数控机床润滑系统的自动控制毕业论文.docx
《数控机床润滑系统的自动控制毕业论文.docx》由会员分享,可在线阅读,更多相关《数控机床润滑系统的自动控制毕业论文.docx(12页珍藏版)》请在冰豆网上搜索。
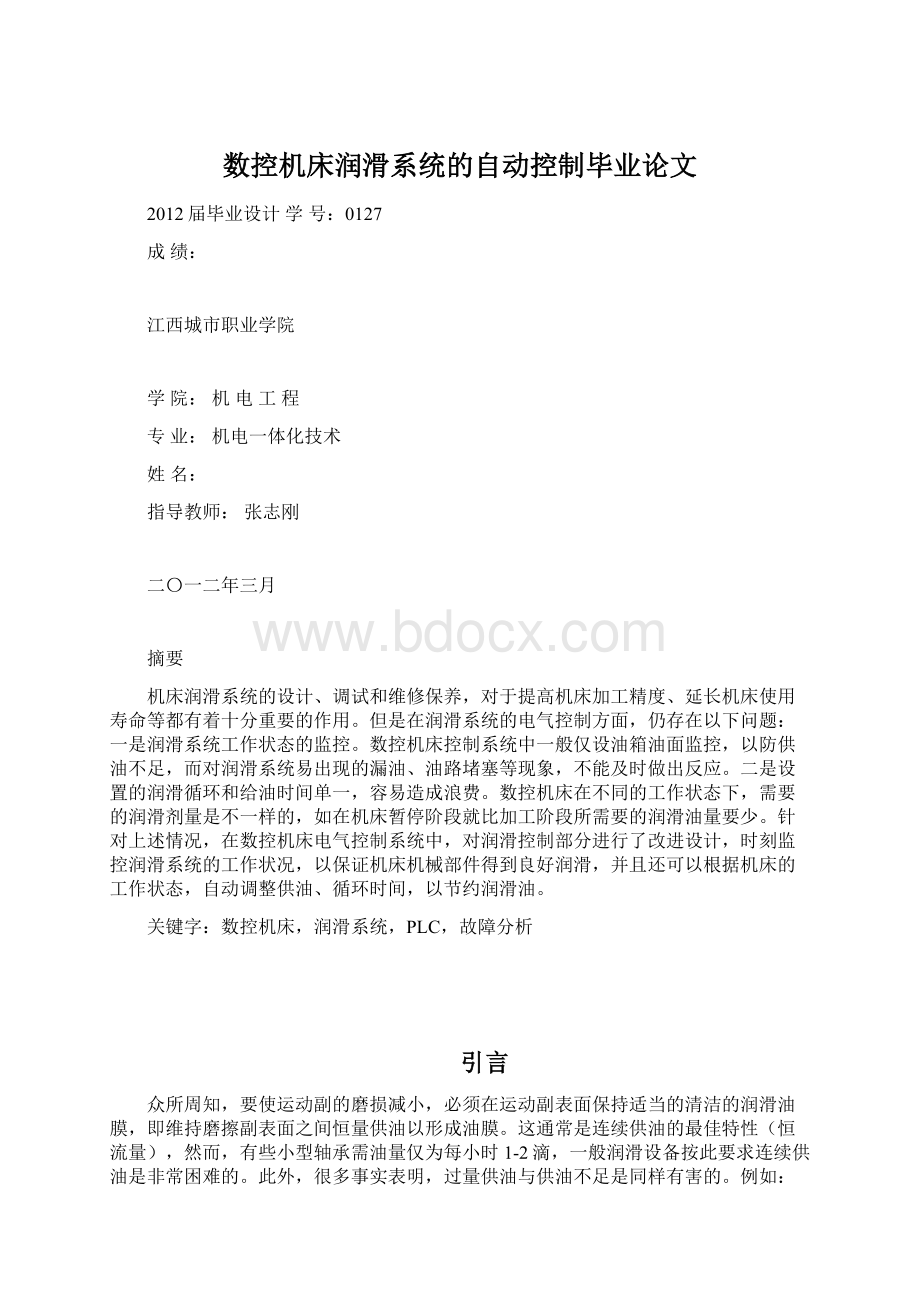
数控机床润滑系统的自动控制毕业论文
2012届毕业设计学号:
0127
成绩:
江西城市职业学院
学院:
机电工程
专业:
机电一体化技术
姓名:
指导教师:
张志刚
二〇一二年三月
摘要
机床润滑系统的设计、调试和维修保养,对于提高机床加工精度、延长机床使用寿命等都有着十分重要的作用。
但是在润滑系统的电气控制方面,仍存在以下问题:
一是润滑系统工作状态的监控。
数控机床控制系统中一般仅设油箱油面监控,以防供油不足,而对润滑系统易出现的漏油、油路堵塞等现象,不能及时做出反应。
二是设置的润滑循环和给油时间单一,容易造成浪费。
数控机床在不同的工作状态下,需要的润滑剂量是不一样的,如在机床暂停阶段就比加工阶段所需要的润滑油量要少。
针对上述情况,在数控机床电气控制系统中,对润滑控制部分进行了改进设计,时刻监控润滑系统的工作状况,以保证机床机械部件得到良好润滑,并且还可以根据机床的工作状态,自动调整供油、循环时间,以节约润滑油。
关键字:
数控机床,润滑系统,PLC,故障分析
引言
众所周知,要使运动副的磨损减小,必须在运动副表面保持适当的清洁的润滑油膜,即维持磨擦副表面之间恒量供油以形成油膜。
这通常是连续供油的最佳特性(恒流量),然而,有些小型轴承需油量仅为每小时1-2滴,一般润滑设备按此要求连续供油是非常困难的。
此外,很多事实表明,过量供油与供油不足是同样有害的。
例如:
对一些轴承在过量供油时会产生附加热量、污染和浪费。
大量实验证明,周期定量供油,既可使油膜不被损坏又不会产生污染和浪费,是一种非常好的润滑方式。
因此当连续供油成为不合适时可采用经济的周期供油系统来实现。
该系统使定量的润滑油按预定的周期时间对各润滑点供油,使运动副均适合采用周期润滑系统来润滑
机床润滑系统在机床整机中占有十分重要的位置,其设计、调试和维修保养,对于提高机床加工精度、延长机床使用寿命等都有着十分重要的作用。
现代机床导轨、丝杆等滑动副的润滑,基本上都是采用集中润滑系统。
集中润滑系统是由一个液压泵提供一定排量、一定压力的润滑油,为系统中所有的主、次油路上的分流器供油,而由分流器将油按所需油量分配到各润滑点:
同时,由控制器完成润滑时间、次数的监控和故障报警以及停机等功能,以实现自动润滑的目的。
集中润滑系统的特点是定时、定量、准确、效率高,使用方便可靠,有利于提高机器寿命,保障使用性能。
第2章数控机床的系统构成
数控机床一般是由数控装置(CNC)、数控辅助部件、输入输出设备、伺服单元、驱动装置(或称执行机构)、可编程控制器(PLC)及电气控制装置、机床本体及测量装置组成的,如图2-1所示
