真空热处理和形变热处理.docx
《真空热处理和形变热处理.docx》由会员分享,可在线阅读,更多相关《真空热处理和形变热处理.docx(18页珍藏版)》请在冰豆网上搜索。
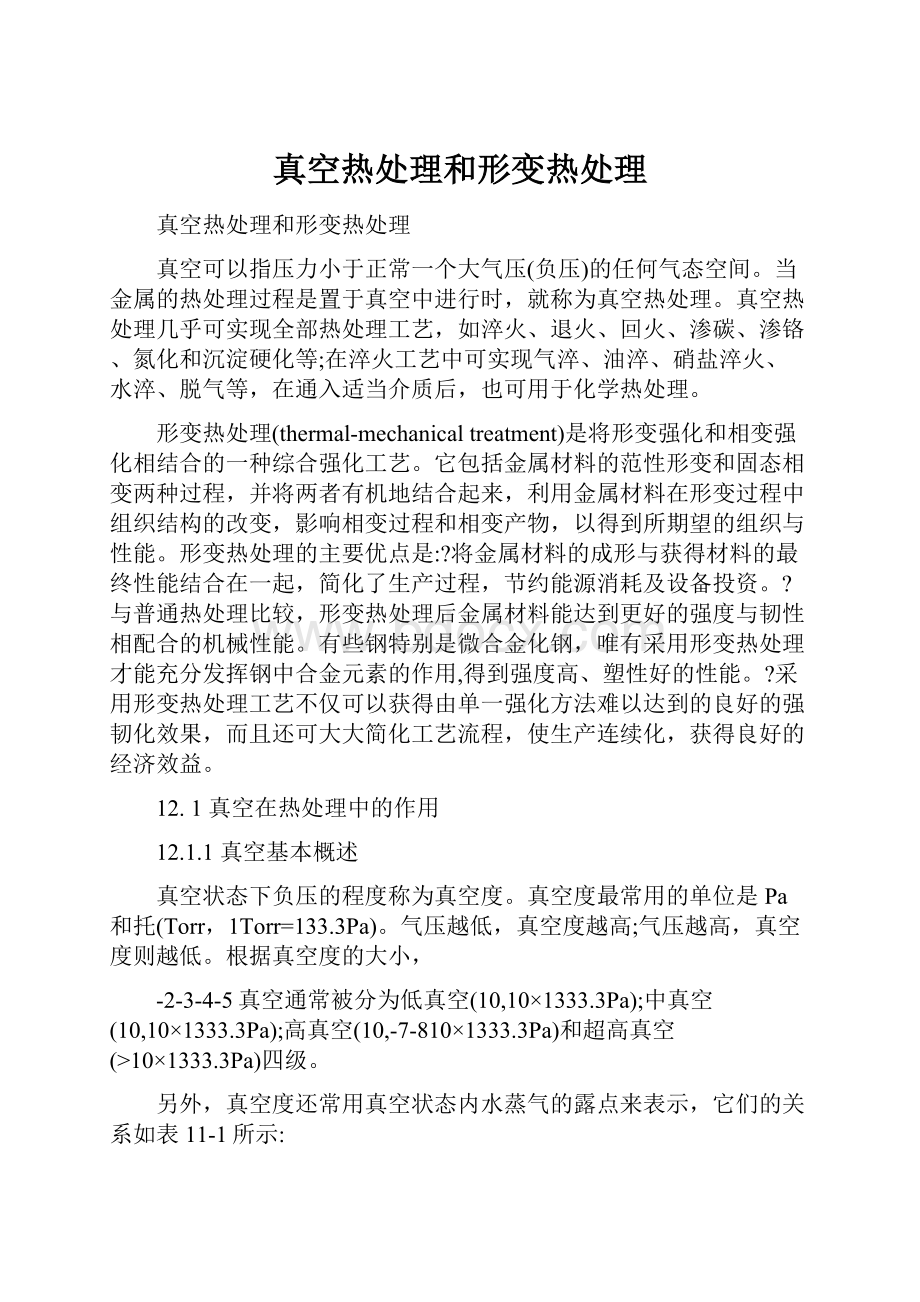
真空热处理和形变热处理
真空热处理和形变热处理
真空可以指压力小于正常一个大气压(负压)的任何气态空间。
当金属的热处理过程是置于真空中进行时,就称为真空热处理。
真空热处理几乎可实现全部热处理工艺,如淬火、退火、回火、渗碳、渗铬、氮化和沉淀硬化等;在淬火工艺中可实现气淬、油淬、硝盐淬火、水淬、脱气等,在通入适当介质后,也可用于化学热处理。
形变热处理(thermal-mechanicaltreatment)是将形变强化和相变强化相结合的一种综合强化工艺。
它包括金属材料的范性形变和固态相变两种过程,并将两者有机地结合起来,利用金属材料在形变过程中组织结构的改变,影响相变过程和相变产物,以得到所期望的组织与性能。
形变热处理的主要优点是:
?
