铣床操作规范.docx
《铣床操作规范.docx》由会员分享,可在线阅读,更多相关《铣床操作规范.docx(17页珍藏版)》请在冰豆网上搜索。
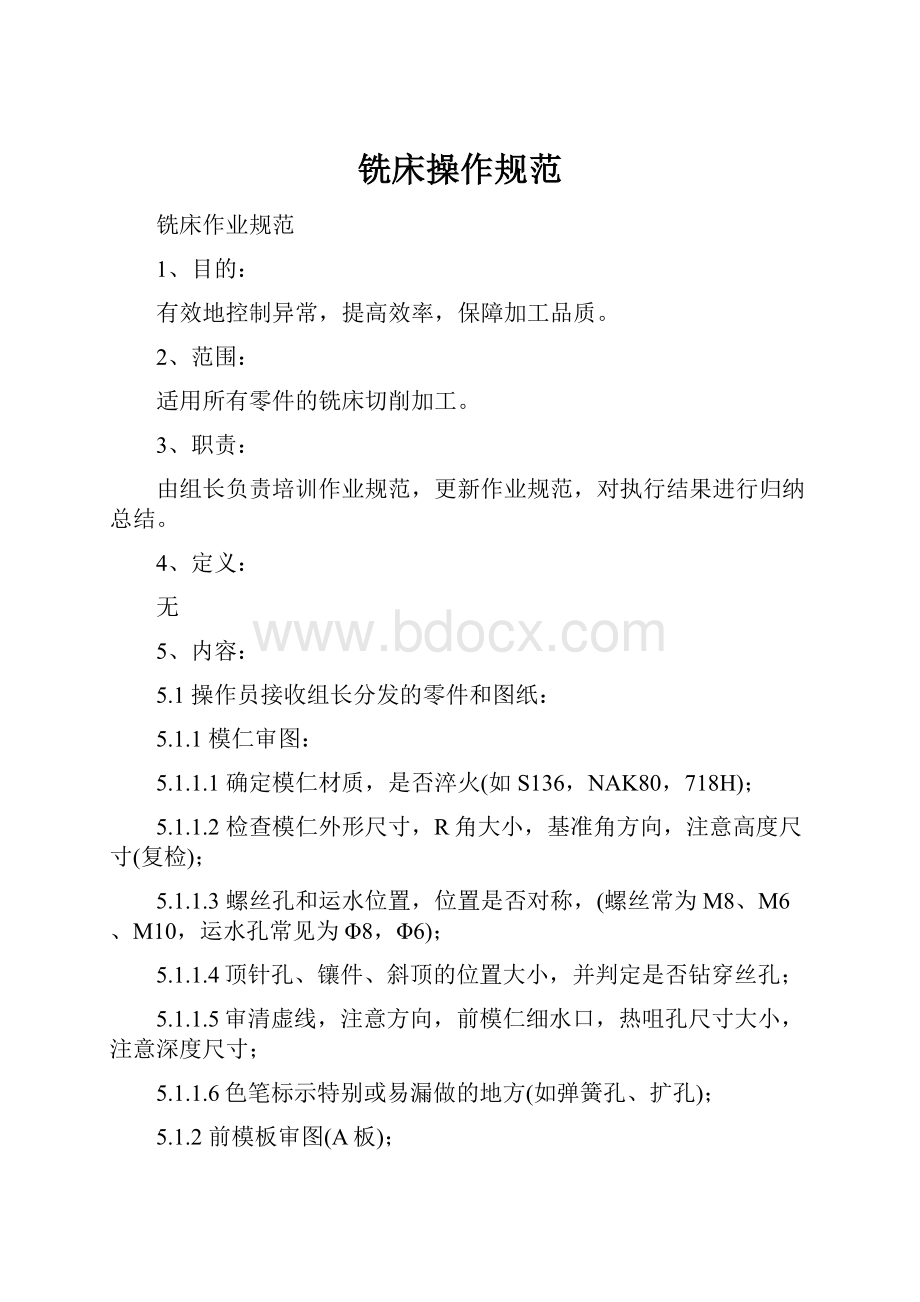
铣床操作规范
铣床作业规范
1、目的:
有效地控制异常,提高效率,保障加工品质。
2、范围:
适用所有零件的铣床切削加工。
3、职责:
由组长负责培训作业规范,更新作业规范,对执行结果进行归纳总结。
4、定义:
无
5、内容:
5.1操作员接收组长分发的零件和图纸:
5.1.1模仁审图:
5.1.1.1确定模仁材质,是否淬火(如S136,NAK80,718H);
5.1.1.2检查模仁外形尺寸,R角大小,基准角方向,注意高度尺寸(复检);
5.1.1.3螺丝孔和运水位置,位置是否对称,(螺丝常为M8、M6、M10,运水孔常见为Φ8,Φ6);
5.1.1.4顶针孔、镶件、斜顶的位置大小,并判定是否钻穿丝孔;
5.1.1.5审清虚线,注意方向,前模仁细水口,热咀孔尺寸大小,注意深度尺寸;
5.1.1.6色笔标示特别或易漏做的地方(如弹簧孔、扩孔);
5.1.2前模板审图(A板);
5.1.2.1确定图纸模号、基准;
5.1.2.2铲基槽深度大小及铲基螺丝孔位置尺寸;
5.1.2.3斜导柱斜度、大小,看清标注位置是正面还是反面的尺寸;
5.1.2.4定位圈大小、公差,应注意其深度常有小数;
5.1.2.5进浇口、流道的尺寸与形状,判定是否由铣床加工;
5.1.3后模板审图(B板);
5.1.3.1确定图纸、模号、基准;
5.1.3.2行位槽深度、大小,应注意三个视图尺寸是否一致;
5.1.3.3运水孔位置、深度,防水圈大小、深度;
5.1.3.4顶针孔、螺丝孔大小、位置尺寸;
5.1.3.5开闭器位置是否与A板一致;
5.1.3.6用色笔标示,特殊的地方;
5.1.4顶针板审图:
5.1.4.1图纸为上、下顶出板,应注意虚实线;
5.1.4.2顶针杯头为分类标注(如:
A类、B类、C类),应看清深度(一般为4mm,常见6mm);
5.1.4.3检查是否有弹力胶,限位螺丝,丝筒针扩孔;
5.1.4.4撑头孔大小及位置,位置是否对称;
5.1.4.5斜顶座位置、方向,一般为反面加工,应特别注意方向;
5.1.5面板审图:
5.1.5.1视孔的大小,初步判定加工方法;
5.1.5.2特别注意台阶的虚实线,是否有排气槽;
5.1.5.3注意前模铲基、斜导柱位置、尺寸、公差;
5.1.5.4拉料针杯头深度,方向;
5.1.6底板审图:
5.1.6.1顶出孔的大小,位置;
5.1.6.2螺丝孔大小,位置是否对称;
5.1.6.3司筒针的位置、尺寸;
5.1.7剥料板:
5.1.7.1注意图纸的正反方向;
5.1.7.2拉针孔的大小,位置是否对称;
5.1.7.3运水孔的大小与位置;
5.2加工前准备内容:
5.2.1根据图纸要求和加工思路选择工具:
5.2.1.1刀具;
5.2.1.2钻咀;
5.2.1.3分中棒;
5.2.1.4卡尺;
5.2.1.5夹具:
批士、码铁、扳手;
5.2.1.6根据个人身高选择垫板;
5.2.1.7选用防护用品如防护镜、防护铁丝网;
5.3选择机床:
