任务4精车台阶轴.docx
《任务4精车台阶轴.docx》由会员分享,可在线阅读,更多相关《任务4精车台阶轴.docx(16页珍藏版)》请在冰豆网上搜索。
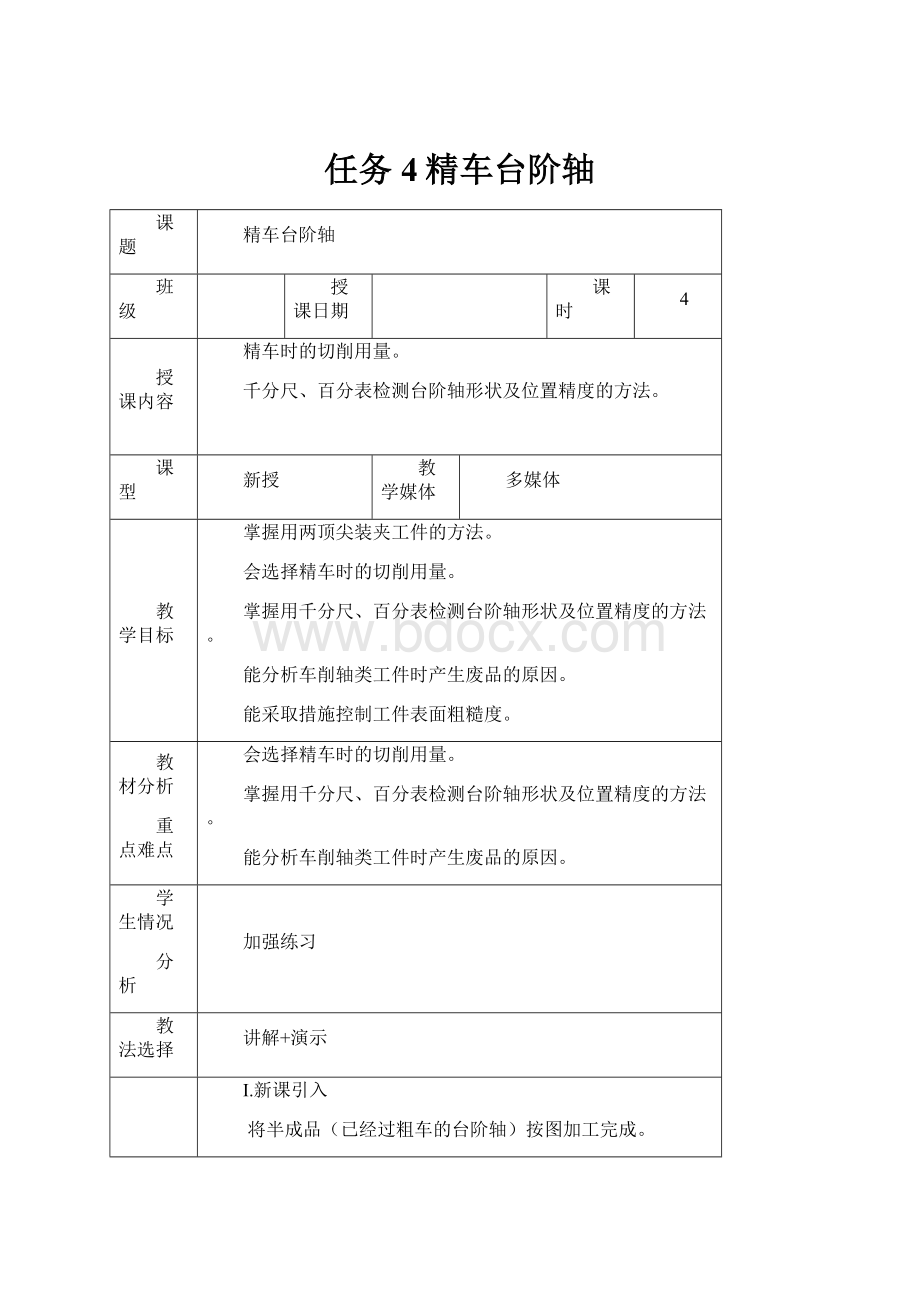
任务4精车台阶轴
课题
精车台阶轴
班级
授课日期
课时
4
授课内容
精车时的切削用量。
千分尺、百分表检测台阶轴形状及位置精度的方法。
课型
新授
教学媒体
多媒体
教学目标
掌握用两顶尖装夹工件的方法。
会选择精车时的切削用量。
掌握用千分尺、百分表检测台阶轴形状及位置精度的方法。
能分析车削轴类工件时产生废品的原因。
能采取措施控制工件表面粗糙度。
教材分析
重点难点
会选择精车时的切削用量。
掌握用千分尺、百分表检测台阶轴形状及位置精度的方法。
能分析车削轴类工件时产生废品的原因。
学生情况
分析
加强练习
教法选择
讲解+演示
Ⅰ.新课引入
将半成品(已经过粗车的台阶轴)按图加工完成。
Ⅱ.新课
一、工件用两顶尖装夹
1.装夹形式
用两顶尖装夹工件
1—前顶尖2—鸡心夹头3—工件4—后顶尖
2.适用场合
适用于轴类工件的精加工或须经多次装夹加工的工件,以及工序较多、车削后还须铣削、磨削等加工的工件。
3.装夹特点
采用两顶尖装夹的特点是装夹方便,不需找正,装夹精度高;缺点是装夹刚度低,影响切削用量的提高。
4.前顶尖
前顶尖分为装夹在主轴锥孔内的前顶尖和在卡盘上车制的前顶尖两种。
工作时前顶尖随同工件一起旋转,与中心孔无相对运动,不产生摩擦。
前顶尖
a)主轴孔内的前顶尖b)在卡盘上车制的前顶尖
5.鸡心夹头
用鸡心夹和前顶尖装夹工件时,靠鸡心夹4和螺钉1夹紧工件5一端外圆处,并使夹头上的弯拨杆2伸出工件轴端,夹头的弯拨杆插入拨盘3的凹槽中,通过拨盘来带动工件回转。
用拔盘带动工件转动
1—紧固螺钉2—拨杆3—拨盘4—鸡心夹头5—工件6—尾座锁紧手柄
二、精车时工件的检测
1.长度尺寸的测量
可用游标卡尺或游标深度尺测量长度尺寸。
2.外径尺寸的测量
可用千分尺测量外径尺寸
千分尺(最常用,精度为0.01㎜)
用途分:
外径千分尺、内径千分尺、深度千分尺、内测千分尺螺纹千分尺、壁厚千分尺等
⑴结构形状
测力装置:
保证测量面与工件接触时具有恒定的测量力,以便
测出正确的尺寸测量前必须校零
⑵刻线原理及读数方法
微分筒转1格时,测微螺杆移动0.01㎜
读数方法:
①先读出固定套管上露出刻线的整毫米和半毫米数;
②再看微分筒上的哪一格与固定套管的基准线对齐,读出小数
部分(0.01㎜乘以转过的格数)
③将上述两个部分的尺寸相加即为被测工件的尺寸
3.百分表
指示式量仪,其刻度值为0.01㎜。
(刻度值为0.001㎜或0.002
㎜为千分表)
作用:
测量工件的形状和位置精度,测量内径以及找正工件在机床上的安装位置
种类:
钟表式、杠杆式
原理:
钟表式——测杆的直线移动经过齿轮齿条传动放大,转变
为指针的摆动
钟表式百分表表面上一格的分度值为0.01mm,常用测量范围有0~3、0~5和0~10mm。
