铸造车间实习报告熔炼篇.docx
《铸造车间实习报告熔炼篇.docx》由会员分享,可在线阅读,更多相关《铸造车间实习报告熔炼篇.docx(26页珍藏版)》请在冰豆网上搜索。
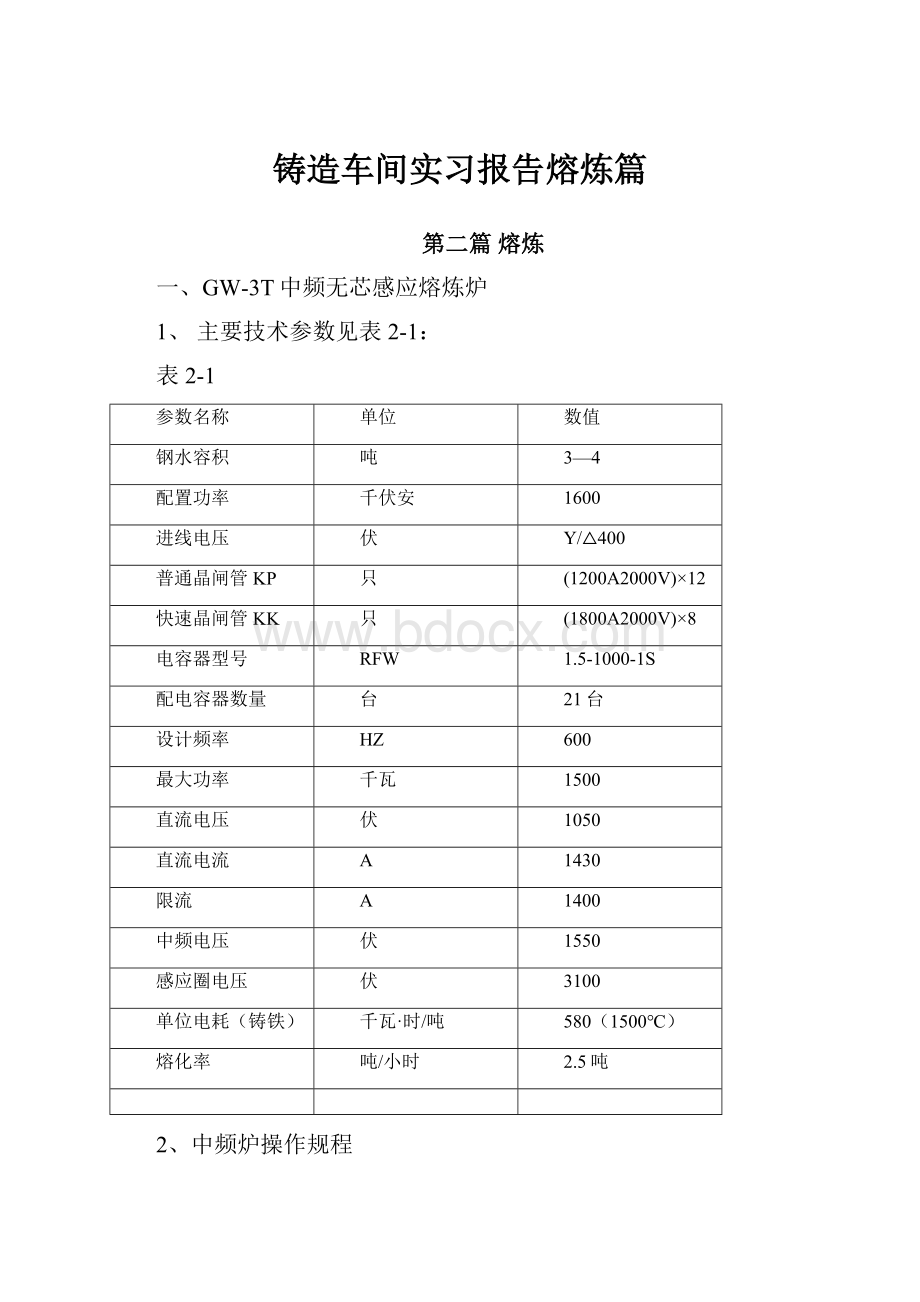
铸造车间实习报告熔炼篇
第二篇熔炼
一、GW-3T中频无芯感应熔炼炉
1、主要技术参数见表2-1:
表2-1
参数名称
单位
数值
钢水容积
吨
3—4
配置功率
千伏安
1600
进线电压
伏
Y/△400
普通晶闸管KP
只
(1200A2000V)×12
快速晶闸管KK
只
(1800A2000V)×8
电容器型号
RFW
1.5-1000-1S
配电容器数量
台
21台
设计频率
HZ
600
最大功率
千瓦
1500
直流电压
伏
1050
直流电流
A
1430
限流
A
1400
中频电压
伏
1550
感应圈电压
伏
3100
单位电耗(铸铁)
千瓦·时/吨
580(1500℃)
熔化率
吨/小时
2.5吨
2、中频炉操作规程
见附表2-13吨中频无芯感应熔炼炉安全操作规程。
二、工艺流程
修筑坩埚——烘烤和坩埚烧结——加料——升温融化——铁水保温——取样光谱分析—成分调整——升温并进行保温——出炉——孕育或炉外球化——浇注铸件
1、坩埚修筑
(1)按照“坩埚模具”图焊制坩埚模具;要求外形必须圆整;所有外表面焊缝均须打磨平整,内部焊缝要剔除焊渣。
图2-1坩埚模具
(2)感应圈涂层的安装
A.感应圈涂层材料的混合
选择专用灰浆箱,尽量靠近炉体放置→倾倒感应圈涂层材料,注意不得混入任何包装袋碎片及其他杂物→先彻底均匀地混合干燥的材料,注意消除颗粒的偏析→缓慢地加入水,并彻底翻转多次,直至涂料能快速流动。
★注意:
涂料的混合过程一般为3~5分钟,不应超过10分钟;混制涂料及涂抹全过程不能超过30分钟。
B.感应圈涂层材料的首次涂挂
检查感应圈是否与炉体同心→用镘刀将涂料抹进并密封各圈感应圈匝间的缝隙→填平底层感应圈和炉底、上部顶层感应圈和支撑架之间的空隙→逐渐加厚涂料的涂挂厚度至略大于规定尺寸→用刮板刮制上大下小的圆台体侧面和底面。
★注意:
涂料涂挂厚度:
上部距耐火垫圈内侧10mm,下部距感应圈内侧35mm。
C.感应圈涂层的修补
★注意:
清理掉感应圈涂层上的所有绝热材料、杂质,用适量涂料修补。
D.感应圈涂层的固化
正常情况下,大修或新修感应圈涂层的空气固化时间为24小时;若需加速干燥过程,可在初次固化(需5小时)后,插入约500W的保温灯加温;小修的感应圈涂层空气固化时间为6小时。
★注意:
不得使用明火或燃烧器加速干燥过程。
E.感应圈涂层的固化
若是正常的炉衬修筑:
将中频炉中铁液流尽→冷却一段时间后,注水加速冷却→压缩空气向炉中吹气→冷却完毕→拆除炉嘴部位凝铁→用气垫钻拆除炉衬→倾斜炉体,倒出炉料→继续拆除直至干净。
图2-2炉体内吹压缩空气图2-3气垫钻拆除炉嘴炉衬
(3)铺设石棉布
截取三块至少要比未打结炉衬的炉子深度长100mm的石棉布(我公司为2.2m),将三块石棉布铺于炉壁,接缝保持10mm压叠不得露出感应圈涂层,把伸出炉口的石棉布压在炉体顶部。
图2-4铺设石棉布
