伺服电机步进电机丝杠导轨的计算选择.docx
《伺服电机步进电机丝杠导轨的计算选择.docx》由会员分享,可在线阅读,更多相关《伺服电机步进电机丝杠导轨的计算选择.docx(10页珍藏版)》请在冰豆网上搜索。
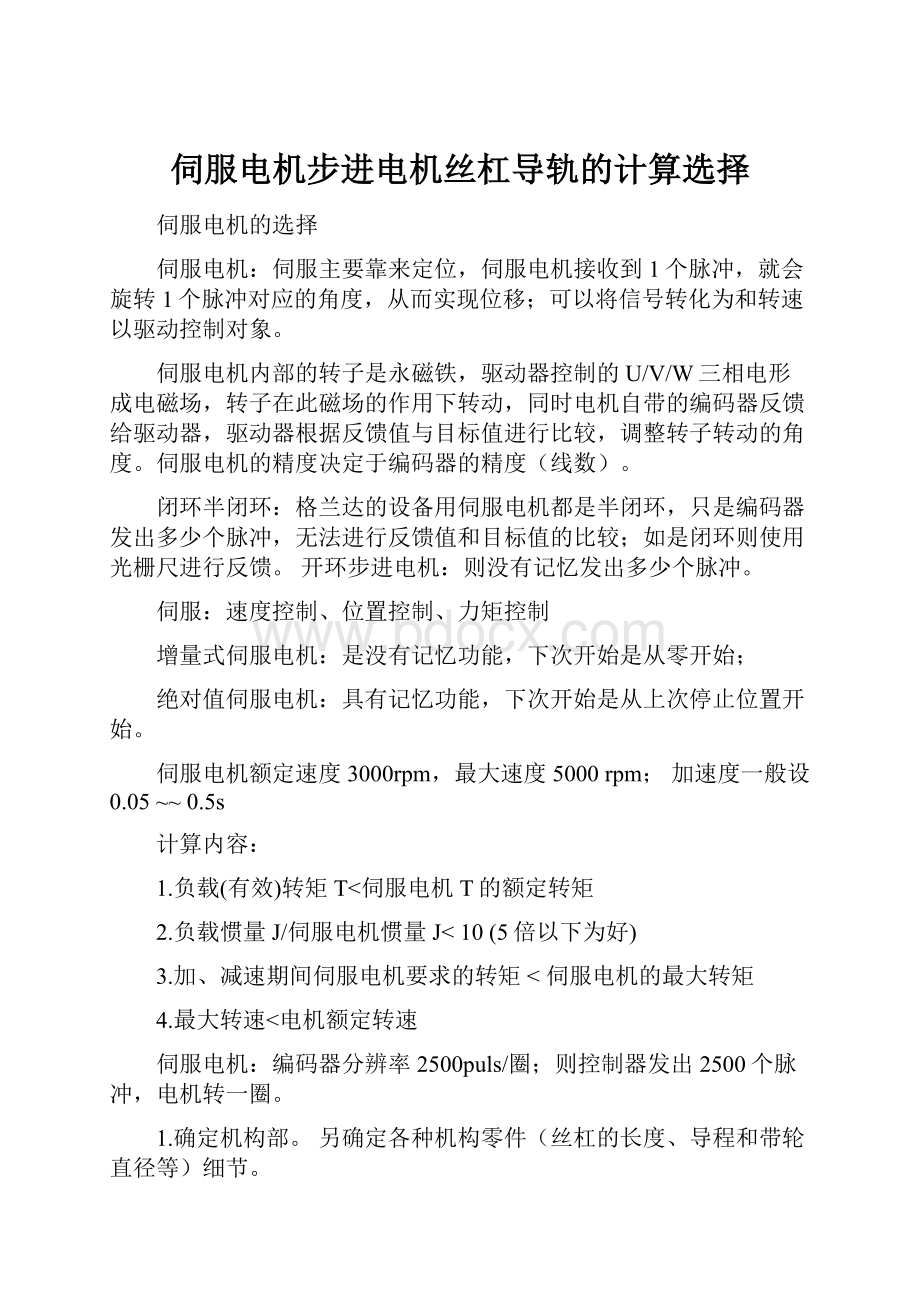
伺服电机步进电机丝杠导轨的计算选择
伺服电机的选择
伺服电机:
伺服主要靠来定位,伺服电机接收到1个脉冲,就会旋转1个脉冲对应的角度,从而实现位移;可以将信号转化为和转速以驱动控制对象。
伺服电机内部的转子是永磁铁,驱动器控制的U/V/W三相电形成电磁场,转子在此磁场的作用下转动,同时电机自带的编码器反馈给驱动器,驱动器根据反馈值与目标值进行比较,调整转子转动的角度。
伺服电机的精度决定于编码器的精度(线数)。
闭环半闭环:
格兰达的设备用伺服电机都是半闭环,只是编码器发出多少个脉冲,无法进行反馈值和目标值的比较;如是闭环则使用光栅尺进行反馈。
开环步进电机:
则没有记忆发出多少个脉冲。
伺服:
速度控制、位置控制、力矩控制
增量式伺服电机:
是没有记忆功能,下次开始是从零开始;
绝对值伺服电机:
具有记忆功能,下次开始是从上次停止位置开始。
伺服电机额定速度3000rpm,最大速度5000rpm;加速度一般设0.05~~0.5s
计算内容:
1.负载(有效)转矩T<伺服电机T的额定转矩
2.负载惯量J/伺服电机惯量J<10(5倍以下为好)
3.加、减速期间伺服电机要求的转矩<伺服电机的最大转矩
4.最大转速<电机额定转速
伺服电机:
编码器分辨率2500puls/圈;则控制器发出2500个脉冲,电机转一圈。
1.确定机构部。
另确定各种机构零件(丝杠的长度、导程和带轮直径等)细节。
典型机构:
滚珠丝杠机构、皮带传动机构、齿轮齿条机构等
2.确定运转模式。
(加减速时间、匀速时间、停止时间、循环时间、移动距离)
运转模式对电机的容量选择影响很大,加减速时间、停止时间尽量取大,就可以选择小容量电机
3.计算负载惯量J和惯量比(xkg.)。
根据结构形式计算惯量比。
负载惯量J/伺服电机惯量J<10单位(xkg.)
计算负载惯量后预选电机,计算惯量比
4.计算转速N【r/min】。
根据移动距离、加速时间ta、减速时间td、匀速时间tb计算电机转速。
计算最高速度VmaxxtaxVmax+tbxVmax+xtdxVmax=移动距离则得Vmax=0.334m/s(假设)
则最高转速:
要转换成N【r/min】,
1)丝杆转1圈的导程为Ph=0.02m(假设)最高转速Vmax=0.334m/s(假设
