铸造工艺指导书.docx
《铸造工艺指导书.docx》由会员分享,可在线阅读,更多相关《铸造工艺指导书.docx(28页珍藏版)》请在冰豆网上搜索。
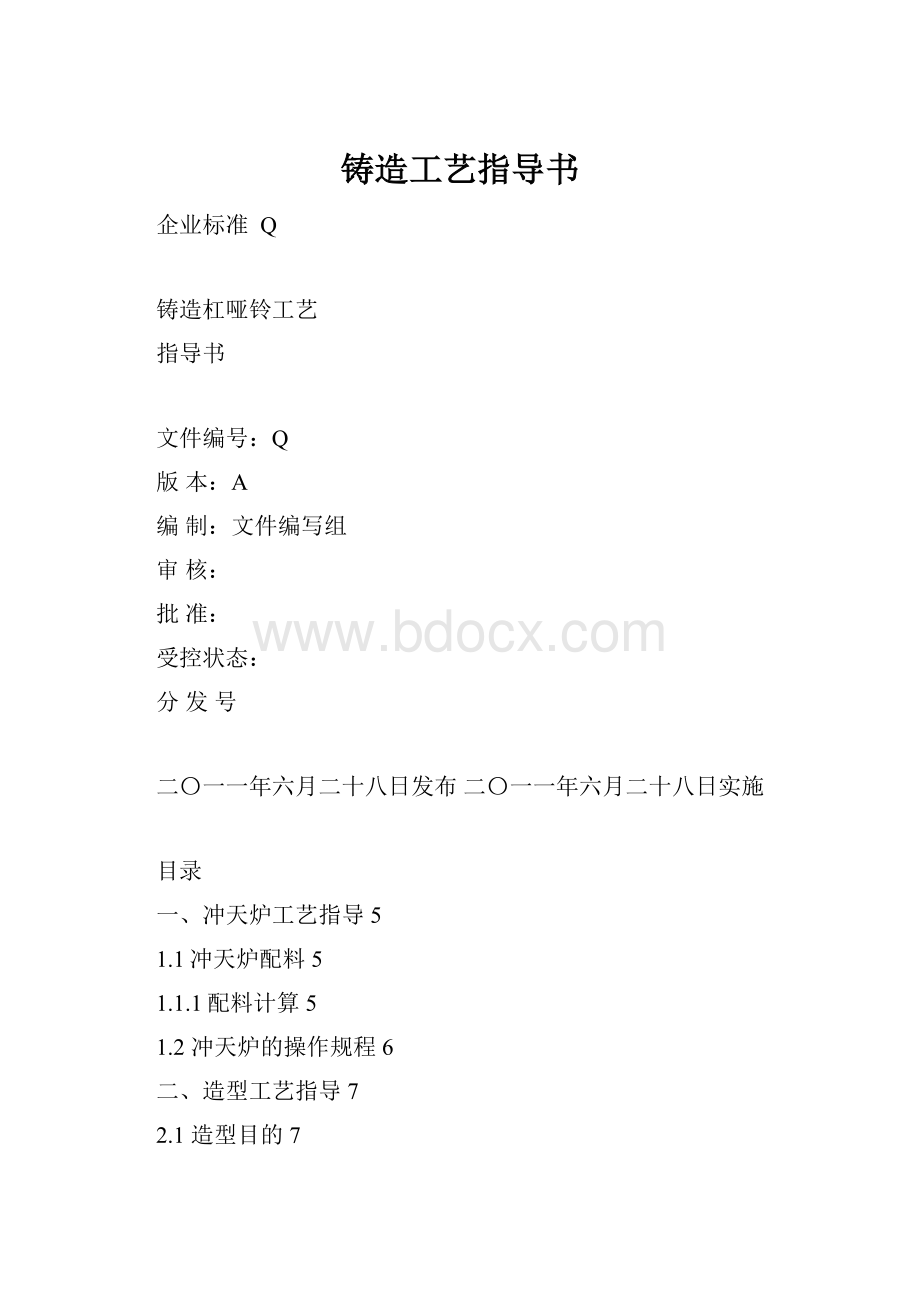
铸造工艺指导书
企业标准Q
铸造杠哑铃工艺
指导书
文件编号:
Q
版本:
A
编制:
文件编写组
审核:
批准:
受控状态:
分发号
二〇一一年六月二十八日发布二〇一一年六月二十八日实施
目录
一、冲天炉工艺指导5
1.1冲天炉配料5
1.1.1配料计算5
1.2冲天炉的操作规程6
二、造型工艺指导7
2.1造型目的7
2.2作业内容7
2.2.1造型准备:
7
2.2.2参数设定:
7
2.2.3造型:
7
2.3造型操作规程9
2.3.1.造型准备9
2.3.2造型9
2.3.3检查、修型9
2.3.4合型11
三、浇注作业指导11
3.1浇注准备11
3.2浇注12
3.3规程细则13
3.4生产安全:
15
四、抛丸作业指导15
4.1抛丸目的15
4.2抛丸机15
4.3抛丸滚筒操作工艺16
4.4电气设备的操作次序:
17
4.4清理滚筒工艺19
4.5维护保养与使用安全19
五、机加工工艺指导书21
5.1作业要求21
