烧结培训课件动力.docx
《烧结培训课件动力.docx》由会员分享,可在线阅读,更多相关《烧结培训课件动力.docx(29页珍藏版)》请在冰豆网上搜索。
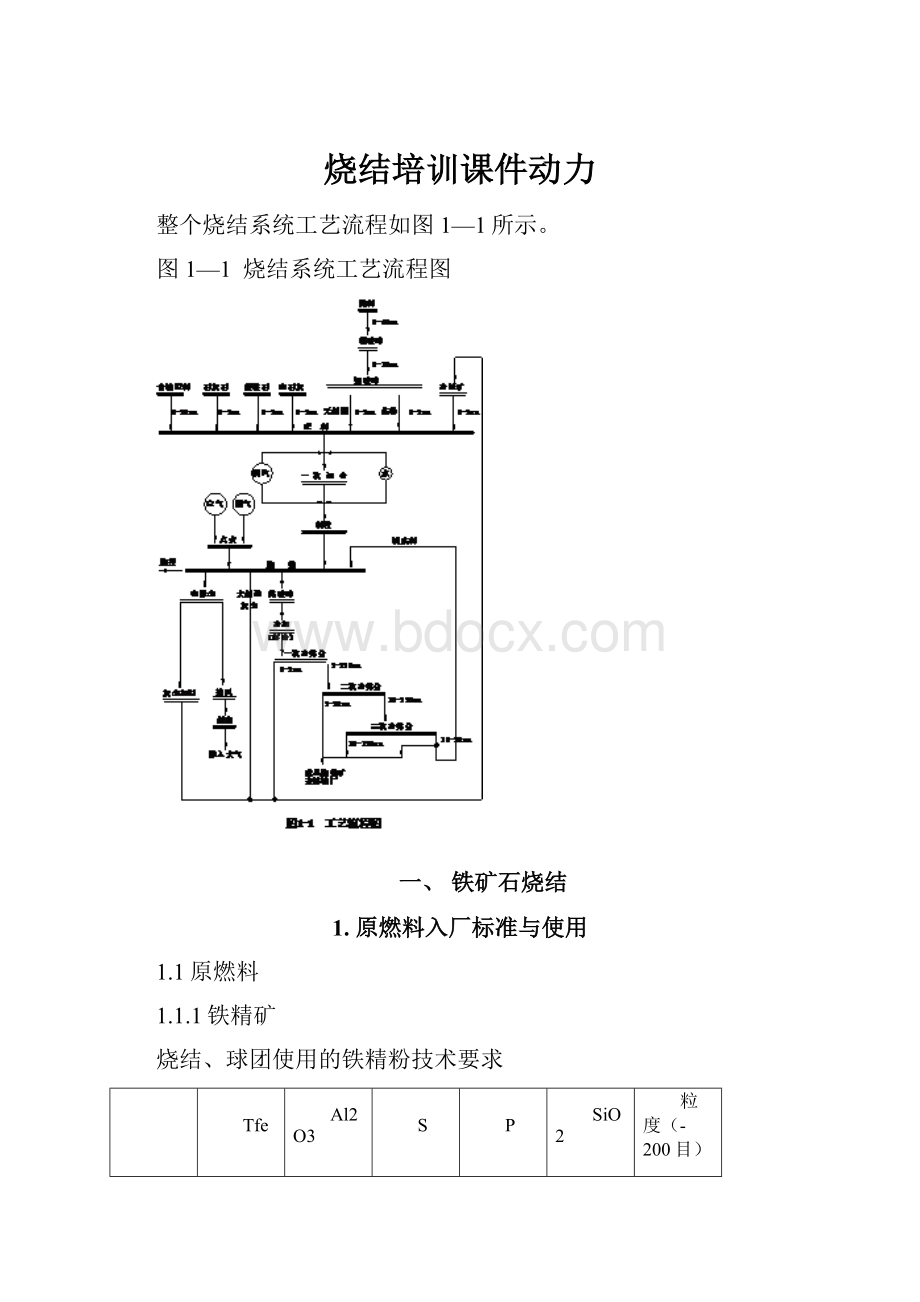
烧结培训课件动力
整个烧结系统工艺流程如图1—1所示。
图1—1烧结系统工艺流程图
一、铁矿石烧结
1.原燃料入厂标准与使用
1.1原燃料
1.1.1铁精矿
烧结、球团使用的铁精粉技术要求
Tfe
Al2O3
S
P
SiO2
粒度(-200目)
用于球团
≥66
<2
<0.05
<0.1
-
>78
用于烧结
≥66
<2
<0.05
<0.1
<6
-
精矿粉是天然矿石经过破碎,磨碎,选矿等加工处理成的矿粉.烧结用精矿粉粒度-200目≥55%;竖炉用精矿粉粒度-200目≥65%。
铁矿粉分类
铁矿物按照不同存在形态,分为磁铁矿,赤铁矿,褐铁矿,菱铁矿四大类.
