座椅总成技术条件精讲.docx
《座椅总成技术条件精讲.docx》由会员分享,可在线阅读,更多相关《座椅总成技术条件精讲.docx(32页珍藏版)》请在冰豆网上搜索。
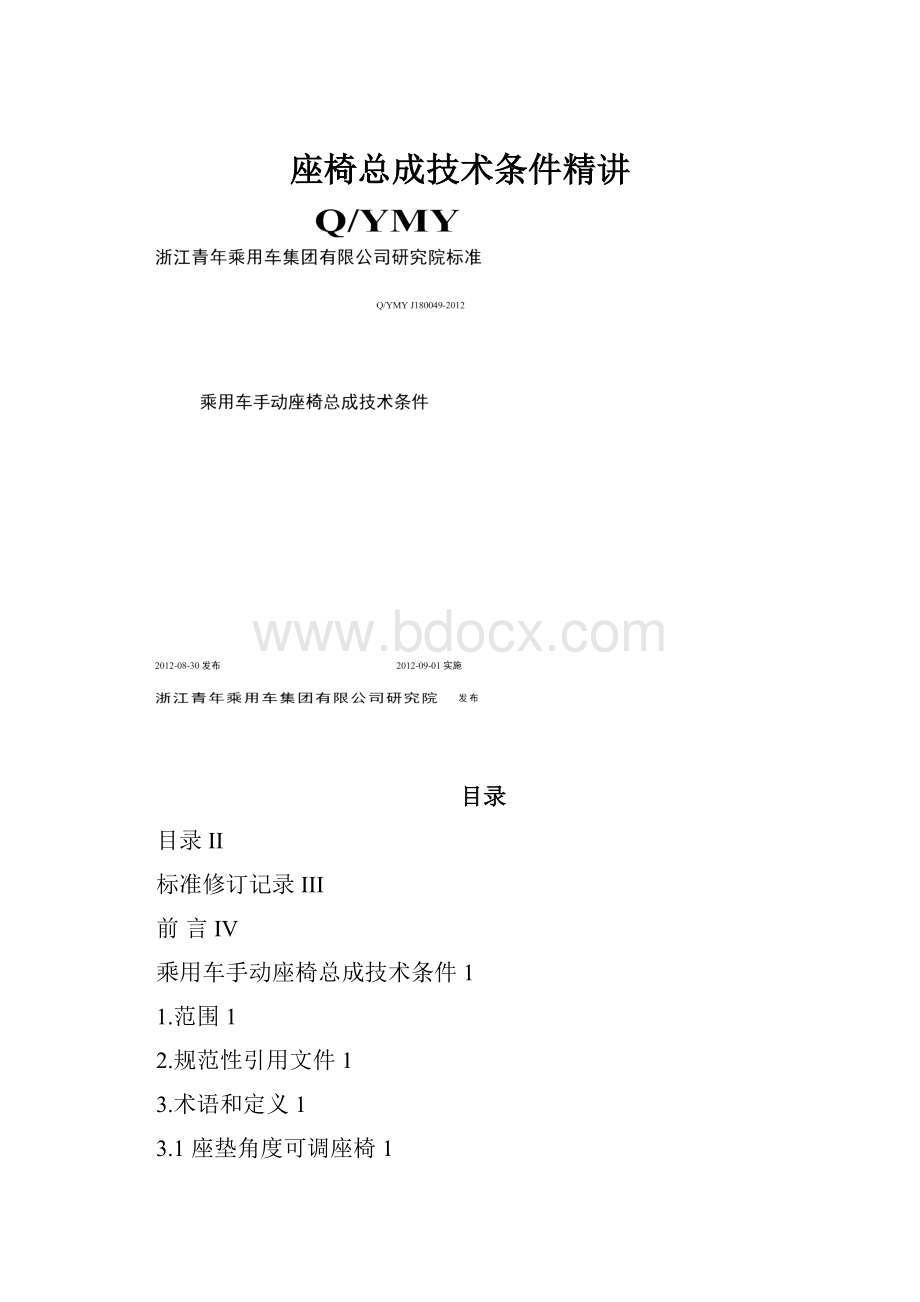
座椅总成技术条件精讲
目录
目录II
标准修订记录III
前言IV
乘用车手动座椅总成技术条件1
1.范围1
2.规范性引用文件1
3.术语和定义1
3.1座垫角度可调座椅1
3.2靠背倾角可调座椅1
3.3头枕分离式座椅1
3.4座垫角2
3.5座垫宽2
3.6靠背高2
3.7靠背宽2
4.技术要求2
4.1一般要求2
4.2外观要求2
4.3尺寸2
4.4材料要求2
4.5使用性能3
4.7抗疲劳与耐久性4
4.8座椅操作特性7
5.试验方法8
6.检验规则16
7.标志、包装、运输、贮存17
标准修订记录
版本号
日期
编制人/修订人
修订内容描述
备注
V0.01
2012-06-30
丁鹏
首次编写
V1.00
2012-8-30
丁鹏
正式发布
编制:
校对:
审核:
标准:
批准:
前言
本标准所涉及座椅总成是青年汽车乘用车集团专用手动调节座椅产品。
为确保产品的质量,特制定本企业标准。
本标准以符合国家标准和行业标准为前提,在立足于产品国产化要求和产品性能的实际情况下制定的。
对国家规定的强检项目都做了严格的规定。
本标准由浙江青年汽车集团乘用车集团提出并归口。
本标准由浙江青年汽车乘用车集团研究院总工程师批准。
本标准起草单位:
浙江青年汽车乘用车集团研究院车身部。
本标准主要起草人:
丁鹏。
本标准为首次发布。
乘用车手动座椅总成技术条件
1.范围
本标准规定了乘用车座椅用手动座椅总成的技术要求、试验条件、检验规则、标志、包装、运输和储存。
本标准适用于乘用车用手动座椅总成的检验。
2.规范性引用文件
下列文件中的条款通过本标准的引用而成为本标准的条款。
凡是注日期的引用文件,其随后所有的修改(不包括勘误的内容)或修订版均不适用于本标准,然而,鼓励根据本标准达成协议的各方研究是否可使用这些文件的最新版本。
凡是不注日期的引用文件,其最新版本适用于本标准。
GB11550汽车座椅头枕的性能要求和试验方法
GB11563H点确定程序
GB11551关于正面碰撞乘员保护的设计规则
GB14167汽车安全带安装固定点
GB/T5453织物透气性试验方法
GB8410汽车内饰材料燃烧特性
GB/T10802软质聚氨酯泡沫塑料
GB14166汽车安全带性能要求和试验方法
GB14167汽车安全带安装固定点
GB15083汽车座椅、座椅固定装置及头枕强度要求和试验方法
QC/T55汽车座椅动态舒适性试验方法
QC/T56汽车座椅衬垫材料性能试验方法
QC/T484汽车油漆涂层
QC/T625汽车用涂镀层和化学处理层
JB/T5943工程机械焊接件通用技术条件
SAEJ826H点测量仪和设计步骤和规范
SAEJ1756汽车内饰材料确定成雾特性的试验
