焊接冶金学.docx
《焊接冶金学.docx》由会员分享,可在线阅读,更多相关《焊接冶金学.docx(20页珍藏版)》请在冰豆网上搜索。
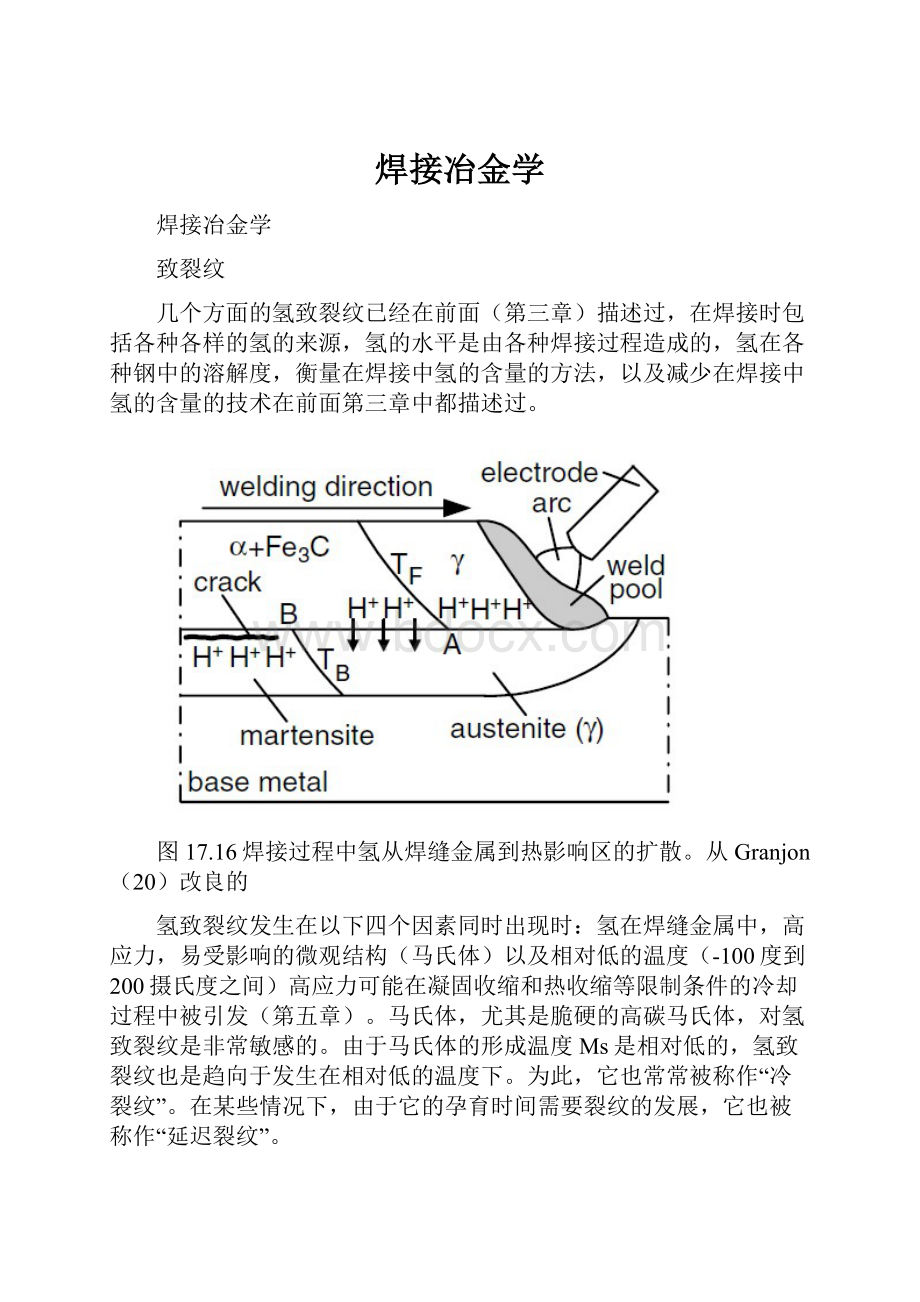
焊接冶金学
焊接冶金学
致裂纹
几个方面的氢致裂纹已经在前面(第三章)描述过,在焊接时包括各种各样的氢的来源,氢的水平是由各种焊接过程造成的,氢在各种钢中的溶解度,衡量在焊接中氢的含量的方法,以及减少在焊接中氢的含量的技术在前面第三章中都描述过。
图17.16焊接过程中氢从焊缝金属到热影响区的扩散。
从Granjon(20)改良的
氢致裂纹发生在以下四个因素同时出现时:
氢在焊缝金属中,高应力,易受影响的微观结构(马氏体)以及相对低的温度(-100度到200摄氏度之间)高应力可能在凝固收缩和热收缩等限制条件的冷却过程中被引发(第五章)。
马氏体,尤其是脆硬的高碳马氏体,对氢致裂纹是非常敏感的。
由于马氏体的形成温度Ms是相对低的,氢致裂纹也是趋向于发生在相对低的温度下。
为此,它也常常被称作“冷裂纹”。
在某些情况下,由于它的孕育时间需要裂纹的发展,它也被称作“延迟裂纹”。
描述了在焊接过程中氢从焊缝金属到热影响区的扩散。
TF和TB的关系是奥氏体/(铁素体+珠光体)和奥氏体/马氏体各自的转变温度。
因为焊缝金属从奥氏体(γ)转变为铁素体和珠光体(a+Fe3C),氢是被从前者到后者拒绝的,因为氢在铁素体中的溶解度比在奥氏体中的低。
焊缝金属中的含碳量通常比基底金属的低,是因为填充金属比基底金属含碳量低。
同样地,很有可能焊缝金属从奥氏体转变成铁素体和珠光体,在热影响区之前奥氏体转变成马氏体(M)。
在焊缝金属铁素体中氢的中比在奥氏体材料中更高。
相变硬化材料
扩散率和温度的函数。
修改自Coe。
氢在铁素体中的高扩散率帮助了这个扩散过程。
相反,氢在奥氏体中的低扩散率阻止了氢从热影响区到基底金属的扩散,此过程发生在热影响区奥氏体向马氏体转变之前。
在热影响区,氢和马氏体的组合促进了氢致裂纹的形成。
氢致裂纹的形成机制尚未充分弄明白,虽然有很多的理论被提出来。
在这里就不讨论这些理论,因为这是比焊接冶金学更倾向于物理冶金的学科。
实际上,无论如何,对它都有足够的认识,Troiano提出氢通过减少材料紧密结合的晶格强度来促进裂纹的增长,Petch提出氢通过减少裂纹表面能量来促进裂纹扩展。
Beachem提出氢帮助裂纹尖端之前的微观变形。
Savage以及其他人解释到:
焊缝氢致裂纹是以Troiano的理论为基础的。
Gedeon和Eagar报告他们的结果证实了以及延伸了Beachem的理论。
“焊道下裂纹”.这个裂纹本质上是平行于融合边界线的。
氢致裂纹能处的裂纹。
这种形式的裂纹叫做”焊趾裂纹“同样图中还展示了焊接根部裂纹,未焊透是非常明显的。
这种裂纹叫做”根部裂纹“。
的焊道下裂纹,放大倍数8×,翻印于Bailey
图17.191040钢角焊焊缝中的氢致裂纹(放大倍数4.5×)由BuehlerU.K.,Ltd.,Coventry,UnitedKingdom提供
