型腔加工工艺规程.docx
《型腔加工工艺规程.docx》由会员分享,可在线阅读,更多相关《型腔加工工艺规程.docx(12页珍藏版)》请在冰豆网上搜索。
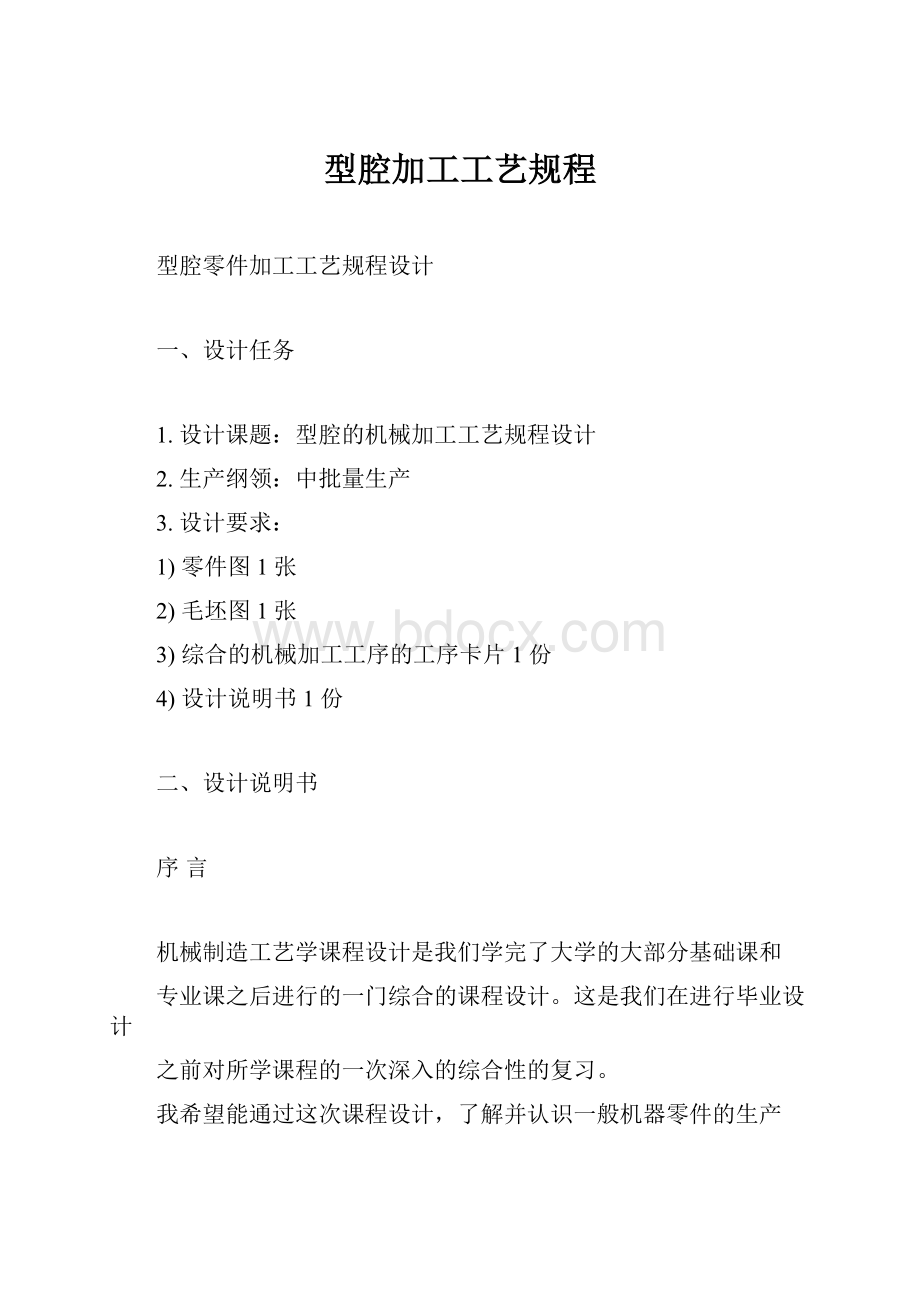
型腔加工工艺规程
型腔零件加工工艺规程设计
一、设计任务
1. 设计课题:
型腔的机械加工工艺规程设计
2. 生产纲领:
中批量生产
3. 设计要求:
1) 零件图1 张
2) 毛坯图1 张
3) 综合的机械加工工序的工序卡片1 份
4) 设计说明书1 份
二、设计说明书
序言
机械制造工艺学课程设计是我们学完了大学的大部分基础课和
专业课之后进行的一门综合的课程设计。
这是我们在进行毕业设计
之前对所学课程的一次深入的综合性的复习。
我希望能通过这次课程设计,了解并认识一般机器零件的生产
工艺过程,巩固和加深已学过的技术基础课和专业课的知识,理论
联系实际,从中锻炼自己分析问题、解决问题的能力,为后续课程
的学习打下良好的基础。
一、零件的分析
(一)零件的作用
型腔。
毛坯由石蜡铸造而成
(二)零件的工艺分析
35mm、10mm、5mm 三个尺寸是以 B 面为设计基准,
100mm、90mm、80mm、60mm 则是以原点 O 为设计基准。
型腔有
两组加工表面,他们之间有一定的位置要求。
现分述如下:
1、以 100*100 面为基准的加工表面
这一组加工表面包括:
四个尺寸 100*30mm 的与基面相垂直的平面,
90*90mm 的平面,80*80mm 的凹槽以及 40*35mm 的凸台
2、4*φ 10 深的孔
这两组加工表面之间有着一定的位置要求,主要是:
φ 10 的两孔之间的位置要求是 60±0.025
由以上分析可知,对于两组加工表面而言,可以先加工其中一组表
面,然后借助于专用夹具加工另一组表面,并且保证他们的位置精
度要求。
二、工艺规程设计
(一)确定生产类型
已知此零件的生产类型为中批量生产,所以初步确定工艺安排
为:
在加工过程划分阶段,工序应适当集中,机床设备可采用专用
设备,但以使用通用设备为主。
(二)确定毛坯的制造形式
材料为石蜡,由于零件毛坯尺寸不大,形状简单,石蜡不能承受
力矩,所以要选铸件做为毛胚,铸件可以一次性成型,适合石蜡这
种材质材料的加工,且零件属于中批量生产,故可采用铸造成型,
精加工采用铣削。
这从提高生产、保证加工精度上考虑,也是应该
的
(三)基面的选择
合理地选择定位基准,对于保证零件的尺寸和位置精度有着决
定性的作用。
基面选择是工艺规程设计中的重要工作之一。
基面选
