通用的可靠性设计分析方法.docx
《通用的可靠性设计分析方法.docx》由会员分享,可在线阅读,更多相关《通用的可靠性设计分析方法.docx(12页珍藏版)》请在冰豆网上搜索。
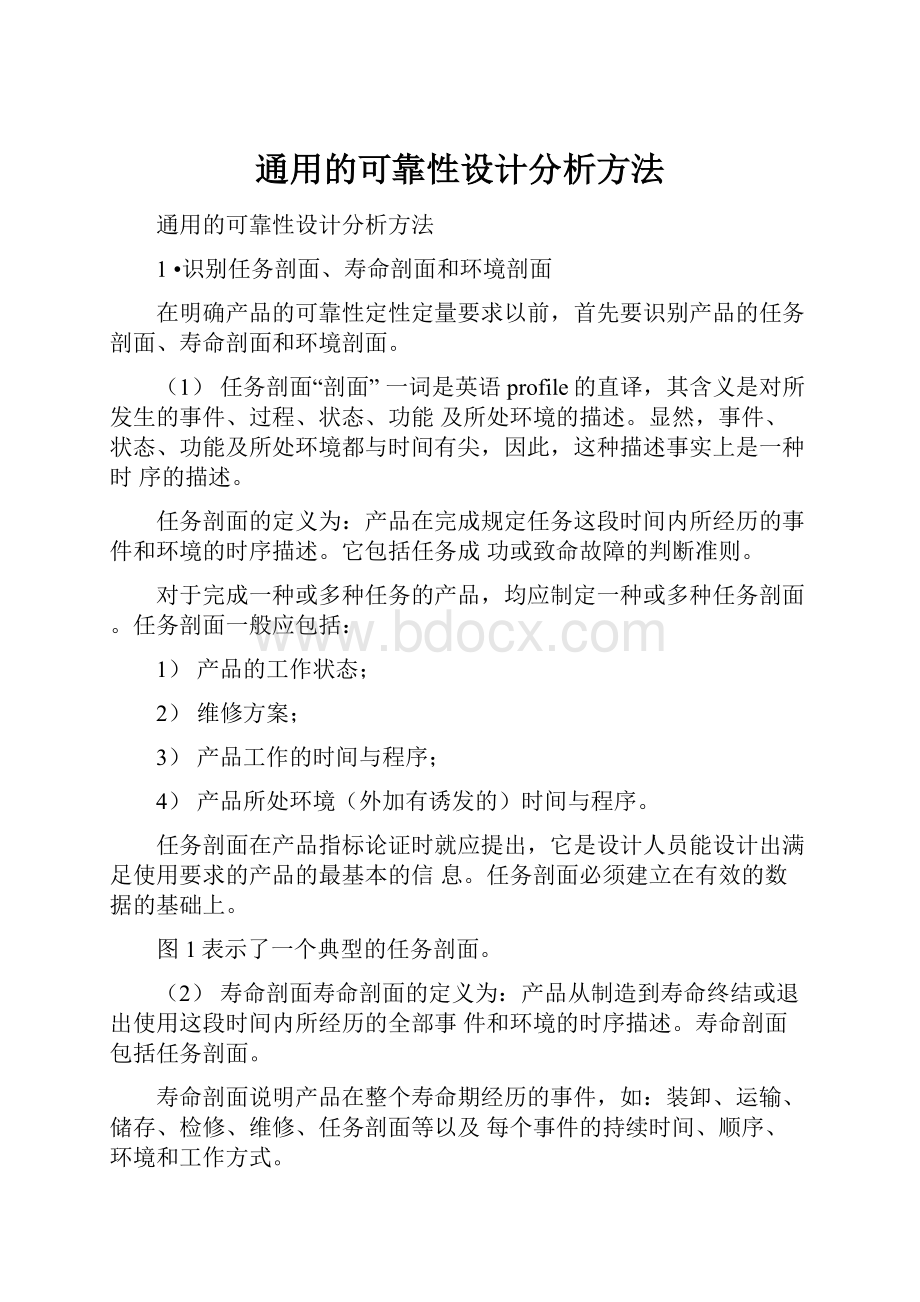
通用的可靠性设计分析方法
通用的可靠性设计分析方法
1•识别任务剖面、寿命剖面和环境剖面
在明确产品的可靠性定性定量要求以前,首先要识别产品的任务剖面、寿命剖面和环境剖面。
(1)任务剖面“剖面”一词是英语profile的直译,其含义是对所发生的事件、过程、状态、功能及所处环境的描述。
显然,事件、状态、功能及所处环境都与时间有尖,因此,这种描述事实上是一种时序的描述。
任务剖面的定义为:
产品在完成规定任务这段时间内所经历的事件和环境的时序描述。
它包括任务成功或致命故障的判断准则。
对于完成一种或多种任务的产品,均应制定一种或多种任务剖面。
任务剖面一般应包括:
1)产品的工作状态;
2)维修方案;
3)产品工作的时间与程序;
4)产品所处环境(外加有诱发的)时间与程序。
任务剖面在产品指标论证时就应提出,它是设计人员能设计出满足使用要求的产品的最基本的信息。
任务剖面必须建立在有效的数据的基础上。
图1表示了一个典型的任务剖面。
(2)寿命剖面寿命剖面的定义为:
产品从制造到寿命终结或退出使用这段时间内所经历的全部事件和环境的时序描述。
寿命剖面包括任务剖面。
寿命剖面说明产品在整个寿命期经历的事件,如:
装卸、运输、储存、检修、维修、任务剖面等以及每个事件的持续时间、顺序、环境和工作方式。
寿命剖面同样是建立产品技术要求不可缺少的信息。
图2表示了寿命剖面所经历的事件。
图1任夯剖面示例
图£寿命制面所经历的事件
(3)环境剖面环境剖面是任务剖面的一个组成部分。
它是对产品的使用或生存有影响
的环境特性,如温度、湿度、压力、盐雾、辐射、砂尘以及振动冲击、噪声、电磁干扰等及其强度的时序说明。
产品的工作时间与程序所对应的环境时间与程序不尽相同。
环境剖面也是寿命剖面和任
务剖面的一个组成部分。
2•明确可靠性定性定量要求
明确产品的可靠性要求是新产品开发过程中首先要做的一件事。
产品的可靠性要求是进
行可靠性设计分析的最重要的依据。
可靠性要求可以分为两大类:
第一类是定性要求,即用一种非量化的形式来设计、分析
以评估和保证产品的可靠性;第二类是定量要求,即规定产品的可靠性指标和相应的验证方
法°
可靠性定性要求通常以要求开展的一系列定性设计分析工作项目表达。
常用的可靠性定
性设计工作项目见表1。
表・常用的可靠性定性设计分析项目
目的
序号定性设计分析项目名称
1謝症和贾佃可靠性设计准则擀同类产品的成熟经验和失败魏训以设计扌首令的形式要求设计人咼贯彻落实
2进行故障模式戟响(危害度)分检杳系统可能发生的故曄,确定设计污案的可行性,发现设计中潜在的间趣析(施
