精密加工技术的发展现状与应用.docx
《精密加工技术的发展现状与应用.docx》由会员分享,可在线阅读,更多相关《精密加工技术的发展现状与应用.docx(14页珍藏版)》请在冰豆网上搜索。
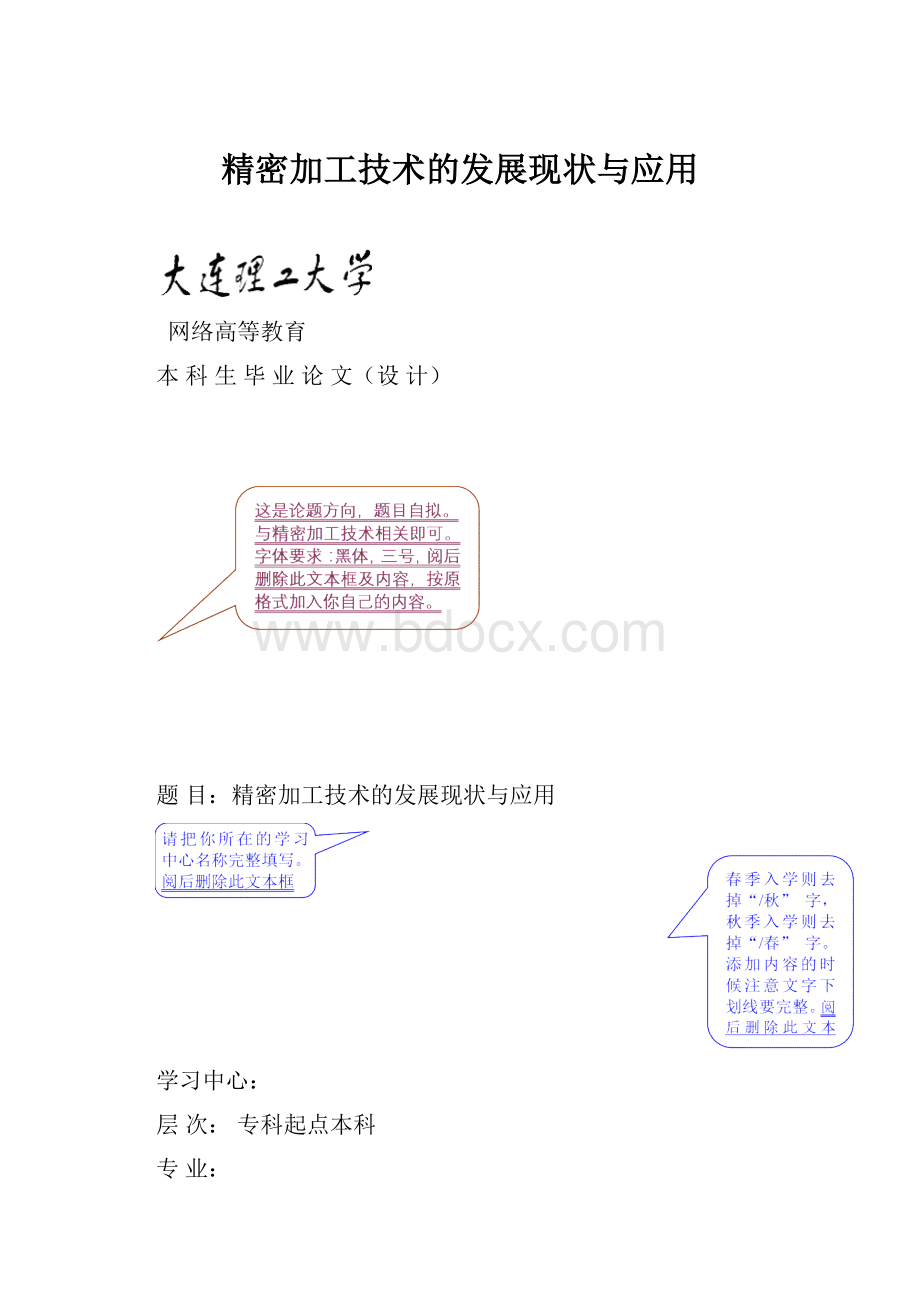
精密加工技术的发展现状与应用
网络高等教育
本科生毕业论文(设计)
题目:
精密加工技术的发展现状与应用
学习中心:
层次:
专科起点本科
专业:
年级:
年春/秋季
学号:
学生:
指导教师:
完成日期:
年月日
内容摘要
通过对(
)等几种传统精密加工方法的论述对比,论述现有的传统精密加工方法;再通过对(
字体要求:
宋体,小四号,行距为固定值22磅。
阅后删除此文本框及内容,按原格式加入你自己的内容。
然后去掉下划线或括号。
)的最新精密加工发展来论述目前国内精密加工发展趋势及前景;同时通过对(
)等发达国家最新的精密加工技术发展情况来论述目前国外精密加工技术的发展方向及前景。
最后论述的精密加工和超精密加工的几点问题。
关键词:
写作规范;排版格式;毕业论文
引言
为了满足现代先进制造与加工技术的需要,提高生产效率和改善零件的加工质量,精密加工技术和超精密加工技术已成为目前高科技技术领域的基础,超精密加工技术已成为社会生产发展的一个重大趋势。
(从引言开始是正文的第一页,页码从1开始编排。
注意引言内容不要与摘要内容雷同。
引言,或称前言,主要阐述立题的背景与问题的提出。
诸如本课题所及的国内外现状、理论依据、研究的意义,并点出自己要研究的主题和本论文要解决的问题等。
)
页码,宋体,五号,居中,底部,正文起始页页码为1。
阅后删除此文本框
1精密加工技术的发展现状
注:
章、节序号的后面,空一个字——即汉字输入状态下敲两下空格键。
这样,序号与标题文字之间界限清楚。
阅后删除此文本框。
1.1砂带研磨
砂带研磨是用粘有磨料的混纺布为磨具对工件进行加工,属于涂附磨具削加工的范畴,有生产率高、表面质量好,使用范围广等特点。
国外在砂带材料及制作工艺上取得了很大的成就,有了适应于不同场合的砂带系列,生产出通用和专用的砂带磨床,而且自动化程度不断提高(己有全自动和自适应控制的砂带磨床),但国内砂带品种少,质量也有待提高,对机床还处于改造阶段。
(
)
1.2精密切削
也称金刚石刀具切削(SPDT),是用高精密的机床和单晶金刚石刀具进行切削加工,主要用于铜、铝等不宜磨削加工的软金属的精密加工,如计算机用的磁鼓、磁盘及大功率激光用的金属反光镜等,比一般加工精密要高1---2个等级。
例如用精密车削加工的液压马达转子柱塞孔圆柱度为0.5~1μm,红外反光镜的表面粗糙度Ra0.01~0.02μm,还具有较好的光学性质[1]。
从成本上看,用精密切削加工的光学反射镜,与过去用镀铬经磨削加工的产品相比,成本大约是后者的一半或几分之一。
但许多因素对精密切削的效果有影响,所以要达到预期的效果很不容易。
同时,金刚石刀具切削较硬的材料时磨损较快,如切削黑色时磨损速度比切削铜104倍,而且加工出的工件的表面粗糙度和几何形状精度均不理想。
(
