烟灰缸的设计与数控加工毕业设计.docx
《烟灰缸的设计与数控加工毕业设计.docx》由会员分享,可在线阅读,更多相关《烟灰缸的设计与数控加工毕业设计.docx(37页珍藏版)》请在冰豆网上搜索。
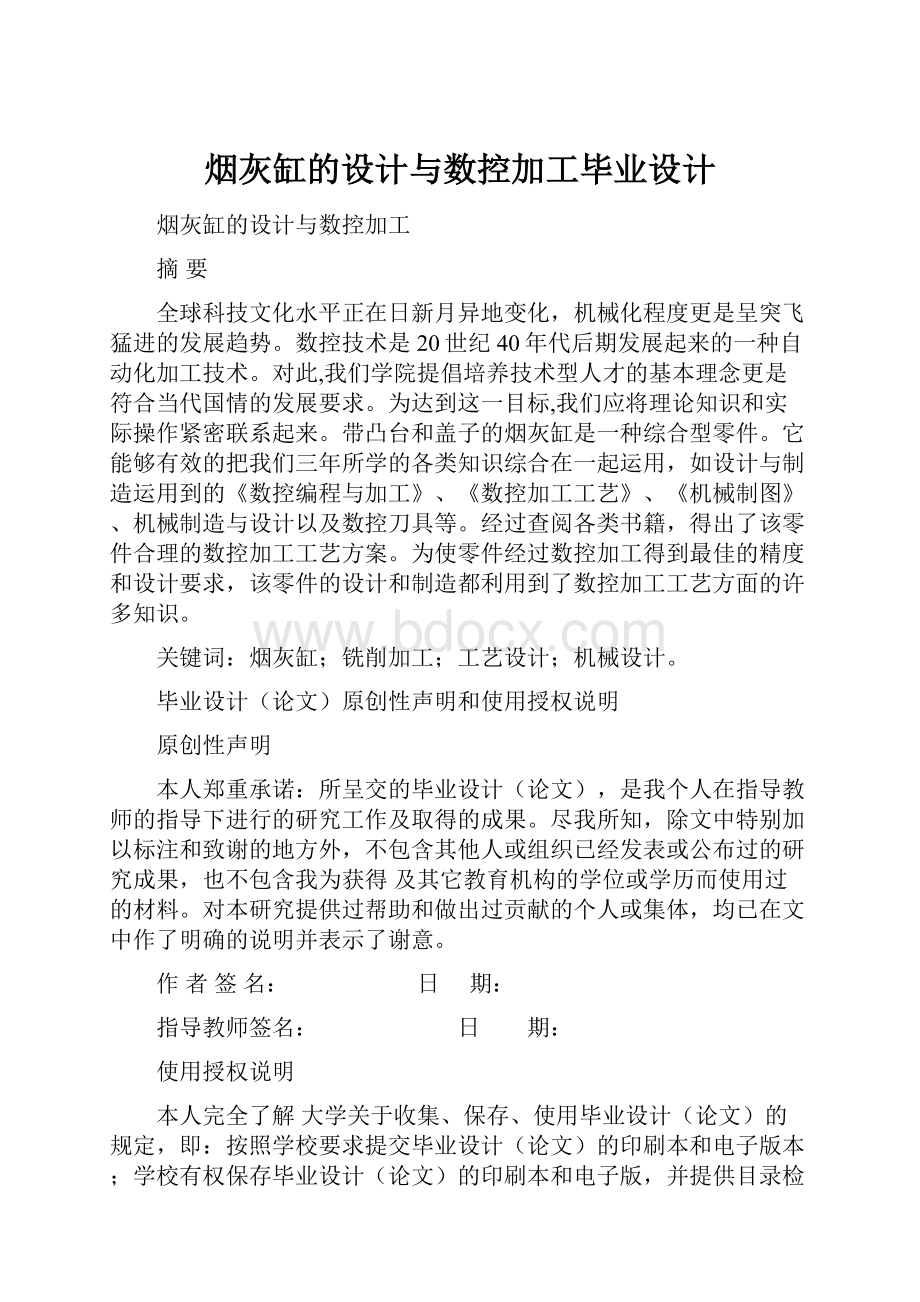
烟灰缸的设计与数控加工毕业设计
烟灰缸的设计与数控加工
摘要
全球科技文化水平正在日新月异地变化,机械化程度更是呈突飞猛进的发展趋势。
数控技术是20世纪40年代后期发展起来的一种自动化加工技术。
对此,我们学院提倡培养技术型人才的基本理念更是符合当代国情的发展要求。
为达到这一目标,我们应将理论知识和实际操作紧密联系起来。
带凸台和盖子的烟灰缸是一种综合型零件。
它能够有效的把我们三年所学的各类知识综合在一起运用,如设计与制造运用到的《数控编程与加工》、《数控加工工艺》、《机械制图》、机械制造与设计以及数控刀具等。
经过查阅各类书籍,得出了该零件合理的数控加工工艺方案。
为使零件经过数控加工得到最佳的精度和设计要求,该零件的设计和制造都利用到了数控加工工艺方面的许多知识。
关键词:
烟灰缸;铣削加工;工艺设计;机械设计。
毕业设计(论文)原创性声明和使用授权说明
原创性声明
本人郑重承诺:
所呈交的毕业设计(论文),是我个人在指导教师的指导下进行的研究工作及取得的成果。
尽我所知,除文中特别加以标注和致谢的地方外,不包含其他人或组织已经发表或公布过的研究成果,也不包含我为获得及其它教育机构的学位或学历而使用过的材料。
对本研究提供过帮助和做出过贡献的个人或集体,均已在文中作了明确的说明并表示了谢意。
作者签名:
日 期:
指导教师签名:
日 期:
使用授权说明
本人完全了解大学关于收集、保存、使用毕业设计(论文)的规定,即:
按照学校要求提交毕业设计(论文)的印刷本和电子版本;学校有权保存毕业设计(论文)的印刷本和电子版,并提供目录检索与阅览服务;学校可以采用影印、缩印、数字化或其它复制手段保存论文;在不以赢利为目的前提下,学校可以公布论文的部分或全部内容。
作者签名:
日 期:
1绪论1
2零件的分析2
2.1结构分析4
2.2精度分析4
2.3毛坯、余量分析4
3设备的选择5
4工艺文件的编制6
4.1定位基准的选择6
4.1.1粗基准的选择6
4.1.2精基准的选择6
4.2夹具、刀具以及冷却液的确定7
4.2.1夹具的确定7
4.2.2刀具的选择8
4.2.3冷却液的确定9
4.3工艺方案的确定9
4.4切削用量的确定10
4.4.1切削速度Vc10
4.4.2确定主轴转速11
4.4.3切削进给速度11
4.4.4背吃刀量的确定12
4.5进给速度的确定12
4.6填写工艺文件13
4.6.1机械加工工艺过程卡13
4.6.2数控加工工艺卡14
5零件的加工21
5.1数控加工过程21
5.2部分手工编制的程序单22
6零件的质量分析24
总结25
致谢26
参考文献27
1绪论
随着机械行业的不断发展,近年来数控加工和数控设备的应用呈突飞猛进的趋势。
