廖世超基于Dynaform软件的U形件回弹模拟及方案优化.docx
《廖世超基于Dynaform软件的U形件回弹模拟及方案优化.docx》由会员分享,可在线阅读,更多相关《廖世超基于Dynaform软件的U形件回弹模拟及方案优化.docx(29页珍藏版)》请在冰豆网上搜索。
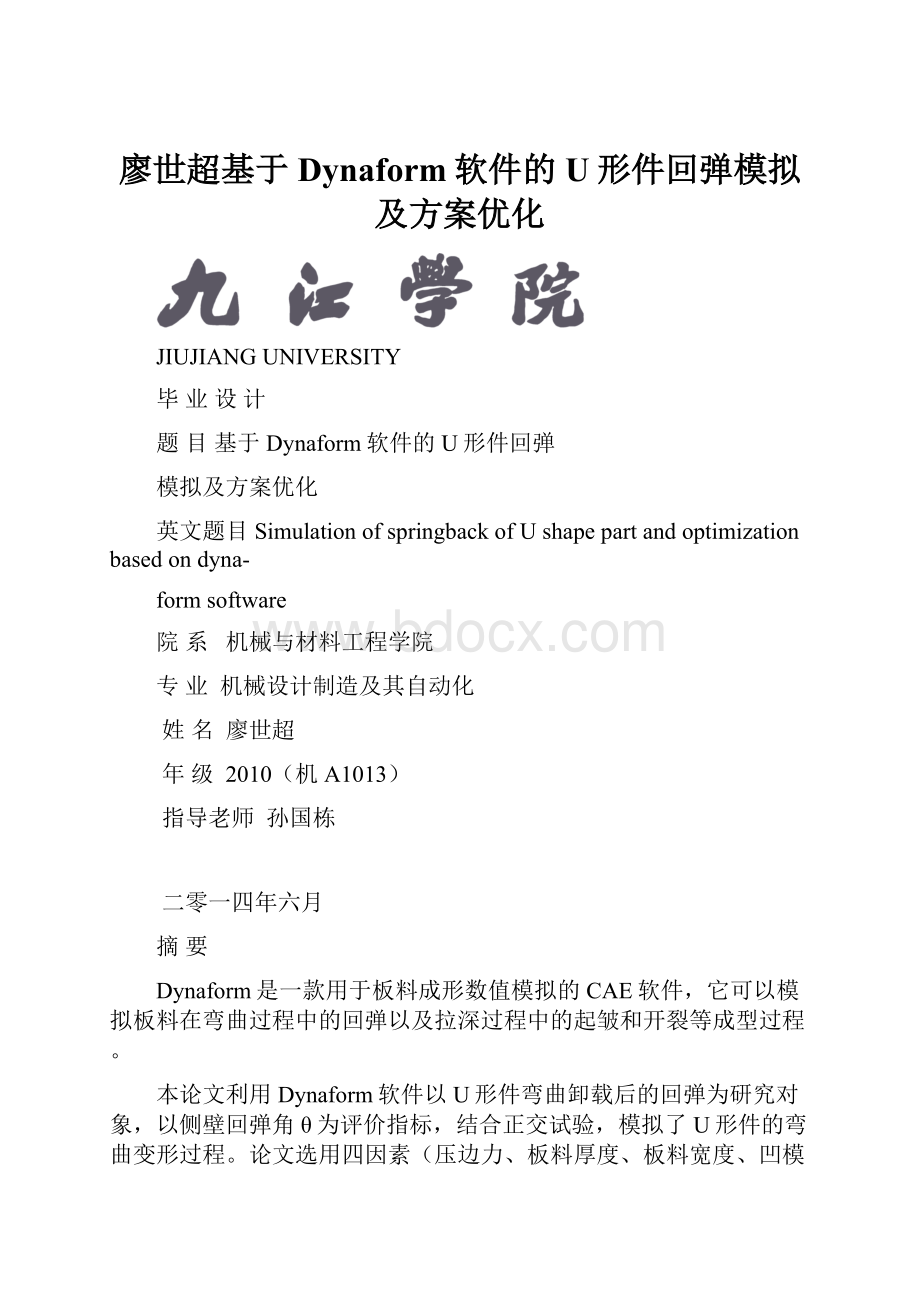
廖世超基于Dynaform软件的U形件回弹模拟及方案优化
JIUJIANGUNIVERSITY
毕业设计
题目基于Dynaform软件的U形件回弹
模拟及方案优化
英文题目SimulationofspringbackofUshapepartandoptimizationbasedondyna-
formsoftware
院系机械与材料工程学院
专业机械设计制造及其自动化
姓名廖世超
年级2010(机A1013)
指导老师孙国栋
二零一四年六月
摘要
Dynaform是一款用于板料成形数值模拟的CAE软件,它可以模拟板料在弯曲过程中的回弹以及拉深过程中的起皱和开裂等成型过程。
本论文利用Dynaform软件以U形件弯曲卸载后的回弹为研究对象,以侧壁回弹角θ为评价指标,结合正交试验,模拟了U形件的弯曲变形过程。
论文选用四因素(压边力、板料厚度、板料宽度、凹模圆角半径)三水平计算了9组试验下的弯曲回弹角。
运用极差分析法筛选出所给条件下的最优工艺方案:
压边力为4000N,坯料厚度为1.5mm,坯料宽度为80mm,凹模圆角半径为3mm。
优化后的弯曲回弹角为0.828°,相比于优化前的平均弯曲回弹角(1.565°),降低了47%。
【关键词】Dynaform;U形件;回弹角;正交试验;极差分析
Abstract
DynaformsoftwareisaCAEsoftwarewhichisusedinsheetmetalforming.Thissofewarecanstimulatespringbackofbendingandwrinkleorcrackofdrawing.
ThebendingofU-shapedpartisstimulatedbymeansofDynaformsoftwareandthespringbackanglewascalculatedbyTaguchimethodinwhichfourfactorsandthreelevelswereinvolved,includingbinderforce,thicknessofblank,widthofblankandradiusofchamperofdie.Throughcomparingthespringbackanglefromninevariedtechnologicalcombina-
tions,anoptimalparametercombinationwasobtained.Theoptimalparameteristhatbinderforceis4000N,thicknessofblankis1.5mm,widthofblankis80mmandradiusofchamperofdieis3mm.Theminimumspringbackangleafteroptimizationis0.828°whichis47%lowerthanthatofaveragevaluebeforeoptimization.
