光学零件加工技术课程设计工艺规程编制模板.docx
《光学零件加工技术课程设计工艺规程编制模板.docx》由会员分享,可在线阅读,更多相关《光学零件加工技术课程设计工艺规程编制模板.docx(14页珍藏版)》请在冰豆网上搜索。
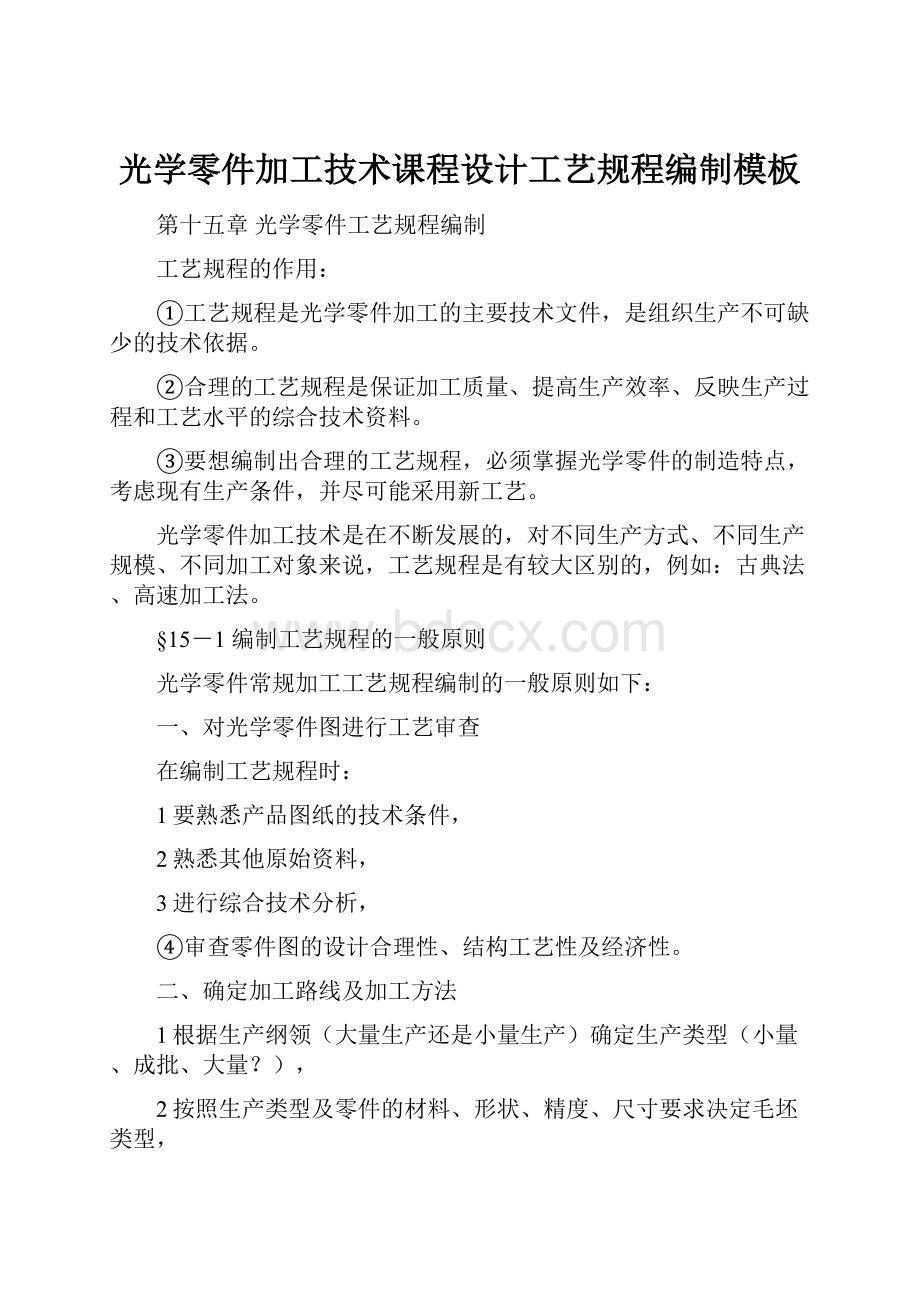
光学零件加工技术课程设计工艺规程编制模板
第十五章光学零件工艺规程编制
工艺规程的作用:
①工艺规程是光学零件加工的主要技术文件,是组织生产不可缺少的技术依据。
②合理的工艺规程是保证加工质量、提高生产效率、反映生产过程和工艺水平的综合技术资料。
③要想编制出合理的工艺规程,必须掌握光学零件的制造特点,考虑现有生产条件,并尽可能采用新工艺。
光学零件加工技术是在不断发展的,对不同生产方式、不同生产规模、不同加工对象来说,工艺规程是有较大区别的,例如:
古典法、高速加工法。
§15-1编制工艺规程的一般原则
光学零件常规加工工艺规程编制的一般原则如下:
一、对光学零件图进行工艺审查
在编制工艺规程时:
1要熟悉产品图纸的技术条件,
2熟悉其他原始资料,
3进行综合技术分析,
④审查零件图的设计合理性、结构工艺性及经济性。
二、确定加工路线及加工方法
1根据生产纲领(大量生产还是小量生产)确定生产类型(小量、成批、大量?
),
2按照生产类型及零件的材料、形状、精度、尺寸要求决定毛坯类型,
③根据生产类型及毛坯类型确定加工路线和加工方法。
