化工过程设计作业.docx
《化工过程设计作业.docx》由会员分享,可在线阅读,更多相关《化工过程设计作业.docx(24页珍藏版)》请在冰豆网上搜索。
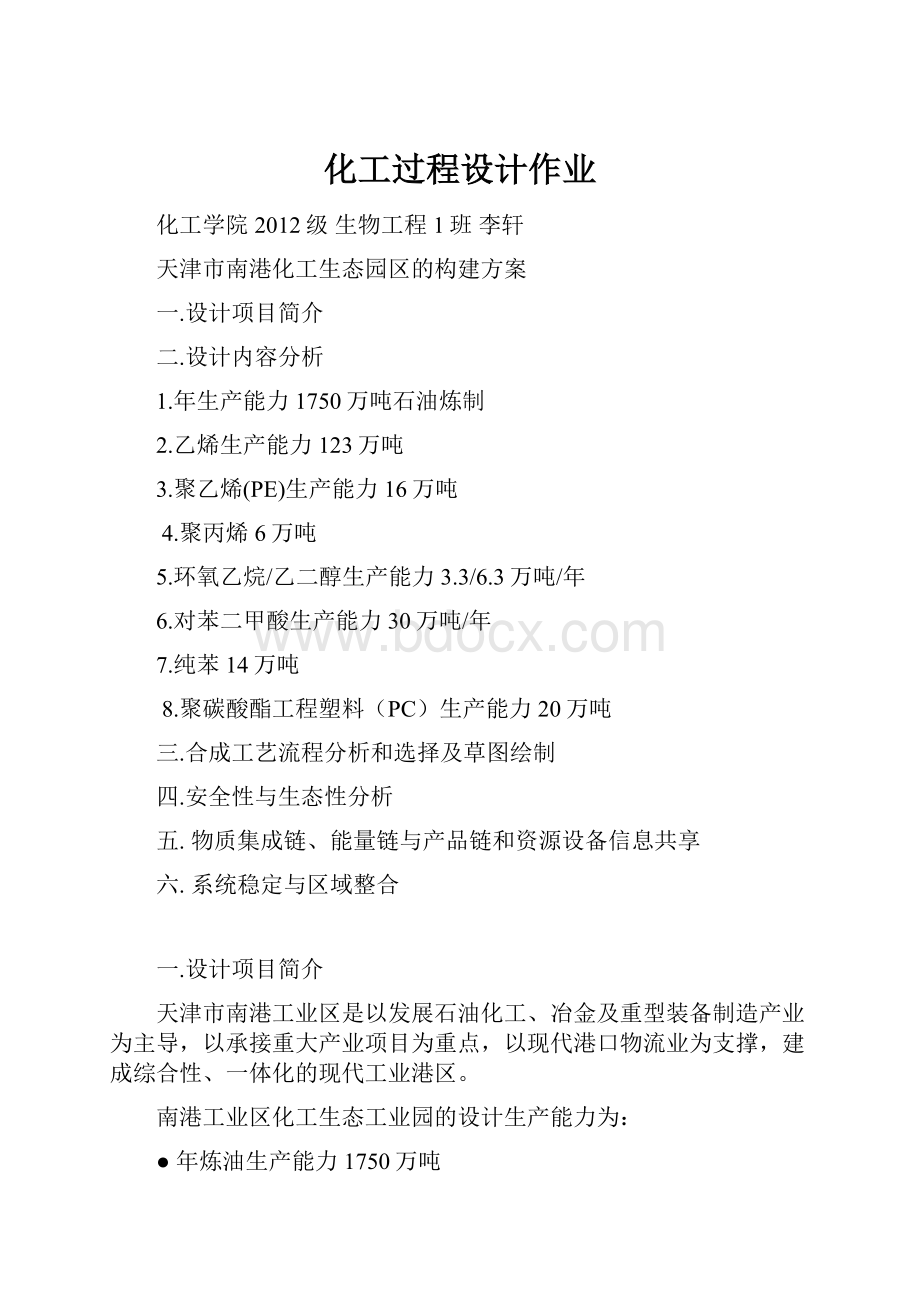
化工过程设计作业
化工学院2012级生物工程1班李轩
天津市南港化工生态园区的构建方案
一.设计项目简介
二.设计内容分析
1.年生产能力1750万吨石油炼制
2.乙烯生产能力123万吨
3.聚乙烯(PE)生产能力16万吨
4.聚丙烯6万吨
5.环氧乙烷/乙二醇生产能力3.3/6.3万吨/年
6.对苯二甲酸生产能力30万吨/年
7.纯苯14万吨
8.聚碳酸酯工程塑料(PC)生产能力20万吨
三.合成工艺流程分析和选择及草图绘制
四.安全性与生态性分析
五.物质集成链、能量链与产品链和资源设备信息共享
六.系统稳定与区域整合
一.设计项目简介
天津市南港工业区是以发展石油化工、冶金及重型装备制造产业为主导,以承接重大产业项目为重点,以现代港口物流业为支撑,建成综合性、一体化的现代工业港区。
南港工业区化工生态工业园的设计生产能力为:
●年炼油生产能力1750万吨
●乙烯生产能力123万吨
●聚乙烯生产能力16万吨
●聚丙烯6万吨
●环氧乙烷/乙二醇生产能力3.3/6.3万吨
●对苯二甲酸生产能力30万吨
●纯苯14万吨
●聚碳酸酯工程塑料(PC)生产能力20万吨
结合化工过程设计概论课程所讲内容,提出南港化工生态工业园区(优化的产业链、能量链与产品链)的构建方案,以尽可能达到节能降耗减排(二氧化碳等废气)、原子经济性(变废为宝、循环利用等)、零排放(环境友好)目标。
二.设计内容分析
不难看出,南港区化工项目是以石油炼制和石油化工为主导的,而且石油化工的原料主要是石油炼制过程中所得到的石油馏分和炼厂气。
那么我们就应该从石油炼制为起点,将炼油厂和石油化工厂进行联合,组成石油、化工联合工业园区,利用燃油厂提供的馏分油、炼厂气为原料,生产各种基本有机化工产品和三大合成材料。
1.年生产能力1750万吨石油炼制
在不同的地域出产的原油中,各组烃类含量相差较大,在同一种原油中,各组烃类在各个馏分中的分布也有很大差异。
并且原油的组成和性质对石油化工生产影响很大,对于以烯烃及其衍生物为主要产品的生产,应尽量选用富含直链烷烃的烷基原油作原料,而不宜用环烷基原油。
我国所产石油大多属于直链烷烃石油,对于提高烯烃及其衍生物生产率大有裨益。
原油一次加工
原油预处理
原油中含有少量的泥沙和铁锈等固体杂质以及水和各种油溶性盐等。
为了减少石油炼制过程中的能量消耗,稳定蒸馏塔内蒸馏操作减轻对钢质蒸馏塔的腐蚀及管路的结盐堵塞,并减少二次加工过程的影响,必须对原油进行脱盐脱水预处理。
原油的常压蒸馏
在常压下,将原有预热至200—240℃后送入初馏塔,塔顶蒸出大部分轻汽油,塔底油送至常压加热炉加热至360—370℃进入常压塔。
