第四章 材料切削加工基础1.docx
《第四章 材料切削加工基础1.docx》由会员分享,可在线阅读,更多相关《第四章 材料切削加工基础1.docx(28页珍藏版)》请在冰豆网上搜索。
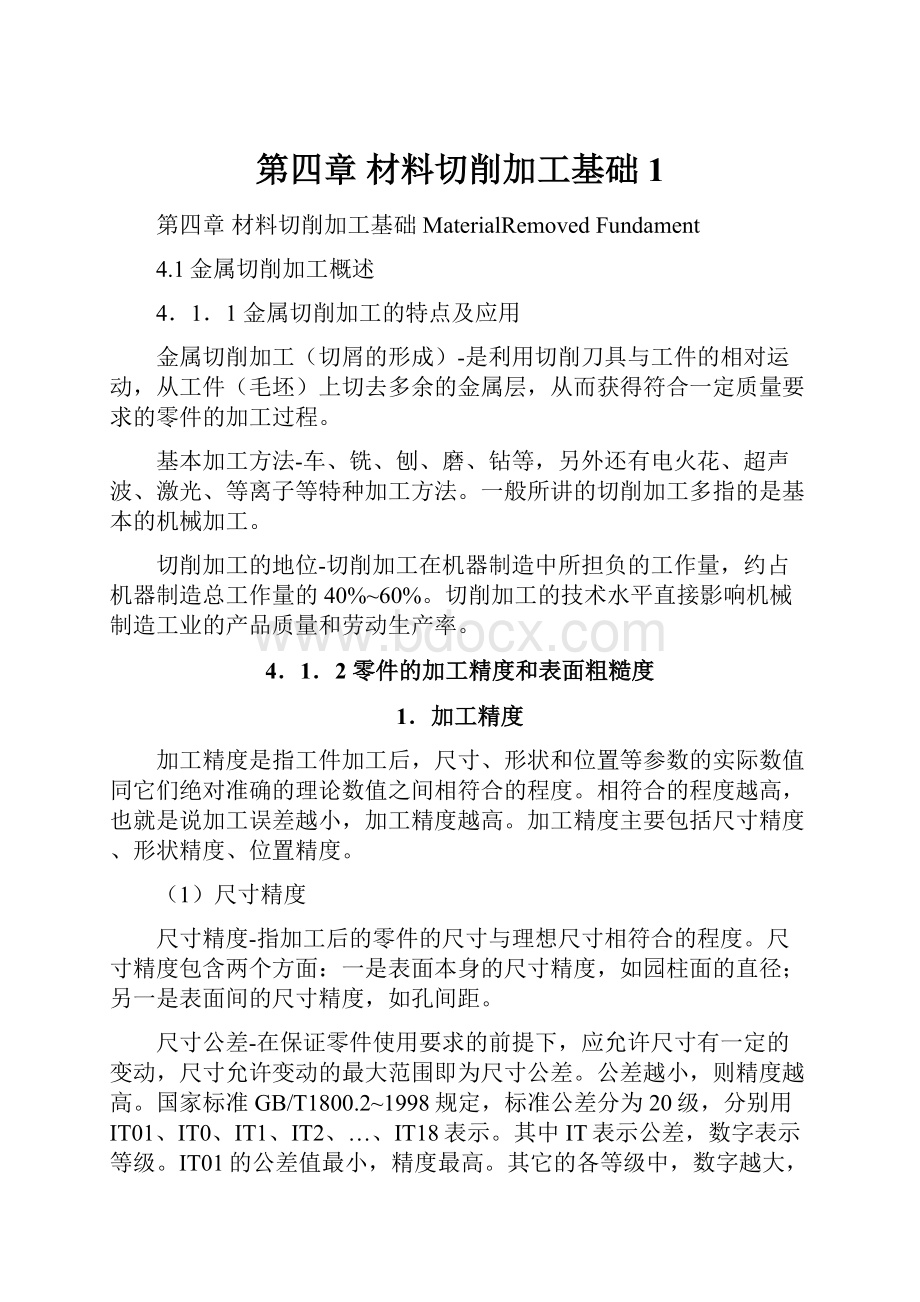
第四章材料切削加工基础1
第四章材料切削加工基础MaterialRemovedFundament
4.1金属切削加工概述
4.1.1金属切削加工的特点及应用
金属切削加工(切屑的形成)-是利用切削刀具与工件的相对运动,从工件(毛坯)上切去多余的金属层,从而获得符合一定质量要求的零件的加工过程。
基本加工方法-车、铣、刨、磨、钻等,另外还有电火花、超声波、激光、等离子等特种加工方法。
一般所讲的切削加工多指的是基本的机械加工。
切削加工的地位-切削加工在机器制造中所担负的工作量,约占机器制造总工作量的40%~60%。
切削加工的技术水平直接影响机械制造工业的产品质量和劳动生产率。
4.1.2零件的加工精度和表面粗糙度
1.加工精度
加工精度是指工件加工后,尺寸、形状和位置等参数的实际数值同它们绝对准确的理论数值之间相符合的程度。
相符合的程度越高,也就是说加工误差越小,加工精度越高。
加工精度主要包括尺寸精度、形状精度、位置精度。
(1)尺寸精度
尺寸精度-指加工后的零件的尺寸与理想尺寸相符合的程度。
尺寸精度包含两个方面:
一是表面本身的尺寸精度,如园柱面的直径;另一是表面间的尺寸精度,如孔间距。
尺寸公差-在保证零件使用要求的前提下,应允许尺寸有一定的变动,尺寸允许变动的最大范围即为尺寸公差。
公差越小,则精度越高。
国家标准GB/T1800.2~1998规定,标准公差分为20级,分别用IT01、IT0、IT1、IT2、…、IT18表示。
其中IT表示公差,数字表示等级。
IT01的公差值最小,精度最高。
其它的各等级中,数字越大,则公差等级越高,相应的精度也就越低。
一般IT01~IT13用于配合尺寸,其余的用于非配合尺寸。
(2)形状精度
形状精度是指零件上的各形状要素与理想形状要素的符合程度。
当零件的尺寸精度满足要求时,并不意味着其形状也符合要求。
如加工一个
的轴,其实际尺寸为24.95,符合精度要求。
但轴的某一截面的实际形状不是理想的圆形,故其形状不一定满足要求。
关于形状误差方面,其表达符号及相应的含义详见表4-3
表4-3形状公差
名称
符号
含义简介
直线度
零件被测要素直线(如轴线、平面交线等)与理想直线的符合程度
平面度
零件被测要素平面表面的凹凸不平程度
园度
回转体零件的横剖面上的实际轮廓与理想园形的符合程度
园柱度
园柱轮廓表面的实际形状与理想园柱相差的程度
线轮廓度
零件上被测的实际轮廓线与理想轮廓线相差的程度
面轮廓度
零件上被测的实际轮廓面与理想轮廓面相差的程度
(3)位置精度
位置精度是指零件上的表面、轴线等的实际位置与理想位置相符合的程度。
零件加工时应允许有一定的误差,国家标准GB/T1182-1996、GB/T4249-1996、GB/T16671-1996规定了3类共8种标准位置公差,其表达符号及相应的含义详见表4-4。
表4-4位置公差
类别
名称
符号
含义简介
定
向
平行度
零件上被测要素(面或直线)与基准要素平行的程度