包括以组合机床为主的大量生产方式的出现,机床都在向以数控设备为主的生产方式转变。
社会上对掌握数控技术的人才需求量越来越大,在我们学院数控设备的更新速度也越来越快。
为适应实际社会生产的能力和提高全面的数控加工能力,必要将自己学到的知识运用于实践当中,这样既可以巩固自己所学的知识,又可以提升自己的动手能力有。
此设计是烟灰缸零件的加工,也是作为数控专业学生,在毕业之前对所学知识的运用和总结。
说明书就是根据我们数控专业学生所需掌握的知识及技术要求编写的,它体现了数控加工各个方面的特点。
并合理的制定出了数控加工工艺规划。
自己利用设备,亲自动手执行零件的实体加工,加工出合格的零件。
这样既能对三年学习的《数控编程与加工》、《数控加工工艺》、《机械设计基础》、《机械制造及基础》、《机械制图》等多门学科的理论知识进行巩固,又能锻炼我们的实际动手能力和实际加工过程中问题的处理。
在这过程中我具体地了解了工件、刀具的材料、加工的工序、以及热处理等等一系列的知识。
这对于我今后的工作和学习都打下了夯实的基础。
2零件的分析
其余
图2-1烟灰缸底座图
图2-2烟灰缸上盖图
图2-3装配图
2.1结构分析
从图2-1、2-2可以看出该零件的加工内容主要有平面、轮廓、凸台、型腔等。
需要粗、精铣上下平面、外轮廓、凸台、型腔等加工工序才能完成。
由图2-1可以看出零件底座加工的重难点在于需要两次装夹加工才能完成,在图2-3中可以看出整个零件在加工过程中的重难点是如何控制和保证零件在加工完成后能很好地达到配合要求。
2.2精度分析
该零件最高精度等级为IT9级。
部分外轮廓无尺寸精度要求。
凸台外轮廓四边的粗糙度为1.6,接触处的粗糙度为3.2,其它表面粗糙度均为6.3。
底座和上盖的配合采用间隙配合。
但加工时由于装夹不当极容易生产震动。
如果定位不好也会导致表面粗糙度,加工精度难以达到要求。
毛坯材料不得有裂纹和气孔,并锐边去毛刺,符合GB/T1804-M国家标准。
2.3毛坯、余量分析
毛坯主要是指锻件和铸件,因模锻时的欠压量与允许的铣模量会造成余量多少不等,铸造时也会因沙型误差、收缩量及金属液体的流动性差不能充满型腔等造成余量不充分、不稳定。
在铣削时,一次定位将决定工件的“命运”,加工过程的自动化很难照顾到此处余量不足的问题。
因此,除板料外,不管是锻件,铸件,还是型材,只要准备采用数控铣削加工,其加工面均有较充分的余量。
余量大小主要考虑加工时要不要分层切削,分几层切削,也要分析加工中与加工后的变形程度。
由以上分析,该零件的材料我选择铸铝(铸铝:
硬度较低,具有良好的切削性能且加工后较易得到精度和表面质量的要求)。
其底座毛坯尺寸为105mm×105mm×30mm,盖子毛坯尺寸为105mm×105mm×21mm。
各留有5mm的加工余量。
3设备的选择
我院有多台具有FANUC-0i系统的数控铣床,但应根据加工零件的结构形状、精度要求、表面质量等考虑选择数控设备。
综合以上因素,我选择了KVC650数控立式加工中心,这台机床加工时的功率、转速、切削力、工作台面积等参数不仅能满足加工要求,而且它还是一台加工中心,能够减少多次人为换刀而带来的误差。