(4)坩埚的填筑
A.填筑坩埚底部
向炉底倒入一定厚度的炉料,每层炉料厚度不超过125mm,用特制炉叉均匀捣实浮料后,使用电动筑炉器,从炉底中心开始以螺旋线形式向外圆周捣结,每层至少捣结四遍;捣实后用叉子把表面刮松,重新均匀振动过程中偏析出来的大颗粒防止分层;加入另一层浮材料重复上面的操作;打结好的炉底要比规定的炉底厚度高出25mm;将炉底刮平至规定的厚度并使炉底保持水平,最后核对炉底水平度;刮松已经打结好的坩埚底部与坩埚壁接触的材料表面。
B.安置坩埚模具
用塔吊安置坩埚模具,注意保证坩埚壁厚一致并与感应圈同心;使用楔形木楔成120°固定模具。
C.填筑坩埚壁
将打结完成并已刮松的坩埚底部与坩埚壁接触的材料表面全部叉四遍;添加耐火材料时须仔细检查每一层,注意不要让任何包装袋碎片及其他杂物混入粉料或进入填筑的炉衬内;填加耐火材料时,每层浮材料厚度不超过125mm,用叉子和铲子整平;用振动器沿同一方向小距离逐步紧实,注意每次紧实的间距不可过大,每层至少捣结四遍;在填加和打结每层耐火材料时要随时注意保证对坩埚模具的定位要求;打结完成后坩埚壁顶面须高出正常熔化液面75~100mm。
★注意:
如果炉衬耐火材料进入背衬和坩埚涂层之间,须全部清除干净。
如无法清除干净,全部炉衬就必须拆除重新填筑。
图2-5炉叉图2-6电动筑炉机
(5)修筑炉嘴
采用常温固化或可加热固化的可塑料捣筑,然后修成炉嘴的形状;要使可塑料和感应圈涂层完全接触,此处不铺设背衬。
2、烘烤和坩埚烧结
坩埚修筑完成后,开始送电用40-60%功率送电,使铸铁复合料有一定的强度,送电时间10-30分钟;然后以500℃/小时的升温速度将炉料加热到1000℃;再以580℃/小时升温速度将炉料加热到1580℃;在此温度下保温1小时,烧结炉衬;降温至正常熔化状态开始生产。
具体烧结曲线见图2-7。
★注意:
烧结过程必须严格按照烧结曲线进行烧结。
若两次熔炼时间间隔较长时,如果炉衬温度低于1000℃,须采用冷炉衬起熔工艺以保护炉衬,操作步骤同上。
图2-7烧结曲线
3、熔炼过程中各种炉料的添加顺序
先加入熔点较低、元素烧损较小的炉料,熔点较高、元素烧损较大的炉料后加,铁合金最后加入。
一般采用的加料顺序为生铁→废钢→回炉料。
其他合金加入顺序为:
增碳剂应加在炉子的中下部,炉内保留一些铁水或者先加入200Kg生铁,再加入增碳剂,上面接着加料;增碳剂按照1%的量分批加入。
锰铁、铬铁可在前期加入炉底铁水内,也可在后期加入。
增硫剂在后期加入。
硅铁、钼铁后期加入,直接投入溶清的铁水内合金的烧损最小,如果加入量比较大,也可随着最后一批铁料加入。
铜、镍待铁水熔清后加入。
4、通电熔化
(1)送电前,检查各运动构件的相互连接状况是否良好,润滑油是否足够。
当炉体各部位经检查符合要求后,炉体可投入正式运行。
(2)送电前,打开各冷却水管路阀门,并观察各回水是否流畅。
①控制柜和电容器柜进水压力:
0.1MPa-0.2MPa,进水温度:
≤30℃
②熔炼炉进水压力:
0.2MPa-0.3MPa,进水温度:
≤35℃
③各个水接头无渗漏。
(3)送电操作步骤:
①打开控制柜门,接通电源,进行盘面操作,中频炉控制面板见图2-8。
