机械设计制造及其自动化专业课程设计.docx
《机械设计制造及其自动化专业课程设计.docx》由会员分享,可在线阅读,更多相关《机械设计制造及其自动化专业课程设计.docx(20页珍藏版)》请在冰豆网上搜索。
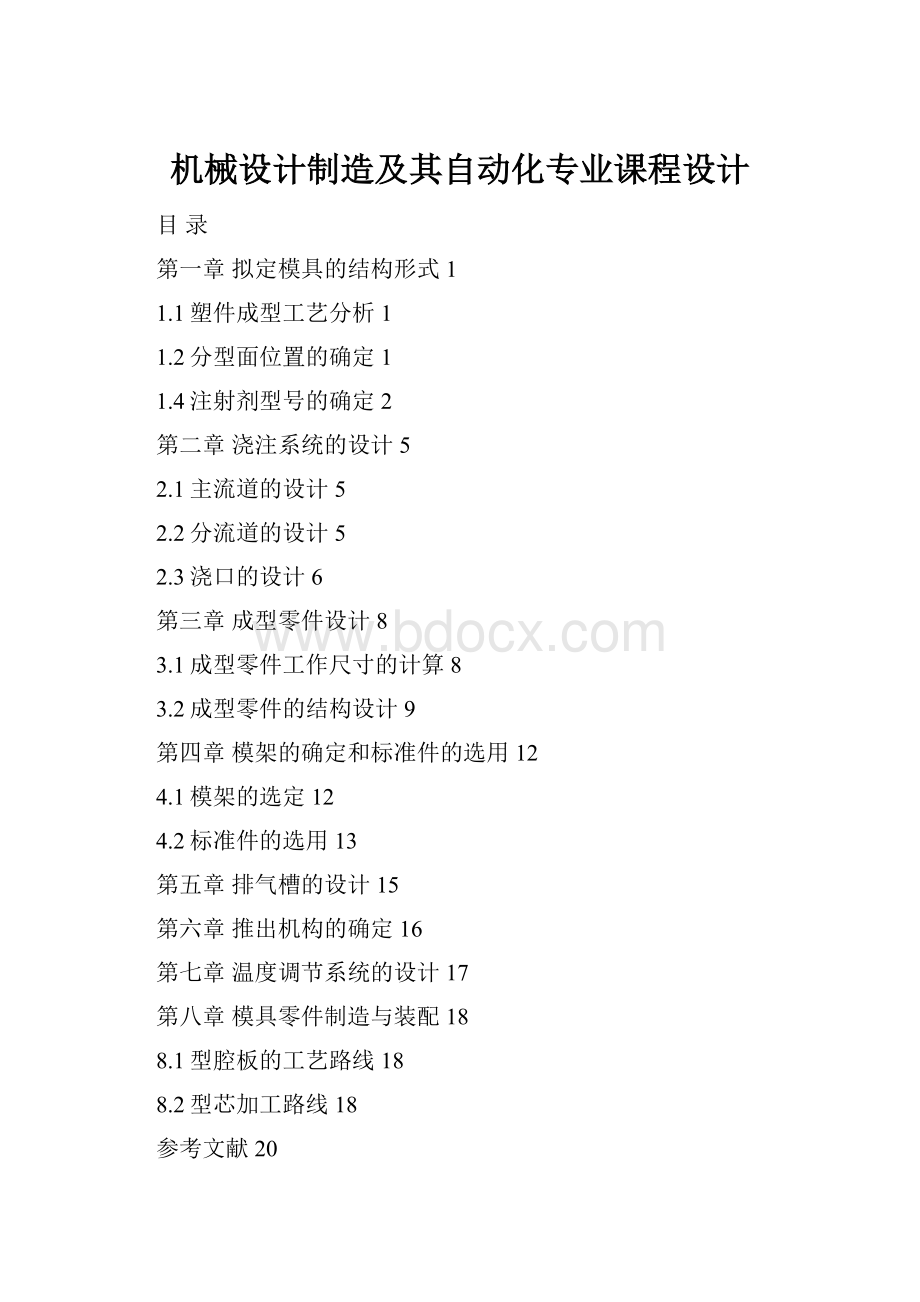
机械设计制造及其自动化专业课程设计
目录
第一章拟定模具的结构形式1
1.1塑件成型工艺分析1
1.2分型面位置的确定1
1.4注射剂型号的确定2
第二章浇注系统的设计5
2.1主流道的设计5
2.2分流道的设计5
2.3浇口的设计6
第三章成型零件设计8
3.1成型零件工作尺寸的计算8
3.2成型零件的结构设计9
第四章模架的确定和标准件的选用12
4.1模架的选定12
4.2标准件的选用13
第五章排气槽的设计15
第六章推出机构的确定16
第七章温度调节系统的设计17
第八章模具零件制造与装配18
8.1型腔板的工艺路线18
8.2型芯加工路线18
参考文献20
第一章拟定模具的结构形式
1.1塑件成型工艺分析
聚乙烯(PP)成型特性;
1.结晶性料,吸湿性小可能发生熔体破裂,长期与热金属接触易发生分解;
2.流动性极好溢边值在0.03左右;
3.冷却速度快,浇注系统及冷却系统散热应适度;
4.成型收缩范围大收缩率大,易发生缩孔、凹痕、变形、,取向性强;
5.注意控制成型温度,料温低取向性明显,尤其低压高温时更明显。
模具温度低于50度以下塑件无光泽,易产生熔接痕、流痕;90度以上时易发生翘曲、变形;
6.塑件应壁厚均匀,避免缺口、尖角,以防止应力集中。
综合PP的性能分析:
1件(PP)的成型特性和使用性能分析:
吸湿性小,流动性极好,溢边值0.03mm左右,PP综合性能较好,冲击韧度,力学强度较高,尺寸稳定,耐化学性,电性能良好,易于成型和机械加工。
2件(PP)的结构分析:
该塑件结构较简单,制造精度较高,大批量,没有特殊要求,可用注射成型加工。
1.2分型面位置的确定(如下图所示)
1.3型腔数量的确定
