创新标杆精细管理交流材料.docx
《创新标杆精细管理交流材料.docx》由会员分享,可在线阅读,更多相关《创新标杆精细管理交流材料.docx(12页珍藏版)》请在冰豆网上搜索。
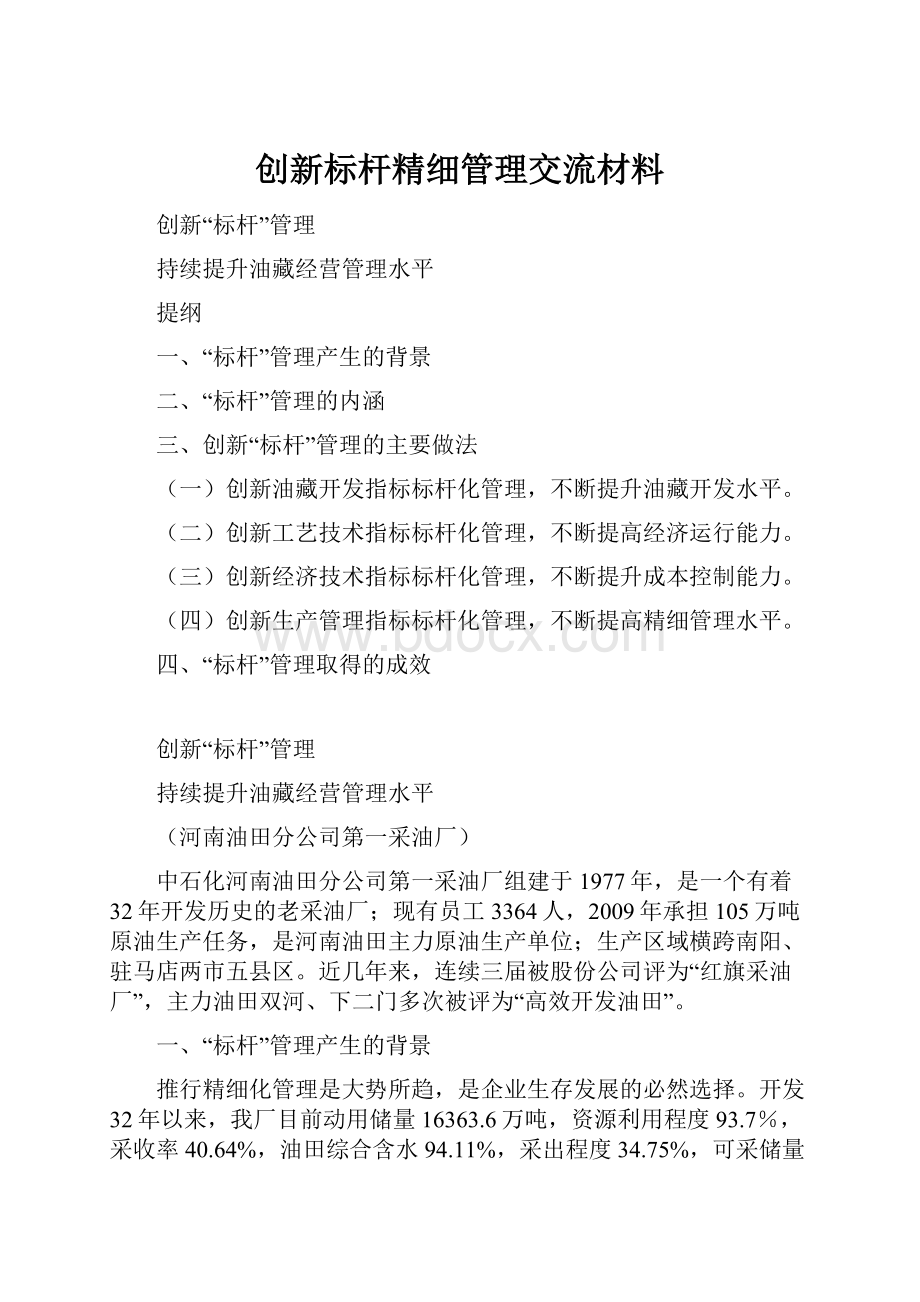
创新标杆精细管理交流材料
创新“标杆”管理
持续提升油藏经营管理水平
提纲
一、“标杆”管理产生的背景
二、“标杆”管理的内涵
三、创新“标杆”管理的主要做法
(一)创新油藏开发指标标杆化管理,不断提升油藏开发水平。
(二)创新工艺技术指标标杆化管理,不断提高经济运行能力。
(三)创新经济技术指标标杆化管理,不断提升成本控制能力。
(四)创新生产管理指标标杆化管理,不断提高精细管理水平。
四、“标杆”管理取得的成效
创新“标杆”管理
持续提升油藏经营管理水平
(河南油田分公司第一采油厂)
中石化河南油田分公司第一采油厂组建于1977年,是一个有着32年开发历史的老采油厂;现有员工3364人,2009年承担105万吨原油生产任务,是河南油田主力原油生产单位;生产区域横跨南阳、驻马店两市五县区。
近几年来,连续三届被股份公司评为“红旗采油厂”,主力油田双河、下二门多次被评为“高效开发油田”。
一、“标杆”管理产生的背景
推行精细化管理是大势所趋,是企业生存发展的必然选择。
开发32年以来,我厂目前动用储量16363.6万吨,资源利用程度93.7%,采收率40.64%,油田综合含水94.11%,采出程度34.75%,可采储量采出程度85.50%,已全面处于特高含水后期递减阶段的开发。
综合含水逐年上升,产量递减逐年加大;剩余油分布日趋复杂,认识和挖潜难度逐年加大;调整和挖潜措施效果变差,实物工作量不断增加,生产成本不断攀升,给油田进一步深度开发带来前所未有的困难和矛盾。
在这种大背景下,要实现原油稳产、成本控制等各项生产经营目标,就必须眼睛向内,苦练内功,主动挖潜,向管理要产量,向管理要效益,推行精细化管理,走内涵式发展之路。
精细化管理的持续推进,为“标杆”管理奠定了坚实的基础。
探索精细化管理,我厂先后经历了从“看板”管理、到“模板”管理、再到“标杆”管理的三个阶段。
2001年,借鉴松下管理经验,推行“成本费用看板管理法”,把成本费用绘制成图板,将指标倒算分解,让员工了解费用,分析节超原因,制订措施办法,初步实现了生产现场管理和成本现场管理的有机结合,营造了全员参与成本控制的氛围。
2005年,推行以“一井一策”为核心内容和以“设备长周期经济运行”为主的精细化管理。
同时,借助股份公司推行经济活动分析模板之际,我厂不断深化模板的推广运用,通过完善基础消耗台帐,规范基础资料,梳理生产流程,细分控制节点,创建了采油厂经济基础数据统计模板,建立经济技术指标数据对比分析支撑体系,完善了厂、矿、队三级经济活动分析机制,各项生产经济技术管理指标得以量化。
2007年,为建立良性的经济技术指标循序提升机制,深入推进精细管理,我厂实施“标杆”管理,逐步建立经济技术指标“标杆”体系,搭建厂、矿、队、站多层次的“比优赛好”平台。
先后得到了油田分公司、集团公司的充分肯定,多次组织现场经验交流,有力地促进了“标杆”管理的深度推广。
“标杆”管理迅速在全厂6个矿大队、12个采油队、5个联合站、4个测试队、130个计量站和班组全面展开。
