大中型球罐组焊新工艺探讨.docx
《大中型球罐组焊新工艺探讨.docx》由会员分享,可在线阅读,更多相关《大中型球罐组焊新工艺探讨.docx(16页珍藏版)》请在冰豆网上搜索。
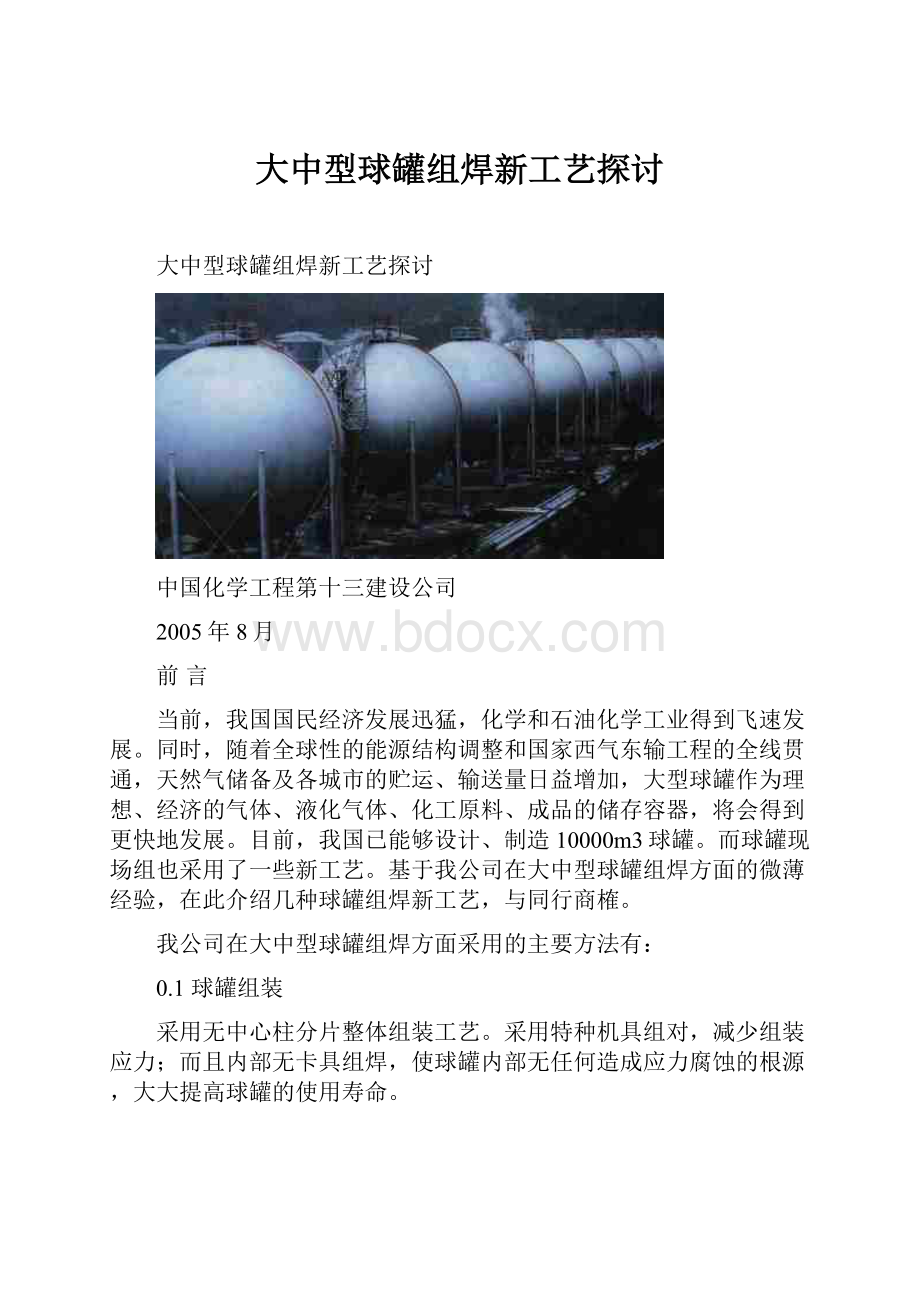
大中型球罐组焊新工艺探讨
大中型球罐组焊新工艺探讨
中国化学工程第十三建设公司
2005年8月
前言
当前,我国国民经济发展迅猛,化学和石油化学工业得到飞速发展。
同时,随着全球性的能源结构调整和国家西气东输工程的全线贯通,天然气储备及各城市的贮运、输送量日益增加,大型球罐作为理想、经济的气体、液化气体、化工原料、成品的储存容器,将会得到更快地发展。
目前,我国已能够设计、制造10000m3球罐。
而球罐现场组也采用了一些新工艺。
基于我公司在大中型球罐组焊方面的微薄经验,在此介绍几种球罐组焊新工艺,与同行商榷。
我公司在大中型球罐组焊方面采用的主要方法有:
0.1球罐组装
采用无中心柱分片整体组装工艺。
采用特种机具组对,减少组装应力;而且内部无卡具组焊,使球罐内部无任何造成应力腐蚀的根源,大大提高球罐的使用寿命。
图0-1所示为中心柱分片组装球罐现场。
图0-1采用无中心柱分片组装球罐
0.2球罐焊接
采用CO2+药芯焊丝自动焊接技术。
工艺可靠性强,焊缝成型美观,焊接合格率高(98%以上)。
我公司引进的是美国林肯公司制造的DC400和DC600自动焊机,已成功地应用于大庆球罐、山东鲁西化肥厂球罐、青海格尔木球罐、攀枝花球罐、沧化集团球罐、广东湛江球罐等。
2.3球罐探伤
探伤选用铱-190γ或钴60射线全景曝光工艺。
2.4球罐热处理
采用柴油内燃法整体热处理工艺,应用计算机控制,使球罐整体受热均匀,球罐各热电偶升温曲线平滑、一致。
我公司柴油内燃法球罐焊后整体热处理工法获得国家一级工法。
1.大中型球罐无中心柱组装方法
1.1球罐无中心柱组装方法的优点
球罐的现场组装是整个球罐组焊工程的关键工序之一,工作量大,所用机具设备多,组装质量要求严,组装时既要使生产效率提高,又要减少组装的误差和应力,确保组装质量。
所以选择合理、先进的组装方法,不仅能提高组装质量,而且能提高效率,降低成本,缩短工期。
采用无中心柱分片组装工艺,用特种机具组对,能减少组装应力,内部无卡具组焊,使球罐内无任何造成应力腐蚀的根源,大大提高球罐的使用寿命。
为大中型球罐的现场安装提供了先进的工艺。
我公司大中型球罐无中心柱现场组装工法已获得省(部)级工法,并已申报国家级工法。
1.2.组焊程序
