数控机床几何误差及其补偿方法研究.docx
《数控机床几何误差及其补偿方法研究.docx》由会员分享,可在线阅读,更多相关《数控机床几何误差及其补偿方法研究.docx(12页珍藏版)》请在冰豆网上搜索。
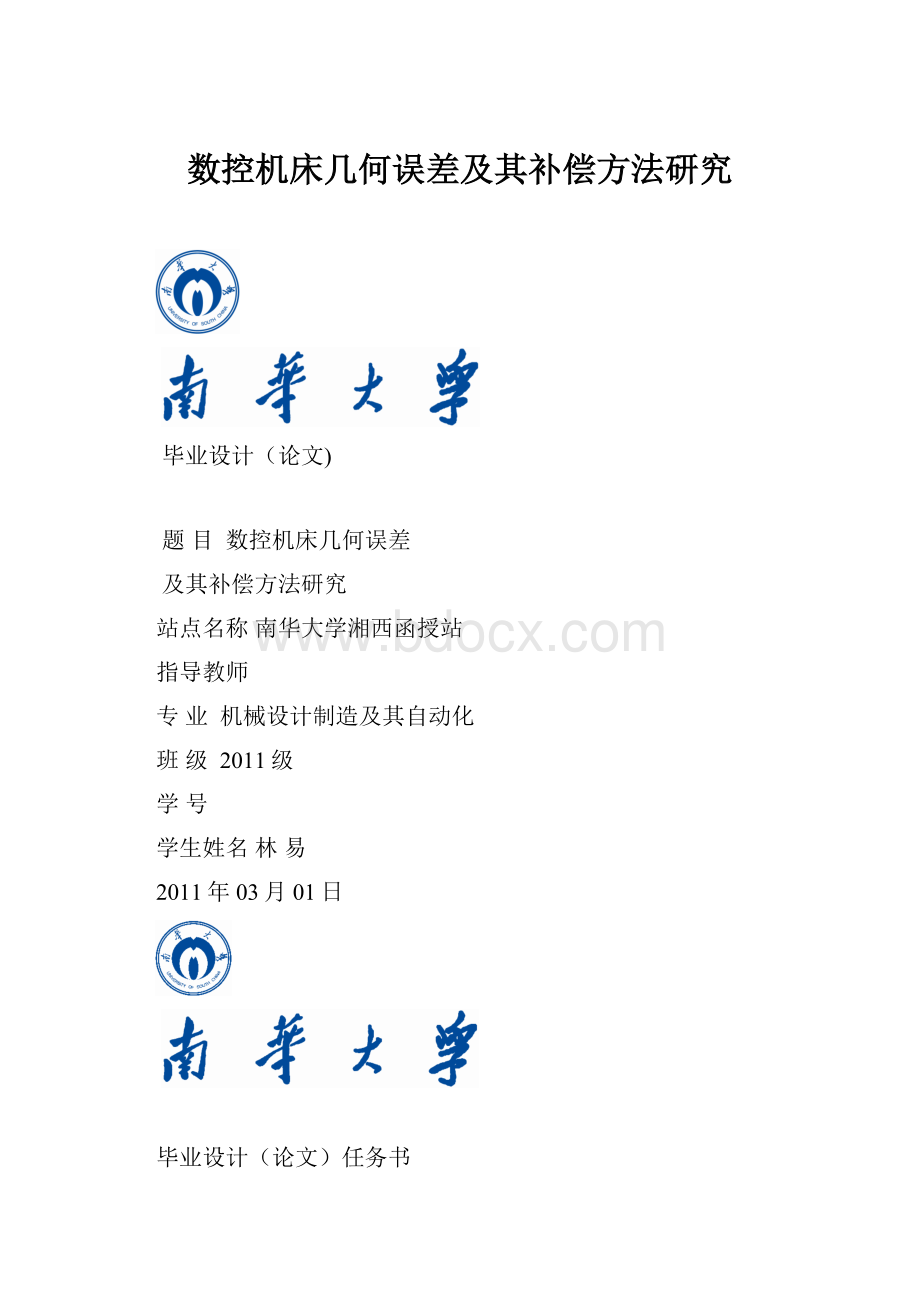
数控机床几何误差及其补偿方法研究
毕业设计(论文)
题目数控机床几何误差
及其补偿方法研究
站点名称南华大学湘西函授站
指导教师
专业机械设计制造及其自动化
班级2011级
学号
学生姓名林易
2011年03月01日
毕业设计(论文)任务书
站(点):
南华大学湘西函授站
题目:
数控机床几何误差
及其补偿方法研究
起止时间:
2010年03月01日
至2011年03月01日
学生姓名:
林易
专业班级:
机械设计制造及其自动化
指导教师:
站(点)负责人:
袁小波
2011年03月01日
南华大学毕业设计(论文)开题报告
设计(论文)题目
数控机床几何误差及其补偿方法研究
设计(论文)题目来源
自选
设计(论文)题目类型
起止时间
一、设计(论文)依据及研究意义:
研究表明,几何误差和由温度引起的误差约占机床总体误差的70%,其中几何误差相对稳定,易于进行误差补偿。
对数控机床几何误差的补偿,可以提高整个机械工业的加工水平,对促进科学技术进步,提高我国国防能力,继而极大增强我国的综合国力都具有重大意义。
二、设计(论文)主要研究的内容、预期目标:
(技术方案、路线)
文中通过对检测系统的测试误差的分析,得出几何误差产生的原因。
进行数控机床的误差补偿,误差测量是关键,误差模型是基础。
通过误差的补偿,可以有效的提高机床的精度,为提升我国制造业水平作贡献。
三、设计(论文)的研究重点及难点:
对数控机床几何误差产生的原因作了比较详细的分析,将系统误差的补偿方法进行了归纳
四、设计(论文)研究方法及步骤(进度安排):
(1)首先了解数控机床的组成及其结构,分析出几何误差产生的原因,检测误差的方法
(2)了解几何误差补偿技术,学会用误差补偿技术来减小误差
五、进行设计(论文)所需条件:
1.倪军。
数控机床误差补偿研究的回顾与展望[J].中国机械工程,1997,8
(1):
29~32。
2.RameshR,MannanMA,PooAN.Errorcompensationinmachinetools—areviewpartI:
geometric,cutting—forceinducedandfixture—dependenterrors。
InternationalJournalofMachineTools&Manufacture,2000,40:
1235~1256。
3.J.Ni,Studyononlineidentificationandforecastingcompensatorycontrolofvolumetricerrorsformultipleaxismachinetools。
PhDdissertation,UniversityofWisconsin-Madison,1987.
六、指导教师意见:
签名:
年月日
数控机床几何误差及其补偿方法研究
机械设计制造及其自动化专业专升本科
摘要
对数控机床几何误差产生的原因作了比较详细的分析,将系统误差的补偿方法进行了归纳,并在此基础上阐述了各类误差补偿方法的应用场合,为进一步实现机床精度的软升级打下基础。