常压塔塔顶汽油馏分与初馏塔的轻汽油合并,称为直馏汽油,可作为催化重整生产芳烃的原料,也是裂解制取乙烯的重要原料。
从常压塔侧线出抽出其他不同沸点范围的馏分:
航空煤油馏分,轻柴油馏分,重柴油馏分。
原油的减压蒸馏
常压塔底产物是常压重油。
要想从重油中分离出裂化原料和润滑油馏分等各种高沸点馏分,且不破坏产品的质量和收率,就必须对其进行减压蒸馏,是高沸点馏分在较低的温度下汽化,以避免高沸点馏分的分解。
原油二次加工
原油的二次加工有催化裂化、加氢裂化、延迟焦化、催化重整、烷基化、油品加氢精制、电化学精制以及润滑油加工装置等。
其目的在于提高轻质油收率,提高油品质量,增加油品品种以及提高炼油厂的经济效益。
通过二次加工,主要可获得各种小分子烃类。
原油常、减压蒸馏工艺流程如图1所示。
原油三次加工
三次加工主要是件炼厂气进一步加工生产高辛烷值汽油和各种化学品的过程,包括石油烃烷基化、异构化、烯烃叠合等。
因此,我们可以考虑将炼油产和石油化工厂联合,组成石油化工联合企业,利用燃油厂提供的馏分油、炼厂气为原料,生产各种基本有机化工产品和三大合成材料。
分析
通过上面的分析,我们可以考虑使原油依次经过初馏塔、常压加热炉、常压塔、减压加热炉、减压塔,依次完成对原油的预处理、常压蒸馏和减压蒸馏,并对各馏分进行相应的产品化处理,得到直馏汽油、石脑油、航空煤油、轻柴油、重柴油、及减压渣油。
其中石脑油引到石油化工厂进行脱硫、催化重整后,可分离得到苯、甲苯、二甲苯、氢气以及重整汽油直馏煤油和直馏柴油的部分流股引出进行裂解后,也可得到苯、甲苯、二甲苯以及小分子烯烃,在后续生产过程中作为原料使用。
另外,通过对其他馏分如减压柴油、炼厂气等的二次加工可以得到各种所需的烃类产品。
乙烯生产能力123万吨
乙烯可通过直馏汽油、直馏煤油等馏分的裂解、分离处理得到。
考虑到要达到123万吨/年的乙烯生产能力,以及16万吨的聚乙烯生产能力,这意味着必须要达到乙烯的实际生产能力要达到139万吨/年。
这是一个非常大的产量,而且是在1750万吨/年的炼油能力基础上实现的。
因此,可将减压柴油进行加氢处理,然后再催化裂解生产乙烯。
另外,聚丙烯生产过程中所要用到的原料丙烯也可通过与乙烯生产类似的途径制得,只是在分离过程中的分离条件略有区别。
烃类裂解是石油系原料中的较大分子的烃类在高温下发生断链反应和脱氢反应生成较小分子的乙烯和丙烯的过程。
它包括脱氢、断链、异构化、脱氢环化、芳构化、脱烷基化、聚合、缩合和焦化等诸多反应,十分复杂,所以裂解是许多化学反应的综合过程。
一般通过烃类裂解过程的一次反应高温裂解实现乙烯和丙烯的生产,主要包括烷烃的断链反应、脱氢反应,烯烃的断链反应,以及环烷烃的开环裂解反应。
3.聚乙烯(PE)生产能力16万吨
聚乙烯树脂(PE)是通用合成树脂中产量最大的品种,在工业、农业、包装以及日常工业中具有广泛的用途。
近年来,在各工艺技术并存的同时,新技术不断涌现。
PE主要合成工艺比较详见表1。
