杠杆夹具说明书.doc
《杠杆夹具说明书.doc》由会员分享,可在线阅读,更多相关《杠杆夹具说明书.doc(15页珍藏版)》请在冰豆网上搜索。
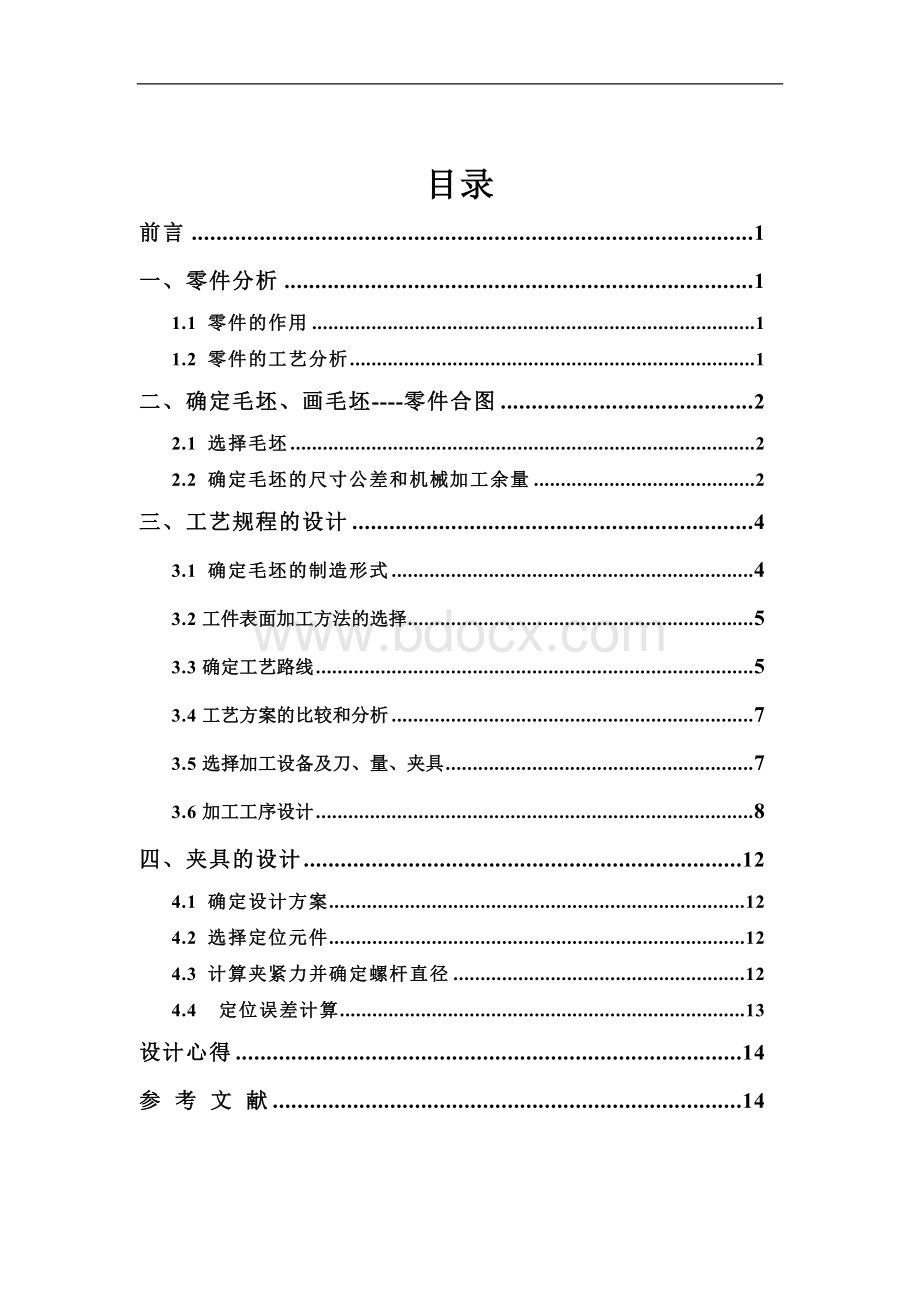
目录
前言 1
一、零件分析 1
1.1零件的作用 1
1.2零件的工艺分析 1
二、确定毛坯、画毛坯----零件合图 2
2.1选择毛坯 2
2.2确定毛坯的尺寸公差和机械加工余量 2
三、工艺规程的设计 4
3.1确定毛坯的制造形式 4
3.2工件表面加工方法的选择 5
3.3确定工艺路线 5
3.4工艺方案的比较和分析 7
3.5选择加工设备及刀、量、夹具 7
3.6加工工序设计 8
四、夹具的设计 12
4.1确定设计方案 12
4.2选择定位元件 12
4.3计算夹紧力并确定螺杆直径 12
4.4定位误差计算 13
设计心得 14
参考文献 14
前言
机械制造技术基础课程设计是在学完了机械制造技术基础和大部分专业课,并进行了生产实习的基础上进行的一个教学环节。
这次设计使我们能综合运用机械制造工艺学中的基本理论,并结合生产实习中学到的实践知识,独立地分析和解决工艺问题,初步具备了设计一个中等复杂程度零件(杠杆零件)的工艺规程的能力和运用夹具设计的基本原理和方法,拟定夹具设计方案,完成夹具结构设计的能力,也是熟悉和运用有关手册﹑图表等技术资料及编写技术文件等基本技能的一次实践机会,为今后的毕业设计及未来从事的工作打下良好的基础。
由于能力所限,经验不足,设计中还有许多不足之处,望程老师指教。
一、零件分析
1.1零件的作用
杠杆是铣床进给机构中起支撑固定作用的零件Φ25孔与轴连接起支撑本零件的作用,左右两孔Φ8H7各装一拨叉,控制铣床工作台自动进给的离合器。
Φ10孔通过销与另一杠杆连接,操纵手柄即可实现铣床工作台三个方向的自动进给。
1.2零件的工艺分析
其材料为HT200。
该材料有较高的强度、耐磨性、耐热性适应用于较大应力。
杠杆的Φ25+0.052mm孔的轴线合两个端面有着垂直度的要求。
现分述如下:
本夹具用于在立式钻床上,加工Φ8(H7)孔。
工件以Φ25+0.052mm孔及端面和水平面底、Φ30的凸台分别在台阶定位销7、支承钉11上实现完全定位。
钻Φ8(H7)mm孔时工件为悬臂,为防止工件加工时变形,采用了螺旋辅助支承2,当辅助支承2与工件接触后,用螺母1锁紧。
要加工的主要工序包括:
粗精铣宽度为Φ40mm的上下平台、钻Φ10(H7)+0.015孔、钻Ф8(H7)+0.015,Ф8(H7)-0.015的小孔、粗精铣Φ30凸台的上下表面。
加工要求有:
Φ40mm的平台的表面粗糙度各为Ra6.3um(上平台)、Ra3.2(下平台)、Φ10(H7)孔为Ra3.6um、Φ25(H9)和Φ8(H7)孔表面粗糙度都为Ra1.6um。