3.术语和定义
下列术语和定义适用于本标准。
3.1座垫角度可调座椅
是指座垫俯仰倾角可调节的座椅。
3.2靠背倾角可调座椅
是指靠背倾角可调节的座椅。
3.3头枕分离式座椅
是指头枕和靠背分开的座椅。
3.4座垫角
是指在座椅中心平面上,人体大腿中心线与水平面的夹角。
3.5座垫宽
是指通过座椅R点并与座椅中心平面垂直的垂直面上,座垫的最大宽度。
3.6靠背高
是指在座椅中心平面上,沿平行于人体躯干基准线,靠背顶端至座垫与靠背交点的距离。
3.7靠背宽
是指在座椅中心平面上,沿靠背距座垫与靠背交点270mm处的靠背宽度。
4.技术要求
4.1一般要求
4.1.1座椅必须符合本标准规定的要求,并按规定程序批准的图样和有关技术文件制造,所有材料和元器件应符合相应标准的规定,并经检验合格。
4.2外观要求
4.2.1面料的材质、颜色和花纹需经青年汽车乘用车研究院认可。
4.2.2所有护面须符合其对应结构图的缝制及外观要求。
4.2.3护面外观无缺陷,同一护面无色差。
4.2.4护面上不可有可见的外露针眼及返修的痕迹。
4.2.5座椅表面无污染、破损、开裂等缺陷和客户不能接受的褶皱。
4.3尺寸
4.3.1座椅H点的测量,应满足设计要求,误差范围为12.5mm。
躯干角度误差为±3°。
假人的型号采用SAEJ826的规定。
4.3.2座椅安装位置尺寸符合设计要求,确保座椅能轻松地安装。
应用检具来检测。
4.3.3座椅处于任何给定的位置,滑道手柄应能复位。
滑道调节后应能够锁定座椅。
4.4材料要求
4.4.1在(-30~70)℃的环境温度下,座椅护面、软垫等非金属材料应能满足使用要求。
4.4.2座椅面料应具有阻燃性能,其燃烧特性必须满足GB8410的要求。
4.4.3座椅与人体接触部分的护面材料应具有较好的透气性,其透气量不小于0.2m3/m2/s。
4.4.4座椅上各焊接组件不应有焊接错位、虚焊等缺陷,其焊接质量应符合JB/T5943的有关规定。
座椅各总成装配后,应连接牢固、使用可靠。
4.4.5座椅的金属件应进行表面防锈处理,其油漆涂层应符合QC/T484中TQ10的有关规定,电镀层和化学处理层应符合QC/T625的有关规定。
4.4.6护面总成应缝合牢固,缝合部位不允许漏缝、开缝、脱线、跳线。
缝制加工所选缝线质量和缝制工艺,应保证不低于护面材料强度,在正常使用及试验条件下不得早期损坏。
4.4.7座椅装配护面总成后,表面应饱满、整洁,不应有外露线头、脱色、污迹、破损、皱褶及划伤。
4.4.8座椅衬垫材料为聚氨脂泡沫塑料,应满足GB/T10802的要求。
4.4.9座椅非金属材料的排放性能试验应满足以下条件:
a)可凝结水试验按照SAEJ1756的试验方法,其界定值为:
G≤3mg;
b)气味测试按照SAEJl351的测试方法,其界定值为:
气味评分小于或等于3.5级。
4.5使用性能
4.5.1座椅的外表面和内部不应存在任何危及乘员安全的尖锐突出物。
4.5.2座椅的调节器应调节自如、锁止可靠、操作轻便,无卡滞现象。