其具体参数如表3-1所示:
表3-1立式加工中心KVC650/参数
名称:
立式加工中心
规格型号:
KVC650
工作台面积(长X宽):
405X1370mm
T型槽(槽数-宽度X间距):
5-16X60mm
工作台承载工件最大值:
700Kg
行程(纵向/横向/垂向)机动:
650/450/500mm
主轴电机功率:
5.5/7.5Kw
主轴锥孔:
BT40
主轴转速:
20-6000r/min
进给速度(X、Y/Z):
5-8000mm/min
快速移动(X、Y/Z):
10000mm/min
刀库容量:
10(可选16)把
相邻刀具最大直径:
Ф100mm
刀具最大长度:
250mm
定位精度:
0.018mm
重复定位精度:
0.012mm
4工艺文件的编制
4.1定位基准的选择
4.1.1粗基准的选择
选择粗基准时,主要要求保证各加工面有足够的余量,使加工面与不加工面间的位置符合图样要求,并特别注意要尽快获得精基面。
具体选择时应考虑原则:
1、选择重要表面为粗基准
2、选择不加工表面为粗基准
3、选择加工余量最小的表面为粗基准
4、选择较为平整光洁、加工面积较大的表面为粗基准以便工件定位可靠、夹紧方便。
5、粗基准在同一尺寸方向上只能使用一次因为粗基准本身就是未经机械加工的毛坯面,其表面粗糙且精度低,若重复使用将产生较大的误差。
在加工零件产品之前铣削装夹面时,用作粗基准装夹的是毛坯的两侧面,如下图4-1所示:
图4-1粗基准示意图
4.1.2精基准的选择
精基准的选择应保证零件加工精度出发,同时考虑装夹方便结构简单。
选择精基准一般应考虑如下原则。
1、“基准重合”原则:
为满足加工表面相对设计基准的位置精度,应选择加工表面的设计基准为定位基准。
2、“基准统一”原则:
当某一组精基准定位可以比较方便的加工其它表面时,应尽可能在多数工序中采用粗精基准定位。
3、“自为基准”原则:
当工件精加工或光整加工工序要求余量尽可能小而均匀时,应选择加工表面本身作为定位基准。
4、“互为基准”原则:
为了获得均匀的加工余量或较高的位置精度,可采用互为基准反复加工的原则。
在加工零件产品时,用作装夹零件的部位是已经加工过夹持面,如下图4-2所示:
图4-2精基准示意图
4.2夹具、刀具、冷却液的确定
4.2.1夹具的确定
夹具是一种装夹工件的工艺设备,广泛的应用于机械制造过程的切削加工、热处理、配件、焊接和检测等工艺过程中。
在现代生产中,机床夹具是一种不可缺少的工艺设备,它直接影响着工件加工的精度、劳动生率和产品的制造成本等。
1、专用夹具:
一般在产品相对稳定、批量较大的生产中采用各种专用夹具,可获得较高的生产率和加工精度。
除大批量生产之外,中小批量生产中也需要采用一些专用夹具,但在结构设计时要进行具体的技术和经济分析。
2、组合夹具:
组合夹具是一种模块化的夹具。
标准的模块元件具有较高的精度和赖磨性,可组装成各种夹具。
夹具用完可拆卸,清洗后可留、待组装新的夹具。