图2-1数控机床的硬件构成
第3章润滑的分类
集中润滑系统按使用的润滑元件可分为阻尼式润滑系统、递进式润滑系统和容积式润滑系统。
3.1单线阻尼式润滑系统
此系统适合于机床润滑点需油量相对较少,并需周期供油的场合。
它是利用阻尼式分配器,把泵打出的油按一定比例分配到润滑点。
一般用于循环系统,也可以用于开放系统,可通过时间的控制,以控制润滑点的油量。
该润滑系统非常灵活,多一个润滑点或少一个都可以,并可由用户安装,且当某一点发生阻塞时,不影响其他点的使用,故应用十分广泛。
图3-1所示为单线阻尼式润滑系统。
3.2递进式润滑系
递进式润滑系统主要由泵站、递进片式分流器组成,并可附有控制装置加以监控。
其特点是能对任一润滑点的堵塞进行报警并终止运行,以保护设备;定量准确、压力高,不但可以使用稀油,而且还适用于使用油脂润滑的情况。
润滑点可达100个,压力可达21MPa。
递进式分流器由一块底板、一块端板及最少三块中间板组成。
一组阀最多可有8块中间板,可润滑18个点。
其工作原理是由中间板中的柱塞从一定位置起依次动作供油,若某一点产生堵塞,则下一个出油口就不会动作,因而整个分流器停止供油。
堵塞指示器可以指示堵塞位置,便于维修。
图3-2所示为递进式润滑系统。
3.3容积式润滑系统
该系统以定量阀为分配器向润滑点供油,在系统中配有压力继电器,使得系统油压达到预定值后发讯,使电动机延时停止,润滑油从定量分配器供给,系统通过换向阀卸荷,并保持一个最低压力,使定量阀分配器补充润滑油,电动机再次起动,重复这一过程,直至达到规定润滑时间。
该系统压力一般在50MPa以下,润滑点可达几百个,其应用范围广、性能可靠,但不能作为连续润滑系统。
图3-3容积式润滑系统
第4章润滑系统的控制原理
机床润滑系统的控制分为两部分:
电器控制和PLC自动控制。
4.1电气控制原理
润滑系统电器控制图如图4-1,通过控制交流接触器KM1来控制润滑电机主电源。
经过PLC的自动控制来实现自动控制。
图4-1润滑系统电器控制原理图
4.2自动控制原理
如图4-2,为润滑系统自动控制流程图。
当系统准备好之后,CNC发出信号,使得润滑系统开始工作,首次润滑15s后,电机停止工作
图4-2,为润滑系统自动控制流程图
当压力开关SP2因压力降低而接通时,开始计时30min,计时完成后,当压力开关SP2断开,润滑电动机再次工作20S,并循环工作。
QF4为电动机过载保护开关,SL为润滑油检测开关,当电动机过载或润滑油不足时则使系统发出报警信号。
第5章数控机床润滑系统的PLC控制
在数控系统中,大部分的自动控制都是通过PLC来实现的,润滑系统的控制也一样,通过PLC程序控制电机的工作。
本节以F21V-14为例,讲述一下润滑系统PLC的控制。
5.1润滑PLC控制原理