5.3.1根据图纸要求和加工要求选择机床;
5.3.1.1粗加工选择10号、11号机床,如:
开框、开料;
5.3.1.2半精加工选择8号、9号机床,如:
规范件、面、底板、顶针板、运水孔、螺丝孔;
5.3.1.3精加工选择2号-7号机床,如:
模仁、镶件的穿线孔、沉头、挂台及模胚A、B板;
5.4检查机床:
5.4.1校正机头;
5.4.1.1将工作台清洁干净;
5.4.1.2放置一块长宽超过(300X300)mm的平板;
5.4.1.3将校表紧固于主轴上;
5.4.1.4校表针接触面板0.2mm处;
5.4.1.5旋转主轴,拧松机头固定螺丝,作如下调整;
a.如平板前方表针显示高于0.2mm,则要顺时针拧动螺丝,反之则逆时针;
b.如平板后方表针显示高于0.2mm,则要逆时针拧动螺丝,反之则顺时针;
c.如平板左方表针显示高于0.2mm,则要逆时针拧动螺丝,反这则顺时针;
d.如平板右方表针显示高于0.2mm,则要顺时针拧动螺丝,反之则逆时针;
5.4.1.6当校表旋转一周后,平板四边都处于0.2mm(±0.01)时,可拧紧机头螺丝,将主轴旋转一周做检查,如表针未动,则机头已校正;
5.4.2检查电子显示器是否完好;
5.4.2.1检查归零功能是否正常;
5.4.2.2检查分中功能是否正常;
5.4.2.3对照刻度摇动机床,目视电子显示器的距离与刻度是否相符;
5.5装夹工件:
5.5.1模仁装夹:
5.5.1.1尺寸小于150mm以内的用批士装夹,大于150mm的用码铁装夹;
5.5.1.2批士装夹可一次两块,也可定位一次一块;
5.5.1.3检查工件的基准面,照图纸方向摆放;
5.5.1.4用批士装夹,模仁高出批士15mm;
5.5.1.5用码铁装夹,垫块与码铁尽量外移,以防阻碍加工,并确定装夹是否牢固;
5.5.2前后模胚(A、B板):
5.5.2.1用两个以上码铁装夹;
5.5.2.2工件基准面照图纸摆放;
5.5.2.3装夹时码铁避开加工位置;
5.5.2.4装夹在机床有效行程之内并确定是否牢固;
5.5.3面板(同5.5.2);
5.5.4顶针板(同5.5.2);
5.5.5铜公装夹:
5.5.5.1用批士装夹;
5.5.5.2装夹时不可敲击;
5.5.5.3不可用力过大;
5.5.6加工模仁R角装夹;
5.5.6.1装夹时按R加工模式选择X轴自动走刀;
5.5.6.2一次可装夹4块同一尺寸的工件;
5.5.6.3装夹时需用G字夹固定;
5.5.7装夹工件的基准面,照图纸方向摆放;
5.5.8工件装夹在铣床的有效行程内;
5.5.9零件Y向尺寸大于150mm的选择码铁装夹,小于150mm的用批士装夹;
5.5.9.1模胚用码铁装夹,左右各压一个。
需加工行位槽的模胚,需三个以上的码铁装夹;
5.5.9.2装夹铜公或铝制工件时,选择不重要位置进行装夹,并注意装夹力度,以免压伤或变形;
5.6工件校表:
5.6.1目视校正:
5.6.1.1装夹于铣床平台的零件,目视机床基准边与零件平面是否平行;
5.6.1.2装夹于批士的零件,目视零件与批士基准面是否平行;
5.6.2校表校正:
5.6.2.1装夹于铣床平面的零件,用码铁轻微固定后,将校表固定于主轴上,移动X或Y轴使表针于零件接触,来回移动机床X或Y轴,视校表显示状况用铜锤敲击零件进行校正;