由于使用组合夹具可缩短生产准备周期,元件能重复多次使用并具有减少专用夹具数量等优点。
3、通用夹具:
已经标准化的可加工一定范围内不同工件的夹具,称为通用夹具,其尺寸、结构已经规范化,而且具有一定的通用性,这类夹具适应性强,可用于一定形状和尺寸范围内的各种工件,价格便宜。
其缺点是夹具精度不高,生产率也比较低,较难装夹。
一般实用于单件小批量生产中。
4、数控加工的特点对夹具提出几点要求:
1)当零件加工批量不大时,应尽量采用组合夹具、可调试夹具及其他通用夹具,以缩短生产准备时间、节约生产费用。
2)在成批生产时才考虑采用专用夹具,并力求结构简单。
3)零件的装卸要快速、方便、可靠,以缩短机床的停顿时间。
4)夹具上各零件应不妨碍机床对零件各表面的加工,即夹具要开敞,其定位、夹紧机构元件不能影响加工中的走刀。
经综合分析:
该零件应选用平口虎钳装夹。
平口虎钳图如下图所示:
图4-3平口虎钳
4.2.2刀具的选择
切削用刀具材料应具备的性能如表4-1所示:
表4-1切削所用刀具材料应具备的性能
希望具备的性能
作为刀具使用时的性能
希望具备的性能
作为刀具使用时的性能
高硬度(常温及高温状态)
耐磨损性
化学稳定性良好
耐氧化性耐扩散性
高韧性(抗弯强度)
耐崩刃性、耐破损性
低亲和性
耐溶着、凝着(粘刀)性
高耐热性
耐塑性变形性
磨削成形性良好
刀具制造的高生产率
热传导能力良好
耐热冲击性、耐热裂纹性
锋刃性良好
刃口锋利、微小切削性能
4.2.3冷却液的确定
现有冷却液分为:
水溶液、乳化液和切削油三大类。
通过查阅资料选择常用的冷却液,根据表4-2进行选择。
表4-2常用冷却液
冷却液名称
主要成份
主要作用
水溶液
水、防锈添加剂
冷却
乳化液
水、油、乳化剂
冷却、润滑、清洗
切削油
矿物油、动植物油、极压添加剂
润滑
从工件材料考虑,切削铝时不得使用水溶液,考虑到冷却液作用和价格,选择乳化液可以满足要求。
从刀具材料考虑,所选高速钢刀具一般采用乳化液作为冷却液,其冷却效果很好,它的主要作用:
冷却、润滑、清洗而且还有一定的防锈作用。
4.3工艺方案的确定
根据零件图样,制定以下工艺方案,选取最佳一种,(即加工工时最短,又能保证质量)分析下面三套工艺方案进行比较:
方案1:
(1)底座:
铣夹持面→粗铣上平面→精铣上平面→铣外轮廓→粗铣凸台→精铣凸台→内腔粗加工→内腔精加工→铣4×7的缺口→掉头装夹→铣掉夹持面和四只小脚并保证尺寸精度→去毛刺;
(2)上盖:
铣夹持面→铣上平面→铣外轮廓→内腔粗加工→内腔精加工→调头装夹铣掉夹持面→去毛刺;
方案2:
(1)铣夹持面→粗铣上平面→精铣上平面→铣外轮廓→粗铣凸台→精铣凸台→内腔粗加工→精铣内腔→铣4×7的缺口→掉头装夹→铣掉夹持面和四只小脚→去毛刺;
(2)上盖:
铣夹持面→铣上平面→铣外轮廓→内腔粗加工→内腔精加工→调头装夹铣掉夹持面→去毛刺;
方案3:
(1)铣夹持面→粗铣上平面→精铣上平面→铣外轮廓→内腔粗加工→内腔精加工→粗铣凸台→精铣凸台→铣4×7的缺口→掉头装夹→铣掉夹持面和四只小脚→去毛刺;