【Keywords】Dynaform;U-shapedpart;springbackangle;orthogonaltest;rangeanalysis;
前言
随着世界工业的迅猛发展,冲压件运用愈来愈广泛,生产制造业对冲压件需求很巨大,特别是对于航空航天、汽车、包装、造船等工业来说,以往的精度要求已无法满足现状。
在进行冷冲压成形的过程中回弹是无法避免的物理现象,影响零件的最终形状尺寸。
回弹量的大小对拉延件的几何尺寸精度产生直接影响,影响零件的最终形状尺寸。
所以对于冲压件的外力矩卸载后的回弹要求越来越严格,因此进行对弯曲变形产生的回弹进行研究是有十分重大的意义。
本论文系统地阐述板料冲压弯曲成形过程和介绍Dynaform回弹数值模拟技术。
运用正交试验法拟定试验项目,利用Dynaform对弯曲的变形过程以及弯曲卸载后产生的回弹进行数值模拟,对于模拟结果选择极差计算选取最优方案以优化生产工艺要求和降低成本。
第一章概论
1.1弯曲变形基础知识
1.1.1弯曲变形原理
弯曲就是按照一定的工艺要求使板料、金属管坯料进行形变,从而得到一定形状要求的零件的冲压成形工艺[1]。
能够进行弯曲的材料很多,例如:
各类板料及型材,也可以是棒料、管材。
弯曲工业在航空航天及汽车工业中具有十分广泛的应用,同时也适用于其他各类板料件生产。
用弯曲方式加工的零件种类非常多,其中包括U形件、V形件等。
图1.1示为U形件加工过程。
图1.1U形件加工过程
弯曲工序不仅可以利用模具在冲压机上进行,还可以在专用的设备上进行。
如折弯机、拉弯机等,虽然它们成形方法不同,但变形过程机特点却是存在部分相同的规律。
弯曲变形可根据变形区的的力学特性、工件形状、弯曲方式及使用设备等类别进行分类[2]。
1.通过对变形区的力学特性进行分,可分为四类:
弹性弯曲、弹-塑性弯曲、纯塑性弯曲、无硬化纯塑性弯曲。
(1)弹性弯曲:
变形区内各个部分的应力数值均小于材料的屈服强度,变形区域内只引发弹性变形。
(2)弹-塑性弯曲:
靠近变形区内外层应力数值大于工件材料屈服强度,而弯曲胚料中部的应力数值小于工件材料屈服强度,胚料变形区内既有弹性变形又有塑性变形。
(3)纯塑性弯曲:
胚料变形区的塑性变形很大,而中性层附近的弹性变形几乎可以忽略不计,且中性层到内、外层的应力和应变成线性关系。
(4)无硬化纯塑性弯曲:
即理想的纯塑性弯曲状况,假设弯曲过程中不存在加工硬化。
2.按工件形状分,有L形弯曲、V形弯曲、U形弯曲、Z形弯曲、多角弯曲等。
3.按弯曲设备分,有压弯机、折弯、滚弯及拉弯。
4.按坯料与模具相接触的成分划分,有自由弯曲、接触弯曲及校正弯曲等。
1.1.2弯曲变形过程
板料的弯曲变形过程一般可分为三个阶段[3]。
弯曲变形时,外部施加力矩作用在工件板料上,工件板料的曲率随着施加力矩的变化而产生变化,在工件板料变形区中,内层部分的坯料纤维在受到外力矩产生的切向应力的作用下发生压缩变形;相反地,坯料外层金属在受到外力矩产生切向拉应力作用下发生拉伸变形。
随着外部施加的力矩的逐渐增大,弯曲变形的程度也随着外力矩的增大而增大,因而弹性弯曲变形逐渐转变为塑性弯曲变形。
1.弹性变形阶段
