循环流化床锅炉专业知识讲解.docx
《循环流化床锅炉专业知识讲解.docx》由会员分享,可在线阅读,更多相关《循环流化床锅炉专业知识讲解.docx(50页珍藏版)》请在冰豆网上搜索。
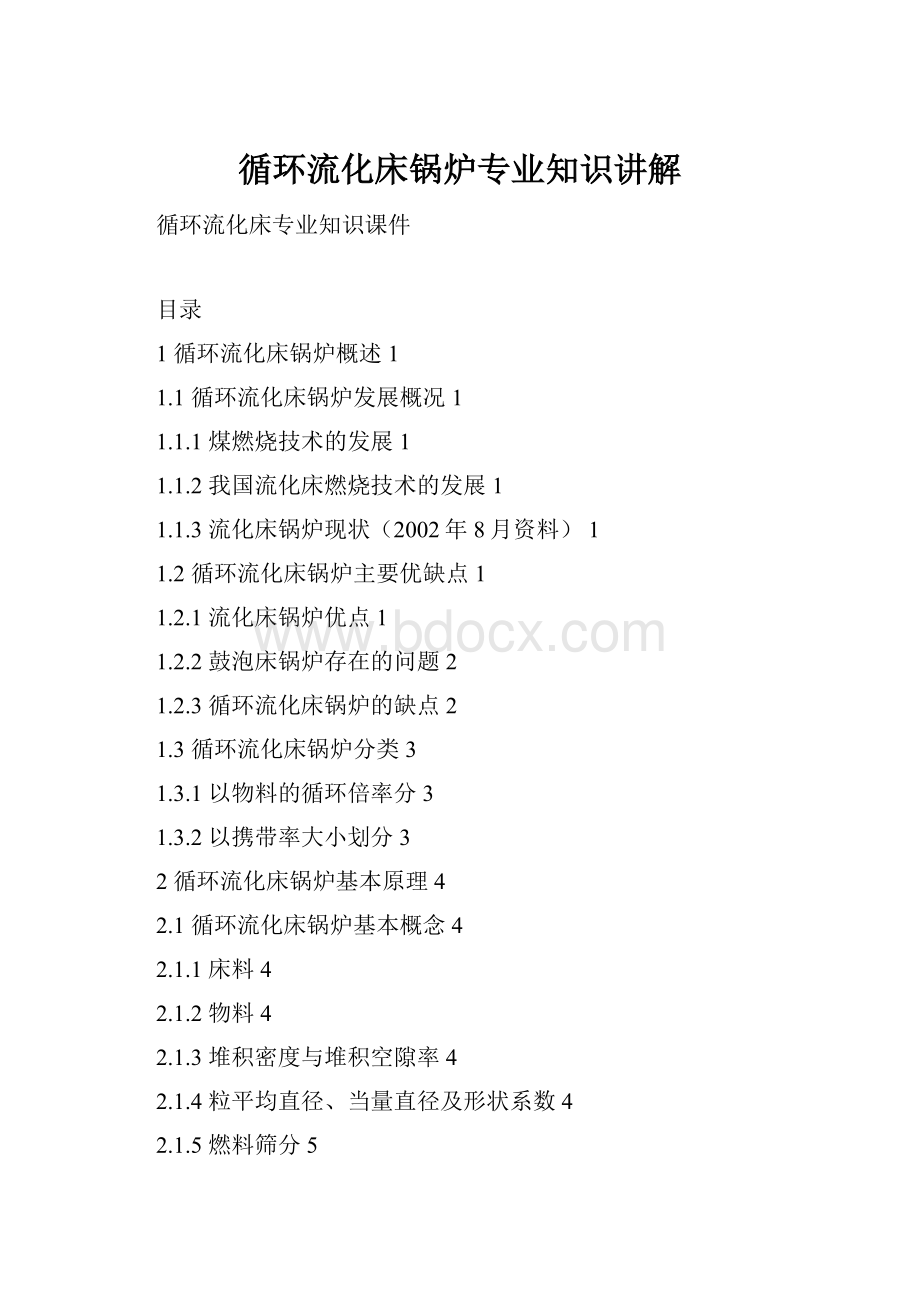
循环流化床锅炉专业知识讲解
循环流化床专业知识课件
目录
1循环流化床锅炉概述1
1.1循环流化床锅炉发展概况1
1.1.1煤燃烧技术的发展1
1.1.2我国流化床燃烧技术的发展1
1.1.3流化床锅炉现状(2002年8月资料)1
1.2循环流化床锅炉主要优缺点1
1.2.1流化床锅炉优点1
1.2.2鼓泡床锅炉存在的问题2
1.2.3循环流化床锅炉的缺点2
1.3循环流化床锅炉分类3
1.3.1以物料的循环倍率分3
1.3.2以携带率大小划分3
2循环流化床锅炉基本原理4
2.1循环流化床锅炉基本概念4
2.1.1床料4
2.1.2物料4
2.1.3堆积密度与堆积空隙率4
2.1.4粒平均直径、当量直径及形状系数4
2.1.5燃料筛分5
2.1.6燃料粒比度5
2.1.7流态化5
2.1.8流化速度5
2.1.9临界流速与临界流量5
2.1.10“散式”流态化和“聚式”流态化5
2.1.11物料循环倍率5
2.2流化床的形成6
2.2.1流化床的形成过程6
2.2.2几种不正常的流化状态7
2.3循环流化床锅炉炉内动力特性9
2.3.1床层高度、阻力与气流速度变化的关系9
2.3.2炉内物料颗粒运动和浓度分布10
2.4循环流化床锅炉煤燃烧与炉内传热11
2.4.1煤的燃烧11
2.4.2炉内传热13
3循环流化床锅炉主要设备及作用15
3.1燃烧设备15
3.1.1燃烧室15
3.1.2布风板与风帽15
3.1.3点火方式与点火装置(启动燃烧器)17
3.1.4给煤机与给煤方式19
3.2物料循环系统21
3.2.1物料循环系统组成及作用21
3.2.2物料分离器21
3.2.3回料立管24
3.2.4回料阀25
3.3风烟系统27
3.3.1风系统的分类及作用27
3.3.2送风系统的几种布置形式28
4循环流化床锅炉的运行30
4.1循环流化床锅炉的启动和停炉30
4.1.1锅炉冷态实验30
4.1.2锅炉点火启动32
4.1.3锅炉压火热备用33
4.1.4锅炉压火后启动33
4.1.5停炉33
4.2循环流化床锅炉运行调节35
4.2.1锅炉运行调节的主要任务35
4.2.2水位监视与调整35
4.2.3过热蒸汽温度的监视与调整36
4.2.4过热蒸汽压力控制36
4.2.5锅炉燃烧调节36
4.3循环流化床锅炉事故分析38
4.3.1灭火38
4.3.2结焦事故39
4.3.3烟道内可燃物再燃烧39
循环流化床锅炉专业知识课件
1循环流化床锅炉概述
1.1循环流化床锅炉发展概况
1.1.1煤燃烧技术的发展
在19世纪80年代,随着蒸汽机的发明,开发出了固定床层燃技术,至今,我国工业锅炉的绝大多数仍然是层燃锅炉。
至20世纪30年代,层燃技术已不能满足电力工业对更大容量更高效率的燃煤锅炉的需求,从而开发了煤粉燃烧技术。
60多年来,煤粉燃烧技术已得到了长足的发展,现在仍然是统治着全世界燃煤发电厂的燃烧方式。