钢对氢致裂纹的敏感性的测试方法有很多,比如植入测试,理海大学限制测试,RPI扩张拉力裂纹测试,控制热量猛烈测试,理海位置焊接性测试。
由于篇幅的限制,在这就描述前两种测试。
图17.20是植入测试的原理图。
在这个测试中,把一个圆柱形的有缺口的样本插入到一个相似材料制成的金属板的洞中。
一个焊接跑道修改在样本上,它坐落于这样一个地方,它的顶部变成了融合区的一部分,它的凹口正好位于热影响区。
在焊接之后焊缝冷却之前,一个负载施加于这个样本,失败的时间是确定的。
作为一个氢致裂纹敏感性的评估,应力的施加已经决定了失败的时间。
如图17.21所示高强度,低合金管道钢。
在这种情况下,在焊缝冷却至125°C应力加载到样本上。
氢致裂纹的植入式测试
图17.21HSLA管道钢的植入式测试由Vasudevan等人重印由美国焊接学会提供
Lehigh约束样本。
Stout等人重印。
由美国焊接学会提供
由上所示,焊缝是由低氢焊条(E7018,基础石灰岩覆盖物)产生的比焊缝是由高氢焊条(E7010,纤维素类覆盖物)产生的,在没裂纹产生的情况下以及要更长时间产生裂纹,有更高的临界应力值。
换句话说,前者对氢致裂纹较后者更不敏感。
用Ar+2%O2做保护气体的气体金属电弧焊是最不敏感的。
很明显,没有电焊条覆盖物的出现来把氢引入这些焊缝中。
中显示了Lehigh约束样本。
样本设计成边上和端部割缝加工。
插槽越长,金属板限制焊缝的程度越低。
一个焊道被做在了连接点的根部,用来阻止氢致裂纹的插槽长度是确定的。
裂纹被检测出是可见的或者被穿过焊缝中央的横断面所检查出来。
。
图17.23预热在高强钢氢致裂纹中的效果GedeonandEagar重印由美国焊接学会提供
两种普通的方法被用来选择最适合的温度。
一种方法是用经验推断表格,它列出了钢和推荐的焊接工艺,包括了预热和层间温度,例如,列出了各种等级的碳钢和低合金钢。
另一种方法是把有裂纹倾向与碳当量的各种钢的淬硬性联系起来。
一个合金钢碳当量的公式如下:
图17.24所示基于此公式的推荐的预热和层间温度。
图17.24碳当量在需要通过预热阻止氢致裂纹的效果重印于Lesnewich
A.2焊后加热焊后热处理,像前面部分描述的那样,在冷却到室温之前能被用于焊缝应力消除。
如果应力消除热处理在焊接完成时不能立即实施,将完整的焊件保持在适当的温度,能使奥氏体与马氏体转变成更不容易受影响的显微结构。
焊后加热也能帮助氢从工件中扩散出来(第三章)。
大多数碳钢的焊后热处理温度范围是590–675°C(1100–1250°F)。
A.3焊珠回火焊珠回火在多程焊接过程中也能有效的减少氢致裂纹。
这个在前面也描述过。
B.适当焊接过程和材料的使用。
B.1低氢过程的使用和减少消耗低氢焊接过程的使用(比如气体保护钨极电弧焊或者气体保护金属极电弧焊代替电弧焊或者药芯焊丝电弧焊)和消耗(比如基础的而不是有纤维质的电焊条)减少出现在焊接区氢的数量(第三章)。
电焊条应该保存在密闭容器中。
