完整版电弧炉冶炼浇注工艺规程LB.docx
《完整版电弧炉冶炼浇注工艺规程LB.docx》由会员分享,可在线阅读,更多相关《完整版电弧炉冶炼浇注工艺规程LB.docx(10页珍藏版)》请在冰豆网上搜索。
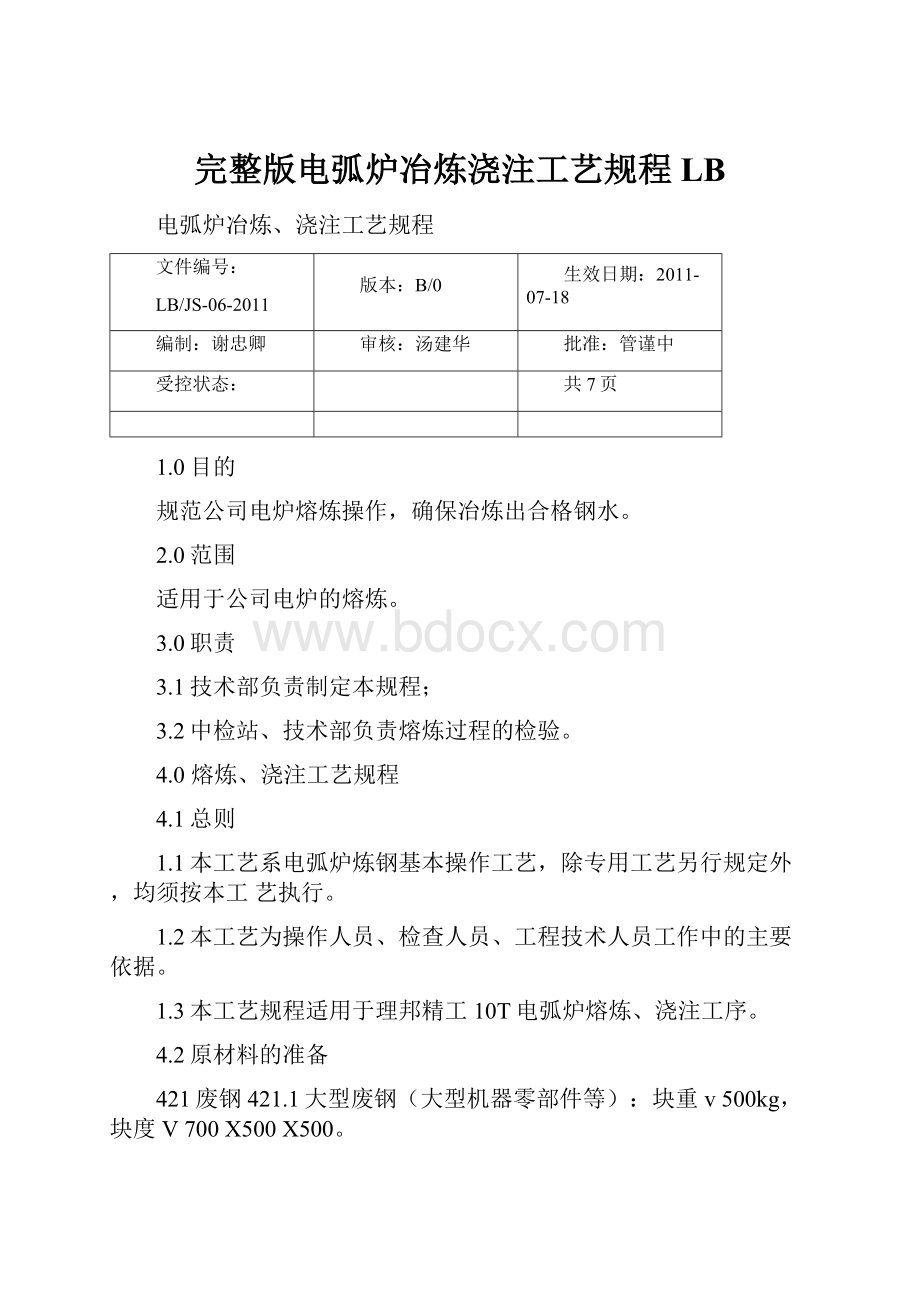
完整版电弧炉冶炼浇注工艺规程LB
电弧炉冶炼、浇注工艺规程
文件编号:
LB/JS-06-2011
版本:
B/0
生效日期:
2011-07-18
编制:
谢忠卿
审核:
汤建华
批准:
管谨中
受控状态:
共7页
1.0目的
规范公司电炉熔炼操作,确保冶炼出合格钢水。
2.0范围
适用于公司电炉的熔炼。
3.0职责
3.1技术部负责制定本规程;
3.2中检站、技术部负责熔炼过程的检验。
4.0熔炼、浇注工艺规程
4.1总则
1.1本工艺系电弧炉炼钢基本操作工艺,除专用工艺另行规定外,均须按本工艺执行。
1.2本工艺为操作人员、检查人员、工程技术人员工作中的主要依据。
1.3本工艺规程适用于理邦精工10T电弧炉熔炼、浇注工序。
4.2原材料的准备
421废钢421.1大型废钢(大型机器零部件等):
块重v500kg,块度V700X500X500。
421.2中小废钢(钢材及切头、锻铆件等):
块重v200kg,块度V600X500
X400。
4.2.1.3钢屑、轻薄料压块:
块度V700X400X400
4.2.1.4回炉料(浇冒口、废铸件等):
块重v500kg,块度V700X500X400。
4.2.1.5废钢应按成分、块度分类存放。
不应带有冰块、砂块、有色金属等,
严禁封闭容器、易爆炸物等物品入炉。
4.2.1.6炉料应无油、干燥。
油污料和严重锈蚀的炉料应清除污、锈
4.2.1.7严禁装入油漆桶、涂料桶类物品入炉。
4.2.2合金及辅助材料
4.2.2.1所用各种合金材料和辅助材料应保持干燥、洁净。
4.2.2.2各种材料的主要成份、块度,必须符合原材料技术要求,使用前必须
清楚成份含量,并经烘烤使用。
4.2.2.3各种合金辅料使用条件及干燥温度如下表:
材料名称
块度尺(mm)
烘烤温度「C)
烘烤时间(h)
硅铁
50-150
>400°C
>2
锰铁
30-150
>400C
>2
铬铁
50-150
>400C
>2
钼铁
<100
>200°C
>2
矿石
30-150
>600C
>2
萤石
5-50
>100C
>8
石灰
<100
>400C
>4
硅铁粉
60-100C
>6
422.4严禁使用粉化石灰造渣。
422.5电极必须存放于干燥地方,搬运时严禁破损。
4.2.2.6认真填写原材料烘干记录。
4.3补炉与烘炉
4.3.1补炉材料:
补炉材料必须提前半小时混合均匀。
干式捣打料(XYD--2):
含MgO>80%,堆积密度2.45-2.6;卤水(比重1:
3)。
4.3.2出钢后立即检查炉况,需要补炉时,应先将炉底之剩钢、残渣全部扒出,然后进行修补。
4.3.3对炉底和炉壁被侵蚀及破坏部位进行修补,侵蚀严重处要少量多次重复补炉。
补炉的原则是“高温、快补、薄补”,维护炉膛原状。