(2)上盖:
铣夹持面→铣上平面→铣外轮廓→内腔粗加工→内腔精加工→调头装夹铣掉夹持面→去毛刺;
分析:
方案1将粗精加工一起完成,这样可以节省时间和换刀的次数,避免因换刀而引起的长度补偿误差。
方案2中先加工凸台再加工内腔。
此过程中容易影响工件的热膨胀而变形,可能导致加工后配合困难。
而方案3将粗精加工分开进行,增加了换刀次数和加工时间,因换刀而引起的长度补偿误差值增大。
所以选择方案1加工零件。
综上所述:
在方案1中将外轮廓粗精铣放在一个工序中,可以减少换刀的次数,从而提高了加工的效率,减少了加工所用的时间,并且能够较好地减少工件的变形。
因此采用方案1。
4.4切削用量的确定
切削用量应根据加工性质、加工要求、工件材料及刀具的尺寸和材料等相结合确定。
切削用量包括:
主轴转速,背吃刀量及进给速度等。
对于不同的加工方法需要选用不同的切削用量。
切削用量的选择原则是:
1、保证零件加工质量和表面粗糙度,充分发挥刀具的切削性能。
2、保证合理的刀具切削性能和耐用度。
并充分发挥机床的性能,最大限度地提高生产率降低成本。
4.4.1切削速度Vc
切削速度的高底主要取决于被加工零件的精度,材料,刀具的材料和刀具的耐用度等因素:
式中:
T—耐用度;fz—每齿进给量
ap—背吃刀量;Z—铣刀齿数
D—铣刀直径
式中:
qv、m、yv、xv、pv、mv为指数,cv、kv为系数,都由实验确定,也可参考有关切削用量手册选用。
4.4.2确定主轴转速
主轴根据允许的切削速度Vc(m/min)选择
N=1000Vc/πD
其中:
N---主轴转速
Vc—切削速度(m/min),通常由刀具寿命来确定切削速度
D---工件或刀具的直径(mm)
4.4.3切削进给速度
进给速度F是切削时单位时间内工件与铣刀沿进给方向的相对位移,是根据工件的加工精度和表面粗糙度的要求,以及刀具和工件材料进行选择,最大进给速度受到机床刚度和进给系统性能制约,不同的机床和系统,最大进给速度不同,当加工精度和表面粗糙度质量要求高时,进给速度应选小一些,通常在(20—50)m/min范围内选取。
在轮廓加工中,在接近拐角处应适当降低进给量,以克服由于惯性或工艺系统变形在轮廓拐角处造成“超程”或“欠程”现象。
切削进给速度与铣刀的转速n、铣刀齿数Z及每齿进给量fz的关系为:
F=fzZn
根据公式可以看出:
每齿进给量fz的选取主要取决于工件材料的力学性能、刀具材料、工件表面粗糙度等因素。
当工件材料的强度和硬度越高,fz越小;反之则越大。
硬质合金铣刀的每齿进给量高于同内高速钢铣刀。
工件表面粗糙度值越小,fz就越小。
4.4.4背吃刀量的确定
在机床工件和刀具的刚度允许条件下,应尽可能使背吃刀量等于工件的加工的余量。
这样可以减少走刀次数,提高生产效率。
为了保证加工表面质量,可留少量精加工余量一般留0.2~0.3mm。
根据表4-3选取切削用量:
表4-3切削用量的选取
工件材料
铝
钢
刀具直径
(mm)
刀槽数
转速(r/min)
进给速度
