都会为我们解答设计过程中遇到的各种问题,并将自己多年总结的经验与我们分享,为我们即将迈入工作岗位打下了一定的基础,在此表示对宋老师的感谢。
通过自己动手设计并取得成功,让我充分体会到了在设计过程中探索的艰难和成功时的喜悦。
在整个设计中我学会了团队合作,学会了自我学习和独立思考的能力,增强了对自身能力的信任,相信这些所学将会对今后的学习工作生活产生非常重要的影响。
八、参考文献
[1]柯建宏.机械制造技术基础课程设计[M].华中科技大学出版社,
[2]熊梁山.机械制造技术基础[M].华中科技大学出版社,2000
[3]王中任.机械设备数控技术[M].国防工业出版社,2010
[4]机床夹具设计.第二版[M].上海:
上海科技技术出版社,1990
[5]杨叔子.机械加工工艺师手册[M].北京:
机械工业出版社,2000
九、附录
1.靠背侧板零件毛坯图;
2.整个零件的机械加工工艺过程卡
3.所设计夹具对应工序的机械加工工序卡
4.夹具装配图
5.数控铣床程序