钢结构桥梁.docx
《钢结构桥梁.docx》由会员分享,可在线阅读,更多相关《钢结构桥梁.docx(37页珍藏版)》请在冰豆网上搜索。
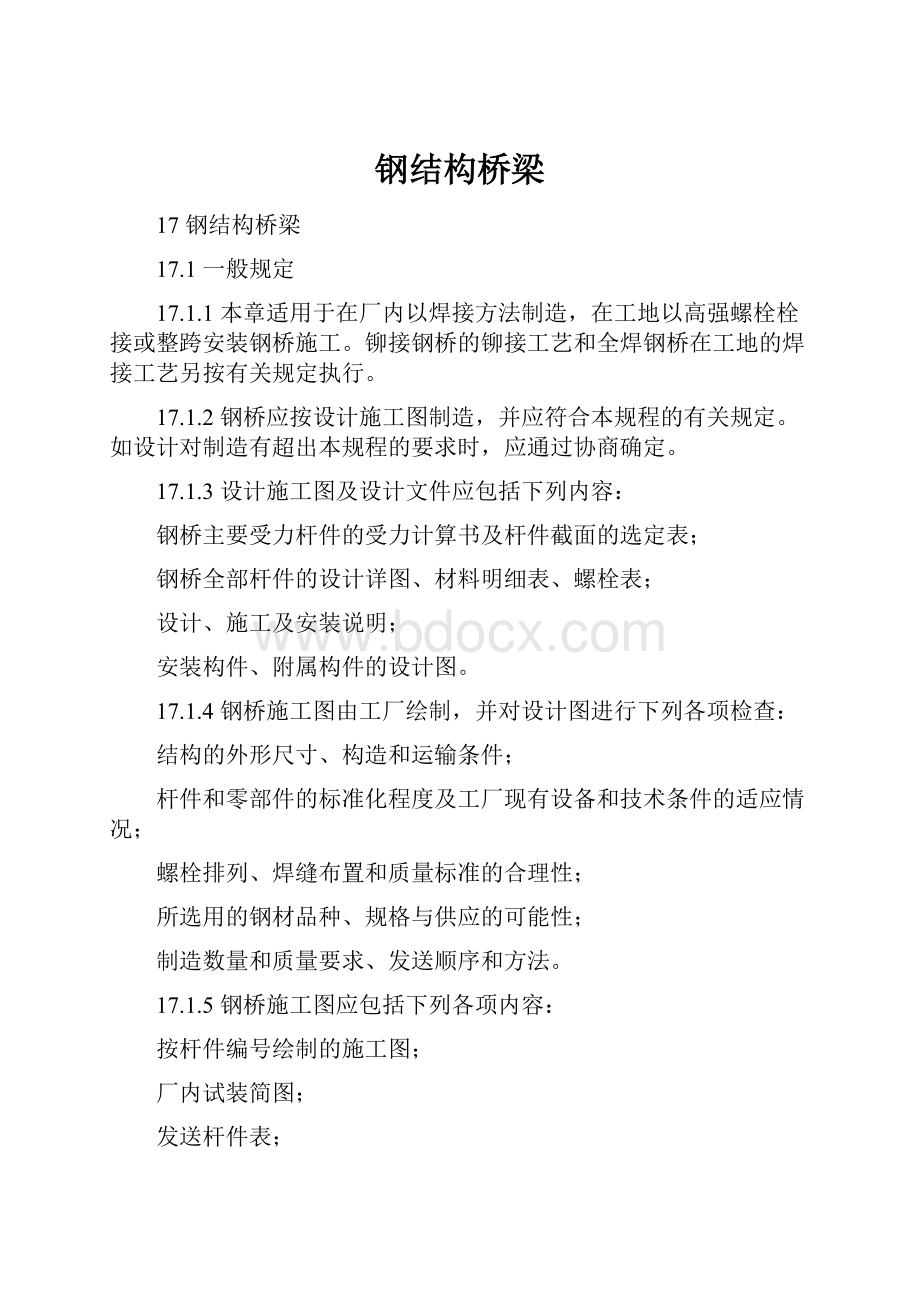
钢结构桥梁
17钢结构桥梁
17.1一般规定
17.1.1本章适用于在厂内以焊接方法制造,在工地以高强螺栓栓接或整跨安装钢桥施工。
铆接钢桥的铆接工艺和全焊钢桥在工地的焊接工艺另按有关规定执行。
17.1.2钢桥应按设计施工图制造,并应符合本规程的有关规定。
如设计对制造有超出本规程的要求时,应通过协商确定。
17.1.3设计施工图及设计文件应包括下列内容:
钢桥主要受力杆件的受力计算书及杆件截面的选定表;
钢桥全部杆件的设计详图、材料明细表、螺栓表;
设计、施工及安装说明;
安装构件、附属构件的设计图。
17.1.4钢桥施工图由工厂绘制,并对设计图进行下列各项检查:
结构的外形尺寸、构造和运输条件;
杆件和零部件的标准化程度及工厂现有设备和技术条件的适应情况;
螺栓排列、焊缝布置和质量标准的合理性;
所选用的钢材品种、规格与供应的可能性;
制造数量和质量要求、发送顺序和方法。
17.1.5钢桥施工图应包括下列各项内容:
按杆件编号绘制的施工图;
厂内试装简图;
发送杆件表;
工地拼装简图。
17.1.6钢桥制造使用的钢材、焊接材料、涂装材料和紧固件应符合设计要求和现行国家标准的规定。
17.1.7进厂的原材料除应有生产厂家的出厂质量证明书外,还应按合同要求和有关现行国家标准进行检查和验收,并做好检查记录。
17.1.8钢桥制造和检验所使用的量具、仪器、仪表等应定期由二级以上计量机构检定合格方可使用。
特大桥工地用尺与工厂用尺应互相校对。
17.1.9工地拼装设计应保证产品质量和操作方便,并应符合下列要求:
17.1.9.1钻孔样板、胎型应有足够的刚度,样板厚度不小于12mm。
固定式钻孔样板(立体样板)应考虑温度变化的影响。
钻孔样板制造及安装允许偏差应符合下列规定;
1)钻孔套样板制造允许偏差
(1)钻孔套内径应比钻头直径大0.1-0.2mm,特殊情况应按设计要求而定;钻孔套硬度应比钻头硬度大2-3度(洛氏);
(2)两相邻钻孔套中心距允许偏差±0.25mm;
(3)极边钻孔套及任何对角钻孔套中心距允许偏差±0.35mm;
(4)两块孔群布置相同的样板重叠时比钻孔套内径小0.35mm的试孔器应能自由通过所有各孔。
2)固定钻孔套样板安装允许偏差
(1)相邻样板孔群中心距允许偏差±0.25mm;
(2)板边两样板孔群中心距允许偏差±0.35mm;
(3)各样板孔群水平中心距允许偏差0.25mm;
(4)两块相对样板中心纵向允许错位0.25mm;
(5)后档板与相对样板纵向和横向允许偏差±1mm;
(6)成对方向长净空距离允许偏差1.0mm;
(7)对线器与样板中心线的允许偏差0.25mm。