表1列出了4种有竞争力的PE生产工艺——高压法、淤浆法、溶液法及气相法。
综合比较看出:
高压法需特别技术与设备,操作压力高(150~400MPa),投资大,近年来尽管LDPE市场受LLDPE冲击,但LDPE以其透光性、柔软性及加工性好仍具有一定竞争力,其工艺技术仍在开发之中。
淤浆法和溶液法都使用溶剂,生产成本高,生产能力受到限制。
淤浆聚合中的一些低密度聚合物在溶剂中溶解度大,溶胀后使反应体系粘度增大,导致操作困难溶液法生产高分子量产品时溶液粘度增大,搅拌困难,限制
了生产能力的提高。
气相流化床工艺由于不受溶液法中粘度的限制和淤浆法中溶解度的限制、投资和操作费用低、原料及公用工程消耗低、产品范围广、操作弹性大等优点而发展迅速,目前新建装置约70%采用气相法工艺。
这是PE工艺的发展方向。
流化床工艺可生产HDPE和LLDPE,尤其是LLDPE在主链旁生成短支链,结晶度比LDPE高,填补了HDPE和LDPE之间的性能空白带,LLDPE与LDPE相比有优异的抗刺穿性、抗冲击性及抗拉伸性能,可广泛用于薄膜,如包装、衬里膜及农膜。
另外LLDPE比LDPE抗撕裂强度高,可用于模塑及管材等领域故LLDPE在近20年来消费量增长迅速。
气相流化床工艺可生产熔融流动指数(MFI从<0.001直到>100)和密度(890~970kg/m3)范围非常宽的产品,从70年代初开始迅速成为PE主导工艺,目前(2000年),单线最大生产能力已达0.45Mt/a。
因此从上述PE工艺比较看出,气相流化床工艺是PE工艺中最具竞争力的生产工艺,也是未来的发展方向,加之采用茂金属催化剂,其市场竞争力将更强。
综合上述分析,我们可以将聚乙烯生产工艺确定为采用茂金属催化剂催化的气相流化床工艺。
4.聚丙烯6万吨
聚丙烯树脂是全球发展最快的热塑性树脂之一,全球消费量目前仅次于线形低密度聚乙烯(LLDPE)。
不断增加的市场需求不但加快了PP装置的投资建设也推动了PP技术的开发这些开发主要集中于新催化剂、新工艺和新产品的研究。
催化剂技术进展发挥先导作用
传统催化剂
传统的聚丙烯催化剂如Ziegler-Natta催化剂一直在不断发展。
Z/N催化剂近期的主要发展是拓宽Z/N催化剂体系的产品范围和开发给电子体系。
主要表现在如下方面:
能够在反应器中不经减黏裂化得到高熔融流动指数(MFR)的产品;通过改进催化剂,提高聚合物的结晶性和等规度;生产刚性更好的产品;降低产品的热封温度;改进光学性能;采用两段聚合双峰树脂生产技术使聚丙烯树脂的分子量分布更宽,使产品具有最优的刚性和抗冲击性能的综合性能;用两个均聚反应器组成的反应器体系可以生产分散度为3.2~10的产品;产品的挠曲模量可以达到2300MPa以上。
另外,传统Z/N催化剂和茂金属的混合催化剂体系也将有所发展,目前的主要发展是在单个反应器中生产双峰分布或多峰分布的树脂,工艺更容易控制,分子量分布更稳定共聚产品的柔韧性更好。
茂金属催化剂
茂金属催化剂是20世纪90年代以来最受关注的烯烃聚合催化剂。