驾驶员或乘客在乘坐姿态下,座椅角度调节器的调节力矩应不大于10Nm,上下、前后调节器的调节力应不大于60N;若座椅高度可调,调节手轮操作力矩不大于1Nm~4Nm。
4.5.3座椅头枕可上下调节时,操作力为20N~80N。
4.5.4座椅头枕可旋转调节时,扭矩为4Nm~8Nm。
4.5.5座椅总成的强度应满足GB15083的要求。
4.5.6座椅头枕的材料、结构尺寸和性能应符合GB11550的规定。
4.5.7安全带的安装固定点的位置和强度应符合GB14167的规定。
4.5.8座椅必须有良好的造型及减振性能,避免引起乘员的共振反应。
4.5.9可翻折后座椅靠背解锁力不大于50N。
4.5.10可向前翻转后座椅坐垫抬起力不大于100N。
4.5.11前排座椅腰托调节力无载荷时应不大于49N。
4.5.12前排座椅地图袋拉起力
实车装配座椅,调整机构位于设计标准位置上,在地图袋中间位置加负荷20N后,无杂物袋脱落、破损、靠板的脱落等发生。
4.5.13座椅乘坐时应无咯吱咯吱的响声。
4.6座椅强度要求
4.6.1强度要求见表1。
表1实际强度评价指标
项目名称
技术指标
最大负载
后向负载
当骨架变形决定最大负载的时候(即由于座椅骨架变形最大负载不再增加),此时最大负载应当是1470N(150kgf)。
当最大负载是由骨架破折、机构破碎、或由锁止机构释放决定的时候,此时最大负载应当是1764N(180kgf)。
前向负载
此时最大负载应当是1058N(108kgf),靠背骨架破坏时承受的最大负载应大于1274N(130kgf)。
骨架弹性变形
位移和力
应当符合图3。
4.6.2座椅座垫向下强度要求见表2,对座椅加载5880N,保持一定时间后,加载至7056N,当产生评价特性任一情况,应判定试验失败。
表2座椅座垫向下强度评价指标
测试项目
评价特性
技术指标(N)
滑道锁止机构释放
释放安装了保险带固定点的滑道的锁止机构
对座椅加载5880N,保持一定时间后,加载至7056N
释放没有安装保险带固定点的滑道的锁止机构
破裂强度
座垫骨架和座垫骨架固定支架破裂
高度调节机构破裂
滑道锁止机构破裂
4.6.3座椅总成纵向调节功能试验
座椅总成纵向调节功能试验测试座椅纵向调节的操作力。
在座椅座垫上H点位置向下加载60Kg的力载荷,用测力计测量手柄打开的操作力,此开启操作力应小于80N。
空载下滑动力小于80N,负载下滑动力小于120N。
机械滑轨的调节步长小于等于10mm。
4.7抗疲劳与耐久性
4.7.1在完成下列表3中的循环次数后,要符合评价指标,如果出现表3中的情况应判定试验失败。
表3骨架耐疲劳性评价标准
循环次数
评价指标
13000
1调节机构不能正常操作或操作力超出测试标准;如是电动座椅,调节机构出现不正常的操作速度或作用力超出测试标准。
2螺栓等出现松动。
3饰件,手柄,按钮,兜袋等出现缺陷。
4扶手和腰托不能正常锁止。
40000
1靠背骨架出现损伤,但不包括角度调节器安装区域。