测量时,测量头移动的距离等于小指针的读数(整数部分)加上大指针的读数(小数部分)。
杠杆式——利用杠杆齿轮放大原理
杠杆式百分表是利用杠杆齿轮放大的原理制成的,其体积较小,由于杠杆式百分表的球面测杆可以根据测量需要改变位置,因此使用灵活、方便。
杠杆式百分表表面上一格的分度值为0.01mm,测量范围为0~0.8mm。
注意:
使用前需将长针对准“0”位,钟表式的量杆必须垂直于
被测量的工件表面
百分表
a)钟表式b)杠杆式
1—大分度盘2—小分度盘3—小指针4—大指针5—测量杆6—测量头7—球面测杆
3.数显百分表
新式的钟表式百分表用数字计数器计数和读数,又称为数显百分表。
数显百分表的测量范围为0~30mm,分辨率为0.01mm。
其特点是体积小,质量小,功耗小,测量速度快,结构简单,便于实现机电一体化,且对环境要求不高。
使用百分表时的注意事项
1.百分表应固定在磁性表座或百分表支架上使用,可以调节百分表的上下、前后、左右位置。
2.测量前,应转动罩壳使表的长指针对准“0”刻线。
3.测量杆的行程不要超过它的示值范围,以免损坏表内零件。
4.提压测量杆的次数不要过多,距离不要过大,以免损坏机件及加剧零件磨损。
5.测量平面或圆形工件时,钟表式百分表的测头应与平面垂直或与圆柱形工件的中心线垂直。
6.为避免剧烈振动和碰撞,不要使测量头突然撞击在被测表面上,以防止测杆产生弯曲变形,更不能敲打表的任何部分。
7.严防水、油、灰尘等进入表内,不要随便拆卸表的后盖。
4.形状、位置精度的检测
(1)圆柱度误差的检测
工件在V形架上检测圆柱度误差
1—百分表2—被测件3—V形架
(2)端面圆跳动误差的检测
端面圆跳动误差——百分表的测量头靠在所需测量的端面上,工件转1周,百分表读数的最大差
(3)径向圆跳动误差的检测
径向圆跳动误差——百分表触头和工件外表面接触,转动工件,百分表读数最大值与最小值之差
工件在两顶尖间测量端面圆跳动和径向圆跳动误差
1,6—顶尖2—测量端面圆跳动误差3—杠杆式百分表
4—测量径向圆跳动误差5—工件
三、积屑瘤
1.形成:
用中等切削速度切削钢料或其它塑性金属,有时在车刀前面上近切削刃处牢固地粘着一小块金属,这就是积屑瘤。
2.影响
(1)保护刀具
(2)增大实际
(3)影响工件表面质量和尺寸精度
积屑瘤对粗加工有益,精加工应避免
3.影响积屑瘤的主要因素
切削速度对积屑瘤的形成影响最大。
用中等切削速度(15~30m/min时)切削塑性金属材料时,最易产生积屑瘤。
切削速度达到70m/min以上时,切削温度很高,切屑底层金属变软,磨擦系数明显下降,一般不会产生积屑瘤。
低速切削(5m/min以下),切削温度达不到冷焊温度,不会产生积屑瘤。
由此可见,在精加工时,为了避免产生积屑瘤,减小工件表面粗糙度,采用高速钢车刀低速切削(5m/min以下),或硬质合金车刀高速切削(70m/min以上)可避免和减少积屑瘤的产生。
此外,增大前角γo,减少进给量f,减小前刀面表面粗糙度值和注入充分的切削液,都可减少积屑瘤的产生。