17.1.9.2采用先钻孔后组焊工艺时,钻孔样板应预留焊接收缩量。
17.1.10焊接工艺应进行焊接工艺评定,保证焊接接头的质量。
已确定的工艺参数施工中不得随意改动。
17.1.11焊工应定期进行技能考核,合格后由主管单位发给合格证书,持合格证书者才能进行焊接工作。
17.2钢桥制造
17.2.1钢桥制造应制定工艺流程,并严格按其实施。
17.2.2作样应符合下列要求:
样板、样杆、样条制作的允许偏差应符合表17.2.2的规定:
样板、样杆、样条制作允许偏差表17.2.2
检查项目
允许偏差(mm)
两相邻孔中心距离
±0.5
矩形对角线两孔中心距离、两极边孔中心距离
±1.0
孔中心与孔群中心线的横向距离
0.5
样板长度、宽度、样杆长度
+0.5
-1.0
曲线样板上任意点偏离
1.0
1对于形状复杂的零部件在图中不易确定的尺寸,应通过放样校对后核实确定。
17.2.3号料应符合下列要求:
号料前应检查钢料的牌号、规格、质量,确认无误合格后方可号料;
如钢料不平直、有浮锈、油漆等污物影响号料及切割质量时,应矫正清理后再号料;
号料所划的切割线应准确清晰,号料尺寸允许偏差:
±1mm;
零部件的刨(铣)加工量、焊接收缩量应按样板、样杆、样条要求预留;
5零部件采用气割时,应根据钢板厚度和切割方法预留切口量。
一般预留2~4mm,较厚者可适当增加;
在不切边的钢板(毛边料)上号料时,应甩去毛边;
零部件号料后应作明显标记,并打上钢印。
17.2.4切割应符合下列要求:
剪切边缘应整齐,无毛刺、反口,缺肉等缺陷,剪切零件允许偏差应符合下列规定:
1)板件长度:
±2mm;
2)型钢长度:
±2mm;
3)型钢剪切线与边缘垂直度:
≤1.5mm。
1)手工气割:
±2mm;
2)自动、半自动切割:
±1.5mm;
3)精密切割:
±1.0mm。
5%,且不大于2mm,当型钢肢宽大于100mm时,切割线与边线垂直度偏差应不大于2mm;
精密切割切割面质量应符合表17.2.4的规定;
精密切割切割面质量要求表17.2.4
项目等级
1
2
附注
表面粗糙度
Ra25μm
Ra50μm
按表面粗糙度>>GB1
崩坑
不允许
1m长度内容许
有一处1mm
超限修补按焊接有关规定办理
塌角
半径≤0.5mm
气割前应将料面上的浮锈及脏物清除干净。
钢料应放平、垫稳,割缝下面应留有空隙。
17.2.5零件矫正和弯曲
17.2.5.1矫正前,剪切的反口应修平,气割挂渣应铲净;
600~800℃,矫正后钢材温度应缓慢冷却,温度尚未降至室温时,不得锤击钢料或用水急冷;
17.2.5的规定;
15倍,否则必须热弯,冷作弯曲后零件边缘不得产生裂纹;
900~1000℃之间。
17.2.6边缘加工:
17.2.6.1零件刨(铣)加工余量不应小于3mm,加工面表面粗糙度不得低于Ra25-μm;顶紧加工面与板面垂直度偏差应不小于0.01t(t-板厚),且不得大于0.3mm;