关键词 数控机床;几何误差;误差补偿
CNCmachinetoolgeometricerrorandtheircompensationmethodsresearch
Abstract
OnthecausesofCNCmachinetoolgeometricerrormadeamoredetailedanalysis,thesystemhascarriedontheinduction,theerrorcompensationmethodbasedontheapplicationsofallkindsoferrorcompensationmethodwasdescribed,inordertofurtherrealizethemachinetoolaccuracyofsoftgroundwork。
Keywords:
Numericalcontrolmachinetools;Geometricerrors;Errorcompensation
目 录
前言...............................................1
一 几何误差产生的原因.............................2
1。
1 机床的原始制造误差...............................2
1.2 机床的控制系统误差...............................2
1.3 热变形误差.....................................2
1。
4 切削负荷造成工艺系统变形所导致的误差...............2
1。
5 机床的振动误差.....................................2
1。
6 检测系统的测试误差..................................3
1。
7 外界干扰误差........................................3
1.8 其它误差........................................3
二 几何误差补偿技术..............................4
2。
1 单项误差合成补偿法................................4
2。
2 误差直接补偿法..................................5
2。
3 相对误差分解、合成补偿法...........................6
参考文献...........................................8
前言
提高机床精度有两种方法。
一种是通过提高零件设计、制造和装配的水平来消除可能的误差源,称为误差防止法(errorprevention)。
该方法一方面主要受到加工母机精度的制约,另一方面零件质量的提高导致加工成本膨胀,致使该方法的使用受到一定限制。
另一种叫误差补偿法(errorcompensation),通常通过修改机床的加工指令,对机床进行误差补偿,达到理想的运动轨迹,实现机床精度的软升级.研究表明,几何误差和由温度引起的误差约占机床总体误差的70%,其中几何误差相对稳定,易于进行误差补偿。
对数控机床几何误差的补偿,可以提高整个机械工业的加工水平,对促进科学技术进步,提高我国国防能力,继而极大增强我国的综合国力都具有重大意义.