四、工件表面粗糙度的控制
1.影响表面粗糙度的因素
(1)残留面积
(2)积屑瘤
用中等切削速度切削塑性金属产生积屑瘤后,因积屑瘤既不规则又不稳定,一方面其不规则部分代替切削刃切削,留下深浅不一的痕迹;另一方面一部分脱落的积屑瘤嵌入已加工表面,使之形成硬点和毛刺,表面粗糙度变大。
(3)振动
刀具、工件或机床部件产生周期性的振动会使已加工表面出现周期性的振纹,使表面粗糙度明显变大。
2.减小工件表面粗糙度的方法
(1)减小残留面积高度
减小主偏角和副偏角
增大刀尖圆弧半径
减小进给量
(2)防止工件表面产生毛刺
(3)避免磨损亮斑
(4)防止切屑拉毛加工表面
(5)防止和消除振纹
机床、刀具方面、工件方面切削用量方面
(6)合理选用切削液,保证充分冷却和润滑
常见表面粗糙度值大的现象
a)残留面积b)毛刺c)切屑拉毛d)振纹
五、任务实施
(一)准备工作
1.工件毛坯
按图所示检查经过粗车的半成品,看其尺寸是否留出精加工余量,形状、位置精度是否达到要求。
2.工艺装备
普通车床(配三爪自定心卡盘),前、后顶尖,鸡心夹头,0.02mm/(0~150)mm的游标卡尺,25~50mm的千分尺,百分表,45°车刀,
90°精车刀。
(二)车削步骤
步骤一:
修研中心孔(对精度要求很高的工件)
1.用三爪自定心卡盘夹住油石的圆柱部分
2.在两顶尖间装夹已粗车的工件。
3.主轴低速旋转,手握工件分别修研两端中心孔
修研中心孔
步骤二:
车削前顶尖
1.用活扳手将小滑板转盘上的前、后螺母拧松
2.将小滑板逆时针方向转30°,使小滑板上的基准“0”线与30°刻线对齐,然后锁紧转盘螺母
3.用双手配合均匀且不间断地转动小滑板手柄,手动进给分层车削前顶尖锥面(车刀应对准中心高)
4.再将转盘上的螺母拧松,将小滑板恢复到原来位置后再紧固
车削前顶尖
步骤三:
在两顶尖间装夹工件
1.用鸡心夹夹紧台阶轴右端39mm的外圆处,并使夹头的拨杆伸出工件轴端
2.根据工件长度调整好尾座位置并紧固
3.将夹有夹头一端工件的中心孔放置在前顶尖上,并使夹头的拨杆贴近卡盘的卡爪侧面
4.同时用右手摇动尾座手轮,使后顶尖顶入工件中心孔
5.支顶合适后将尾座套筒的固定手柄压紧
步骤四:
精车台阶轴的左端
1.选取背吃刀量αp=0.48mm,进给量ƒ=0.1~0.2mm,转速n=500r/min
2.将90°车刀调整至工作位置,精车50±0.1mm的外圆,表面粗糙度Ra值达到3.2μm
精车Ф(50±0.1)㎜外圆
步骤五:
精车台阶轴的左端
1.精车左端外圆至尺寸要求,长度为50±0.1mm,表面粗糙度值Rα值达到3.2μm,圆柱度误差小于等于0.015mm
2.用45°车刀倒角C1.5mm
精车Ф40㎜外圆
倒角
步骤六:
精车台阶轴的右端
1.工件调头,用两顶尖装夹(铜皮垫在40mm的外圆处)
2.精车右端外圆38mm,长89.5mm至尺寸要求,表面粗糙度Rα值达到1.6μm,径向圆跳动误差小于等于0.03mm
3.用45°车刀倒角C1.5mm
精车外圆
注意事项