(C)A)提出改曲S施
分析造成产品某种蔽障状态的各种原因和条件,确定各种原因或具组合,发现设计中的漣弱环节,提出改逬措施
在MCA分析的基础上,确宦少数的矢腱件和重要件,提出更详尽具体的质壘控常
在产品研制的各个阶段•对可靠性工作计划和实施情况进行有效地监督和控制
可靠性定量要求是指:
选择和确定产品的故障定义和判据、可靠性指标以及验证时机和验证方法,以便在研制过程中用量化的方法来评价和控制产品的可靠性水平。
确定可靠性指标主要考虑下列因素:
1)国内外同类产品的可靠性水平;
2)用户的要求或合同的规定;
3)本企业同类产品的可靠性水平;
4)进度和经费的考虑与权衡。
应该指出,上述各项有尖的基础数据并非很容易得到。
它有一个逐步积累的过程。
当前,多数民用机械产品的用户一般还不会在合同中提出明确的可靠性定量要求。
但潜在的要求是的的确确客观存在的,制造方有责任进行必要的市场调研,征求用户的意见,使其所研制开发的产品在可靠性方面有竞争力。
可靠性指标不是越高越好,它要和技术可能性、研制开发周期、成本效益等几方面进行综合分析和权衡。
•般情况下'有定量可靠性要求的新产品在研制过程中有一个可靠性增长的过程。
此外'还需要考虑数字指标的随机性所带来的置信水平问题。
3•制定和贯彻可靠性设计准则
制定和贯彻靠性设计准则是一项重要的可靠性定性设计方法,它可以在进行产品设计的同时把可靠性设计到产品中去。
这种方法的实用性强,效费比高,应予优先采用。
可靠性设计准则一般都是针对某个型号或产品的,但也可以把各个型号或产品的可靠性设计准则的共性内容,综合成某类产品的可靠性设计准则,例如:
柴油机设计准则、载货汽车设计准则、拖拉机设计准则等。
当然,这些共性的可靠性设计准则经剪裁、补充后又可成为专用产品的可靠性设计准则。
产品主管设计师应组织有尖专家编制可靠性设计准则。
该准则将同类产品的成熟经验和失败教训以设计指令的形式要求设计人员贯彻落实,使每条设计准则均有相应的设计保证措施。
设计准则一般在方案设计开始前制定,经反复征求意见,完善、修改后再正式颁发。
在施工设计阶段结束时,应提出设计准则贯彻实施报告。
和可靠性设计准则相似的一种可靠性设计文件是可靠性设计检查表”。
它用向设计人员提问题
的方式促使设计人员考虑产品可靠性要求和消除可能存在的设计隐患。
4•系统可靠性模型的建立和可靠性分配
(1)系统可靠性模型的建立建立可靠性模型是为了定量分配、估算和评估产品的可靠性。
为了建模,要在产品工作原理图的基础上画出产品的可靠性框图。
产品的工作原理图是表示产品各单元之间的功能联系,而可靠性框图则是以各种串•并•旁联的方框组合表示系统各组成单元之
间的完成规定功能中的尖系。
这两者是不能混淆的。
表2是最常见的可靠性框图模型及其数学表达式。