磁铁矿的主要存在形式是Fe3O4,比密度为4.9-5.2,硬度为5.5-6.5,有金属光泽,具有磁性。
其理论含铁量为72.4%。
磁铁矿晶体为八面体,组织结构致密坚硬,一般成块状和粒状,表面颜色由钢灰色到黑色,条痕均为黑色,俗称青矿。
赤铁矿的矿物成分是不含结晶水的三氧化二铁(Fe2O3),密度为4.8-5.3,硬度不一,结晶完整的赤铁矿硬度为5.5-6,理论含铁量为70%。
赤铁矿的条痕为红色。
褐铁矿是一种含结晶水的三氧化二铁,可用mFe2O3.nH2O来表示。
褐铁矿的条痕为黄褐色.
菱铁矿是一种铁的碳酸盐,化学式FeCO3,理论含铁量为48.2%。
在碳酸铁的矿床中,碳酸盐的一部分铁往往与其它金属组成各种复盐。
1.1.2氧化铁皮
烧结使用的氧化铁皮技术要求
项目
TFe(%)
水份(%)
粒度(mm)
其它
指标
≥69
≤5
≤20
不能含有耐火砖、泥土、煤渣等杂质
1.1.3熔剂
烧结使用的熔剂技术要求
名称
CaO+MgO%
CaO
SiO2
MgO%
P%
S%
烧损%
粒度
mm
粒度
范围%
石灰石粉
-
≥53.0
≤2
≤2
≤0.05
≤0.035
≤45
0-3
≮10
菱镁石粉
-
≤2.5
≤5.5
≥41
0-3
≮10
生石灰
-
≥82
≤2.8
≤0.03
≤0.025
0-3
≮10
烧结用生石灰粒度≤3mm粒级含量不低于90%。
烧结用生石灰中的熔瘤、焦炭等杂质应捡出,且新鲜、干燥、不得混入外来杂物。
1.1.4燃料
名称
固定碳
灰份
挥发份
S
水分
粒度
%
碎焦
≥83
<15
≤2.5
≤1.0
<10
0-25mm
焦粉
≥83
<15
≤2.5
≤1.0
<10
0-25mm
烧结使用的燃料技术要求
2.燃料加工
燃料先入对辊破碎机粗破碎。
经过对辊破碎以后的燃料产品粒度<10mm,再入四辊破碎机细碎。
经过四辊破碎后的燃料粒度,应能满足烧结工艺要求。
焦粉粒度≤3mm的部分>80%,无烟煤粒度≤3mm的部分>75%,正常情况下禁止煤焦混用。
如果焦煤混用要提前报告作业规划室工艺工程师经批准后实施,视焦煤粉混合比例和烧结原料结构确定粒度合格率,原则上破碎后≤3mm的粒级≥70%。
燃料进入四辊和对辊破碎前,先由除铁器除铁,各台除铁器必须保持正常使用和清洁。
选用二台φ1200×1000对辊破碎机与二台φ1200×1000四辊破碎机组成的破碎系统,其中粗细破碎设备一工一备。
对辊
序号
名称
参数
单位
备注
1
额定处理量
16~65
t/h
2
最大给料尺寸
40
mm
3
产品粒度:
<12
mm
4
辊缝调整范围
2~12
mm
弹簧装置调整
5
辊子直径
1200
mm
6
辊子长度
1000
mm
7
辊子数量
2
套
8
辊子间隙
12
mm
四辊
破碎物料
焦碳、无烟煤
设备规格
辊子直径
1200㎜
辊子宽度
1000㎜
设备参数
数值
单位
生产率
入料10~0㎜,上辊间隙
8㎜,下辊间隙3㎜
60~65
吨/时
入料20~0㎜,上辊间隙
8㎜,下辊间隙3㎜
35~55
辊间隙调节方式
油缸液压调节
润滑方式
手动干油集中润滑
1.1.5原料的接受和贮存
外返矿由原料场送到配料室1#矿槽储位。
混匀矿由原料场送到配料室2#~7#矿槽储位。
熔剂(不算生石灰)由原料场送到配料室8#~9#矿槽储位。
固体燃料由燃料受矿槽送到配料室10#~11#原煤矿槽储位。
