关于华能如东300MW海上风电场工程高桩承台和钢管桩的结构特点和质量控制不含防腐防锈部分的专题报告.docx
《关于华能如东300MW海上风电场工程高桩承台和钢管桩的结构特点和质量控制不含防腐防锈部分的专题报告.docx》由会员分享,可在线阅读,更多相关《关于华能如东300MW海上风电场工程高桩承台和钢管桩的结构特点和质量控制不含防腐防锈部分的专题报告.docx(17页珍藏版)》请在冰豆网上搜索。
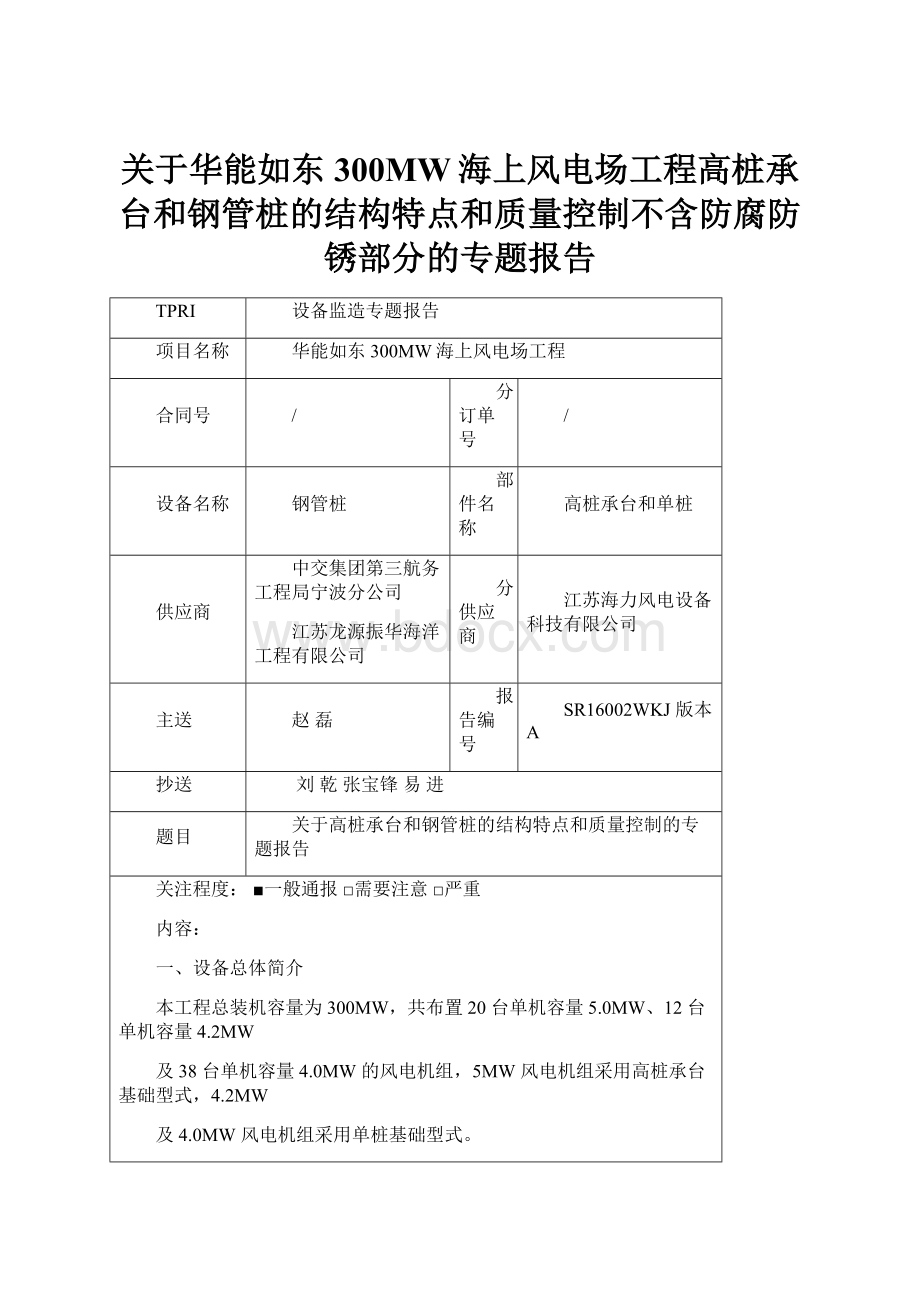
关于华能如东300MW海上风电场工程高桩承台和钢管桩的结构特点和质量控制不含防腐防锈部分的专题报告
TPRI
设备监造专题报告
项目名称
华能如东300MW海上风电场工程
合同号
/
分订单号
/
设备名称
钢管桩
部件名称
高桩承台和单桩
供应商
中交集团第三航务工程局宁波分公司
江苏龙源振华海洋工程有限公司
分供应商
江苏海力风电设备科技有限公司
主送
赵磊
报告编号
SR16002WKJ版本A
抄送
刘乾张宝锋易进
题目
关于高桩承台和钢管桩的结构特点和质量控制的专题报告
关注程度:
■一般通报□需要注意□严重
内容:
一、设备总体简介
本工程总装机容量为300MW,共布置20台单机容量5.0MW、12台单机容量4.2MW
及38台单机容量4.0MW的风电机组,5MW风电机组采用高桩承台基础型式,4.2MW
及4.0MW风电机组采用单桩基础型式。
二、结构特点
高桩承台:
由8根直径为2.0m、壁厚24~30mm的钢管桩组成,平均桩长约为81.0m。
每根钢管桩由长度2~3m的管节组焊而成,每节管节由整张钢板卷圆焊接而成,每根钢管桩焊有四个起重吊耳和一个翻身吊耳。
单桩:
直径为5.5m~5.8m、壁厚55~80mm,平均桩长70m。
由长度2~3m的管节组焊而成,每节管节由两张钢板拼焊后,卷圆焊接而成,每根钢管桩安装有两个起重吊耳、一个翻身吊耳和一个工作平台。
三、技术标准
风电机组基础的设计和施工应遵循(但不限于)下列规程规范(本技术要求中所列
规程规范,除有特殊说明外,均指有效的最新版):
3.1总领性规范
(1)《风电场工程等级划分及设计安全标准》(FD002)
(2)《风电机组地基基础设计规定》(FD003)
(3)《浅海钢质固定平台结构设计与建造技术规范》(SY/T4094)
(4)《港口工程桩基规范》(JTJ254)
3.2钢结构设计规范
(1)《材料与焊接规范》(CCS2014)
(2)《船舶及海洋工程用结构钢》(GB712)
(3)《低合金高强度结构钢》(GB1591)
(4)《厚度方向性能钢板》(GB/T5313)
(5)《碳素结构钢》(GB/T700)
(6)《钢结构设计规范》(GB50017)
(7)《钢结构工程施工质量验收规范》(GB50205)
(8)《海上平台栏杆》(CB/T3756)
(9)《钢格栅板及配套件第1部分:
钢格栅板》(YB/T4001.1)
(10)《花纹钢板》(GB/T3277)
(11)《热轧钢板和钢带的尺寸、外形、重量及允许偏差》(GB/T709)
(12)《结构用无缝钢管》(GB/T816)
(13)《无缝钢管尺寸、外形、重量及允许偏差》(GB/T17395)
(14)《六角螺栓-C级》(GB/T5780)