择的正确与合理,可以使加工质量得到保证,生产率得以提高。
否
则,加工工艺过程会问题百出,更有甚者,还会造成零件大批报废,
使生产无法正常进行。
粗基准的选择:
在选择粗基准时,考虑的重点是如何保证各加
工表面有足够多的余量,及保证不加工表面与加工表面间的尺寸,
位置符合零件图样设计要求。
粗基准的选择原则:
1、保证不加工表面与加工表面相互位置要求原则。
当有些不加
工表面与加工表面之间有相互位置要求时,一般不选择加工表面作
为粗基准。
2、保证各加工表面的加工余量合理分配的原则。
应选择重要加
工表面为粗基准。
3、粗基准不重复使用的原则。
粗基准的精度低,粗糙度数值大,
重复使用会造成较大的定位误差,因此,同一尺寸方向的粗基准,
通常只允许使用一次。
现选取顶平面作为粗基准,利用顶平面作主要定位面,以消除
三个自由度,再用虎台钳装夹工件,用以消除另外三个自由度,达
到完全定位。
精基准的选择:
精基准的选择原则主要考虑如何减少误差,保
证加工精度和安装方便以及以及设计基准和工序基准重合问题。
当
二者不重合时,应该进行换算。
1、基准重合原则:
应尽可能选择零件的设计基准作为定位基准,
以避免产生基准不重合原则。
2、基准统一原则:
应尽可能选用精基准定位加工各表面,以保
证各表面之间的位置精度。
3、自为基准原则:
有些精加工或光整加工工序要求加工余量小
而均匀,应选择加工表面为精基准。
4、互为基准反复加工原则:
有些相互位置精度要求较高的表面,
可以采用互为基准反复加工的原则来保证
5、定位可靠性原则:
精基准应凭整光洁,具有相应的精度,确
保定位简单准确,便于安装,夹紧可靠。
考虑保证零件的加工精度和装夹准确方便,依据“基准统一和
基准重合”原则,以粗加工后的底平面为精基准。
第一道工序一般只能以为加工的毛坯面作为定位基准,这种基准称
为粗基准。
此零件以一个 A 面作为定位基准,铣削出定位粗基准。
然后翻转装夹,再以这个粗基准作为定位基准加工上端面即 B 面。
然后加工侧面,将一个加工过的侧面作为精基准,加工零件的最大
外轮廓。
在第一道工序之后,根据基准统一原则,纵向铣削应使尽
量多的表面加工时都用已加工的上端面作为定位基准,加工型腔、
梯台面、ø10 孔。
横向的铣削都以加工过的侧面作为定位基准。
以
保证各加工面的位置精度。
(一)制定工艺路线
制定工艺路线的出发点,应当是使零件的几何形状、尺寸精度及
位置精度等技术要求能得到合理的保证,在生产纲领已确定的情况下,可
以考虑采用万能性机床配以专用工夹具,并尽量使工序集中来提高生
产率。