N=Vmax/Ph=0.334/0.02=16.7(r/s)
=16.7x60=1002(r/min)<3000(电机额定转速)
2)带轮转1全周长=0.157m(假设)最高转速Vmax=1.111(m/s)
N=Vmax/Ph=1.111/0.157=7.08(r/s)
=7.08x60=428.8(r/min)<3000(电机额定转速)
5.计算转矩T【N.m】。
根据负载惯量、加减速时间、匀速时间计算电机转矩。
计算移动转矩、加速转矩、减速转矩
确认最大转矩:
加减速时转矩最大<电机最大转矩
确认有效转矩:
有效(负载)转矩<电机额定转矩
6.选择电机。
选择能满足3~5项条件的电机。
1.转矩[N.m]:
1)峰值转矩:
运转过程中(主要是加减速)电机所需要的最大转矩;为电机最大转矩的80%以下。
2)移动转矩、停止时的保持转矩:
电机长时间运行所需转矩;为电机额定转矩的80%以下。
3)有效转矩:
运转、停止全过程所需转矩的平方平均值的单位时间数值;为电机额定转矩的80%以下。
Ta:
加速转矩ta:
加速时间Tf:
移动转矩tb:
匀速时间Td:
减速转矩td:
减速时间tc:
循环时间
2.转速:
最高转速运转时电机的最高转速:
大致为额定转速以下;(最高转速时需要注意转矩和温度的上升)
3.惯量:
保持某种状态所需要的力
步进电机
步进:
是将电信号转变为角位移或线位移的开环控制元步进电机件。
可以通过控制脉冲个数来控制角位移量,从而达到准确定位的;同时可以通过控制来控制电机转动的速度和加速度,从而达到调速的目的。
1.步进电机的最大速度600~~~1200rpm加速度一般设0.1s~~~1s
1.确定驱动机械结构2.确定运动曲线3.计算负荷转矩4.计算负荷惯量5.计算启动转矩6.计算必须转矩7.电机选型8.选型电机验算9.选型完成
选定电机:
1.负载惯量J/伺服电机惯量J<10(5倍以下为好)
2.在起动脉冲速度f1时,起动转矩>负载转矩T
3.在最大脉冲速度f0时,离开转矩(是不是必须转矩)>负载转矩T
步进选型计算见(KINCO步进选型中12页的例题)
伺服选型计算见(松下伺服选型计算伺服电机选型方法)
1千克·米(kg·m)=9.8牛顿·米(N·m)。
脉冲当量(即运动精度)&=<0.05
(0.05为重复定位精度)200为两相步进电机的脉冲数m为细分数200=360/1.8i减速比1/x
C电机转一圈的周长
无减速比电机转一圈丝杠走一个导程
电机转速(r/s)V=P为脉冲频率
例:
已知齿轮减速器的传动比为1/16,步进电机步距角为1.5°,细分数为4细分,滚珠丝杠的基本导程为4mm。
问:
脉冲当量是多少?
