汽轮机设备选型原则.docx
《汽轮机设备选型原则.docx》由会员分享,可在线阅读,更多相关《汽轮机设备选型原则.docx(13页珍藏版)》请在冰豆网上搜索。
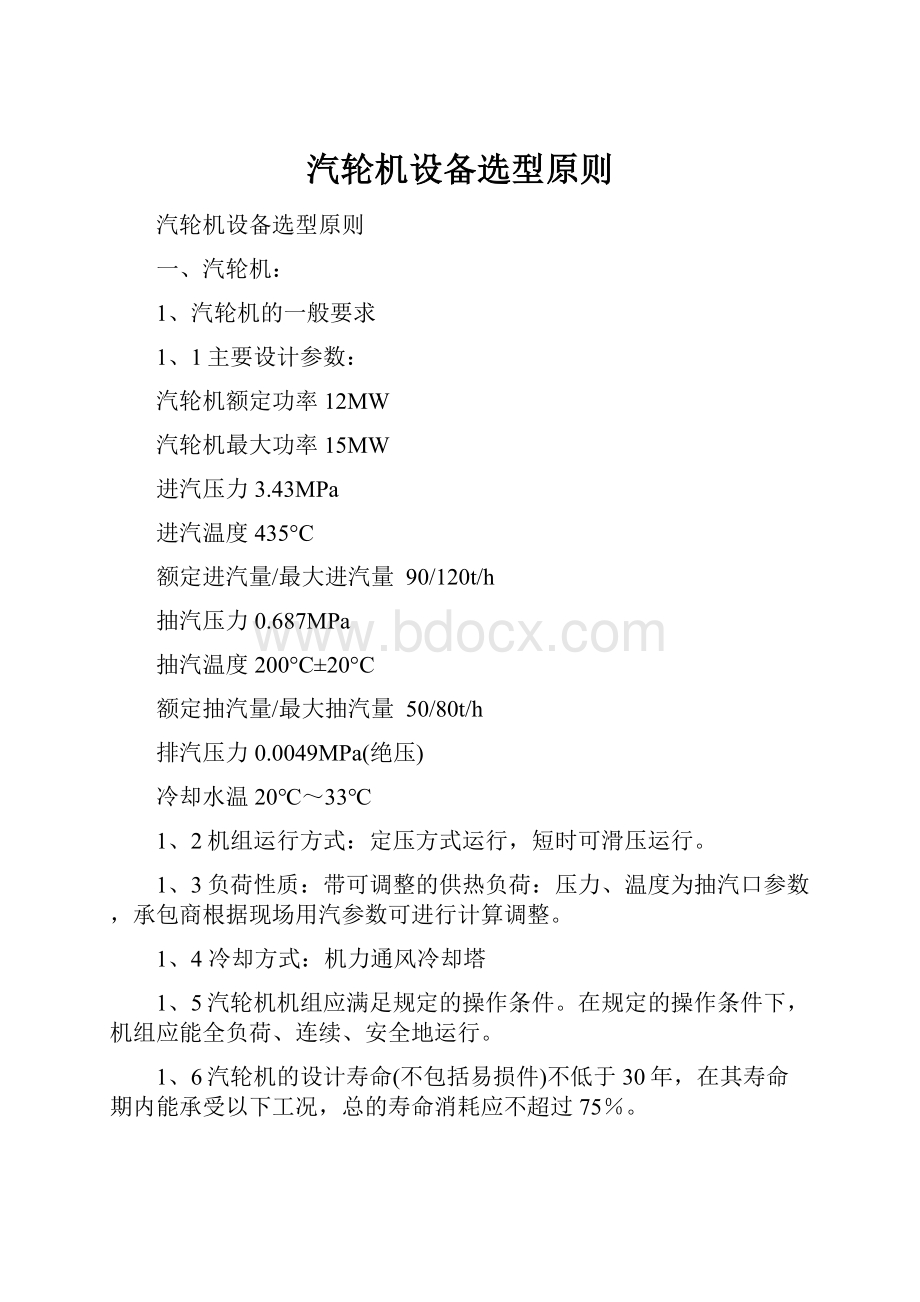
汽轮机设备选型原则
汽轮机设备选型原则
一、汽轮机:
1、汽轮机的一般要求
1、1主要设计参数:
汽轮机额定功率12MW
汽轮机最大功率15MW
进汽压力3.43MPa
进汽温度435°C
额定进汽量/最大进汽量90/120t/h
抽汽压力0.687MPa
抽汽温度200°C±20°C
额定抽汽量/最大抽汽量50/80t/h
排汽压力0.0049MPa(绝压)
冷却水温20℃~33℃
1、2机组运行方式:
定压方式运行,短时可滑压运行。
1、3负荷性质:
带可调整的供热负荷:
压力、温度为抽汽口参数,承包商根据现场用汽参数可进行计算调整。
1、4冷却方式:
机力通风冷却塔
1、5汽轮机机组应满足规定的操作条件。
在规定的操作条件下,机组应能全负荷、连续、安全地运行。
1、6汽轮机的设计寿命(不包括易损件)不低于30年,在其寿命期内能承受以下工况,总的寿命消耗应不超过75%。
1、7汽轮机及所有附属设备应是成熟的、先进的,并具有制造类似容量机组、运行成功的经验。
不得使用试验性的设计和部件。
1、8机组的设计应充分考虑到可能意外发生的超速、进冷汽、冷水、着火和突然振动。
防止汽机进水的规定按ASME标准执行。
1、9机组配汽方式为喷嘴调节,其运行方式为定压运行,短时可滑压运行。
1、10汽轮机进排汽及抽汽管口上可以承受的外力和外力矩至少应为按NEMASM23计算出的数值的1.85倍。
1、11所有与买方交接处的接管和螺栓应采用公制螺纹。
1、12轴封应采用可更换的迷宫密封以减少蒸汽泄漏量,优先选用静止式易更换的迷宫密封。
1、13转子的第一临界转速至少应为其最大连续转速120%。
1、14整个机组应进行完整的扭振分析,其共振频率至少应低于操作转速10%或高于脱扣转速10%。
1、15材料:
所使用的材料应是新的,所有承压部件均为钢制。
所有承压部件不得进行补焊。
主要补焊焊缝焊后需热处理。
1、16低压缸与凝结器联接方式为弹性连接。
2、汽轮机转子及叶片
2、1汽轮机设计允许不揭缸进行转子的动平衡,即具有不揭缸在转子上配置平衡重块的条件,并设有调整危急保安器动作转速的手孔。
2、2叶片的设计应是成熟高效的,使叶片在允许的频率变化范围内不致产生共振。
2、3低压末级及次末级叶片应具有必要的防水蚀措施。
2、4应使叶根安装尺寸十分准确,具有良好互换性,以便顺利更换备品叶片。
2、5叶片组应有防止围带断裂的措施。
2、6发电机与汽轮机连接的靠背轮螺栓能承受因电力系统故障发生振荡或扭振的机械应力而不发生折断或变形。
2、7汽轮机转子应为不带中心孔结构,汽轮机转子应为整锻转子。
3、汽缸
3、1汽缸的设计应能使汽轮机在起动、带负荷、连续稳定运行及冷却过程中,因温度梯度造成的变形最小,能始终保持正确的同心度。