2滑道出现损伤。
3高度调节机构和座垫骨架出现损伤(座垫-高度调节机构式)。
4滑道锁止机构,角度调节器,靠背骨架角度调节器安装区域,高度调节机构和座垫骨架。
5整椅-高度调节机构式,头枕骨架,旋转锁止机构出现裂纹。
6电动滑道,电动角度调节器,电动高度调节机构操作不正常。
7滑道和角度调节器出现故障。
72000
1滑道出现脱离和滑道锁止机构出现损伤。
2角度调节器出现脱离和损伤。
3靠背骨架角度调节器安装区域出现损伤。
4高度调节机构和座垫骨架(整椅-高度调节机构式)出现损伤。
5头枕骨架出现脱离和损伤。
6旋转机构出现损伤,旋转锁止机构出现分离。
4.7.2在完成下列表4中的循环次数后,要符合评价指标,如果出现表6中的情况应判定实验失败。
表4座椅滑道操作疲劳性评价标准
循环次数
评价标准
2000
1调节机构不能正常操作或操作力超出测试标准;如是电动座椅,调节机构出现不正常的操作速度或作用力超出测试标准。
2螺栓等出现松动。
3饰件,手柄,按钮,兜袋等出现缺陷。
4扶手和腰托不能正常锁止。
4000
1扶手支撑和腰托支撑或旁侧支撑出现损伤。
2角度调节器不能保持翘起的功能。
3螺栓等出现松开或分离。
骨架出现变形。
护面出现损伤,切口或裂纹。
4饰件,手柄,按钮,兜袋等出现损伤。
6000
1靠背骨架出现损伤,但不包括角度调节器安装区域。
2滑道出现损伤。
3高度调节机构和座垫骨架出现损伤(座垫-高度调节机构式)。
4滑道锁止机构,角度调节器,靠背骨架角度调节器安装区域,高度调节机构和座垫骨架。
5整椅-高度调节机构式,头枕骨架,旋转锁止机构出现裂纹。
6电动滑道,电动角度调节器,电动高度调节机构操作不正常。
7滑道和角度调节器出现故障。
8000
1滑道出现脱离和滑道锁止机构出现损伤。
2角度调节器出现脱离和损伤。
3靠背骨架角度调节器安装区域出现损伤。
4高度调节机构和座垫骨架(整椅-高度调节机构式)出现损伤。
5头枕骨架出现脱离和损伤。
6旋转机构出现损伤,旋转锁止机构出现分离。
4.7.3在完成下列表5中的循环次数后,要符合评价指标,如果出现表5中的情况应判定实验失败。
表5角度调节器操作疲劳性评价指标
循环次数
评价指标
2000
1调节机构不能正常操作或操作力超出测试标准;如是电动座椅,调节机构出现不正常的操作速度或作用力超出测试标准。
2螺栓等出现松动。
3饰件,手柄,按钮,兜袋等出现缺陷。
4扶手和腰托不能正常锁止。
4000
1扶手支撑和腰托支撑或旁侧支撑出现损伤。
2角度调节器不能保持翘起的功能。
3螺栓等出现松开或分离。
骨架出现变形。
护面出现损伤,切口或裂纹。
4饰件,手柄,按钮,兜袋等出现损伤。
6000
1靠背骨架出现损伤,但不包括角度调节器安装区域。
2滑道出现损伤。
3高度调节机构和座垫骨架出现损伤(座垫-高度调节机构式)。
4滑道锁止机构,角度调节器,靠背骨架角度调节器安装区域,高度调节机构和座垫骨架。
5整椅-高度调节机构式,头枕骨架,旋转锁止机构出现裂纹。