弹性变形阶段即是在板料弯曲变形过程的开始阶段,此时外部施加的力矩不大,在坯料变形区域内表面和外表面上产生的应力均小于坯料的材料的屈服极限,因此仅仅是在板料内部变形区产生弹性变形。
沿着板料厚度的垂直方向分划为拉伸变形区和压缩变形区两个区域以应力中性层为分界线,两区域变形的切向应力分布如图1.2。
由坯料外侧到板料中心,切向应力渐渐变小。
从弯曲工艺的层面来分析,人们总是希望回弹越小越好,从而控制弹性变形的区域占变形区域的很小部分从而降低使外力卸载后回弹现象。
弹性变形区域的大小与材料种类、弯曲半径等许多因素关系较大。
图1.2弹性变形阶段切向应力分布如图
2.弹塑性变形阶段
在经历弹性变形阶段后,随着变形的进行,板料变形区域内的曲率半径随着外部施加的的弯曲力矩的增大持续减小。
变形区域内表面、外表面材料变形比弹性变形时更加激烈。
首先由弹性变形状态过渡到塑性变形状态,然后塑性变形从内、外表面扩展到应力中性层[4]。
沿着板料厚度的垂直方向划分为弹性变形区与塑性变形区以两个区域的应力达到屈服极限的层次为界限。
变形区域内的切向应力分布如由中性层开始到板料边缘切应力由小变大,最后趋向于平衡。
弹塑性变形阶段的特点是:
当卸除外部施加的弯曲力矩之后,塑性变形区域的材料保存着残留的弹性变形,而残留的弹性变形引起回弹回复作用的发生,因而弹塑性变形阶段中残留的弹性变形是产生回弹的主要原因[5]。
3.纯塑性变形阶段
当弯曲零件的相对弯曲半径很小时,由于此阶段产生的变形程度很大,我们近似地认为板料的整个横截面均发生塑性变形,板料的弯曲变形为纯塑性变形,这时的切向应力分布与其他阶段时不一样。
1.1.3弯曲卸载后的回弹
弯曲变形类似于其他的塑性成形工艺,在弯曲变形过程中同时有着弹性变形的存在。
一旦卸载弯曲力矩,中性层周围的弹性变形以及内、外层总变形种弹性变形部分随之引发回复作用,使得实际上弯曲件的弯曲角和相对弯曲半径与理论上及相应的模具角度、半径不一致,这种现象称为弯曲回弹[6]。
如图1.3所示
图1.3弯曲回弹现象
弯曲变形过程中在毛坯横截面上切向应力的变化如图1.4所示。
其中图a是在弯矩M的作用下毛坯横截面上切向应力的分布;图b是在毛坯在受到反向弯矩M′=-M时的切向应力分布;图c是受弯矩M作用的弯曲毛坯施加反向力矩M′时(等同于卸载状态下外作用力矩为零的情况),实际上图c所示的切向应力就是卸载后的残余应力[7]。
图1.4弯曲变形受力情况
弯曲回弹的形式一般划分为两类[8]。
改变弯曲件的弯曲半径由回弹以前的弯曲件弯曲半径转变为回弹后的回弹半径,弯曲半径的改变量可由应变中性层曲率半径的变化量ΔK来表示,如公式1-1所示。
(1-1)
其中:
ρ为卸载前应变中性层的曲率半径弯,ρ′为卸载弯曲后应变中性层的曲率半径。
弯曲曲中心角的变化由回弹前工件弯曲中心角α变为回弹后α′。
曲率半径变化量和回弹角均可表示为弯曲件的回弹量。
弯曲中心角的变化值称为回弹角,如式1-2所示。
(1-2)
1.1.4影响弯曲回弹的因素
弯曲件的回弹直接影响弯曲件的精度,为保证弯曲件的精度,必须考虑工件材料的回弹值。
影响工件回弹的因素众多[9],其中主要包括坯料的的形状尺寸、材料的力学性能、凹模圆角半径、压边力、弯曲方式、弯曲中心角、坯料厚度、相对弯曲半径及校正力等。
以下介绍部分影响因素。
1.材料的力学性能