三、设计必要的专用样板,或选择通用样板。
主要是标准样板和工作样板。
四、确定加工余量及毛坯尺寸
根据生产类型、加工方法、毛坯类型确定各工序的加工余量。
应先从最后一道工序开始确定加工余量,例如,透镜的加工余量应先从定心磨边开始给定直径尺寸,棱镜和平面镜应先从抛光开始给定厚度尺寸,然后再考虑各工序中的相应余量。
最后给出总余量和毛坯尺寸。
五、设计及选用工夹具、机床、测量仪器
在确定加工路线和加工余量后,按各工序的要求,设计必要的工、夹具,如透镜的精磨、抛光工、夹具设计,包括粘结膜、贴置模、精磨模、抛光模等的设计。
并根据生产条件选用机床和测量仪器。
六、选用必需的光学辅料。
光学零件生产中所使用的光学辅料主要有清洗材料、粘结材料、磨料、抛光剂、抛光模层材料、保护材料等,应根据生产需要进行认真地选择。
七、填写光学零件工艺卡片
将光学零件工艺规程编制的结果写入工艺卡片,作为技术文件,直接用于管理和指导生产。
§15-2透镜工艺规程编制的步骤
透镜工艺规程编制的步骤如下:
一、设计球面标准样板
1、参照第十章表10-1确定标准样板的外形和尺寸。
2、若系弧形样板则按如下步骤设计、计算:
(1)根据标准样板的外径大小,选择球径仪的测环口径。
测环口径应比标准样板直径小5~10㎜为宜。
(2)根据球径仪测环的形式,确定球面矢高计算公式,计算矢高(一般应给出凹凸面的矢高和)。
(3)按图纸规定的标准样板精度等级⊿R,取其1/2~1/5⊿R来计算矢高的制造公差.