脉冲当量是每一个脉冲滚珠丝杠移动的距离
滚珠丝杠导程为4mm,滚珠丝杠每转360°滚珠丝杠移动一个导程也就是4mm
那么每一度移动(4/360)mm
电机4细分,步距角为1.5°,则每一个脉冲,步进电动机转1.5/4
那么一个脉冲,通过减速比,则丝杠转动(1.5/4)*(1/16)度
那么每个脉冲滚珠丝杠移动距离(及脉冲当量)&:
&=(1.5/4)*(1/16)*(4/360)=0.0003mm或者&=<0.05
例:
必要脉冲数和驱动脉冲数速度计算的示例
下面给出的是一个3相步进电机必要脉冲数和驱动脉冲速度的计算示例。
这是一个实际应用例子,可以更好的理解电机选型的计算方法。
1.1?
驱动滚轴丝杆
如下图,2相步进电机(1.8°/步)驱动物体运动1秒钟,则必要脉冲数和驱动脉冲速度的计算方法如下:
必要脉冲数=
100
10
×
360°
1.8°
×细分数m=[脉冲]
例:
精度要求0.01mm的雕刻机,导程5mm,步进电机驱动器一般用多少细分好呢?
如果确认是“精度”而不是“分辨率”的话,要考虑误差问题。
一,1)、你选择丝杠本身精度要高于0.01mm,
2)、其次电机细分只表示了分辨率,并不等同于电机精度。
假设你丝杠精度0.005mm,那么剩给电机的允许误差也就只有0.005mm了(暂不考虑其他误差因素)
0.005//5*360=0.36,表示你的电机精度要高于0.36度,所以你要选择绝对精度高于0.36度的电机。
二,至于细分,就简单了。
0.01/5*360=0.72;表示步进角0.72度时可达到0.01mm的分辨率
360/0.72=500;表示0.01mm分辨率时,电机一圈500步即可。
在实际使用时,你要尽可能选择细分高些,一方面提高运动平稳性,一方面也提供更高的步进分辨率。
滚珠丝杠的选型
一.已知条件:
UPH、工作台质量m1、行程长度ls、最高速度Vmax、加减速时间t1和t3、
定位精度+-0.3mm/1000mm、往复运动周期、游隙0.15mm
二.选择项目:
丝杠直径、导程、螺母型号、精度、轴向间隙、丝杠支撑方式、马达
三.计算:
1.精度和类型。
(游隙、轴向间隙)0.15mm,选择游隙在0.15以下的丝杠,查表选择直径32mm以下的丝杠。
32mm游隙为0.14mm。
为了满足+-0.3mm/1000mm则,+-0.3mm/1000=x/300则x=+-0.09mm.必须选择±0.090mm/300mm以上的导程精度。
参照丝杠精度等级,选择C7级丝杠。
丝杠类型:
根据机构确定丝杠类型是:
轧制或研磨、定位或传动
2.导程。
(以直线速度和旋转速度确定滚珠丝杠导程)导程和马达的最高转速Ph>=60*1000*v/(N/A)1.Ph:
丝杆导程mm2.V:
预定的最高进给速度m/s3.N:
马达使用转速rpm4.A:
减速比
3.直径。
(负载确定直径)动载荷、静载荷;计算推力,一般只看动载荷
轴向负荷的计算:
u摩擦系数;a=Vmax/t加速度;t加减速时间;
水平时:
加速时承受最大轴向载荷,减速时承受最小载荷;垂直时:
上升时承受最大轴向载荷,下降时承受最小载荷;
1.加速时(上升)N:
Fmax=u*m*g+f-m*a2.减速时(下降)N:
Fmin=u*m*g+f-m*a3.匀速时N:
F匀=u*m*g+fu因螺杆轴直径越细,螺杆轴的容许轴向负荷越小
4.长度。
(总长=工作行程+螺母长度+安全余量+安装长度+连接长度+余量)。