其中串联模型是指组成产品的所有单元中的任一单元发生故障都会导致整个产品故障。
并联模型亦称作工作储备模型。
r/n模型是指组成产品的
所有单元都工作,但至少r个正常,产品才能正常工作。
r/n模型亦称表决模型。
在建立产品的可靠性框图模型时,应从系统级向分系统、设备、部件极细化,但不一定细化到零部件,这要视具体情况而定。
表2常见的可靠性框图及其数学表达式
序
号
可靠性框图
数学表达式
•4
串联模型
n
R.g二匸(二i
I
12加K
MTBFg—1/A,
假设各单元失效间隔时间服从指数分布
JV
R3=1一口(1一R")
21
注:
Rs—系统可靠度;Ri—单元可靠度;入s—系统失效率;入i単元失效率;MTBFs—系统平均失效平均间隔时间。
(2)可靠性分配工程中常用的可靠性分配方法有比例分配法和加权分配法。
1)比例分配法。
如已知系统各单元的相对失效率比心
则可按下式进行可靠性分配:
入i=入ski
式中入一一第i个单元的失效率;
入s统的失效率。
此方法以相似产品的失效率统计数据为基础。
2)加权分配法。
此方法是对各子系统与完成规定任务的有尖因素进行评分,得出各子系统的加权系数,据此进行可靠性分配。
评分时考虑的因素:
①复杂程度;②技术水平和成熟程度;③工作时间;④重要程度。
5•故障模式、影响(危害度)分析(FailtModes,Effects(andCriticality)Analysis(C)FME
A)
FME(C)A分析是另一个重要的可靠性定性设计分析方法。
此方法研究产品的每个组成部分可能存在的故障模式,并确定各个故障模式对产品其他组成部分和产品要求功能的影响。
它亦能同时考虑故障发生的概率和危害度的等级。
系统的可靠性指标是多个故障模式综合影响的结果,而要提高系统的可靠性就必须具体分析各组成单元的故障模式对系统的影响和危害程度。
FME(C)A分析可用于设计的各个阶段,即方案设计、技术设计和施工设计,亦可用于工艺设计和工艺装备设计。
FME(C)A分析所用的表格见表3。
此表可随设计阶段、产品对象、分析要求的不同而作必要的调整,分析者可酌情适当增减栏目。
严酷度的等级举例见表4。
表3FVE(0A表①
(子)系统名称
设SiSfliJ
序7代号
名称
功能
故障
模式
12
S
4
E
故障
最绥影局部影响
严酷度故陣检测方
厦因
n,响
等级
法
6
7S
5
负责
故障发主概率
危害度崖议改进负责部数
值
措施「」
11
12
1314
坝写说图号或分
②析识别号
分析的萼部件或子系统容称
分析对故陣克彖功能现形式
设想的对自身和故障原上一级的因彫响
对系统
的影响
见表4
检测方法或按统计数据分:
很提出的改按方法难度低、低*中等、高分参若文給补偿极四类或更多类措施
负责改
进部n
1FMEA分析时不作11、丄两项・
2各栏埴表说明详见養等文献〔冬51.