材料的屈服强度越大,弹性模量E越小,硬化应变越严重(应变硬化指数n越大),弯曲件的回弹量夜越大。
其回弹值也与材料力学性能的稳定性有关,材料的力学性能越稳定,回弹值越小。
材料的屈服极限强度的值越高,在一定的变形程度范围内,弯曲变形区截面内的应力越大,从而引起更大的回弹变形,因此回弹值夜越大;回弹值也与材料的弹性模量(E)值有关,随着弹性模量的增大,弯曲件越能抵抗弹性变形,故回弹值则越小;在总变形量相同的条件下随着应变硬化指数n值得增大,增大了弹性变形在总变形中所占比例,因而卸载弯曲后回弹值就愈大。
2.相对弯曲半径r/t
相对弯曲半径的大小对回弹的影响:
相对弯曲半径减小时,坯料的弯曲程度增大。
坯料外部的总切向变形程度随着相对弯曲半径的减小而增大,板料中性层两侧的纯弹性变形比例所占越小,在总变形中弹性变形所占比例越小,因此回弹角也小。
与之相反,当相对弯曲半径增大时,坯料在变形过程中发生弹性变形所占比例越大,因而回弹就小。
3.弯曲中心角
随着弯曲中心角的增大,坯料弯曲变形区域的长度和宽度越大,在相同弯曲的弯曲情况下,单位长度上的变形量就越小,总变形中的弹性变形所包含的比例就相应越大,从而卸载后角度的回弹值就越大,但不影响曲率半径的回弹值。
另外,对于那些形状较为复杂的零件,若用坯料一次冲压弯曲成形则也会使回弹角减小,而因为在弯曲时材料的各个部分产生相互牵制同时弯曲件表面与冲压模具之间存在摩擦力也影响弯曲件应力状态,降低弯曲卸载后回弹现象的产生,故回弹角减小[10]。
4.校正弯曲
校正弯曲时,回弹值较小。
校正弯曲变形区的变形应力状况与其他弯曲状况是不同的,因为校正弯曲时校正力比自由弯曲时大的多。
当校正弯曲力十分大时,使的变形区内侧与外侧均产生与切向应变方向一致的拉应变,内、外侧金属纤维受拉伸长。
这样就使得内、外侧材料回弹趋势相互抑制,使校正弯曲时的回弹量比自由弯曲时减少很多。
影响弯曲回弹量的因素还包括材料厚度差异、毛坯与模具表面的摩擦、模具与模具坯料间隙和模具圆角半径等因素的影响[11]。
1.2Dynaform软件简介
Dynaform是一款专业的CAE工具,它是美国ETA公司和LSTC公司联合开发的一个专业软件包。
Dynaform的求解器和前、后置处理器分别是基于LS-DYNA和ETA/FEMB。
处理器和求解器的完美结合造就了Dynaform的强大功能[12]。
Dynaform的功能模块中包含拉延、压边、回弹、弯曲、多工步成形等模块,成形过程包括了钣金成形过程、液压冲压成形、滚压成形、模具成形等一系列成列过程。
用户可以利用Dynaform软件的数值模拟技术,非常清晰的了解各类坯料在不同的成形过程中的应力分布状况和随应力产生的变形的状况。
对于弯曲成形过程中可能出现的各种类型的缺陷包括拉断、裂纹、起皱等,Dynaform在模拟成形过程中都能预测到。
同时还可以预测到在成形过程中所需的载荷以及卸载载荷后引起的的回弹[13]。
Dynaform在模拟过程中还能提供一些比较充分的科学理论依据来帮助用户提高工艺设计和模拟分析能力,从而能够帮助用户在产品设计过程中提高模具设计质量,提升模具设计工艺,降低模具制造成本,减少试模时间。
Dynaform软件在世界范围内的运用十分普遍,称为各大制造企业的必备辅助分析CAE软件,特别实在汽车、航空航天、钢铁、造船等行业得到十分广泛应用。