5.2各工段操作规程21
5.2.1车工安全技术操作规程21
5.2.2磨工安全技术操作规程22
5.2.3砂轮磨刀工安全技术操作规程24
5.2.4刨床安全操作规程24
5.2.5铣工安全技术操作规程25
5.2.6钻工安全技术操作规程27
5.2.7钳工安全技术操作规程28
5.2.8焊接工、喷焊工安全技术操作规程29
5.3保养事项31
六、浸塑作业指导32
6.1浸塑的重要性32
6.2浸塑工艺流程32
6.3浸塑的操作规程32
七、包胶作业指导33
八、烤漆作业指导34
纸箱车间35
附录37
一、冲天炉工艺指导
1.1冲天炉配料
冲天炉,铁液成分易发生偏差。
同时,冲天炉熔炼往往使用数种质量等级不同的铸造生铁,这一切都要求配料必须认真计算,使用传统的试算法、表格法和联立方程求解法已不可能。
大型冲天炉,多设炉前化验设施,这为调整成分提供了方便,铁液成分发生了偏差,通过调整计算,可以及时调整。
1.1.1配料计算
根据技术标准和铸件结构特点,合理确定铸件(铁液)成分。
该成分必须经过实践考验,不能简单的抄自某些手册的平均值。
根据各厂不同情况,合理确定熔化过程中各元素的增减率。
一般应根据日常炉料成分与铁液成分进行换算。
(1)计算炉料要求成分.