茂金属催化剂的工业化为生产物理机械性能明显改进的聚丙烯树脂创造了条件如可生产超刚性等规聚丙烯、高透明的间规聚丙烯、等规聚丙烯和间规聚丙烯的共混物及超高性能的聚丙烯抗冲共聚物。
非茂金属单活性中心催化剂
近几年才开始发展的非茂金属单活性中心催化剂由于具有合成相对简单,产率高且有利于降低催化剂成本,可以生产多种聚烯烃产品的特点,预计将是今后若干年的研究热点。
聚合工艺向简化流程方向发展
自1957年聚丙烯商业化投产以来,聚丙烯催化剂和工艺技术的进步及产品应用的不断开发,使聚丙烯成为全世界范围内最有活力的聚合物之一。
在70~80年代开发了高活性和高等规度的催化剂,使聚丙烯工艺技术得到很大发展,简化了流程,省去了脱除催化剂残渣和副产品无规聚合物等工序。
同时催化剂和工艺技术等各方面的改进使装置的投资和生产成本不断下降,企业效益不断改善,世界上许多聚丙烯工业公司都发展了自己的专有技术。
PP生产工艺主要分为淤浆法,本体法、气相法及液相本体和气相相结合的工艺。
在20世纪80年代前,占主导地位的PP工艺是溶剂淤浆聚合工艺,但目前溶剂淤浆法由于工艺长,操作复杂和能耗高等原因已被逐渐淘汰,而气相和本体法显现了旺盛的生命力。
近几年新上的PP装置几乎90%以上都是气相和本体聚合工艺,而这些气相和本体聚合工艺新的发展趋势就是大型化,目前各工艺大都接近40×10t/a的生产能力;另一个就是不断优化工艺流程、设备布置和控制系统使工艺投资更低、产品质量更好,产品单耗和能耗更低。
下面表2是对几种典型工艺及其最新进展进行分析。
生产装置大型化减低能耗和最大限度生产高性能化的产品,是PP成套技术的发展方向。
因此考虑到提高生产能力,进一步减低PP产品的能耗和单耗,降低生产成本,提高工艺的市场竞争力,以及技术上可行、工艺上合理、确保健康、安全、环保的基础上,宜选用气相本体法进行合成。
5.环氧乙烷/乙二醇生产能力3.3/6.3万吨/年
环氧乙烷合成
工业上生产环氧乙烷有两种方法,其一是氯醇法,其二是乙烯直接氧化法。
氯醇法于70年代在世界范围内已被淘汰,目前只有少数发展中国家有少量生产。
乙烯直接氧化法又分为空气氧化法及氧气氧化法,由于氧气氧化法具有环氧乙烷收率高,成本低,装置投资少等优点,逐渐取代了空气氧化法而成为占绝对优势的工业生产环氧乙烷方法。
因此,在这里,考虑到绿色环保的因素,我们直接排除对氯醇法的考虑,使用氧气氧化法进行生产。
考虑到后面乙二醇的生产是以环氧乙烷为原料进行的,故应使环氧乙烷的年生产能力达到7.8万吨。
乙烯气化过程可分为深度氧化及有选择性的氧化两种反应,前者直接生成二氧化碳和水,后者可有选择地氧化成环氧乙烷,所适用的催化剂为银。
在银催化剂作用下乙烯有选择性地发生氧化反应其主副反应如下:
乙烯氧化是强放热反应,尤其深度氧化反应,为选择性氧化反应放热的十多倍。
因此催化剂的选择性非常重要,否则会因副反应进行而引起操作条件的恶化,甚至变得无法控制,造成反应器“飞温”事故。