4.3.4炉体损坏严重时,若补炉材料用量在500-700kg时,补炉后应用电极烘烤30min;若补炉材料用量超过700kg,应酌情延长烘烤时间。
4.3.5出钢槽用整体浇制特种耐火材料。
修补时不得采用水玻璃砂修补,出钢
槽应干燥,流畅;更换新出钢槽时,应用木柴彻底烘烤。
436当炉体大修或中修后,或停炉时间较长时,开炉前应按要求烘烤炉衬和出钢槽,氧化期宜采用矿石脱碳,以便进一步加强炉衬的烘烤烧结。
437补炉后应认真检查炉体水冷系统,发现渗漏及时联系处理。
4.4配料
4.4.1配料前根据所炼钢种确定氧化期脱碳量,配碳量二钢种规格中限+氧化期脱碳量。
4.4.2氧化期脱碳量的确定,一般碳钢件脱碳量为0.2-0.3%,一般合金钢铸件脱碳量为:
030.4%,重要合金钢铸件脱碳量为:
040.5%。
大修炉后第一炉的脱碳量应在0.5%以上,中修炉后第一炉的脱碳量应在0.4%以上。
4.4.3熔清碳上、下偏差不得超过配碳量的+0.05%,若下偏差低于规格要求
0.05%时,必须做增碳处理,二次化验合格后,方能进行氧化。
4.5装料
4.5.1装料前再次检查电路设备完好情况,如有故障及时修理或更新
4.5.2超装量大于25%时,应与技术部门协商,方可进行。
4.5.3检查电极有无损坏,以及是否足够一炉使用,否则要及时接好,避免在冶炼过程中接放电极。
4.5.4装炉料前炉底必须先铺石灰一层,重量为炉料重的1%左右,以利于提
前造渣和减轻装料对炉底的冲击,并减少热损失。
4.5.5装料应按大、中、小、轻,适当比例配加,以保证装料紧密。
装料次序为:
薄铁皮或长钢屑铺底一大料一中料一小料或钢屑,高硫及大块料应放在料斗中心,以利于去硫和熔化。
渣铁避免装在电极位置,防止不导电,配加的生铁应在料斗的下中层。
4.5.6炉料入炉时,不得碰撞炉墙,如有炉料接触水冷炉盖时,一定要排除,避免起弧烧坏炉盖。
4.5.7装二次料时,要求小料和轻薄炉料,入炉速度要求快,减少热损失。
加料次数应在2次以内,不宜超过3次。
4.5.8所有入炉材料均需准确称重,并做好记录。
4.6熔化期
4.6.1在熔化初期(穿井和电极回升阶段),应满负荷送电(电压240V、电流
10000-12500A),快速熔料。
4.6.2为了节约电能和提高冶炼速度,通电后45分钟一1小时后,当炉内形成钢水熔池时(炉料熔化70%左右),就开始吹氧助熔,氧压力为0.5Mpa,吹氧管插入的深度为钢渣的交界面上,吹氧管与钢水面夹角为15°,当大块炉
料难于熔化时,采用吹氧切割帮助熔化,为了防止搭桥,配合吹氧进行捣料,加快熔化速度,防止搭桥塌料砸断电极。
4.6.3炉料熔化过程中,应根据炉料情况适当补加渣料。
4.6.4炉料全部熔清后,搅拌取熔清样分析C、P、S、Cu、Mn、Mo,取样应具有代表性。
465熔清碳应保证氧化期脱碳量。
碳量不足时应用生铁增碳至符合要求,并搅拌均匀,再取样分析。
4.6.6熔化末期加入适量的石灰及碎矿石,提前造好碱度与FeO含量适当且流动性良好的泡沫渣,保持渣量在3%左右。
4.6.7熔化末期若磷含量较高,应流掉部分炉渣,做好前期去鳞操作。
