含铌铁水脱硅行为研究.docx
《含铌铁水脱硅行为研究.docx》由会员分享,可在线阅读,更多相关《含铌铁水脱硅行为研究.docx(27页珍藏版)》请在冰豆网上搜索。
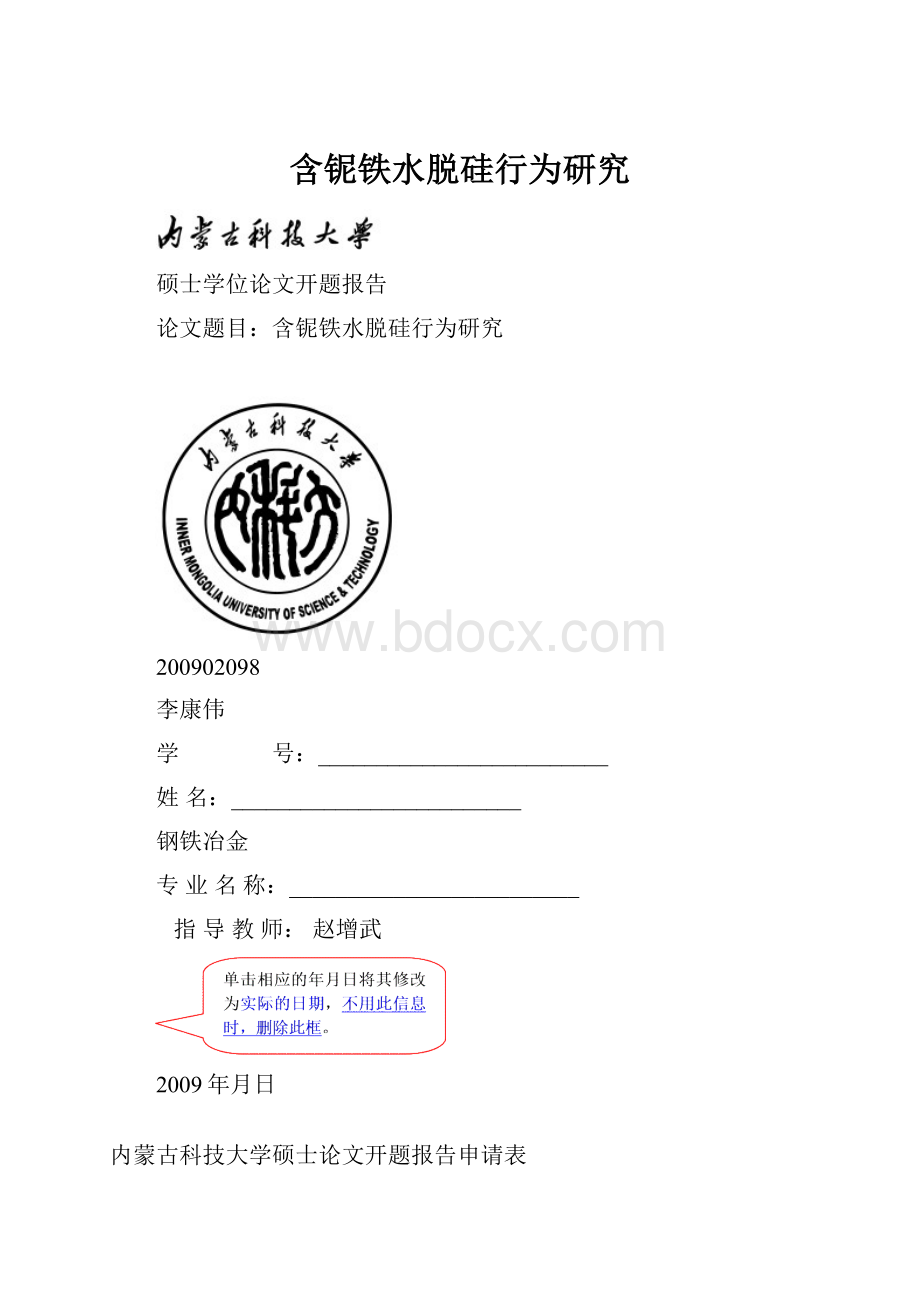
含铌铁水脱硅行为研究
硕士学位论文开题报告
论文题目:
含铌铁水脱硅行为研究
200902098
李康伟
学 号:
_________________________
姓名:
_________________________
钢铁冶金
专业名称:
_________________________
指导教师:
赵增武
2009年月日
内蒙古科技大学硕士论文开题报告申请表
姓名
李康伟
学号
200902098
导师姓名
李保卫
职称
教授
专业
钢铁冶金
年级
2009级
课题名称
含铌铁水脱硅行为研究
关键词
开题报告申请:
(已取得学分,本学期工作简介,开题申请)
研究生签字年月日
导师意见:
签字年月日
学院意见:
签字年月日
学科建设与研究生处审核意见:
盖章年月日
注:
本表请用A4纸打印,一式两份,与开题报告一起装订,院系、学科建设与研究生处各交一份。
文献总结及选题报告
研究方向
学号
200902098
姓名
李康伟
指导教师
李保卫
论文题目
含铌铁水脱硅行为研究
关键词
主要内容:
组织单位
报告日期
评议意见:
主要评定教师签字:
导师意见:
签字:
学院主管领导意见:
签字:
目 录
1文献综述1
1.1铁水预处理概论1
1.1.1铁水预处理的化学冶金学意义1
1.1.2铁水预处理的必要性1
1.2国内外铁水预脱硅的基本现状2
1.2.1高炉炉内的铁水预脱硅技术2
1.2.2高炉炉外铁水预脱硅技术3
1.3铁水预脱硅经济意义5
1.4脱硅原理、影响因素及脱硅剂5
1.4.1脱硅原理5
1.4.1.1硅氧化的热力学5
1.4.1.2硅氧化的动力学6
1.4.2影响因素6
1.4.2.1温度的影响7
1.4.2.2渣量的影响7
1.4.2.3铁水初始含硅量对脱硅效率的影响8
1.4.2.4渣碱度的影响8
1.4.2.5(FeO)的作用9
1.4.2.6搅拌的作用9
1.4.3脱硅剂选择11
1.4.3.1脱硅剂种类11
1.4.3.2脱硅渣起泡12
1.5含铌铁水中碳、铌的氧化12
1.5.1铌的氧化12
1.5.2碳的氧化13
2课题研究的目的和意义14
3研究方案及进程15
3.116
参考文献17
1文献综述
1.1铁水预处理概论
铁水预处理是指高炉铁水在进入炼钢炉之前预先脱除某些杂质的预备处理过程,包括预脱硫、预脱硅和预脱磷,简称铁水“三脱”。
铁水预脱硅是一种发展较早的铁水预处理工艺,是分步精炼工艺的发展。
能改善炼钢炉的技术经济指标,降低炼钢费用,也可作为预处理脱磷、脱硫的前处理,可降低脱磷处理剂消耗,进一步生产纯净优质钢。
铁水预脱磷是近几年发展较快的铁水预处理工艺,对于减轻减轻转炉负担,缩短转炉冶炼周期,提高转炉产量,冶炼低磷钢种,提高钢种规格,提高钢的质量。
铁水预脱硫则是指铁水在进入炼钢炉前的脱硫处理过程,又称为炉外脱硫,它是铁水预处理中最先发展成熟的工艺。