5.6.2.2装夹于批士的零件,先用校表校平工件顶面的水平,再校平X或Y方向的水平;
5.6.2.3铜公或铝制品零件用胶锤敲打不重要的位置进行校正;
5.6.3工件寻边:
5.6.3.1分中棒用刀具夹头装夹;
5.6.3.2分中棒碰数时低于工件面3-5mm;
5.6.3.3机台转速400-600转/分;
5.6.3.4工件应四面碰数,且每面重复三次;
a.第一次接触工件时,记录显示器的数据,前后左右碰数后进行分中;
b.第二次分中,距离第一次分中数0.05mm时,步进量每次0.01mm,做第二次分中;
c.第三次做记数检查;
5.7模仁加工:
5.7.1加工R角:
5.7.1.1审图(同5.1.1);
5.7.1.2加工前准备内容(同5.2);
5.7.1.3选择机床(同5.3);
5.7.1.4检查机床(同5.4);
5.7.1.5装夹工件(同5.5);
5.7.1.6工件校正(同5.6);
5.7.1.7开如加工;
A.选用R5飞刀加工;
B.对刀:
a.从侧面(b面)对刀,Y轴归零,进刀0.5mm后再归零;
b.从平面(a面)对刀,Z轴归零进刀0.5mm后再归零;
c.Y轴向模仁中心进刀17mm(R12+R5)(变量)后再归零;如图:
5.7.1.8R角程序设计:
(以9#机床为例)
a.进入数显R角设计控制面
b.SIMPLE输入模式2或3;
c.ARC选用YZ;
d.RADIUS输入12(即R角大小);
e.TLDA输入10(为直径);
f.MAXCUT输入0.3(即Z轴每次进刀量);
5.7.1.9机床主轴转速为2220转\分;
5.7.1.10按程序每步\次进刀加工;
5.7.2加工螺丝孔:
5.7.2.1用Φ2.0以上的中心钻打点:
转速2220转\分;
5.7.2.2选择钻头:
牙径
M3
M4
M5
M6
M8
M10
M12
M16
钻径
Φ2.4
Φ3.3
Φ4.3
Φ5.2
Φ6.8
Φ8.7
Φ10.5
Φ14
5.7.2.3孔深为:
15-18mm,加工时限位;
5.7.2.4机床主轴转速M3-M6为1110转\分;
M8-M12为660转\分;
M16为420转\分;
5.7.2.5每加工约4mm深需提起一次机头排屑;
5.7.2.6每提起一次机头加一次冷却液;
5.7.2.7加工要领:
无异声,手感好,排出铁屑为银白色条状;
5.7.2.8完工后倒角,攻牙;
5.7.3加工运水:
5.7.3.1用Φ2.0以上的中心钻打点,转速2220转\分;
5.7.3.2选择钻头钻孔;
5.7.3.3孔深需从模仁底部拿数,加工时限位;
5.7.3.4长水路要先画线并检查,打点;
5.7.3.5孔与孔之间将钻穿时,要减缓加工速度;
5.7.3.6用风枪检测水路是否连通;
5.7.3.7堵水孔径比运水大2MM,深为8-10mm;
5.7.3.8机头转速为660转\分-1110转\分;
5.7.4前模仁:
5.7.4.1加工热咀孔:
a.用Φ2.0以上的中心钻打点,转速2220转\分;
b.选Φ6-Φ8的钻头钻通,转速1110转\分;
c.用16-Φ20的铣刀开粗,转速420转\分;
d.用Φ25.4的倒角铣刀加工到数,深度可+0.5mm,转速为210转\分;