垂直度
零件上被测要素(面或直线)与基准要素垂直的程度
倾斜度
零件上被测要素(面或直线)与基准要素有一定的倾斜,实际倾斜的程度与理想倾斜的程度的差值
定
位
同轴度
被测回转面的轴线与基准轴线相重合的程度
对称度
被测要素(平面、轴线、直线)相对于基准要素对称的程度
位置度
被测要素(点、线、面)的实际位置与理想位置偏离的程度
跳
动
园跳动
被测的回转表面相对于以基准轴线为轴线的理论回转面的偏离程度。
根据测量方向的不同,有端面、径向、斜向园跳动
全跳动
含义与园跳动相似,不同的是反映整个表面的跳动。
有端面、径向两种
2.表面粗糙度
无论用何种方法加工,在零件表面总会留下微细的凹凸不平的刀痕,出现交错起伏的现象。
粗加工后的表面用肉眼就能看到,精加工后的表面用放大镜或显微镜仍能观察到。
表面上微小峰谷间的高低程度称为表面粗糙度,也称微观不平度。
yp1
y
国家标准GB/1031-1995规定了表面粗糙度的评定参数和评定参数允许数值系列。
常用参数是轮廓算术平均偏差Ra和微观不平度十点高度Rz,其含义分别见图4-1、图4-2。
或近似地
或近似地
表面粗糙度对零件的疲劳强度、耐磨性、耐腐蚀性、配合性能等方面均有很大影响。
表面粗糙度的值越小,零件的表面质量越高,但零件的加工也越因难,加工成本也越高。
因此在设计零件时,应根据实际情况合理选用,即在满足技术要求的条件下,尽可能选用较大的值。
表4-5列出了不同加工方法所能达到的表面粗糙度,供选用时参考。
表4-5表面粗糙度选用举例
加工方法
表面粗糙度参数(Ra/μm)
表面状况
应用举例
粗车、镗、刨、钻
100
明显可见的刀痕
如粗车、粗刨、切断等粗加工后的表面
25.5
粗加工后的表面,焊接前的焊缝、粗钻也壁等
粗车、铣、刨、钻
12.5
可见刀痕
一般非结合表面,如轴的端面、倒角等
车、镗、刨、铣、钻、锉、磨、粗铰、铣齿
6.3
可见加工痕迹
不重要零件的非配合表面,如支柱、支架、外壳等的端面。
紧固件的自由表面、紧固件通孔的表面等。
车、镗、刨、铣、拉、磨、锉、滚压、铣齿、刮1~2点/㎝2
3.2
微见加工刀痕
与其它零件连接,但不形成配合的表面。
如箱体、外壳等的端面。
车、镗、刨、铣、拉、磨、铰、滚压、铣齿、刮1~2点/㎝2
1.6
看不清加工刀痕
安装直径超过80㎜的G级轴承的外壳孔、普通精度齿轮的齿面、定位销孔等重要表面。
车、镗、拉、磨、立铣、滚压、刮3~10点/㎝2
0.8
可辨加工痕迹的方向
要求保证定心及配合特性的表面。
如锥销与园柱销的表面,磨削的轮齿表面、中速转动的轴颈等。
铰、磨、镗、拉、滚压、刮3~10点/㎝2
0.4
微辨加工痕迹的方向
要求长期保持配合性质稳定的配合表面。
如IT7级的轴、孔配合表面,精度较高的轮齿表面等。
布轮磨、磨、研磨、超级加工
0.2
不可辨加工痕迹的方向
工作时受变应力作用的重要零件的表面。
保证零件的疲劳强度、防腐性和耐久性,并在工作时不破坏配合性质的表面。
超级加工
0.1
暗光泽面
工作时承受较大变应力作用的重要零件的表面。
保证精确定心的锥体表面等
0.05
亮光泽面
保证高度气密性接合的表面。
如活塞、柱塞和汽缸内表面等
0.025
镜状光泽面
高压柱塞泵中柱塞和柱塞套的配合表面等精密表面
0.012
雾状光泽面