生石灰由运输部送到配料室12#~14#矿槽储位。
除烧结内返矿外的所有原燃料在使用之前,必须有化学成份。
原料场根据烧结中控反馈的烧结混匀矿和熔剂配料矿槽、燃料矿槽、外返矿配料矿槽的料位信息,及时向烧结供料。
白灰厂根据烧结中控反馈的生石灰配料矿槽的料位信息,及时向烧结供料。
熔剂(不包括生石灰)分为石灰石和菱镁石,不得互相混料,必须按照指定的储位储存。
确因工作需要,某个储位需更换另一品种的熔剂时,必须将该储位的熔剂倒空以后方可进另一种熔剂。
生石灰运送方式,采用汽车罐车用压缩空气送至配料室生石灰配料槽。
所用石灰石和菱镁石(粒度为3~0mm)在原料场贮存,由胶带机运至配料室石灰石配料槽。
固体燃料分为焦粉和无烟煤,
烧结用固体燃料为焦炉筛下焦(粒度为15~0mm)、高炉筛下焦(粒度为15~0mm)和无烟煤(粒度为40~0mm)。
因工作需要,储位需要倒换,必须将该储位的固体燃料倒空以后方可进另一种料。
固体燃料采用汽车运输,直接卸料至燃料受矿槽,由胶带机运至燃料破碎室。
根据生产作业计划、矿槽库存量,及时组织进料工作。
中控操作人员应密切监视CRT画面显示的矿槽库存量,使其槽位在合理范围,并提前联系料场或管控中心作好上料准备,避免出现空仓待料现象。
进入烧结厂的各种原燃料必须附有原料的名称、代码、料号、理化性能、料堆号、重量,正常生产时可在公司的ERP计算机通讯网上通讯,或用电话联系。
3.配料
所有配料计算和配比调整计算要求用计算机计算。
正常生产时,在计算机画面上进行配料系统的启停、调整、监视等操作。
发生配料矿槽棚料、卡料等异常情况,应启用相同品种的其他矿槽后,再处理棚料、卡料等异常情况。
根据公司用料计划、烧结矿技术质量标准、原燃料主要化学成分、混合料技术指标确定配料比。
配比由厂作业规划室下达,需微调时,必须由当班工长进行计算。
考虑到取制样时间的滞后,前后相邻两次配比调整时间原则上应至少间隔2小时。
烧结矿成分波动较大时、应检查下料量、校对计量秤、重新验算配料比、及时调整操作。
配料矿槽工艺参数及槽位正常时的管理基准
名称
格数
有效容积(m3)
堆积
密度
(t/m3)
贮存量(t)
用量
(t/h)
贮存时间
(h)
一格
全部
一格
全部
含铁原料
6
375
2250
2.2
787.5
4725
445
10.62
石灰石
1
375
375
1.6
600
600
34.1
17.6
返矿灰尘
1
535
535
1.7
909.5
909.5
101
9.0
生石灰
3
597
1791
0.8
478
1434
46.98
30.52
菱镁石
1
375
375
1.6
600
600
27.89
21.5
燃料
2
375
750
0.8
300
600
28.0
21.43
原料种类
混匀铁料
燃料
冷返矿
生石灰
石灰石
菱镁石
灰尘
配料设备种类
电子配料秤
电子配料秤
电子配料秤
密封式电子配料秤
电子配料秤
电子配料秤
数量
6
4
2
3
2
2
能力
正常
170
18
170
40
40
34
t/h
最大
350
45
350
80
70
46
最小
100
8
80
20
20
20
工作状态
3工3备
2工2备
1工1备
2工1备
1工1备
1工1备
圆盘
返物料名称:
含铁混匀矿
给料粒度:
<20mm
物料含水:
正常<8%,最大<12%
圆盘直径:
φ3200mm
额定处理能力:
Q=50~350t/h
圆盘转速:
1~4.2r/min
4.矿及辅料
4.1返矿
参与配料的返矿有外返矿和内返矿。
外返矿为高炉块矿矿槽、球团矿矿槽、烧结矿矿槽的筛下物。
内返矿为烧结成品冷筛的筛下物,机头、机尾、整粒电除尘器的排灰,大烟道的排料,都是烧结过程内部循环的返矿。
烧好内返矿是稳定烧结生产的有效措施,好的内返矿外观呈青黑色、含粉少,未烧结的夹生料少,大于5mm的颗粒少,在胶带机转运过程中基本不扬尘。
4.2辅料
厂内除尘灰做为烧结用辅料分三个系统向烧结供料。
由机头电除尘、机尾电除尘和整粒布袋除尘系统捕集的含铁除尘灰由皮带送到烧结区的冷返矿槽,配料布袋除尘系统捕集的含铁除尘直接按规定时间加在配料大皮带上,燃料布袋除尘系统捕集的含碳除尘直接落在燃料皮带上,进入燃料矿槽。
高炉瓦斯灰单独参加配比,并根据瓦斯灰含碳量适当减少燃料配比。
氧化铁皮及其它粗颗粒除尘灰按产生量以一定比例进行混合,混匀造堆后参与配料。
5.混合与制粒
5.1加水控制
5.1.1正常生产时,混合料水份控制在目标值±0.2%以内。
混合料水份目标值与配料总量、返矿配比、生石灰配比、气候、物料粒度、矿粉亲水性、熔剂品种变化等因素有关。
混合料目标值由厂部制定。
5.1.2杜绝跑稀料或跑干料。
5.1.3雨水等特殊季节,当配合料自然水分超过混合料水分目标值时,可不加水,必要时可以临时增加返矿配比以求混合料自然水分低于目标值。
5.1.4一、二混加水量分别为总加水量的80%、20%。
5.2预热蒸汽控制
先在混合机、制粒机进料端处混合料仓和制粒机内用蒸汽将混合料预热到45~65度,预热混合料时蒸汽冷凝变成的水参加混合机造球,不会引起混合料水分超出允许范围,由于混合料与蒸汽的传热方式为对流传热,热效率高达55%以上;混合料运到烧结机上矿槽后,在矿槽周边及中间加一些蒸汽喷嘴用蒸汽进一步将混合料温度预热到65度以上,满足烧结工艺对混合料温度的要求。
混合机和制粒机的设备参数
序号
名称
参数
单位
一次
二次
1
给料方式
胶带机改向轮直插筒体内
胶带机改向轮直插筒体内
2
传动方式
右式(顺料流方向看)
右式(顺料流方向看)
3
规格
Ф3800×14000
Ф4000×18000
mm
4
正常处理量
850
420
t/h
5
最大处理量
1010
505
t/h
6
物料堆比重
1.7±0.1
1.7±0.1
t/m3
7
物料安息角
35
35
度
8
混合时间
2.02
3.47
min
9
筒体直径
3.8
4.0
m
10
筒体长度
14
18
m
11
转速
6.5
8.5
rpm
12
安装角度
2.7
1.5
度
13
填充率
11.79-14.88
7.24-8.72
%
6.布料
6.1混合料布料
混合料布料的基本要求是沿着烧结机长度和宽度方向均匀一致,高度方向合理偏析——由上向下粒度逐渐增大、含炭量逐渐减少,整个料层有一定的松散性。
6.2铺底料布料
铺底料布料厚度为25mm,铺底料粒度为10mm~20mm。
7.烧结点火
点火温度一般控制在1050℃~1150℃。
点火炉烧嘴前煤气压力>3kPa,助燃空气压力>3.5kPa。
混合煤气压力低于2.5kPa时,煤气快速切断阀自动进行切断,同时联系能源中心。
正常生产时,合适的烧结点火要求是空煤气比例合适,空燃比为4-5:
1。
整个火焰呈青白色、或黄亮色,火焰燃烧均匀,幕帘式烧嘴火焰呈幕帘状。