煤粉炉不但可以燃烧各种不同的煤种,并能达到90%以上的锅炉效率,煤粉炉的单机最大容量已达1300MW。
煤粉炉可设计成超临界蒸汽参数的机组,并实现了运行操作的全部自动化。
1.1.2我国流化床燃烧技术的发展
我国是国际上最早开展流化床燃烧技术研究开发的国家之一。
自从1965年建成第一台燃烧油页岩的工业鼓泡流化床锅炉(在广东茂名投产)以来,流化床煤燃烧技术很快在全国得到推广。
现在全国有3500余台鼓泡流化床锅炉在运行,数量为居世界之首。
我国对循环流化床锅炉技术的研究和开发起步较晚,80年代以后,我国循环流化床技术发展迅速。
(1988年第一台35t/h锅炉在山东明水电厂投产)。
居不完全统计,至2002年底,已有830余台循环流化床锅炉投入运行,但大多数为容量在75t/h—220t/h以下的中小型锅炉。
1.1.3流化床锅炉现状(2002年8月资料)
世界上作为一种先进的清洁煤燃烧技术,流化床锅炉技术20多年来得到了很大发展。
现在,容量为350MW的世界上最大的鼓泡流化床锅炉已在日本建成投产。
在循环流化床锅炉的国际市场上,已售出的循环流化床锅炉(不包括中国生产的循环流化床锅炉)已超过450台,其中容量超过200MW的循环流化床锅炉为12台以上,有6台已投入运行。
两台当前最大的300MW容量的循环流化床锅炉于2002年在美国佛罗里达洲的JEA电厂投入运行。
容量为600MW的循环流化床锅炉的设计也已完成。
这些说明了循环流化床锅炉已开始进入大容量燃煤电站锅炉领域。
1.2循环流化床锅炉主要优缺点
1.2.1流化床锅炉优点
1.2.1.1低温燃烧
炉内新燃料比例很小,只有2%—3%,即使燃烧温度仅为850—900℃,流化床锅炉也能高效稳定地燃烧任何固体燃料。
1.2.1.2燃料适应性广
几乎可以燃烧各种煤,至今已成功在流化床锅炉上燃烧过的燃料包括一切种类的煤,其中有高灰分、高水分的褐煤,低挥发分的无烟煤,各种煤的煤矸石、洗矸、洗煤泥浆,石煤,各种石油焦,油页岩,泥煤,城市垃圾,油污泥,废轮胎,农林业生物质废料(如树皮、木屑、稻壳、甘蔗渣)等,也可燃烧各种液体燃料和气体燃料。
1.2.1.3有利于环境保护
流化床锅炉NOX的生成量仅为煤粉炉的1/4—1/3,又由于炉内温度最适合脱硫,向炉内投入适量石灰石,就可以达到90%的脱硫效率。
所以,流化床是一种经济有效的低污染煤燃烧技术。
1.2.1.4燃烧强度大
炉内混合强烈,而且在整个炉膛中进行,燃烧热强度大,炉膛截面积和体积小
1.2.1.5床内传热能力强
鼓泡床内传热系数可答233—326W/(m2K),循环流化床锅炉炉膛内气固两相混合物对水冷壁的传热系数在250—100W/(m2K)
1.2.1.6负荷调节性能好
储热量大,在负荷低于25%额定负荷下也能保持稳定燃烧。
1.2.1.7易于操作和维护
炉温低,不存在炉内结渣,炉膛内不需布置吹灰器,炉温低也减小了发生传热危机和爆管的机会。
燃烧的腐蚀作用也小,但磨损严重,可在易磨部位采取防磨措施,已经得到解决。
1.2.1.8灰渣便于综合利用
低温烧透的灰活性好,含碳量低,可以用作制造水泥的掺和料或其它建筑材料的原料。
1.2.2鼓泡床锅炉存在的问题