3、2汽缸进汽部分及喷嘴室设计能确保运行稳定、振动小。
3、3汽缸上的压力、温度测点必须齐全,位置正确,符合运行、维护、集中控制和试验的要求。
3、4汽缸端部汽封及隔板汽封有适当的弹性和推挡间隙,当转子与汽封偶有少许碰触时,可不致损伤转子或导致大轴弯曲。
3、5汽缸必须具有足够的强度和刚度,确保在任何运行工况下都不得发生跑偏、变形等现象。
4、轴承及轴承座
4、1主轴承的型式应确保不出现油膜振荡,各轴承的设计失稳转速应避开额定转速25%以上,并具有良好的抗干扰能力。
4、2检修时不需要揭开汽缸和转子,就应能够把各轴承方便地取出和更换。
4、3主轴承应是水平中分面的,不需吊转子就能够在水平、垂直方向进行调整,同时应是自对中心型的。
4、4轴承箱结构必须有足够的强度及刚度,在任何运行工况下均不得发生变形及前倾等现象。
台板与轴承箱之间应采用润滑好且不易失效的材料,卖方说明所选用的材料特性。
5主汽门、调速汽门
5、1主汽门、调速汽门应严密不漏,其强度和严密性应能承受在主蒸汽管道上做1.5倍设计压力的水压试验。
5、2主汽门、调速汽门能在汽机运行中进行遥控顺序试验,还具备检修后能够进行单独开闭试验的性能。
要求主汽门及调速汽门的关闭时间应小于0.15S。
6油系统
6、1提供一套成熟的供油系统。
满足机组的在起动、停机、正常运行和事故工况下,满足汽轮发电机组所有轴承的用油量。
7、盘车装置
7、1盘车装置应是自动啮合型的,能使汽轮发电机组转子从静止状态转动起来,投入时不应发生撞击。
2)盘车装置的设计应能做到自动退出而不发生撞击,且不再自行投入。
8、轴封供汽系统
8、1轴封供汽系统是自动的并具有汽封压力、温度自动调整控制功能,符合防止汽轮机进水进冷气等而损坏汽轮机的措施。
9、汽轮机疏水和排汽系统
9、1疏水系统的设计应能排出所有设备包括管道和阀门内的凝结水。
系统还应使停用设备、管道、阀门保持在运行温度状态。
10、保护装置
10、1汽轮机必须设有数量足够的、十分安全的成熟可靠的危急保安系统,防止超速。
10、2危急保安系统的跳闸系统有联锁保护,防止汽轮机突然再进汽。
10、3汽轮机组分别在单元控制室操作台上及汽机就地设置手动紧急停机操作装置。
11、调速系统
调节系统采用数字电液调节系统(简称DEH),它由505E数字控制器、阀位控制器、电液转换器供油系统、错油门、油动机、高压调速汽门及低压旋转隔板组成。
DEH系统将比一般液压调节系统控制精度高,自动化水平大大提高,热负荷自整性也高,它能实现升速(自动或手动)、配合电气并网、负荷控制(阀位控制或功频控制)、抽气热负荷控制及其它辅助控制,并与DCS通迅,控制参数在线调整和超速保护功能等。
能使汽轮机适应各种工况并长期安全运行。
抽汽式汽轮机既可作纯冷凝运行也可作抽汽方式运行。
当不带抽汽按纯冷凝运行时,可以不投旋转隔板油动机,让旋转隔板全开。
凝结器选型原则
1、技术参数
冷却面积1000m2
冷却水量3200~3600t/h