2×Φ8(H7)孔有平行度分别为0.1um(A)、0.15um(A)。
Φ10(H7)孔的平行度为0.1um(A)。
杠杆有过渡圆角为R5,则其他的过渡圆角则为R3。
其中主要的加工表面是孔Ф8(H7),要用Ф8(H7)钢球检查。
二、确定毛坯、画毛坯----零件合图
2.1选择毛坯
该杠杆在工作中的载荷平稳,根据零件要求,毛坯采用铸造。
该杠杆的零件的轮毂尺寸不大,且生产类型为大量生产,为提高质量和生产毛坯的精度,故采用金属模铸造。
毛坯的拔模斜度为5°。
2.2确定毛坯的尺寸公差和机械加工余量
由教材可知,要确定的毛坯机械加工余量和尺寸公差,先确定以下各项因素:
⑴公差等级
有杠杆的功能和技术要求,确定该零件的公差等级为普通级。
⑵零件的分模面
根据该杠杆零件的形为特点,该零件的Φ25、Φ8轴线组成的平面为分模面,属于直分模面。
⑶零件的表面粗糙度
由零件图可知,该杠杆的各加工表面粗糙度Ra均大于1.6um。
根据上述诸因素,可查表确定该铸件的尺寸公差和机械加工余量,所得结果见下表:
各加工表面表面总余量
加工表面
基本尺寸
加工余量等级
加工余量数值(mm)
说明
Ф40mm的上下平台
54
G
4
加工上下底面
宽度30mm的平台
25
H
4
加工上表面
Ф30的凸台上下面
15
H
3
加工上下表面
Φ25(H9)孔
25
G
5
加工内孔
由参考文献得出:
主要毛坯尺寸及公差
主要尺寸
零件尺寸
总余量
毛坯尺寸
公差CT
2×ф8(H7)之间的中心距离
16
8
168
4
Ф10(H7)孔尺寸
10
2.0
10
3
Ф25(H9)孔尺寸
25
3.0
25
4
Ф8(H7)孔尺寸
8
2.0
8
3
三、工艺规程的设计
3.1定位基准的选择
(1)粗基准的选择。
对于本零件而言,按照粗基准的选择原则,选择本零件的加工表面就是直径为Ф40mm的下肩面表面作为加工的粗基准,可用压板对肩台进行加紧,利用一组V形块支承Φ40mm的外轮廓作主要定位,以消除x、y两个自由度。
再以一面定位消除x、y、z三个自由度,达到定位要求,就可加工Φ25(H7)的孔。
(2)精基准的选择。
主要考虑到基准重合的问题和便于装夹,采用Φ25(H7)的孔中心线及其上下肩面作为精基准。
3.2工件表面加工方法的选择
本零件的加工表面有:
粗精铣宽度为Φ40mm的上下平台、钻Φ10(H7)孔、钻2×Ф8+0.015的小孔、粗精铣Φ30凸台的平台。
材料为HT200,加工方法选择如下:
1、Φ40mm圆柱的上肩面:
公差等级为IT8~IT10,表面粗糙度为Ra6.3,采用粗铣→半精铣的加工方法,并倒R3圆角。
2、Φ40mm圆柱的下肩面:
公差等级为IT8~IT10,表面粗糙度为Ra3.2,采用采用粗铣→精铣的加工方法,并倒R3圆角。
3、Φ30mm的凸台上下表面:
公差等级为IT13,表面粗糙度为Ra6.3,采用粗铣→半精铣的加工方法。
4、钻Φ10(H7)内孔:
公差等级为IT7~IT8,表面粗糙度为Ra3.2,平行度为0.1mm(A),采用钻孔→粗铰→半精铰的加工方法。
5、扩Φ25(H9)内孔:
公差等级为IT6~IT8,表面粗糙度为Ra1.6,采用扩孔钻扩孔→精铰的加工方法,并倒1×45°内角。
6、钻Φ8(H7)内孔:
公差等级为IT6~IT8,表面粗糙度为Ra1.6,采用钻孔→粗铰→精铰的加工方法。
3.3确定工艺路线
1、工艺路线方案一:
工序5:
铸造时效涂底漆
工序10:
粗精铣宽度为Ф40mm的上下平台面和宽度为30mm的平台面
工序15:
粗精铣Φ30凸台底面,粗精铣Φ30凸台上面
工序20:
扩孔钻扩孔Ф25(H9)使尺寸达到Ф24.8mm,铰孔Ф25(H9)使尺寸达到Ф25(H9)。
工序25:
钻铰Φ10H7孔
工序30:
钻铰Φ8H7孔
工序35:
检验
工序40:
入库
2、工艺路线方案二:
铸造
时效
涂底漆
工序10:
粗精铣宽度为Ф40mm的上下平台和宽度为30mm的平台。
工序20:
粗精铣宽度为Φ30mm的凸台表面
工序30:
钻2×Ф8(H7)的小孔使尺寸达到7.8mm。
工序40:
扩孔钻钻孔Ф25(H9)使尺寸达到Ф24.8mm。
工序50:
铰孔Ф25(H9)使尺寸达到Ф25(H9)。
工序60:
钻Φ10(H7)的内孔使尺寸达到9.8mm。
工序70:
粗铰Φ10(H7)内孔使尺寸达到9.96mm。
工序80:
精铰Φ10(H7)内孔使尺寸达到Φ10(H7)mm。
工序90:
粗铰2×Φ8(H7)小孔使尺寸达到7.96mm。
工序100:
精铰2×Φ8(H7)小孔使尺寸达到Φ8(H7)。
工序110:
检验入库。
3.4工艺方案的比较和分析:
上述两种工艺方案的特点是:
方案一是根据宽度为40mm的上下肩面作为粗基准,Ф25(H7)孔作为精基准,所以就要加工Ф25孔时其尺寸达到要求的尺寸,那样就保证了2×Ф8小孔的平行度误差精度等。
而方案二则先粗加工孔Ф25,而不进一步加工就钻Ф8(H7),那样就很难保证2×Ф8的平行度误差精度。
所以决定选择方案一作为加工工艺路线比较合理。
3.5选择加工设备及刀、量、夹具
由于生产类型为大批生产,故加工设备宜以采用通用机床为主,辅以少量专用机床。
其生产方式为以通用机床加专用夹具为主,辅以少量专用机床的流水生产线。
工件在各机床上的装卸及各机床间的传送均由人工完成。
粗精铣宽度为Ф40mm的上下平台和宽度为30mm的平台。
考虑到工件的定位夹紧方案及夹具结构设计等问题,采用立铣,选择X5012立式铣床(参考文献:
机械工艺设计手册,主编:
李益民,机械工业出版社出版社),刀具选D=10mm的削平型立铣刀(参考文献:
机械工艺设计手册,主编:
李益民,机械工业出版社出版)、专用夹具、专用量具和游标卡尺。
粗精铣宽度为Φ30mm的凸台表面。
采用X5021立式铣床,刀具选D=10mm的削平型铣刀,专用夹具、专用量检具和游标卡尺。
扩孔钻扩孔Ф25(H9)使尺寸达到Ф24.8mm。
采用立式Z535型钻床,刀具选D=24.7mm的锥柄扩孔钻(莫氏锥度3号刀),专用钻夹具和专用检具。
铰孔Ф25(H9)使尺寸达到Ф25(H9)。
采用立式Z535型钻床,刀具选D=25mm的锥柄机用铰刀,并倒1×45°的倒角钻用铰夹具和专用检量具。
钻2×Ф8(H7)的小孔使尺寸达到7.6mm。
采用立式Z518型钻床,刀具选用D=7.6mm的直柄麻花钻,专用钻夹具和专用检量具。
钻Φ10(H7)的内孔使尺寸达到Φ9.8mm。
采用立式Z518型钻床,刀具选用D=9.8mm的直柄麻花钻,专用的钻夹具和量检具。
粗铰Φ10(H7)内孔使尺寸达到Φ9.8mm。
采用立式Z518型钻床,刀具选用D=9.8mm的直柄机用铰刀,专用夹具和专用量检具。
精铰Φ10(H7)内孔使尺寸达到Φ10(H7)mm。
采用立式Z518型钻床,选择刀具D=10mm的精铰刀,使用专用夹具和量检具。
粗铰2×Φ8(H7)小孔使尺寸达到Φ7.9mm。
采用立式Z518型钻床,选择刀具为D=7.9mm直柄机用铰刀,使用专用夹具和专用量检具。
精铰2×Φ8(H7)小孔使尺寸达到Φ8(H7)。
采用立式Z518型钻床,选择刀具为D=8mm的直柄机用铰刀,使用专用的夹具和专用的量检具。
(参考资料和文献均来自:
机械工艺设计手册,主编:
李益民,机械工业出版社出版)
3.6加工工序设计
根据本次设计的要求,工序设计只设计老师所给出工序的计算。
1、下面是对铣Φ30凸台面的加工设计。
各工步余量和工序尺寸及公差(mm)
加工表面
加工方法
余量
公差等级
工序尺寸
Φ30凸台面左上面1
粗精铣
3
—
15
Φ30凸台面左上面2
粗精铣
3
—
15
粗铣1面使凸台厚度为19mm
精铣1面使凸台厚度为18mm
粗铣2面使凸台厚度为16mm
精铣2面使凸台厚度为15mm
这三部工序全都采用X5201铣床来进行加工的,故:
(1)参考文献:
机械设计工艺简明手册,并参考X5201铣床主要技术参数,取铣削深度为粗铣2mm,精铣1mm取铣Φ30凸台面的进给量f=240mm/min(0.3mm/r),用插入法求得铣Φ30凸台面的切削速度为v=25m/min,由此算出转速为:
n=1000v/πd=1000×25/3.14×10r/min=796r/min
按机床实际转速取n=800r/min,则实际切削速度为v=3.14×10×800=25.12m/min
从参考文献得知:
Ff=9.81×42.7dof0.8KF(N)
M=9.81×0.021d2of0.8KF(N