LD处理和DCL处理技术.docx
《LD处理和DCL处理技术.docx》由会员分享,可在线阅读,更多相关《LD处理和DCL处理技术.docx(12页珍藏版)》请在冰豆网上搜索。
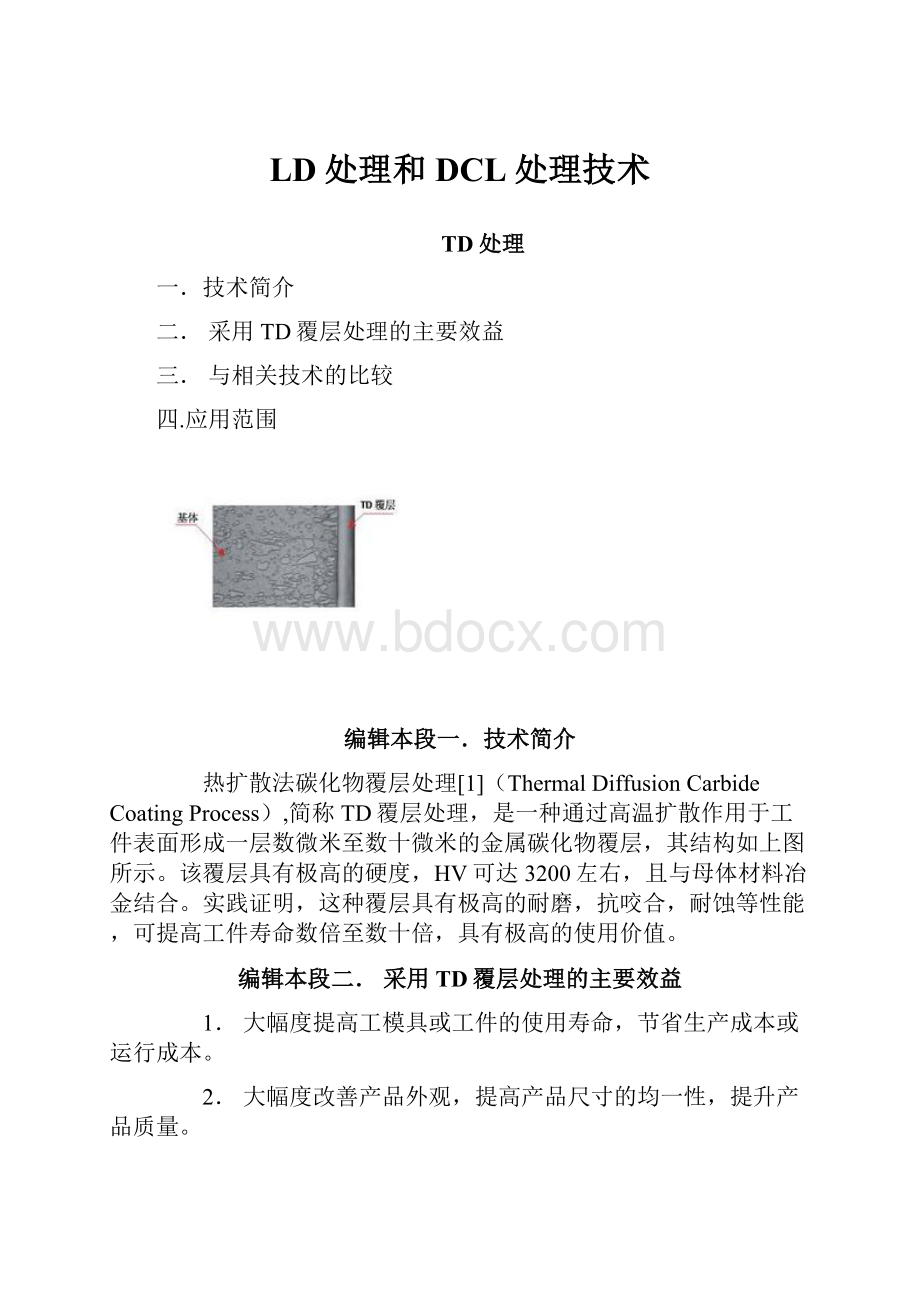
LD处理和DCL处理技术
TD处理
一.技术简介
二.采用TD覆层处理的主要效益
三.与相关技术的比较
四.应用范围
编辑本段一.技术简介
热扩散法碳化物覆层处理[1](ThermalDiffusionCarbideCoatingProcess),简称TD覆层处理,是一种通过高温扩散作用于工件表面形成一层数微米至数十微米的金属碳化物覆层,其结构如上图所示。
该覆层具有极高的硬度,HV可达3200左右,且与母体材料冶金结合。
实践证明,这种覆层具有极高的耐磨,抗咬合,耐蚀等性能,可提高工件寿命数倍至数十倍,具有极高的使用价值。
编辑本段二.采用TD覆层处理的主要效益
1.大幅度提高工模具或工件的使用寿命,节省生产成本或运行成本。
2.大幅度改善产品外观,提高产品尺寸的均一性,提升产品质量。
3.大幅度节省维修时间和劳动强度,并减少因维修停机所带来的损失。
4.摩擦系数降低,抗咬合性能大幅度提高,无须润滑或减少润滑或无须采用高级润滑产品。
编辑本段三.与相关技术的比较
通过在工件表面形成一层高硬度的耐磨材料是提高工件耐磨,抗咬合,耐蚀等性能,从而提高其使用寿命的有效而又经济的方法,TD覆层处理技术以碳化钒覆层为例,其表面硬度可达HV3200左右,较传统的表面处理方法如渗碳HV~900;渗氮HV~1200;镀硬铬HV~1000;甚至渗硼HV1200~1800等表面处理的硬度高得多,因此具有远优于这些表面处理方法的耐磨性能。