将金属材料的成形与获得材料的最终性能结合在一起,简化了生产过程,节约能源消耗及设备投资。
?
与普通热处理比较,形变热处理后金属材料能达到更好的强度与韧性相配合的机械性能。
有些钢特别是微合金化钢,唯有采用形变热处理才能充分发挥钢中合金元素的作用,得到强度高、塑性好的性能。
?
采用形变热处理工艺不仅可以获得由单一强化方法难以达到的良好的强韧化效果,而且还可大大简化工艺流程,使生产连续化,获得良好的经济效益。
12.1真空在热处理中的作用
12.1.1真空基本概述
真空状态下负压的程度称为真空度。
真空度最常用的单位是Pa和托(Torr,1Torr=133.3Pa)。
气压越低,真空度越高;气压越高,真空度则越低。
根据真空度的大小,
-2-3-4-5真空通常被分为低真空(10,10×1333.3Pa);中真空(10,10×1333.3Pa);高真空(10,-7-810×1333.3Pa)和超高真空(>10×1333.3Pa)四级。
另外,真空度还常用真空状态内水蒸气的露点来表示,它们的关系如表11-1所示:
表11-1真空度和露点的关系
-1-2-3-4-5真空度(×133.3Pa)1001011010101010
露点(?
)1118-40-59-74-88-101
真空炉中的气体包括残留空气、炉体,工件内释放的气体;润滑油蒸发气体和外界渗入气体等,非常复杂,必须要用真空泵不停排气以保证达到所需要的真空度。
12.1.2真空热处理的优越性
真空热处理(vacuumheattreatment)方法所得到的金属工件表面可以获得一般热处理所没有的特殊效果,显示出一定的优越性。
真空气氛在钢的热处理过程中,主要有以下几种有益或有害的作用:
1(脱脂
工件在热处理之前,由于机械加工或压力成型,往往在表面粘有油污。
粘附在金属表面的油脂、润滑剂等蒸气压较高,在真空加热时,自行挥发或分解成水,氢气和二氧化碳等
气体,并被真空泵抽走,与不同金属表面产生化学反应,得到无氧化、无腐蚀的非常光洁的表面。
不过,生产中工件一般仍要进行预先脱脂处理,以减轻油污对于真空系统的污染。
2(除气
金属在熔炼时,液态金属要吸收H、O、N、CO等气体,由于冷却速度太快,这些气222
体留在固体金属中,生成气孔及白点等各种冶金缺陷,使材料的电阻、磁导率、硬度、强度、塑性、韧性等性能受到影响,根据气体在金属中溶解度,与周围环境的分压平方根成正比的关系,分压越小即真空度越高,越可减少气体在金属中的溶解度,释放出来的气体被真空泵抽走。
金属内部的脱气是按下列步骤进行的:
?