最近几十年来,国内也快速地引进这款软件运用于制造业。
现在已经非常普遍,如中国东风、一汽、上海宝钢、黎明航空、江铃汽车等知名企业都已在运用Dynaform辅助设计过程[14]。
1.3国内外回弹研究现状综述
二十世纪末至今,包括国外和国内外的诸多研究人员对U形件回弹问题进行了广泛和深入的科学研究和试验,并取得了一系列丰厚的成果。
如“2mm工程”、“近零冲压”等研究项目,这些项目的研究目标控制成形过程中的回弹,从而将整车几何误差控制在2mm范围以内。
近些年国内上海大众汽车也正在展开“2mm工程”[15]。
综合国内外学者的研究,发现他们的研究方向大致可分为三类[16]:
1.第一类是理论研究,主要是根据变形塑性理论对一些典型的成形工艺建立经过科学简化的力学模型,用解析方法或数值试验方法获得分析结果,以研究和展现成形过程中回弹现象的机理;
2.第二类是实验研究及回弹的工程控制;
3.第三类是根据有限元数值模拟技术进行数值模拟。
近几十年以来,在冲压弯曲成形中回弹问题的研究发现上国内外学者所取得的主要成果可以总结为:
解析法、实验法、有限元数值模拟方法、回弹的预测和优化控制、U形件弯曲回弹的研究等。
1.4本论文的研究目的和意义
随着人们生活条件的提高,各类市场需求急速扩张,制造业得以飞速发展。
特别是航空航天、汽车、包装、造船等行业,这类制造业的制造业的迅猛发展对冲压件需求愈来愈巨大。
过去的精度要求以及工艺要求以无法满足现状。
因此进行对弯曲变形产生的回弹进行研究起着尤为重要的地位。
在进行冷冲压成形的过程中回弹是无法避免的物理现象,影响零件的最终形状尺寸。
回弹量的大小对拉延件的几何尺寸精度产生直接影响,影响零件的最终形状尺寸。
所以对于冲压件的外力矩卸载后的回弹要求越来越严格。
因此对冲压件的弯曲回弹工艺方案进行参数优化具有深远的意义。
第二章Dynaform模拟分析处理
本文运用目前最为广泛的专业板料分析CAE工具——Dynaform来对U形件弯曲成形过程中的弯曲回弹进行数值模拟分析。
在Dynaform软件的仿真环境中,可以模拟坯料厚度、坯料宽度、压边力、凹模圆角、模具尺寸、模具间隙等一系列环境参数,来辅助成形分析过程[17]。
2.1模型的构建
先将用CATIA软件建立毛坯轮廓线和下模DIE实体模型转换为IGS格式的文件,将转换后的毛坯轮廓线和下模DIE实体模型导入Dynaform软件中进行分析。
第一步,打开Dyanform。
第二步,打开菜单栏FILE/IMPORT,导入毛坯轮廓线和下模。
第三步,打开菜单栏Prats/edit,将毛坯层命名为BLANK,单击modify。
将下模命名为DIE,单击modify(二者颜色和编号均不能重复),点击OK确定,导入Dynaform软件后的模型文件如图2.1所示。
图2.1导入Dynaform后的毛坯层与下模
2.2网格的划分与处理
2.2.1网格划分
在导入毛坯层BLANK与下模DIE模型后,分别对毛坯层BLANK层和下模DIE模型进行网格划分。
在任务工具窗口点击surfacemesh,将全局网格边长设置为3.0,点击partmesh/selectsurfaces/part/blank2,单机击ok,然后单机apply后显示已划分网格。