(mm/min)
转速(r/min)
进给速度
(mm/min)
切削速度
(m/min)
每齿进给量
(mm/齿)
切削速度
(m/min)
每齿进给量
(mm/齿)
12
2
3450
372
695
84
285
0.07
26
0.06
16
2
2800
343
610
80
268
0.07
24
0.06
20
2
2560
326
550
75
253
0.07
23
0.05
100
2
820
152
400
75
55
0.07
15
0.05
7
2
2360
284
720
86
250
0.07
17
0.04
根据表4-3选取背吃刀量为:
粗加工2mm,精加工0.2mm。
4.5进给路线的确定
进刀方式是指加工零件前,刀具接近工件表面的运动方式;退刀方式是指零件(或零件区域)加工结束后,刀具离开工件表面的运动方式。
这两个概念对复杂表面的高精度加工来说是非常重要的。
进刀、退刀路线是为了防止过切、碰撞和飞边,在切入前和切出后的引入点和切出点引出的线。
进刀,退刀方式有如下几种:
1、沿坐标轴的Z轴方向直接进刀、退刀
2、沿曲面的切失方向以直线进刀或退刀
3、沿曲面的失方向进刀或退刀
4、沿圆弧旋线或斜线退刀
5、沿螺旋线斜线进刀方式
对精度要求很高的面来说,应选择沿面的切矢方向或圆弧方向进刀,退刀方式,这样不会在工件的进刀或退刀处留下驻刀痕迹而影响工件的表面加工质量。
4.6填写工艺文件
4.6.1机械加工工艺过程卡
表4-4烟灰缸加工工艺过程片
工序号
工序名称
工序内容
设备
1
备料
毛坯105mm×105mm×30mm
2
划
划前后面加工线
3
铣削
铣削夹持面
虎钳
粗铣各部分尺寸
立式加工中心
精铣各部分尺寸
4
钳
去毛刺
锉刀
5
清洗
6
检测
检验各部分尺寸及精度
量具
表4-5烟灰缸上盖加工工艺过程片
工序号
工序名称
工序内容
设备
1
备料
毛坯105mm×105mm×21mm
2
划
划前后面加工线
3
铣削
铣削夹持面
虎钳
粗铣各部分尺寸
立式加工中心
精铣各部分尺寸
4
钳
去毛刺
锉刀
5
清洗
6
检测
检验各部分尺寸及精度
量具
4.6.2数控加工工序卡
表4-6粗/精铣上表面
工厂
数控加工工序卡
产品名称或代号
零件图号
烟灰缸
(1)
材料
铸铝
使用设备
KVC650
工序号
2
程序编号
夹具名称
平口虎钳
夹具编号
工步号
工步内容
刀具号
刀具规格/mm
主轴转速/(r/min)
进给速度
/(mm/min)
背吃刀量/mm
备注
1
粗铣上平面
T01
Ф100
820
152
2
2
精铣上平面
T02
Ф20
2650
326
0.2
表4-7粗/精铣外轮廓
工厂
数控加工工序卡
产品名称或代号
零件图号
烟灰缸
(1)
材料
铸铝
使用设备
KVC650
工序号
2
程序编号
夹具名称
平口虎钳
夹具编号
工步号
工步内容
刀具号
刀具规格/mm
主轴转速/(r/min)
进给速度
/((mm/min))
背吃刀量/mm
备注
1
粗铣外轮廓
T02