1.2.1球罐组装程序如下:
基础检查→球壳板复验→下段支柱安装→外架搭设→赤道带组装→调整赤道带及组装质量检验→下温带组装→下极带组装→上温带组装→上外架搭设→上极帤组装→防护棚搭设→内架搭莶→总体点焊→糄装质量检查。
1.2.2赤道带组装
赤道带组装是球罐整体组装的基准,建立在下段支柱安装就位的前提下,所以必须调整好支柱垂直度,在基础上按球壳板堍验尺寸加焊接收缩量放她基准线,用吊车将下段支柱吊装就位。
然后用地脚螺栓固定再搭设外脚手架。
按中心位置在两段支柱上各焊好等分的定位螺栓孔敿3个(见图一),根据支柱直径和板的重量,依据设计要求,一般采用Φ08--32mm璄高强度螺栓。
吊装第一块带上段支柱的赤道板,并按要求将其与下段支柱按中心线对中,锁紧螺栓,用拖拉绳将赤道板锚固(见图二),并使之略往外倾斜。
继续吊装第二块上支柱的赤道板,同时安装好相邻支柱间的拉杆,然后插入第一块不带支柱的赤道带板,利用龙门卡具调整好间隙(2±2mm),曲率控制在≤5mm,赤道带依次组装直至整体闭合。
图一:
球罐支柱上各焊好等分的定位螺栓孔板
图䪌:
用拖拉声绳固定赤道带板
赤道娦吊装宜连续作业,中途停止吊装时,尤其是过夜,两敞开端必须用锚绳向内、外拉固,以防大风。
还应注意赤道带组装完成后伊下用筋板封口,不昒整道焊缝点焊,减少整体周长收缩。
赤道带是整个球罐安装的基准带,其组装精度至关釉要,对于偶媃各带及整个球罐的组装质量影働很大,必须精心调整,以保证椭圆度、上下弦口水平度、对口间隙、错边量、角变形等技术参数达到规范要求后再进行下一步组装工序。
椭圆度可利用柱间拉杆调整,对口间隙、错边量、角变形用组装卡具调整。
支柱的垂直度要符合设计图纸及规范要求,在球罐径向和周向两个方向测量支柱的垂直度,确保垂直度在允许偏差内即可。
1.2.3下温带组装
吊装第一块下温带板时,上口用卡具与赤道带固定,下口用导链及钢丝绳拉在赤道带上弦口外侧的吊耳上,如图三,用卡具调整环缝间隙,用导链调整曲率,以后每隔一块板在下口用倒链固定一块。
下温带板组装时,要注意其下垂趋势,所以收口间隙控制在3mm以内为宜。
图三:
下温带板固定
1.2.4下极带组裁
下极带吊装完后,先调整与赤道帤连接的环缝,再调整纵缝,然后吊装下极边板,调整完后点焊固定。
考虑到罐内作业需要采光通风,人员进出罐方便等,下极顶中心敿勯暂不吊装,待罐内焊接作业结束后,再组装焊接。
1.2.5上温带组装
上温带板吊装时,下口用卡具与赤道带固定,上口用导链拉在预先埋好的锚点上,如图三,导链可隔两块板拉一个。