物理气相沉积(PVD),物理化学气相沉积(PCVD),化学气相沉积(CVD),TD覆层处理是现代的几种表面超硬化处理方法,其中PVD,PCVD工艺温度低,变形较小,所形成的氮化钛覆层HV可达2000左右,但由于这两种方法形成的氮化钛涂层与母体材料的结合力较差,实际应用中,容易出现涂层的剥落,在使用条件较为苛刻的场合,如引伸类模具;根本就无法达到满意的使用效果,甚至根本无效果.因此PVD,PCVD往往难以发挥超硬化合物覆层的性能优势.
高温CVD法形成的碳化钛覆层与TD覆层处理获得的表面覆层硬度接近,并且高温CVD法和TD覆层处理的覆层与基体都是冶金结合,具有PVD和PCVD无法比拟的膜基结合力,因此是目前最有效的表面超硬化方法.相比而言,CVD覆层的运行成本较高,后续处理也比较麻烦,其应用主要集中在硬质合金工件上.而TD覆层处理由于后续处理比较方便,因此既可以用于钢铁材料,也可以用于硬质合金.此外,TD覆层处理技术在无须褪去原先覆层的情况下,可以进行多次重复处理.
编辑本段四.应用范围
TD覆层处理可广泛应用于由于各类磨损所引起的模具与工件或工件与工件之间的拉伤或磨损超差的问题.其中因咬合或粘结而引起的拉伤或拉毛问题,TD覆层处理是目前世界上最好的解决方法之一.因磨损而引起的工件尺寸超差等问题,通过TD覆层处理后,提高使用寿命上十倍是很正常的.
所处理工件的材料,含碳量大于0.3%的各类钢铁材料,硬质合金等.一般推荐各类中高合金工模具钢.
