南水北调中线室内配套工程供水工程管线工程焊接钢管检验方案.docx
《南水北调中线室内配套工程供水工程管线工程焊接钢管检验方案.docx》由会员分享,可在线阅读,更多相关《南水北调中线室内配套工程供水工程管线工程焊接钢管检验方案.docx(39页珍藏版)》请在冰豆网上搜索。
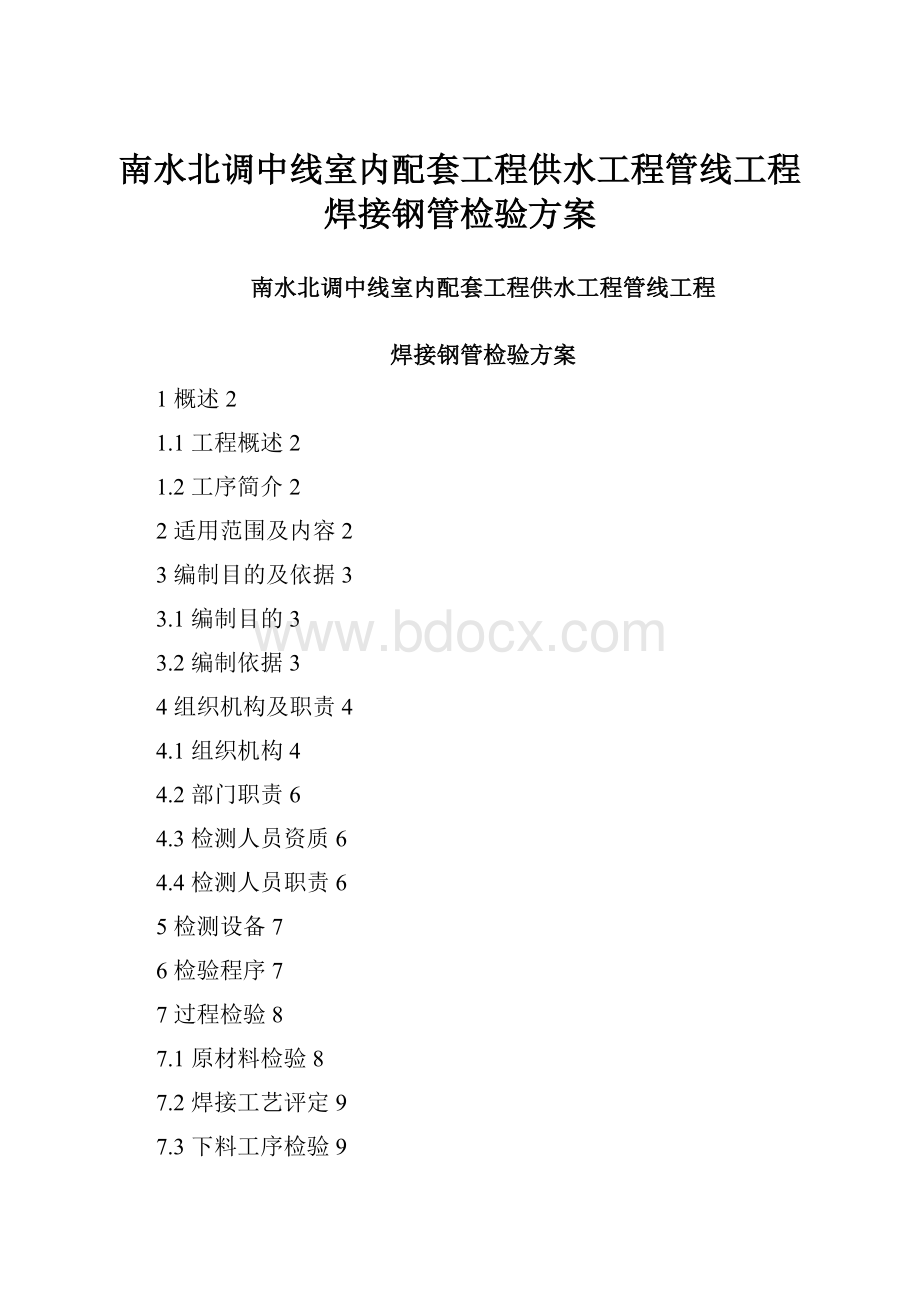
南水北调中线室内配套工程供水工程管线工程焊接钢管检验方案
南水北调中线室内配套工程供水工程管线工程
焊接钢管检验方案
1概述2
1.1工程概述2
1.2工序简介2
2适用范围及内容2
3编制目的及依据3
3.1编制目的3
3.2编制依据3
4组织机构及职责4
4.1组织机构4
4.2部门职责6
4.3检测人员资质6
4.4检测人员职责6
5检测设备7
6检验程序7
7过程检验8
7.1原材料检验8
7.2焊接工艺评定9
7.3下料工序检验9
7.4卷管工序检验10
7.5组对工序检验11
7.6焊接工序检验13
7.7无损检测14
7.8除锈工序检验15
7.9防腐工序检验16
8出厂检验及防护18
8.1出厂检验18
8.2成品防护及运输19
9四方验收19
附表1~14:
20
附录1:
测量仪器适用方法简介:
34
1概述
1.1工程概述
某市南水北调中线室内配套工程某供水工程管线工程(A0+000~A43+850)输水管线途径某市宝坻区及宁河县两个行政区,管线工程出自某供水泵站,主干管至芦台经济技术开发区东边界某分水口,干线长43.85km。
管外径皆为1820mm,按不同使用条件,管壁厚为22~36mm。
钢管材质均为Q235B镇定钢,管道工作压力0.5MPa。
1.2工序简介
本次工程所用钢管均为直缝焊接钢管,利用钢管进行卷制、接长并焊接;在无损检测合格后进行除锈及涂装,工艺流程图如下:
2适用范围及内容
本检测方案适用于某供水工程用钢管的加工及施工检测,本检测方案规定了钢管检测的适用依据、质保体系、检验程序、检验部门的职责、检验人员资质、过程检验的内容及方法、出厂验收的内容及四方验收等相关内容。
3编制目的及依据
3.1编制目的
为保证钢管的加工质量及施工质量,满足工程图纸,规范及相关标准要求,特编制本检测方案,用于钢管的加工及施工质量检验。
3.2编制依据
本方案编制主要依据下述设计要求、规范、规程及标准
(1)合同及设计文件
(2)GB50268-2008《给水排水管道工程施工及验收规范》
(3)SL432-2008《水利工程压力钢管制造安装及验收规范》
(4)NB/T47013.1-13-2015《承压设备无损检测》
(5)GB/T9445-2015《无损检测人员资格鉴定与认证》
(6)SY/T0414-2007《钢制管道聚乙烯胶粘带防腐层技术标准》
(7)GB50726-2011《工业设备及管道防腐工程施工规范》
(8)GB50727-2011《工业设备及管道防腐工程施工质量验收规范》
(9)GB50212-2014《建筑防腐工程施工规范》
(10)GB/T18370-2014《玻璃纤维无捻纱布》
(11)GB/T13657-2011《双酚A基环氧树脂》
(12)GB/T1447-2005《纤维增强塑料拉伸性能试验方法》
(13)GB/T1449-2005《纤维增强塑料拉伸性能试验方法》