如空煤气比例过高,火焰呈暗红色。
空煤气比例过低,煤气不能完全燃烧,火焰呈暗绿色。
火焰交点应到达料面。
烧结机的设备参数表
序号
名称
参数
单位
1
有效烧结面积
384
m2
2
有效烧结长度
96
m
6
烧结台车尺寸(宽×长)
4000×1500
mm
7
台车拦板高度
700
mm
8
烧结台车运行速度
1.5~4.5
m/min
9
烧结台车数量
156
个
10
烧结料层厚度
650
mm
360m2烧结点火器技术性能
1、点火器型式:
HMLD—360高、焦混合煤气幕帘式
2、点火温度:
1150±50℃
3、点火时间:
60~90sec
4、点火热耗:
92.1MJ/t.s(2.2×104kcal/t.s)
5、点火器炉膛高:
350mm
6、点火煤气量:
6000~7094Nm3/h;最大9067Nm3/h(常温)
7、助燃空气量:
13000~15370Nm3/h;最大19640Nm3/h(常温)
8、点火烧嘴型式:
ML—68型幕帘式高、焦混合煤气烧嘴
9、点火烧嘴数量:
8台×2排=16台(两排垂直并列布置)
8.抽风烧结
抽风系统为双系列,每系列有一根大烟道,26个风箱。
风箱和烟道的负压可通过调节风箱蝶阀开度、或主风机进口阀开度来控制。
当两根大烟道流量、温度、负压不平衡时,应检查烧结机的布料等参数,必要时考虑调节风箱蝶阀开度、主风机进口阀。
大烟道废气温度:
90℃-150℃。
生产时烧结饼表面状态:
正常料面颜色为青黑发亮或黑亮色,异常情况料面颜色为大面积黄色;正常情况料面整体固结均匀,异常情况有料面过融或夹生料。
生产时机尾排矿部状态:
正常时整个台车料同时落下,异常情况成碎状落下;正常情况扬尘不多,异常情况红尘翻滚;正常情况落下时有“咚”的清脆声音,异常时烧结饼啪啦啦裂开,声音沉闷而小;正常时单辊破碎机咬入需要一定时间,异常时通过破碎机过快;正常时红火层沿着烧结机台车宽度方向均匀平直,厚度约占料层总厚度的1/3,异常情况较多,如有花脸、红火层厚度在1/3以上,不均匀,有未烧透的生料等。
正确控制各个风箱负压,保证混合料正常点火,充分利用抽风能力,达到较高的生产率。
当烧结抽风系统漏风情况不变时,风箱和大烟道负压取决于料层的透气性,负压突然升高说明透气性变坏、乃混合料水分过大或过小、配碳量过大或过小、混合料粒度变细、压料过紧或料层表面过融所致,操作中要判明情况,具体情况具体对待。
抽风系统负压逐渐下降,说明漏风现象加剧,如同时风量减少,说明风机叶片磨损或挂泥,要及时清扫或更换转子。
为充分利用抽风能力,应减少和杜绝漏风现象,经常检查抽风系统,堵漏风。
停机时间≤2小时,不停主风机,只关闭风箱闸门或主风机风门。
烧结机停机时,为避免台车上烧结矿中含有生料,一般在停机以后再继续抽风20分钟后,再关闭主风机风门。
主抽风机为SJ20000型离心鼓风机,共二台。
主电机N=6700KW。
风量20000m3/min(工况),升压(静压)16500Pa,入口压力-16000Pa,出口压力500Pa。
主抽风机设备参数
序号
名称
参数
单位
备注
1
型号
HowdenL3NDBL6T
2
风机入口流量
20000
M3/min
3
风机静压升
16500
Pa
4
风机入口压力
-16000
Pa
5
风机出口压力
500
Pa
6
风机转速
1000
Rpm
7
风机轴功率
6018
Kw
8
风机全压效率