仪器的测量表面和配合表面,尺寸超过100㎜的块规工作面
0.008
镜面
块规的工作表面,高精度测量仪器的测量面及其磨擦机构的支承表面
4.1.3切削用量及选用
1.切削要素
切削要素包括切削用量三要素和切削层几何参数。
切削用量三要素-指切削速度vc、进给量f、背吃刀量ap,其数值的大小反映了切削运动的快慢和刀具切入工件的深浅。
切削速度vc—切削刃上选定点相对于工件主运动的瞬时速度,单位为m/s。
若主运动为旋转运动(图2-1),切削速度一般为其最大线速度。
计算公式为:
(m/s)
式中D—工件待加工表面的直径或刀具的最大直径(㎜)
n—主运动的转速(r/s)
若主运动为往复直线运动(图2-2),则以其平均速度为切削速度,其计算公式为:
(m/s)
式中l–往复运动行程长度(㎜)
–主运动每秒往返次数(str/s)
●进给量f—工件或刀具运动的一个循环(或单位时间)内,刀具在进给方向上相对工件的位移量。
可用刀具或工件每转或每行程的位移量来表述和度量
例如车削时(图2-3),工件每转一转,车刀沿工件轴线方向移动的距离即为进给量,单位为㎜/r,称为每转进给量。
刨削时,刀具每往复一次,工件移动的距离即为进给量,单位为㎜/str,称为每行程进给量。
铣平面时,铣刀每转一齿或一分钟,工件沿进给方向移动的距离,分别称为每齿进给量(㎜/z)、每分钟进给量(㎜/min)。
●背吃刀量ap—如图2-3所示,车外园时,工件在切削加工过程中形成了三个表面,分别为:
待加工表面(工件上即将被切削的表面)、已加工表面(工件上已切去切屑后留下的表面)、加工表面(工件上正被切削刃切削的表面,也就是待加工表面与已加工表面间的过渡表面)。
待加工表面与已加工表面之间的垂直距离,即为背吃刀量,单位为㎜。
ap值的大小直接影响主切削刃的工作长度,反映了切削负荷的大小。
对于外园车削来说
式中D、d分别为工件待加工表面直径与已加工表面的直径。
切削层-切削时,切削刃正在切削的这层金属。
其几何参数指切削厚度、切削宽度、切削面积,见图2-3。
●切削厚度hD—刀具或工件每移动一个进给量的距离后,刀具切削刃相邻两个位置间的垂直距离,单位为㎜。
车外园时,
(㎜)
●切削宽度bD—沿主切削刃所量得的待加工表面与已加工表面间的距离,即切削刃与工件接触的长度,单位为㎜。
车外园时,
(㎜)
●切削面积AD—垂直于主运动方向上切削层的截面面积,即背吃刀量和进给量的乘积,或切削宽度与切削厚度的乘积,单位为㎜2。
车外园时,AD=bD×hD=ap×f(㎜2)。
2.切削用量的选择原则
粗加工阶段:
以提高生产率为主,因此应尽可能多地切除加工余量,在选择合理的刀具耐用度后,把背吃刀量选得大些,其次选择较大的进给量,最后确定合适的切削速度;对于有硬皮的铸件、锻件的第一刀加工,其背吃刀量应大于硬皮厚度;
精加工阶段:
为保证工件获得需要的尺寸精度和表面粗糙度,应选择较小的进给量和背吃刀量,较高的切削速度。
只有在受到刀具等工艺条件限制不能使用较高切削速度时,才考虑选用较低的切削速度。
●背吃刀量的选择:
不论是粗加工还是精加工,最佳方法是一次走刀就能完成切削加工。
但当切削余量较大时,切削力较大,这时就会由于机床功率、刚度、刀具强度等方面的不足而无法一次完成。