当前,我厂“标杆”管理工作流程和运作体系日臻成熟,已经成为推进精细化管理的一个利器。
二、“标杆”管理的内涵
经过多年的探索实践,不断创新和完善,逐步凝炼出符合我厂油藏经营管理实际的“标杆”管理内涵和体系。
“标杆”管理涵义:
是指一个企业在不断寻找最佳指标的过程中,通过比较、分析、判断,把较为先进的指标作为标杆,从而推动企业内部不断改进、超越自己、超越标杆、追求卓越,创造优异业绩。
“标杆”管理基本原理:
以行业、系统、部门中的最佳指标为基准,通过分类排序、找准定位、比较分析、重新设计等一系列措施,使学习有榜样,赶超有目标,最终达到“全面对接、重点剖析、扬长治短、整体提升”的目的。
“标杆”管理基本理念:
“产量、安全、成本”三位一体化管理。
“标杆”管理原则:
没有最好,只有更好。
“标杆”管理宗旨:
始终追求更优的运行参数;始终追求更高的开发水平;始终追求更好的开发效益。
“标杆”管理目标:
在竞争中不断进步、不断成长。
“标杆”管理流程:
分级成立“标杆”管理领导小组,建立厂、矿、队、站四级管理机构,专人管理,专人负责;通过定标、立标、对标、超标、奖标、再立标,形成了指标循序提升的“标杆”管理良性运作机制。
三、创新“标杆”管理的主要做法
在“产量、安全、成本”三位一体管理理念的统领下,我厂创新观念,科学实践,丰富和拓展“标杆”管理的内涵和外延。
强化“安全生产是本职、经济运行是水平”思想;倡导岗位员工“安全经济地把事情做正确”;营造时时要产量、人人要安全、个个讲成本的氛围;力求参数最优、产量最佳、效益最大。
在采油、集输、测试三大系统设置30个标杆指标。
使“标杆”管理融入生产经营全过程,不断推动“标杆”管理向纵深发展。
(一)创新油藏开发指标标杆化管理,不断提升油藏开发水平。
地质系统结合自身特点,把储量、采收率、自然递减、含水上升率四项核心开发指标作为“标杆”指标来管理,精雕细刻,精查细找,精益管理,不断提升油藏开发管理水平。
一是精雕细刻,精耕细作,努力增加可采储量,提高采收率。
以“主力油田采收率突破50%、力争60%”为目标,培育水驱开发、三次采油、滚动勘探三个主战场。
水驱油藏:
抓住油田注水开发的灵魂,把分注井层段合格率作为标杆指标,点面结合,提升注水效率,实现了“由定期季度整体调整转变为定期与不定期相结合随时调整;由主要考虑注采及压力平衡指标转变为主要考虑剩余油的流动和采出;由动态变化后被动调整转变为围绕实现地质目标的超前培育调整”的三个转变,年增油在1.5万吨以上。
三采油藏:
形成了以“调、堵、分、解、修”为核心的三次采油动态调整技术体系。
“调”:
就是细化调整,分区实现注聚浓度的优化调整,预见性动态调整,促进弱势方向油井见效扩大聚驱效果。
“堵”:
就是堵水调剖,聚窜井堵水、注聚过程及时调剖,减缓窜流,扩大注聚波及体积。
“分”:
就是分注分采,减小层间干扰。
“解”:
就是分类解堵,提高储量动用程度。
“修”:
就是修换并用,保持正常注聚。
截止2009年上半年,累计注聚井223口,累计注干粉41782吨,注交联剂10407吨,累计增油120.3万吨,提高采收率5.5个百分点。
滚动开发:
解放思想、冲破禁锢,精查细找,通过老储层重新认识、分析、论证,寻找各种类型的新储量,形成以“隐蔽圈闭评价”为核心的滚动增储技术体系。
2007年以来,老井复查165层,共找到各种类型的新储量48层、206.9万吨。