即:
X炉=X件/(1+η)
式中X炉——炉料中某元素的要求含量,
X件——铸件(铁液)中某元素的要求含量,
η——熔化过程中,各元素的增减率。
生产之前,X炉应该预先计算好,公布到炉前。
计算Si炉时,首先应从Si件中减去孕育(以及球化或蠕化)处理铁液时的增硅量。
(2)计算钢铁预加量
常规生铁预加量(kg)=批料总量(kg)×[(C炉-C钢)/(C铁-C钢)]×Yb×(1-Hy)
回炉铁预加量(kg)=批料总量(kg)×[(C炉-C钢)/(C回-C钢)]×Hy
废钢预加量(kg)=批料总量(kg)-各种常规生铁预加量(kg)-回炉铁预加量(kg)
式中C炉——炉料要求含碳量;
C钢——废钢含碳量
C铁——各种常规生铁含碳量
C回——回炉铁含碳量
Yb——各种常规生铁预加比。
Hy——回炉铁预加比。
根据回炉铁库存数量确定。
(3)计算硫(磷)平均含量
硫(磷)平均含量=[Σ各种炉料预加量(kg)×各种炉料硫(磷)含量(%)]/批料总量(kg)
(4)计算高硫(磷)生铁允许使用量
允许使用量(kg)=批料总量(kg)×[S(P)-硫(磷)平均含量(%)]/高硫(磷)生铁中硫(磷)含量(%)
(5)计算常规生铁实际加入量
常规生铁实际加入量(kg)=常规生铁预加量(kg)-高硫(磷)生铁允许用量(kg)
(6)计算废钢和回炉铁实际加入量
废钢实际加入量(kg)=废钢预加量(kg)-废钢调整量(kg)
回炉铁实际加人量(kg)=回炉铁预加量(kg)+废钢调整量(kg)
1.2冲天炉的操作规程
(1)冲天炉在开路前,必须清除炉坑周围所有的障碍物,工作场地、炉前坑和炉底部不得积水,不准堆放易燃、易爆物品。
(2)检查吊车、钢丝绳和各种吊具,确保安全可靠。
(3)检查底板、前炉和后炉炉门、前炉盖和风眼盖等部分,确保牢固密封。
(4)检查铁水包、出铁槽和各种开炉工具,应确保烘干、齐备、完好。
(5)出铁前,应对准出铁槽放正铁水包,出铁时,操作人员必须站在出铁槽侧面,并带好防护眼镜。
(6)保持冲天炉风眼畅通。
(7)禁止将冷湿铁棒与铁水接触,加入铁水的各类合金均应预热烘干,防止铁水喷溅伤人。
(8)吊炉盖时,必须挂牢,人离开后再起吊。
(9)冲天炉内炉料发生“栅料”时,应立即停风并打开全部盖,出净渣、铁,用铁棒撞击料层。
(10)打炉时,必须清理周围现场,人离开后方可打炉,并用水冷却剩余的铁水和炉料,防止火灾发生。
(11)工作完毕,要清理炉前和炉子周围场地,保持整洁,通道畅通。
二、造型工艺指导
2.1造型目的
为使造型作业有所依据,以保证生产顺利进行,特制定之。
2.2作业内容
2.2.1造型准备:
按照型板及芯框装卸规定安装型板,吹扫干净并由班长检查确认。
2.2.2参数设定:
按照所生产产品《造型作业标准》中的要求设定所有参数,由班长检查确认,并记录在造型日报表上。
首模造型时用手动缓慢合紧造型室,检查是否有撞型的危险防止撞模。
2.2.3造型:
按照《造型机设备操作》操作造型机进行造型作业。
造型作业中检查造型的前5模,重点检查是否有以下几种缺陷,并将检查结果记录在生产日报上;(_zo|_Vg2_XA粘板、B掉砂、C松砂模)
检查下芯的前5模,重点检查是否有以下几种缺陷,并将检查结果记录在生产日报上;(o__8_wU#_A砂芯放置位置、B擦砂、C断芯)v/--3T9_
每更换型板后,检查脱模剂喷洒位置正确,脱模剂的喷洒依《造型作业标准》,应能保证良好拔模。
ve"_NI7_%a
操作工每十分钟检查型腔的吹扫情况、型板无带砂、掉砂;下芯到位、无擦砂。
e)___90LM
砂模硬度每批产品检测一次,检查位置为型腔内壁;砂模硬度规格:
70-80。
p*_p9_SZL
每小时班长确认检查吹扫型腔的风管位置及风向正确,风压合适。
k?
|w~s{__M
每次更换模板,班长确认造型机射砂压力、挤压压力、合模压力等参数满足《造型作业标准》要求,操作者检查储砂量是否充足,检查砂模厚度有无异常变动。
lvHns_6f0
操作工每十分钟检查模具批号在造型过程中无脱落,每20分钟检查脱模剂喷嘴位置应正确。
qr^p%1*Q|_ CfCD6_DG|_
造型过程中对所有生产、质量定时检查信息应及时填写入《造型日报表》。
l,_{Dg
每种产品的每天的生产数量要及时汇总。
.qq>Wn_+_
2.2.4换模板
造型结束,拆卸模具、下芯框;检查换下之模板,有问题立即送模具维修室修理。
_4!