(14)SL205-2007《水工金属结构防腐蚀规范》
(15)SL582-2012《水工金属结构制造安装质量检验通则》
(16)SL734-2016《水利工程质量检测技术规程》
(17)GB/T709-2006《热轧钢板和钢带的尺寸、外形、重量及允许偏差》
(18)GB/T700—2006《碳素结构钢》
(19)GB/T14977-2008《热轧钢板表面质量的一般要求》
(20)GB/T8923.1-2011《涂覆涂料前钢材表面处理表面清洁度的目视评定第1部》
(21)SL105-2007《水工金属结构防腐蚀规范》
4组织机构及职责
4.1组织机构
为保证钢管及管件的加工进度与质量,特组织了以下组织机构。
总工程师
4.2部门职责
厂长责成生产副厂长主管制管厂全面质量工作,各科室、各车间、各班组配合生产副厂长的质量管理工作,具体分工如下:
a:
主管副厂长岗位职责
生产主管厂长主管制管厂质量工作,全面负责产品生产过程的质量及产品出厂质量,制定质量检验的程序,规定各检测岗位人员的职责,处理生产过程中出现的质量问题,批准质量提升的管理办法及方法。
b:
质量管理机构职责
设立生产管理部为制管厂质量管理机构。
《生产管理部岗位职责》,生产管理部部长负责生产管理部管理工作,《生产生产管理部部长岗位职责》。
4.3检测人员资质
检测人员应符合SL734-2016《水利工程质量检测技术规程》的相关要求,并经过专业培训,熟练掌握检测的方法及标准,取得相应资格证书。
4.4检测人员职责
生产管理部设质检员、焊接质检员、无损检测员负责产品检验工作,各岗位质检人员按照岗位要求、产品质量要求及检验批次要求,完成质量检验工程,并及时将质量检验结果上报主管领导及生产部门,并在相应的质检记录上签字存档。
5检测设备
检测设备应符合工程质量验收规范所规定的精度要求,并委托第三方对检测设备进行检验,并取得相应的检定证书。
本次工程用到的主要检测仪器如下:
生产检验工序
检验器具
下料
钢卷尺,钢板尺,焊接检验尺,游标卡尺
卷管
钢卷尺、弧度样板,钢板尺
组对
钢卷尺,钢板尺,焊接检验尺,游标卡尺
焊接
焊接检验尺,放大镜,钢直尺
无损检测
超声波检测仪,射线检测仪
除锈
粗糙度对比试块,除锈等级对比图片
防腐
涂层测厚仪,针孔探测仪
出厂检验
经纬仪,钢卷尺,涂层测厚仪,针孔探测仪
6检验程序
钢管及管件制作检验程序为三检制检验程序,分别为自检,互检和专检。
各检验工序的检验人员及职责如下:
自检:
由生产工段检验人员检验,并填写相关记录,检验合格后方可进入下一工序继续生产加工。
互检:
半成品构件在进入下道工序时,由该工序的检验人员对上道工序流转下来的产品进行检验,确认合格方可继续生产加工,检验合格后填写相关检验记录。
专检:
由质检部门委托的专职质检人员进行成品构件的最终检验,确定产品是否符合出厂要求,并填写相关记录,专职质检人员还需按批次对过程工序进行检验,填写相关抽检记录。
钢管检验记录表格样式见过程检验条款中规定的相关表格。
7过程检验
7.1原材料检验
7.1.1检验标准:
《碳素结构钢》GB/T700
7.1.2检测项目:
屈服强度,抗拉强度,断后伸长率,弯曲试验,冲击试验
7.1.3取样基数:
同炉号同批次,每60吨一组,不足60吨时按60吨处理