对于形状较简单的,又是大批量生产的,若采用一模一腔的结构,其生产效率不是很高,同时生产周期也会增加,因此要采用一模多腔注射成型,但一般不超过4个腔,综合塑件的质量,几何形状,精度,批量大小以及经济效益来看,可以采用一模4腔进行生产加工。
1.4注射剂型号的确定
注射量的计算:
通过计算得到塑件的体积V=15.838CM³,塑件密度为0.9g/CM³
所以单个塑件质量m1=р.v=14.22g,
⑴按预选型腔数来选择注射机
1模具所需塑料熔体注射量
m=nm1+m2
式中m——一副模具所需塑料的质量或体积(g或cm3);
n——初步选定的型腔数量;
m1——单个塑件的质量或体积(g或cm3);
m2——浇注系统得质量或体积(g或cm3);
在学校做设计时以0.6nm1来估算,即
m=1.6nm1
由计算得m1=9.955cm3,则总的m=1.6nm1=1.6*4*14.22=91.008g
2塑件和流道凝料(包括浇口)在分型面上的投影面积及所需锁模力
A=nA1+A2;Fm=(nA1+A2)P型
式中A——塑件及流道凝料在分型面上的投影面积(mm2);
A1——单个塑件在分型面上的投影面积(mm2);
A2——流道凝料(包括浇口)在分型面上的投影面积(mm2);
Fm——模具所需的锁模力(N);
P型——塑料熔体对型腔的平均压力(Mpa);
根据多型腔模具的统计分析,大致是每个塑件在分型面上的投影面积A1的0.2~0.5倍,因此可用0.35nA1来估算。
成型时塑料熔体对型腔的平均压力,其大小一般是注射压力的30%~65%。
部分塑料注射压力p0,见《塑料模具设计指导》第7页,设计中常按表2-2中型腔压力进行估算。
由计算得A1=π(37.5/2)²=1104mm2,
查表取P型=25Mpa,Fm=1.35nA1P型=1.35*4*1104*25N=149.04KN(塑模具设计指导P7)
3选择注射机型号
根据上面计算得到的m和Fm值来选择一种注射机,注射机的最大注射量(额定注射量G)和额定锁模力F应满足
G≥m\a
式中a——注射系数,无定型塑料取0.85,结晶型塑料取0.75。
由m=91.008cm3,a取0.85
则91.0088÷0.75=121.3g,
F>Fm
Fm=149.04KN.