17.2.6.2除施工图及工艺文件另有规定外,刨(铣)加工范围及允许偏差应符合表和表的规定;
零件矫正允许偏差(mm)表17.2.5
零件
名称
简图
说明
允许偏差
钢
件
平面度
每米范围
f≤1
马刀形
弯曲
全
长
范
围
l≤8000
f≤3
l>8000
f≥4
型
钢
直线度
每米范围
f≤0.5
角钢肢
垂直度
全长范围
Δ≤0.5
角钢肢
平面度
联结部位
Δ≤0.3
其余部位
Δ≤0.5
槽钢腹板
平面度
联结部位
Δ≤0.3
其余部位
Δ≤0.5
槽钢翼缘
垂直度
联结部位
Δ≤0.5
其余部位
Δ≤1.0
刨、铣加工范围及允许偏差表17.2.6-1
类别
范围及偏差
零件
全焊梁、栓焊梁
范围
允许偏差
宽度
孔边距
板梁及桁架主弦、斜竖杆、纵横梁、梁托架,平联杆件
盖板(Ⅰ型)
两边
±2.0
竖板(箱型)
两边
±1.0
腹板
两边
±1.0
主桁架节点板
三边
+2.0
座板
四边
±1.0
拼接板、鱼形板、桥门、节点弯板
两边
±2.0
支承节点板、拼接板、支承角
支承边
+0.3
+0.5
填板
按工艺要求
±2.0
平联、横联节点板
焊接边
±0.3
箱形杆件内隔板
四边
±0.5
Ⅰ形、槽形隔板的腹板
两边
-0.5
加劲肋
焊接边端
按工艺要求
P
+0.5
-1.0
B
+1.5
注:
①腹板宽度应按盖板实际厚度偏差及焊接收缩量配制;
②特殊要求除外;
③箱形杆件内隔板板边垂直度偏差不得大于0.5mm;
④马刀形弯曲,长度10米及以下允许2mm;10米以上允许3mm,但不得有锐弯。
零部件
范围
项目
允许偏差(mm)
简图
盖
板
周
边
长度
+2
1
宽度
+2
腹
板
周
边
长度
+2
1
宽度
+1
隔
板
周
边
宽B
+0.5
高H
+0.5
对角线差
1
垂直度
h/2000
缺口定
位尺寸
b
+2
h
+2
竖肋
纵肋
按工艺文件
高(H)
0.5
长(L)
(2)
缺口定位尺寸h
2
零件应根据预留加工量及平直度要求两边均匀加工。
已有孔(或锁口)的零件按孔(或锁口)中心线找正边缘;
刨(铣)边时应避免油污污染钢料。
发现油污污染时,应在焊前清洗;
边缘加工后,应将边缘刺屑清除干净;
零件磨边、磨头、磨弧时,应磨去剪切边缘的飞刺及气割边缘的挂渣、切口棱角的波纹,同时应将崩坑等缺陷部位磨修匀顺。
17.2.7制孔应符合下列要求:
1.5~3.0mm,允许偏差符合表规定;
17.2.7.3组装件可预钻小孔,组装后进行扩钻。
预钻孔径至少较设计孔径小3mm;
的规定;
扩钻孔严禁飞刺和铁屑进入板层。
扩孔后的飞刺、铁屑及污垢应清除干净,并应用足够的螺栓、冲钉使板层紧固密贴。
存在的间隙用0.3mm的塞尺(千分页)探入,深度不得超过20mm。
对定位冲钉和组装螺栓的要求应按和规定办理。
高强度螺栓孔允许偏差表
序
号
名称
公称直径及允许偏差(mm)
1
螺
栓
公称直径
12
16
20
22
24
27
30