a)采用宽筛分燃料时,固体未完全燃烧热损失增大锅炉热效率下降
b)石灰石的钙利用率低,要使脱硫效率达到90%以上,钙硫摩尔比一般需在3左右,消耗大量石灰石。
c)鼓泡床锅炉的床内埋管及炉墙和尾部受热面的磨损问题还有待彻底解决。
d)随着鼓泡床锅炉容量的增大,床的截面几积增大,限制了鼓泡床锅炉向大型化发展。
1.2.3循环流化床锅炉的缺点
a)循环流化床锅炉的气固分离和床料循环系统比较复杂,运行维修费用高。
b)燃烧效率受燃烧温度限制,一般略低于煤粉炉。
c)床内流速高,固体浓度大,炉内存在还原性气氛区域,受热面的磨损与腐蚀问题仍要十分重视。
d)添加石灰石在燃烧中脱硫,脱硫效率低于烟气湿法脱硫。
对于发达国家更严格的SO2排放标准仍存在问题。
1.3循环流化床锅炉分类
1.3.1以物料的循环倍率分
a)低倍率循环流化床锅炉,K<15;
b)中倍率循环流化床锅炉K=15~40;
c)高倍率循环流化床锅炉,K>15。
1.3.2以携带率大小划分
携带率大小即炉室出口单位烟气携带物料的多少,按其可分为:
a)低携带率循环流化床锅炉v<3kg/Nm2;
b)中携带率循环流化床锅炉v=5kg/Nm2;
c)高携带率循环流化床锅炉v>8kg/Nm2。
2循环流化床锅炉基本原理
2.1循环流化床锅炉基本概念
2.1.1床料
锅炉启动前,步风板上先铺有一定厚度、一定粒度的“原料”称做床料。
2.1.2物料
主要是指循环流化床锅炉运行中在炉膛内燃烧或再热的物质。
它不仅包括床料成分,还包括锅炉运行中给入的燃料、脱硫剂、返送回来的飞灰以及燃料燃烧后产生的其它固体物质。
分离器捕捉下来通过回料阀返送回炉膛的物料叫循环物料,未被捕捉下来的细小颗粒一般称做飞灰,炉床下部排出的较大颗粒叫炉渣
2.1.3堆积密度与堆积空隙率
a)堆积密度
单位体积固体颗粒燃料或物料自然堆放时的质量叫堆积密度ρ堆(Kg/m3)。
b)颗粒密度
若把燃料紧紧密合,没有空隙,这时单位体积的燃料质量称为颗粒密度或真实密度ρ粒(Kg/m3)。
c)颗粒空隙率
燃料、床料或物料堆积时,其粒子间的空隙所占的体积份额ε堆。
ε堆=1-ρ堆/ρ粒
1-ε堆=ρ堆/ρ粒
空隙率的意义:
常常以物料在炉内的空隙率来确定其流化状态。
1)鼓泡床流化状态:
流化速度u小于3m/s,空隙率ε在0.45左右;
2)湍流床流化状态:
流化速度u=4—7m/s,空隙率ε=0.65—0.75;
3)快速床流化状态:
流化速度u大于8m/s,空隙率ε=0.75—0.95;
注意:
在锅炉冷态实验或运行中,炉内床料或物料的空隙率与堆积空隙率ε堆不同,它是床料或物料在流化状态下的空隙率,是随着流化速度大小的变化而变化的,用ε表示。
2.1.4粒平均直径、当量直径及形状系数
循环流化床锅炉燃料粒径一般为0~25mm
全部颗粒的平均直径为d平=∑xidi
相当于球形颗粒的当量直径为d当=ψd平(ψ是形状系数,不同颗粒,ψ不同)
颗粒平均直径、当量直径对于循环流化床锅炉设计、改造、调试都比较重要。
2.1.5燃料筛分
如果进入锅炉的燃料粒径粗细范围较大,即筛分较宽,就称做宽筛分;粒径粗细范围较小,就称做窄筛分。