7.1.4取样方式:
可连续取样
7.1.5取样数量:
每10组中,7组自检,3组见证,再抽取1组抽检
7.1.6检验依据:
GB/T700—2006《碳素结构钢》
7.1.7检验记录表格见附表1
7.2焊接工艺评定
钢管加工前应依据NB/T47014《承压设备焊接工艺评定》进行焊接工艺评定,合格后方可钢管加工及施工。
详见《焊接工艺评定报告》。
7.3下料工序检验
7.3.1下料尺寸检验
(1)检验标准:
《水利工程压力钢管制造安装及验收规范》SL432-2008第4.1.1款
序号
项目
允许偏差(mm)
1
宽度和长度
±1
2
对角线相对差
2
3
对应边相对差
1
4
失高(曲线部分)
0.5
(2)检测项目:
下料长度,下料宽度,对角线相对差,失高(曲线部分)
(3)检测数量:
每张钢板
(4)检测方式:
使用钢卷尺量取相应尺寸
(5)检验依据:
《水工金属结构制造安装质量检验通则》SL582-2012
7.3.2下料端口检验
(1)检验标准:
《水利工程压力钢管制造安装及验收规范》SL432-2008第4.1.10及第4.1.11款,《承压设备无损检测》NB/T47013.3-2015
(2)检测项目:
端口质量
(3)检验数量:
逐张检验
(4)检验方式:
超声波检测
(5)检验依据:
《水工金属结构制造安装质量检验通则》SL582-2012,《承压设备无损检测》NB/T47013.3-2015
7.3.3检验记录表格见附表2
7.4卷管工序检验
7.4.1检验标准:
《水利工程压力钢管制造安装及验收规范》SL432-2008第4.1.12款
序号
检验项目
技术要求
检验方法
1
瓦片的弧度
不大于1.5mm
使用弦长900mm的样板检查弧度,使用塞尺测量样板与钢管之间的间隙
2
实测周长与设计周长差
不大于5.4mm
在每个管口距边沿50mm处用钢卷尺测量。
相邻关节周长差
极限偏差10mm
3
纵缝对口错边量
不大于2mm
用弧度样板紧靠管壁,用塞尺或钢直尺测坡口量测的间隙差
4
环缝对口错边量
30mm及以下板厚的钢管环缝错边量应不大于3mm;30mm以上板厚的钢管环缝错边量应不大于板厚的10%。
用焊检尺测量
5
焊缝处的弧度
极限间隙4mm
采用弦长500mm的样板检测
6
圆度检测
不大于5.4mm
测量分为两次,每次选取两个相互垂直的直径进行测量,其差量应不大于5.4mm,两次之间的测量位置应错开45°,即四个测量数据成米字型分布
7.4.2检测项目:
瓦片的弧度,实测周长与设计周长差,相邻关节周长差,纵缝对口错边量,环缝对口错边量,焊缝处的弧度,圆度
7.4.3检测数量:
逐根钢管检验
7.4.4检测方式:
使用钢卷尺、样板、钢直尺、焊接检验尺量取相应尺寸
7.4.5检验依据:
《水工金属结构制造安装质量检验通则》SL582-2012
7.4.6检验记录表格见附表3
7.5组对工序检验
7.5.1检验标准:
《水利工程压力钢管制造安装及验收规范》SL432-2008第4.1.12款
序号
检验项目
技术要求
检验方法
1
管长
不大于±10mm
钢卷尺
2
主管、支管的管口圆度
不大于5.4mm
每个管口用钢卷尺测2对相互垂直的直径,两次测量错开45°,取差值较大的两相互垂直直径之差为被测管口的圆度
3
主管、支管的管口实测周长与设计周长差