≥85%
%
9
配套电机功率
6700
KW
9.烧结矿FeO的管理
热FeO目标值≤10%,考核波动范围为:
FeO目标值±1.0%。
烧结矿FeO偏离目标值,可通过调整固体燃料配比来使烧结矿FeO达到目标值,固体燃料配比调整时,要充分考虑该调整对烧结过程、返矿、转鼓指数、筛分指数、RDI等指标的影响,在调整前要综合分析。
10.烧结矿MgO的管理
烧结矿MgO的目标值根据高炉冶炼需要确定,考核波动范围为:
MgO目标值±0.50%。
烧结矿MgO日常控制管理中,必须根据烧结矿的MgO含量,适当调整菱镁石配比。
11.烧结矿作业
热烧结矿由水冷式单辊破碎机进行破碎,经过破碎后的烧结矿粒度≤150mm。
单辊破碎机的主轴和齿冠用水冷却`,水压≥0.245MPa。
序号
名称
参数
单位
备注
1
型式
合金堆焊齿辊水冷剪切式
2
处理能力
870~1100
t/h
3
齿辊转速
7.77
r/min
4
给料温度
~850
℃
5
破碎后粒度
≤150
mm
6
工作宽度
4240
mm
热烧结矿由鼓风环式冷却机冷却,冷却后的烧结饼温度≤150℃,表面呈乌黑略有亮泽。
不允许有未烧透的烧结饼进入冷却机,以免“二次烧结”,降低冷却效果和造成烧结矿结大块。
台车布料应均匀、平整,厚度1400±100mm。
冷却机与烧结机之间实现速度、层厚同步调节,一般情况下保证环冷机厚铺慢转、料面平整,密切关注料面变化,防止出现冷却机严重堆料或卸料漏斗堵塞而影响正常运行。
在组织生产时,应根据产量、天气、烧结矿被冷却程度以及冷却风机的设备状态来决定冷却风机的运转台数。
正常情况时,1#冷却风机是生产时必须运转的风机。
冷却风机的运转台数必须保证把烧结饼冷却到150℃下,但也不宜低于60℃,避免过度冷却,浪费电力。
序号
名称
参数
单位
4
有效冷却时间
40~120
min
6
正常冷却时间
80
min
7
环冷机冷却面积
415
m2
9
环冷机台车数量
72
个
10
台车宽
3500
mm
11
料层厚度
1400(台车拦板高1500)
mm
14
冷却风机数量
5
台
15
进料温度
700-800
℃
16
排料温度
<150
℃
17
给矿粒度(未经筛分)
0-150
mm
12.整粒筛分作业
冷矿筛分由两个系统组成,两个系列同时工作,互为备用。
采用三次冷筛流程。
1~3次筛筛缝宽度或筛孔尺寸分别为5mm、10mm、20mm。
每个系列冷矿筛分由1台3000×9000与2台3000x7500振动筛串联完成,第一段筛出5~0mm冷返矿,第二段筛出10~5mm小成品,第三段筛出20~10mm铺底料,筛上为>20mm成品烧结矿,各段处理量如下:
序号
设备名称
型
号
数
量
筛分物料
物料粒度
mm
筛孔mm
物料堆比重
t/m3
最大处理量
(t/h)
电机型号功率
筛面倾角
(°)
振幅
1
一次冷矿筛
TDSS3000×9000上振式三轴椭圆等厚振动筛
2
冷烧结矿
0~150
5
1.7
810
Y315M-6
90KW×1台
11,18,25
长轴8-10mm、短轴3-5mm
2
二次冷矿筛
TDSS3000×7500上振式三轴椭圆等厚振动筛
2
冷烧结矿
0~150
10
1.7
637
Y315S-6
75KW×1台
10,15,20
长轴8-10mm、短轴3-5mm
3
三次冷矿筛
TDSS3000×7500上振式三轴椭圆等厚振动筛