x^_=
换下的模板吹扫干净,并上防锈油。
__!
_8U__y
所有更换下的模具、下芯框连同模具卡交模具维修站检查并保存。
_:
__D`4__
注:
生产过程中如发现异常(如:
粘板、模型松动等问题),应及时联络相关部门处理,并记录在《造型生产日报》内。
^Yh8$:
__aA
2.3造型操作规程
2.3.1.造型准备
1.检查模具型号是否与生产型号相同,模具铸字标示是否齐全、完好、符合要求。
详细要求见该产品《毛坯作业指导书》——造型工序。
2.模具及平板是否有损坏、破裂及变形现象。
若有应立即修理。
3.查看砂箱是否与《毛坯作业指导书》——造型工序中规定的砂箱规格形同。
4.检查砂箱是否完好,有无破裂,如破裂应及时更换或修理,并清除粘砂及锈皮等附着物。
2.3.2造型
1.用铁锨将地面弄平,把模具放在上面,两人握紧砂箱把手抬起并轻放在模具平板上,使之装配完好。
加少量面砂紧实,然后逐层加面砂并均匀紧实,直至模型全部覆盖。
2.逐层加背砂至砂箱充满并均匀紧实,刮去箱面多余型砂。
3.在箱面上均匀扎5mm出气孔。
数量10-20个左右。
4.翻转模型及砂箱,并使箱面稳固接触在平整地面上,轻轻敲击模型使之松动,取出模型。
2.3.3检查、修型
1.仔细检查砂型是否完好,有无掉砂(块)现象,进行必要的修型,如无法修型则报废。
2.修型时,一定要确保型腔形状、尺寸准确,表面光滑。
3.检查铸字是否完好,有无缺损、漏字,铸字位置是否正确,若有不符合要求的应修整后重新按字。
2.3.4合型
1.将上砂型立于平整地面上放好,使之不能晃动。
2.用压缩空气吹净上、下砂型中的浮砂。
3.四人握住上砂型手柄将之轻轻抬起,并轻放于下砂型上,检查止扣是否合上。
锁紧箱卡,准备浇注。
三、浇注作业指导
3.1浇注准备
1浇注工应全面了解当日的浇注铸件的材质、重量及要求的浇注温度。
大炉班组长或炉前控制人员应与包长安排好浇注顺序。
2.铁水出炉前应与车工联系好,配合好,保证起吊设备工作正常,充分做好出炉浇注准备。
3.检查浇包的修理与烘干质量,不合格的浇包由包长上报组长处理。
4.清除浇注通道的不安全因素。
5.备好保温、聚渣的材料和挡渣扒渣的工具及倒剩余铁液的铁模。
6.检查砂箱卡子、压铁块、不合时要上报组长处理。
7.砂型的浇口杯应摆在同一直线上,保证浇注顺利进行。
8.球化处理要快,扒渣应人等包,不得延续时间,浇包从吊出炉坑开始至扒渣完,1、2、3吨包用时应≤3分钟,5吨、7吨包≤5分钟。
铁水转跨,天车工及浇注人员也照执行,否则车间要给予处罚。
3.2浇注
浇注现场生产组织工作由造型班组长负责,浇注顺序、温度、材质控制等技术问题,由技术员和炉前控制人员负责。
出铁时,铁液流应冲入浇包中心,不准冲在包壁上或冲在包梁上。
吊包中铁液面原则上应低于包口30mm~50mm,吊运时应上好保险(主、副)。
第一次盛铁液的浇包或大修后的浇包,在烘烤后先盛上少量铁水烫包(烫包后合掉),使浇包充分干透,防止呛火。
冲天炉的第一包铁液浇芯骨、冷铁或不重要件。
按铸件材质、浇注温度、浇注顺序进行浇注。
浇注时,包咀撒聚渣剂,浇包咀尽量接近浇口杯。