6电动滑道,电动角度调节器,电动高度调节机构操作不正常。
7滑道和角度调节器出现故障。
8000
1滑道出现脱离和滑道锁止机构出现损伤。
2角度调节器出现脱离和损伤。
3靠背骨架角度调节器安装区域出现损伤。
4高度调节机构和座垫骨架(整椅-高度调节机构式)出现损伤。
5头枕骨架出现脱离和损伤。
6出现损伤,旋转锁止机构出现分离。
4.7.4在完成下列表6的循环次数后,要符合评价指标,如果出现表6中的情况应判定实验失败。
表6座椅高度调节机构操作耐久性评价指标
循环次数
评价指标
2000
1调节机构不能正常操作或操作力超出测试标准;如是电动座椅,调节机构出现不正常的操作速度或作用力超出测试标准。
2螺栓等出现松动。
3饰件,手柄,按钮,兜袋等出现缺陷。
4扶手和腰托不能正常锁止。
4000
1扶手支撑和腰托支撑或旁侧支撑出现损伤。
2角度调节器不能保持翘起的功能。
3螺栓等出现松开或分离。
骨架出现变形。
护面出现损伤,切口或裂纹。
4饰件,手柄,按钮,兜袋等出现损伤。
6000
1靠背骨架出现损伤,但不包括角度调节器安装区域。
2滑道出现损伤。
3高度调节机构和座垫骨架出现损伤(座垫-高度调节机构式)。
4滑道锁止机构,角度调节器,靠背骨架角度调节器安装区域,高度调节机构和座垫骨架。
5整椅-高度调节机构式,头枕骨架,旋转锁止机构出现裂纹。
6电动滑道,电动角度调节器,电动高度调节机构操作不正常。
7滑道和角度调节器出现故障。
8000
1滑道出现脱离和滑道锁止机构出现损伤。
2角度调节器出现脱离和损伤。
3靠背骨架角度调节器安装区域出现损伤。
4高度调节机构和座垫骨架(整椅-高度调节机构式)出现损伤。
5头枕骨架出现脱离和损伤。
6旋转机构出现损伤,旋转锁止机构出现分离。
4.8座椅操作特性
4.8.1角度调节器操作特性
4.8.1.1操作特性
a)靠背和角度调节器应能光滑操作,不能出现粗糙滑道。
b)座盆旁侧不能妨碍到操作角度调节器手柄。
c)操作点为手柄末端往内30mm。
4.8.1.2靠背向前翻转速度
a)测量靠背从设计位置到垂直位置的向前翻转速度。
b)翻转速度应该在114.6°/s到171.9°/s之间。
4.8.1.3角度调节器手柄操作力
a)操作点为手柄末端往内30mm。
b)操作力应符合表7。
表7操作力
操作力
类型
标准
疲劳试验后
手轮
(0.6——2.4)Nm
(0.6——2.4)Nm
手柄
(20——70)N
(20——70)N
4.8.2座椅滑道操作特性要求
a)锁止机构误用,评价标准:
完成上面试验后,至少一侧的锁止卡爪处于锁止状态。
同时,另一侧的锁止卡爪与试验前位置不能超过3个锁止窗口。
b)操作力评价指标见表8。
表8操作力评价指标
操作力
标准(N)
疲劳试验后(N)
滑道操作力
向前
-20℃~90℃时操作力≤98
-20℃~90℃时操作力≤98
向后
-40℃~-20℃时操作力≤176.4
-40℃~-20℃时操作力≤176.4
手柄操作力
9.8~78.4