②将电路电源柜门上的“功率调节”旋钮逆时针旋到底,再按“控制合”按钮,“控制电源”灯亮,使控制系统通电。
观察整流脉冲变压器指示灯应全亮。
③按“贮能”按钮,贮能电机动作,贮能到位。
如果电机不动作,请电工检查。
④按“主电源合”按钮,主开关合闸。
此时直流电压表应反偏。
⑤按“复位”按钮,则控制板上的红灯熄灭,“保护X”灯也熄灭。
(如“保护X”灯未熄灭,再按一下“贮能”按钮,接着按“复位”按钮。
)
⑥顺时针慢旋“功率调节”旋钮,电炉频率表从靠近零位上升到最高位,反复扫频,逆变脉冲变压器指示灯闪烁,直流电压表应会上下摆动。
经过数次摆动后,电炉频率表应指示工作频率,并可听到电炉啸叫声,相关仪表停止摆动,并指向适当位置,表明启动成功。
⑦继续顺旋“功率调节”旋钮,使电炉电压达到工作位置。
经常观察两只直流电流表,指示值应基本相同。
如果指示值相差过大,应请电工检查。
(4)送电和开炉应有专人负责,送电后严禁接触感应器和电缆,开始送电十分钟内用40-60%功率送电,以防电流波动太大。
然后再改用高电压送电,使炉料自下而上地慢慢加热和熔化。
(5)熔化过程中加入的造渣材料和铁合金必须经过高温烘烤,调节功率时应根据炉内钢水调整,绝对不能一次将调功旋钮调到底。
(6)在熔化过程中,应经常观察坩埚的侵蚀情况、冷却水的水温和电炉功率表,若有漏炉危险时,应立即停止熔化。
(7)在熔化过程中应经常观察各种仪器的指示表,当发现表值超过规定时,应立即停电进行检查,只有发现并排除了故障后,方可继续熔化;如果在熔化过程中发现炉体变红,应立即停止熔炼。
(8)在熔化过程中应经常检查各管路及水冷电缆是否漏水,不要让炉渣或水接触水冷电缆。
(9)向炉内倾倒铁水时必须停电。
★注意:
在炉料全部熔化后,应立即扒渣,防止结成“渣盖”。
如结成“渣盖”,应立即停电,将“渣盖”打碎扒出炉外,或用高温铁水烫化,否则容易造成下部的铁液温度过高。
图2-8中频炉控制面板
5、光谱分析
铁水熔清后,升温至1430℃-1450℃之间取样做光谱成分分析,取样之前一定要先停电,待炉内渣子返上来之后,打净炉内渣子再取样。
因为炉渣中夹带有未熔化的增碳剂,如留在炉内会继续增碳。
扒渣干净后用坩埚舀取铁水,浇注金属铸型中,待冷却后砸断试样送至化验室进行成分化验。
★注意:
舀取铁水时,必须将坩埚深入液面以下,反复搅动使铁液成分均匀。
图2-7浇注试样图2-8试样
6、调整铁水成分
增碳和增硅都需要时,要先进行增碳,再进行增硅操作,加入合金及增碳剂后要等材料完全熔化且成分均匀后才能取样分析成分,这个过程需要5-10分钟(尤其是增碳剂的熔化较慢)。
增碳剂的加入量在8Kg以上,需要倒出一包铁水,然后往炉内加碳,把铁水倒回炉内。
当中频炉内铁水成份不符合要求时,应对中频炉内铁水进行调整。
中频炉内铁水成份的调整是通过加入各种铁合金、生铁、废钢、增碳剂等材料,来实现各成分的调整,最终达到符合要求的原铁水成份。
此时,需保证所加材料充分熔化并均匀后方可取样进行含量分析,只有当成份符合工艺要求,才可出水进行浇注。
(1)、碳含量调整
A.增碳
a.采用增碳剂,加入量按下面公式计算:
X=(C终-C原)×炉内铁水量/(A×η)