因此,生产中往往需要多次走刀,第一次走刀的背吃刀量,应在机床工艺系统的承受能力范围内尽可能取大值,其后的背吃刀量相对的可取小些。
●进给量的选择:
当选定背吃刀量后,切削力的大小主要受进给量的影响。
因此,粗加工时,由于对加工表面质量的要求不高,可在工艺系统允许的范围内尽可能取大值。
精加工时,为减小切削力,同时保证较高的表面质量,宜选择较小数值。
●切削速度的选择:
在选定了背吃刀量及进给量后,可根据合理的刀具耐用度,用计算法或查表法选择切削速度。
粗加工时,若所选的切削速度较大,使得切削功率超过机床承受能力,这时应适当降低切削速度。
4.1.4切削刀具
1.常用刀具切削部分材料
目前机械加工中常用的刀具切削部分的材料主要有:
碳素工具钢、合金工具钢、高速钢、硬质合金及陶瓷材料等
●碳素工具钢
是一种含碳量较高的优质钢(含碳量一般为0.7%~1.3%)。
其优点是淬火后硬度较高,可达60~66HRC,刃磨容易,价格低廉,但不能耐高温,在200~250℃时即开始失去原来的硬度,所以切削速度不能太高。
热处理时,淬透性差、变形大、易产生裂纹,所以不宜用来制造复杂的刀具。
常用的牌号主要有T10A、T12A等,多用于制造锯条、锉刀等手工工具。
●合金工具钢
在碳素工具钢中加入一定的铬(Cr)、钨(W)、锰(Mn)等合金元素,能够提高材料的耐热性、耐磨性和韧性,同时还可减小热处理时的变形,淬火后具有较高的硬度(60~66HRC)。
其含碳量一般为0.85%~1.5%,能耐350~400℃的高温,常用的牌号为9SiCr、CrWMn等。
由于具有刃磨容易、热处理性能好、工艺性能好等优点,常用于制造丝锥、板牙、铰刀等形状复杂、切削速度较低(v<0.15m/s)的刀具。
●高速钢
又称锋钢、白钢,含有较多的钨、铬、钼、钒等合金元素。
常用牌号为W18Cr4v和W6Mo5Cr4V2,能耐550~600℃的高温。
与前面的工具钢相比,高速钢的耐磨性、耐热性有显著的提高。
与后面的硬质合金相比,具有较高的抗弯强度和抗冲击韧性,工艺性能、热处理性能也较好,容易刃磨锋利。
因此,常用于制造钻头、铣刀、拉刀和齿轮刀具等形状复杂的刀具。
由于耐热性不高,多用于切削速度不高的场合(v<0.5m/s),是目前使用最广的刀具材料之一。
●硬质合金
由耐磨性和耐热性都很高的碳化物(WC、TiC等)粉末,用Co、Mo、Ti等做粘结剂烧结而成。
硬度可达74~82HRC,耐温高达850~1000℃,故可用于高速切削(1.5~5m/s)。
但与高速钢相比,其抗弯强度较低、承受冲击能力较差、刃口也不能太锋利。
硬质合金也是目前国内使用最广泛的刀具材料之一,常制成各种形式的刀片,焊接或夹固在车刀、刨刀等刀具的刀柄上使用。
常用的硬质合金有三类:
1、由WC和Co组成的钨钴类(YG类);2、WC、TiC和Co组成的钨钴钛类(YT类);3、在钨钴钛类硬质合金中添加少量碳化钽(TaC)或碳化铌(NbC)而成的通用硬质合金(YW类)。
目前国产的硬质合金主要为前两类。
YG类硬质合金抗弯强度和韧性较好,适于铸铁、青铜等材料的加工。
常用牌号有YG8、YG6、YG3等,其中数字表示Co含量的百分比。
Co含量少,则较脆、耐磨性好,适用于精加工。
粗加工时宜选用含钴量较多的型号,如YG8。
YT类硬质合金比YG类硬质合金硬度高,耐热性好,适于加工钢材等塑性材料。