国内目前运行的循环流化床锅炉,其燃料粒径要求一般在0.1~10mm、0.1~15mm,特殊的要求0.1~20mm,均属宽筛分。
2.1.6燃料粒比度
燃料各粒径的颗粒占总量的份额之比称作粒比度。
又称燃料颗粒特性。
按着粒比度在坐标图上作出的是一条连续的曲线。
称作颗粒特性曲线。
2.1.7流态化
当气体或液体以一定的速度流过固体颗粒层,并且气体或液体对固体颗粒产生的作用力与固体颗粒所受的其他外力相平衡,固体颗粒层会呈现出类似于液体状态的现象。
这种操作状态称为流态化。
2.1.8流化速度
是指床料或物料流化时动力流体(一次风)的速度。
也称空塔速度。
2.1.9临界流速与临界流量
临界流速是指床料开始流化时(床层由静止状态转变为流态化时)的一次风风速,此时的一次风风量叫做临界流量。
2.1.10“散式”流态化和“聚式”流态化
“聚式”流态化是指一般的气固流态化,由于气体并不均匀地流过颗粒床层,一部分气体形成气泡经床层短路逸出,颗粒则被分成群体作紊流运动,床层中的空隙率随着位置和时间的不同而变化,这种流态化称为“聚式”流态化。
2.1.11物料循环倍率
由物料分离器捕捉下来且返送回炉内的物料量与给进的燃料量之比。
即K=W/B,如某台220t/h循环流化床锅炉额定负荷设计燃煤量35t/h,物料分离器分离下来且返送回炉内的物料量为550t/h,那么该炉的循环倍率为:
K=W/B=500/35=14。
影响物料回送量的因素:
a)一次风量;b)燃料颗粒特性;c)分离器效率;d)回料系统。
2.2流化床的形成
2.2.1流化床的形成过程
注:
a—固定床空气流速低,空气穿过床料颗粒间隙由上部出去,床料高度未发生明显变化,床料未被流化。
b—流动床(散式流态化)空气流速增大,床料开始膨胀,料层高度发生变化,上部有一个确定的界面;颗粒有一些小幅度运动;颗粒聚集的倾向很小;存在很小的压力波动。
c—鼓泡床(聚式流态化)空气流速继续增加,流化速度u=1—3m/s,(u=2uc)床料内产生大量气泡,小气泡聚集成较大气泡穿过料层并破裂,气固两相扰动强烈,床面是确定的界面,周期性地有气泡破裂穿出;有一个较明显幅度的压力波动。
d—湍流床(聚式流态化)空气流速继续增大,床料内气泡消去,小气泡和颗粒群来回运动,混合更加剧烈,看不清料层界面,但床内仍存在一个密相区和稀相区。
湍流床的流化速度u=4—5m/s。
e—快速床(聚式流态化)空气流速继续增加,流化速度u=6—10m/s,床料上下浓度更趋于一致,但仍有浓度大小之分,料层界面难以直观确定;集中在靠近壁面处的颗粒团向下运动,床内中心区的气体和分散的颗粒一起向上运动;在不变的给料速率下,由于u的增加使颗粒愈加稀薄。
f—喷流床空气流速继续增大,床料将均匀地全部喷出床外。
也叫气力输送,煤粉炉类似这种状况。
说明:
a)不论是流动床,还是鼓泡床、湍流床以及快速床,均属流化床,形成各流化状态的流化速度u与床料颗粒大小、密度以及粘性等许多因素有关。
b)不是在任何情况下都能够观察到上面所列的各种形式,因为这些形式之间的过渡点,不仅取决于气固系统的特性,而且也取决于其他条件。
2.2.2几种不正常的流化状态
2.2.2.1沟流