允许偏差
±0.43
±0.52
±0.84
螺
栓
孔
公称直径
13.5
17.5
22
24
26
30
33
允许偏差
+0.43
+0.52
+0.84
2
不圆度(最大和最小直径差)
1.00
1.50
3
中心线倾斜度
不应大于板厚的3%,且单层板不得大于2mm,多层板叠合不得大于3mm
孔距允许偏差表
定位方位
检查项目
允许偏差(mm)
说明
卡
钻
孔
套
样
板
两相邻孔距
±0.35
个别相邻孔距允许偏差≤0.5
板边孔距
±0.5
±2.5*
*仅适用于整孔下承板梁的主梁与横梁,联结系的联结孔
两组孔群中心距
±0.5
±1.0*
孔群中心线与杆件中心线的横向偏离
1.5
号
孔
两相邻孔距
±0.5
板边及对角线孔距
±1.0
孔中心与孔群中心线的横向偏离
+1
17.2.8杆件组装应符合下列要求:
和表的规定。
焊接杆件允许偏差表
类别
简图
项目
允许偏差(mm)
焊
接
梁
焊
接
梁
对接高低差
T≥25
Δ≤1
T<25
Δ<0.5
对接间隙b
+1
宽度B
+1
高度H
有水平拼接时为±1.0
盖板中线与腹板中线的偏移
Δ≤1.0
桁梁
高
度
H
+1.5
纵横梁
+1.5
板
梁
H≤2m
+2
H>2m
+4
无孔两竖板中心偏移
Δ≤2.0
拼接缝隙
Δ≤0.3
拼接缝隙
Δ≤0.3
盖板倾斜
Δ≤0.5
组合角钢肢高低差
Δ≤0.5(接合处)
Δ≤1.0(其余处)
板梁、纵横梁加劲肋间距s
±1.0(有横向联结关系者)
±3.0(无横向联结关系者)
板梁腹板、纵横梁腹板的局部平面度
Δ<1.0
磨光顶紧
缝隙
Δ<0.2
焊接箱梁组装允许偏差表1
类别
简图
项目
允许偏差(mm)
零
部
件
及
单
元
组
装
高度H
+1.5
-0.5
竖板中心与水平板中心偏离
Δ<1
盖板、腹板、单元纵肋、竖肋间距S
+1
整体组装隔板间距S
±2
主
梁
跨度L
±5
宽度B
±2
高度H
±2
横断面对角线差
|c1-c2|<3
侧弯
f≤5
的规定办理;
图零件焊接前清除范围(虚线)示意图
10倍的腹板厚度(交叉焊缝除外)。
配料与组装时应将焊缝错开,错开最小距离应符合图的规定;
图焊接杆件中焊缝错开最小距离示意图
1-盖板2-腹板水平加劲肋3-竖肋
4-腹板5-盖板对接接头6-焊缝
0.1mm,定位处的冲钉不得少于两个;
中定位焊的规定;
组装时,应用冲钉使绝大多数孔正确就位,每组孔应打入10%冲钉,但不得少于两个,冲钉直径应不小于设计孔径0.3mm,采用预钻小孔组装的杆件,使用冲钉直径应不小于预钻孔径0.5mm;
组装时,应用螺栓紧固,保证零件相互密贴,一般在任何方向每隔320mm至少有一个螺栓。
组装螺栓的数量不得少于孔眼数量的30%;
组装后的第一个杆件,应经检验人员确认合格后,方可批量组装。
17.2.9焊接应符合下列要求:
一般要求如下:
1)焊工应熟悉工艺要求,明确焊接工艺参数;