水侧设计压力0.6MPa
蒸汽压力0.0049MPa(绝压)
蒸汽流量40t/h
冷却水温20℃~33℃
2、结构形式:
单壳体、双流程二道制表面式、采用全焊接结构。
3、与汽轮机的连接形式:
弹性连接
4、冷却水管材质:
HSn70-1A或不锈钢
5、一般要求
1)凝汽器应为双流程式,水室设有分隔板,循环水能通过一侧的进出口,凝汽器可单侧运行,凝汽器单侧运行时,循环水入口温度为33℃时,汽机能达到75%额定负荷。
2)凝汽器设计考虑承受最大工作压力,汽机厂提供水室底部承压保证值。
3)凝汽器的设计使循环冷却水平均分配到所有的换热管子之中。
4)对于凝汽器的防腐采用涂覆盖层或阴极保护,
6结构要求
1)壳体
a)凝汽器壳体采用焊接钢结构,其强度和刚度能承受管道的转移荷载和设计压力,防止汽轮机传递来的振动造成冲击和共振。
c)为防止高速、高温气流冲击凝汽器管和内部构件,使流量分配装置和挡板具有足够的强度。
d)壳体上部设人孔门,用于检查低压加热器和抽汽管。
在凝汽器上部人孔门外,还有格栅平台和扶梯。
e)壳体上留有各汽、水管道的接管。
2)排汽颈部
a)排汽颈部有膨胀节以吸收来自任何方向的位移。
b)开设必要的孔洞,以便安装设在凝汽器内的设备及管道。
3)水室
a)水室管板采用碳钢板。
b)水室内部凡接触到循环水的材料具有抗腐蚀能力。
c)每个水室设置供排气和排水用的接口。
4)热井
a)热井出水口设有防涡流装置,并在该处设置滤网。
b)热井放水口管道带有水封隔离门,该管能在1小时内排出正常水位下的全部凝结水。
c)热井内部用档板分隔开,并配有接头以便测量水室内管束的导电度,还配有检漏装置以检测凝汽器管子是否损坏。
泵的选型原则
1、给水泵
1、1进水温度:
104°C
1、2流量:
90t/h
1、3扬程:
800m
1、4效率:
1、5必要汽蚀余量:
1、6结构形式:
卧式、多级阶段式高压给水泵
1、7泵的吸入和吐出管方位要求垂直向上
1、8给水泵无需暖泵即可冷态启动带至满负荷
1、9泵轴锻钢并有较高精度,同轴度小于0.02mm
1、10径向轴承是自对中心型,平衡盘100%平衡轴向力
1、11密封形式:
快装式机械密封
1、12性能曲线:
(流量—扬程)从最大运行点到出口关闭点的变化应当平缓,水泵出口扬程升高不高于设计点总扬程的30%
1、13给水泵最小流量不超过设计流量的28%。
1、14当多台给水泵并列运行时,在正常运行到最小流量范围内,各台水泵分担的负荷差异限制在5%以内。
1、15给水泵的设计寿命不小于30年,大修周期为4年
1、16给水泵采用可拆卸式的抽屉式进口滤网
1、17机械密封室内的水温应低于该室内水压下的饱和温度,并留有足够的余量,以避免密封面因水汽化造成干磨而损坏。
1、18轴封处有可更换的轴套,以保护泵轴。
1、19采用滑动轴承、稀油润滑。
用油环进行自润滑,循环水冷却。
1、20泵通过弹性联轴器同电机相连。
1、20材质要求
零件名称
前段、中段、后段
叶轮
叶轮挡套、密封环、导叶套