不大于±5.4mm
在每个管口距边沿50mm处用钢卷尺测量,将实测值与设计值进行比较
4
支管中心距离S1
不大于±S1(mm)÷1000
钢卷尺
5
主管、支管的中心高程相对差
不大于4mm
用水准仪和标尺测量
6
主管、支管的管口垂直度
不大于2mm
由管口顶部中心挂垂线,用钢直尺测管口顶部中心和底部中心至垂线的距离差
7
主管、支管管口平面度
不大于2mm
用电子经纬仪测量
8
纵缝对口错边量
不大于2mm
用弧度样板紧靠管壁,用塞尺或钢直尺测坡口两侧的间隙差
9
环缝对口错边量
30mm及以下板厚的钢管环缝错边量应不大于3mm;30mm以上板厚的钢管环缝错边量应不大于板厚的10%。
用焊接检验尺测量
7.5.2检测项目:
管长,主管、支管的管口圆度,主管、支管的管口实测周长与设计周长差,支管中心距离S1,主管、支管的中心高程相对差,主管、支管的管口垂直度,主管、支管管口平面度,纵缝对口错边量,环缝对口错边量
7.5.3检测数量:
逐根钢管检验
7.5.4检测方式:
使用钢卷尺、样板、钢直尺、焊接检验尺量取相应尺寸
7.5.5检验依据:
《水工金属结构制造安装质量检验通则》SL582-20127.5焊接工序。
7.5.6检验记录表格见附表4
7.6焊接工序检验
7.6.1焊接外观检验
(1)检验标准:
《水利工程压力钢管制造安装及验收规范》SL432-2008第4.1.12款
序号
项目
检测标准
检测手段
1
裂纹
不允许
目测
2
表面夹渣
不允许
目测
3
咬边
深度不大于0.5
焊接检验尺
4
未焊满
不允许
目测
5
表面气孔
不允许
目测
6
焊瘤
不允许
目测
7
飞溅
不允许
目测
8
焊缝余高
Δh
手工焊
δ≤25,Δh=0~2.5
25<δ≤50,Δh=0~3
焊接检验尺
自动焊
0~4
焊接检验尺
9
对接接头
焊缝宽度
手工焊
盖过每边坡口宽度1~2.5,且平缓过渡
焊接检验尺
自动焊
盖过每边坡口宽度2~7,且平缓过渡
焊接检验尺
7.6.2检测项目:
焊缝外观
7.6.3检测数量:
逐根钢管,逐条焊缝检验
7.6.4检测方式:
使用焊接检验尺量取相应尺寸
7.6.5检验依据:
《水工金属结构制造安装质量检验通则》SL582-2012
7.6.6检验记录表格见附表5~8
7.7无损检测
7.7.1焊接煤油渗透检验
(1)检验标准:
《钢制焊接常压容器》JB/T4735-1997中15.2.5.7的规定
(2)检测项目:
焊缝质量
(3)检测数量:
逐根钢管,逐条焊缝检验
(4)检测方式:
将焊接接头能够检查的一面清理干净,涂以白粉浆,晾干后,在焊接接头的另一面涂以煤油,使表面得到足够的浸润,经半小时后以白粉浆上没有油渍为合格。
(5)检验依据:
《钢制焊接常压容器》JB/T4735-1997
7.7.2焊缝内部检验
(1)检验标准:
《水利工程压力钢管制造安装及验收规范》SL432-2008
(2)检测项目:
焊缝质量
(3)检测数量:
钢种
板厚
一类焊缝的检测
方法和比例(%)
二类焊缝的检测
方法和比例(%)
碳素钢
-
UT
RT
UT
RT
100
2
50
1
(4)检测方式:
超声波检测与射线检测
(5)检验依据:
《承压设备无损检测》NB/T47013-2015