9.8~78.4
座椅高度调节机构操作特性要求见表9。
表9座椅高度调节机构操作特性评价标准
操作方向
操作力标准(N)
向上
9.8~58.8
向下
4.9座椅刚度与间隙
4.9.1座椅骨架纵向刚性试验按5.18测试,评价指标:
当加载147N时,加载点变形不许超过15mm;且施加49N时,加载点变形不许超过10mm。
4.9.2座椅骨架侧向刚性试验按5.19测试,评价指标:
当加载147N时,加载点变形不许超过8mm。
4.9.3靠背骨架扭转刚性试验按5.20测试,评价指标:
当加载98N时,加载点变形不许超过80mm。
4.9.4座椅靠背的间隙试验按5.21测试,评价指标:
距转轴200mm处偏移量为±1.5mm。
4.10正面碰撞要求
正面碰撞要求按5.22测试,通过汽车向前的碰撞试验,对配置假人的座椅状况进行验证分析,要求在减速时,人不允许从安全带里滑出,座椅零部件及止动和调节装置不准碎裂或拉断,允许弯曲。
靠背松开装置仍需保持功能完好。
4.11后部碰撞要求
后部碰撞要求按5.23测试,通过汽车向后的碰撞试验,对配置假人的座椅进行验证分析,在碰撞时,靠背可弯曲,但不允许冲撞其它物体。
座椅零部件不允许碎裂或拉断,座椅和地板之间的固定装置不允许扯断,座椅止动装置不允许松开,且应保持其功能完好。
靠背松开装置仍需保持功能完好。
4.12颠簸和蠕动试验
颠簸和蠕动试验验证座椅的骨架、泡沫和面套的疲劳寿命,在100次每分钟的频率下,进行座垫100000次、靠背50000次的振动试验,试验后的样品应无异常情况出现,座椅骨架无裂缝,泡沫无变形,面料和衬垫无破损,H点最大变动在额定范围之内。
4.13模拟人体进出座椅试验
模拟人体进出座椅试验对带面套的座椅进行面料耐磨性测试,模拟人体进出进行15000次的整椅试验,试验后的座椅面套不应出现端裂、结团,不应脱散和漏底,不允许出现损伤,缝线不允许断裂。
5.试验方法
5.1试验环境:
温度为(23±5)ºC,相对湿度为(45—70)℅。
5.2测量座椅尺寸规格所使用的三维H点装置应符合4.3.1的规定。
5.3座椅面料的燃烧特性按GB8410规定的试验方法进行。
5.4座椅护面材料的透气性按GB/T5453规定的试验方法进行。
5.5座椅总成的强度要求按GB15083规定的试验方法进行。
5.6座椅头枕的性能按GB11550中第5章规定的试验方法进行。
5.7座椅衬垫材料的性能按QC/T56规定的试验方法进行。
5.8座椅蒙皮材料强度测试方法
a)专用拉力机、撕力器;
b)将试片放入撕力器的弯曲部分,紧压试片,使其牢固的固定在撕力器上;
c)加力,直到试片撕裂为止并记录撕裂过程中最大的力(如图1)。
图1蒙皮试验方法
5.9座椅用软质聚氨酯泡沫塑料试验方法
5.9.1表观密度
a)试样尺寸:
软泡300mm×300mm×50mm;
b)在分析天平上精确称取试样的重量,精确到0.01g,用千分卡尺测量样品的尺寸,精确度为±0.1%,每个样品测量三次,至少测定5个样品,取其平均值;