2)焊接前应检查并确认所使用的设备工作状态正常,工具仪表良好,齐全可靠方可施焊;
3)焊接工作宜在室内进行。
湿度不宜高于80%。
焊接环境温度低合金钢不应低于5℃,普通碳素结构钢不得低于0℃;
4)主要杆件应在组装后24小时内焊接。
5)定位焊、手弧焊及埋弧焊的预热应按表的规定执行;
预热温度及范围表
材质
板厚
预热温度
预热范围
低合金钢
16Mnq
15~32mm
80~120℃
50~80mm
6)焊接材料可按表或经过焊接工艺评定合格的工艺要求选用,并应满足下列要求:
(1)焊剂、焊条应按表规定烘干使用;
(2)焊剂中的脏物、焊丝上的油锈等必须清除干净;
(3)焊剂的粒度,埋弧自动焊宜1.0-3.0mm,埋弧半自动焊宜0.5-1.5mm。
7)施焊时母材的非焊接部位严禁焊接引弧;
8)定位焊应按下列规定进行:
(1)定位焊不得有裂纹、夹渣、焊瘤等缺陷。
(2)焊前应按施工图或工艺文件检查焊件坡口尺寸根部间隙等,如不合要求不能定位焊;
(3)定位焊缝长可为50~100mm,间距400~600mm,焊脚尺寸不得大于设计焊脚尺寸的一半;
(4)定位焊缝应距设计焊缝端部30mm以上;
(5)如有定位焊缝开裂,应查明原因,清除开裂的焊缝,并在保证杆件尺寸正确的情况下补充定位焊。
焊接材料选用表表
埋弧焊
手弧焊
定位焊及返修焊
母
材
接头
焊丝
焊剂
母材
焊缝类别或接头
焊条
方法
原焊接
方法
焊接材料
Q235
16Mnq
各种接头
H08E或H08A
HJ-431
HJ-350
16
Mnq
主要焊缝
E5015
E4315
手弧焊(定位焊)
(返修焊)
埋弧焊
16Mnq
E5105
16Mnq
对接接
头(不
开坡口)
H08E
次要焊缝
E5003
Q23516Mnq
E4315
16
Mnq
对接焊缝
E4315
埋弧焊(返修焊)
埋弧焊
与原焊缝相同
对接接头(开坡口)
H08MnA
H10Mn2
其余焊缝
E4303
角焊逢
H08A
或
H08E
Q235
------
E4303
手弧焊(定位焊)
(返修焊)
手弧焊
与原焊缝相同
焊条、焊剂烘干温度表
焊接材料
烘干温度
保温时间
保存温度
说明
酸性焊条
100-150℃
2小时
80-100℃
-------
碱性焊条
(低氢)
350-400℃
2小时
100-150℃
从箱中取出4小时以上时应重新烘干
HJ-431
250-350℃
HJ-350
300-400℃
9)焊接前应清除焊接区的有害物,清除范围应按17.2.8规定范围并应符合下列要求:
(1)埋弧焊及用低氢焊条焊接的杆件,焊接区两侧应清除铁锈,氧化皮等影响焊接质量的脏物;
(2)清除定位焊飞溅的熔渣;
(3)熔焊缝背面应将熔渣及缺角清除干净再焊。
10)埋弧自动焊应在距杆件端部80mm以外的引弧板上引、熄弧,埋弧自动焊焊接中不能断弧,如有断弧应将停弧外刨成1:
5斜坡后再继续搭接50mm施焊;