利用51口长停井、低效井补孔,累计产油6.2万吨。
近年来,我厂分注井层段合格率始终保持在70%以上,可采储量持续增加,采收率持续提高。
与2007年相比,可采储量由6520.5万吨提高到6650.6万吨;采收率达到40.64%,其中主力油田双河、下二门、魏岗采收率分别达44.41%、46.34%和46.38%。
二是精细研究,精益开发,努力实现主力油层深度开发。
重点开展了“四个评价一个恢复”,即:
主力油层流动单元潜力评价和细分动用;中强水淹层、同层潜力评价和分类动用;长期封堵层油气再富集评价和择优动用;高含水井间剩余油评价与平面液流转向;主力油层注采井网恢复与面积动用率提高。
近三年先后在双河油田Ⅰ5Ⅱ1-3、Ⅳ5-11、Ⅴ下、Ⅵ、Ⅶ下、ⅧⅨ等6个单元开展了规模研究和动用,增加可采储量135万吨,提高采收率2-3个百分点。
三是以油藏经营管理为中心,建立三级目标管理体系。
进一步明确原油产量和主要开发指标的责任比重和控制目标,把开发指标作为标杆指标细分到区块单元、油矿、采油队,完善生产运行预警和考核机制,建立与油藏经营管理相适应的厂、矿、队三级目标化管理体系:
厂(地研所)负责油藏、开发单元技术政策、攻关研究、指标控制,开发部署、调整、目标检查考核;油矿负责油藏单元指标的变化分析、实时监控、方案实施;采油队负责资料采集、日常动态变化分析及生产基础管理。
把主要开发指标纳入绩效考核之中,按季度、半年、年度进行考核,充分发挥考核激励约束作用。
(二)创新工艺技术指标标杆化管理,不断提高经济运行能力。
围绕提高“三大系统”效率、提升作业效能、延长设备运行周期等工艺技术指标,优化调整,攻坚克难,不断提升经济运行能力和水平。
一是优化运行参数,提高机采系统、注水系统效率。
按照“查-定-治-比-超”管理运行模式,优化运行参数,提高系统效率。
查:
对全厂各采油队、计量站、单井的机采效率进行详细排查、找准挖潜方向;定:
针对潜力空间确定指标任务;治:
通过抽汲参数优化、杆管泵优化、平衡优化、电机合理匹配、节能新技术的推广应用,进行综合治理;比:
以参数最优、效率最高、能耗最低、效益最佳为标准进行对比;超:
逐年提高系统效率标杆指标值。
机采系统效率由2006年的31.46%提高到2008年的32.18%、2009年的32.34%;同时,采取推广应用高压变频调速、机泵合理匹配、拆级改造、管网调整及运行参数自动优化调控等技术措施,注水系统效率2006年的53.56%提高到2007年的53.89%、2008年的54.09%、2009年的54.23%。
二是实施“1234”工程,提升作业措施效能。
坚持油藏、井筒、地面一体化管理,对照标杆指标,遵循“指标先进就是效益、管理精细就是节约”,实施“1234”工程。
即:
建立“1个”防偏磨体系,成立防偏磨攻关小组,从偏磨机理(管杆失稳、井眼轨迹、坐封原因、低产低液、产出液介质五种类型)研究入手,在双河油田江河区进行锚定管柱、杆柱连续扶正、简化管柱、优化举升工艺、统一杆径试验,成功后,在全厂范围内进行推广应用;开展“减少停、等作业专项治理”和“提高作业施工质量”“2项活动”,强化作业各环节的衔接,作业施工一次成功率由2006年的91.8%提高到2007年的92.9%、2008年的93.3%、2009年的95.5%;推行工程设计编审流程、监督管理、井下作业运行管理“3个规范”,强化油矿、采油队对维护作业的责任,提升作业管理水平,提高作业运行效率;实行“4个加强”:
加强井下作业材料的采购和检测管理,把好采购质量关;加强旧管杆的使用管理,建立梯级使用制度;加强井下作业过程管理,实行月度分析和公报制度;加强作业费用管理,控制作业费用增长。
维护作业频次由2006年的0.61下降到2007年的0.56,2008年的0.52;检泵周期由2006年的470天提高到2007年的528天、2008年的605天;躺井频次由2006年的1.254下降到2007年的1.018,2008年的0.683。
(删除)
三是实行“四单”管理模式,提高设备运行效率。
“四单”就是对单井、单机、单车、单台设备实行单机核算、单机管理。
联合站内,对设备实行单机挂牌制度,明确责任人,使设备运行参数、能耗指标、技术指标和站内排名,一目了然。
同时,按岗位性质的不同,将标杆指标、全厂排名以及各岗位分月运行情况挂牌上墙,使各项动态指标参数显形化。
按照“健康、亚健康、不健康”三类级别,定期对设备进行健康评价,制订保养、维修、工艺优化、匹配调整等方案,实现设备的经济、安全、高效运行。
四是实施测试“零缺陷”管理,提高测试质量。
测试系统以单井为对象,将各种静、动态基础数据、相关指标以及测试工艺、注意事项等编制成手册,便于操作人员随时查阅,实现测试工与油水井“零距离”接触;建立“测试信息综合管理平台”,将单井测试管理手册内容网络化,资源共享,使测试部门、地质部门、生产运行部门等相关技术管理人员随时掌握测试进度,发现测试问题,审核测试成果,提高了测试信息传递效率,使管理人员与测试过程“零距离”接触;以测试工艺问题井为对象,科学制订测试施工指导规范,并严格按照施工指导规范进行标准化施工,缩短测试工期,提高测试效率,最终实现测试质量“零缺陷”管理。
2008年与2007年对比,测试符合连续天数增加13天,测试设备连续运转天数增加47天。
(三)创新经济技术指标标杆化管理,不断提升成本控制能力。
围绕成本控制目标,细分成本控制节点,以各生产运行环节先进的经济技术指标—标杆指标为标尺,科学合理的看待挖潜空间,不断深化全面预算管理,推动降本增效工作深入开展,持续提升成本控制能力。
一是依靠“标杆”指标,深化落实全面预算管理。
基于“标杆”管理的视角,建立起编制预算-执行预算-分析差异-制定措施-调整预算的闭环式全面预算管理模式。
在业务预算的基础上确定财务预算,比如,利用提液电力单耗标杆指标,结合提液量和电价,预算原油提升过程的电费;以年度预算为目标,由财务、地质、采油、注水,计划等部门滚动编制月度预算,以月保季、以季保年,确保预算在计划内平稳运行;在预算总量控制下,量入为出、优化配置,适时调整;将预算管理指标层层分解到矿、队、班组,细化到单井、单机、单车、单台设备,层层落实责任,层层传递压力,使全面预算管理更具指导性。
二是围绕“标杆”指标,持续推进降本增效、节能降耗。
以先进的标杆指标作为降本增效的目标,成立厂、矿、队、班站“四级层面”上的降本增效项目组,实行项目化管理,使“标杆”管理与降本增效工作相互融合、相互促进。
引导岗位员工主动优化工作制度、优化工艺流程、优化生产参数,进而推动降本增效工作“三个转变”,即:
树立源头降本的思想,千方百计优化新井、措施、老井产量结构,持之以恒开展稳油控水工程,控制无效提液和无效注水,推动降本增效由末端治理向源头控制转变;倡导“大地质”、“大采油”、“大安全”、“大财务”理念,赋予各大专业以降本增效的内涵,促进各系统、各部门的协调与统一,实现系统和谐、局部完善、单点最优、能耗最低、效益最大,推动降本增效由局部改进向整体优化转变;在技术深度创新上做文章,在机制创新上下功夫,推动降本增效由现场改善向技术创新、机制创新转变。
比如,围绕降低提液电力单耗,厂部专门成立了“降低提液电力单耗”项目组。
通过实施稳油控水工程,实现源头降本,2009年上半年减少提液35万方,减少电量消耗361万千瓦时;实施电泵替代工程,减少高能耗设备,减少电量消耗150万千瓦时;优化工作制度,优化生产参数,优化电加热时间,实施油井间开,节电216万千瓦时。
2006年19个厂级降本增效项目,实现降本增效4607万元;2007年26个厂级降本增效项目,实现降本增效6100万元;2008年18个厂级项目,实现降本增效9731万元;2009年上半年,15个厂级项目累计完成降本增效2520万元。
三是审视“标杆”指标,深入开展经济活动分析。
近年来,我厂通过大力推广运用经济活动分析模板,坚持经济活动分析例会制,灵活采取专题分析、重点分析和全面分析相结合的分析方式,按照标杆指标的变化,确立不同层面的分析重点,从基层抓起,不断提升发现问题、分析问题、解决问题的能力。
通过“细分析、找差距、定措施、超标杆”,不断推动经济活动分析模板运用向纵深发展,进而推动标杆指标的进一步刷新。
比如:
在经济活动分析时,通过对单井耗材分析,物资管理部门发现个别基层材料管理存在漏洞,专门制定了完善的“一库三定”制度。
“一库”,就是以矿、大队为区域成立中心库房,逐步取消下属基层簸箩库;“三定”,就是定性领料、定量消耗、定额库存。
实施后,油井单井耗材由2006年的17901元/口,降低到2007年17626元/口、2008年的16578元口,成本控制能力和水平得到提高。
(四)创新生产管理指标标杆化管理,不断提高精细管理水平。
在生产管理上,我厂将进罐率、泵效、水质达标率、连续安全生产天数等生产管理指标标杆化,确立标杆指标值,以提高生产组织运行效率、夯实生产管理基础、确保安全生产,持续推进精细化管理水平整体提高。
一是依托管理标杆指标,提高生产组织运行效率。
在日常生产管理上,分月度、季度、年度进行立标、对标、超标,形成不同层面上比、学、赶、帮、超的氛围。
在生产应急管理上,我厂建立厂、矿、队、站四级应急预警管理机制,根据生产运行中出现的异常情况,逐级启动。
在新井投产上,做到“三个超前”、“两个到位”。
“三个超前”即:
超前介入、超前运行、超前施工;“两个到位”即:
地方工作协调到位、施工现场管理到位。
连续无躺井天数由2007年的65天上升到2008年的82天;采油时率由2007年的97.3%上升到2008年97.8%;进罐率由2007年的96.16%上升到2008年的96.32%;新井投产周期由15天缩短到7天。
二是依托“标杆”管理,提高油水井运营能力。
我厂针对油水井所处开发单元、开发阶段、井身结构、产出液性质的不同,采取“一井一策”精细化管理,使油水井管理更具针对性,措施更加具体有效。
同时,转变油水井分析诊断模式,分析方式由单人、单专业向地质、工程、班站组成的团队分析转变;分析内容由单一向“地下、井筒、地面”结合、“产量、成本、安全”三位一体系统集成的转变。