(6)根据设计要求,射线检测Ⅱ级合格,其中顶管部分射线检测Ⅰ级片比例80%,直埋管部分射线检测Ⅰ级片比例50%比例。
7.8除锈工序检验
7.8.1检验标准:
《水工金属结构防腐蚀规范》SL105-2007,喷砂除锈等级为Sa2.5级
7.8.2检测项目:
除锈等级是否达到Sa2.5
7.8.3检测数量:
逐根钢管检验
7.8.4检测方式:
参照粗糙度相对样块目测检查除锈级别
7.8.5检验依据:
《水工金属结构防腐蚀规范》SL105-2007
7.8.6检验记录表格见附表9
7.9防腐工序检验
7.9.1聚丙烯胶带检验
(1)检验标准:
《水工金属结构防腐蚀规范》SL105-2007,电火花检测电压不小于7kv
(2)检测项目:
电火花检测
(3)检测数量:
逐根钢管检验
(4)检测方式:
使用针孔检测仪对钢管表面外防腐进行涂刷式检测。
探头移动速度不大于0.3m/s
(5)检验依据:
《水工金属结构防腐蚀规范》SL105-2007
7.9.2特加强级环氧树脂玻璃钢检验
(1)检验标准:
《水工金属结构防腐蚀规范》SL105-2007,电火花检测电压不小于3.5kv,防腐层厚度不小于3.5mm
(2)检测项目:
电火花检测,涂层测厚仪检测
(3)检测数量:
电火花逐根钢管检验,厚度检测每节钢管四个点。
(4)检测方式:
电火花检测:
使用针孔检测仪对钢管表面外防腐进行涂刷式检测。
探头移动速度不大于0.3m/s。
涂层厚度检测:
在1dm²的基准面上做3次测量,其中每次测量的位置应相距25~75mm,应取这3次测量值的算术平均值为该基准面的局部厚度。
每10㎡至少应测量3个局部厚度。
且85%以上的局部厚度应达到设计厚度,没有达到设计厚度的部位,其最小局部厚度应不低于设计厚度的85%。
(5)检验依据:
《水工金属结构防腐蚀规范》SL105-2007
7.9.3饮水容器无毒环氧涂料检验
(1)检验标准:
《水工金属结构防腐蚀规范》SL105-2007,电火花检测电压不小于1.5kv,防腐层厚度不小于0.3mm
(2)检测项目:
电火花检测,涂层测厚仪检测
(3)检测数量:
电火花逐根钢管检验,厚度检测每节钢管四个点。
(4)检测方式:
电火花检测:
使用针孔检测仪对钢管表面外防腐进行涂刷式检测。
探头移动速度不大于0.3m/s
涂层厚度检测:
在1dm²的基准面上做3次测量,其中每次测量的位置应相距25~75mm,应取这3次测量值的算术平均值为该基准面的局部厚度。
每10㎡至少应测量3个局部厚度。
且85%以上的局部厚度应达到设计厚度,没有达到设计厚度的部位,其最小局部厚度应不低于设计厚度的85%。
(5)检验依据:
《水工金属结构防腐蚀规范》SL105-2007
7.9.4检验记录表格见附表9
8出厂检验及防护
8.1出厂检验
钢管出厂需经专职检验人员按照相关技术要求及标准进行100%检测,合格后填写《检验报告》,并对钢管喷涂标识及编号,整理第三方无损检测报告,母材复试报告及相关材料合格证,汇总后报送监理。
《检验报告》格式见附表10
8.2成品防护及运输
成品管堆放需在管底部端口处放置垫块,单层码放。
运输过程车辆地板上放置软垫,防止破坏外防腐,禁止使用钢丝绳对运输的管道进行固定及吊装。
9四方验收
钢管到达施工场地,需经过制造方、施工方、监理方及业主方同时到场检验,检验合格后方可施工。