由于料层中阻力大小不同使得大量的空气从阻力小的地方穿过料层而其他部位仍处于固定床状态,这种现象就称作沟流。
a)分类
一般分为贯穿沟流和局部沟流两种。
贯穿沟流局部沟流
b)危害
1)床料流化质量下降;
2)料层容易结焦;
3)影响炉内传热和燃烧的稳定性。
c)原因
1)一次风速太低;
2)料层太薄,或严重不均,或炉床内结焦;
3)给煤太湿,播煤风、回料风调整不合理,造成在给煤口下或回料口处形成堆集现象;
4)布风板设计不合理,风帽太少,节距太大。
2.2.2.2节涌
a)现象
料层中的气泡聚集汇合接近炉床宽度时,料层就被分成几层,一层比较稠密的床料一层稀疏床料的“空气”向上运动,当达到某一高度后崩裂,固体颗粒喷雨而下,这种现象称作节涌。
b)危害
1)燃烧不稳定;
2)在断层下部易引起结焦;
3)若床内布置有埋管,将使埋管磨损加剧。
c)原因
1)布风板、风帽设计不合理;
2)床料颗粒过粗;
3)料层过薄等。
d)说明
节涌现象易在鼓泡床与湍流床之间的流化过程中产生,因此常称这一状态为不稳定流化状态。
锅炉应尽可能避免在这一状态下运行。
2.2.2.3分层
a)现象
颗粒较大的煤快以及冷灰沉积在炉床低部,细而轻的颗粒悬浮于上部的现象。
b)危害
冷灰过多使流化质量下降;床内温度下降;影响锅炉燃烧。
2.3循环流化床锅炉炉内动力特性
2.3.1床层高度、阻力与气流速度变化的关系
2.3.1.1理想情况下关系
当气流速度开始增大时,料层阻力随着增大,而料层厚度却不再增高,颗粒基本保持不动;如果气流速度继续增大,达到临界流化速度时,气流速度再增大,料层阻力基本保持一定值,但料层高度却随气流速度的增加而增高,料层空隙率不断增大。
当气流速度增大到某一值后,床料颗粒被气流大量携带出床外,若不及时补充,随着气流速度和床料带出量的增大,料层阻力下降,最终趋近于零。
注:
A—固定床状态料层越厚,阻力越大;气流速度越大,阻力越大;气流速度增大,料层厚度不变。
B—流化床状态气流速度增大,阻力不变,料层厚度增大。
C—气力输送状态(喷流床)气流速度增大,阻力减小,料层厚度增大。
2.3.1.2实际情况下关系
实际情况采用宽筛分燃料和分段送风等原因,在锅炉运行中,炉内将沿高度形成多工况流态。
此时不能确定床层高度,影响炉内压差变化的因素也更多。
所以压差随气流速度的变化很难用一条简单的曲线表示
2.3.2炉内物料颗粒运动和浓度分布
2.3.2.1鼓泡床炉
a)颗粒运动
小气泡向上运动不断形成大气泡,气泡上浮时,由于尾迹迁移的作用,使床层下部的颗粒被携带到床层上部,促进床内混合。
b)浓度分布
物料的浓度分布只与流化速度有关;炉内有清晰料层界面,界面以下部分的物料密度很大,称做密相区;界面以上部分仅悬浮一些细小颗粒,密度很低,称做稀相区或稀疏相区。
2.3.2.2循环流化床炉(以快速流化床为例)
a)颗粒运动特点
1)单一颗粒向上运动与后续上浮的颗粒形成颗粒团或颗粒带,颗粒团不稳定极易破碎与新颗粒结成新的颗粒团。
2)物料沿壁面形成“面壁流”,浓度高,向下流动;中心物料浓度相对低,向上运动,产生“内循环”。
b)浓度分布
没有清晰料层界面,炉内物料混合比较均匀,但仍有差别:
物料在床内沿高度呈下部密、上部稀的结构;沿径向呈中心稀、外径处浓密结构。