b.采用生铁,加入量按下面公式计算:
X=(C终-C原)×炉内铁水量/(D-C终)
公式内符号含义:
X:
指需加入的生铁量,单位Kg
C终:
指最终要调整到的铁水含碳量,按百分含量计
C原:
指还未调整的铁水含碳量,按百分含量计
炉内铁水量:
指要调整的炉内铁水量,单位Kg
A:
增碳剂中碳的百分含量,按批料化验单(一般按95%左右)
η:
增碳剂中碳的吸收率(一般按80%左右)
D:
生铁中碳的百分含量,据所加生铁的批化验单确定(一般按4.1-4.5%)
B.降碳
a.采用废钢,加入量按下面公式计算:
X=(C原-C终)×炉内铁水量/(C终-E)
公式内符号含义:
X:
指需加入的废钢量,单位Kg
C终:
指最终要调整到的铁水含碳量,按百分含量计
C原:
指还未调整的铁水含碳量,按百分含量计
炉内铁水量:
指要调整的炉内铁水量,单位Kg
E:
指废钢中碳的百分含量,据所加废钢的批化验单确定(一般按0.25%左右)
增碳剂加入量(kg)速查见表2-2。
(2)、硅元素调整
A.增硅
采用75#硅铁调整,加入量按下面公式计算:
X=(Si终-Si原)×炉内铁水量/(F×η)
公式内符号含义:
X:
指需加入的75#硅铁量,单位Kg
Si终:
指最终要调整到的铁水含硅量,按百分含量计
Si原:
指还未调整的铁水含硅量,按百分含量计
炉内铁水量:
指要调整的炉内铁水量,单位Kg
F:
指75#硅铁中硅的百分含量,据所加硅铁的批化验单确定(一般按约72%)
η:
指所加硅铁中硅的吸收率(一般按90%左右计算)
B.降硅
采用废钢降硅调整,加入量按下面公式计算:
X=(Si原-Si终)×炉内铁水量/(Si终-G)
b.加入废钢后的炉内铁水碳终含量,计算公式如下:
C终=(C原×炉内铁水量+X×E)/(炉内铁水量+X)×100%
c.根据计算加入废钢后的碳终含量,再通过加入增碳剂调整碳含量,
根据计算结果,操作上可以同时加入废钢和增碳剂进行一次调整
公式内符号含义:
X:
指需加入的废钢量,单位Kg
C终:
指加入废钢后的铁水含碳量,按百分含量计
C原:
指还未加入废钢的铁水含碳量,按百分含量计
E:
指废钢中碳的百分含量,据所加废钢的批化验单确定(一般按0.25%左右)
Si终:
指最终要调整到的铁水含硅量,按百分含量计
Si原:
指还未调整的铁水含硅量,按百分含量计
炉内铁水量:
指要调整的炉内铁水量,单位Kg
G:
指废钢中硅的百分含量,据所加废钢的批化验单确定(一般按0.3%左右)
75硅铁加入量(kg)速查见表2-3。
(3)、锰元素调整
A.增锰
采用65#锰铁调整:
X=(Mn终-Mn原)×炉内铁水量/(F×η)
公式内符号含义:
X:
指需加入的65#锰铁量,单位Kg
Mn终:
指最终要调整到的铁水含锰量,按百分含量计
Mn原:
指还未调整的铁水含锰量,按百分含量计
炉内铁水量:
指要调整的炉内铁水量,单位Kg
F:
指65#锰铁中锰的百分含量,据所加锰铁的批化验单确定(一般按约62%左右)
η:
指所加锰铁中锰的吸收率(一般按90%左右计算)
B.降锰
a.采用废钢调整降锰:
X=(Mn终-Mn原)×炉内铁水量/(Mn终-G);