金属中的气体元素向表面扩散;?
气体从金属表面逸出;?
气体被真空炉排除。
其中,第?
步中气体的扩散速度是影响脱气效果的主要因素,故真空热处理时脱氢较易而脱氧、氮则较难。
3(分解氧化物
金属表面的氧化膜、锈蚀、氧化物,氢化物在真空加热时被还原、分解或挥发而消失,使金属表面光洁。
钢件真空度达0.133~13.3Pa即可达到表面净化效果,金属表面净化后,活性增强,有利于C、N、B等原子吸收,使得化学热处理速度增快且成分分布均匀。
当真空度足够,氧的分压低于氧化物分解压力时,可以使表面已经形成的氧化物发生分解而被去除,获得光亮的表面。
4(表面保护
真空热处理实质上是在极稀薄的气氛中进行,炉内残存的微量气体不足以使被处理的金属材料产生氧化脱碳,增碳等作用。
使金属材料表面的化学成分和原来表面的光亮度保持不变。
大多数金属在含氧、水蒸气和CO等氧化性气氛中加热时会发生氧化现象;有氧存在时2
还可能引起钢的脱碳。
理论上讲,金属(M)与其氧化物(MO)存在下列可逆反应:
2MO,2M,O(式12-1)2
真空热处理中,当氧的分压大于分解压力(PO)时,反应向左方向进行,生成氧化物。
2
要达到金属不被氧化的目的,必须使炉内氧的分压低于氧化物的分压。
一般来说,只要炉内
-5氧的分压达到10×1333.3Pa时,大多数金属都可避免被氧化,从而获得光亮的表面。
真空热处理同样具有下列不利现象:
(1)合金元素的蒸发
各种金属在不同温度下有不同蒸气压,当真空度提高时,蒸气压高的金属(Mn、Cr)容易蒸发、损害材料本身化学成分构成并污染其它金属表面,使零件之间,或零件与料筐之间粘结,造成电气短路,材质改性等缺陷。
对于钢来说,真空热处理时最容易蒸发的合金元素是Mn、Cr,而它们又是钢中常用的金属元素。
通常零件应先抽成高真空,加热至800ºC以下;800ºC以上应通以惰性气体,将真空度降低20,26.7Pa。
(2)真空加热油淬引起钢件渗碳
-2钢经真空加热油淬后会引起渗碳。
如:
30CrMnSiN2A钢在真空度为10×1333.3Pa、加热温度为900?
情况下油淬就可发现有渗碳现象。
这是由于在高温真空加热时对表面的净化作用使得材料表面处于活性状态,当炽热的工件与淬火油接触时,在油蒸气的包围下引起渗碳过程。
一般来说,这种钢件渗碳对于材料表面性能是有害的。
减轻真空油淬渗碳可采用推迟工件进入油中的时间;淬火开始阶段使油上方保持低压状态;工件浸入油中前稍稍氧化等。
12.2真空热处理工艺
真空热处理热效率高,可实现快速升温和降温;稳定性和重复性好,表面质量好,工作环境好,操作安全,没有污染和公害等优势,应用范围日益扩大。
下面就几种常规真空热处理、化学真空热处理和几种特殊真空热处理工艺进行简要的介绍:
12.2.1钢的真空退火、真空淬火及回火
1.真空退火
对于钢来说,真空退火的主要目的之一就是要求表面达到一定的光亮度。
真空退火钢件的光亮度是由真空度、退火温度和出炉温度有关的。
例如,对于工具钢(尤其是含铬的合金钢),退火温度、真空度与光亮度的关系如图12.1
-2所示,在10×1333.3Pa真空度下退火,光亮度较差,一般都在40%以下;而当真空度提高到-410×1333.3Pa时,除Cr12高铬钢外,光亮度均可达到90%以上。
真空退火时的出炉温度对产品光亮度的影响也很大。
出炉温度越高,光亮度就越低。
除抗氧化性能较好的高合金钢(如不锈钢等)外,钢的出炉温度均应在200?