Ф20
2340
280
2
2
精铣外轮廓
T02
Ф20
2560
326
0.2
表4-8粗/精铣内型腔
工厂
数控加工工序卡
产品名称或代号
零件图号
烟灰缸
(1)
材料
铸铝
使用设备
KVC650
工序号
2
程序编号
O0003
夹具名称
平口虎钳
夹具编号
工步号
工步内容
刀具号
刀具规格/mm
主轴转速/(r/min)
进给速度
/(mm/min)
背吃刀量/mm
备注
1
粗铣内型腔
T03
Ф12
3200
345
2
2
精铣内型腔
T03
Ф12
3450
370
0.2
表4-9粗/精铣凸台轮廓
工厂
数控加工工序卡
产品名称或代号
零件图号
烟灰缸
(1)
材料
铸铝
使用设备
KVC650
工序号
2
程序编号
O0009
夹具名称
平口虎钳
夹具编号
工步号
工步内容
刀具号
刀具规格/mm
主轴转速/(r/min)
进给速度
/(mm/min)
背吃刀量/mm
备注
1
粗铣凸台轮廓
T02
Ф20
2340
280
2
2
精铣凸台轮廓
T02
Ф20
2560
326
0.2
表4-10粗/精铣放烟槽
工厂
数控加工工序卡
产品名称或代号
零件图号
烟灰缸
(1)
材料
铸铝
使用设备
KVC650
工序号
2
程序编号
夹具名称
平口虎钳
夹具编号
工步号
工步内容
刀具号
刀具规格/mm
主轴转速/(r/min)
进给速度
/(mm/min)
背吃刀量/mm
备注
1
粗铣放烟槽
T04
Ф7
2360
250
2
2
精铣放烟槽
T04
Ф7
2855
286
0.2
表4-11粗/精铣底座底面
工厂
数控加工工序卡
产品名称或代号
零件图号
烟灰缸
(1)
材料
铸铝
使用设备
KVC650
工序号
2
程序编号
夹具名称
平口虎钳
夹具编号
工步号
工步内容
刀具号
刀具规格/mm
主轴转速/(r/min)
进给速度
/(mm/min)
背吃刀量/mm
备注
1
粗铣底座
T02
Ф20
2340
280
2
2
精铣底座
T02
Ф20
2560
326
0.2
表4-12粗/精铣上盖内型腔
工厂
数控加工工序卡
产品名称或代号
零件图号
烟灰缸
(2)
材料
铸铝
使用设备
KVC650
工序号
2
程序编号
O0006
夹具名称
平口虎钳
夹具编号
工步号
工步内容
刀具号
刀具规格/mm
主轴转速/(r/min)
进给速度
/(mm/min)
背吃刀量/mm
备注
1
粗铣内型腔
T05
Ф16
2435
267
2
2
精铣内型腔
T05
Ф16
3216
324
0.2
表4-13刀具卡片
产品名或代号
零件名称
烟灰缸
零件图号
程序序号
工步号
刀具号
刀具名称
刀柄型号
刀具直径/mm
刀具长度/mm
补偿值/mm
备注
1
T01
面铣刀Ф100mm
BT40
Ф100
50
-25
2
T02
立铣刀Ф20mm
BT40
Ф20
75
0
3
T03
立铣刀Ф12mm
BT40
Ф12
75
0
4
T04
立铣刀Ф7mm
BT40
Ф7
75
0
5
T05
球头铣Ф16m