根据以上计算,查《塑料模具设计指导》第188页预选用SZ-125/630型的卧式注射机。
其主要技术参数如下:
理论注射溶剂/cm³
140
移模行程/mm
270
注射压力/MPa
126
最大模具厚度/mm
300
注射速率/g/s
110
最小模具厚度/mm
150
塑化能力/g/s
16.8
模具定位孔直径/mm
125
锁模力/KN
530
喷嘴球半径/mm
15
拉杆内间距/mm
370×320
喷嘴孔直径/mm
3
⑵注射机有关参数的较核
1型腔数量的校核
n≤(KMt/3600-m2)/m1=(0.8×16.8×3600×30/3600-0.6×4×14.22)/14.22=25.95>>4
故型腔数量校核合格
2注射剂压力的校核
该项是校核所选注射机的额定压力pe能否满足塑件成型时所需要的注射力P0,塑件成型时需要的压力一般由塑料流动性,塑件结构和壁厚以及浇注系统类型等因素所决定,生产实践中其p0值一般为70Mpa~150Mpa。
设计中要求
k,一般取1.25~1.4
pe≥k,p0,取k,=1.3,p0取90Mpa
则1.3X90=117<126MPa
注射机的注射压力的校核满足
3锁模力的校核
锁模力是指注射机的
F≥k0AP型
式中P型——型腔的平均压力,选用参见表2-2;
k0——锁模力安全系数,一般取k0=1.1~1.2。
P型取25Mpa,k0取1.2
故F≥k0AP型=1.2×149.04=178.85<530
注射机的锁模力的校核满足要求
4开模行程校核与推出机构的校核
㈠开模行程校核
H=H1+H2+a+(5~10)mm≤S
式中H1——推出距离(mm);
H2——包括浇注系统凝料在内的塑件高度(mm);
a——取出浇注系统凝料必需的长度(mm)。
H1=44mm,H2=88mm,a=52mm,
则总的结果为190mm<270mm,
注射机的开模行程校核满足要求。
第二章浇注系统的设计
2.1主流道的设计
主流道小端尺寸d=注射机喷嘴尺寸+(0.5~1)mm。
d=3.5+0.5=4
主流道长度L≤60mm。
主流道锥角a一般在20~40范围内选取,对黏度大的塑料,a可取30~60.在本次设计中a取30。
长度L=52mm。
主流道的结构形式如下图所示
2.2分流道的设计
①对于半圆形截面分流道,分流道的直径在《塑料成型模具与设备》第121页表4-2查取。
得:
D=6mm
②分流道的长度
分流道要尽可能的短,且少弯折,便于注射成型过程中最经济地使用原料和降低注塑机的能耗,减少压力损失和热量损失。
分流道的长度一般在8~30mm之间,一般根据型腔布置适当加长或缩短,但最短不宜小于8mm。
分流道的长度取94mm
③分流道与浇口的连接形式
采用圆弧过渡有利于熔体的流动及填充。
④分流道的布置形式
采用平横式流道系统可见如下图
2.3浇口的设计
1浇口的形式确定
浇口的设计与塑件的形状,截面尺寸,模具结构,注射工艺参数及塑料性能等因素有关。
浇口的截面尺寸要小,长度要短,这样才能增大料流速度,快速冷却封闭。
便于与塑件分离或切除,且浇口的痕迹不明显。
采用点浇口,开模时浇口可以自动拉断,利于自动化操作,浇口除去后残留痕迹小。
2浇口尺寸确定
(A)、浇口厚度h
通常取塑件浇口处的0.5~1.5mm。
h=0.75mm
(B)、浇口宽度b
b=2mm
(C)、浇口长度L
通常取L=0.5~2mm。
取L=1mm
浇口的形式如下图所示:
第三章成型零件设计
3.1成型零件工作尺寸的计算
⑴凹模和型芯径向尺寸计算
1凹模的径向尺寸计算
PP的收缩率为1.0%~3.0%,平均收缩率为S=(1.0%+3.0%)=2.0%=0.02
在已知的给定条件下的平均收缩率S,塑件径向尺寸(Ls)0-△,设凹模径向尺寸为:
(Lm)+&z0,计算公式如下:
Lm=(Ls+LsS%-x△)+&z0
式中x——修正系数,一般值在½~~¾.