以下。
图12.1工具钢真空退火温度、真空度与光亮度的关系
2.真空淬火
真空淬火冷却速度快,需要采用适当的淬火介质如水、油、气等。
其中,油冷具有广泛的适用范围;气冷的冷速较小,且价格较贵,有一定的应用;水冷冷速较快,但是由于水冷的特点,只适用于低碳、低合金钢。
真空淬火一般采用特殊的真空淬火油。
真空淬火油应具有蒸发量小,不易污染真空炉;蒸气压低,不影响真空气氛;真空中冷却能力强;稳定性好等特点。
真空淬火油的冷却能力一般随着真空度的增加而不断降低。
从提高淬火钢的光亮度来说,希望保持更低的压力,而压力过低又会降低淬火油的冷却能力。
为了兼顾二者的要求,一般采用先在低压下加热,临淬火之前通入高纯度的保护气氛(惰性气体或氮气),增高压力,再淬火。
真空热处理加热主要靠辐射传热进行,故其在工件中引起的应力和形变与普通淬火相
比要小。
3.真空回火
由于600?
以下在真空中加热缓慢,而回火温度大部分在此范围,故真空回火热处理时应在排气、升温后,立即通入惰性气体。
惰性气体可以进行强制对流传热。
12.2.2钢的真空渗碳、渗氮
1.真空渗碳
真空渗碳工艺曲线图见图12.2。
工件进入真空炉后,先排气降低真空度至0.133Pa,随后通电加热使温度达到渗碳温度(1030,1050?
)并保温。
经过一段时间的保温,由于工件和炉内材料脱气,真空度会有所降低,此过程结束后,真空度继续上升。
经过适当的均匀热保温后,通入渗碳剂进行渗碳,此时真空度又下降。
几分钟后,停止通入渗碳剂,真空度上升,保温,进行扩散。
如此循环数次后,渗碳完成。
随后,通入氮气并将工件移入冷却室,冷至550,660?
后,重新移入加热室,在真空状态下加热到淬火温度,借重结晶细化晶粒。
加热保温结束后,通入氮气,并进行油淬。
图12.2真空渗碳的工艺曲线
1-抽真空;2-升温脱气;3-均热;4-渗碳及扩散;5-淬火加热(细化晶粒);6-淬火冷却
真空渗碳时,由于不存在渗碳气体和钢件的平衡反应,钢件在高温下处于碳氢化合物气体中,数分钟内表面即可达到很高的合碳量,从而增大了工艺控制的难度。
到目前为止生产中仍采用在不同温度和气压条件下碳传递速度的试验测定数据来控制。
这些数据存储在数据库和有关碳渗入和扩散的计算机程序中。
当计算的钢件表面合碳量达到奥氏体的饱和极限时,控制系统就中止渗碳(强渗)。
此过程仅持续数分钟,依次施行渗碳、排气和扩散直到获得规定的渗层厚度为止。
和常规气体渗碳相比,真空渗碳具有一系列优点,诸如在渗层中不会出现内氧化和反常组织,工件表面光亮、渗速快,易于实现离子渗碳和高温渗碳,进一步提高渗速。
真空渗碳后再施行高压气淬,可使渗碳淬火的钢件形变减到最低程度。
如Ipsen公司开发的RVTC低压渗碳和冷腔高压气淬双室炉,可用于航空工业的齿轮、轴承或特种零件的渗碳淬火。
乙炔渗碳的半连续式低压渗碳、油中淬火、清洗、回火生产线已用于生产汽车变速箱齿轮,每条线每日生产量可达5400kg。
2.真空渗氮
真空渗氮是使用真空炉对钢铁零件进行整体加热、充入少量气体,在低压状态下产生活
性氮原子渗入并向钢中扩散而实现硬化的;而离子渗氮是靠晖光放电产生的活性N离子轰击并仅加热钢铁零件表面,发生化学反应生成核化物实现硬化的。