11)埋弧自动焊焊剂覆盖厚度不得小于20mm,埋弧半自动焊不得小于10mm。
焊接后应待焊缝稍冷却再敲去熔渣。
焊缝磨修和返修焊应符合下列要求
1)焊缝尺寸超出表允许的正偏差的焊缝及小于1mm且超差的咬边应磨修匀顺,焊缝咬边超过1mm或外观超出负偏差的缺陷应用手弧焊进行返修焊;
2)杆件焊接后两端引板应用气割切除并磨平切口,不得损伤杆件;
3)气孔、裂纹、夹渣、未熔透等超出表及本节无损检验规定时,应查明原因,用碳弧气刨清除缺陷,用原焊接方法进行返修焊。
16Mnq钢板厚度大于25mm时,返修焊应预热100~150℃。
返修焊采用埋弧焊、半自动焊时,应将清除部位的焊缝两端刨成1:
5的斜坡,再进行焊接;
4)返修后的焊缝应随即铲磨匀顺,并按原质量要求进行复验。
返修焊次数不宜超过两次。
焊缝检验应符合下列要求:
所有焊缝应进行外观检查,不得有裂纹、未熔合、夹渣、弧坑和超出表规定的缺陷;
无损检验应符合下列规定:
1)零部件的焊缝应在焊接24小时后进行无损检验;
2)对接焊缝应按表的规定进行超声波探伤。
其余有关技术要求按(GB11345)钢焊缝手工超声波探伤方法和探伤结果分析执行;
3)焊缝内部质量应按表、表17.2.10-6规定进行射线探伤检验。
焊缝接头抽探其数量不少于10%并不得少于一个接头,引弧试板应全部探伤,并应符合下列要求:
(1)Ⅰ、Ⅱ类横向对接焊缝长度大于1200mm时,焊缝中部增加探伤范围250~300mm;
(2)检验报告要规范化,主要内容包括探伤方法、探伤部位、检验范围、探伤比例、验收标准、缺陷情况、返修情况、探伤结论、检验人员及核查人员签字;
(3)其技术要求可执行《钢焊缝射线照相及底片等级分类法》(GB3323-82);
(4)检验记录和报表要存档保存7年;
4)进行局部探伤的焊缝、探伤过程中如果发现裂纹或较多的其它缺陷时,应继续探伤,必要时至焊缝全长;
序号
项目
质量要求(mm)
1
气孔
横向对接焊缝
不容许
纵向对接焊缝主要角焊缝
直径小于1
每米不多于3个
间距不小于20
其他焊缝
直径小于1.5
2
咬边
受拉部件横向对接焊缝
不容许
竖加劲肋角焊缝腹板侧受拉区
受压部件横向对接焊缝≤0.3
纵向对接及主要角焊缝≤0.5
其他焊缝≤1
3
焊脚
尺寸
埋弧焊K+2手弧焊K
手弧焊全长10%范围内允许K
4
焊波
h<2(任意25mm范围内)
5
余高铲磨(对接接头)
b<15时,h≤3;15<b≤25时,h≤4;
b>25时,h≤4b/25
6
余高铲磨(对接接头)
Δ1+0.5表面粗糙度Ra50μm
Δ2-0.3
7
平均未熔透
(箱形杆件)Δ≤
对接焊缝类别及超声波探伤范围表
焊接类别
适用范围
探伤范围
1
板梁、箱形梁、纵梁、横梁受拉翼缘(或受拉区部件)拉杆(或拉压杆)的横向对接焊缝
全部
2
板梁、箱形梁、纵梁、横梁受压翼缘(或受压区部件)压杆的横向对接焊缝
全部
板梁、箱形梁的纵向对接焊缝
两端各1m