4.7氧化期:
氧化期的任务是去鳞,除气和夹杂物,提高钢水的温度。
因此在低温下,提前去鳞,在高温下,借助于氧化去碳,造成熔池钢水沸腾,促使钢水中气体溢出和夹杂物上浮。
去碳只是手段,而不是目的,所以为了完成氧化期的任务,就必须有足够的温度,一定的脱碳量和脱碳时间。
吹氧氧化是提高温度,加快反应速度行之有效的方法。
4.7.1开始氧化的条件:
4.7.1.1炉料全部熔清后取样化验。
4.7.1.2碳符合所炼钢种熔清碳要求。
4.7.1.3炉渣流动性良好。
7.1.4钢水温度达到1570C以上。
4.7.2吹氧氧化的氧压为0.7—1.0Mpa,氧枪插入深度距炉渣面200mm左右,氧枪和钢水面的夹角为15°,并进行移动吹氧。
4.7.3用矿石和氧气进行综合氧化沸腾时,矿石的烘烤,块度应符合工艺要求,矿石分批加入,每吨钢水降低0.01%碳,加矿为1.2kg,矿石加入的间隔时间为5分钟
4.7.4吹氧氧化用氧量为每吨钢水每脱0.10%的碳约耗氧15m3左右
4.7.5在氧化期中,要保持高温沸腾均匀,自动流渣,当补加渣料时应去氧化渣,严禁产生大沸腾和抛钢现象。
4.7.6如起镁砂,应扒除部分或全部渣子,重造新渣。
4.7.7最后一批矿加工完或吹氧后,静沸腾5分钟后进行搅拌,取样分析C、
P,如达到工艺要求,加锰铁进行预脱氧,锰铁的加入量为配锰量的0.20%
4.7.8氧化期总渣量为炉料重的3—3.5%左右。
4.7.9扒渣条件:
4.7.9.1含碳量、含磷量符合工艺要求。
4.7.9.2钢水温度不应低于出钢温度。
4.7.9.3钢水沸腾静止。
4.7.9.4炉渣流动性良好,进行扒渣。
4.7.10扒渣应迅速、干净、以免钢水降温,吸气和回磷,同时要尽量不带出钢水。
4.7.11氧化期注意事项:
4.7.11.2脱碳速度,每分钟脱碳0.02—0.04%。
4.7.11.3取样要有代表性,样勺插入炉内中心。
4.7.12氧化期的电力要求,按附表进行配电操作。
4.8还原期
还原期主要任务是脱氧、脱硫,获得合适的化学成份和适宜的出钢温度。
温度是完成上述任务的主要因素。
4.8.1扒渣后迅速加入锰铁(配Mn达规格中限)和稀薄渣料,薄渣料占炉
料重量的0.8—1%,其配比为石灰:
萤石=5:
2.加完后进行搅拌,并开始封闭出钢口和电极孔。
4.8.2稀薄渣形成后,加还原造渣,其配比为石灰:
萤石:
碳粉:
电石=3:
1:
1:
1,重量为炉料重的1.2—1.5%,一次加完,封闭炉门,保持还原气氛20—30分钟左右,时刻注意炉内还原性气氛的良好性,及时用碳粉或碳化硅粉调节,对硫要求不高的钢种可以不加电石。
4.8.3还原期任务完成后,出钢前必须加硅铁粉破坏电石渣,用量为料重的
0.08—0.09%,分批加入,渣好后(渣白)取样分析钢水成份,根据分析结果调整各元素含量。
4.8.4良好的白渣形成后加入硅铁,配硅达到规格中限,加完硅铁后,要充分搅拌,经常看温度。
4.8.5加完硅铁到出钢的时间不大于15分钟。
4.8.6还原期渣量为3—3.5%。
487还原期要确保钢水的脱氧去气含量,严禁吹氧提温及使用大电压