DLC处理
“DLC”是英文“DIAMOND-LIKECARBON”一次的缩写。
DLC是一种由碳元素构成、在性质上和钻石类似,同时又具有石墨原子组成结构的物质。
类金刚石薄膜(DLC)是一种非晶态薄膜,由于具有高硬度和高弹性模量,低摩擦因数,耐磨损以及良好的真空摩擦学特性,很适合于作为耐磨涂层,从而引起了摩擦学界的重视。
目前制备DLC薄膜的方法很多,不同的制备方法所用的碳源以及到达基体表面的离子能量不同,沉积的DLC膜的结构和性能存在很大差别,摩擦学性能也不相同。
常见的制备DLC薄膜的方法有真空蒸发[1]、溅射[2]、等离子体辅助化学气相沉积[3]、离子注入[4]
等。
这些方法中,传统的真空蒸发镀膜法具有较高的沉积速度,生成的薄膜纯度高,但由于热蒸发的原子或分子在基板上能量很低(约02eV),其表面迁移率很低,导致薄膜与基体结合强度差,加上已经沉积的原子对后来飞到的原子会造成阴影效果,使得真空蒸发镀膜技术的应用受到很大的限制。
离子注入法能使材料的摩擦因数、耐磨性、耐腐蚀性等发生显著变化,而且注入层与基体材料之间没有清晰的界面,因而与基体结合牢固,表面不存在粘附破裂或剥落。
然而,离子注入的注入层太薄,仅数百纳米,在耐磨工况下应用受到一定限制。
为了克服真空蒸发镀膜法结合力差以及离子注入法注入层浅的问题,科研人员把薄膜蒸发沉积与离子注入技术结合起来,研究出了真空蒸发离子束辅助沉积技术[5,6]。
该技术在用蒸发源(电子束)将元素沉积在基片上的同时,用离子轰击镀层,以获得比离子注入层更厚、比蒸发镀膜法附着力更大的高性能致密膜层。
因此这种方法有利于增强薄膜的摩擦学性能。
本文作者用真空蒸发离子束辅助镀膜的方法制备了DLC薄膜,测试了其摩擦学性能,并对DLC薄膜的表面形貌对其摩擦学行为的影响进行了研究。
弹簧钢及Ti6Al4V球表面经真空蒸发离子束辅助镀膜处理后形成了光滑、致密的DLC薄膜,摩擦学试验结果表明,DLC薄膜降低了基体材料的摩擦因数,改善了摩擦学性能。
磨损表面的SEM和AFM分析表明,DLC薄膜的表面磨损较轴承钢为轻,表现出轻微的磨损痕迹,表明弹簧钢基体经真空蒸发离子束辅助技术处理后,表面摩擦学性能获得显著改善。
AFM分析还表明,Ti6Al4V球表面镀DLC薄膜后,磨痕表面比磨损前原始表面平整光滑,表面粗糙度小,其摩擦学性能在摩擦过程中进一步得到改善。
Diamond-likecarbon
碳素的天然结构有两种,空间立体结构(金刚石)和平面网状结构(石墨),而两者共存的结构就是DLC,其实DLC的定义是具有非晶质(amorphous)结构的碳素。
所以,DLC的定义非常广泛,只要含有碳元素,而且是非晶质结构(没有固定的结构形态),那么它就是DLC,不管里面还掺杂有其它元素什么的,统统都叫DLC。
类金刚石镀膜(DLC)的主要性能
1、力学性能
a.硬度及弹性模量。
不同的沉积方法制备的DLC膜硬度及弹性模量差异很大,用磁过滤阴极电弧法可以制备出硬度达到甚至超过金刚石的DLC膜[10],广州有色金属研究院用阴极电弧法制备的DLC膜最高硬度可达50GPa以上,而用离子源结合非平衡磁控溅射法制备的DLC膜硬度达21GPa[11]。
膜层内的成分对膜层的硬度有一定的影响,Si、N的掺入可以提高DLC膜的硬度。