浇口杯应保持充满,并不应引起铁液飞溅或产生漩涡。
吊包浇注必须三人操作,否则,按违反工艺纪律进行处罚。
浇注时,应注意挡渣、引气。
浇注中如果发生跑火,必须采取措施。
轻者细流慢浇,同时堵漏,严重者,上报值班主任。
交界铁水应征得炉前控制人员同意方可浇注工艺许可的铸件。
标牌、标识不明不倒火(材质、重量、产品型号)。
出现批量废品的件,若大炉已反馈,询问炉前技术员,白班工没采取措施,不倒火,但应上报技术主任。
低温铁水不应倒铸件。
铁水温度控制:
壁厚<3-5mm,HT浇注温度应>1400℃,QT>1360℃
壁厚为5-10mm,HT浇注温度应>1380℃~1420℃,QT>1350℃
壁厚为20-40mm,HT浇注温度应>1350℃,QT>1340℃
壁厚为>40mm,HT浇注温度应>1300℃,QT>1300℃
铁水牌号不同,不得搭配倒火,严格控制案牌号进行浇注。
铁水量不足不得浇注,灰铁、球铁包根铁水应合火。
小端包不撒界砂和无人打扫,不许倒火。
小端包每天空活后应按工艺进行修搪,并充分烘干,否则,按违犯工艺纪律车间进行一次性处罚。
潮模牙子箱不压箱,不得倒火(由造型工负责)。
浇口杯没按工艺、不符合规定,严重者不倒火,大炉应信息反馈。
每包火打火后应进行扒渣、保温处理。
合铁模的铁水,冷却后吊出兵进行分类存放。
浇注结束后应与组长取得联系,将浇注信息进行反馈,班组长应认真填写浇注纪录。
浇注工应清理浇注现场,现场不应有铁片及其它杂物。
3.3规程细则
1.浇注工必须全面熟悉所浇铸件的工艺文件,浇注前应了解浇注顺序、所需钢水材质、重量以及铸型的分布情况。
2.检查浇包数量、修包质量以及烘干预热等是否合格,天车运行是否正常。
3.消除浇注通道的不安全因素。
4.检查砂箱卡子、锁箱螺栓是否紧实牢固,压铁重量和位置是否合适,冒口圈、浇口杯、浇口塞等是否安放妥当。
5.按浇注顺序,工艺要求以及铸件要求的浇口塞等是否安放妥当。
6.浇注时注孔要对准浇口杯,按照慢-快-慢的原则一次注满,不许断流。
7.浇注开始后应立即引气,边浇注边引气,大型铸件应点燃出气孔旁的引火材料。
8.浇注大件时,浇完后从冒口点注一、二次,点浇前必须将冒口的薄壳撬开。
9.需要加覆盖剂的铸件,在钢水浇至冒口高度1/3时按规定数量投放。
10.浇注后应立即铲除从水口、冒口上溢出的钢水,并去掉浇口杯,以利于落砂及铸件的正常收缩。
11.待钢水完全凝固后,铸型方可移动。
12.浇注后期,注意包中钢水量,对于重要件和150Kg以上铸件不允许出现喝渣现象。
13.将剩余的钢水倒入剩余槽(型)内。
14.浇剩的砂型要将浇冒口盖好,以便重新安排.如果砂型存放时间不超过48小时,可以正常浇注.如果超过48小时,则应检查确认铸型是否符合要求,方可决定能否浇注。
15.浇注完毕由浇铸本人如实填写《浇注记录表》。
16.浇注完毕后,应全面检查、清理现场,并熄灭火源。
3.4生产安全:
1、工作前应穿戴好劳动保护用品。
2、浇注使用的全、架要安全可靠。
3、经常检查吊具,吊包等是否安全可靠。
4、炉前与浇注区不得有积水。
5、铁水包不可盛得太满,出铁和吊运时要上好安全卡。
6、浇注过程中不要直接窥视冒口。