)
1.3超精密磨削
用精确修整过的砂轮在精密磨床上进行的微量磨削加工,金属的去除量可在亚微米级甚至更小,可以达到很高的尺寸精度、形位精度和很低的表面粗糙度值。
尺寸精度0.1—0.3µm,表面粗糙度Ra0.2—0.05µm,效率高,应用范围广泛,从软金属到淬火钢、不锈钢、高速钢等难切削材料,及半导体、玻璃、陶瓷等硬脆非金属材料,几乎所有的材料都可以利用磨削进行加工。
但磨削加工后,被加工的表面在磨削力及磨削热的作用下金相组织要发生变化,易产生加工硬化、淬火硬化、热应力层、残余应力层和磨削裂纹等缺陷,需要合理管控。
(
)
1.4珩磨
珩磨是用油石砂条组成的珩磨头,在一定压力下沿工件表面往复运动,加工后表面粗糙度可达Ra0.4—0.1µm,最好可到Ra0.025µm,主要用来加工铸铁及钢,不宜用来加工硬度小韧性好的有色金属。
(
)
1.5精密研磨
精密研磨是与抛光通过介于工件和工具间的磨料及加工液,工件及研具作相互机械磨擦,使工件达到要求尺寸与精度的加工方法。
精密研磨与抛光对于金属和非金属工件都可以达到其他加工方法所不能达到的精度和表面粗糙度,被研磨表面的粗糙度Ra≤0.025µm,加工变质层很小,表面质量高,精密研磨的设备简单,主要用于平面、圆柱面、齿轮面及有密封要求的配偶件的加工,也可用于量规、量块、喷油嘴、阀体与阀芯的光整加工。
但精密研磨的效率低,如干研速度一般为10---30m/min,湿研速度为20---120m/min。
对加工环境要求严格,防止有大磨料或异物混入时,将使表面产生很难去除的划伤。
(
)
1.6抛光
抛光是利用机械、化学、电化学的方法对工件表面进行的一种微细加工,主要用来降低工件表面粗糙度,常用的方法有:
手工或机械抛光、超声波抛光、化学抛光、电化学抛光及电化学机械复合加工等。
手工或机械抛光是用涂有磨膏的抛光器,在一定的压力下,与工件表面做相对运动,以实现对工件表面的光整加工。
加工后工件表面粗糙度Ra≤0.05µm,可用于平面、柱面、曲面及模具型腔的抛光加工。
手工抛光的加工效果与操作者的熟练程度有关。
超声波抛光是利用工具端面做超声振动,通过磨料悬浮液对硬脆材料进行光整加工,加工精度0.01~0.02µm,表面粗糙度Ra0.1µm。
超声抛光设备简单,操作、维修方便,工具可用较软的材料制作,而且不需作复杂的运动,主要用来加工硬脆材料,如不导电的非金属材料,当加工导电的硬质金属材料时,生产率较低。
化学抛光是通过硝酸和磷酸等氧化剂,在一定的条件下,使被加工的金属表面氧化,使表面平整化和光泽化。
化学抛光设备简单,可以加工各种形状的工件,效率较高,加工的表面粗糙度一般为Ra≤0.2µm,但腐蚀液对人体和设备有损伤,污染环境,需妥善处理。
主要用来对不锈钢、铜、铝及其合金的光亮修饰加工。
电化学抛光是利用电化学反应去除切削加工所残留的微观不平度,以提高零件表面光亮度的方法。
它比机械抛光具有较高的生产率和小的表面粗糙度:
一般可达Ra0.2µm,若原始表面为Ra0.4~0.2µm,则抛光后可提高到Ra0.1~0.08µm,加工后工件具有较好的物理机械性能,使用寿命长,但电化学抛光只能加工导电的材料。