划分网格后如下图图2.2所示。
划分毛坯层网格后,切换“DIE”为当前零件层,同样划分下模网格。
图2.2网格划分完成后的毛坯层与下模模型
2.2.2网格检查
因为利用Dynaform自动划网格的功能时分所得到的网格可能存在一些的潜在缺陷,随着工件的复杂程度增大缺陷也可能增多。
这些潜在的缺陷影响分析结果的正确性与准确性,因此需要对前面步骤所得的网格单元进行检查是否存在不合理缺陷。
Dynaform常有两项网格检查。
(1)将DIE层切换为当前零件层,切换后单击Preprocess,选择ModelCheck/Repair,在弹出的对话框中选择AutoPlateNormal工具按钮。
选择后,在弹出窗口中,选择CURSORPICKPART按钮,之后利用鼠标选择零件,当鼠标变为“+”形状时,选择在工作窗口上的DIE零件法线做为所选方向。
法线方向选择完毕后单击Yes确定所选择法线的方向。
(2)第二项是运用边界线检查零件层网格,利用从Dynaform窗口菜单栏中的BoundaryDisplay和ModelCheck/Repair检查零件层网格检查完成时,此时边界线高亮显示。
检查网格所得结果如图2.3所示。
图2.3检查网格后的毛坯层BLANK与下模DIE模型
2.3进行快速设置
快速设置是在传统的建模方法的基础上进行改进得到的新的设置方法,它与传统设置相比,能够大幅度减少设置时间。
但是拉延模拟设置方法灵活性没有传
统设置强,在本论文中,选择快速设置。
(1)创建压边圈BINDER层
在模拟过程中需要定义一个从Dynaform窗口菜单栏part/create中创建一个BINDER层,将其作为压边圈零件。
将为BINDER设为为当前零件层,之后Dynaform软件菜单栏part/addpart选择下模的法兰部分,添加网格到新建零件层,angle选项定义为1,选定BINDER作为目标零件层,自动划分网格。
(2)从DIE层中分离BINDER层
经过创建BINDER层的操作后,DIE层和BINDER层拥有了不同的单元组,但它们还有共享的节点因为它们沿着共同的边界,因此需要将他们分离开来,使得它们拥有各自相互独立的运动。
单击PARTS/Separate菜单选项,跳出Selectpart对话框,分别单击DIE和BINDER零件层,单击OK分离。
关闭除了BINDER外的所有零件层,观察所得的压边圈最终所得压边圈、坯料及下模数据如下图2.4所示。
模具侧边颜色较浅部分为压边圈BINDER层。
图2.4分离后的BLANK、下模DIE与BINDER层模型
(3)工具以及坯料定义
在Dynaform软件菜单栏上选择setup/drawdie,弹出快速设置的窗口,如图2.5示,在快速设置对话框中,若某项工具未定义,则其显示为高亮色。
在本文中,模拟类型选择singleaction及lowertoolavailable。
图2.5快速设置的窗口
点击binder,进入defindpart界面,点击selectpart在弹出的defindbinder界面中选择add按钮,然后从零件列表选中binder。
单击definebinder界面的ok及完成了对零件层Binder的定义。
同样的方法,定义DIE。
在快速设置工作界面中在设teriallibrary中选择材料。