(15)《六角头螺栓全螺纹C级》(GB/T5781)
(16)《钢结构用高强度大六角头螺栓》(GB/T1228)
(17)《港口工程桩基规范》(JTJ254)
(18)《钢结构高强度螺栓连接技术规程》(JGJ82)
(19)《紧固件机械性能螺栓、螺钉和螺柱》(GB/T3098.1)
及其他相关规范
3.3焊接规范
(1)《材料与焊接规范》(CCS2014)
(2)《浅海固定平台建造与检验规范》(CCS2004)
(3)《钢制压力容器焊接规程》(NB/T47015-2011)
(4)《钢结构焊接规范》(GB50661)
(5)《气焊、电弧焊及气焊保护焊焊缝坡口的基本型式与尺寸》(GB985)
及其他相关规范
3.4防腐蚀规范
(1)《涂料:
用保护漆系统对钢结构的防腐第2部分:
环境分级》(ISO12944-2)
(2)《涂装前钢材表面锈蚀等级和除锈等级》(GB892)
(3)《海上风电场钢结构防腐蚀技术标准》(NB/T31006)
(4)《海上构筑物的保护涂层腐蚀控制》(SY/T6930)
(5)《色漆和清漆用于近海建筑及相关结构的保护性涂料系统的性能要求》
(ISO20340)
(6)《色漆和清漆钢结构防腐油漆系统防腐》(ISO12944系列)
(7)《色漆和清漆漆膜厚度的测定》(GB/T13452.2)
(8)《金属镀层和化学覆盖层厚度系列及质量要求》(CB/T3764)
(9)《热喷涂操作安全》(GB11375)
(10)《漆膜颜色标准样卡》(GSB05-1426)
(11)《铝-锌-铟系合金牺牲阳极》(GB4948)
(12)《铝-锌-铟系合金牺牲阳极化学分析方法》(GB/T4949)
(13)《海港工设施牺牲阳极保护设计与安装》(GJB156A)
(14)《海港工程混凝土结构防腐蚀技术规范》(JTJ275)
及其他相关规范
3.5检测验收规范
(1)《风力发电场项目建设工程验收规程》(DL/T5191)
(2)《材料与焊接规范》(CCS2014)
(3)《浅海固定平台建造与检验规范》(CCS2004)
(4)《舰船用高强度船体结构钢焊接材料的鉴定、出厂和进货检验规则》(CB1124)
(5)《船舶焊接检验指南》(CCS2013)
(6)《承压设备焊接工艺评定》(NB/T47014)
(7)《承压设备产品焊接试件的力学性能检验》(NB/T47016)
(8)《承压设备无损检测》(NB/T47013.1~9)
(9)《涂漆和应用有关产品之前钢材底层的准备-表面清洁度评定检验》
(ISO8502-4)
(10)《色漆与清漆拉开法附着力试验》(GB/T5210)
(11)《港口工程桩基动力检测规程》(JTJ249)
(12)《牺牲阳极电化学性能试验方法》(GB/T17848)
(13)《建筑工程质量检验评定标准》(GB/T50301)
(14)《混凝土结构工程施工质量验收规范》(GB50204)
(15)《水运工程质量检验标准》(JTS257)
(16)《钢筋焊接及验收规程》(JGJ18)
及其他相关规范
3.6混凝土结构设计规范
(1)《混凝土强度检验评定标准》(GB/T50107)
(2)《混凝土拌和用水标准》(JGJ63)
(3)《混凝土外加剂应用技术规范》(GB50119)