488还原期电力曲线根据附表进行。
4.9出钢
出钢是电炉炼钢的最后一环,出钢过程中操作的好坏,直接影响到钢的质量。
4.9.1出钢应具有以下条件
4.9.1.1白渣流动性良好。
4.9.1.2化学成份调整合适,达到规格要求,加入的铁合金已全部熔化
4.9.1.3温度达到出钢温度(各钢种规定的浇注温度)。
4.9.1.4加硅铁后,取潮模样,收缩良好。
4.9.1.5出钢槽干燥清洁,出钢口放大,以使钢渣混出。
4.9.2出钢前,加铝量1.1—1.5kg/吨钢水(湿雨季可以加1.5kg/吨钢)加入包内预热,等待出炉。
4.9.3炉后取潮模样,收缩良好,方可浇注,并保存好备查。
4.9.4取样或测温前一定要进行搅拌,后方可进行。
4.9.5钢包充分烘烤,温度达到750C以上(颜色暗红色)。
4.9.6钢包从停止烘烤到出钢的时间间隔v5min。
4.9.7出钢过程中应达到如下要求:
497.2钢水流不得直接冲包壁,包柱。
4.9.7.3大口喷吐,钢渣混冲,防止钢水氧化,以利脱硫。
4.9.8出钢后在钢包内测温,并做好记录。
4.10浇注
4.10.1浇注前的准备
4.10.1.1浇注工必须熟悉本炉钢水材质、重量以及所浇铸件的数量、重量;
4.10.1.2清除浇注通道的不安全因素;
4.10.1.3检查砂箱卡子、锁箱螺栓是否紧固牢实;
4.10.1.4备好草灰、发热剂、干砂、引气材料、铁锨。
水管等用具;
4.10.1.5备好倒剩余钢水和渣子的地坑。
4.10.2操作要求
4.10.2.1钢水出炉后要在钢包中镇静5—10分钟再浇注(重要的合金钢铸件出钢后要吹氩精炼5分钟左右,吹氩压力为0.2—0.3Mpa),具体镇静时间长短应根据出钢温度、出钢降温、钢水在钢包中的降温以及要浇注的砂箱数来决定;参见下表
钢水量(T)
<15
V20
备注
出钢降温(C)
40—60
30—50
自然气温咼取下限、自然气温低取取上限,钢水量大取下限、钢水量小取上限;
钢水在钢包中降温速度(C
/分)
2—3
1.5—2.5
4.10.2.2浇注时钢包不能摆动,必须对正浇口杯,钢包底距浇口杯不得高于
150—200mm;
4.10.2.3按浇注顺序、工艺要求进行浇注;
4.10.2.4开始浇注后的第一个铸件应是较大的铸件,以便将包底部温度较低的
钢水及时放出,以保证能够关严注口,再浇小铸件,薄壁铸件和结构复杂的铸件,最后浇厚壁及结构简单铸件;
4.10.2.5浇注时,浇口杯应保持充满,并不得引起钢水飞溅或漩涡;
4.10.2.6浇注开始后应立即引火;
4.10.2.7浇注时若发生跑火,应将大流改为小流,但不能停流,当跑火不能封堵时,应停止浇注;
4.10.2.8浇注时如发生钢水猛烈沸腾,并从冒口连续喷出钢夜时,应立即停止浇注;
4.10.2.9浇注剩余钢水要返回炉内或倒入专门地坑中;
4.10.2.10浇注完毕,在砂箱上标注铸件名称、浇注时间、开箱时间;
4.10.3钢水总量浇注完1/4左右时,浇注试验棒,钢水的化学成份有疑点时
以试验棒的分析结果为准
5.0记录
5.1作好熔炼及浇注记录,含钢种、炉号等信息。