在我国,铁水预脱硫是目前钢铁企业工艺技术结构调整、增铁节焦、改善钢材质量、扩大纯净钢冶炼品种、提高钢铁产品竞争力和附加值的最有效途径。
1.1.1铁水预处理的化学冶金学意义
近代钢铁冶金生产实践表明,传统钢铁冶金工艺—“高炉炼铁—转炉炼钢”有其不合理的地方:
(1)能耗高:
如硅在高炉先还原而后在炼钢炉再氧化,这一过程浪费了能耗。
研究表明[1]:
铁水每增加0.1%Si,高炉多耗热209,200kJ(50,000kcal)/t铁,而在转炉中,扣除熔渣热损失后1kgSi的有效发热量仅约6276kJ(1500kcal),能量利用率仅3%,这些热量仅能熔化废钢约4kg。
(2)不能满足现代工业对钢材质量的需求。
传统的转炉炼钢工艺在同一熔池中进行脱硅、脱磷、脱硫、脱碳等许多热力学条件相互矛盾的反应,极不合理,使一些化学反应难以充分进行,限制了钢质量的进一步提高。
因而,迫切需要对这种传统的钢铁冶金工艺进行改革,使其合理化、最优化。
20世纪80年代,近海石油的开采、汽车工业和大型建筑工程对钢材质量特别是钢中磷、硫含量的苛刻要求,使得在日本钢铁企业形成了一系列以铁水预处理为基础的“高炉炼铁——铁水预处理——转炉炼钢——炉外精炼——连铸”的钢铁冶金优化工艺,从而率先开创了纯净钢冶炼的先河。
因此,改革传统钢铁冶金工艺的出路之一就是采用铁水预处理,即走“高炉炼铁——铁水炉外预处理(脱硅、脱磷、脱硫)——转炉少渣炼钢(脱碳、升温)——钢水炉外精炼(去气体、去夹杂、合金化等)——连铸连轧或热装热
送”的钢铁冶金优化工艺道路。
这一新工艺尽管从工艺步骤上看,增加了工序,但从钢铁生产的连续性看并不影响生产率,其化学冶金学意义在于各分工序创造了最佳的冶金反应环境。
这样,高炉的主要任务是分离脉石、还原铁矿石,铁水预处理则主要完成脱硅、脱磷、脱硫,转炉进行脱碳、升温,钢水炉外精炼去气体、去夹杂、合金化等。
1.1.2铁水预处理的必要性
(1)提高钢材性能和扩大转炉冶炼钢种
汽车用钢、海上采油平台用钢、石油管线钢、硅钢等要求更高的性能,原工艺
不能满足要求,采用铁水预处理可以提高钢的纯净度和性能。
采用铁水预处理对于
新品种开发也起着重要作用。
抗氢致裂纹钢、IF钢,转炉冶炼高碳钢、合金钢、不
锈钢、耐腐蚀钢等用铁水预处理后开发了许许多多的新钢种,大大扩大了转炉冶炼
钢种的范围。
通过铁水预处理保证了钢性能的稳定性、均匀性。
(2)提高炼铁、炼钢技术指标
预处理技术不断开阔,保证良好的脱硅、脱磷、脱硫效果前提下,降低成本以及简单实用的操作技术已成为近些年的发展趋势。
(3)保证连铸和连铸坯质量
许多非金属夹杂物影响连铸顺利进行,有时会造成漏钢。
同时引起铸坯内裂
纹,严重影响铸坯表面质量,降低连铸坯收得率、轧材合格率。
因此国内外大型企
业炼钢用铁水基本上全部经预脱硫处理。
1.2国内外铁水预脱硅的基本现状
铁水脱硅有二种方式:
一种在高炉内进行,另一种是在高炉外进行。
1.2.1高炉炉内的铁水预脱硅技术
高炉炉内进行脱硅,即生产低硅铁水,既可降低高炉焦比,又配合了少渣炼钢。
但是低硅冶炼时高炉炉缸的热贮备很少,原燃料条件差时必须保持铁水含硅在较高的水平。