除此之外,还应当考虑经济效果,以便使生产成本尽量下降。
1、工艺路线方案一
工序 1 铣基准面。
粗、精铣削 A 面作为定位粗基准面,见平即可。
工序 2 第二次装夹,粗、精铣削上端面即 B 面,将上端面作为纵向
加工的定位基准,保证厚度尺寸 35mm。
工序 3 加工两个未被装夹的侧面,以其中一个侧面作为横向加工的
定位基准,加工零件的外轮廓。
工序 4 铣台阶面型腔轮廓,沿型腔轮轨迹铣削出型腔的轨迹,保证
尺寸和精度要求。
工序5以底平面定位并夹紧工件,采用划线找正,钻
4×φ10mm×15mm 的孔,保证两孔中心的距离为60±0.025mm。
工序6 检验。
2、工艺路线方案二
工序 1 铣基准面。
粗、精铣削 A 面作为定位粗基准面,见平即可。
工序 2 第二次装夹,粗、精铣削上端面即 B 面。
粗、精型腔轮廓,
沿型腔轨迹铣削出型腔的轨迹,保证尺寸和精度要求。
工序 3 粗精铣、台阶面、周铣四个侧面,保证尺寸和精度要求。
工序4以底平面定位并夹紧工件,采用划线找正,钻
4×φ10mm×15mm 的孔,保证两孔中心的距离为60±0.025mm。
工序5检验。
(二)工艺方案的比较与分析
工序名称
工序间余量
/mm
经济精度
/mm
表面粗糙度
/um
工序基本尺
寸 /mm
半精铣
2
IT8
2.5
35
粗铣
4
IT11
5
37
毛坯(铸造)
±2
41
工序名称
工序间余量
/mm
经济精度
/mm
表面粗糙度
/um
工序基本尺
寸 /mm
半精铣
2
IT8
2.5
100
粗铣
4
IT11
5
102
毛坯(铸造)
±2
106
1、表 1 型腔厚度的加工余量、工序尺寸及毛坯尺寸表
表 2 型腔长度、宽度的加工余量、工序尺寸及毛坯尺寸表
两个工艺路线的分析:
相比工艺路线方案一,工艺路线方案二
只采用数控铣床和钻床就可实现凹件的完全加工,而且工艺路线方
案二的工序更少,因而能提高生产效率,节约成本。
因此选用工艺
路线方案二。
(三)机械加工余量、工序尺寸及毛坯尺寸的确定
零件材料为石蜡,毛坯重量约为 318 克,生产类型为中批量生
产,采用铸造成型的毛坯。
根据上述原始资料及加工工艺,分别确定各加工表面的机械加
工余量、工序尺寸及毛坯尺寸如下:
(四)确定切削用量及基本工时
加工条件:
XK713A 数控铣床,一把 YT15 面铣刀,刀盘直径
125mm,宽 20mm,齿数 20,通用夹具,0~200、0.2mm 游标卡尺,柴
油冷却。
a.确定背吃刀量
端面的总加工余量为 4mm,由毛坯图已知铣削宽度为
ae=106mm,两次走刀加工 ,ap=2mm.