选择材料后单击ok确认。
确认之后,可以利用preview预览模具的运动关系,如图2.6所示。
(4)设置分析参数以及分析求解
在定义完工具与胚料后在QuickSetup界面中的Apply按钮,之后再点击SubmitJob选项,在弹出的工作界面中选中FullRunDyna选项,同时选中DynainOutput、AdaptiveMesh、SpecifyMemory选项,其他参数默认为缺省值,完成设置。
点击OK进行计算求解。
运算界面中包含有系统预计时间,但时间不太准确,因电脑配置差异而不同。
计算机分析计算完成后,保存计算结果。
图2.6preview预览图
2.4回弹模拟
进行回弹计算时,第一步,创建Dynaform数据库,在Dynaform窗口菜单栏中的file/new选项中新建,然后file/saveas另存数据库文件,此数据库文件存储地址与分析计算的地址应当不一样,以免覆盖之前计算结果文件。
第二步,Dynaform窗口菜单栏中的file/import中在导入模型(回弹计算的模型文件为后缀为.dynain的文件)。
如下图2.7所示。
图2.7分析计算结果图
第三步,毛坯及材料参数设定。
单击Dynaform窗口菜单栏中的setup/springback按钮,如图2.8所示,在弹出的对话框中点击BLANK,打开defineblank中的selectpart和add按钮,添加刚才带入的零件。
单击OK定义毛坯完成。
单击Dynaform窗口菜单栏中material/none,弹出material对话框。
在new中选择合适材料(必须与成形中的材料参数相同)同时选择板材厚度。
第四步选择求解算法及自适应网格处理,Springback对话框中选择中单步隐式算法,同时选中Coarsening(网格粗化)按钮,进行网格粗化。
进行网格粗化是为了大大地节约计算时间及降低不稳定性。
而且还有利于回弹分析计算的收敛。
配置完成后点击SubmitJob进入设置分析选项界面,在下拉菜单中选中FullRunDyna,输入TITLE,单击OK后开始进行回弹计算。
图2.8springback界面
2.5回弹结果测量
在默认的存储位置会生成得到d3plot的文件,此文件即为回弹分析计算结果文件,而该d3plot文件是在回弹计算中采用单步隐式得到的,因此它只有两帧,一帧为回弹前结果,另一帧为回弹后结果,分别打开观察变化。
(1)在Postprocess工具栏点击FLD(成形极限图)按钮,打开“Frames(帧)”下拉菜单,选中SingleFrames选项,同时选择第二帧。
创建成形极限图,观察成形极限图2.9可以发现,在弯曲成形后U形件的部分是绿色区域时,是属于安全范围内的,因此只需考虑回弹而不用考虑其它状况的发生,如成形时的拉裂、起皱等缺陷。
图2.9成型极限图
(2)测量计算结果
利用Dynaform窗口菜单栏中的Postprocess工具栏中的measure工具对d3plot文件的第一帧的侧壁回弹角θ进行测量。
同样对第二帧的侧壁回弹角θ进行测量,回弹前后对比如图2.10所示。
得到回弹前、后的侧壁回弹角θ,测量结果如图2.11所示,完成分析过程。
图2.10回弹前后对比图
图2.11模拟回弹结果测量
第三章U形件数值模拟正交试验
正交试验法是研究与处理多参数多因素试验的试验方