进而,建立油水井健康评价体系,将油水井的各类生产参数分为健康、亚健康、不健康三大类别,对健康状态的参数,提出保持对策;对亚健康状态的参数,提出优化对策;对不健康状态的参数,提出整改对策。
油水井运营能力持续提高,泵效由2006年的64.4%提高到2007年的66.9%、2008年的67.8%;提液用电单耗由2006年的12.08千瓦时/吨,降低到2007年的11.51千瓦时/吨、2008年的9.83千瓦时/吨;注水用电单耗由2006年的9.26千瓦时/方,降低到2007年的9.14千瓦时/方、2008年的8.97千瓦时/方。
三是依托“标杆”管理,提升安全管理水平。
我厂把基层作为安全管理的重点,将全年安全生产无事故作为最基本的要求,在采油、集输、测试三大系统将连续安全生产天数作为标杆指标,对基层实行HSE体系审核量化打分制,规范基层安全管理,筑牢安全管理根基。
几年来,我厂连续实现了安全生产无事故,连续被勘探局评为HSE管理先进单位。
四是立足“标杆”管理,建立问题管理应急机制。
为了及时解决日常管理中出现的问题,我厂建立起以计量站既为始点、又为终点的闭环式问题管理机制。
自下而上、逐级解决、逐级上报,留下痕迹,形成问题追踪处理路线,借助问题优化管理,促进问题的及时发现、分析和解决,全面提升“标杆”管理水平。
问题管理机制的建立,加快了问题解决的节奏,提高了问题解决的效率,干部职工主动工作、自主管理的积极性和主动性得以发挥。
如:
采油7队发现该队百米提液用电单耗指标排名靠后,分析认为主要与电泵井比例偏高有关,全队16.3%的电泵井、耗电量却占总耗电量的40.62%。
该队将这个问题按照程序向油矿、厂部汇报后,得到了高度重视,经过科学论证,对其中8口电泵井改为抽油机或螺杆泵进行生产,日节电10834千瓦时,节电幅度达74.1%,同时实施参数优化,该队百米提液用电单耗由2007年的0.85千瓦时/吨降低2008年的0.72千瓦时/吨。
目前,基于标杆指标的提升,我厂问题管理处理系统平台已经建立,实现了问题上报、处理和解决的程序化、网络化、可视化。
处理问题,站、队、矿、厂整体联动,相互督促,“标杆”管理的效能得到有效提升。
2009年以来,计量站向基层队上报“标杆”管理问题1287个,解决923个;基层队向矿(大队)上报364个,解决326个;矿(大队)向厂部上报38个,解决26个,有12个问题由于条件不成熟暂时进入厂“标杆”管理问题库留待解决,作为下步科研攻关、技术改造、设备更新的依据。
五是激活“标杆”潜能,全面推行计量站“121”精细管理模式。
我厂把井站和班组作为“标杆”管理的前沿主阵地,本着抽象事情具体化、复杂问题简单化、常规工作标准化的原则,将计量站油水井健康评价表与“标杆”管理的“计量站生产经营指标”和“计量站技术经济指标”两块展板、以及计量站综合管理手册融合使用,形成计量站“121”标准化、精细化管理模式,使产量任务、降本增效和安全环保落实到具体的油水井运行参数和“标杆”指标之中。
引导员工发现问题,促使员工解决问题。
逐渐形成和完善基层“能发现问题、善分析问题、会解决问题”的独立运行机制,实现了“从要我干到我要干,从要我算到我要算,从要我管到我要管”的飞跃,从根本上激活了“标杆”管理的潜能。