随着电化学加工技术的发展,还产生了多种新型的复合加工方法,例如超精密电解磨削、电化学机械复合光整加工、电化学超精加工等。
它们主要以降低工件的表面粗糙度值为目的,加工去除量很小,一般在0.01~0.1mm,对于表面粗糙度达到Ra0.8~1.6µm的外圆,平面、内孔及自由曲面均可一道工序加工到镜面,表面粗糙度Ra0.05µm,甚至更低。
电化学机械加工属于一种加工单位极小的精密加工方法,从原理上讲加工精度可以达到原子级,所以加工精度具有大的潜力,但由于左右其加工精度的因素目前还不是很清楚,所以在实际应用中,其加工表现出一定的不稳定性,这在很大程度上限制了它在工业生产中的应用。
(
)
2国内精密加工技术发展现状
(2.1北京机床研究所
北京机床研究所是国内进行精密加工技术研究院的主要单位之一,研究出了多种不同类型的超精密机床、部件和相关的高精度测试仪器等,如精度达0.025µm的精密轴承、JCS-027超精密车床、JCS-031超精密铣床、JCS-035精密车床、超精密车床数控系统、复印机感光鼓加工机床、红外大功率激光反光镜、超精密振动一位移测微仪等,达到了国内领先、国际先进水平[2]。
2.2航天航空工业部三零三部所
航天航空工业部三零三部所在超精密主轴、花岗岩坐标量测机等方面进行了研究及产品生产。
哈尔滨工业大学在金刚石超精密切削、金刚石刀具晶体定向和刃磨、金刚石微粉砂轮电解在线休整技术等方面进行了卓有成效的研究。
清华大学在集成电路超精密加工设备、磁盘加工及检测设备、微位移工作台、超精密砂带磨削和研抛、金刚石微粉砂轮超精密切削、非圆截面超精密切削等方面进行了深入研究,并有相应产品问世。
3.3其他研究所
中科院长春光学精密机械研究所、华中理工大学、沈阳第一机床厂、成都工具研究所、国防科技大学等都进行了这一领域的研究,成绩显著。
但总体来说。
我国在超精密加工的效率、精度可靠性,特别是规格(大尺寸)和技术配套性方面与国外比,与生产实际要求比,还有相当大的差距。
3.4超精密加工技术发展趋势
超精密加工技术向更高精度、更高效率方向发展;向大型化、微型化方向发展;向加工检测一体化方向发展;机床向多功能模块化方向发展;不断探讨适合于超精密加工的新原理、新方法、新材料。
)
3国外精密加工技术发展趋势
3.1美国
美国是开展超精密加工技术研究最早的国家,也是迄今处于世界领先地位的国家。
早在50年代末,由于航天等尖端技术发展的需要,美国首先发展了金刚石刀具的超精密切削技术,称为“SPDT技术”(SinglePointDiamondTurning)或“微英寸技术”(1微英寸=0.025µm),并发展了相应的空气轴承主轴的超精密机床。
用于加工激光核聚变反射镜、战术导弹及载人飞船用球面非球面大型零件等等。
如美国LLL实验室和Y-12工厂在美国能源部支持下,于1983年7月研制成功大型超精密金刚石车床DTM-3型,该机床可加工最大零件2100mm、重量4500kg的激光核聚变用的各种金属反射镜、红外装置用零件、大型天体望远镜(包括x光天体望远镜)等,该机床的加工精度可达到形状误差为28nm(半径),圆度和平面度为12.5nm,加工表面粗糙度为Ra4.2nm.该机床与该实验室1984年研制LODTM大型超精密车床一起仍是现在世界上公认的技术水平最高、精密度最高的大型金刚石超精密车床。