通过对解剖高炉内铁水中硅行为的调查[5],已基本弄清了炉高方向上硅含量的变化:
在软熔带下方1450℃左右的铁水中几乎不含硅,风口循环区温度1900℃以上含硅最高,炉芯部温度较低含硅亦低,两风口循环区之间温度有1800℃,焦炭内铁液含硅达5%以上。
当高硅铁水离开风口水平落下穿过渣层时,会发生2FeO+Si→2FeO+SiO2的脱硅反应。
根据铁水含硅在风口平面以下不再上升的现象,设想通过风口喷入脱硅剂进行炉内预脱硅。
与炉外脱硅相比,炉内脱硅能保持铁水温度不变;而炉外用固体脱硅剂操作,将使铁水温度下降50℃左右。
通过风口向炉内喷吹脱硅剂来进行脱硅的方法主要有:
(1)喷吹石灰石粉进行铁水脱硅
由于石灰石在风口循环区内会分解成CaO和CO2,此CaO与渣中或焦炭灰分中的SiO2结合,有助于抑制SiO2+C→SiO+CO反应的发展,因此可达到脱硅的效果。
日本千叶2号高炉采用此法,在喷吹量为8kg/t铁的条件下,在1490℃时[Si]下降0.1%。
(2)喷吹烧结矿粉进行铁水脱硅
从风口向炉内喷入粒度<3mm的烧结矿粉,每次喷25~45min,停吹30min,再继续
喷,如此反复。
(3)喷吹铁磷进行铁水脱硅
千叶2号高炉在向炉内喷入铁鳞时,喷入量为32kg/t铁,铁水温度在1450~1480℃时,[Si]下降约0.15~0.20%,但[S]却上升0.01%。
(4)喷吹瓦斯灰进行铁水脱硅
日本住友金属和歌山4号高炉,在对炉内喷吹瓦斯灰时,保持高炉入炉焦比等各种操
作条件不变,以风温调节炉热。
结果表明,喷吹物对风口循环区的透气性和通液性无不良
影响。
当铁水温度为1510℃,矿焦比为3.29时,只要喷入瓦斯灰量大于10kg/t铁,就有
降[Si]效果,喷吹量30kg/t铁时,[Si]从0.50%降至0.40%。
研究指出[10],通过缩短Si在炉内还原时间、抑制Si还原温度,减少渣—焦、煤气—
铁水作用面积及改变炉渣组成(控制SiO2的活度)都可以获得低硅生铁。
有人[11提出在炉缸渣口水平开设喷吹口,连续地向炉缸内喷吹压缩空气或富氧空气,喷入氧量约为鼓风带入氧量的5~10%,使已还原的硅重新氧化成SiO2。
在推行低硅铁冶炼技术时,要特别注意冶炼条件,不能忽视客观条件和铁水温度去片
面追求铁水的过低含硅量,这就是说低硅铁冶炼在一定的冶炼条件下有个低限范围。
例如
在杭钢生产条件下,生产实践归纳出的合适生铁含硅量为0.3~0.4%,低于0.3%时铁水温
度不足,生产难度增加,而且要求外部条件特别严格,困难很大[12]。
1.2.2高炉炉外铁水预脱硅技术
高炉炉外脱硅可以较灵活地调整Si含量。
常用的方法主要有两种:
(1)高炉铁水沟连续脱硅
高炉铁水沟脱硅处理的优点是不占用时间,处理能力大,温降小,渣铁分离方便;缺点是用于脱硅反应的氧利用率低、脱硅水平波动较大和工作条件较差。
经研究表明[15]在高炉铁水沟连续脱硅处理前后铁水含硅量与处理时间的关系为:
式中:
,
——处理前后铁水含硅量,%
t——处理时间,min
高炉铁水沟连续脱硅过程中脱硅量随时间的变化如图:
高炉铁沟连续脱硅分为以下几种。