(4)《水运工程混凝土质量控制标准》(JTJ269)
(5)《水运工程混凝土结构设计规范》(JTS151)
(6)《水运工程混凝土施工规范》(JTS202)
(7)《普通混凝土力学性能试验方法标准》(GBT50081)
(8)《混凝土结构耐久性设计规范》(GB50476)
(9)《通用硅酸盐水泥》(GB175)
(10)《高强高性能混凝土用矿物外加剂》(GB/T18736)
(11)《混凝土外加剂》(GB/T8076)
(12)《建筑用砂》(GB/T14684)
(13)《建筑用卵石、碎石》(GB/T14685)
(14)《混凝土泵送施工技术规程》(JGJ/T10)
3.7其他
(1)《水运工程土工合成材料应用技术规范》(JTJ239)
(2)《土工合成材料长丝机织土工布》(GB/T17640)
及其他相关规范
四、制造及质量控制
4.1制造工序
高桩承台制造工序:
原材料入厂检验→钢板下料→坡口制作→卷板→纵缝焊接→回圆→管节组对→环缝焊接→焊缝质量检查→防腐→管段组对→环缝焊接→焊缝质量检查→最终防腐→验收
单桩制造工序:
原材料入厂检验→钢板拼板焊接→钢板下料→坡口制作→卷板→纵缝焊接→回圆→管节组对→环缝焊接(包括法兰焊接)→焊缝质量检查+法兰测平→防腐→管段组对→环缝焊接→焊缝质量检查→最终防腐→验收
4.2制造工序及质量控制
4.2.1原材料入厂检验:
所用板材采应从国内大型钢材生产厂家购买,且均采购正火一级探伤板。
高桩承台用钢板材质为Q345C、Q345D,单桩用钢板材质为Q345C、Q345D、DH36。
DH36、DH36-Z25型钢材(具体以施工图为准)应符合《船舶及海洋工程用结构钢》GB712等相关标准的规定;Q345C、Q345D型钢材(具体以施工图为准)应符合《低合金高强度结构钢》GB/T1591等相关标准的规定。
4.2.1.1原材料入厂检验包括:
a钢板产品质量证明书以及抽检复验报告,质量证明材料中应包含材料材质、熔炼分析、拉伸试验、冲击试验、探伤试验等数据。
b超声波抽检,按板材数量的20%做“田”字形探伤抽检,如抽检发现存在不合格板材则该批次抽检数量加倍,依此类推。
超声波检查按照《承压设备无损检测》(NB/T47013)、《承压设备无损检测第三部分:
超声检测》(NB/T47013.3)执行。
c化学成分、力学性能抽检,数量按照《低合金高强度结构钢》(GB1591)规定为每批次钢材抽检一组钢板样本。
d外观检验,钢管桩用钢板材料必须是新的,钢板表面不允许有任何缺陷,比如麻点、裂纹、皱折、贴边等,不允许采用补焊的方式修补。
e尺寸检查,用于钢管桩制作的钢板,其长度、宽度允许偏差均应满足《热轧钢板和钢带的尺寸、外形、重量及允许偏差》(GB/T709)相关规定。
f为保证制作全程的可追溯性,每块钢板上必须标记有以下信息(包括但不限于):
炉批号、件号、材质和质量等级等。
g桩顶法兰与桩体焊接前,应出具完整的质量合格证与相关检测、试验报告,经监理单位验证批准之后才可焊接。
h有Z向性能要求的钢材,按轧制坯验收,应逐张对Z25钢板的含硫量进行检验,分析结果应满足《厚度方向性能钢板》GB/T5313的要求。
4.2.1.2易出现问题:
a对所有入厂钢板简单的按照数量的20%抽检,未按照材质、批次分类抽检。