DLC膜具有较高的弹性模量,虽低于金刚石(1100GPa),但明显高于一般金属和陶瓷的弹性模量。
b.内应力和结合强度。
薄膜的内应力和结合强度是决定薄膜的稳定性和使用寿命,影响薄膜性能的两个重要因素,内应力高和结合强度低的DLC膜容易在应用中产生裂纹、褶皱,甚至脱落,所以制备的DLC膜最好具有适中的压应力和较高的结合强度。
大部分研究表明,直接在基体上沉积的DLC膜的膜/基结合强度一般比较低,广州有色金属研究院通过采用Ti/TiN/TiCN/TiC中间梯度过渡层的方法提高DLC膜与基体的结合强度,在模具钢上沉积DLC膜的结合强度达44N-74N[12],制备的膜导总体厚度可达5um。
2、摩擦性能
DLC膜不仅具有优异的耐磨性,而且具有很低的摩擦系数,一般低于0.2,是一种优异的表面抗磨损改性膜。
DLC的摩擦系数随制备工艺的不同和膜中成分的变化而变化,其摩擦系数最低可达0.005[13]。
掺杂金属元素可能降低其摩擦系数,但加入H能提高润滑作用,环境也对摩擦系数有一定的影响。
但总的来说,DLC膜与传统的硬质薄膜(如上述的TiN、TiC、TiAlN等)相比,在摩擦系数方面具有明显优势,这些传统硬质薄膜的摩擦系数都在0.4以上。
国此,DLC膜有可能在许多摩擦学领域替代这些传统硬膜。
广州有色金属研究院制备的掺金属DLC膜具有良好的抗摩擦磨损性能及低达0.13-0.15的摩擦系数[14]。
3、热稳定性
由于DLC属亚稳态的材料,热稳定性差是限制DLC膜应用的一个重要因素,在300?
C以上退火时即出现了sp3键向sp2键转变,为此,人们进行了大量的工作试图提高其热稳定性。
有研究发现:
Si的加入可以明显改善DLC膜的热稳定性,含20at%Si的DLC膜在740?
C退火时才出现sp3键向sp2键转变[15]。
同样,金属(如Ti、W、Cr)的掺入也可提高DLC膜的热稳定性,我们正在对这方面进行研究。
4、耐腐蚀性
纯DLC膜具有优异的耐蚀性,各类酸、碱甚至王水都很难侵蚀它。
但掺杂有其他元素的DLC膜的耐蚀性有所下降,这是由于掺杂的元素首先被侵蚀,从而破坏了膜的连续性所致。
5)表面状态
DLC膜表面一般较光洁,对基材的表面光洁度没有太大的影响,但随着膜厚的增加,表面光洁度会下降。
不同的沉积方法所得到的DLC膜表面光洁度也是不同的,广州有色金属研究院采用离子源技术沉积的DLC膜表面质量明显优于电弧离子镀。
DLC膜具有很好的抗粘结性,特别是对有色金属(如铜、铝、锌等),对塑料、橡胶、陶瓷等也有抗粘结性。
DLC膜在机械功能领域上的应用
(1)钻头、铣刀
DLC膜可以应用于钻头和铣刀上,特别是掺杂金属的DLC膜,它不仅具有高的硬度,还具有低的摩擦系数、抗有色金属粘结。
荷兰的Hauzer公司制备的掺金属DLC膜层,用于切削高强度铝合金时,能减少表面所谓的切屑瘤(BUE)。
结果是延长工具的寿命并使工件材料在切削后表面光滑。
特别是在干切削和深孔加工方面,膜层性能非常好[16]。
广州有色金属研究院也进行了在铣刀上镀TiAlN+DLC膜,在加工有色金属时明显提高使用寿命及加工质量。
(2)光盘模具及其辅助模具
光盘模具是生产CD、CDR、DVD的重要工具,为了减少它与母盘(镍盘)的摩擦,希望模具表面硬且摩擦系数小,目前,国外大多采用DLC膜层,大大提高了模具的寿命和盘片的质量。