四、“标杆”管理取得的成效
推行“标杆”管理以来,有力促进了开发生产、安全环保、节能降耗、降本增效等各项工作的有机融合,各项经济技术指标得到了有效提升,达到了“全面对接、重点剖析、扬长治短、整体提升”的目的,精细化管理水平迈上了一个新的台阶。
(一)主要生产经济技术指标得到提高。
主要开发指标得到提升:
自然递减率由2006年的14.93%下降到2007年的13.6%、2008年的11.98%;阶段含水上升率由2006年的0.86下降到2007年的0.52、2008年的0.19;油井措施有效率保持在76%以上,分层注水合格率达到71.8%以上,油藏一二类开发管理单元达到83.0%。
产量超、成本降的目标得以实现:
2008年生产原油104.5万吨,超产1万吨;实际油气单位完全成本1606元/吨,较计划节余20元/吨,成本费用控制在分公司下达的指标以内。
基础管理水平得到提升,经济技术指标得到提高:
与2007年相比,2008年吨商品油耗电258元,同比下降26.85元;提液单耗9.83千瓦时/吨,同比下降1.68千瓦时/吨;注水单耗9.06千瓦时/吨,同比下降0.17千瓦时/吨;油井单井耗材16578元,同比下降1048元;油井维护作业639井次,同比下降172井次;作业频次1.11,同比下降0.15井次/口。
(二)业绩评价体系更加科学合理。
推行“标杆”管理后,我厂将“标杆”指标纳入业绩评价体系与评先标准体系,建立基层队领导班子和科级干部“360°”考核评价机制,修订完善厂百面红旗评比标准体系,制订了比较详细的评先标准和打分细则。
无论是考核、评价还是评先,都让事实说话,让指标说话,让数据说话,个人的工作绩效与单位“标杆”指标的先进程度紧密挂钩,减少了人为因素的影响,实现了定性考核向定量考核的转变。
(三)技术效益型基层队伍已基本成型。
“标杆”管理的推行,推进了生产、经济、技术一体化的进程,各基层队、各计量站都能正确量化指标、找准位置,解剖差距、明确目标方向,基础管理工作逐步实现了由模糊粗放向精细化、过程量化控制的转变,有效解决了基层管理的问题,初步实现了以产量为中心向以产量效益为中心的转变,全厂技术效益型基层队建设已基本成型。
(四)精细文化初步形成,持续发展更具活力。
“标杆”管理的推广应用,有力推动了企业精细化管理向纵深发展,激活了内部潜能,基层主动管理、自主提高的积极性显著提高,为各级班子、组织、队伍、团队,搭建了一个公开、公平、公正的竞争平台,为不同层次、不同层面的员工,提供了一个施展个人才华的舞台,企业可持续发展的能力得到增强。
随着“标杆”管理的持续推进,各单位、各部门之间的交流更加有效,协作、配合意识更加浓厚,学习、交流更加积极主动。
同时,“大地质”、“大采油”、“大作业”、“大安全”、“大财务”、“大降本”等理念得到广泛认同,产量是核心、安全是前提、成本是关键已成共识,有力促进了全厂各大专业之间的有机融合,精细文化已初步形成。
虽然“标杆”管理在我厂已经推行两年多的时间,初步形成了比较系统和规范的具有我厂特色的做法,也得到了股份公司的肯定和好评。
下步,我厂将进一步坚定信心,科学实践,以改革创新的精神不断丰富和完善“标杆”管理,不断拓展“标杆”管理的覆盖面,不断优化调整,使标杆设置更加科学,指标设置更加合理,努力把“标杆”管理打造成为推进我厂精细化管理的利器。