b钢板入厂复验抽检数量小于总数量的20%。
c原材料质量证明书为复印件,DH36钢板船级社认证缺失。
d原材料化学成分、力学性能抽检报告提交不及时。
4.2.1.3质量控制:
a对原材料入厂超声探伤进行现场见证,检查过程中应严格按照炉批号对每一批钢板按照数量的20%抽检。
b认真核对制造厂提供的原材料质量证明文件,确保无遗漏项。
c超声波探伤人员资质和设备,理化检验单位资质。
4.2.2钢板的划线、切割和坡口加工
4.2.2.1工艺要求:
a钢板由于运输、存储及轧制、冷却等环节而发生波浪、整体弯曲、局部凸起、边缘折弯等变形,影响切割、卷筒质量时,在切割前必须进行矫正。
b钢板下料时,应根据工艺要求预留切割、磨削刨边和焊接收缩等的加工余量。
c直管环缝间距不应小于2000mm。
d钢板划线的极限偏差应符合:
表1钢板划线的极限偏差
序号
项目
极限偏差(mm)
1
宽度和长度
±1
2
对角线相对差
2
3
对应边相对差
1
4
矢高(曲线部分)
±0.5
e坡口角度应与焊接工艺评定角度一致,坡口表面应打磨平整、光滑。
4.2.2.2易出现问题:
a焊接坡口切割角度与焊接工艺不一致。
b焊接坡口表面火焰切割过程中因操作不当,留有凹坑、疤痕等未打磨干净。
4.2.2.3质量控制:
a对下料尺寸抽检,包括下料板厚、宽度、边长和对角线长度。
b对坡口尺寸和表面质量抽检,应重点检查双面坡口。
4.2.3卷板、回圆
4.2.3.1工艺要求:
a钢管管节的钢板卷制应遵守NB/T47015的规定。
b钢板卷制前,应清除坡口处有碍焊接的毛刺、氧化物。
c管节纵缝焊接完成后必须进行回圆,回圆后管节椭圆度应不大于5mm。
4.2.3.2易出现问题:
管节纵缝焊接完成后未进行回圆,或者回圆不彻底,导致管节椭圆度超差。
4.2.3.3质量控制:
对管节回圆抽检,主要检查管节椭圆度及纵焊缝外观质量。
4.2.4管节组对:
4.2.4.1工艺要求:
a管节组对拼接时,相邻管节的管径差应不大于3mm;相邻管节对口的板边高差不超过t/10(t为板厚),且不大于3mm。
b为组装、运输和安装需要,在管节上加焊和拆除卡具、吊耳等附加物时,应注意不伤及母材,焊接位置应保证起吊时不损伤钢管和产生过大的局部应力。
若对后续工序无不良影响时,附加物可不予拆除。
c管节组对过程中严禁捶打、顶压等强行组对方式。
表2管节外形尺寸允许偏差
偏差名称
允许偏差
说明
钢管外周长
±0.1%周长,且不大于10mm
测量外周长
管端椭圆度
≤0.3%D,且不大于5mm(多桩)
±0.1%D,且不大于5mm(单桩)
两相互垂直的直径之差
一般管节椭圆度(单桩)
不大于10mm
管端平整度
2mm
多管节拼接时,以整根质量要求为准
桩总轴线弯曲矢高
不大于0.1%桩长,且不得大于30mm
桩体总长度
0~300mm
焊后桩顶法兰外形尺寸允许偏差
偏差名称
允许偏差
极限偏差(mm)
法兰椭圆度
不大于4mm
两相互垂直的直径之差
法兰平整度
不大于2mm
最高与最低之差值
法兰内倾度
0.5~1.5mm
4.2.4.2易出现问题:
a管节组对过程中易出现强行组对现象。
b组对管节板厚不一致时,组对错边量已出现超差。
4.2.4.3质量控制:
a检查管节组对错边量,重点不同板厚筒节组对错边量检查。