7、挡渣工站立位置不要正对包嘴。
8、搬压铁或其他重物要小心谨慎。
9、包里剩余铁水应倒入回炉铁模内,不得随地乱倒。
10、浇注时,闲人不得靠近。
11、浇注结束后,清理场地。
四、抛丸作业指导
4.1抛丸目的
主要清除铸件粘砂和表面异物,铲磨割筋、披缝和毛刺等凸出物,以及打磨和精整铸件表面以及表面缺陷的局部掩盖等。
4.2抛丸机
滚筒的壳体由铸铁制成,其内部用螺栓固定着铸钢护板,护板上有格子孔和螺旋的导筋,以便在工作时翻动工件,在护板与滚筒壳体之间也有回收弹丸用的螺旋带。
整个滚筒系统支承在机座的两对托轮上,由减速电动机,经链条和链轮带动托轮,托轮依靠摩擦使滚筒做低速回转。
因滚筒转速低,工件的撞伤,棱角外的磨损较少发生,由弹丸的反射作用,能清理形状较复杂的工件。
端盖设在滚筒的一端,故装卸料比较方便,便于更换护板及维修工作。
在清理零件时,首先根据被清理工件的情况,调整清理时间,将被清理的工件装入滚筒,关门按次序开动集尘器、抛丸器、最后开动滚筒进行清理,滚筒转动后,被清理工件在护板斜筋的作用下,不断地翻动,使表面受到均匀地清理,弹丸经护板的小孔流入外层滚筒体,在滚筒螺旋带的作用下,回收至箱形构架内,再由提升斗运送至分离器,筛去大的芯骨、毛刺等杂物。
细小的砂粒、尘土、弹丸末等,则被气流分离带走,完整的弹丸流入抛丸器内循环使用。
清理完毕后,依次停止抛丸器、滚筒、集尘器。
4.3抛丸滚筒操作工艺
1.抛丸滚筒开机生产前应检查现场是否有影响安全操作的障碍物,电器是否安全可靠,除尘器等处是否有不安全因素,抛头叶轮、叶片、护板是否完好。
2.上料后滚筒门要关紧,不允许有松动,先启动除尘机后再开抛头生产。
3.铸件清理好后先停抛头电机,再停滚筒电机,待停止后方可打开滚筒门卸料。
4.抛丸后的铸件,应放入指定的区域内;铸件的周转过程中,严禁碰伤与碰裂。
同一筒抛丸的铸件应壁厚,重量和形状相近,易碎、易裂的铸件不得采用抛丸滚筒工艺方式进行清理。
5.每周吹灰一次,每月对变速箱和需要加油的地方加油,以保证设备正常运转。
6.设备工作时人不允许离开场地,发现问题及时汇报,本机备件要堆放整齐。
7.搞好文明生产,保持场地整洁。
4.4电气设备的操作次序:
把滚筒端盖关闭以后,合上总开关2d后,电源电路接通。
(1)开始工作启动次序:
按下起动按钮SB2,接通电气控制线路。
按下启动按钮SB4,集尘器电动机M1开始动作。
按下启动按钮SB6,抛丸器电动机M2运转。
按下启动按钮SB8,滚筒电动机M3运转。
(2)工作停止掀动按钮的次序:
时间继电器KT1动作,抛丸器电动机M2自动停止运转。
限位开关SQ1动作,滚筒电动机M3停止运转。
掀下启动按钮SB3,集尘器电动机M1停止运转。
若出现非常工作情况时,按下启动按钮SB1,整机立即停止工作。
(3)需单独手动非计时启动停止工作的次序:
按下SB5按钮,抛丸器电动机M2停止运转。
按下SB7按钮,滚筒电动机M3停止。
按下SB3按钮,集尘器电动机M1停止运转。
(4)进行非计时工作时:
按下启动按钮SB4、KM1线圈通电,使其常开触点闭合,主触点接通,集尘电动机M1运转,辅助触点KM1由于自锁作用,使放开SB4时,不会使线路断电。