如图5-1,首先通过两个相互作用的时间继电器(T),实现润滑工作时的间隙工作;再使用PLC准备好信号,使XO为1,开始首次润滑;首次润滑结束后,当SP开关闭合时,中间继电器M1开始工作,使得润滑系统再次工作;20s后使得时间继电器T2为1,当SP开关断开时,中间继电器M0开始工作,使得时间继电器T3工作,延时30min后时间继电器T3为1,中间继电器M1停止工作,所有的延时器都复位,当SP开关再次闭合时,中间继电器M1再次工作,由此实现了润滑系统的周期动作。
然后再通过SL,QF4开关实现润滑系统的报警。
并且使用X3实现润滑系统的手动控制。
图5-1润滑系统PLC控制梯形图
5.2润滑系统I/O地址分配
如图5-2,X0为PLC准备好信号,X1为SP压力检测信号开关,X2为液面检测信号开关,X3为FR电动机过载报警信号开关。
Y1为正常运行信号,Y2为润滑油管道泄漏报警信号.Y3润滑油管道堵塞报警信号,Y4为润滑油油量不足信号。
图5-2润滑系统PLC外部接线图
第6章润滑系统故障分析
6.1润滑系统工作状态的监控
润滑系统中除了因油料消耗,油箱油过少而使润滑系统供油不足外,常见的故障还有油泵失效、供油管路堵塞、分流器工作不正常、漏油严重等。
因此,在润滑系统中设置了下述检测装置,用于对润滑泵的工作状态实施监控,避免机床在缺油状态下工作,影响机床性能和使用寿命。
6.1.1过载检测在润滑泵的供电回路中使用过载保护元件,并将其热过载触点作为PLC系统的输入信号,一旦润滑泵出现过载,PLC系统即可检测到并加以处理,使机床立即停止运行。
6.1.2油面检测润滑油为消耗品,因此机床工作一段时间后,润滑泵油箱内润滑油会逐渐减少。
如果操作人员没有及时添加,当油箱内润滑油到达最低油位,油面检测开关随即动作,并将此信号传送给PLC系统进行处理。
6.1.3压力检测机床采用递进式集中润滑系统,只要系统工作正常,每个润滑点都能保证得到预定的润滑剂。
一旦润滑泵本身工作不正常、失效,或者是供油回路中有一处出现供油管路堵塞、漏油等情况,系统中的压力就会显现异常。
根据这个特点,设计时在润滑泵出口处安装压力检测开关,并将此开关信号输入PLC系统,在每次润滑泵工作后,检查系统内的压力,一旦发现异常则立即停止机床工作,并产生报警信号。
6.2润滑时间及润滑次数的控制
为了要使机床运动副的磨损减小,必须在运动副表面保持适当的清洁的润滑油膜,即维持摩擦表面之间恒量供油以形成油膜。
但是数控机床运动副需要的润滑油量不是太多时,采用连续供油方式既不经济也不合理。
因为过量供油与供油不足同样是有害的、会产生附加热量、污染和浪费。
因此,润滑系统均采用定期、定量的周期工作方式。
集中润滑系统本身可以配置微处理器,专门用于设定润滑泵停止的时间和每次供油时间,以控制润滑泵间隙工作,设计人员往往也借此来简化自己的PLC程序。
但机床在不同的工作状态下,如刚刚通电初始工作阶段、加工运行和因调整、检测工件而使机床暂停运行时,机床对润滑油的需求量各不相同。