b.采用生铁和废钢调整:
X=(Mn终-Mn原)×炉内铁水量/(Mn终-D)
c.加入适量废钢降碳;
公式内符号含义:
X:
指需加入的废钢量,单位Kg
D:
生铁中锰的百分含量,据所加生铁的批化验单确定(一般按0.2%左右)
Mn终:
指最终要调整到的铁水含Mn量,按百分含量计
Mn原:
指还未调整的铁水含Mn量,按百分含量计
炉内铁水量:
指要调整的炉内铁水量,单位Kg
G:
指废钢中Mn的百分含量,据所加废钢的批化验单确定(一般按0.5%左右)
★注:
此时炉内铁水碳量调整再通过参照增碳剂计算公式,加入增碳剂来调整。
锰铁加入量(kg)见表2-4。
(4)、降磷
方法参见降锰的方法
(5)、硫的调整
A.降硫
当铁水含硫量不超过0.06%时,优先采用脱硫剂降硫,脱硫剂加入量一般为所处理的铁水量的2.5-3%;
当铁水含硫量超过0.06%时,也可采用生铁与废钢降硫,方法参见降锰的方法。
B.增硫
可采用加入硫铁来调整硫量,加入量按下面公式计算:
X=(S终-S原)×G/(η×F)
公式内符号含义:
X:
指需加入的硫铁量。
单位Kg
S终:
指最终要调整到的铁水含S量,按百分含量计
S原:
指还未调整的铁水含S量,按百分含量计
G:
指要调整的炉内铁水量,单位Kg
η:
指所加硫铁中硫的吸收率(一般按45%左右计算)
F:
指硫铁中S的百分含量,据所加硫铁的批化验单确定
(6)、其它合金元素的调整
A.合金元素含量的降低,原则上采用该调整元素更低含量的生铁或废钢来调整。
生铁或废钢的加入量按下面公式计算:
X=(A原-A终)/(A终-B)×G
公式内符号含义:
X:
指需加入的生铁或废钢量,单位Kg
A终:
指调整后终铁水中应调整到要求的A元素终含量,按百分含量计
A原:
指调整前原铁水中还未调整的A元素含量,按百分含量计
G:
指要调整的炉内铁水量,单位Kg
B:
指生铁或废钢中A元素的百分含量,按批化验单确定
B.合金元素含量的增加
采用合金锭或板(粒)进行调整,公式计算:
X=(A终-A原)×铁水量/(F×η)
公式内符号含义:
X:
指需加入的合金量,单位Kg
A终:
指最终要调整到的铁水含合金量,按百分含量计
A原:
指还未调整的铁水含合金量,按百分含量计
铁水量:
指要调整的铁水量,单位Kg
F:
指合金中元素的百分含量,据所加合金的批化验单确定
η:
指所加合金中元素的吸收率
C.各元素的吸收率
所加铬铁中铬的吸收率一般按90%左右计算;所加铜的吸收率一般按98%左右计算,所加钼铁中钼的吸收率一般按95%左右计算;所加镍的吸收率一般按99%左右计算,所加锡的吸收率一般按90%左右计算。
★注意问题:
当钼铁在铁水包内微调时,其粒度应不大于3mm。
当铜在铁水包内微调时,其块度应不大于8×40×40mm。
当镍在铁水包内微调时,其块度应不大于6×30×30mm。
当需要调整锡时,一般根据工艺卡片的要求,在转运包内进铁水1/3时,将锡倒入包
内,继续出铁水,使锡在铁水中充分熔融均匀。
原铁水质量kg
Mn质量分数增量%(%)
(%)
0.1
0.2
0.3
0.4
0.5
0.6
0.7
0.8
0.9
500
0.8
1.7
2.5