b. 确定进给量及基本工时
根据《工艺手册》中表 4.2-38,XK713A 数控铣床,刀杆直径
为 22mm,再查《切削手册》表 3.15 和《工艺手册》表 4.2-38 可得,
我们可以取进给量 f=0.10mm/z。
c.计算切削速度
根据《切削手册》表 3.27 可得,Cv=186mm, qv=0.2,yv=0.4,
uv=0.2,m=0.2,xv=0.1,Pv=0,修正系数 kv=1.1,选择刀具使用寿命
T=60min.
vc=Cvdqvkv/(TmapxvfyvaeuvzPv)
=186×1250.2×1.1/(600.2×20.1×0.10.4×600.2×200) ≈ 4.87m/min.
d.确定铣床主轴转速
nw=1000vc/( π ×dw)=1000×4.87/(3.14×22) ≈ 70.51r/min
根据《工艺手册》表 4.2-39,与 70.51r/min 相近的转速为
75r/min。
现选择 nw=75r/min.所以实际切削速度为 v=5 m/min.
e.计算基本时间
按《工艺手册》表 6.2-7, l =106mm,
l 1 = 0.5(d - d 2 - a2e ) +(1~3) =32mm.
l 2=2mm.
时间 t=
l + l1 + l2
fMz
=140/150=0.93min,取时间 t=56s。
因为分两次
加工,所以切削时间 T=2×56s=112s
工序2用数控铣床以底平面为精基准半精铣顶平面,保证其厚度
尺寸为35mm。
然后加工四周、凹槽,保证其尺寸要求和精度要求。
在工序 2 的半精加工中,端面的总加工余量为 2mm,由毛坯图
已知铣削宽度为 ae=106mm,两次走刀加工,ap=1mm。
基本加工时
间的算法同上。
工序4 以底平面定位并夹紧工件,钻4×φ10mm×15mm 的孔,保
证两孔中心的距离为60±0.025mm。
加工条件:
Z515 钻床, Φ 10mm 标准锥柄麻花钻,通用夹具,
0~200、0.2mm 游标卡尺,柴油冷却。
a.确定进给量
根据《切削手册》表 2.7,f=1.0~1.2,查《工艺手册》4.2-16,
根据机床实际进给量取 f=0.12mm/r
b.选择钻头磨钝标准及耐用度
根据《切削手册》表 2.12 可得,钻头后刀面的最大磨损限度为
0.8~1.2mm,使用寿命为 70min.
c.计算切削速度
根据《切削手册》表 2.30,Cv=4.8, zv=0.4, xv=0, yv=0.7,m=0.2,
表 2,31 得,修正系数 kv=1.0.
vc=Cvd0zvkv/(Tmapxvfyv)=4.8×39×1.0/(700.2×19.50×0.120.7) ≈ 18m/m
in
nv=1000vc/( π dw)=1000×18/(3.14×39) ≈ 147r/min
根据《工艺手册》表 4.2-15,按机床实际钻速选取
nw=125r/min,则实际切削速度为 v=15m/min.
e.计算基本时间
按《工艺手册》表 6.2-7, l =15mm,
l1 =
D
2
cot κr + (1 ~ 2) =1~2mm, κr =90。
,取 l 1=2mm.
l 2=3mm.
时间 t=
l + l1 + l2
nw f
=20/15=1.33min,取时间 t=80s。
因为要加工 4 个孔,所以切削时间 T=4×80s=320s
最后,将以上各工序的切削用量、工时定额的计算结果,连同
其他加工数据,一并填入机械加工工艺过程综合卡片。
参考文献
1、赵家奇主编,机械制造工艺学课程设计指导书,机械工业出版社,
2006 年.
2、王先逵主编,机械制工艺学,机械工业出版社,2011 年.
3、卢秉恒主编,机械制造技术基础,机械工业出版社,2011 年.
4、肖诗纲主编,切削用量手册,机械工业出版社,1993 年.
5、邹青主编,机械制造技术基础课程设计指导教程,机械工业出版
社,2009 年
6、陈宏钧万向明主编,典型零件机械加工生产实例,机械工业出
版社,2010 年
7、马宏伟主编,数控技术,电子工业出版社,2011 年
8、王伯平主编,互换性与测量技术基础。
机械工业出版社,2011
年