一 几何误差产生的原因
普遍认为数控机床的几何误差由以下几方面原因引起:
1.1 机床的原始制造误差
是指由组成机床各部件工作表面的几何形状、表面质量、相互之间的位置误差所引起的机床运动误差,是数控机床几何误差产生的主要原因。
1.2 机床的控制系统误差
包括机床轴系的伺服误差(轮廓跟随误差),数控插补算法误差。
1。
3 热变形误差
由于机床的内部热源和环境热扰动导致机床的结构热变形而产生的误差.
1.4 切削负荷造成工艺系统变形所导致的误差
包括机床、刀具、工件和夹具变形所导致的误差。
这种误差又称为“让刀”,它造成加工零件的形状畸变,尤其当加工薄壁工件或使用细长刀具时,这一误差更为严重.[摘自领硕学术网www.lsxueshu。
com]
1。
5 机床的振动误差
在切削加工时,数控机床由于工艺的柔性和工序的多变,其运行状态有更大的可能性落入不稳定区域,从而激起强烈的颤振。
导致加工工件的表面质量恶化和几何形状误差。
1.6 检测系统的测试误差
包括以下几个方面:
(1)由于测量传感器的制造误差及其在机床上的安装误差引起的测量传感器反馈系统本身的误差;
(2)由于机床零件和机构误差以及在使用中的变形导致测量传感器出现的误差。
1。
7 外界干扰误差
由于环境和运行工况的变化所引起的随机误差.
1.8 其它误差
如编程和操作错误带来的误差。
上面的误差可按照误差的特点和性质,归为两大类:
即系统误差和随机误差。
数控机床的系统误差是机床本身固有的误差,具有可重复性。
数控机床的几何误差是其主要组成部分,也具有可重复性。
利用该特性,可对其进行“离线测量”,可采用“离线检测-—开环补偿"的技术来加以修正和补偿,使其减小,达到机床精度强化的目的。
随机误差具有随机性,必须采用“在线检测——闭环补偿”的方法来消除随机误差对机床加工精度的影响,该方法对测量仪器、测量环境要求严格,难于推广。
二 几何误差补偿技术
针对误差的不同类型,实施误差补偿可分为两大类。
随机误差补偿要求“在线测量”,把误差检测装置直接安装在机床上,在机床工作的同时,实时地测出相应位置的误差值,用此误差值实时的对加工指令进行修正.随机误差补偿对机床的误差性质没有要求,能够同时对机床的随机误差和系统误差进行补偿。
但需要一整套完整的高精度测量装置和其它相关的设备,成本太高,经济效益不好。
文献[4]进行了温度的在线测量和补偿,未能达到实际应用.系统误差补偿是用相应的仪器预先对机床进行检测,即通过“离线测量”得到机床工作空间指令位置的误差值,把它们作为机床坐标的函数。
机床工作时,根据加工点的坐标,调出相应的误差值以进行修正。
要求机床的稳定性要好,保证机床误差的确定性,以便于修正,经补偿后的机床精度取决于机床的重复性和环境条件变化。
数控机床在正常情况下,重复精度远高于其空间综合误差,故系统误差的补偿可有效的提高机床的精度,甚至可以提高机床的精度等级.迄今为止,国内外对系统误差的补偿方法有很多,可分为以下几种方法:
2。
1 单项误差合成补偿法
这种补偿方法是以误差合成公式为理论依据,首先通过直接测量法测得机床的各项单项原始误差值,由误差合成公式计算补偿点的误差分量,从而实现对机床的误差补偿。
对三坐标测量机进行位置误差测量的当属Leete,运用三角几何关系,推导出了机床各坐标轴误差的表示方法,没有考虑转角的影响。
较早进行误差补偿的应是Hocken教授,针对型号Moore5—Z
(1)的三坐标测量机,在16小时内,测量了工作空间内大量的点的误差,在此过程中考虑了温度的影响,并用最小二乘法对误差模型参数进行了辨识.由于机床运动的位置信号直接从激光干涉仪获得,考虑了角度和直线度误差的影响,获得比较满意的结果.1985年G。
Zhang成功的对三坐标测量机进行了误差补偿。
测量了工作台平面度误差,除在工作台边缘数值稍大,其它不超过1μm,验证了刚体假设的可靠性。