常用牌号有YT5、YT15、YT30等,其中数字代表TiC含量的百分比。
TiC含量越高,则韧性越低、耐磨性越高,适用于精加工。
粗加工中则应用TiC含量少的硬质合金,如YT5。
YW类硬质合金的韧性、与钢粘附的温度比YT类硬质合金高。
既可用于加工铸铁等脆性材料,也可用于加工钢类等塑性材料,还可加工高温合金、不锈钢等难加工钢材。
其牌号主要有YW1与YW2两种,前者用于精加工,后者用于粗加工。
各类常用的刀具材料的主要性能和用途见表4-6
表4-6刀具材料主要性能表
种类
硬度
承受最高温度(℃)
抗弯强度MN/㎡
工艺性能
用途
碳素工具钢
60~66HRC
(81.5~84.5HRA)
~200
2500~2800
可冷热加工成形,刃刃性能好,需热处理
用于手动工具,如锯条、锉刀等
合金工具钢
60~66HRC
(81.5~84.5HRA)
250~300
2500~2800
同上
用于低速、成形刀具,如丝锥、板牙等
高速工具钢
63~70HRC
(83~87HRA)
550~600
2500~4500
同上,但钡类差
用于钻头、铣刀、车刀等
硬质合金
89~94HRA
800~1000
1000~2500
压制烧结后使用,不能冷热加工,多镶片使用
用于车刀刀头、铣刀等
陶瓷材料
94HRA
900~1200
500~700
同上
车刀刀头,适于连续刀削
立方氮化硼
8000~9000HV
1400~1500
~300
压制烧结而成,可用金刚石砂轮磨削
硬度、强度极高的材料精加工,在空气中1000~1100℃极保持稳定
金刚石
10000HV
700~800
~300
用天然金刚石刃磨极因难
有色金属的高精度、高光洁度切削
2.刀具的几何形状及参数
图2-5所示的各种刀具,它们的一个刀齿的作用都类似一把车刀,与车刀的切削部分有着共同的特点。
因此,只要清楚了车刀的几何结构及其参数特征,就可应用到其它刀具上。
1)车刀的组成
如图2-4所示,车刀由刀头、刀杆两部分组成。
刀杆安装在机床的刀架上,支承刀头工作。
刀头又称为切削部分,主要担任切削工作。
切削部分由前刀面、主后刀面、副后刀面三个面组合而成,其中的各结构要素的定义如下:
前刀面——刀具上切屑流过的表面
主后刀面——与工件上的加工表面相对的表面
副后刀面——与工件上已加工表面相对的表面
主切削刃——前刀面与主后刀面的相交线,切削时,该线担负主要的切削任务
副切削刃——前刀面与副后刀面的相交线,也起一定的切削作用,但不明显。
刀尖——主切削刃与副切削刃相交的部位。
为增强刀尖的强度与耐磨性,一般在刀尖处磨出一直线或一段园弧,而非一个尖点。
2)车切削部分的几何参数
在切削加工过程中,刀具的锋利程度对切削加工过程有很重要的影响。
刀具的锋利程度是由刀具切削部分的几何结构决定的。
为便于设计、制造和使用刀具,有必要对刀具切削部分的几何结构进行描述。
为了确定和测量刀具切削部分的几何参数,一般采用三个互相垂直的辅助平面组成参考坐标系(图2-6所示),以它为基准,来测量各刀面和切削刃的空间位置。
基面——通过主切削刃上选定点,与该点切削速度方向垂直的平面。
切削平面——过主切削刃上选定点,与主切削刃相切,且垂直于基面的平面。
正交平面——过主切削刃上选定点,同时与基面和切削平面都垂直的平面。