b检查管节组对过程,严禁强行组对。
4.2.5焊接:
4.2.5.1焊工资质:
a焊接由具备海洋工程、压力容器、电力等相关行业焊工证的人员负责实施。
b每位焊工上岗前,应经由发包人(或委托监理、监造单位)组织的资质审查、实地焊接考试的方式审核,审核通过后的焊工方可承担相应的焊接工作。
c在本项目钢结构焊接时,上岗焊工应按照焊工证及考试合格所允许的施焊形式、焊接等级、焊接范围内进行焊接施工。
d各焊工应有各自的识别代号,以便将他们的识别代号写在各自的焊接焊缝的旁边,距焊脚不超过100mm。
这些识别代号应保留到焊缝得到认可后方可取消。
任何没有焊工识别代号的焊缝将不予认可。
4.2.5.2焊接材料:
a钢管桩的焊接自动埋弧焊选用焊材:
焊丝:
牌号H10Mn2,规格Φ4.8;焊剂SJ101。
二氧化碳气体保护焊选用焊材:
焊丝:
牌号GFL-71Ni,规格Φ1.2。
b焊接材料制造厂应向施工方和监理单位提交焊接材料试验报告,试验报告应包括下列内容:
①试验日期、环境条件、焊接材料预处理状态;②焊接材料认可等级、牌号、型号、尺寸;③试板材料(牌号)、等级、力学性能、化学成份(包括细化晶粒元素);④焊接位置;⑤焊接采用的电流、电压、焊接速度和设备型号、保护气体成分;⑥各项试验成果。
c焊接材料的抽样复检按《舰船用高强度船体结构钢焊接材料的鉴定、出厂和进货检验规则》(CB1124)规定的进货检验项目进行抽样复检。
复验合格的标准埋弧焊按照《埋弧焊用碳钢焊丝及焊剂》GB/T5293-1999执行,药芯焊丝按照《低合金钢药芯焊丝》GB/T17493-2008执行。
d本工程同种焊接方法所采用的焊接材料应采购同一批次,且应报业主、设计及监理(或监造)工程师,经焊接工艺评定后最终确定。
焊接试板的相关规定见3.1.3条。
e焊接材料在存放和运输过程中,应密封防潮并满足《材料与焊接规范》等相关规范的规定。
f施焊前必须对焊条、焊剂进行适当的烘干和保温处理。
g施工单位申请代用材料,应提供代用材料的技术标准、质量证明书和试验报告。
只有在证明其材料不降低工程的的安全性与工程质量、不增加工程造价、不影响施工进度的前提下,经监理、设计、项目业主批准后,才能采用代用材料。
且施工单位不得使用未经监理人检查、验收的材料。
4.2.5.3焊接工艺评定:
a施工方应会同监理人按NB/T47014的规定进行焊接工艺评定,并按评定合格的工艺编写焊接工艺评定报告,报送相关的专业部门审批及监理人。
焊接工艺评定报告的编制参考NB/T47015附录所示的推荐格式。
b焊接工艺评定的试件,其试板钢材和焊接材料应与制作钢管所用的材料相同。
试焊位置应包含现场作业中所有的焊接部位,并应按施工图纸要求作相应的预热后热或焊后热处理。
c按NB/T47014的规定可不作焊接工艺评定的焊缝,施工方必须提交已进行过的合格评定报告,报送监理人审批,经监理人批准后,可不另作评定。
d对接焊缝试板尺寸不少于长300mm、宽250mm,焊缝位于宽度中部;角焊缝试板高度不少于300mm。
试板的约束度应与实际结构相近,焊后过大变形应予校正。
e试板应打上试验程序编号钢印和焊接工艺标记。
试验程序和焊接工艺应有详细说明。
f施工方应会同监理人对试板焊缝全长进行外观检查和无损探伤检查(检查方法与生产性施焊焊缝相同),并进行力学性能试验。