(4)设计标准样板制造用的各种球模和夹具。
二、设计球面工作样板
1、按磨边前的零件直径确定工作样板的直径和其他尺寸。
工
作样板的直径一般大于零件直径1~3mm。
工作样板的其他尺寸见§10-1。
2、设计工作样板制造用的各种球模和夹具。
三、确定透镜定中心磨边的工艺过程
1、根据零件中心偏差的要求,确定是否需要定中心磨边。
2、根据零件直径、中心偏差要求的大小和设备情况确定定中
心磨边方法。
3、确定定中心磨边的余量,一般可按下列情况考虑。
(1)焦距ƒˊ<300㎜的透镜,磨边余量按第八章表8-2选取。
但当中心厚度及边缘厚度相差较小时,磨边余量要按边厚差计算公式来计算,见§8-4。
(2)焦距ƒˊ≥300㎜的透镜,磨边余量一般按可能控制的边厚差计算,见§8-4。
(3)偏心透镜的磨边余量,取上述磨边余量及偏心量之和。
(4)确定厚透镜磨边余量时,要考虑厚度方向的偏斜。
4、选择定中心磨边用的工具及辅助材料
(1)设计或选择定中心磨边用的接头和辅助工具。
(2)选择磨论、磨边胶、冷却液、清洗剂等。
5、编制透镜定中心磨边工艺的规程
四、确定透镜的精磨、抛光工艺过程
1、加工顺序
(1)应加工曲率半径大的一面,若是修厚度尺寸或修边厚差的零件,应先加工曲率半径小的一面。
(2)应先加工表面疵病要求低的表面。
(3)对凹凸球面透镜,应先加工凹面。
2、设计镜盘
镜盘的设计,见第十一章。
3、设计模具
(1)按镜盘尺寸确定粘结模、精磨模、抛光模的主要尺寸,详见第十一章。
(2)根据零件的精度要求,设计手修模。
(3)确定各种球模的结构、尺寸及材料,详见第十一章。
4、确定透镜精磨、抛光余量
透镜精磨及抛光的余量,按下述情况确定:
(1)透镜厚度公差大于±0.1㎜时,其单面余量为0.06~0.1。
(2)透镜厚度公差小于±0.1㎜时,其余量还应加上修磨余量。
修磨余量一般为0.01~0.05。
(3)特硬或特软材料,厚度余量应相应减少或增加。
(4)如果要求按胶合厚度配合尺寸时,则控制单件厚度公差为胶合厚度公差之半,或者两单件厚度公差之和为胶合厚度公差。
5、选择透镜精磨、抛光用的设备及辅助材料
根据工艺要求,选择磨料、抛光粉、粘结材料、抛光模层材料、保护材料以及清洗材料等。
6、编制透镜精磨及抛光的工艺规程。
五、确定透镜粗磨工艺过程
1、加工顺序的安排
在一般情况下,粗磨加工应按如下顺序安排:
(1)应先加工曲率半径较大的一面。
(2)凹凸透镜应先加工凹面。
(3)球面铣磨后,如达不到粗磨完工表面质量要求时,还应考虑手修加工。
(4)如是需钻孔的透镜,一般应将钻孔安排在磨球面之前。
(5)铣槽应根据零件的结构要求酌情安排。
2、确定粗磨余量
(1)根据毛坯种类(型料或块料)和尺寸的不同,应给及不同的余量,见表15-1。
表15-1粗磨余量
直径(边长)
<65
>65~120
>120~200
毛坯表面种类
单面余量
零件种类
底面
上表面
底面
上表面
底面
上表面
透镜
块料
1.0
1.0
1.2
1.2
1.5
1.5
型料
1.0
0.8
1.2
1.0
2.0
1.2
平面镜
块料
1.0
1.0
1.5
1.5
1.8
1.8
型料
1.2
0.8
1.8
1.2
2.5
1.5
棱镜
块料
1.0
1.0
1.5
1.5
1.8
1.8
型料
1.2
0.8
1.8
1.2
2.5
1.5
(2)铣磨达不到粗磨完工的表面质量要求时,应考虑留手修余量,见表21-2。
表15-2手修余量
铣磨后的粗糙度
单面手修余量(㎜)
达180#砂眼
达240#砂眼
达280#砂眼
1.30
1.20
0.10
(3)需要划切的零件应留有划切的余量。
划切余量见表21-3。
表15-3划切余量单位:
㎜
毛坯直径
余量