附表1:
附表2:
附表3:
附表4:
附表5:
附表6:
附表7:
附表8:
附表9:
附表10:
附表11:
附表12
附表13:
附表14:
附录1:
测量仪器适用方法简介:
1.钢卷尺的使用
1.1使用方法
测量时钢卷尺零刻度对准测量起始点,施以适当拉力,直接读取测量终止点所对应的尺上刻度。
需测量直径但又无法直接测量时,可通过测量圆周长来求得直径。
1.2.注意事项
使用时不要前倾后仰、左右歪斜。
拉力不宜过大。
尺的长度是以在20℃、50N拉力标准状况下的测得值为依据。
1.3温度误差补正计算方法
不同温度环境下使用钢卷尺时,应通过线膨胀公式将测量值换算成20℃的值。
温度误差=实际测定值×尺带膨胀系数×(使用温度-20℃)。
尺带膨胀系数为0.0000115
2.焊接检验尺的使用
3.游标卡尺的使用
游标卡尺作为一种被广泛使用的高精度测量工具,它是由主尺和附在主尺上能滑动的游标两部分构成。
如果按游标的刻度值来分,游标卡尺又分0.1、0.05、0.02mm三种。
3.1游标卡尺的读数方法
以刻度值0.02mm的精密游标卡尺为例,读数方法,可分三步;
1)根据副尺零线以左的主尺上的最近刻度读出整毫米数;
2)根据副尺零线以右与主尺上的刻度对准的刻线数乘上0.02读出小数;
3)将上面整数和小数两部分加起来,即为总尺寸。
如上图所示,副尺0线所对主尺前面的刻度64mm,副尺0线后的第9条线与主尺的一条刻线对齐。
副尺0线后的第9条线表示:
0.02x9=0.18mm
所以被测工件的尺寸为:
64+0.18=64.18mm
3.2游标卡尺的使用方法
将量爪并拢,查看游标和主尺身的零刻度线是否对齐。
如果对齐就可以进行测量:
如没有对齐则要记取零误差:
游标的零刻度线在尺身零刻度线右侧的叫正零误差,在尺身零刻度线左侧的叫负零误差(这种规定方法与数轴的规定一致,原点以右为正,原点以左为负)。
测量时,右手拿住尺身,大拇指移动游标,左手拿待测外径(或内径)的物体,使待测物位于外测量爪之间,当与量爪紧紧相贴时,即可读数,如下图所示:
3.3使用注意事项
游标卡尺是比较精密的量具,使用时应注意如下事项:
1)使用前,应先擦干净两卡脚测量面,合拢两卡脚,检查副尺0线与主尺0线是否对齐,若未对齐,应根据原始误差修正测量读数。
2)测量工件时,卡脚测量面必须与工件的表面平行或垂直,不得歪斜。
且用力不能过大,以免卡脚变形或磨损,影响测量精度。
3)读数时,视线要垂直于尺面,否则测量值不准确。
4)测量内径尺寸时,应轻轻摆动,以便找出最大值。
5)游标卡尺用完后,仔细擦净,抹上防护油,平放在合内。
以防生锈或弯曲。
4.钢直尺的使用
4.1由于钢直尺的刻线间距为1mm,而刻线本身宽度就有0.1~0.2mm,所以用钢直尺测量物件的长度尺寸,测量结果是不太准确的,测量时读数误差比较大,只能读出毫米数,也就是说使用钢直尺的最小读数值为1mm,小于1mm数值,只能估读。
4.2钢直尺的读数分为两部分,一部分为测量值,另一部分为估计值。
通常钢直尺的前10cm精确值为0.5mm,10cm之后的为1mm,所以直尺的测量读数估计值是分度值的下一位小数。
4.3注意使用钢直尺的测量长度时尽量不使用“0”刻度作为零点,这样很容易对准非断面位置,从而造成读数的人