3.3
4.2
5.0
5.8
6.7
7.5
1000
1.6
3.4
5.0
6.6
8.4
10.0
11.6
13.4
15.0
1500
2.5
5.0
7.5
10.0
12.5
15.0
17.5
20.0
22.5
3000
5.0
10.0
15.0
20.0
25.0
30.0
35.0
40.0
45.0
5000
8.3
16.7
25.0
33.3
41.7
50.0
58.3
66.7
75.0
表2-2增碳剂加入量(kg)速查表
表2-375硅铁加入量(kg)速查表
原铁水质量kg
C质量分数增量%(%)
(%)
0.1
0.2
0.3
0.4
0.5
500
0.6
1.2
1.9
2.5
3.1
1000
1.2
2.4
3.8
5.0
6.2
1500
1.8
3.8
5.6
7.5
9.4
3000
3.6
7.8
11.2
15.0
18.8
5000
6.3
12.5
18.8
25.0
31.3
表2-4锰铁加入量(kg)速查表
原铁水质量kg
Si质量分数增量%(%)
(%)
0.1
0.2
0.3
0.4
0.5
500
0.7
1.4
2.1
2.9
3.6
1000
1.4
2.8
4.3
5.6
7.5
1500
2.1
4.3
6.4
8.4
10.7
3000
4.2
8.6
12.4
16.8
21.4
5000
7.1
14.3
21.4
28.6
35.7
6、出炉
(1)当金属液的各项指标符合技术要求时,开始出铁水,出铁水时只允许倾炉机构有电。
(2)若熔炼结束,炉内一般不留铁液,避免炉体上下温差较大致使坩埚产生裂纹。
(3)出铁时缓慢控制炉体倾斜,时刻注意行车显示屏,即将达到出铁重量时迅速停止倾动,将炉体复位,出铁重量应控制在10Kg范围内。
7、孕育或球化处理
(1)孕育:
金属凝固之前,在一定条件下向铁水中加入少量物质,以促进石墨形核,显著改善组织和性能的处理方法。
我公司采用浇包内孕育和随流孕育两种方式的结合的方式,能够有效地减少孕育剂用量。
浇注包内孕育
a.孕育剂为硅钡钙合金75#硅铁粒,粒度为1~3mm,使用前加热烘干。
b.孕育剂加入量0.4%~0.5%。
c.孕育剂加入方式:
出铁水前将孕育剂投入包内,依靠铁水的翻滚将其均匀熔化。
d.实际生产中有特殊要求的孕育剂加入量以铸造工艺卡的要求为准
.铁液随流孕育
a.孕育剂为硅钡钙合金75#硅铁,粒度为0.2~0.7mm,使用前加热烘干。
b.孕育剂加入量0.05%。
c.孕育剂加入方式:
开启浇注机随流孕育。
d.实际生产中有特殊要求的孕育剂加入量以铸造工艺卡的要求为准。
在确保浇注温度前提下,每包铁水从出炉至浇注完毕应在8min内完成,以避免孕育衰退,时间以时钟或专用计时设备的计量结果为准。
(2)球化处理:
加入铁液中能使石墨在结晶生产时长成球状的元素称为球化元素。
表2-3是各种球化元素的分类。
球化能力强的元素都是很强的脱氧及去硫元素,并且在铁液中不溶解,与铁液中的碳能够结合。
虽然具有使石墨球化作用的元素有多种,但在生产条件下,实用的目前是Mg、Ce、Y三种。
工业上常用的球化剂即是以三种元素为基本成分而制定的。