自然投入法
这是一种早期使用的方法,即将粒度约3mm的脱硅剂投入到流动的铁水表面,借铁
水从主沟和倾斜流槽落入混铁车或铁水罐时的冲击搅拌作用,使脱硅剂与铁水混合产生脱硅反应。
此法工艺流程及设备都比较简单,但脱硅效率较低,一般为50%左右。
气体搅拌法
在自然投入法的基础上,向铁水表面吹压缩空气加强搅拌,以促进熔剂脱硅反应进行。
该法较自然投入法熔剂利用率高。
液面喷吹法
是在投入法基础上,将粒度小于1mm的脱硅剂依靠载气喷向铁水表面。
它和一般喷
吹法的主要区别在于喷枪不插入铁水内部。
射入铁水内部和浮于铁水表面的粉剂随铁水流
动落入混铁车内,靠落差冲击达到铁水与脱硅剂的进一步混合。
此法脱硅效果比较好,脱
硅剂利用率也高。
在许多场合下采用简便的出铁沟脱硅方式,脱硅率很难突破50%,同时受高炉操作因
素影响很大。
(2)在高炉—转炉间的铁水预处理车间进行铁水脱硅
从高炉来的铁水注入鱼雷型铁水罐或铁水罐内进行脱硅处理。
脱硅处理时,用氮气作载气通过耐材喷枪把粉剂吹入铁水中,同时吹氧气以防止温降。
这种脱硅法的优点是脱硅反应时氧的利用率高,工作条件好,处理后铁水中硅含量稳定;缺点是脱硅处理要占用一定时间及温度降低较多。
一般情况下当铁水硅含量高,在高炉出铁沟脱硅达不到目标要求时,才在运输容器中进行补充脱硅,以保证铁水含硅量在0.15%以下。
采用氧化铁系脱硅剂时,各种脱硅方法的脱硅效率顺序如下:
铁水罐气体搅拌脱硅法<出铁沟脱硅法<鱼雷罐车喷吹脱硅法<铁水罐喷吹脱硅法。
正确选择脱硅方法,应该考虑以下因素:
1)铁水含硅量。
当铁水含硅量>0.45%(质量百分数)时,以炉前铁水沟脱硅为
宜;含硅量<0.45%时,以铁水罐喷吹脱硅为好。
喷吹脱硅过程中,需顶吹部分O2作为气体氧化剂,以防止铁水降温太大[17];
2)出铁速度。
随着高炉出铁速度增大,脱硅剂喷吹强度提高,但为了避免喷溅和
脱碳,喷吹强度一般不允许很高;
3)扒渣能力。
若炼钢厂扒渣能力不足,应采用两段脱硅法,利用挡渣器分离渣铁
研究表明,脱硅后的渣子若不排掉,会对脱磷和脱硫产生不利影响。
1.3铁水预脱硅经济意义
铁水中的硅是转炉熔化大量废钢的廉价热源,从理论上讲,铁水中的硅含量降
低0.1%,转炉中熔化废钢的能力大约降低10kg/t。
另一方面熔剂的消耗也减少
了,每吨铁水约少用10kg石灰。
如果每吨熔剂(造渣材料)的成本低于每吨铁水和
废钢的差价,那么降低铁水中的含硅量从经济上来讲,可以认为是合理的[54]。
另外,降低硅含量,可以减少转炉的渣量,提高金属收得率,降低耐火材料的
消耗和提高生产率。
加拿大Dofasco钢厂资料[55]统计表明,铁水降硅0.1%,将增加
转炉炼钢金属收得率0.2%,延长炉衬寿命110炉。
少渣吹炼也会使转炉中合金元素
的收得率提高,例如锰和铬等。
从而有可能在转炉中使用便宜的合金化材料锰矿和
铬矿,而不用昂贵的锰铁和铬铁,这在经济上有重要意义。
当采用氧化铁系脱硅剂时,铁水中硅还原氧化铁,使铁水量增加。
这又从另一
方面提高了铁水脱硅的经济意义。
1.4脱硅原理、影响因素及脱硅剂
1.4.1脱硅原理
1.4.1.1硅氧化的热力学