在乙始直接氧化制环氧乙烷的生产工艺中原料乙烯消耗占环氧乙烷生产成本的2/3,因此,降低乙烯消耗,或者说提高催化剂的活性和选择性是提高过程经济效益的最有效手段。
因此致力于银催化剂的研究,包括活性组分、制造方法、载体、测试评价方法等一直是非常活跃的领域。
乙二醇合成
乙二醇是石油化工的重要原料,是乙烯的重要衍生物之一,也是二元醉中产量最大的产品,其用途很广泛,是生产合成纤维、塑料、油漆、胶黏剂、表面活性剂、炸药等产品不可缺少的物质,也可直接用作溶剂、防冻剂等。
生产乙二醇有很多途径,可采用不同的原料和不同的方法进行生产,通常以乙烯和合成气为原料。
以乙烯为原料常通过化学反应转化为二氯乙烷、氯乙醇、环氧乙烷、乙二醇单醋酸酯,乙二醇二醋酸酯等物质,通过它们的水解即可得乙二醇。
亦可由合成气(CO,H2)通过化学反应生成乙二醇。
由乙烯直接氧化生产环氧乙烷,再由环氧乙烷催化水合生产乙二醇的方法是目前世界各国普遍采用生产乙二醇的方法。
但这条工艺路线由于乙烯氧化生成环氧乙烷的选择性较低,使乙烯的消耗定额高,而且进一步提高选择性的困难较大。
因而随着合成纤维及塑料生产的迅速发展,对乙二醇需要量的不断增加,同时也由于石油资源的限制及石油价格的上涨,促进了以合成气为原料生产技术的开发,从目前研究情况看,许多合成乙二醇的过程均可与传统的乙烯直接氧化再水合的工艺相争。
结合本生产项目的实际,在前面的工艺步骤中已经制备出环氧乙烷,因此考虑直接以环氧乙烷为原料,直接水合生产乙二醇。
在液相中,环氧乙烷与水反应即可生成乙二醇:
在通常条件下,此反应进行得很慢,无工业价值,要使反应较快进行,就必须升温或使用催化剂。
目前环氧乙烷催化水合生产乙二醇的方法主要有:
液相酸催化水合法,阳离子交换树脂水合法,加压水合法等。
6.对苯二甲酸生产能力30万吨/年
对苯二甲酸(TA)是一种重要的、具有广阔应用前景的基础化工原料,广泛应用于化工和聚酯工业生产中。
TA工业上传统生产方法主要以对二甲苯为原料、金属卤化物为催化剂的液相空气氧化技术,但此技术会产生重金属污染物,且卤化物腐蚀设备。
20世纪50年代以来,国外相继开发了几种非硝酸氧化法合成TA的新工艺,例如英国诺丁汉大学与杜邦聚酯技术公司合作,开发了在超临界水中从对二甲苯生产TA的连续法绿色工艺。
下面首先就当前主要的对苯二甲酸的合成方法作简要说明。
上述合成方法中,有几种是以对二甲苯为原料的合成TA方法,还有几种是以其它原料合成TA的方法。
其中液相氧化法技术已日趋成熟,是现在主要工业生产方法,缺点是使用了有毒催化剂,不符合绿色化学标准。
加氢精制法特点是溶剂损失很小,能有效控制结晶的粒径大小,生产成本较低,产品质量稳定。
该方法是目前世界上TA生产的主要方法,目前装置产能占世界TA总量的80%以上。
精密氧化法的缺点是溶剂醋酸(HAc)的消耗量比较大。
其生产的MTA用于生产聚酯,对聚合反应要求较高,要添加某些助剂来封闭醛基。