试板不得有缺陷。
若需修整的缺长度超过试焊长度的5%,则该试件无效,须重作评定。
g试板力学性能试验对接试板评定项目、数量和方法按NB/T47015的规定执行。
h焊接试板认可试验的有效范围:
工艺认可试验结果适用于与试验使用相同级别的钢材和焊接材料,但钢板的厚度不得超过试板厚度的±25%,材料的碳含量不得超出试验时的0.02%。
焊接坡口形式不允许任意改动。
手工电弧焊时,焊接电流或电弧电压值的变动范围不超出±15%,或采用焊接材料制造厂推荐的数据。
焊接速度变动范围应不超出±10%。
埋弧自动焊时,电弧电压变化应不超过±7%,焊接电流变化应不超过±10%。
预热温度变化范围不允许超过认可试验时预热温度的±25℃。
焊后热处理的加热温度、保温时间、加热和冷却速率及温度梯度等的变化范围不允许超过认可试验温度规定的范围。
i焊接工艺评定中必须给出详细的焊接信息、焊接要求、焊接程序鉴定报告及其他所有相关信息。
焊接程序鉴定报告应包括(但不限于):
焊接工艺、焊接方法、焊接位置、槽口几何形状和详细信息、电特性、原材料、焊接材料、采用的相关规范与技术要求等。
4.2.5.4焊接:
a焊前清理:
所有拟焊面及坡口两侧各20mm范围内的氧化皮、铁锈、油污、水汽及其它杂物应清除干净,每一焊道焊完后也应及时清理,检查合格后再焊。
b定位焊:
定位焊采用二氧化碳气体保护焊,定位焊不得保留在钢管的任何焊缝内。
c预热、保温:
钢板施焊前,焊缝区域要根据材料类型和部件厚度按照《钢制压力容器焊接规程》(NB/T47015)要求充分预热,预热温度应为80~250℃。
埋弧焊应连续进行,不得已断弧时,应采取相应措施接焊。
单桩焊后应进行保温,保温温度为200℃~300℃,保温时间不低于1小时。
d钢管桩的钢板焊接采用双面坡口焊,焊接时必须保证完全焊透,必须调节热量耗费,使得焊接熔合域在5%~10%之间。
相邻管段的纵焊缝宜错开90°以上,且不得低于60°,同时间距不得小于2000mm。
全焊透的焊接接头,均应清根后再进行反面焊接。
e各种焊接材料应按NB/T47015的规定进行烘焙和保管,焊接时,应将焊条放置在专用的保温筒内,随用随取。
f焊接环境要求,焊接环境温度应大于0℃(低于0℃时,应在施焊处两侧200mm范围内加热到15℃以上或再进行焊接施工),相对湿度<90%,且焊接工作区必须采取适当的措施防风雨。
g为尽量减少变形和收缩应力,在施焊前选定定位焊焊点和焊接顺序应从构件受周围约束较大的部位开始焊接,向约束较小的部位推进。
h拼板、纵缝焊接应设引弧和断弧用的引熄弧板;严禁在母材上引弧和断弧。
定位焊的引弧和断弧应在坡口内进行。
拆除引熄弧板时不应伤及母材,拆除后应将残留焊疤打磨修整至与母材表面齐平。
i焊接工作不允许伤害桩体,不允许在桩体任何部位进行引弧。
除图纸要求外,不允许在桩体的任意部位焊接把手或者接地线部件等。
4.2.5.5焊缝检验:
a钢管桩纵、横向焊缝均为一级焊缝;焊接质量等级应符合《承压设备无损检测》(NB/T47013)等规范要求,并达到I级标准。
b外观检查,焊波应均匀,焊缝边缘应平顺过渡到母材,对接焊缝余高除图纸特别说明外,均不应超过3mm,焊缝表面不得有裂纹、夹渣、未熔合以及不允许存在的气孔、焊瘤、弧坑和咬边。