使用激光干涉仪和水平仪测量得的21项误差,通过线性坐标变换进行误差合成,并实施了误差补偿。
X—Y平面上测量试验表明,补偿前,在所有测量点中误差值大于20μm的点占20%,在补偿后,不超过20%的点的误差大于2μm,证明精度提高了近10倍。
除了坐标测量机的误差补偿以外,数控机床误差补偿的研究也取得了一定的成果.在1977年Schultschik教授运用矢量图的方法,分析了机床各部件误差及其对几何精度的影响,奠定了机床几何误差进一步研究的基础。
Ferreira和其合作者也对该方法进行了研究,得出了机床几何误差的通用模型,对单项误差合成补偿法作出了贡献.J。
Nietal更进一步将该方法运用于在线的误差补偿,获得了比较理想的结果.Chenetal建立了32项误差模型,其中多余的11项是有关温度和机床原点误差参数,对卧式加工中心的补偿试验表明,精度提高10倍。
Eung—SukLeaetal几乎使用了同G.Zhang一样的测量方法,对三坐标Bridgeport铣床21项误差进行了测量,运用误差合成法得出了误差模型,补偿后的结果分别用激光干涉仪和Renishaw的DBB系统进行了检验,证明机床精度得以提升。
2.2误差直接补偿法
这种方法要求精确地测出机床空间矢量误差,补偿精度要求越高,测量精度和测量的点数就要求越多,但要详尽地知道测量空间任意点的误差是不可能的,利用插值的方法求得补偿点的误差分量,进行误差修正,该种方法要求建立和补偿时一致的绝对测量坐标系.
1981年,Dufour和Groppetti在不同的载荷和温度条件下,对机床工作空间点的误差进行了测量,构成误差矢量矩阵,获得机床误差信息。
将该误差矩阵存入计算机进行误差补偿。
类似的研究主要有A。
C。
Okaforetal,通过测量机床工作空间内,标准参考件上多个点的相对误差,以第一个为基准点,然后换算成绝对坐标误差,通过插值的方法进行误差补偿,结果表明精度提高了2~4倍。
Hooman则运用三维线性(LVTDS)测量装置,得到机床空间27个点的误差(分辨率0。
25μm,重复精度1μm),进行了类似的工作.进一步考虑到温度的影响,每间隔1。
2小时测量一次,共测量8次,对误差补偿结果进行了有关温度系数的修.这种方法的不足之处是测量工作量大,存储数据多。
目前,还没有完全合适的仪器,也限制了该方法的进一步运用和发展。
2。
3相对误差分解、合成补偿法
大多数误差测量方法只是得到了相对的综合误差,据此可以从中分解得到机床的单项误差。
进一步利用误差合成的办法,对机床误差补偿是可行的。
目前,国内外对这方面的研究也取得一定进展.
2000年美国Michigan大学JunNi教授指导的博士生ChenGuiquan做了这样的尝试,运用球杆仪(TBB)对三轴数控机床不同温度下的几何误差进行了测量,建立了快速的温度预报和误差补偿模型,进行了误差补偿.Christopher运用激光球杆仪(LBB),在30分钟内获得了机床的误差信息,建立了误差模型,在9个月的时间间隔内,对误差补偿结果进行了5次评价,结果表明,通过软件误差补偿的方法可以提高机床的精度,并可保持精度在较长时间内不变.
误差合成法,要求测出机床各轴的各项原始误差,比较成熟的测量方法是激光干涉仪,测量精度高。
用双频激光干涉仪进行误差测量,需时间长,对操作人员调试水平要求高.更主要的是对误差测量环境要求高,常用于三坐标测量机的检测,不适宜生产现场操作。
相对误差分解、合成补偿法,测量方法相对简单,一次测量可获得整个圆周的数据信息,同时可以满足机床精度的检测和机床评价。
目前也有不少的误差分解的方法,由于机床情况各异,难以找到合适的通用数学模型进行误差分解,并且对测量结果影响相同的原始误差项不能进行分解,也难以推广应用。
误差的直接补偿法,一般以标准件为对照获得空间矢量误差,进行直接补偿,少了中间环节,更接近机床的实用情况。
但获得大量的信息量需要不同的标准件,难以实现,这样补偿精度就受到限制.