对于中.小型塑件x=3/4
△——塑件公差值。
&z——凹模的制造公差,取&z=△/3.
Lm1=(Ls+LsS-3/4△)+&z0
=(15+15*2.0%-3/4x0.38)+0.38/30
=φ15.02+0.130mm
Lm2=(Ls+LsS-3/4△)+&z0
=(37.5+37.5*2.0%-3/4x0.56)+0.56/30
=37.83+0.190mm
Lm3=(Ls+LsS-3/4△)+&z0
=(30+30*2.0%-3/4x0.50)+0.50/30
=30.23+0.170mm
2型芯的径向尺寸计算
已知在给定条件下的平均收缩率S,塑件径向尺寸(ls)+△0,设型芯径向尺寸为
(lm)0-&z,计算公式如下:
lm=(ls+lsS+x△)0-&z
式中x——修正系数,一般值在½~~¾.
对于中.小型塑件x=3/4
△——塑件公差值。
&z——凹模的制造公差,取&z=△/3.
lm1=(ls+lsS+3/4△)0-&z
=(31.5+31.5*2.0%+3/4*0.56)0-0.56/3=32.550-0.19mm
lm2=(24+24*2.0%+3/4*0.50)0-0.50/3=24.860-0.17mm
Lm3=(9+9*2.0%+3/4*0.28)0-0.28/3=9.390-0.09mm
⑵凹模深度与型芯高度尺寸计算
1凹模深度尺寸计算
已知在给定条件下的平均收缩率S,塑件高度尺寸(Hs)0-△,设凹模深度尺寸为:
(Hm1)+&z0,则计算公式如下:
Hm=(Hs+HsS-x`△)+&z0
式中x`——修正系数,一般值在1/2~2/3.
对于中.小型塑件x`=2/3
△——塑件公差值。
&z——凹模的制造公差,取&z=△/3.
Hm1=(36+36*2.0%-2/3*0.56)+0.560=35.9+0.190mm
Hm2=(45+45*2.0%-2/3*0.64)+0.64/30=45.47+0.210mm
2型芯高度尺寸计算:
已知在给定条件下的平均收缩率S,塑件孔的深度尺寸为(hs)+△0,设塑件高度尺寸为(hm)0-&z,则计算公式如下:
hm=(hs+hsS+x`△)0-&z
式中x`——修正系数,一般值在1/2~~2/3.
对于中.小型塑件x`=2/3
△——塑件公差值。
&z——凹模的制造公差,取&z=△/3.
hm=(hs+hsS+2/3△)0-&z
=(33+33*2.0%+2/3*0.56)0-0.56/3=34.030-0.19mm
3.2成型零件的结构设计
3型芯的设计如下图所示
对于凸模的径向尺寸的公差可以采用配作加工法,与凹模进行配合加工保证双面间隙小于塑料的溢边值。
4凹模的设计如下图
第四章模架的确定和标准件的选用
4.1模架的选定
塑件投影宽度B′=88mm,塑件投影长度L′=108mm
由公式B′≤B-10得B≥98,查标准模(塑料模具设计指导书表7-1)得可选4号以上模架均可,5号模架较为适合,其复位杆直径为d=12.5mm.