由于自重作用,上温带板有下垂趋势,为避免因下垂而造成最后一块板安装不上,所以上温带的收口应选择3~5mm。
上温带板吊装完后,也是先调整与赤道带连接的环缝,再调整纵缝,要避免弦口“露头”现象。
调整环缝时,必须保证赤道板和温带板的纵向弧度,切勿错口。
调整好后点焊固定,环缝丁字口处暂不点焊,其余各处点焊固定。
1.2.6上极带组装
上极带的组装与下极带组装基本相同。
吊装第一块上极外边板时,下口用卡具与上温带固定,上口用导链拉在预先埋好的锚点上。
上极外边板组装时,也要注意其下垂趋势。
上极外边板吊装完后,仍先调整其与上温带的环缝,后调整纵缝,然后吊装上极边板,调整完后点焊固定纵缝。
1.3球罐组对几何尺寸检查
球罐组装完成后,要对组装尺寸进行认真测量、调整,如有几何尺寸不符合标准要求,应加以调整,保证各部分的尺寸都符合规范要求。
表1-1中的数据是我们通过在北京燃气集团小屯储配厂四台10000m3球罐其中的第十一号罐施工过程中统计出来的。
表1-1北京燃气集团小屯储配厂四台第十一号球罐组对尺寸检查
项目
国家标准
自定标准
偏差
椭圆度
焊前50mm焊后80mm
焊前0~40mm焊后0~60mm
焊前10mm焊后20mm
棱角度
焊前7mm焊后10mm
焊前0~7mm焊后0~10mm
无
柱腿直线度
10mm
0~8mm
无
错边量
3mm
0~3mm
无
柱腿垂直度
15mm
0~15mm
无
余高
0-3mm
0-1mm
2mm
1.4球罐组对焊缝应力检查
在上述球罐施工中,经兰州石油机械研究所进行的声发射测试,各部位的焊缝应力均能达到国家和省部级的规范要求。
球罐组装完成后,内部工卡具焊点少,有利于清除固定块后的补焊、打磨及检测,组对作业环境好,整体工作量减少,使整体球罐外观相比以前有所提高。
1.5施工安全
由于在整个球罐的组装过程中,操作人员全部都在整体的固定钢制脚手架管平台上工作,较以往的传统工艺在挂架上和移动架上工作安全性得到大大提高。
1.6其他应注意的事项
1.6.1拖拉绳的选用:
以板重量的1/3选用拖拉绳的规格
①注:
按国家标准,拖拉绳应选用6×19+1,5倍的安全系数。
举例:
如①板重6吨,6×1/3=2吨。
查钢丝绳选用表为Φ15.5钢丝绳。
如②板重8吨,8×1/3=2.6吨
查钢丝绳选用表为Φ18.5钢丝绳。
如③板重11吨,11×1/3=3.6吨
查钢丝绳选用表为Φ21.5钢丝绳。
如④板重14吨,14×1/3=4.6吨
查钢丝绳选用表为Φ24.5钢丝绳。
拖拉绳的长度,一般拖拉绳与地面夹角为45°,以此数据来选用拖拉绳的长度.