c)表观密度——试样质量(g)/试样体积(cm3)。
5.9.2拉伸强度
a)用裁样机裁哑铃状试样,至少5个,试样厚度约10mm,其中央平行部分标以40mm长的标线,测定平行部分的准确厚度;
b)测量试片的横切面的长度和宽度,取几个点,记录最小数值,精确到0.05mm,将试片置于强力拉力机的夹具上,选择合适的载荷范围和拉伸速度,慢慢调节样品在中心轴上,开动仪器,记下负荷读数,测定和记录断裂前瞬间两基线内侧间的距离,剔除断裂的标距外的试样,同一试样至少测试5个不同部位的样品,取平均值;
c)拉伸强度(Mpa)=F/A
式中F表示断裂载荷,N;A表示平均截面积mm2。
5.9.3撕裂强度
a)从中心部位切取,无空隙和块状物,试样一端切40mm长的切口,AB的尺寸为试样厚度,厚度的方向为泡沫上升的方向,试样数量至少3个(如图2);
b)按AB方向测量试样厚度,每个试样测量三点,取平均值,将试样张开,夹在仪器的夹具上,以(50~200)mm/min的速度施加负荷。
用刀片切割试样,保持刀口在中心位置,记录试样断裂或至少撕裂50mm后的最大值;
c)撕拉强度=F/T
其中F——测得的最大力值,N
T——试样的平均厚度,cm。
注:
撕裂强度测定与拉伸强度相同。
5.9.4压缩强度
a)仪器:
压缩试验机,其力和位移的范围应满足测试要求,须备有两块表面抛光且不会变形的方形或圆形的平行板,板的边长或直径至少为100mm,其中一块是固定的,而另一块可按规定条件做恒定移动;
b)试片尺寸50mm×50mm×50mm,圆形或正方形均可,或面积在(25~230)cm2之间,厚度在50mm±1mm,表皮应除去;
c)操作:
测量试样尺寸,精确至0.05mm,至少测三点取平均值,将试样放在压板间,按规定的速度反复压缩载荷。
5.9.5压缩永久变形
a)仪器和设备:
压缩装置由两块大于试样尺寸的平板,定位件和夹具组成,测试过程中,两平板应相互平行和不变形,两平板间的距离可按所需的形变高度进行调节。
(测定薄形材料,应备有必要数量的正方形玻璃片,玻璃片的厚度为1.0mm~1.5mm,边长为500mm~550mm);
b)试样尺寸:
长(50±1)mm,宽(50±1)mm,厚(25±1)mm,顶面与底面互相平行,相邻各边互相垂直,垂直边不带表皮。
薄形材料的试样应叠合在一起,其总厚度至少是25mm,各试样之间用玻璃片隔开,测试时,整个组合件作为单个试样,试样数目为5个;
c)操作:
测定试样的初始厚度(d0),若是薄形材料,其初始厚度(d0)是在水平位置测得组合试样的总厚度中扣除玻璃片的厚度而得到的。
把组合试样置于压缩装置的两平板之间,将试样压缩至安装初始厚度的50%或75%,并维持此条件,在特殊情况下,可以允许压缩90%,在15min内将已压缩的试样置于Φ70的烘箱内并维持22h,从烘箱内取出压缩装置并在1min内从装置中取出试样,放置于低热导率(如木版)的平面上,物体表面的温度应是实验室室温。
若是薄形材料,应取出试样中的