热力学方程:
………………………………
(1)
……………………………………
(2)
……………………………(3)
由公式
(2)和(3)可以导出硅的分配比:
………………(4)
式中:
——温度为T时脱硅反应的平衡常数;
——
的活度;
——Fe的活度;
——FeO的活度;
——
的活度系数;
——Si的活度系数;
———Si的分配比;
——渣铁界面的
的浓度,%;
——渣铁界面上Si的浓度,%;
由公式(4)可知熔渣氧化性、碱度,降低温度有利于脱硅反应进行。
1.4.1.2硅氧化的动力学
动力学模型:
此反应可认为分成以下步骤:
(1)[Si]→[Si]*,铁液本体的硅通过铁液边界层扩散到渣—铁界面;
(2)(FeO)→(FeO)*,熔渣本体的FeO通过渣液边界层扩散到渣—铁界面;
(3)[Si]*+2(FeO)*=(SiO2)*+2[Fe]*,到达界面的硅和FeO在界面上进行化学反应生成
(4)(SiO2)*→(SiO2),界面上生成的SiO2通过渣液边界层扩散到熔渣本体;
(5)[Fe]*→[Fe],界面上生成的Fe通过铁液边界层扩散到铁液本体
以上步骤中,(3)为界面化学反应,
(1)、
(2)、(4)、(5)为反应有关物质在相应扩散层中的扩散过程。
成田等人用氧化铁脱硅实验发现:
渣中FeO含量大于40%时,铁水中硅向渣铁界面扩散是反应的限制环节。
FeO含量小于10%时,渣中FeO向渣铁界面扩散是反应的限制环节。
FeO含量在10%~40%之间,为两种扩散的混合控制。
一般情况下,渣中FeO含量在10%~40%之间之间,所以脱硅速率反应式为:
………………(5)
式中
——铁水的传质速率常数,
;
——硅的传质速率常数,
;
——铁液的密度,
;
——熔渣的密度,
;
A——渣铁接触面积;
——熔渣的体积;
由公式(5)可知,加强搅拌,增大金属和渣的传质系数有利于脱硅。
1.4.2影响因素
从以上热力学公式及动力学公式可得知,影响脱硅因素主要为:
渣碱度,渣氧化性,温度,搅拌强度。
从ChisatoYAMAGA等人研究中我们可以这几个因素的影响
1.4.2.1温度的影响
由脱硅热力学公式可以看出,脱硅是放热反应,故低温有利于脱硅。
上图中可以看出,随着温度的降低,终硅含量明显降低。
1.4.2.2渣量的影响
在其他条件一定的条件下,理论上渣量越大,提供的氧化剂,CaO增大,提高了硅在渣铁间的分配比。
从上图看出,渣量越大,脱硅幅度越大
1.4.2.3铁水初始含硅量对脱硅效率的影响
生产实践表明[24],铁水初始含硅量越高,脱硅量和脱硅效率都越高,如图1.3所示。
这是因为铁水初始硅含量高,铁水中[Si]的活度大,有利于脱硅反应的进行。
但是铁水初始硅含量过高,要达到炼钢所需的含硅铁水,脱硅剂消耗亦相应增加。
1.4.2.4渣碱度的影响
渣碱度对脱硅影响比较大,随着硅的氧化反应,二氧化硅进入渣中,脱硅渣碱度降低,很大程度上破坏了脱硅热力学条件。
同时,二氧化硅含量的增加,渣粘度增大,脱硅过程产生的CO得不到及时排放,容易造成泡沫渣。
所以应维持适当的渣碱度,创造合适的脱硅热力学条件,提高脱硅率。