玻璃厚度
<10
10~30
30~50
50~100
<3
3~5
5~10
10~20
0.5~1
0.3~0.8
0.5~1.0
0.8~1.5
0.3~0.8
0.5~1.0
0.8~1.2
0.8~1.2
1.0~1.5
1.0~2.0
(4)磨凸起部分时,一般不考虑留余量。
(5)用散粒磨料和用固着磨料磨具加工时,应给于不同的加工余量。
(6)选择磨料的粒度号。
(7)需钻孔的零件,孔的断面应有修裂纹的余量。
(8)特硬或特软材料的加工余量,应适当减少或增大。
3、确定透镜粗磨完工尺寸
(1)根据抛光完工应达到的球面曲率半径和粗磨球面曲率半径的修正量,确定粗磨完工的球面曲率半径。
(2)粗磨完工的零件直径等于定中心磨边前的直径,其公差一般在0.1~0.3㎜左右。
若不需要定心磨边,粗磨完工直径即为零件完工直径。
(3)粗磨完工的厚度尺寸,为零件完工的厚度尺寸的上限加上两面精磨、抛光余量,其公差酌情而定。
(4)具有凹面的零件应计算出凹面的矢高,给出总厚度尺寸。
(5)倒角尺寸按零件设计及工艺要求给定。
4、设计粗磨工装
(1)如采用铣磨加工方法,则由透镜口径大小选择磨轮中径和粒度,计算出磨头中心线及主轴中心线间的夹角。
(2)如果用散粒磨料粗磨,设计单块加工用粗磨模,并设计必要的夹具和选用量具等。
5、选择磨料、冷却液、粘结材料、清洗材料。
6、编制透镜粗磨工艺规程。
六、透镜毛坯加工
1、确定毛坯尺寸
(1)按生产量尽可能选用热压成型料或棒料。
(2)块料毛坯尺寸尽可能为零件直径的整数倍。
(3)线尺寸为零件完工尺寸加上各道工序的加工余量,允差为自由公差。
(4)型料毛坯尺寸,由粗磨完工的球面曲率半径、直径和修正量来计算确定。
(5)按热压成型料的外形尺寸,计算出毛坯的重量。
(6)绘制毛坯图。
2、绘制毛坯图应注意的问题
一般应在毛坯外形尺寸下面,用括号注明完工尺寸,以便参考。
§15-3透镜工艺规程编制举例
现以一双胶合物镜中的凹凸透镜的生产工艺规程编制为例说明之。
凹凸透镜的生产图纸见图15-4和图15-5。
一、工艺分析
由图15-4和图15-5可以看出:
⑴双胶合物镜两外表面的光圈要求较高,用甲醇胶胶合后表面会变形,需要手修。
⑵双胶合物镜完工后,要求检查像质,此要求较难达到,在胶合、镀膜等工序中应考虑采取必要的工艺措施。
⑶双胶合物镜加工工序应先胶合而后镀膜。
⑷凹凸透镜的光圈要求较高,应考虑表面修整方法。
二、编制工艺规程
(一)设计标准样板
⑴标准样板的外形尺寸。
根据该零件的曲率半径,按第十章的表10-1确定之,见表15-4。
表21-4标准样板尺寸单位:
㎜
零件曲率半径R
样板直径D
样板总高H
凸面
凹面
凸面
凹面
390.8
1694.3
130
130
130
130
30
25
30
25
⑵标准样板矢高的计算。
此标准样板,采用带钢珠测环的球径仪测量矢高。
由第十章的(10-1)式得矢高计算公式:
(15-1)
其中
(15-2)
式中,
--理论矢高,
--样板曲率半径,
--钢珠球心所在圆平面的半径,
--理论测环半径,
---钢珠半径。
根据零件球面曲率半径和标准样板直径,选择最大测环,其r和ρ值为:
r1=59.957ρ1=5.142
将r和ρ值代入(15-1)和(15-2)式,计算后得两球面的双矢高如下:
2hR390.8=9.2552
2hR1694.3=2.12242
然后用下式验算曲率半径:
(15-3)
演算结果:
R1=390.793
R2=1694.292
此值均在产品图上球面公差⊿R和N的要求范围以内。
⑶矢高制造公差。
由下式求得:
(15-4)
式中,K取2/5~1/5,计算后(绝对值)得:
⊿hR390.8=0.001
⊿hR1694.3=0.0005