c无损探伤,焊缝无损探伤应遵守NB/T47013的规定。
各部件焊缝采用100%超声波探伤,质量等级为I级;对于UT检验无法判断或有疑问时采用射线探伤;其中桩体的环向焊缝还应按10%比例抽检进行磁粉探伤,重点检查T型接头部位,验收等级为I级。
4.2.5.6易出现问题:
a焊接预热温度小于80℃,焊接过程中保温措施不当,层间温度不符合焊接要求。
b焊接过程中焊接参数的选用与焊接工艺不一致。
c焊接用引熄弧板设计不合理,引熄弧板去除后对母材环缝坡口位置造成损伤。
d大风、阴雨天气,室外焊接过程中焊接层间温度保温困难。
e焊接试板尺寸不符合标准要求。
f未按NB/T47015的规定对焊接材料进行烘焙和保管,焊接时未将焊条放置在专用的保温筒内。
g焊缝存在气孔、未融合等缺陷。
h焊缝超声波检查出现超标缺陷。
4.2.5.7质量控制:
a检查焊接参数的选用是否符合焊接工艺要求。
b检查焊接材料是否按要求烘焙和保温。
c检查焊接预热温度和层间温度。
d检查焊接人员资质和焊接设备。
e检查焊接材料的质量证明书及检验报告。
f检查焊接试板的制作。
g检查焊缝超声波和无损检测,有本单位持证人员对焊缝按20%的比例做超声波抽检。
五、典型质量问题及分析、处理
5.1监造人员对车间纵缝焊接过程进行现场见证时发现,制造厂引弧板使用不规范,引弧板存在碳刨坡口过短、引弧板坡口未焊满问题,导致近期引弧板割除后纵缝返修率较多,影响工程质量及进度。
已经要求制造厂进行专项整改,引弧板引弧长度应≥50mm。
(照片1、照片2)
照片1碳刨长度过短照片2引弧板未焊满
5.2监造人员对筒节外观及椭圆度现场见证时发现部分筒节椭圆度大于5mm,其中54-3-中椭圆度测量结果1992~2012,椭圆度为20mm,是测量数据中椭圆度最大偏差。
监造人员已要求制造厂进行整改,制造厂初步确定筒节在回圆过程存在质量失控,工人将未回圆的筒节进行强制组对,应力未得到释放,极大的影响塔筒内在质量,制造厂已对不合格筒节校圆,监造人员将继续跟踪处理结果。
5.4监造人员对管段总装组对焊接检查时发现,制造厂将防变形筋板焊接在纵焊缝位置。
制造厂已对筋板进行割除,对割除位置进行MT检测,未发现超标缺陷。
制造厂对员工进行教育,严禁筋板焊接在纵焊缝上,后续跟踪检查未发现类似问题。
(照片3)
照片3筋板焊接于纵焊缝上照片4焊剂未预热
5.5监造人员对管节拼版焊接检查时发现,制造厂使用未烘干的、已潮湿的焊剂进行焊接作业。
监造人员立即叫停了焊接作业,工人更换了烘干的焊剂再次进行作业,同时通报班组长以及生产部长,要求对该类情况进行自检、处罚。
雨水较多天气,极易产生焊接缺陷,制造厂应重视此类质量问题。
(照片4)
5.6监造人员对17#钢管桩焊接试板制备现场见证时发现,焊接试板宽度仅220mm,不符合NB/T47016标准要求。
制造厂已作废该试板,并重新制作了焊接试板。
(照片5)
照片5焊接试板制作尺寸不合格照片6引弧板使用不符合要求
5.7监造人员对车间纵缝焊接现场见证时发现,引弧板存在二次利用现象,且引弧长度过短,不满足技术规范要求。
单桩坡口角度较大,不能使用碳刨的方式处理引弧板,制造厂已将不符合要求的引弧板全部去除,重新使用符合要求