真空渗氮又称为真空排气式氮碳共渗,其特点是通过真空技术,在加热、保温、冷却的整个热处理过程中,不纯的微量气体被排出,可使金属表面活性化和清净化;含活性物质的纯净复合气体被送入,使表面层相结构的调整和控制、质量的改善、效率的提高成为可能。
经X射线衍射分析证实,真空渗氮处理后,渗层中的化合物层是ε单相组织,没有其他脆性相(如FeC、FeO)存在,硬度高,韧性好,分布均匀。
“白层”单相ε化合物层可达到334
的硬度和材质成分有关。
材质中含Cr量越高,硬度也呈增加趋势。
Cr13,时,硬度可达到1200HV;含Cr18,(质量分数,余同)时,硬度可达1500HV;含Cr25,时,硬度可达1700HV。
无脆性相的单相ε化合物层的耐磨性比气体氮碳共渗组织的耐磨性高,抗摩擦烧伤、抗热胶合、抗熔敷、抗熔损性能都很优异。
但该“白层”的存在对有些模具和零件也有不利之处,易使锻模在锻造初期引起龟裂;焊接修补时易生成针孔。
真空渗氮还有一个优点,就是通过对送入炉内的含活化物质的复合气体的种类和量的控制,可以得到几乎没有化合物层(白层),而只有扩散层的组织。
其原因可能是在真空炉排气至0.l33Pa(1×10-3Torr)后形成的,另一个原因是带有活性物质的复合气体在短时间内向钢中扩散形成的组织。
这种组织的优点是耐热冲击性、抗龟裂性能优异。
因而对实施高温回火的热作模具,如用高速钢或4Cr4MoSiV(H13)钢制模具可以得到表面硬度高、耐磨性好、耐热冲击性好、抗龟裂而又有韧性的综合性能;但仅有扩散层组织时,模具的抗咬合性、耐熔敷、熔损性能不够好。
由于模具或机械零件的服役条件和对性能的要求不一,在进行表面热处理时,必需调整表面层的组织和性能。
真空渗氮除应用于工模具外,对提高精密齿轮和要求耐磨耐蚀的机械零件以及弹簧等的性能都有明显效果,可接受处理的材质也比较广泛。
12.3形变热处理的作用和强韧化机理
形变热处理已广泛应用于生产金属与合金的板材、带材、管材、丝材,和各种零件如板簧、连杆、叶片、工具、模具等。
形变热处理工艺中的塑性变形,可以用轧、锻、挤压、拉拔等各种形式;与其相配合的相变有共析分解、马氏体相变、脱溶等。
形变与相变的顺序也多种多样:
有先形变后相变;在相变过程中进行形变;也可在某两种相变之间进行形变。
12.3.1形变对钢基体的作用
1.形变对母相的作用
形变热处理中,形变使相变前的母相的组织结构甚至成分都起变化,形变后或形变过程中的相变在相变动力学和相变产物的类型、形貌等方面,都不同于一般热处理,从而得到良好的性能。
形变对母相组织结构带来的变化随形变条件(形变温度、道次形变量、总形变量、形变速度……)及金属材料成分的不同而有差异,根据对相变的作用,母相形变后的组织结构基本上属于三类:
?
在再结晶温度以上形变,道次形变量如超过再结晶临界变形量,则母相发生动态或静态的再结晶,使晶粒得到细化;如进行多道次形变,则发生多次再结晶,母相的晶粒显著细化。
?
在材料的再结晶温度以下形变,母相不发生再结晶,而产生大量晶体缺陷,或仅发生回复过程,形成多边化亚结构。
?