假如它们暴露了,它们需要置于300–400°C(600–800°F)温度下烘干。
B.2更低强度的填充金属的使用比基底金属更低强度的填充金属的使用能帮助减少热影响区的应力水平,还能减少氢致裂纹的发生机会。
B.3奥氏体不锈钢作为填充金属的使用奥氏体不锈钢和镍基合金已经被用于HTLA钢焊接的填充金属。
氢的扩散率在奥氏体中(包括镍基合金)比在铁素体中更低(图17.17)同样地,氢被收集在奥氏体焊缝金属中,不能到达热影响区而引起裂纹。
此外,奥氏体焊缝金属良好的延展性能帮助阻止过分高的残余应力在热影响区的发展,从而减少了对氢致裂纹的敏感性。
再热裂纹是一个在含有铬、钼有时还有钒和钨等元素来增强抗腐蚀和耐高温强度的低合金铁素体钢中公认的问题。
这些合金钢有时被称作抗蠕变铁素体钢,频繁的被用于提高温度原子能和化石能量应用领域的提高温度的服务。
抗蠕变铁素体钢通常被重新加热至550–650°C,在焊接后减压和减少氢致裂纹的敏感性或者应力腐蚀裂痕。
然而在重新加热的过程中,裂纹可能发生在热影响区。
例如,铁素体钢易受再加热裂纹的影响包括–––1Mo–1V,和–1Mo。
Nakamura等人提出合金元素在裂纹敏感性的效果的公式如下:
当碳钢的值大于或者等于0时,钢可能受再热裂纹的影响。
CrMoV钢中的再热裂纹。
所示,裂纹来到热影响区原奥氏体晶界。
–1Mo钢的断裂面经过Gleeble热量焊接仿真模拟和在冷却过程以及在一个升高温度贯穿整个再加热过程的张引力的保持。
晶粒间裂纹是很明显的。
图17.25CrMoV钢中的再热裂纹(a)宏观结构(放大倍数×35)(b)微观结构(放大倍数×1000)裂纹来自于原奥氏体bainitic结构来自于Bailey
图17.26扫描电子显微镜下的一个由再热裂纹引起的–1Mo铁素体钢的断裂面
Nawrocki等人重印由美国焊接学会提供。
再热裂纹的机制解释如下。
在焊接热影响区附近的熔合线在奥氏体相域被加热到一个很高的温度。
先前存在于碳化物中的Cr,Mo,和V溶解,奥氏体晶粒生长。
随后的快速冷却不允许有足够的时间为碳化物再沉淀,导致的结果是这些合金元素过度饱和随着奥氏体转变成马氏体(假如淬硬性是足够的)当热影响区的粗粒度晶粒为了消除应力被再加热到高温时,优良的碳化物沉淀物在原奥氏体内部晶粒的位错中,在应力解除之前使它们增强。
因为晶粒内部比晶界增强更多以及这个现象发生在应力解除之前,所以裂纹可能发生在晶界上。
再热裂纹的敏感性能被样品紧凑张力时裂纹的生长长度所评估或者仅仅是一个CharpyV型凹口样品,它装载和保持在再加热温度下(假定在600°C左右)。
这个Vinckier测试在图17.27也被用过。
这个试样是由两片焊接在一起的50mm厚的板材组成。
这个式样的末端是与不锈钢块焊接在一起。
根据再加热,试样受到由不锈钢块更高的热膨胀系数引起的拉伸载荷。
再热裂纹的Vinckier测试。
来自于Glover等人。
图17.28扫描电子显微镜照相技术下的––铁素体钢断裂面(a)单程样品(b)多程样品。
Nawrocki等人重印由美国焊接学会提供