1.6.2拖拉绳受力角度α必须大于30°角,见图三。
1.6.3所有的“吊耳”焊后必须作着色无损检查。
1.6.4赤道带吊起的第一块板必须要有抗风拖拉绳,以后依次最边赤道板必须有抗风拖拉绳。
1.6.5上下温带和上下极板则隔块加拖拉绳固定调节。
1.6.6外脚手架管的搭设要合理,即要考虑对组装人员的可操作,又要适应以后焊接人员的作业。
1.7效益分析:
从工程实践效果分析此工艺在组装过程中,所有的球壳板都处于自由状态,内在应力小,为焊接工序打下了良好的基础,与以前的工艺比较,以前组装一台大中型球罐所需人员58人,工期为15天,采用此工艺所需人员29人,工期为7天,使用吊车节约8个台班,较以前节约资金一半以上,工期缩短了一半,劳动力节约了一半,在组装过程中每台球罐降低成本节约资金30万元
2.大型球罐自动焊接技术
球罐壁板焊接采用非对称X型坡口对接形式,选用美国BUG-O公司制造的焊接设备,采用CO2+药芯焊丝自动焊方法进行焊接,自动焊工程量可达球罐焊接工程量80%以上。
2.1.CO2+药芯焊丝自动焊工艺原理
CO2+药芯焊丝电弧焊始于上世纪50年代末,经过近三十年的发展与完善,到80年代中期趋于成熟。
由于其高效、优质的特点,已在国内外造船、钢结构、容器制造领域得到广泛应用。
CO2+药芯焊丝电弧焊是一种由管状可熔化的焊丝与焊件之间的电弧所产生的热量进行焊接的方法。
在焊接过程中,CO2气体不但起屏蔽保护作用,还参与焊接冶金反应。
此外,在药芯焊丝内部装有焊剂混合物,焊接时,在电弧热作用下,熔化状态的焊剂材料、焊丝金属、母材金属和保护气体相互之间发生冶金作用,同时形成一层较薄的液态熔渣包覆熔滴并覆盖熔池,对熔化金属形成又一层保护,实际上这种焊接方法是一种气渣联合保护的方法。
这种焊接方法,焊接电流随送丝速度的大小变化而变化,送丝速度和焊接电压都可以预先设定。
焊接时,可根据不同的焊接位置,采用不同的规范,以获得不同的熔滴过度形式,从而达到保证焊接质量的目的。
2.2.焊接设备和焊接材料
CO2+药芯焊丝自动焊所需的基本设备包括:
焊接电源(美国林肯公司制造的DC400和DC600),磁吸式轨道,爬行机构,摆动机构。
焊前先把磁吸式轨道沿平行于焊缝方向铺设,再把摆动机构固定在爬行机构上,爬行机构通过齿轮与磁吸式轨道上的齿条啮合,在轨道上沿平行于焊缝方向爬行。
爬行机构上设有速度调节旋钮,通过它可调节焊接速度。
在摆动机构上设有摆动幅度、摆动速度、左右摆动停留时间、摆动方式选择等旋钮,可根据工艺要求在焊接前进行设置,也可在焊接中随时调节。
把焊枪固定在摆动机构的摆臂上,调整好焊枪与工件之间的角度,设置好各种焊接参数,即可在球罐上进行自动焊接。
焊接材料为φ1.6药芯焊丝,保护气体为CO2,纯度大于99.7%。
2.3焊接工艺试验
焊接前应按照相关标准进行焊接工艺试验。
2.4.大型球罐CO2+药芯焊丝自动焊主要技术问题
2.4.1定位焊在小坡口一侧进行,定位焊必须按工艺要求进行。
实践证明,定位焊的质量好坏是产生焊接缺陷的主要原因。
2.4.2根据缺陷统计分析,环缝缺陷远高于纵缝缺陷。
分析原因主要是横焊过程中焊道高低不平、宽窄不一、调节焊速不匀所致。
2.4.3每层的焊接厚度不宜太厚,一般打底层焊接厚度为5~6mm,其他层在3~4mm。
实践证明,大型球罐应用自动焊技术,提高了生产率,减轻了焊工的劳动强度,取得了一定经济效益和社会效益
3.采用柴油内燃法进行焊后整体热处理
球罐是一种焊接约束力较大的压力容器,焊前预热对于防止裂纹的产生、保证焊接质量是非常重要的。
而球罐在组装和焊接过程中不可避免的存在残余应力,残余应力的存在会不同程度地影响设备的安全运行。
因此,球罐焊后残余应力的消除是球罐组焊非常重要的环节。
目前消除球罐残余应力的方法有振动法、内燃法、电热法及超压法等几种。
此处介绍采用柴油内燃法进行焊前预热和焊后整体热处理。
该方法的特点是:
采用柴油内燃法进行加热、应用计算机控制,使球罐整体受热均匀,球罐各热电偶升温曲线平滑、一致。
我公司柴油内燃法球罐焊后整体热处理工法获得国家一级工法。
3.1热处理工艺
3.1.1原理
利用金属再结晶原理,消除球罐在球壳板压制、组对、焊接过程中产生的残余应力。