形变诱发第二相由母相中析出,析出的第二相又与位错交互作用,使母相的成分与结构皆发生变化。
形变对相变的作用形变热处理中,形变后的母相组织经常是以上几类的综合。
现以钢的奥氏体为例,说明形变后的奥氏体对以后的相变及相变产物的作用。
2.形变对铁素体,珠光体型相变的作用
形变后产生了再结晶的细奥氏体晶粒,使冷却转变后的铁素体也相应得到细化。
形变后未发生再结晶的奥氏体中的大量晶体缺陷,为此后铁素体的转变提供了大量形核位置,并使铁素体形核的热激活过程更容易进行,这两者使转变后的铁素体晶粒细化;此外形变的奥氏体有加速扩散过程,加速铁素体转变速度,提高铁素体形成的温度等作用。
3.形变对淬火时马氏体、贝氏体相变的作用
再结晶的奥氏体仅能细化所转变的马氏体或贝氏体组织。
形变而未再结晶的奥氏体,对淬火时的马氏体和贝氏体转变的作用却是多方面的。
奥氏体中的大量晶体缺陷使以共格方式长大的马氏体、贝氏体晶体长大受阻,使转变后的组织得到细化。
奥氏体中的晶体缺陷可被其转变的马氏体、贝氏体所继承,使转变后的马氏体或贝氏体组织的位错密度高于一般热处理形成的马氏体和贝氏体的位错密度。
当奥氏体在形变过程产生形变诱发第二相析出时,这种现象尤为突出。
形变诱发析出的第二相质点,钉扎了奥氏体已有的可动位错;在进一步形变时,促进奥氏体增殖大量新的位错,大大增加奥氏体中的位错密度,相应地增加转变后的马氏体的位错密度。
马氏体、贝氏体中位错密度提高,是形变淬火得以提高钢的强度的主要原因。
这样的马氏体组织在回火时,由于位错密度高,为碳化物提供了大量形核位置,结果使回火马氏体中的碳化物质点更细小,分布更均匀。
形变诱发由奥氏体中析出第二相,降低奥氏体中碳和合金的含量,有利于减少孪晶马氏体,增多板条状马氏体的数量。
马氏体组织的细化、孪晶马氏体的减少,以及回火时均匀的碳化物分布,是形变淬火钢韧性好的原因。
奥氏体形变中形成的亚晶粒,比较稳定,不仅可为直接形成的马氏体所继承,还能遗传给重新加热淬火,再次形成的马氏体组织,使形变淬火后再加热淬火的钢的强度仍高于一般淬火钢。
形变奥氏体除可以细化所转变的贝氏体外,还能改变转变的贝氏体组织类型。
低碳贝氏体钢未形变的奥氏体转变为上贝氏体组织,形变的奥氏体则转变为颗粒状贝氏体组织,这种组织的塑性、韧性比上贝氏体要好。
4.形变诱发马氏体相变
在Ms,Md温度范围内形变能诱发奥氏体转变为马氏体,而在Ms温度以上就发生马氏体转变。
Md称为形变诱发马氏体开始转变点。
形变诱发马氏体可提高钢的强度,更重要的是,在奥氏体基体中的应力集中,由于形变诱发马氏体的产生而得以弛豫,避免微裂纹的产生与扩展,提高钢的塑性。
12.3.2影响形变热处理强化效果的因素
钢在形变热处理后之所以能够获得良好的强韧性是由形变导致钢的显微组织和亚结构的特点所决定的。
其强韧化基理主要有细化显微组织、改变位错密度和亚结构、弥散化碳化物等。
而影响形变热处理强化效果的因素有很多,其中最主要的因素有形变温度、型变量和形变后淬火前的停留时间等。
1.形变温度
当变形量确定时,形变温度越低,强化效果越好,但塑性和韧性会有所下降。
这是由于
形变温度越高越有利于钢组织的回复、多边形化和呈现结晶过程的发生和发展。
2.形变量
在低温形变淬火时,形变量越大,强化效果越显著,塑性则有所下降。
为获得较好的强化效果,通常形变量应?