按下启动按钮SB6、KM2线圈通电,其中主触点闭合,辅助触点KM2的自锁作用,使SB6松开后仍然通路,同时继电器KM5线圈通电,常开触点闭合,主触点KM5与KM2形成通路,使M2电机运转。
从而KM5保护了热继电器FR2,不会使刚启动的抛丸电机M2因为电流过大使热继电器FR2断开而影响抛丸器电机M2的起动。
按下启动按钮SB8时,接触器KM2线圈通电,主触点KM3闭合,使滚筒电机M3运转,辅助触点KM3闭合,其自锁作用使松开的SB8不会使线路断电,同时KM3的常闭触点断开,KM5失电,使其触头断开,FR2担负工作。
按下按钮SB5接触器KM2线圈断电,主触点KM2断开,抛丸电机M2停止工作,辅助触点KM2恢复常开状态,撤掉SB5外力后,因接触器KM2线圈失电。
按下SB7接触器KM3线圈断电,主触头KM3断开,滚筒电机M3停止工作,辅助触点KM3断开,此时按下SB3按钮,
接触器KM1失电,使集尘电机M1停止运转。
(5)进行计时工作时:
集尘电机M1开动后,调整清理时间,按下起动SB6,抛丸电机运转。
按下按钮SB8,滚筒电机M3运转,同时计时器KT1得电、计时。
计时到达终点后,时间继电器KT1常闭触头断开,交流接触器KM2线圈失电,主触头恢复常开,抛丸电机停止运转,辅助触头KM2使抛丸控制线路永久断电,辅助触头KM2断开。
抛丸器停止后,滚筒再旋转一周,限位开关SQ1动作后,使滚筒电机M3停止工作。
按下按钮SB3,除尘电机M1停止工作。
4.4清理滚筒工艺
1.工作前清除场地周围不安全的障碍物。
2.用滚筒清理的铸件必须壁厚,重量和形状相近,滚筒料上好拧紧料门螺钉后方可开车生产。
3.操作人员在工作时不允许远离现场,并经常检查设备运转情况,如发现异常立即停车修理。
4.爱护设备,及时更换易损件,每月给减速箱加油一次,保证设备运转正常。
5.搞好文明生产,保持清理滚筒场地周围整洁。
4.5维护保养与使用安全
1.未经学习本机操作及使用说明的人员,一律不允许操作。
2.当抛丸器叶轮未完全停止运转时,不允许打开端盖,打开端盖前应将全部电门按钮断电。
3.每一工作班后,均应将机器扫清一遍,并检查各易损件的使用情况,当发现有严重损坏时即应更换。
4.各种铸件在清理之前,应先进行落砂,否则滚筒内积砂过多,影响分离效果,且加快零件的磨损。
5.更换分丸办程序,先卸开分离器与导入管连接的两螺钉,然后用木锤轻打导入管,待其松动时取下,然后用套筒板手取下固定螺母(左螺旋),即可取下分配轮。
6.更换定向套程序:
首先取下分丸轮,然后拆下固定压块的螺钉,即可用手取出。
如果因砂末,弹丸阻塞而不易直接取出时,也可同定向套压圈一同取出。
7.更换叶片次序:
先取出叶片紧固螺钉,然后用木锤轻打叶片而取下,安装时螺孔内的弹丸末要预先用丝攻全部赶出,否则会损坏圆盘上的螺纹线。
五、机加工工艺指导书
5.1作业要求
凡机械加工件必须符合产品图样、工艺规程和作业要求。
经加工的零件表面不允许有锈蚀和磕碰、划伤、裂纹等缺陷。
除有特殊要求外,加工后的零件不允许留有尖棱、尖角和毛刺。