5.7.4.2大镶件穿线孔:
a.用Φ2.0以上的中心钻打点,转速2220转\分;
b.选用Φ2.5-5钻头钻孔,转速1110转分-2220转\分;
c.穿线孔位置靠近镶件边缘3mm-5mm进行加工;
5.7.4.3细水口加工;
a.用Φ2.0的中心钻打点,转速2220转\分;
b.用小于孔径的钻咀开粗;
C.深度及孔径留余量单边0.5mm-1.0mm;
5.7.4.4基准角:
a.选用Φ8-Φ10的铣刀,转速660转\分;
b.按图纸d在相对应的角加工,形状如图;
c.深度为PL面下0.5-0.8mm,长宽为10X10;
5.7.4.5字码槽;
a.选用Φ10的铣刀,转速660转\分;
b.在模仁侧面有空余地方加工;
c.槽长为60-70mm,深度为0.5-0.7mm;
5.7.4.6打字码;
a.选用英文和阿拉伯数字两种字码;
b.按要求打:
模具编号→零件名称→热处理(材质);
如:
PB437→CAV→HRC52℃±2℃(NAK80);
5.7.5后模仁;
5.7.5.1穿线孔;
a.选择小于孔径1.0-2.0mm的钻咀加工,转速为1110-2220转\分;
b.Φ2.5以下的孔由打孔机加工;
c.从正面钻穿线孔;
d.按图纸要求背面逃孔;
5.7.5.2基准角:
a.选用Φ8-Φ10的铣刀,转速660转\分;
b.按图纸d在相对应的角加工,形状如图;
c.深度为PL面下0.5-0.8mm,长宽为10X10;
5.7.5.3字码槽;
a.选用Φ10的铣刀,转速660转\分;
b.在模仁侧面有空余地方加工;
c.槽长为60-70mm,深度为0.5-0.7mm;
5.7.5.4打字码:
a.选用英文和阿拉伯数字两种字码;
b.按要求打:
模具编号→零件名称→热处理(材质);
如:
PB437→COR→HRC46℃±2℃(718H);
5.7.6加工前模胚(A板);
5.7.6.1钻螺丝孔:
(同5.7.2)
5.7.6.2钻运水孔:
a.用Φ2.0以上的中心钻打点,转速2220转\分;
b.选择钻头钻孔;
c.孔深需从模框底拿数,加工时限位;
d.长水路用钻床加工,加工前画线打点并自检;
e.日精模胚水路接头为管牙1\4底孔钻Φ11.8,转速420转\分;
f.其它模胚水路接头为1\2螺牙,底孔钻Φ11.3,转速420转\分;
5.7.7防水圈槽:
5.7.7.1防水圈用成型刀加工,主轴转速在660转\分以内;
5.7.7.2防水圈深度小防水圈厚度的0.7mm;
5.7.7.3防水圈高出部位用铣刀锣平;
5.7.8点胶口;
5.7.8.1用Φ2.0的中心钻打点,转速2220转\分;
5.7.8.2用小于孔径1-2mm的钻咀钻线割孔;
5.7.8.3冷料井加工到数;
5.7.9铲基槽;
5.7.9.1选择大于螺丝孔直径0.5mm-0.8mm的钻咀钻螺丝扩孔;
5.7.9.2开粗:
a.选择Φ10以上的旧铣刀,机台转速660转\分;
b.从模胚面对刀,每次进刀1.5-2mm,及时加冷却液;
c.每加工5mm重新对刀一次;
d.单边留余量1.0mm,深度留0.5mm;
5.7.9.3粗光;
a.选Φ8以上的旧铣刀,机台转速660转\分;
b.每次进刀量0.1-0.2mm;