由L′≤lt-d-30得lt≥150.5.所以lt宜选206。
故选B×L=200×250系列模架,其基本尺寸分别为:
1导柱:
ø20,间距156X210
2复位杆:
ø12.5,间距80mm×206mm
3螺钉:
8×M12,间距160mm×146mm
4定模座板:
L×B×H=250mm×250mm×25mm
5定模板:
L×B×H=200mm×250mm×20mm
6动模板:
L×B×H=200mm×250mm×40mm
7型芯固定板:
L×B×H=200mm×250mm×32mm
8垫块:
L×B×H=40mm×250mm×80mm
9推杆固定板:
L×B×H=118mm×250mm×16mm
10推板:
L×B×H=118mm×250mm×20mm
11动模座板L×B×H=250mm×250mm×25mm
模架的草图如下:
4.2标准件的选用
标准件包括通用标准件及模具专用标准件两大类。
通用标准件如紧固件等,模具专用标准件如定位圈,浇口套,推管,推杆,导柱,导套等。
在设计模具时,应尽可能选用标准模架和标准件,因为标准件有很大一部分随时可在市场上买到,这对缩短制造周期,减低制造成本是极其有利的。
模架尺寸确定之后,对模架有关零件要进行必要的强度或刚度计算,以校核所选模架是否适当。
①衬套的选用如下图
②直导柱的选用如下图
5复位杆的选用如下图
6拉料杆的选用如下图
第五章排气槽的设计
该套模具是属于小型模具,可以利用型芯、推杆的配合间隙和分型面处的间隙进行排气,在型腔的设计中采用模具间隙比塑料上的溢边值的小的原理来实现排气,因此本次设计不单独开设排气槽。
第六章推出机构的确定
根据塑件的形状特点设计推杆的大小,并且为了能够平稳的将工件推出,应设计足够数量的推杆。
在此模具中应设计直径为6mm的推杆,每个产品4个推杆,共十六个。
推杆的形状如下图所示:
第七章温度调节系统的设计
由于该套模具的模温要求在80度以下,又是小型模具,所以无需设置加热装置。
对于聚丙烯(PP)这样黏度低、流动性好的塑料,因为成型工艺要求模温都不太高,所以常用常温水对模具进行冷却。
第八章模具零件制造与装配
8.1型腔板的工艺路线
工序号
工序名称
工序内容
1
备料
将毛坯锻成平行六面体,尺寸为201mm×251mm×41mm
2
热处理
退火
3
铣平面
水铣各平面,留磨削余量0.6mm,侧面留磨削余量0.5mm
4
磨平面
磨上下平面,留磨削余量0.1-0.3mm,磨相邻两侧面保证垂直
5
钳工划线
划出螺钉孔,导套孔及复位杆的中心线
6
螺钉孔粗加工
在钻床上钻出4个Φ11mm深度为27mm的锥孔
7
型腔粗加工
铣出长宽为36mm×39mm深度为35mm的长方体沉槽,底部铣出33×36同时打通型腔的长方体型芯孔
8
热处理
退火,回火后保证锻件硬度为60-64HRC
11
螺钉孔精加工
扩孔至Φ11.2mm,再绞孔至12mm
12
型腔精加工
精铣型腔内部,达到型腔所要求的大致尺寸,留0.5mm的精加工加工余量
13
研磨型腔
钳工精磨型腔内部结构达到尺寸精度要求
14
检验
根据要求对通孔及沉孔,沉槽进行仔细检验
8.2型芯加工路线
工序号
工序名称
工序内容
1
备料
将毛坯锻成下方是长方体、上方高度为10mm、Φ10的圆柱体,长方体周边尺寸为45mm×38mm,且整个型芯坯料高度为60mm.
2
热处理
退火
3
铣平面
在铣床上铣底平面,平面留磨削余量0.6mm
4
型芯孔粗加工
钻4个φ5.5的孔
6
磨侧面与顶面
留磨削余量0.1-0.3mm
7
钳工划线
划出各定位孔及沉孔,沉孔的中心线
9
热处理
淬火,回火后保证锻件硬度为60-64HRC
11
型芯孔精加工
精铰φ5.5的孔至φ6
13
精磨平面
在磨床上磨底面、侧面至要求尺寸
14
检验
根据图纸要求仔细检查孔的尺寸和精度是否达标
参考文献
[1]夏江梅.《塑料成型模具与设备》.北京:
机械工业出版社,2005
[2]伍先明.《塑料模具设计指导》.北京:
国防工业出版社,2005
[3]阎亚林.《塑料模具图册》.北京:
高等教育出版社,2005
[4]陈于萍.《互换性与测量技术》.北京:
高等教育出版社,2005
[5]闻百桥.《机械制图》.北京:
高等教育出版社,2005
[6]吴兆祥.《模具材料及表面处理》.北京:
机械工业出版社,2005
[7]肖祥芷.《中国模具设计大典》.江西:
江西科学技术出版社,2005