如果增加了防护,比如护套,需要把护套的伸缩比值(一般是1:
8,即护套的最大伸长量除以8)考虑进去。
5.支撑方式。
固定-固定固定-支撑支撑-支撑固定-自由
6.螺母的选择:
7.许用转速计算:
螺杆轴直径20mm、导程Ph=20mm最高速度Vmax=1m/s
则:
最高转速Nmax=Vmax*60*/Ph许用转速(临界转速)N1=r*(d1/)*
r安装方式决定的系数;d1=丝杠轴沟槽谷径;l=安装间距所以有:
最高转速<许用转速
8.刚度的选择9.选择马达
*验证:
刚度验证、精度等级的验证、寿命选择、驱动转矩的选择
*滚珠丝杠副预紧:
1.方式:
双螺母垫片预紧、单螺母变位导程预紧、单螺母增大滚珠直径预紧;
2.目的:
消除滚珠丝杠副的轴向间隙、增大滚珠丝杠副的刚性、
*DN值:
D:
滚珠丝杠副的公称直径,也为滚珠中心处的直径(mm);N:
滚珠丝杠副的极限转速(rpm)
*导程精度、定位精度、重复定位精度
导程精度:
1.有效行程Lu内的平均行程偏差e(um),ep=2*(Lu/300)*V300<=C;
2.任意300mm行程内行程变动量V300(um),V300<=
定位精度:
1).导程精度2).轴向间隙3)传动系统的轴向刚性4)热变形5)丝杠的运动姿势
重复定位精度:
预紧到负间隙的丝杠,重复定位精度趋于零;
直线导轨的选择
1.直线导轨的运动精度:
1)运动精度:
a:
滑块顶面中心对导轨基准底面的平行度;b:
与导轨基准侧面同侧的滑块侧面对导轨基准侧面的平行度。
2)综合精度:
a:
滑块上顶面与导轨基准底面高度H的极限偏差;b:
同一平面上多个滑块顶面高度H的变动量;c:
与导轨基准侧面同侧的滑块侧面对导轨基准侧面间距离W1的极限偏差;d:
:
同一导轨上多个滑块侧面对导轨基准侧面W1的变动量。
3)导轨上有超过两个以上的导轨,只检验首尾两个滑块,中间的不做W1检验,但中间的W1应小于首尾的W1。
2.选择:
1---确定轨宽。
轨宽指滑轨的宽度。
轨宽是决定其负载大小的关键因素之一
2---确定轨长。
这个长度是轨的总长,不是行程。
全长=有效行程+滑块间距(2个以上滑块)+滑块长度×滑块数量+两端的安全行程,如果增加了防护罩,需要加上两端防护罩的压缩长度。
3---确定滑块类型和数量。
常用的滑块是两种:
法兰型,方形。
前者高度低一点,但是宽一点,安装孔是贯穿螺纹孔,后者高一点,窄一点,安装孔是螺纹盲孔。
两者均有短型、标准型和加长型之分(有的品牌也称为中负荷、重负荷和超重负荷),主要的区别是滑块本体(金属部分)长度不同,当然安装孔的孔间距也可能不同,多数短型滑块只有2个安装孔。
滑块的数量应由用户通过计算确定,在此只推荐一条:
少到可以承载,多到可以安装。
滑块类型和数量与滑轨宽度构成负载大小的三要素。
4---确定精度等级。
任何厂家的产品都会标注精度等级,有些厂家的标注比较科学,一般采用该等级名称的第一个字母,如普通级标N,精密级标P。
5---确定其他参数
除上述4个主要参数外,还有一些参数需要确定,例如组合高度类型、预压等级等。
预压等级高的表示滑块和滑轨之间的间隙小或为负间隙,预压等级低的反之。
感官区别就是等级高的滑块滑动阻力大,等级低的阻力小。
表示方法得看厂家选型样本,等级数有3级的,也有5级的。
等级的选择要看用户的实际使用场合,大致的原则是滑轨规格大、负载大、有冲击、精度高的场合可以选预压等级高一点的,反之选低一点。
提示:
1--预压等级与质量无关,2—预压等级与滑轨使用精度成正比,与使用寿命成反比。