滚压精加工的表面,滚压后不得有剥离及脱皮现象。
精加工后的表面、摩擦面和定位面等工作表面不允许在其上打印标记。
经加工后的零件在搬运、存放时,必须防止受到损伤、腐蚀及变形。
成组配对加工的零件,如:
齿轮箱上下盖等需有标记。
5.2各工段操作规程
5.2.1车工安全技术操作规程
1.上机前规范穿戴好劳动保护用品,先检查线路电器及各手柄和润滑部位是否正常,正常后再进行合闸开机操作。
2.装卸卡盘及大的工、夹具时,床面要垫木板,不准开车装卸卡盘。
装卸工件后应立即取下扳手。
禁止用手刹车。
3.床头、小刀架、床面不得放置工、量具或其它东西。
4.装卸工件要牢固,夹紧时可用接长套筒,禁止用榔头敲打。
5.加工细长工件要用顶针、跟刀架。
车头(床头箱)前面伸出部分不得超过工件直径的20~25倍,车头(床头箱)后面伸出超过300毫米时,必须加托架。
必要时装设防护栏杆。
6.用锉刀光工件时,应右手在前,左手在后,身体离开卡盘。
禁止用砂布裹缠在工件上砂光,应比照用锉刀的方法,成直条壮压在工件上。
7.车内孔时不准用锉刀倒角,用砂布光内孔时,不准将手指或手臂伸进去打磨。
8.加工偏心工件时,必须加平衡铁,并要紧固牢靠,刹车不要过猛。
9.攻丝或套丝必须用工具,不准一手扶攻丝架(或拌牙架)一手开车。
10.切大料时,应留有足够余量,卸下砸断,以免切断时料掉下伤人。
小料切断时,不准用手接。
11.操作者在工作中不许离开工作岗位,如需离开时,无论时间长短,都应停车。
12.使用自动走刀时,先检查互锁机构是否可靠,否则应进行修理。
工作完毕后应将总闸拉下。
5.2.2磨工安全技术操作规程
1.工作前必须穿戴好劳动保护用品、禁止戴手套,围巾操作。
2.严格按照润滑图表的规定,进行机床的全部润滑。
3.要经常检查床座导轨的润滑是否良好,充足,以防止研损破坏其精度。
4.新砂轮一定要严格的检查,发现有裂纹时绝对不许使用,在使用前应经平衡检查,否则不许使用。
5.砂轮和法兰盘之间,应垫上0.6—2毫米纸板,砂轮夹盘直径不得小于砂轮直径的1/3。
6.砂轮直径使用减少到一定程度后应取下,再经平衡检查。
7.开始工作时,因砂轮是冷的,应慢慢的轻负荷送刀,使其温升,这样可避免破裂。
8.砂轮在试运转时,人应站在侧面,修磨砂轮时,应戴眼镜,金刚石应禁固在架子上,不可用手夹持工作,吃刀不能过猛。
9.工作台上不能放置工具杂物,砂轮启动转速稳定后,方可进刀,走刀速度和切削量应适当。
10.磨工件如发现火花减少或工件内光如镜时,说明砂轮已经钝化,应及时修正,否则不许继续使用。
11.在装卸工件清扫机床时,检查工件光洁度,必须停车进行,并让开砂轮。
12.在平面磨上,磨厚度较高的工件时,必须有适当高度的挡铁,一并吸牢,在工件上平磨小工件,应用辅助挡铁,挡牢,平磨薄量件时,必须重新打磨砂轮。
使用工装夹件时必须夹牢固。
13.开车时,不准用手清扫铁末、拭摸工件。
14.如因工件材质不同,需要换砂轮时,要将已换下的砂轮要求平放,不准立放。
15.在工作中无论使用大小砂轮都必须利用安全防护装置(如砂轮罩、防护板等),磨削外圆时,要经常检查工件与顶尖润滑情况。
16.操作者在工作中,不许离开