5)不合格的缺陷应及时返修,返修区域修补后返修部位及补焊受影响的区域应按原探伤条件进行检验;
超声波探伤缺陷的等级分类表
检验等级
板厚
(mm)
评定
等级
A
B
C
8-15
8-300
8-300
Ⅰ
2/3δ;最小12
δ/3;最小10,最大30
δ/3;最小10,最大20
Ⅱ
3/4δ;最小12
2/3δ;最小12,最大50
δ/2;最小10,最大30
Ⅲ
<δ;最小20
3/4δ;最小16,最大75
2/3δ;最小12,最大50
Ⅳ
超过三级
注:
①δ为坡口加工侧母材板厚,母材板厚不同时,以较薄侧板厚为准。
②管座角焊缝δ为焊缝截面中心线高度。
超声波幅曲线的灵敏度表
级别
板厚
(mm)
DAC
A
B
C
8-50
8-300
8-300
判废线
DAC
DAC-4dB
DAC-2dB
定量线
DAC-10dB
DAC-10dB
DAC-8dB
评定线
DAC-16dB
DAC-16dB
DAC-14dB
对接焊缝内部质量射线探伤质量要求表
焊缝类别
适用范围
探伤范围(mm)
板厚(mm)
视场范围(mm)
质量要求
气孔允许点数
裂纹、未熔合未焊透
1
板梁、箱形梁、纵梁、横梁受拉翼(受拉区部件),拉杆(或拉压区部件)的横向对接焊缝
两端头各250-300
10-25
10×10
2
不允许
10×50
3-5
25-40
10×20
4
10×50
5-6
2
板梁、箱形梁、纵梁、横梁受压翼缘(或受压部件),的横向对接焊缝板梁箱形梁的纵向对接焊缝
两端头各250-300
10-25
10×10
4-6
不允许
10×50
6-8
25-40
10×50
8-9
对接焊缝内部质量射线探伤质量要求表
焊缝类别
单个条状夹渣长度(mm)
条状夹渣总长
Ⅱ
最少可为3,最大t/4
在任意2t范围内不超过单个条状夹渣允许长度,且在任意12t范围内不大于t
注:
t:
钢板厚度
6)经射线和超声波两种探伤方法检查的焊缝,在不能判断哪种方法更能准确判定焊缝质量时,两种方法应达到各自质量标准,方可认为合格。
杆件矫正应符合下列要求:
杆件矫正的允许偏差应符合表-1、表和表的规定;
简图
项目
允许偏差(mm)
工地孔部分
Δ≤0.5
其余部分
Δ≤2.0
工地孔部分
Δ≤0.5
其余部分
Δ≤2.0
工地孔部分
Δ≤1.0
其余部分
Δ≤3.0
工形、箱形杆件的扭曲
Δ≤3.0
工地孔部分
Δ≤0.7
其余部分
Δ≤1.5
工地孔范围内
Δ≤0.3
其余部分
Δ≤1
板梁的腹板,纵横梁腹板的平面度
Δ≤H/500(且≤5)
工形、箱形杆件(或纵横梁)侧弯
Δ≤2.0(L≤4000);
Δ≤3.0
(4000≤L≤16000)
Δ≤5.0(L>16000)
不设拱度的板梁,纵横梁
Δ≤3
设拱度f的板梁
+5
-3
项目
允许偏差(mm)
腹板平面度
Δ1<h/250且≤3
Δ2<l0/500且≤5
盖板平面度
Δ3<W/250且