使用以上的辅助面所构成的参考坐标系,可定义车刀切削部分的各主要参数,主要有前角γ、后角α、主偏角Kr、副偏角K'r、刃倾角λ等(图2-7)。
前 角——前刀面与基面之间的夹角,在正交平面中测量。
主后角——主后刀面与主切削平面之间的夹角,在正交平面中测量。
主偏角——主切削平面与假定工作平面间的夹角,在基面中测量。
副偏角——副切削刃与假定工作平面间的夹角,在基面中测量。
刃倾角——主切削刃与基面间的夹角。
在主切削面中测量。
3.车刀各参数的作用及选择
●前角:
前角较大时,切屑的塑性变形较小,同时切屑与前刀面间的磨擦也较小,有利于降低切削温度、减轻刀具磨损等。
但前角过大时,将导致切削刃强度下降,刀头散热体积减小,影响刀具使用寿命。
前角大小的选择主要考虑工件材料、刀具材料和加工性质。
若工件强度、硬度都不高,前角可取较大值,反之则取小值;加工塑性材料或韧性材料时,前角可取大些,反之则应取小值;精加工时由于切屑较薄,前角可取大些,而粗加工时则可取小些。
一般硬质合金车刀前角在-5º~20º之间选取,高速钢在相应条件下取大些。
●后角:
后角的大小影响到已加工表面的质量及主后刀面的磨损。
较大的后角可减少主后刀面与工件已加工表面间的磨擦,但后角过大时,会影响切削刃强度,并减小刀头的散热体积。
所以须选择合适的后角。
工件材料硬度、强度较高时,宜选取较小的后角,反之则应取大些;加工脆性材料时,由于刀屑较短,后角宜取小些,反之,加工塑性材料时,宜取大些;粗加工时,切削厚度较大,对表面质量要求也较低,后角宜取小些,而精加工时,后角就应取大些。
硬质合金车刀的后角一般在6º~12º间选取,高速钢可相应大些。
●主偏角:
在背吃刀量和进给量相同的情况下,改变主偏角的大小可以改变切削厚度与切削宽度,也就是改变切削刃工作长度。
主偏角较小,则主切削刃参加切削的长度较大,使刀刃单位长度上的受力减小,刀具寿命较长。
但过小的主偏角,使得刀具切削时的径向分力加大,从而增大工件已加工表面的弹性回复量及加工时的振动。
所以加工细长轴时,一般要取较大的主偏角
通常,加工细长轴时,宜选用75º~90º、甚至大于90º的主偏角;单件或小批生产时,选用通用性好的45º车刀及90º偏刀。
●副偏角:
取较大值时,可减小副后刀面与已加工表面间的磨擦。
但当主偏角选定后,副偏角增大时,加工残留面积也会增大,已加工表面也就越粗糙。
一般粗加工时取5º~10º,精加工时取0º~5º。
●刃倾角:
主要影响刀头强度与加工时的排屑方向
刃倾角一般取-10º~5º。
由于负的刃倾角可使远离刀尖的切削刃先接触工件,故可避免刀头受到冲击、加强刀头强度,所以粗加工时一般取负值。
精加工时,为避免切屑划伤已加工表面,刃倾角常取正值。
4.车刀的工作参数
以上介绍的车刀角度是车刀处于理想状态下的标注角度。
在实际切削中,由于车刀的安装位置变化,将会影响基面、主切削面、正交平面的实际位置,从而使刀具的实际角度发生变化,影响车刀的工作。
刀具工作时的实际角度称为工作角度,工作角度与标注角度往往是不相等的。
如图4-9a所示,当车刀刀尖与工件轴线等高时,其工作前角与标注前角相等,工作后角与标注后角相等。
如图4-9b所示,当车刀刀尖高于工件旋转轴线时,工作前角大于标注前角,工作后角小于标注后角。