c.单边余量留0.1mm,深度留0.1mm;
5.7.9.4精光;
a.选用Φ8以上全新铣刀;
b.每次进刀量为0.02-0.03;
c.用风枪冷却;
d.单边留余量0.01-0.015mm,深度到数;
5.7.9.5倒角:
a.用Φ10-12倒角;
5.7.10热咀孔;
5.7.10.1中心钻定位;
5.7.10.2选择12mm的钻咀钻孔,机台转速660转\分;
5.7.10.3用Φ20、Φ25、Φ30的铣刀扩孔;
5.7.10.4用镗刀或唧咀刀加工到数,孔径大0.1mm;
5.7.11热咀定位圈:
5.7.11.1选择小于孔径2mm以上的刀具开粗,深度留0.5mm。
5.7.11.2用铣刀把深度加工到数;
5.7.11.3用平底镗刀加工定位圈的孔径,转速为660转\分;
5.7.11.4孔径公差控制在+0.02mm-0.05mm;
5.7.12斜导柱孔;
5.7.12.1画线后,用校表校正机头角度;
5.7.12.2用中心钻对好中心点;
5.7.12.3用铣刀踩出一平位,打中心钻;
5.7.12.4选择小于孔径0.4的钻咀钻底孔;
5.7.12.5用与孔径一样大小的钻咀或铣刀加工,速度控制135转\分;
5.7.12.6加工5mm后停机试孔;
5.7.12.7踩斜导柱杯头,深度+0.5mm;
5.7.13开闭器孔;
5.7.13.1中心钻定位;
5.7.13.2选择10mm的钻咀钻孔,深度深于要求尺寸0.5mm-1mm;
5.7.13.3用小于开闭器1mm刀具扩孔;
5.7.13.4选择与开闭器相同的铣刀加工,速度为80-270转\分;
5.7.13.5加工5mm提刀试孔;
5.7.13.6倒角;
5.7.14后模胚(B板)
5.7.14.1钻螺丝孔(同5.7.2);
5.7.14.2钻运水孔;(同5.7.3);
5.7.15行位槽;
5.7.15.1画线后飞刀粗加工,转速2220转\分以上;
5.7.15.2每次进刀量为1.5-2.0mm,单边留余量1.0mm,深度余量0.3mm;。
5.7.15.3用Φ16的旧铣刀中粗;
5.7.15.4每次进刀量为0.3-0.4mm,单边余量留0.2mm深度余量0.2mm;
5.7.15.5用卡尺检查尺寸和分中粗度;
5.7.15.6用Φ10的半新铣刀粗精,机台转速为660转\分;
5.7.15.7每次进刀量0.03-0.04mm,单边余量留0.05mm,深度为0.05mm;
5.7.15.8用Φ10的新铣刀精光,主轴转速为420转\分;
5.7.15.9先光侧面,单边留余量0.01mm,底部到数;
5.7.15.10油板深度到数,长宽单边+0.05mm,转速为660转\分;
5.7.15.11倒角;
5.7.16顶针扩孔;
5.7.16.1中心钻定位;
5.7.16.2选择大于顶针直径0.5mm的钻咀钻孔;
5.7.16.3每加工5mm深度提刀排屑一次,添加冷却水;
5.7.16.4扩孔用钻咀倒角;
5.7.17斜顶导向块凹槽;
5.7.17.1选择10-12mm的旧铣刀粗加工,转速660-800\分;
5.7.17.2侧边余量留0.2mm,深度余量留0.2mm;
5.7.17.3选择Φ8-Φ10mm半新刀精加工到数;