c)浓度分布影响因素
流化速度;物料颗粒特性;循环倍率;给料和回料口高度;二次风口的位置。
2.4循环流化床锅炉煤燃烧与炉内传热
2.4.1煤的燃烧
2.4.1.1鼓泡床燃烧特点
a)颗粒粗,最大可达30mm。
b)流化速度低,一般不大于3m/s。
c)下部粗颗粒在炉内停留时间长,容易燃尽。
d)细小颗粒停留时间短,飞灰中可燃物量增大,锅炉效率下降。
e)炉内温度水平分布均匀,而高度方向是下高上低。
2.4.1.2循环流化床燃烧
2.4.1.2.1循环流化床燃烧特点
a)颗粒细,流化速度高4m/s~10m/s。
b)有物料循环系统(外循环)和炉内“面壁流”,燃料颗粒在炉内停留时间长。
c)采用清洁燃烧方法(加石灰石或其它脱硫剂去SO2,采用欠氧燃烧或分段送风抑制NOX)。
2.4.1.2.2循环流化床煤颗粒的燃烧过程
a)煤粒被加热和干燥;
b)挥发分的析出和燃烧;
c)煤粒膨胀和破裂;
d)焦碳燃烧和再次破裂及碳粒磨损。
(绝大多数表现为焦碳的燃烧)。
2.4.1.2.3劣质燃料的燃烧
a)劣质燃料
指高水分、高灰分、高硫分、低发热量、低灰熔点的燃料。
如泥煤、油页岩、炉渣、木屑、洗煤厂的煤泥、洗矸、采煤厂的煤矸石、垃圾处理厂的垃圾等,也包括难点燃和燃尽的低挥发分的无烟煤、石油焦和焦碳等。
b)可以采用劣质燃料的原因
1)循环流化床炉内蓄热量大,有足够的热量加热新燃料而不会导致炉内的温度有较大的变化。
2)新燃料在炉内停留时间长,远大于其燃尽所必需的时间。
2.4.2炉内传热
2.4.2.1鼓泡床与埋管的热交换
鼓泡床与埋管受热面之间的热量传递主要通过三个途径:
a)颗粒对流放热;通常颗粒粒径比较细(0.04—1mm)时,颗粒对流放热是传热主要方式。
b)颗粒隙间气体对流放热;粒径比较大时(大于0.8mm)直至数毫米时,隙间气体对流放热占主要份额。
c)床层辐射放热。
床温越高,颗粒越大,辐射作用越强。
2.4.2.2循环流化床炉内热交换
2.4.2.2.1传热途径
传热途径分物料对受热面的固体对流;固体辐射;气体辐射三个途径。
2.4.2.2.2运行中各参数调整对传热系数的影响
a)床温的影响
床温升高,传热系数增大。
b)物料浓度的影响
运行中床温维持一定的情况下,物料浓度是最主要的因素。
c)循环倍率的影响
循环倍率越大,炉内物料浓度越大,传热系数越大。
d)流化速度的影响
在一定的物料浓度下,流化速度对传热系数的影响很小—锅炉运行中一般是增加一次风量和给料量同时进行。
e)颗粒尺寸的影响
其他条件相同时,颗粒尺寸小时传热系数大,而颗粒尺寸大时传热系数小,这种实验结果对较短的受热面影响明显(与鼓泡床对竖式布置的埋管影响基本一致),对较长的受热面影响不明显。
f)受热面长度的影响
实验表明:
换热面长度对传热系数有明显的影响,平均传热系数随长度的增加而减小,但在换热面长度超过0.5—1m后,影响不明显。
所以,在实际的循环流化床锅炉中换热面长度将不对传热系数产生实质性的影响。
3循环流化床锅炉主要设备及作用
3.1燃烧设备
循环流化床锅炉燃烧设备主要由燃烧室、点火装置、一次风室、布风板和风帽、给煤机等组成另外还包括物料循环系统和一、二次风系统。