导叶、叶轮、轴套
平衡板、平衡盘、平衡套
材料
优质碳素钢
不锈钢
不锈钢
优质碳素钢
不锈钢
2、凝结水泵
2、1流量
2、2扬程
2、3必要的汽蚀余量
2、4结构形式:
卧式单级悬臂式离心泵
2、5泵的主要材料
零件名称
泵体、泵盖、托架
叶轮
诱导轮
轴
轴套
辅助轴承
材料
HT20-40
硅黄铜80-3
硅黄铜80-3或25钢
40Cr
3Cr13
磷青铜
13—0.5
2、6卖方应保证提供高效、节能、低噪音的凝结水泵是技术先进、经济合理、成熟可靠的产品,并具有较高的灵活性,既能够满足主机运行方式的需要,也能适应启停与变负荷的要求。
2、7水泵的特性曲线
(1)水泵的流量与扬程的关系曲线是无驼峰的运行稳定曲线。
水泵能在选型工况下长期连续运行,并作为泵的最大设计点。
(2)水泵的流量、扬程、效率在正常运行工况下(计算工况)偏差值应符合GB3216的规定。
2、8在任何允许运行工况下均保证水泵不会发生汽蚀。
2、9泵的转子及其主要的旋转部件都进行静平衡和动平衡试验。
静平衡精度不低于GB9239中的G6.3级,动平衡精度不低于GB9239中的G2.5级。
泵的振动应在无汽蚀运转条件下测量,轴承处的振动值符合JB/T8097的规定。
2、10噪声控制标准:
距泵体外壁1米,距地面高(泵高+1)/2米处的噪声不大于85dB(A)。
2、11密封形式:
机械密封
2、12泵通过弹性连轴器有电机驱动,
2、13轴封处具有可更换的轴套。
2、14泵体装入托架检查E面对轴心跳动不大于0.15毫米。
2、15诱导轮装配检查外圆与泵盖间隙不得小于0.1毫米。
2、16联轴器应配置具有封闭端板而可拆卸的刚性保护罩。
2、17泵的使用寿命不少于30年(不包括易损件),易损件寿命大于8000小时。
3、循环水泵
3、1流量
3、2扬程
3、3必要的汽蚀余量
3、4结构形式:
卧式单级双吸离心泵
3、5一次升压直流循环冷却。
3、6泵从关闭点到最大工作点的流量与扬程的特性曲线平缓。
3、7水泵外壳1m出的噪声不大于85dB(A)
3、8封形式:
机械密封
3、9要部件材质:
零件名称
泵体、泵盖
叶轮
蜜蜂体
轴
轴套
密封环
材料
HT250
硅黄铜
QT400--18
2Cr13
3Cr13
硅黄铜
压力容器选型原则
1、除氧器
1、1参数
水箱容积50m3
最大出力150t/h
设计压力0.6MPa
设计温度280℃
壳体材料20#
数量2台
填料、喷嘴等内部零件不锈钢
溶解氧≤15PPm
工作温度104℃
工作压力0.02Mpa
1、2除氧形式:
高效旋膜式,定压运行。
1、3除氧器及给水箱的内部结构、设计时考虑到防冲蚀、腐蚀、松动、旋涡、波动和噪音、以满足设备正常运行、启动、停机和变工况的要求,同时避免除氧器产生超标准的振动。
1、4除氧器出水管采用专用结构引至给水箱最低水位之下,以减少水面波动,保证温度混合均匀。
1、5除氧器与给水箱的蒸气接口、疏水接口采用套管式,以避免简壁受高温应力影响。
?