下面这个公式能用来确定焊接试样的全部应变:
(17.3)
ε是试样的全部的应变,a是热膨胀系数,E是杨氏模量,T是再加热温度,A是横断面面积。
下标1和2分别代表两个不锈钢试样块。
图17.25a,实际上是Vinckier试样的宏观结构。
17.5.4补救办法
多程焊接已经被报道能减少--铁素体钢的结果,受到了Gleeble焊接热量的仿真模拟和
--铁素体钢单程和多程样品失效模式。
Nawrocki等人修改,由美国焊接学会提供。
在冷却和贯穿整个再加热升温过程之间的张应力的维持。
随着单一模拟焊接通道,如图17.28(a)所示来自易碎的晶间破裂模式的再热裂纹是很明显的。
用两个焊接模拟通道,无论如何,再热裂纹是避免了。
如图17.28(b)所示来自微孔隙失效模式是显而易见的,它还增加了失效的时间。
图17.29解释了多程焊接过程的效果。
用单程的焊接程序,产生的晶粒是粗糙的。
正如前面提到的,在再加热优良硬质合金沉淀期间,晶粒内部会产生位错。
同时粗糙的碳化物也能在晶界处形成,同时也能耗尽邻近的碳化物形式的合金元素。
这个也能引起自由沉淀无缺陷领域形成晶界。
同样地,优良的碳化物增强了内部晶粒和自由沉淀无缺陷领域,假如它出现将会减弱晶界。
无论如何,因为晶粒内部比晶界增强的更多,晶粒间的裂纹就发生在晶界。
用多程焊接程序,但是,粗晶粒被精炼,细晶粒内部的碳化物变粗糙,这里不再有自由沉淀无缺陷区域与晶界一起出现。
减少残余应力的水平,在焊接时能获得最小的限制,也能减少抗蠕变铁素体钢中的再热裂纹。
应力集中,比如圆角和边角处以及原来的熔融裂纹处,出现问题的趋势更加突出。
如对能热处理的镍基合金,通过硬质合金沉淀的范围对其快速加热,如有可能,也能被认为是。
图17.30所示的是基于裂纹敏感性的C曲线,可以看出-1Mo比-Mo-V更可行。
图17.30铁素体钢断裂的时间vs温度图Murray提供
17.6层间撕裂
17.6.1原因
焊接结构中的层间撕裂的原因已经被许多研究者描述过。
简言之,它是由于焊缝收缩引起的局部高应力和在基底合金厚度方向上由于存在细长的侧弦的非金属夹杂物平行于轧制方向的低延展性的组合。
撕裂是由这种非金属夹杂物结合破坏引起的(通常是硅酸盐和硫化物)在焊缝附近或者正好在热影响区外面。
图17.31所示是典型的各种钢易受薄片状撕裂的微观结构。
C–Mn钢在T形对接焊接下的层间撕裂,它在轧制方向上有个阶梯式轨道—典型的层间撕裂。
来自Dickinson和Nichols
图17.32在C–Mn钢焊缝附近的层间撕裂。
由TWILtd.许可复制
除了夹杂物的含量和形态,其他的因素有比如氢,预热,电焊条的强度也被报道能影响钢对层间撕裂的敏感性。
例如,由含纤维质的电焊条E7010形成的焊缝,它提供了高的氢的潜能,被发现明显比由气体保护金属极弧焊方法更易受影响。
氢的作用似乎是与脆裂联系在一起而不是冷裂纹。
预热被发现能减少对层间撕裂的敏感性,尤其当含氢电位出现时。
应该指出预热,在运行时约束接合点处加入最终的收缩张力,因此,改善了对层间裂纹的抵抗。