表4严醋度的等级举例
严酷度等级危害程度
17可自誠为主要系统丧失功能,从而导致系统或其环境的重九损坏的潜在原因或造巔人身伤亡潜在原因的任何事件
IIJ可盲尿为主寰系统丧失功能,从而导致该系统或其环境的重大损失的潜在原因,而又几乎不応及人身安全的任何事件
II造戚系統功能、性能退化而对系統或人员的主齡或険库没荷可感觉的损伤的任何事件
I可能咸为乗统功紙性SKIft的原因而对系统或其环境几乎无损坏、对人身安星无掘害的任何事件
FME(C)A分析一定要由有经验的设计人员去做,否则会流于形式。
企业的可靠性工程师可给予指导和帮助。
FME(C)A分析的效果体现在:
对影响产品可靠性的设计、工艺等因素有所改进;否则就是无效的分析。
6•故障树分析(FaultTreeAnalysisFTA)
FTA分析是以故障树的形式进行分析的方法。
它用于确定哪些组成部分的故障模式或外界事件或它们的组合可能导致产品的一种已给定的故障模式。
它以系统的故障为顶事件,自上而下地逐层查找故障原因,直至找出全部直接原因(基本事件,即硬件和软件故障、人为差错和环境因素等),并根据它们之间的逻辑尖系用图表示。
这种图的外形像一棵以系统故障为根的树,故称故
障树。
FTA分析既可用于设计阶段作潜在故障发生原因的深入分析,亦可用事中阶段的故障诊断和事后的失效分析。
既可用于定性分析,也可用于定量分析。
在安全分析和风险评价中也是常用的方法。
7•确定可靠性尖键件和重要件
在FMEA分析的基础上,确定少数的尖键件和重要件,提出更详细具体的质量控制要求是经济地利用有限资源的管理途径。
确定可靠性尖键件和重要件的原则如下:
1)故障会导致人员伤亡、财产严重损失的产品;
2)从寿命周期费用来说是昂贵的产品;
3)只要它发生故障就会引起系统故障的产品;
4)严重影响系统可用性,增加了维修费用和备件数量的产品;
5)难以采购的或用新工艺制造的产品;
6)需进行特殊处理、储存或防护的产品。
要对尖键件和重要件的可靠性改进措施和有效性予以特别的重视。
8•设计评审
要在产品研制的各个阶段,设置设计评审点,对可靠性工作计划和实施情况进行有效的监督管理。
设计评审是对可靠性设计分析实施有效管理的主要途径。
对设计评审的主要要求是:
1)在评审前要充分做好准备工作,评审主管单位应确定评审组成员,会同设计单位拟定评审大纲和评审检查清单,并确定应提交评审的所有文件资料;
2)评审组成员应有足够的时间审阅有尖的文件和资料,并切实按评审检查清单逐项予以评审,实事
求是地给予评价;
3)对评审中提出的问题,产品设计单位应制定相应措施,限期改进。
可靠性设计评审可和一般的设计评审结合进行。
注意在不同设计阶段的评审点应对可靠性设
计分析文件提出不同的要求。
讲求实效,切忌走过场。
9.建立故障报告、分析和纠正措施系统(FailureReporting,AnalysisandCorrectiveAction
SystemsFRACAS)
建立FRACAS系统是实现可靠性增长和获取可靠性信息的重要手段。
FRACAS系统的闭环
流程如图3所示。
建立FRACAS系统的要点如下:
1)建立FRACAS系统的组织机构‘质量部门和技术部门均应有专责人员负责此项工作。
2)应制定产品的FRACAS系统工作规定,并按规定执行。
构成故障报告(信息)的闭环运行,尖键问题能及时得到纠正。
3)应有齐全、完整的文档记录。
4)纠正措施的有效性应经试验确认。
图3FRACAS闭环流程图