在碱性条件下,SiO2与CaO结合形成稳定的硅酸钙,SiOγ(SiO2活度系数)很小,LSi(硅在渣铁之间的分配比)很大,硅氧化进行得很彻底。
在脱硅后期,由于仍是在碱性条件,2SiOγ仍然很小,故渣中SiO2很难还原
如上图看出,随着渣碱度增大,脱硅幅度增大。
1.4.2.5(FeO)的作用
FeO作为最主要的氧化剂,为脱硅提供氧元素。
因此理论上渣中FeO越多,提供越多的有效氧,脱硅效果越好。
图中渣中(FeO)越大,脱硅幅度越大
1.4.2.6搅拌的作用
从脱硅动力学的角度来看,加强搅拌,增大了各反应元素在铁液和渣中的传质速率,同时增大了渣铁间的反应界面区域。
根据Sunayama等的研究,在顶底复吹转炉实验中,研究了搅拌能和铁水传质系数以及铁水密度乘积的关系,得出以下结论:
——铁水传质系数,m/s
——铁水密度,kg/m3
——搅拌能量,
A——比例系数。
如下图所示:
王庆祥等人研究了脱硅动力学,指出加强搅拌,可以降低渣中FeO利用率,降低了扩散层厚度和增加了反应界面面积。
如下图:
总之通过研究影响脱硅热力学和动力学因素分析可知,脱硅的最佳热力学、动力学条件是:
(1)降低反应温度
(2)增大渣量
(3)合适的初始硅含量
(4)提高熔渣碱度;
(5)增大熔渣氧化性;
(6)提高熔池搅拌强度。
1.4.3脱硅剂选择
1.4.3.1脱硅剂种类
铁水预脱硅是实现铁水三脱预处理(预脱硅、预脱硫、预脱磷)的重要一环。
它
对开发新钢种、冶炼优质钢、提高转炉生产能力、降低成本具有重要意义[39~41]。
铁
水脱硅是氧化反应。
脱硅剂以提供氧源的材料为主,以调整炉渣碱度和改善流动性
的熔剂为辅。
常见的氧化剂是含氧化铁及氧化锰的各种固体粉添加方式在炉前铁水沟中连续脱硅时,脱硅剂料,如氧化铁皮(铁鳞)、铁矿石、烧结扩、球团矿、铁精加入量按照铁水的初始含硅量及脱硅目标值来确定,矿粉、高炉炉尘、烧结灰、贫锰矿等。
当采用喷吹法脱硅脱硅剂的加料速度按出铁速度控制。
脱硅剂由皮带运·时,氧气则是良好的气体脱硅剂,同时还对铁水起搅拌料机直接加勤铁水表面,或者用载气经管道送入铁水作用。
固体氧化剂和气体氧化剂分别为脱硅反应提供沟上方,再经减速装置加到铁水表面。
这两种添加方式了固态氧和气态氧。
各种脱硅剂的脱硅能力主要决定的脱硅效果相同,但后者因采用管道输送而不占用出于其中的有效氧含量,常用的脱硅剂中以氧化铁皮的铁场作业面积,适用于多出铁场或旧厂房改造。
在炉前脱硅能力最强,烧结矿粉次之。
当采用气体脱硅剂时,铁水沟中脱硅不额外占用处理时间,处理能力较大,铁还能使铁水温度升高从而减缓整个处理过程的温降,水温降较少,渣、铁分离较方便;然而铁水流经时间短而固体脱硅剂只会使铁水温度降低。
因此,可以同时采暂,用于脱硅反应的氧的利用率较低,难以实现深脱用并调节二者的比例,以适当控制脱硅处理后的铁水硅。
高炉炉外脱硅还可以在铁水包或混铁车中采用喷温度,满足后续工序的要求。
粉脱硅方式进行,此时由于反应时间较充分,脱硅剂可成渣齐l由于脱硅反应生成以5102为主要成分以喷吹到铁水深部,脱硅剂中氧的利用率较高,因此脱的熔渣,为改善脱硅渣的性能,需要随同氧化剂加入含硅效果更好,很显然铁水温降也较大。