5.7.17.4实际尺寸大于图纸尺寸单边0.03mm;
5.7.17.5倒角;
5.7.18防水圈槽;(同5.7.7)
5.7.19顶针板:
5.7.19.1加工顶针扩孔;
a.用复针套入B板;
b.选用两块等高的垫铁将顶出板垫高;
c.用B板坐标加工顶针扩孔;
d.选用大于顶针直径0.5mm钻咀扩孔;
e.倒角;
5.7.19.2加工顶针扩孔沉头;
a.将顶针板码实在工作台面,底面贴实台面,不加垫铁;
b.选择合适刀径的半新立铣刀,端面为平底刀加工;
c.转速设为660转\分;
d.Z轴对刀(以刀端面与工作台接触为准),归零,锁紧摇臂;
e.以Z轴进刀,连续进刀至3.5mm,减缓进给量,最后0.05mm;
f.顶针沉头深度大于顶针杯头厚度0.01mm;
5.7.19.3斜顶座槽;
a.上下出板一起加工螺丝扩孔;
b.选择旧铣刀开粗,侧边余量0.2mm,深度余量留0.1mm;
c.选择半新铣刀精加工,外形尺寸大于图纸尺寸单边0.03mm,深度尺寸+0.01mm;
5.7.19.4撑头孔;
a.中心钻定位,选择12mm的钻咀钻孔;
b.上下顶出一起加工;
c.选择20mm的钻咀扩孔;
d.用唧咀刀直接加工到数;
e.镗刀倒角,四面都需倒角;
5.7.19.5斜顶座耐磨板凹槽;
a.选择6mm-8mm的旧铣刀开粗,留余量0.2mm;
b.选择Φ6mm的半新铣刀精加工到数,外形尺寸大于图纸尺寸单边+0.03mm,深度尺寸+0.01mm;
5.7.20加工面板:
5.7.20.1定位圈;
A.中心钻定位;
B.选择钻咀钻孔,用分段钻圆去除废料;
a.进入分段圆设计控制面;
b.DIA输入孔直径,如Φ70;
c.NUMBER,输入段数;
d.STANG输入起始角度;
e.EDANC输入终止角度;
C.选择镗刀器镗孔至要求尺寸;
D.用镗刀器加工定位圈台阶直径到数;
E.用锣刀锣台阶端面到数;
5.7.21底板:
5.7.21.1顶出孔;
a.中心钻定位;
b.选择12mm钻咀通孔;
c.选择25mm钻咀扩孔;
d.选择唧咀刀加工至要求尺寸;
5.7.21.2撑头螺丝孔;
a.按照图纸要求钻孔,每次加工深度5mm需提起一次摇臂排屑,添加冷却液;
b.螺丝扩孔孔径大于螺丝直径0.5mm-0.8mm;
c.螺丝杯头深度大于杯头尺寸0.5mm;
d.螺丝孔需倒角;
5.7.21.3司筒针压块槽;
a.选择Φ6mm旧刀开粗,单边余量留0.2mm;
b.选择Φ6mm半新刀精加工至要求尺寸;
c.选择钻咀钻螺丝孔;
5.7.21.4司筒针孔;
a.选择大于司筒针直径1mm的钻咀钻孔;
b.选择钻咀倒角;
5.8毛料加工
5.8.1用飞刀加工,进刀量控制在0.8mm以内;
5.8.2需加硬工件的余量为0.8-1.0(双边),不需加硬的余量为0.4-0.5(双边);
5.8.3飞刀转速需1000转/分以上;
5.8.4直角误差用角尺目视校正;
6、完工处理:
6.1自检;
6.2图纸和工件放置于待检区,通知巡检;
6.3清洁机台,将工件送至下一工站。
7、相关文件:
7.1《模具零件图》;
7.2《钢件余量规范》;
7.3《模具工艺卡》。
8、相关表格/记录:
8.1《零件加工控制表》;
8.2《异常分析报告》。
8.3《零件\铜公交接表》;