超临界法使用无毒溶剂代替环境不友好的有机溶剂,是实现绿色化学的有前景的方法之一。
以前对合成TA的经济性评估有又很多,Jennifer等对高温水中合成对苯二甲酸的经济性和环保性做了最新评估。
结果显示这两种方法的总投资基本相同。
但由于高温水氧化法可以减少污染物(如溴)的排放,所以它作为乙酸法合成对苯二甲酸的替代法前景非常乐观。
消极的方面,基于超临界水的过程涉及高温水,需要动力成本消耗,还存在反应器材料的腐蚀问题,而且如果将这个过程用于商业目的,需要进一步研究,必须使得对苯二甲酸的收率高于文献报道的值。
生物酶氧化法优势在于在相对温和的条件下进行且几乎不产生废物,前景非常乐观,但需要克服一些技术上的困难。
现行合成TA所用的无机催化剂都是在高温高压的操作条件下,而且产生大量的重金属废物。
而酶氧化法在相对温和的条件下进行且几乎不产生废物。
但生物转化对二甲苯的现行系统还不能工业化,它存在两个缺点:
1)理论上的限制就是对二甲苯的第二个甲基不能被氧化,过氧化氢会减弱CPO的活性:
2)系统中的对二甲苯在水中的溶解度小。
目前的研究表明这些技术上的困难在将来有可能被克服。
本项目中要实现对苯二甲酸年产量30万吨的设计,本着经济合理并且绿色环保的设计要求,宜选择加氢精制法进行合成。
该工艺以石油炼制二次加工裂解抽提出的对甲苯为原料,分为粗对苯二甲酸生产(即图2中的步骤3a)及其精制(即图2中的步骤4)两部分。
它是以Co2+-Mn2+-Br—为催化剂,乙酸为溶剂,空气为氧化剂,将对二甲苯氧化成对苯二甲酸。
在对二甲苯生成TA同时,还产生了一部分副产品,如4—羧基苯甲醛(4-CBA)、对甲苯甲酸、苯甲酸和间苯二甲酸等,所有这些杂质除4-CBA以外都经过结晶、过滤处理除掉。
精制段是以水为溶剂,将杂质4-CBA加氢催化转化成产品TA。
由于加氢精制法成为合成对苯二甲酸的主要工业方法,所以一直以来人们致力于对此法的反应条件和催化剂的研究,因此在技术上、设备上更加成熟可行。
纯苯14万吨
苯是重要的石油化工原料,产量大,来源广泛。
现在工业上有多种生产苯的方法,其一为煤炼焦过程副产的轻焦油,历史上曾是唯一的工业来源,随着苯的需要量增加,石油苯的出现,煤焦油苯已降为次要地位。
原油中仅含有少量的苯及其它芳烃,没有分离的价值,石油必须经各种加工后才能得到含苯等芳烃的馏分,再经分离提纯得到高纯度的苯。
其中最主要的方法是催化重整过程及由石油馏分裂解生产乙烯过程副产焦油分离苯。
石油芳烃是目前及将来相当长时期内苯的主要来源,其中以催化重整生产芳烃为主要工艺。
但催化重整生成的芳烃中苯的收率较低,甲苯及二甲苯的收率较高,催化重整的发展规模常受到直馏汽油供应量的限制。
因此,各炼油厂多利用二次加工汽油加氢处理后作为催化重整的原料以扩大其原料来源,以期增产芳烃。
与此同时在连续催化重整技术的基础上催化芳构化技术应运而生,其特点是可以利用丙烷、丁烷等轻质烃、以及劣质油品生产芳烃,从而大大扩大了石油芳烃的原料来源。