我们制备的DLC膜层也开始用于该领域,并取得了成功。
图2为广州有色金属研究院制备的DLC膜层光盘模具模仁,其寿命已达开闭合200万次以上(无涂层模具只有50万次左右)[17]。
同时在其辅助模具上镀DLC膜,其寿命也达到了配套使用的要求。
镀膜之后有硬度高,摩擦系数低,耐磨,耐腐蚀,抗粘结性好且环保等特点。
盘模具辅助冲模
(3)芯轴
DLC膜的耐磨减摩及耐腐蚀性,可显著提高齿轮、芯轴等运动部件的使用性能及寿命。
图3为广州有色金属研究院制备的DLC膜层芯轴,其寿命延长了3倍以上,耐腐蚀性提高4倍以上。
(4)刀片上的应用
现在DLC也在各种刀片如剪刀、刮胡刀等上的应用。
DLC膜减小了刀片与皮肤的摩擦,改善了刀片的性能,延长了使用寿命。
图4为广州有色金属研究院开发的DLC膜理发剪刀片,利用DLC膜优越的摩擦性能,明显提高刀片的使用寿命,特别是降低表面摩擦系数后,减小噪音,非常受用户欢迎。
(5)关键零部件上的应用
DLC膜在许多关键零部件也能发挥其优良的性能,如在制成式斯特林制冷机的活塞上的应用(如图5)利用其低的摩擦系数,降低摩擦力,提高耐磨性,达到无油润滑及使用寿命要求。
在缝纫机配件-旋梭上镀DLC膜(如图6)替代原来的电镀硬铬处理,不但避免了污染环境的问题,而且,明显提高工件表面硬度及耐磨性,使用寿命提高了10倍以上,同时,也因表面膜层摩擦系数降低后,使机器运行过程中产生的噪音变小。
(6)其它应用
DLC膜在工模具上的应用其它例子非常多,如:
粉末冶金成型模具、塑胶成型模具、引线框弯曲模具、玻璃片成型模具、镁合金加工模具、在轴承等。
DCL型固硫技术在大型高压煤粉锅炉的应用
作者:
广州石化总厂李广铿
摘要:
通过对固硫剂输送、喷射设施的优化及不同Ca/S摩尔比、不同喷射方式下锅炉SO2的削减量,证实了DCL型燃煤固硫剂是一种投资少、占地小、效率高的新技术,可在220t/h高压煤粉锅炉使用。
关键词:
固硫剂;输送、喷射装置;二氧化硫;削减量
DCL型燃煤固硫剂脱硫技术是国家环保总局下达给中科院的“九五”攻关项目,已通过国家科委的成果鉴定,并于1999年9月在鞍钢第一发电厂130t/h锅炉上进行了工业试验运行并取得成功,Ca/S摩尔比在2.0~2.5时,SO2的排放削减量稳定在59%~66%之间。
中国石化集团广州石油化工总厂与广州市粤首实业有限公司合作在广州石化总厂自备热电站4#锅炉(WGZ220/100-13型高压、单汽包、自然循环、固态排渣煤粉炉)进行DCL型固硫剂示范工程,从固硫剂储存、输送、喷射工艺上采取了先进技术,在试运行中取得较好效果,达到成果鉴定的SO2排放削减率。
在燃煤含硫量为0.8%,Ca/S为2.0和2.5时,SO2排放削减率分别达到了57.9%和65.5%。
一、固硫技术基本原理
煤按不同的含硫量称为低、中、高硫煤。
硫在煤中以无机硫(单质硫、硫酸盐),有机硫(硫醇、硫键、杂环硫)等不同形态存在,在燃烧过程中生成硫氧化物SOx。
SOx排入大气经光化学反应,形成硫酸雾,进而形成酸雨,严重危害生态环境。
固硫技术是指在锅炉燃烧过程的一定温度区域中加入固硫剂脱硫的方法,使燃烧过程中产生的SOx立即转化为MeSOx,固定在炉渣及煤灰中,而不排入大气环境,其原理为:
SO2+MeO+1/20→MeSO4
但此反应式没有表达反应的复杂机理和各种条件因素。
可燃硫燃烧后生成SOx,当锅炉过剩空气系数=2、燃烧室出口温度=1100℃时,绝大部分是SO2,SO3仅为3%~5%,随过剩空气和燃烧室出口温度加大而增加。
如果用CaO来吸收SO2,吸收率是非常低的。
生成的CaSO3在过剩空气为2%~3%时,也只有少部分CaSO3被氧化成稳定的CaSO4,大部分又被分解为CaO与SO2。
而CaO吸收SO3的的效果要好得多,其吸收率取决于CaO的活性(比表面及活化中心),如在CaO中加入一定量的催化剂进行活化处理,CaO对SO3的吸收率则大大提高了。
DCL型固硫剂正是运用这个原理在MeO中加一定量的助剂,将催化的概念引入固硫,通过提高固硫剂的吸附表面及活性,同时将SO2转化为SO3,或使CaSO3转化为CaSO4,从而使CaO固硫率大大提高,DCL型固硫剂不同于传统的固硫剂掺加到原煤中,而是喷到锅炉燃烧中心上部,固硫剂直接与烟气中的SOx反应,对燃烧没有造成不良影响,对锅炉效率影响甚微。
二、DCL型固硫剂炉内喷射基本工艺
按照DCL型固硫剂的技术要求,与烟气最佳反应温度为950℃~1050℃。
固硫剂喷嘴的位置确定在23.1m前墙看火孔处,该处处于锅炉转向室之前,屏式过热器烟气入口中心点下3m处,在锅炉负荷170t/h时,利用阿吉玛红外线热像测得该处温度为1045℃~1075℃,这样完全不用对锅炉进行改造。
DCL固硫剂物理性能:
堆密度:
1.00~1.15t/m3细度:
≤200目
外观:
灰色粉状物 含水量:
≤5%
根据固硫剂容易受潮和粘附力较强的特性,我们在考虑工艺系统设计时,尽量简化系统、优化工艺,并在整个系统中考虑到不发生二次污染,而且要有一定自控程度。
整个工艺流程见图1。
图1 DCL型固硫剂输送喷射工艺流程
如图1所示,100m3储罐为钢结构储料仓,储料仓根据DCL型固硫剂物理特性设置自动加热的空气流化设施,高低料位采用美国DE公司产品。
罐顶设置布袋除尘器,用于处理散装车辆料进罐的动力气源。
发送器输送能力为6~8t/h,气灰度为1:
39。
22层小料仓为2m3×2,同样设置美国DE公司料位计、加热板、布袋除尘器。
喷射部分包括了罗茨风机、螺旋给料机(带变频调速)、喷嘴。
发送系统采用了PLC程控:
小料仓料位低→发送器启动→输送固硫剂往上料仓→上料仓料位高→发送器停运→吹扫输送系统。
整个系统占地在50m2左右,并包括预留第二台炉位置。
为了保证喷嘴不会堵塞,设置罗茨机任何一种状况下停机均联跳对应给料机。
罗茨风机停运、系统设置在程控状态下,给料机不能启动。
其它参数均能在表盘显示,给料机可人工任意调整转速来调节给料量。
固硫剂喷嘴从锅炉标高23.1m处下两个手孔插入,喷嘴采用耐热合金钢铸造,内管钢材为1Gr18Ni9Ti。
助推风利用锅炉热风道送来的热风,气料比为<3kg/m3。
为保证固硫剂能在炉内迅速均匀扩散,喷嘴在出厂前进行了冷态试验,保证足够的旋流强度,使物料离开喷嘴迅速扩散并形成一个回流区,保证固硫剂均匀扩散。
系统中采用了不少外国先进专利技术,整个系统耗能见表1和表2。
表1输送喷射设备电耗表
表2输送喷射设备气耗表