电焊条强度水平的使用,当然,不能比设计要求的更低。
钢对层间撕裂的敏感性评估的方法有许多种,比如,Lehigh悬臂层间撕裂测试,CranefieldLehigh悬臂层间撕裂测试。
如同所示,V凹槽在试样和有50mm2”厚的横梁设置成和它垂直之间的多道焊。
Lehigh悬臂层间撕裂测试Kaufman等人重印由美国焊接学会提供
17.6.3补救办法
一个避免层间撕裂的使用的方法是采用接头设计,它能允许收缩应力沿敏感材料沿轧制方向更起作用以及沿厚度方向的横断面有更少的收缩应力。
图17.34所示就是用的一个这种接头设计。
图17.34角接接头的层间撕裂(a)错误的设计(b)改良的设计
17.7.1插座(牙槽)和管道焊接的失败
图17.35a所示是一个鞍状物牙槽、管道焊件的破裂部位。
钢管(外径150mm)含有0.51%C和0.75%Mn,钢套节含有少于0.1%C。
如图17.35b所示焊道底层裂纹在管子里是很明显的。
如图17.35c所示为这个区域的显微结构,马氏体的硬度水平范围是700–800HV。
没有使用预热和焊后加热,失败就发生在焊后冷却过程中。
图17.35插座和管道焊接失败的焊件:
(a)破裂部位(放大倍数0.4×)(b)焊道层底裂纹(放大倍数7.5×)(c)裂纹区域的马氏体微观结构(放大倍数370×)重印允许来自Naumann
的连杆顶端。
这个杆是由中碳钢或者低合金钢在坚硬和缓和的条件下对基底金属的微观结构的分析制成的。
轴承的顶端连杆在这个引擎里最初是用外部的管子从低端沿着连杆里的长笛顺流而下供油的。
由于后来修正了润滑方法,连杆顶端的小孔和焊缝金属沉积物脱焊了。
连杆在修正后大约五年内就失效了。
图17.36b所示是在热影响区的焊道下裂纹。
这个热影响区展示了一个硬度为450VPN的马氏体组织,它用金刚石锥体在负载3kg的条件下测量的。
因为一个小的焊缝熔敷被铺设到冷金属上,冷却速度是如此之高,从而导致了焊道底层裂纹。
这些裂纹充当了疲劳裂纹的起始点,导致了杆的最终破裂。
断裂面如图17.36a所示是光滑的,贝壳状的,有疲劳造成的特征。
图17.36柴油机引擎连杆的失效:
(a)连杆顶端展示的断裂面和焊缝熔敷(b)贯穿焊缝熔敷部分展示的焊道层底裂纹(放大倍率3.5×)来自Hutchings和Unterweiser
图17.37a所示涡轮压力管道的埋弧焊的一个大裂纹。
管道内径是1.2m,墙的厚度是不同的从6-11mm。
这个管道是由含0.1%C,0.4%Mn,0.02%S,和0.02%P的钢的两块平板做成的。
管道有两个纵向焊缝。
在双叶之间的第一次焊接接缝之后,跟着进行冷轧操作。
然后,第二个接缝被焊合,在焊接一周后管道再次进行冷轧。
管道被安装在鞍式支座上,并隔开14m的距离。
区域周围的微观结构。
如同所示,层间撕裂,可能是由于硫和磷的纵梁非金属夹杂物,是很明显的。
冷轧操作,重力在鞍式支座间的管道部分起作用,内部的压力循环本能够有助于层间撕裂所需要的压力。
图17.37水轮机压力管道的失效:
(a)管道的破裂(b)层间撕裂展示的沿着裂纹的焊缝微观结构。