其次是乙烯工厂的副产裂解焦油,其中苯含量较其它芳烃高。
生产乙烯的原料和裂解条件不同,乙烯收率不同,裂解焦油的组成以及苯等芳烃收率也不同。
因此,苯的来源和规模受到乙烯装置裂解原料的制约。
裂解焦油组成复杂,含不饱和化合物较多,必须经过加氢才能作为进一步分离芳烃或脱烷基制苯的原料。
苯和二甲苯是芳烃中需要量较大的产品,甲苯则较少,因此甲苯脱烷基歧化将其转化为苯和二甲苯,满足了市场的需要。
甲苯脱烷基制苯有热脱烷基法与催化脱烷基法。
热脱烷基法反应温度较高,过程无需催化剂,空速大、反应器体积小,运转周期长,可达一年以上,对原料的适应性强,允许原料中芳烃含量可低达30%,补充氢的杂质含量不受限制,氢耗低,产品苯的纯度高,因此较催化脱烷基优越,广泛被采用。
甲苯歧化及烷基转移虽增加二甲苯的收率,但却减少了苯的收率,因此要考虑二者间的供需平衡,实现本项目中苯的生产需求和对苯二甲酸生产过程中对二甲苯的需求。
聚碳酸酯工程塑料(PC)生产能力20万吨
聚碳酸酯(Polycarbonate,简称PC)作为一种综合性能优良的热塑性工程塑料,具有突出的抗冲击性能、耐蠕变性能、较高的抗张强度、抗弯曲强度、伸长率和刚性,并具有较高的耐热性和耐寒性,可在-100℃~140℃温度范围内使用,电性能优良、吸水率低、透光性好。
由于性能优异,其应用领域非常广泛,已进入到汽车、电子电气、建筑、办公设备、包装、运动器械、医疗保健、家庭用品等领域,而且正迅速地扩展到航空、航天、电子计算机、光盘等高新技术领域,尤其在光盘的应用上发展更快。
PC工业化生产工艺主要分为两大类。
第一类是使用光气的生产工艺。
第二类是完全不使用光气的生产工艺。
截止2004年底,全世界PC总生产能力接近3.0Mt/a。
其中,光气法PC生产工艺约占总生产能力的90%。
除美国GE公司少部分生产装置(生产能力约170kt/a)和中国台湾奇美公司65kt/a生产装置外,世界其他PC生产装置全部使用光气作为生产原料。
但该方法要使用剧毒的光气(COCl2),而且还有许多环境和经济方面的不足,不符合环境保护与可持续发展的社会潮流。
近年来,全世界环境保护呼声日益高涨,各国都相继颁布了更为严厉的环保法规,相应的排放标准也更为苛刻,光气法必然会被逐渐淘汰。
因此,发展一种环境友好、经济效益高的合成方法,成为绿色化学迫切需要解决的问题。
作为南港化工生态工业园区新上马的年产20万吨超大规模双酚A型聚碳酸酯项目,环保问题不容忽视。
本着技术可行、经济合理、环境友好以及安全生产的宗旨,我们应该选取更为绿色的非光气法生产工艺。
下面就对非光气法生产工艺作简要阐述。
以碳酸二甲酯(DMC)和苯酚作为原料生产DPC,可以完全避免使用剧毒的光气。
反应式如下所示:
反应在串连的双塔中进行。
苯酚从第一塔的中上部进料,新鲜的DMC以及从第二塔循环回来的部分物料混合后在中下部进料,通过反应精馏,在第一塔的底部采出甲基苯基碳酸酯进入第二塔中部,甲醇和少量DMC由第一塔上部蒸出。