⒈鸡心夹必须牢靠地夹住工件,以防止车削时移动、打滑,损坏工件和车刀。
⒉注意安全,防止鸡心夹勾住工作服伤人。
3.精车台阶时,应在机动进给精车外圆至接近台阶处改动为手动进给。
4.当车至台阶面时,变纵向进给为横向进给,移动中滑板由里向外慢慢精车台阶平面,以确保其对轴线的垂直度要求。
六、轴类工件的车削质量分析
车削轴类工件时产生废品的原因及预防方法
(一)尺寸精度达不到要求:
⒈看错图样或刻度盘使用不当
⒉没有进行试车削
⒊量具有误差或测量不准确
⒋由于切削热影响使工件尺寸发生变化
⒌机动进给没有及时关闭,使车刀进给长度超过台阶长度
预防方法:
⒈看清楚图样的尺寸要求,正确使用刻度盘,看清楚刻度值
⒉根据加工余量算出背吃刀量,进行试车削,然后修正背吃刀量
⒊量具使用前必须检查和调整零位,正确掌握测量方法
⒋不能在工件温度较高时测量
⒌注意及时关闭机动进给;或提前关闭机动进给,再手动进给到所要求的长度尺寸
(二)产生锥度
⒈用一夹一顶或两顶尖装夹工件时,后顶尖轴线与主轴轴线不重合
⒉用小滑板车外圆时,小滑板的位置不正,即小滑板转盘的基准刻线不对“0”位
⒊用卡盘装夹纵向进给车削时,床身导轨与车床主轴轴线不平行
⒋装夹工件时悬伸较长,车削时因切削力的影响使前端让开,产生锥度
⒌车刀中途逐渐磨损
预防方法:
⒈车削前必须检查尾座,有偏移则进行调整。
⒉检查小滑板转盘的基准刻线是否对“0”,不对则进行调整
⒊检查车床主轴,其轴线应与床身导轨平行,否则应作调整
⒋尽量减小工件的悬伸长度,或采用后顶尖支顶,以提高装夹刚度
⒌选用合适的刀具材料
(三)圆度超差
⒈车床主轴间隙太大
⒉毛坯余量不均匀,车削过程中背吃刀量变化太大
⒊工件用两顶尖装夹时,中心孔接触不良,或后顶尖顶得不紧,或前、后顶尖产生径向跳动
预防方法:
⒈车削前检查主轴间隙,并将其调整合适。
如主轴轴承磨损严重,则需更换。
⒉经半精车后再精车。
⒊工件用两顶尖装夹时必须松紧适当,若顶尖产生径向跳动,应及时修复或更换。
(四)表面粗糙度达不到要求
⒈车床刚度不够,如滑板镶条太松,传动零件(如带轮)不平衡或主轴间隙大引起振动
⒉车刀刚度不够或伸出太长引起振动
⒊工件刚度不够引起振动
⒋车刀几何参数不合理,如选用过小的前角、后角和主偏角等;或车刀严重磨损
⒌切削用量选用不当
预防方法:
⒈消除或防止由于车床刚度不足而引起的振动(如调整车床各部分的间隙等)
⒉提高车刀刚度及正确装夹车刀
⒊提高工件的装夹刚度
⒋需用合理的车刀几何参数(如适当增大前角,选择合理的后角和主偏角等);重磨车刀
⒌进给量不宜太大,精车余量和切削速度应选择恰当
Ⅲ.总结
通过学习学生会以下内容
掌握用两顶尖装夹工件的方法。
会选择精车时的切削用量。
掌握用千分尺、百分表检测台阶轴形状及位置精度的方法。
能分析车削轴类工件时产生废品的原因。
能采取措施控制工件表面粗糙度。
Ⅳ.布置作业
Ⅴ.板书设计
一、工件用两顶尖装夹
二、精车时工件的检测
三、积屑瘤
四、工件表面粗糙度的控制
五、任务实施
六、轴类工件的车削质量分析