3.1.1燃烧室
3.1.1.1结构形式
燃烧室结构可分为:
圆型炉膛、方型炉膛、下圆上方型炉膛;其特点为圆型炉膛或下圆上方型炉膛的圆形部分一般不设水冷壁受热面,完全由耐火砖砌成,内衬耐热防腐耐火材料。
对防磨和压火保温起到一定的作用,但启动时间长,上下结合处不易密封。
而方形炉膛四周一般采用膜式水冷壁,密封好,锅炉体积小,启动速度快,但水冷壁磨损大,水冷壁内侧需衬耐磨耐火材料。
3.1.1.2大型循环流化床锅炉三种不同的炉膛设计方案
3.1.2布风板与风帽
3.1.2.1布风板
a)布风板
流化床锅炉燃烧市下部的炉篦被称做布风板。
b)布风板的作用
1)支承炉内物料;
2)合理分配一次风,使通过布风板及风帽的一次风流化物料,使之达到良好的流化状态。
c)布风板的型式
1)非水冷式布风板
一定厚度的钢板开孔,又叫花板,上设保温层以防花板变形。
2)水冷式布风板
采用拉稀膜式水冷壁形式,在管与管之间的鳍片上开孔布置风帽。
水冷布风板、水冷风箱和炉膛水冷壁构成了一个整体,消除了锅炉运行时热膨胀不均匀的问题。
采用床下点火时必须采用水冷风室和水冷布风板。
d)布风板的结构型式
ab一般为非水冷式;cd一般为水冷式
3.1.2.2风帽
a)作用
使空气第二次分流与导向(第一次在风箱),以足够的速度进入流化床;使空气与固体颗粒能良好的混合;建立良好流化状态。
b)结构
主要有三类:
小孔径风帽、较大孔径风帽、导向风帽。
1)小孔径风帽有多个出气口,阻力大,气流速度大,刚度小,容易阻塞。
2)大孔径风帽一般为一个出气口,阻力小,气流刚度大,不易阻塞。
3)导向风帽能将沉积在床底部的大颗粒灰渣及杂物有效地沿着规定的方向吹直排渣口排出。
3.1.3点火方式与点火装置(启动燃烧器)
3.1.3.1点火方式(常用流态化下点火方式)
固定床点火
流态化点火(又分为上点火、下点火)
3.1.3.2启动燃烧器
布置方式:
床上布置(上点火)、布风板上布置(上点火)、一次风管道内布置(下点火)
a)启动燃烧器床上布置
向下倾斜的启动油燃烧器
b)启动燃烧器布风板上布置
c)启动燃烧器一次风管道内布置
管道燃烧器先将一次风加热至700~800°C的高温,高温一次风进入水冷风箱,再通过布风板将惰性床料流化,并在流态化的条件下对床料进行均匀加热。
其特点为对床料的加热均匀、迅速;炉膛的散热损失小;缩短启动时间;节省启动用燃料。
据估算,一台300MW的循环流化床锅炉,每冷态启动一次,管道燃烧器启动要比床上布置燃烧器节省启动燃料60%。
因此,一次风管道内启动燃烧器现在得到较普遍的采用。
3.1.4给煤机与给煤方式
3.1.4.1给煤机
3.1.4.1.1给煤机布置位置
有前墙布置、前后墙布置(对大容量锅炉)、布置在分离器下热床料返回炉膛的返料密封器上。
也有采用气力输送在密相区给料的。
3.1.4.1.2给煤机结构型式
螺旋给煤机(早期小容量锅炉采用,目前很少用);埋刮板给煤机;皮带给煤机(电站锅炉基本不用);重力给煤机;抛煤机;气力给煤系统;用泥浆泵输送煤泥浆的给料系统和空气吹扫给煤机等。
3.1.4.1.3给料系统举例
3.1.4.2给煤方式
a)正压给煤:
给煤口低,布置有播煤风。