加入的成渣剂使脱硅渣碱度达到0.6-1.0。
可用的脱硅剂有:
铁矿石﹑球团矿﹑烧结矿﹑轧钢铁皮﹑锰矿石和转炉与电炉的除尘灰,示例成分见表1。
在高炉出铁沟内脱硅,各种氧化铁之间的脱硅氧效率没有很大差别;混有石灰的锰矿比氧化铁的脱硅氧效率要高些,锰的还原率可达70%~90%;用氧气顶吹时,脱硅氧效率没有多大增加,但可以一边升温一边脱硅;喷射氧气法,同时
脱硅和升温,脱硅氧效率也高。
脱硅剂
TFe
Ca0
Si02
A1203
MgO
0
氧化铁皮
烧结返矿
烧结矿尘
转炉尘
铁精矿粉
69.2
52.3
47.5
53.6
66.4
O.03
12.O
13.25
12.8
O.54
1.75
7.60
6.80
2.20
9.58
0.18
1.88
3.20
1.71
1.34
23.18
20.98
20.0
22.83
25.71
脱硅溶剂主要有:
CaO﹑CaO+CaF2﹑CaO+CaF2+Na2CO3,其作用是调整渣碱度,提高渣的流动性,降低铁和锰的损耗。
1.4.3.2脱硅渣起泡
脱硅过程中伴随明显的脱硅渣起泡现象,一般加入脱硅剂后,当渣熔化脱硅开始时即开始起泡。
目前尽管已经认识到起泡的原因,但控制的手段不是很多。
日本采取的主要措施是铁水罐上留有一定的空间(约1m),这样脱硅渣的起泡就影响了铁水罐装铁容量。
用固体氧化剂脱硅时,起泡高度为:
实验室70~110%铁水深度,约50~90mm,工业上约为300~1200mm。
脱硅渣起泡的原因现一致认为是脱硅过程中伴随脱碳反应产生的,CO气体穿过渣层上逸时,使渣上涨而形成“泡沫”,类似于转炉中的泡沫渣。
因此渣“起泡”有两个因素:
有起泡源即CO气体。
经计算,脱硅0.15%,生成的CO气体是铁水体积的120倍;
气体穿过渣层逸出的难易程度。
渣层越粘,CO气体逸出越难,起泡越高。
因此减少脱硅过程的渣起泡必须从三个方面着手:
减少脱碳量。
这就要求有适宜的供氧速度和强度,与脱硅反应相一致。
供氧速度过大,脱碳量增加,渣起泡增高;
改善脱硅渣性能。
如:
好的流动性,低的粘度,适宜的渣碱度:
CaO/SiO2以0.5~0.9为宜:
增大渣的表面张力,使渣不宜“起泡”,如加一定量的MnO、Al2O3、CaO、MgO等。
加强搅拌,强化破泡沫渣措施。
如当渣上涨到一定高度时,加入泡泥等压渣剂。
1.5含铌铁水中碳、铌的氧化
1.5.1铌的氧化
5
……………………(6)
……………………(7)
…………(8)
代入
可得:
(9)
在1300℃下,有文献[2]报道
=10-10~10-11左右,现取
=10-9、
=10-10和
=10-11,
=0.005,分别计算含铌铁水中的氧活度。
含铌铁水中铌氧化的氧活度(温度:
1573k;
=0.00724)
10-9
10-10
10-11
0.007285
[Nb]
0.027
0.013
0.006
0.027
0.013
0.006
0.027
0.013
0.006
19.67
9.471
4.371
19.67
9.471
4.371
19.67
9.471
4.371
1.44
8.