2
冷烧结矿
0~150
20
1.7
435
Y315S-6
75KW×1台
5,10,15
长轴8-10mm、短轴3-5mm
成品烧结矿中-5mm部分<6%,否则要汇报中控室考虑和安排清理三次筛筛网,或采取其他措施降低烧结矿筛分指数;烧结返矿中+5mm部分>7%,说明筛分机筛孔有磨通现象,须请示中控室安排检查,需补修处理则补修处理,需更换筛网则更换筛网。
当单系统设备故障时,以另一成品单系统运转来维持低生产率生产,继续往高炉烧结矿槽供料;当需要低生产率生产时,以单系统运转来降低能耗和减少成品设备磨损。
13.烧结矿矿槽
成品烧结矿经转运站经NO.4转运站运往烧结矿槽,正常情况下,烧结矿直接运往高炉矿槽,同时可经槽上胶带机上的移动卸矿车将烧结矿卸至矿槽内贮存。
贮矿槽下设有GZG1003电振给料机,经胶带机转运至高炉矿槽,由于穿越烧结矿厂区运输球团矿的胶带机通廊,限制了烧结矿槽的格数,因此烧结矿槽贮存烧结仅3213t。
装车矿槽可以连续进行,装汽车运出,可贮存在原料场。
14.检化验要求
烧结厂检验项目统计表表5-7
物料名称
理化检验项目
送检样量/频次
烧结精矿粉
TFe、SiO2、CaO、MgO、Al2O3、S、H2O、烧损
5kg,烧损1次/半月、其它1次/班
竖炉精矿粉
TFe、SiO2、CaO、MgO、Al2O3、S、H2O、粒度(-200目)、烧损
5kg,烧损1次/半月、其它1次/班
富矿粉
TFe、SiO2、CaO、MgO、Al2O3、S、H2O、烧损
5kg,烧损1次/半月、其它1次/班
铁皮
TFe、SiO2、H2O、烧损
5kg,烧损1次/半月、其它1次/班
混匀矿
TFe、FeO、MgO、CaO、SiO2、S、P、C、烧损
5kg,烧损1次/半月、其它1次/班
烧结矿返矿
TFe、FeO、CaO、MgO、Al2O3、SiO2、S、粒度(<5㎜)、含炭量、烧损
5kg,烧损1次/半月、其它1次/班
球团矿返矿
TFe、CaO、SiO2、Al2O3、P、粒度(<5㎜)、烧损
5kg,烧损1次/半月、其它1次/班
钢泥
TFe、H2O、SiO2、MgO、Al2O3、FeO、烧损
5kg,烧损1次/半月、H2O/班其它1次/半月
高炉重力除尘灰
TFe、CaO、SiO2、MgO、Al2O3、FeO、含炭量、H2O
5kg,1次/周
高炉布袋除尘灰
TFe、CaO、SiO2、MgO、Al2O3、FeO、含炭量、H2O
5kg,1次/周
烧结混合料
含炭量、H2O、粒度(<1㎜、1-3㎜、3-5㎜、>5㎜)
5kg,1次/天
竖炉混合料
H2O、粒度(-200目)、含炭量
5kg,H2O和粒度1次/班、含炭量1次/班
焦粉
固定碳、灰份(CaO、SiO2、MgO、Al2O3、Fe2O3、TiO2、Na2O、SO3、P2O5等)、挥发份、H2O、S、烧损
5kg,烧损1次/半月、H2O1次/班、其它1次/天
无烟煤
固定碳、灰份、挥发份、H2O、S、烧损
5kg,烧损1次/半月、H2O1次/班、其它1次/天
菱镁石
MgO、CaO、SiO2、Al2O3、H2O、烧损、粒度(<3㎜)
5kg,烧损1次/半月、H2O1次/班、其它1次/天
石灰石
CaO、SiO2、MgO、Al2O3、H2O、粒度(<3㎜)、烧损、
5kg,烧损1次/半月、其它1次/班
生石灰
SiO2、CaO(2次/班)、MgO、Al2O3、活性度