3.1.2燃烧方式:
柴油内燃法。
3.1.3热处理工艺过程
(1)升温恒温降温;
(2)工艺曲线:
按照不同材质、厚度,依据相关标准规范进行。
(3)恒温时球罐各部温差应不大于50℃。
3.2.热处理主要设备、辅助设施及其作用
热处理主要设备、辅助设施及其作用见表2-1。
3.3热处理操作程序、方法及故障排除
3.3.1操作程序
点火升温恒温降温停火。
表3-1热处理主要设备、辅助设施及其作用
序号
设备及设施
用途
备注
1
自动平衡记录仪
自动记录并调整各测量点温度
2
热电偶及补偿导线
测量温度并输入平衡记录仪
3
霍克烧嘴
将柴油雾化并点燃喷出
4
点燃器
点火
5
点火器
保证烧嘴连续燃烧
6
齿轮油泵
向烧嘴供油
7
浮子流量计
计量供油量、调整供油参数
8
空压机
供烧嘴燃油雾化及点火器用空气、
9
柴油槽
贮存油
10
压力表
指示风、油压力
11
烟囱
排烟,并调整升温、恒温、降温速率
12
保温被
绝热用,防止热量消耗
13
钢带
固定保温被
14
防雨棚
防雨,保证热处理正常进行
15
支柱位移装置
在热胀冷缩情况下,保证支柱正常位移
3.3.2操作方法
(1)点火
a.点火准备
检查各装置正常,各项准备就绪,操作人员就位,全开烟囱蝶阀,用空气吹扫罐。
b.点火
开空压机,调压至0.2~0.3MPa,开启液化气阀门,调压至0.02~0.05MPa,向点火器送气。
c.点火时应先开液化气,后开压缩空气。
d.用单嘴预热器点着点火器;
e.调整压缩空气流量,向烧嘴供风;
f.开齿轮油泵向喷嘴供油,烧嘴喷出雾化气体,自动燃烧。
g.点火注意事项
如给油1~2分钟内点不着火,则停止供油,用空气吹2~3分钟后再行供油点火;
点火后如有喘息现象,则应降低风压或加大油量来稳定火焰。
(2)升温
a.火焰正常后,按升温曲线要求逐渐调整或加大油量、风压,逐步升温。
应注意避免升温过快。
b.升温时应注意:
△随时观察燃烧情况;
△火灭后应立即点燃,不能点燃的,停油,用空气吹2~3分钟后再行供油点火;
△因故停火,应关闭烟囱,避免温度下降过快;
△注意观察各测温点,各部温差应≤130℃。
(3)恒温
恒温的温度和时间按照升温曲线规定进行。
a.减少供油量及油压;
b.间断给油加热;
c.调整或关闭烟囱蝶阀;
d.恒温时球罐各部温差应不大于50℃。
(4)降温
规定的恒温时间达到后,降温
降温的温度和时间按照升温曲线规定进行。
(5)停火
按照升温曲线规定的停火自然冷却温度后,停火。
a.先停止供油,后停止供压缩空气(使烧嘴停烧);
b.先停止液化气,后停压缩空气(使点火器熄火);
c.停油后用压缩空气吹扫、清理油管;
d.整理装置,清理现场。
3.4.热处理中常见故障和排除
热处理中常见故障和排除见表3-2。
表3-2热处理中常见故障和排除
序号
常见故障
产生原因
排除方法
1
火焰脉动,产生爆音
燃油或雾化剂含水
排除水分
2
烧嘴孔堵塞
燃油中有杂质或沉淀物
喷嘴清洗干净,燃油过滤
3
雾化不好、火焰偏烧
喷嘴加工缺陷;油黏度过大
提高加工精度,提高油温和雾化
压力
4
火焰反喷
燃油过程中雾化剂压力突降
逐步加大雾化剂压力
4.球罐组焊的质量标准
球罐现场组焊,依据下列法规、标准:
国家质量技术监督局《压力容器安全技术监察规程》
GB150-1998《钢制压力容器》
GB12337-1998《钢制球形储罐》
GB50094-98《球形储罐施工及验收规范》
JB4730-94《压力容器无损检测》
JB4708-2000《钢制压力容器焊接工艺评定》
JB2536-80《压力容器油漆、包装、运输》
我公司编制的《压力容器制造(组焊)质量保证手册》(球罐篇)。
5.应用实例
工程名称
容积
m3
球罐直径
m
介质
球壳板数
(块)
质量
(吨)
数量
(台)
北京燃气集团小屯储配厂
10000
26
天然气
94
7000
4
咸阳天然气公司
5000
21
天然气
54
437
3
蚌埠新奥燃气公司
3500
18
天然气
54
413
2
重庆燃气公司
10000
26
天然气
94
7000
2
广东南海石化80万吨乙烯
1500m3
14.5米
丙烯
34块
345吨
8台