尺寸链的基本术语
1.尺寸链——在机器装配或零件加工过程中,由相互连接的尺寸形成封闭的尺寸组,称为尺寸链。
间隙A0与其它尺寸连接成的封闭尺寸组,形成尺寸链。
2.环——列入尺寸链中的每一个尺寸称为环,A0、A1、A2、A3…都是环。
长度环用大写斜体拉丁字母A,B,C……表示;角度环用小写斜体希腊字母α,β等表示。
3.封闭环——尺寸链中在装配过程或加工过程后自然形成的一环称为封闭环。
封闭环的下角标“0”表示。
4.组成环——尺寸链中对封闭环有影响的全部环,称为组成环。
组成环的下角标用阿拉伯数字表示。
5.增环——尺寸链中某一类组成环,当其他组成环的大小不变,若封闭环随着某组成环的增大而增大,则该组成环为增环。
6.减环——尺寸链中某一类组成环,当其他组成环的大小不变,若封闭环随着某组成环的减小而减小,则该组成环为减环。
7.补偿环——尺寸链中预先选定某一组成环,可以通过改变其大小或位置,使封闭环达到规定的要求,该组成环为补偿环。
封闭环:
基本尺寸:
A0=Ap1+Ap2-Aq3上偏差:
ES0=ESp1+ESp2-EIq3下偏差:
EI0=EIp1+EIp2-ESq3
A0:
封闭环Ap1、Ap2:
增环Aq3:
减环
封闭环基本尺寸=所有增环基本尺寸-所有减环基本尺寸;
封闭环的上偏差=所有增环的上偏差-所有减环的下偏差;
封闭环的下偏差=所有增环的下偏差-所有减环的上偏差。
1.退火:
指金属材料加热到适当的温度,保持一定的时间,然后缓慢冷却的热处理工艺(随炉冷却)。
常见的退火工艺有:
再结晶退火、去应力退火、球化退火、完全退火等。
退火的目的:
主要是降低金属材料的硬度,提高塑性,以利切削加工或压力加工,减少残余应力,提高组织和成分的均匀化,或为后道热处理作好组织准备等。
2.正火:
指将钢材或钢件加热到或(钢的上临界点温度)以上,30~50℃保持适当时间后,在静止的空气中冷却的热处理的工艺。
正火的目的:
主要是提高的力学性能,改善切削加工性,细化晶粒,消除组织,为后道热处理作好组织准备等。
3.淬火:
指将钢件加热到Ac3或Ac1(钢的下临界点温度)以上某一温度,保持一定的时间,然后以适当的冷却速度,获得马氏体(或)组织的热处理工艺。
常见的淬火工艺有淬火,马氏体分级淬火,,表面淬火和等。
淬火的目的:
使钢件获得所需的马氏体组织,提高工件的硬度,强度和耐磨性,为后道热处理作好组织准备等。
4.回火:
指钢件经淬硬后,再加热到Ac1以下的某一温度,保温一定时间,然后冷却到室温的热处理工艺。
常见的回火工艺有:
低温回火,,高温回火和等。
回火的目的:
主要是消除钢件在淬火时所产生的应力,使钢件具有高的硬度和耐磨性外,并具有所需要的塑性和韧性等。
5.调质:
指将钢材或钢件进行淬火及高温回火的复合热处理工艺。
使用于调质处理的钢称。
它一般是指中碳结构钢和中碳。
6.渗碳:
渗碳是指使碳原子渗入到钢表面层的过程。
也是使低碳钢的工件具有高碳钢的表面层,再经过淬火和低温回火,使工件的表面层具有高硬度和耐磨性,而工件的中心部分仍然保持着低碳钢的韧性和塑性。
“四把火”随着加热温度和冷却方式的不同,又演变出不同的热处理工艺。
为了获得一定的强度和韧性,把淬火和结合起来的工艺,称为。
某些合金淬火形成后,将其置于室温或稍高的适当温度下保持较长时间,以提高合金的硬度、强度或电性磁性等。
这样的热处理工艺称为。
7.渗氮:
正火:
850淬火:
840回火:
600