?
1、6水箱给水出口设有防旋涡及防杂物装置,防止杂物进入给水管道。
1、7为防止对筒壁的冲蚀,给水泵再循环管采用喷水管结构。
1、8水箱设置再沸腾装置,满足机组启动过程中迅速加热给水的需要,供方考虑减少再沸腾装置引起的异常振动噪音和防止变形的措施。
1、9为了便于维护和检修,除氧器设有一支DN600取物孔,给水箱设有DN450人孔二只。
1、10正常运行时除氧器本体(排气系统除外)在距设备1.5米处测得的噪音不大于85dB(A)。
1、11除氧器及给水箱的管接基本上采用焊接型式与管道连接。
(因阀门需要采用法兰连接除外)
1、12除易损件外,设备使用寿命30年以上。
1、13材质要求;
a、除氧器壳体及封头:
碳钢钢板20R。
b、除氧器内部:
除氧零部件均采用不锈钢。
C、给水箱封头及壳体:
碳钢钢板20R。
d、给水箱中坚固零件:
不锈钢
e、给水箱内部再沸腾加热装置:
总管碳钢、支管不锈钢、防旋涡装置采用不锈钢。
2、低压加热器
2、1技术参数
加热面积m2
水侧设计压力MPa
汽侧设计压力MPa
出水温度℃
冷却水量t/h
管子材料HSn70-1A
2、2结构形式:
立式全焊接型、U型钢管、双流程表面式加热器
2、3水侧的通流能力满足110%T-MCR的流量。
2、4加热器管侧设计压力,按凝结水泵在关闭点的出口压力计算。
2、5管侧的设计温度,为壳侧设计压力下的饱和温度。
当加热器有过热蒸汽冷却段时,管侧设计温度比壳侧设计压力的饱和温度高20℃。
2、6加热器设置足够的放气和内部挡板,以便在加热器启动和连续运行期间排出不凝结气体,放气能力按进入加热器蒸汽量的0.5%考虑。
2、7管侧水速在均不大于3m/s。
疏水出口管内水速不大于1.2m/s,当加热器中的疏水水位不受控制时,其疏水管内水速不大于0.6m/s。
2、8对于无过热蒸汽冷却段的低压加热器,其给水端差控制在2~3℃,疏水冷却段端差控制在5.6~8℃。
2、9卖方保证在距设备外壳1米处的噪声不得大于85dB(A)。
2、10凝汽器内低压加热器设置防止蒸汽腐蚀所用的不锈钢套。
2、11冷却管子材质采用HSn70-1A,壳体采用20R。
3、高压加热器
3、1技术参数
加热面积m2
水侧设计压力MPa
汽侧设计压力MPa
出水温度℃
冷却水量t/h
管子材料HSn70-1A
3、2结构形式:
立式全焊接型、U型钢管、双流程表面式加热器
3、3水侧的通流能力满足110%T-MCR的流量。
3、4加热器管侧设计压力,按给水泵在关闭点的出口压力计算。
3、5管侧的设计温度,为壳侧设计压力下的饱和温度。
当加热器有过热蒸汽冷却段时,管侧设计温度比壳侧设计压力的饱和温度高20℃。
3、6加热器设置足够的放气和内部挡板,以便在加热器启动和连续运行期间排出不凝结气体,放气能力按进入加热器蒸汽量的0.5%考虑。
3、7管侧水速在均不大于3m/s。
疏水出口管内水速不大于1.2m/s,当加热器中的疏水水位不受控制时,其疏水管内水速不大于0.6m/s。
3、8给水端差控制在2~3℃,疏水冷却段端差控制在5.6~8℃。
3、9卖方保证在距设备外壳1米处的噪声不得大于85dB(A)。
3、10凝汽器内低压加热器设置防止蒸汽腐蚀所用的不锈钢套。
3、11冷却管子材质采用HSn70-1A,壳体采用20R。
4、疏水箱和疏水扩容器选型原则
4、1所选容器满足最大流量要求。
4、2壳体材料为20#。
4、3焊接焊缝符合焊接规程要求。
5、射水器
5、1主要参数
工作水压力MPa
工作水量:
t/h
抽气量Kg/h
5、2采用闭式循环:
设水泵---抽器汽—水箱
5、3按照低耗高效原则选取水泵和电机。