反之如图4-9c所示,工作前角小于标注前角,工作后角大于标注后角。
如图4-10所示,车刀安装时,若刀杆轴线与工件旋转轴线不垂直时,会引起主偏角及副偏角的变化。
图a中,刀杆向右偏移,主偏角增大、副偏角减小。
图c中,刀杆向左偏移,主偏角减小、副偏角增大。
5.车刀的结构形式
车刀的结构形式有:
整体式、焊接式、机夹重磨式、机夹可转位刀片式
●整体式:
刀杆与刀头为一整体,故对较贵重的刀具材料消耗量较大,经济性较差。
早期的刀具大多为这种结构,现在较少使用。
●焊接式:
这种结构的刀头是焊接到刀杆上的。
与后面的两种结构相比,其结构简单、紧凑、刚性好,可以根据加工条件和加工要求方便地磨出所需角度。
但经过高温焊接和刃磨后,硬质合金刀片会产生内应力和裂纹,使切削性能降低。
●机夹重磨式:
刀片与刀杆是两个相互独立的元件,工作时靠夹紧装置将它们固定在一起,图4-11所示为机夹重磨式切断刀的一种典型结构。
机夹重磨式切断刀避免了焊接式的内应力缺陷,提高了刀具耐用度,同时还可使刀杆多次重复使用。
●机夹可转位刀片式:
如图4-12所示,将压制有一定几何参数的多边形刀片,用机械夹固的方法,装夹在标准的刀杆上。
使用时,刀片上一个切削刃用钝后,只需将夹紧机构松开,将刀片转位换成另一个新的切削刃,便可继续切削。
机夹可转位刀片式车刀的优点可归纳为如下几点:
a)由于避免了因焊接而引起的缺陷,所以,在相同的切削条件下,刀具耐用度大为提高
b)在一定条件下,卷屑、断屑稳定可靠
c)刀片转位换成另一个切削刃时,不会改变切削刃与工件的相对位置,从而保证加工尺寸,减少了调刀时间。
d)由于刀片一般不需重磨,有利于涂层、陶瓷等新型刀片的推广使用。
e)刀杆使用寿命长,故可节约大量刀杆材料及制造刀杆的费用。
f)刀片和刀杆可以标准化,有利于减少刀具制造成本,减少工具库存量,提高了经济性
复习思考题
1.简述车刀前角、后角、主偏角、副偏角、刃倾角的作用
2.什么是切削用量?
切削用量各要素对加工质量有何影响?
3.用高速钢制造锯刀,用碳素工具钢制造拉刀,是否合理?
为什么?
4.2金属切削加工的基础理论BasicTheoryofMetalCutting
4.2.1切削过程与切屑种类
金属切削过程实质上就是切屑的形成过程(图3-18,切屑的形成),被切削金属层受到刀具的挤压作用力时,开始产生弹性变形(图a)。
随着切削的继续进行,刀具继续给被切削金属层施加挤压力,金属内部产生的应力与应变也随之不断地加大。
当应变达到材料的屈服极限时,被切削金属层产生塑性变形(图b)。
此时切削仍在继续进行,金属内部产生的应力与应变继续加大,当应力达到材料的断裂强度极限时,被切金属层就会断裂而形成切屑(图c)。
此时,金属内部的应力迅速下降,又重新开始弹性变形、塑性变形、断裂的循环,而形成新的切屑。
带状切屑:
图4-14a所示,切屑的内表面光滑、外表面呈微小的锯齿形。
用较大的前角,较高的切削速度和较小的进给量切削塑性材料时,多获得此类切屑。
有带状切屑的切削过程一般较平稳,切削力波动小,已加工表面较光滑。
但由于切屑连绵不断,有可能刮伤已加工表面或刮伤操作人员,故不太安全,须采取断屑措施。
节状切屑:
图4-14b所示,切屑的外表面呈较大的锯齿形,并有较深的裂纹。
用较小