三、固硫剂在锅炉应用的几个关键问题
1、固硫剂喷入炉内区域选择 实验室高温固硫表明,温度对固硫效率是相当重要的,当温度超过1200℃时SO2重新释放出来,固硫率接近于零。
这是因为:
SO2通过覆盖在CaSO4表面的保护层的扩散速度随着温度的升高而增大;另一种原因可能是在当固硫剂里面的催化剂失效时,SO2与MeO生成的MeSO3又分解为SO2和MeO。
从4#炉试验结果来看,第二种可能更大一些。
4#炉第一次试验,喷嘴装在20.8m处,喷入区域温度高于1200℃,数据显示出口烟气中的SO2较未喷固硫剂时烟气中的SO2还高出5%~10%。
当喷嘴装到23.1m时,(测得温度均为1045℃)固硫效率明显提高。
2、选择合适的钙硫比 不同的固硫剂添加量有不同的固硫效果,取决于原煤含硫量、燃煤用量,它可通过钙硫摩尔比来求得:
M=A×B×X/0.27
式中:
M--固硫剂喷入量t/h
A--锅炉每小时耗煤量t/h
B--煤中含硫量%
X--Ca/S摩尔比
假设220t/h锅炉燃煤量为28t/h,煤中含硫量为0.8%,要求Ca/S摩尔比为2时,则固硫剂喷入量为:
M=28×0.8%×2/0.27=1.66t/h
设定不同的Ca/S摩尔比取决于本炉在哪一种固硫剂喷入量取得最佳固硫效果,它要考虑到安全、经济,对削减SO2排放量的要求等,经优化方式来决定。
广石化220t/h锅炉在应用试运Ca/S摩尔比在2和2.5时,由广州市环境保护科学研究所测得的SO2削减率,见表3。
表3DCL型燃煤固硫剂固硫效果监测结果
注:
广州市环境保护科学研究所监测
需要说明的是,固硫剂喷入炉内后,最终与粉煤灰一起被电除尘捕捉。
不能无限度的提高Ca/S摩尔比,否则,电除尘前烟尘浓度增大后,影响电除尘正常运行。
在电除尘满负荷运行状态下,电除尘出口烟尘排放浓度依然超标。
根据4#炉投入固硫剂后对电除尘前后烟尘浓度和除尘效率检测结果表明,当Ca/S摩尔比在2.5以下时,除尘效率和出口烟尘浓度变化不大。
3、喷嘴助推风对脱硫效率的影响
由于各种锅炉结构不同,设计煤种和实际用的煤种不一样,锅炉的温度场分布不一样,广石化4#炉最后确定的固硫剂喷入位置为23.1m处,该处炉内结构见图2。
图2 固硫剂喷嘴位置
当喷嘴二次风速过高时,SO2排放量曾出现过削减率不到35%,当调整了二次风开度,降低了风速,SO2削减率即上升到55%以上。
在不同锅炉应用时,喷嘴的助推风(二次风)的风速的调整是相当重要的。
四、脱硫成本分析
目前供应商提供的固硫剂为200元一吨,根据Ca/S摩尔比在2.0和2.5时的SO2削减率,按广石化动力事业部4#锅炉试验时的原煤含硫量和耗煤量理论测算,当Ca/S摩尔比在2.0时,削减每吨SO2固硫剂成本为1509元;当Ca/S摩尔比在2.5时,固硫剂成本为1687元,每kW·h发电成本约增加0.006元~0.008元。
SO2排放环境造成的损失远远大于此数,也大大低于国外脱硫设施削减一吨SO2的成本。
DCL型燃煤固硫剂技术,具有投资少、占地小、效率高、运行费用低等优点,对锅炉运行安全可靠性影响甚微,非常适合我国国情。
DCL型固硫剂固硫技术,对新建企业锅炉的环保“三同时”,对现有企业的改扩建、削减企业的SO2排放总量,是一个可行的高新技术(end)