我国实用最多的球化剂是稀土镁合金,国外大都采用镁合金和纯镁球化剂,近年来逐渐加入稀土元素于球化剂中,但用量是很低的,其中一个主要原因是国内铸造生铁中杂质元素含量较高,而国外大多是应用高纯生铁。
表2-5球化元素的分类
球化能力
球化元素
球化条件
强
镁、铈、镧、钙、钇
一般条件
中
锂、锶、钡、钍
要求原铁液含硫极低
弱
钠、钾、锌、镉、锡、铝
冷却速度要快,原铁液含硫极低
某些元素存在在铁液中会使石墨在生长时无法长成球状,这些元素称为反球化元素。
为了保证石墨的良好球化,应对铁液中反球化元素的含量加以限制。
不同的球化元素对反球化元素的干扰作用具有不同的抵抗力,因此当采用不同的球化元素进行球化处理时,对于原铁液中反球化元素的限量要求也不相同。
在用純镁作球化剂时,反球化元素的单项限量值见表3-4。
表2-4反球化元素的界限量
元素
AL
Ti
Pb
Zi
As
Sb
Bi
Sn
Te
Se
界限量
0.05
0.07
0.002
0.03
0.05
0.01
0.002
0.05
0.003
0.03
三、喂丝机及球化处理
喂丝球化技术是一种利用自动化喂丝装置,将镁合金包芯线以一定地速度和长度,连续、均匀地插入到隔断空气有效流动的加盖的铁液处理包底部适当位置启爆,在适宜的铁液温度及高度压力下进行稳定、受控的球化处理工艺方法。
其经济性与球化品质的可靠性及可控性已为愈来愈多的企业所重视。
与冲入法比较具有以下特点:
(1)处理包结构简化,无堤坝或反应室,且无须覆盖剂。
(2)球化剂、接种剂耗用量少,处理后铁液纯度高、渣量少、降温小。
、
(3)喂丝装置为自动化控制,可精确定量控制Mg残,球化质量稳定可靠,球墨数量多且细小,球铁力学性能明显改善。
(4)直接材料成本减少5%以上,综合成本降低约10%。
(5)镁光及烟尘污染大为减轻,且易集中处理。
现在我公司球化工艺采用喂丝球化法,与倒包球化二者球化、孕育成本对比可节省成本21.4元/吨。
详细见表2-7。
表2-7喂丝球化与倒包球化成本对比
喂丝球化
倒包球化
加入量
成本
加入量
成本
球化剂
---
---
1.2%
132
喂丝线
1.1%
165
---
---
孕育剂
0.5%
48.9
0.75%
73.3
覆盖剂
---
---
0.6%
30
总计
---
213.9
---
235.3
倒包次数
2
3
出炉温度
1530
1560
材料价格:
喂丝线14800元/吨,球化剂11000元/吨,孕育剂9775元/吨,覆盖剂5000元/吨。
1、喂丝设备的组成
喂丝设备由主机、控制柜、放线架等部分组成,其中主机部分由主传动、压下装置、旋转装置、气路系统、导线管、升降等五部分组成。
2、喂丝操作
(1)我公司使用WX-4D型铸造喂线机,其控制柜控制面板如下图所示:
喂丝速度显示屏
实际喂丝长度显示指示
(2)操作步骤如图2-9所示
3、注意事项
(1)球化处理时,将待处理的铁水一次性出到铁水包内,铁水液面距球化包上沿保持30~40cm距离。
(2)铁水出炉温度根据铸件浇铸温度的要求来确定,加上铁水处理转运过程中的降温,一般在1480℃~1560℃之间。
(3)铁水的孕育,将一次孕育加入包内,其余