(
)
3.1欧洲
英国克兰菲尔德技术学院所属的克兰菲尔德精密工程研究所(简称CUPE)享有较高声誉,它是当今世界上精密工程的研究中心之一,是英国超精密加工技术水平的独特代表。
如CUPE生产的Nanocentre(纳米工中心)既可进行超精密车削,又带有磨头,也可进行超精密磨削,加工工件的形状精度可达0.1µm,表面粗糙度Ra<10nm。
(
)
3.2日本
字体要求:
宋体,小四号,行距为固定值22磅。
阅后删除此文本框及内容,按原格式加入你自己通过查找资料的内容。
然后去掉下划线或括号。
最好有图片。
日本对超精密加工技术的研究相对于美,英来说起步较晚,但是当今世界上超精密加工技术发展最快的国家.日本的研究重点不同于美国,前者是以民品应用为主要对象,后者则是以发展国防尖端技术为主要目标.所以日本在用于声、光、图象、办公设备中的小型、超小型电子和光学零件的超精密加工技术方面,是更加先进和具有优势的,甚至超过了美国。
(
)
4精密加工技术
4.1精密加工技术
精密加工是指加工精密范围为1-0.1µm,表面精糙度为Ra0.1---0.01µm的加工技术要求[3]。
精密加工技术主要包括:
微细加工和超微细加工、光整加工等加工技术。
4.2超精密加工技术
超精密加工是指被加工零件的尺寸精度高于0.1µm,表面粗糙度Ra小于0.025µm,以及所用机床定位精度的分辨率和重复性高于0.01µm的加工技术,亦称之为亚微米级加工技术,且正在向纳米级加工技术发展。
我们知道,这个界限是有限的,随着加工技术的进步不断变化,今天的超精密加工可能就是明天的一般加工[4]。
超精密加工技术主要包括:
超精密加工的机理研究,超精密加工的设备制造技术研究,超精密加工工具及刃磨技术研究,超精密测量技术和误差补偿技术研究,超精密加工工作环境条件研究。
4.3二者面临的问题
加工精度,包括形位公差、尺寸精度及表面况状,有无表面缺陷也是这一问题的核心。
加工效率,有此类加工可以取得较好的加工精度,却难以取得高的加工效率。
(
字体要求:
宋体,小四号,行距为固定值22磅。
阅后删除此文本框及内容,按原格式加入你自己通过查找资料的内容。
然后去掉下划线或括号。
最好有图片。
)
5研究和探讨
5.1精密加工技术
努力开发加工单位极小的精密加工方法,必须在加工原理的本身就使其误差分散在1nm以下的水平。
目前加工单位比较小的加工方法主要有弹性破坏加工、化工加工、离子束加工、等离子加工等。
目前的金刚石切削和金刚石砂轮精密磨削从其加工原理上看,其加工单位就很大。
5.2开发精密的机械机构
不论是加工装置还是测量装置,都需要精密的机械机构,包括导轨、进给机构及轴承等,超精密空气静压导轨是目前最好的导轨,其直线度可达0.1~0.2µm/250mm,通过补偿技术还可以进一步提高直线度,但是它没有液压静压导轨的刚性大。