在国内,许多研究机构与高校近几年也进行了机床误差补偿方面的研究。
1986北京机床研究所开展了机床热误差的补偿研究和坐标测量机的补偿研究.1997年天津大学的李书和等进行了机床误差补偿的建模和热误差补偿的研究。
1998年天津大学的刘又午等采用多体系统建立了机床的误差模型,给出了几何误差的22线、14线、9线激光干涉仪测量方法,1999年他们还对数控机床的误差补偿进行了全面的研究,取得了可喜的成果。
1998年上海交通大学的杨建国进行了车床热误差补偿的研究.1996到2000年在国家自然科学基金和国家863计划项目的支持下,华中科技大学开展了对数控机床几何误差补偿以及基于切削力在线辩识的智能自适应控制的研究,取得了一些成果。
综上所述:
进行数控机床的误差补偿,误差测量是关键,误差模型是基础。
通过误差的补偿,可以有效的提高机床的精度,为提升我国制造业水平作贡献.
参考文献
1.倪军。
数控机床误差补偿研究的回顾与展望[J]。
中国机械工程,1997,8
(1):
29~32。
2.RameshR,MannanMA,PooAN。
Errorcompensationinmachinetools—areviewpartI:
geometric,cutting-forceinducedandfixture—dependenterrors.InternationalJournalofMachineTools&Manufacture,2000,40:
1235~1256.
3.J.Ni,Studyononlineidentificationandforecastingcompensatorycontrolofvolumetricerrorsformultipleaxismachinetools。
PhDdissertation,UniversityofWisconsin—Madison,1987.
4.RameshR,MannanMA,PooAN。
Errorcompensationinmachinetools—areviewPartII:
thermalerrors.InternationalJournalofMachineTools&Manufacture,2000,40:
1257~1284.
5.LeeteDJ.Automaticcompensationofalignmenterrorinmachinetools。
InternationalJournalofMachineToolDesignandResearch,1961,1:
293~324.
6.HockenR,Simpson,A。
J。
,etat。
Threedimensionalmetrology.AnnalsoftheCIRP,1977,26
(2):
403~408。
7.ZhangG,VealeR,CharltonT,BorchardtB,HockenR。
Errorcompensationofcoordinatemeasuringmachines。
AnnalsoftheCIRP,1985,34
(1):
445~448.
8.SchultschikR.Thecomponentsofthevolumetricaccuracy。
AnnalsoftheCIRP,1977,25
(1):
223~228。
9.KiridenaV,FerriraP.Kinematicmodelingofquasi-staticerrorsofthree-axismachinecenters.Int.J。
Mach.ToolsManufact。
1994,34
(1):
85~100.
10.NiJ.andS。
M.Wu。
Anon-linemeasurementtechniqueformachinevolumetricerrorcompensation。
Journalofengineeringforindustry,1993,115:
85~92。
11.ChenJS,YuanJ,NiJ,WuSM.Real—timecompensationfortime—variantvolumetricerrorsonamachiningcenter,TransactionsoftheASME,journalofEngineeringIndustry,1993,115:
472~479.
12.Eung-SukLee,Suk-HwanSuhandJin-WookShon。
Acomprehensivemethodforcalibrationofvolumetricpositioningaccuracyofcnc—machines。
Advancedmanufacturingtechnology,1998,14
(1):
43~49。
13.DufourP,GroppettiR。
ComputeraidedaccuracyimprovementinlargerNCmachinetools。
M.T。
D.R。
ConferenceProceedings,1988,22:
611~618.
14.A。
C.Okafor,YalcinM.Ertekin。
Derivationofmachinetoolerrormodelsanderrorcompensationprocedureforthreeaxesverticalmachiningcenterusingrigidbodykinematics。
InternationalJournalofMachineToolsandManufacturing,2000,40:
1199~1213.
15.HoomanTajbakhsh,ZainulAbadinandPlacidM。
Ferreira。
L∞Parameterestimatesforvolumetricerrorinmodelsofmachinetools。
PrecisionEngineering,1997,20:
179~187.
16.ChenGuiquan.Rapidvolumetricerrormappingandcompensationforathree-axismachinecenter。
Ph.D。
thesis,MichigenUniversity,USA,2000。
17.ChristopherD。
MizeandJohnC。
Ziegert.Durabilityevaluationofsoftwareerrorcorrectiononamachinecenter.InternationalJournalofMachineToolsandManufacturing,2000,40:
1527~1534。
18.李书和。
数控机床误差补偿的研究[D].天津:
天津大学,1996。
19.廖平兰.机床加工过程宗合误差实时补偿技术[J]。
机械工程学报,1992,28
(2):
65~68。
20.李书和,张奕群,杨世民,张国雄。
多轴机床空间误差的一般模型[J]。
仪器仪表学报,1997,18(4):
364~372。
21.杨建国,薛秉源。
CNC车削中心热误差模态分析及鲁棒建模[J]。
中国机械工程,1998,9(5):
31~35.