60,70%。
图12.3为形变量对0.3C-3Cr-1.5Ni钢机械性能的影响。
在高温形变淬火时,如果钢中有较多铬、钼、钨、钒、锰、镍和硅等延缓再结晶作用的元素时,形变强化过程会一直占主导地位,随形变量的增加而增加(如45CrMnSiMoV等)。
对于一般钢种来说,其强化效果随形变量的增加而先增加后减弱,呈现一个极值。
图12.3形变量对0.3C-3Cr-1.5Ni钢机械性能的影响
3.形变后淬火前的停留时间
图12.4为停留时间对高温形变淬火60Si2V钢性能的影响。
在低温形变淬火中,在亚稳奥氏体形变后将钢再加热至略高于形变温度,并适当保持数分钟使奥氏体发生多边形化,然后再淬火和回火,可以显著地提高钢的塑性,称为多边形化处理。
随多边形化处理温度的提高和时间的延长,钢的塑性不断提高,强度略有下降。
在高温形变淬火时,由于形变温度高于奥氏体的再结晶温度,形变后在此温度停留时可以出现回复、多边形化和再结晶等现象。
图12.4停留时间对高温形变淬火60Si2V钢性能的影响(400?
回火1h)
(a)形变量20%;(b)形变量50%
12.4表面形变热处理的分类
形变热处理种类繁多,名称也很多,但通常可按照形变与相变过程的相互顺序将其分成三种基本类型:
相变前形变、相变中形变和相变后形变等三种。
其中有可按照形变温度(高温、低温)和相变类型(珠光体、贝氏体、马氏体及时效等)又细分成若干种类。
此外,还有表面形变热处理和形变化学热处理等其它热处理工艺等。
图12.5为形变热处理分类示意图。
12.4.1相变前形变的形变热处理
1.高温形变热处理
(1)高温形变淬火(图12.5a)
高温形变淬火是将钢加热至奥氏体稳定区(A以上)进行形变,随后采取淬火以获得马c3
氏体组织,具体包括锻后余热淬火、热轧淬火等。
高温形变淬火后,再于适当温度回火,可以获得很高的强韧性。
适用于结构钢、工具钢、碳钢和合金钢等,一般在强度提高10,30%时,塑性可提高40,50%,冲击韧性则成倍地增长。
图12.5形变热处理分类示意图
(2)高温形变正火(图12.5b)
高温形变正火的加热和形变条件与高温形变淬火相同,但随后采取空冷或控制冷却,以获得铁素体+珠光体或贝氏体组织(这种工艺又叫“控制轧制”)。
采用这种工艺的主要优点在于可显著改变钢的强韧性,特别是可大大降低钢的韧脆转化温度,对于含有微量铌、钡、钒等元素的钢来说,尤为有效。
从形式上看,它很像一般轧制工艺,但实际上区别很大。
主要是轧制温度较低,通常都在A附近,有时甚至在α+γ两相区(800,650?
),而一般轧制c3
的终轧温度都高于900?
。
另外,控制轧制要求在较低温度范围有足够大的形变量,例如对低合金高强度钢规定在900,950?
以下要有50%以上的总形变量。
此外,为细化铁素体晶粒和第二相质点,要求在一定温度范围内控制冷却。
(3)高温形变等温淬火(图12.5c)
高温形变等温淬火是采用与前两者相同的加热和形变条件,但随后在贝氏体区等位,以获得贝氏体组织。
这种贝氏体组织的性能比普通贝氏体要优越得多。
2.低温形变热处理
(1)低温形变淬火(图12.5d)
低温形变淬火是在奥氏体化后快速冷却至亚稳奥氏体区中具有最大转变孕育期的温度(500,600?