因此,最后得总矢高及公差:
2hR390.8=9.2552±0.002
2hR1694.3=2.12242±0.001
⑷加工标准样板用的模具。
此类模具的设计及一般球面模具相同,其工作表面尺寸可参考表15-5。
表15-5加工标准样板用球模尺寸单位:
㎜
曲率半径
R
球磨
面形
粗磨球模
抛光球模
半径
直径
半径
直径
390.8
凸
凹
389.62
391.98
200
200
387
395
160
140
1694.3
凸
凹
1675.49
1713.11
200
200
1690
1699
160
160
(二)设计工作样板
⑴工作样板尺寸。
根据该零件定中心磨边前的直径和曲率半径,确定工作样板尺寸,见表15-6。
表15-6工作样板尺寸单位:
㎜
曲率半径
工作样板直径
工作样板总高
+390.8
-1694.3
61
62
30
30
表15-7工作样板球模尺寸单位:
㎜
球模类型
球模尺寸
曲率半径
粗磨球模
精磨球模
抛光球模
半径
口径
半径
口径
半径
口径
+390.8
-1694.3
-396.5
+1694.3
90
110
-390.8
1694.3
65
80
-395
+1690
80-85
80-85
⑵设计工作样板制造用的模具。
及一般球模设计相同,工作样板制造用球模的工作表面尺寸见表15-7所示。
(三)编制定中心磨边工艺规程
⑴给定磨边余量。
此凹凸透镜焦距较长,磨边余量必须由计算透镜边厚差值确定,边厚差由下式计算:
(15-5)
计算时,逐渐增大磨边余量⊿D值,计算出合理的边厚差。
应以既使磨边余量不易太大,又使精磨抛光加工不困难为原则。
现取磨边余量为6㎜,则得边厚差Δt为:
Δt=0.35mm
⑵设计定中心磨边接头。
定中心磨边接头直径比零件完工直径小0.15~0.3㎜。
⑶设计倒角球模。
倒角球模曲率半径由下式计算:
=37mm(15-6)
(四)编制透镜精磨、抛光工艺规程
⑴由定中心磨边余量计算出的边厚差值,可断定透镜精磨、抛光加工中是否要进行修改边厚差。
⑵从产品图上看到,透镜面形精度要求较高,应设计单块手修模。
⑶进行镜盘设计。
根据第十一章讲到的镜盘设计方法进行镜盘设计.
⑷根据镜盘尺寸确定该透镜加工用的粘结模、精磨模、抛光模、手修模之工作表面尺寸。
计算结果见表15-8。
⑸给定精磨抛光余量(一般取0.15㎜)。
表15-8透镜球模尺寸单位:
㎜
球模类型
球模半径
曲率半径
粘结模
精磨球模
抛光球模
手修球模
半径
口径
半径
口径
半径
口径
半径
口径
-390.8
+1694.3
-406
+1679
280
280
+390.8
-1694.3
280
280
+387
-1699
280
280
+387
-1699
80
80
(五)编制粗磨工艺规程
⑴确定粗磨模曲率半径Rc
Rc=Rp±⊿R(15-7)
Rp为抛光完工后的曲率半径,⊿R一般取0.3~0.8㎜
R390.8的粗磨球模半径为Rc385、直径为Dc180。
R1694.3的粗磨球模半径为Rc1705、直径为Dc180。
⑵计算开球面前的玻璃平板厚度用下式计算玻璃平板厚度尺寸B:
(15-8)
式中,dc—透镜粗磨后的中心厚度;hc—粗磨后凹面矢高;Rc—粗磨后曲率半径;Dc—定中心磨边前透镜直径。
将本例的具体数据代入得:
hc=1.14㎜
B=10.45+1.14=11.59㎜
给定实际制造尺寸及公差
B=11.6-0.1
⑶倒角球模的曲率半径为R42,球模的结构按通用磨具结构设计。
⑷参照粗磨余量规定,取毛坯厚度为14㎜。
⑸绘制毛坯图。
(六)填写工艺卡片。
将工艺规程填入工艺卡片,并在各工序的工艺卡片主页上给出必要的工艺图。
见表15-9~表15-1