同时,由于空气静压导轨的气膜厚度只有10µm左右,所以在使用过程中,要注意防尘。
另外,在导轨的设计中,还可以用多根导轨并联来均化气膜的误差。
用高弹性合金、红宝石制造的滚动导轨,系统误差在0.5µm左右,随机误差不超过0.1µm,确保产品的可靠性。
目前超精密加工所使用的磁悬浮轴承主轴精度低于空气静压轴承主轴,空气静压轴承主轴的回转精度可达0.5µm,国外可达到0.03µm,但这仍然无法满足纳米加工对主轴的精度要求。
要想提高空气静压轴承的回转精度就必须提高轴承的回转精度,而空气静压轴承精度是轴承部件圆度的1/15~1/20,所以,要得到10nm的回转精度,轴和轴套的圆度要达到0.15-0.20µm,同时为了气体流出的均匀性,对于纳米的主轴,多采用此类加工方法。
5.3开发高精度的测试系统
在目前的超精密加工领域中,对加工精度的测量主要有两种方法;激光检测和光栅的测量,而光栅的测量应用最为广泛,精度可达nm级,如北京光电仪研究中心的光栅系统可达0.1µm,俄罗斯的全息光栅系统达10nm,LG100光栅系统的分辨率可达0.1µm,测量范围为100mm[5]。
开发系统误差小、精度高和可靠性高的检测仪器和控制装置的前提是开发高性能的传感器以及祠服从机构。
如果开发出高性能的传感器以及祠服从机构及高精度、高速度和高可靠性的读出装置,就可以通过使用计算机进行检测、分析及计算,以提高检测精度。
与超精密加工有关的技术问题还有很多方面,如湿度控制技术、振动控制技术、环境控制技术等。
比如材料的弹性变形和热变形,就很难使材料的去除加工达到原子级的精度,长100mm的钢制零件,要控制其热变形在0.01mm以内,就必须控制温度变化在0.01℃以内,这在加工领域还很难实现。
只要在上述的一个方面取得发展或突破,必将引导精密加工技术的高速发展。
5.4开发适用于精密加工并能取得高精度、高表面质量的新型材料
例如最近开发超微粉烧结金属、非结晶金属、超微粉陶瓷、非结晶半导体陶瓷、复合、高分子材料等。
只要在上述的方面一个取得发展或突破,必将导致精密加工技术的高速发展。
6结论
字体要求:
宋体,小四号,行距为固定值22磅。
阅后删除此文本框及内容,按原格式加入你自己的内容。
然后去掉下划线或括号。
精密加工方法在今天显得越来越重要,精密加工技术已成为目前高科技技术领域的基础,提高超精密加工的精度已成为目前迫在眉睫的问题。
目前,很多学者正在这方面做着大量的研究和实验,相信不久的将来,超精密加工会取得长足进展。
(
)
参考文献
[1]袁哲俊,王先逵.精密和超精密加工技术.第一版.北京:
机械工业出版社,2007.63-68.
[2]文秀兰,林宋,谭昕,种建林.超精密加工技术与设备.第一版.北京:
化学工业出版社,2006.22-26.
[3]刘贺云,柳世传.精密加工技术.第一版.武汉:
华中理工大学出版社,1991.28-32.
[4]戴一帆、李圣怡.超精密加工精度分析.中国机械工程,1999,10
(2):
2-5.
[5]周旭光.特种加工技术.第一版.西安:
西安电子科技大学出版社,2004.119-123.