)进行形变,然后淬火以获得马氏体组织。
可以在保证一定塑性的条件下,大幅度地提高强度,可使高强度钢的抗拉强度由1800,2800MPa。
适用于强度要求很高的零件如火箭壳体、飞机起落架、炮弹壳、模具和冲头等。
(2)低温形变等温淬火(图12.5e)
低温形变等温淬火是采用与上者相同的加热和形变条件,随后在贝氏体区进行等温淬火以获得贝氏体组织。
采用这种工艺可以在比低温形变淬火略低的温度,得到塑性较高的钢。
适用于热作模具及高强度钢制造的小零件。
12.4.2相变中形变的形变热处理
1.等温形变热处理(图12.5f)
等温形变热处理是将钢加热到A温度以上奥氏体化,然后迅速冷却至A一下亚稳奥c3c1氏体区,在某一温度同时进行形变和相变(等温转变)的工艺。
根据形变和相变温度的不同,又可分为获得珠光体的等温形变处理和获得贝氏体的等温形变处理。
获得珠光体组织的等温形变处理工艺在提高强度方面的效果并不显著,但却可大大提高冲击韧性和降低韧脆转变温度。
获得贝氏体的等温形变淬火在提高强度方面的效果要比前者显著得多,而塑性指标却与之相近,主要适用于通常进行等温淬火的轴、小齿轮、弹簧、链结等小零件。
2.马氏体相变过程中的形变热处理(图12.5f)
利用钢中奥氏体在M,M之间受形变时可诱发形成马氏体而获得强化的工艺。
主要包ds
括:
对奥氏体在室温(或低温)下进行形变,使奥氏体加工硬化,并且诱发生成部分马氏体,再加上形变时对诱发马氏体的加工硬化作用,将使钢获得显著的强化作用。
图12.6为18-8不锈钢在不同形变温度下形变量对机械性能的影响。
如图所示,形变量越大,钢的强度越高,塑性越低;且形变温度越低,上述现象越强烈。
图12.618-8不锈钢在不同形变温度下形变量对机械性能的影响
室温诱发马氏体形变,利用相变诱发塑性(TRIP)现象使钢件在使用中不断发生马氏体转变,从而兼有高强度和超塑性,具有本种特性的钢被称为变塑钢。
这种钢一般在成分设计上保证了在经过特定的加工处理后使其M点低于室温,而M点高于室温。
这样,钢在室温sd
使用时也可具备本种特性。
12.4.3相变后形变的形变热处理
通过这种工艺,可以强化钢冷却转变的产物。
这种转变产物可能是珠光体、贝氏体、马氏体或回火马氏体等,形变温度范围包括室温至Ac以下。
1
1.珠光体的冷形变(图12.5g)
在钢丝铅淬冷拔时,钢丝坯料经过奥氏体化通过铅浴等温分解,获得细密而均匀的珠光体组织,随后进行冷拔。
细密的片状珠光体经大量变形的冷拔后,使其中渗碳体片变得更小,位错密度更高。
且铅浴温度越低、冷拉变形量越大,冷拔钢丝的强度就越高。
2.珠光体的温加工(图12.5h)
在加工珠光体轴承钢时,将退火钢加热至700,750?
进行形变,然后慢速冷却至600?
后出炉。
采用这种工艺比普通球化退火要快15,20倍,且球化效果更好。
3.回火马氏体的时效(图12.5i)
回火马氏体的时效可获得高强度的钢件。
回火马氏体的强化效果主要是由ε碳化物产生,而ε碳化物则由过饱和的α铁素体提供。
如在形变后进行最终的低温回火,则将更有利于ε碳化物的产生,造成回火后钢屈服强度的进一步增高。
但如果继续提高回火温度,将会由于碳化物的沉淀、聚集长大以及α铁素体的回复而导致强化效果的减弱。
图12.6为300M钢回火马氏体组织经小量形变后的性能变化(12.7a)和最终回火温度对强化效果的影响(12.7b)
图12.7300M钢回火马氏体组织