在第二塔中,甲基苯基碳酸酯经过自身的酯交换反应,生成的DPC由塔底抽出,DMC从塔顶抽出后循环回第一塔重新参加反应。
其中DPC的原料DMC工业化生产工艺主要有酯交换法和甲醇羰基氧化法。
酯交换法是以CO2为原料生产PC的工艺流程:
先以CO2、环氧乙烷为原料,在气相条件下,通过高压和催化剂作用生产碳酸乙烯酯(EC),然后EC和甲醇进行酯交换反应生产DMC。
DMC再和苯酚进行酯交换反应生产DPC,副产物乙二醇可以作为聚合级PC原料出售。
反应式如下所示:
该工艺已有生产能力约65kt/a的工业装置(2006年,以DMC计),原料CO2可以是环氧乙烷/乙二醇(EO/EG)装置的副产物。
除此之外,乙二醇通过此方法生产,与传统的蒸馏提纯工艺相比,可以节约大量蒸汽耗量。
非光气法PC工艺完全摆脱使用剧毒的光气作为生产原料。
同时聚合阶段采用本体聚合,不用溶剂,主要原料是CO(来自气化装置)、CO2(来自乙二醇排放气),具有成本低、容易得到等优点。
主要缺点是,由于后期的熔融缩聚反应时体系黏度逐渐增大。
导致体系中小分子物质排放困难,因此设备较复杂,工艺操作要求高。
甲醇羰基氧化法是以CO和甲醇为原料,通过甲醇羰基氧化法生产DMC。
甲醇羰基氧化法的成熟工艺有意大利Enichem公司的液相催化工艺和日本宇部公司气相催化工艺,催化剂分别是CuC12和CuC12、NO。
液相工艺的主要缺点是设备腐蚀问题,甲醇最大转化率98%;气相工艺是20世纪90年代的新技术,甲醇转化接近100%。
GE公司的非光气法PC装置采用以CO为原料合成DMC的工艺,然后再合成DPC,最后通过DPC和双酚A熔融缩聚反应生产PC。
综合考虑项目生产实际以及绿色生产的要求,我们决定应该采用非关起发进行生产。
以碳酸二甲酯(DMC)和苯酚作为原料生产DPC,而DMC的生产工艺宜采用酯交换法进行,这样可以充分利用前面环氧乙烷的合成。
三.合成工艺流程分析和选择及草图绘制
下面对各产物的合成工艺逐个列出。
四.安全性与生态性分析
生态工业技术的开发应该遵循减量化原则、再利用原则、再资源化原则这三个原则。
减量化原则注重将产品灵活化,根据消费的功能需求来优化产品结构,开发出性能更好、更加“灵巧”的产品或技术,以此减少资源和能源的消耗。
在减量化原则中,要遵循物质转化中低物耗、低能耗工艺优先的原则,使资源的利用率达到最高。
再利用原则指的是重要元素在工业系统中的循环代谢。
如通过化学加工,将副产物分解进行资源循环利用。
再资源化原则是针对废弃物的回收利用而言。
所以一个生态化工项目或者园区的“静脉产业”建设是十分重要的,“谁制造,谁分解;谁销售,谁回收;谁污染,谁治理”等理念的推进是十分必要的。
所谓静脉产业,即资源再生利用产业,是以保障环境安全为前提,以节约资源、保护环境为目的,运用先进的技术,将生产和消费过程中产生的废物转化为可重新利用的资源和产品,实