在配置FANUC数控系统的机床中,通常通过控制润滑泵工作的时间来调节提供的润滑油量,但是,习惯考虑的是润滑系统在机床加工运行状态下的供油方式,而没有顾及其它工作状态,这样,当机床处于其它工作状态时,润滑系统所提供的润滑油量要么不够,要么过多。
机床导轨需要的润滑油量近似可用下面公式计算:
(长度+移动行程)×宽度×K。
从公式中可以看出,机床导轨需要的润滑油量与该导轨上的轴的移动距离有关。
欧美生产的数控系统大多以行程量作为依据,来控制润滑泵工作,间隙供油,并在系统中提供了相应的参数,便于机床制造商通过PLC程序对润滑泵进行电气控制。
而在FANUC0i系统中没有类似的控制方法,为了能在配置FANUC0i的数控机床上,采用近似的供油方式控制润滑泵工作,我们改进了润滑控制部分的电气设计,让控制系统能根据机床的具体工作情况自动调整润滑泵工作频率和每次的工作时间,在机床暂停时适当减少供油量,而机床初始工作时适当增加。
现将润滑泵的工作状态分成三类,分别设置润滑泵工作时间和频率。
1)开机初始阶段机床开机,润滑泵即刻开始工作,连续供油一段时间,此时润滑泵工作的时间T1比正常状态下的要长,以便在短时间内提供足够润滑油,使机床导轨上迅速形成一层油膜。
润滑泵运行时间由PLC程序中的TMRB指令设定。
与TMR指令不同,由TMRB设定的时间,用户不能随意修改调整。
2)加工运行阶段机床开机以后,经过空载运行预热后,进入稳定工作状态。
此后,控制系统控制润滑泵间歇工作,以保证机床导轨能够得到定期、定量的润滑。
润滑泵每次工作的时间和其停止的时间由PLC程序中的TMR指令设定。
TMR设定的时间参数,用户可以在PLC数据窗口中根据需要适当调整。
3)暂停阶段工件待加工或加工完毕时,机床往往处于暂停工作状态,润滑油的需求量相应减少,因此,需要及时调整控制方式,适当延长润滑泵停止工作的时间,以减少其工作频率,从而减少油品消耗。
实现的关键是机床处于暂停状态时,系统如何获知。
FANUC0i数控系统中提供了信号MVX(F102.0)、MVY(F102.1)、MVZ(F102.3),用于反映机床各轴的移动状态。
如果该信号状态为“0”,表明相应机床轴静止不动,如果所有移动轴均静止不动,则表明机床此时处于暂停工作状态。
所以,只要上述所有信号状态都为“0”,通过设计,PLC程序自动改变润滑泵工作及停止时间。
此时,润滑泵工作的时间T2和停止的时间T3均使用TMRB指令设定,同样,用户不可以随意修改这两个时间参数。
6.3润滑报警信号的处理
6.3.1压力异常数控机床中润滑系统为间歇供油工作方式。
因此,润滑系统中的压力采用定期检查方式,即在润滑泵每次工作以后检查。
如果出现故障,如漏油、油泵失效、油路堵塞,润滑系统内的压力就会突然下降或升高,此时应立即强制机床停止运行,进行检查,以免事态扩大。
6.3.2油面过低以往习惯的处理方法是将“油面过低”信号与“压力异常”报警信号归为一类,作为紧急停止信号。
一旦PLC系统接收到上述信号,机