汽轮机调速系统的基本原理及常见故障的分析和处理.docx
《汽轮机调速系统的基本原理及常见故障的分析和处理.docx》由会员分享,可在线阅读,更多相关《汽轮机调速系统的基本原理及常见故障的分析和处理.docx(14页珍藏版)》请在冰豆网上搜索。
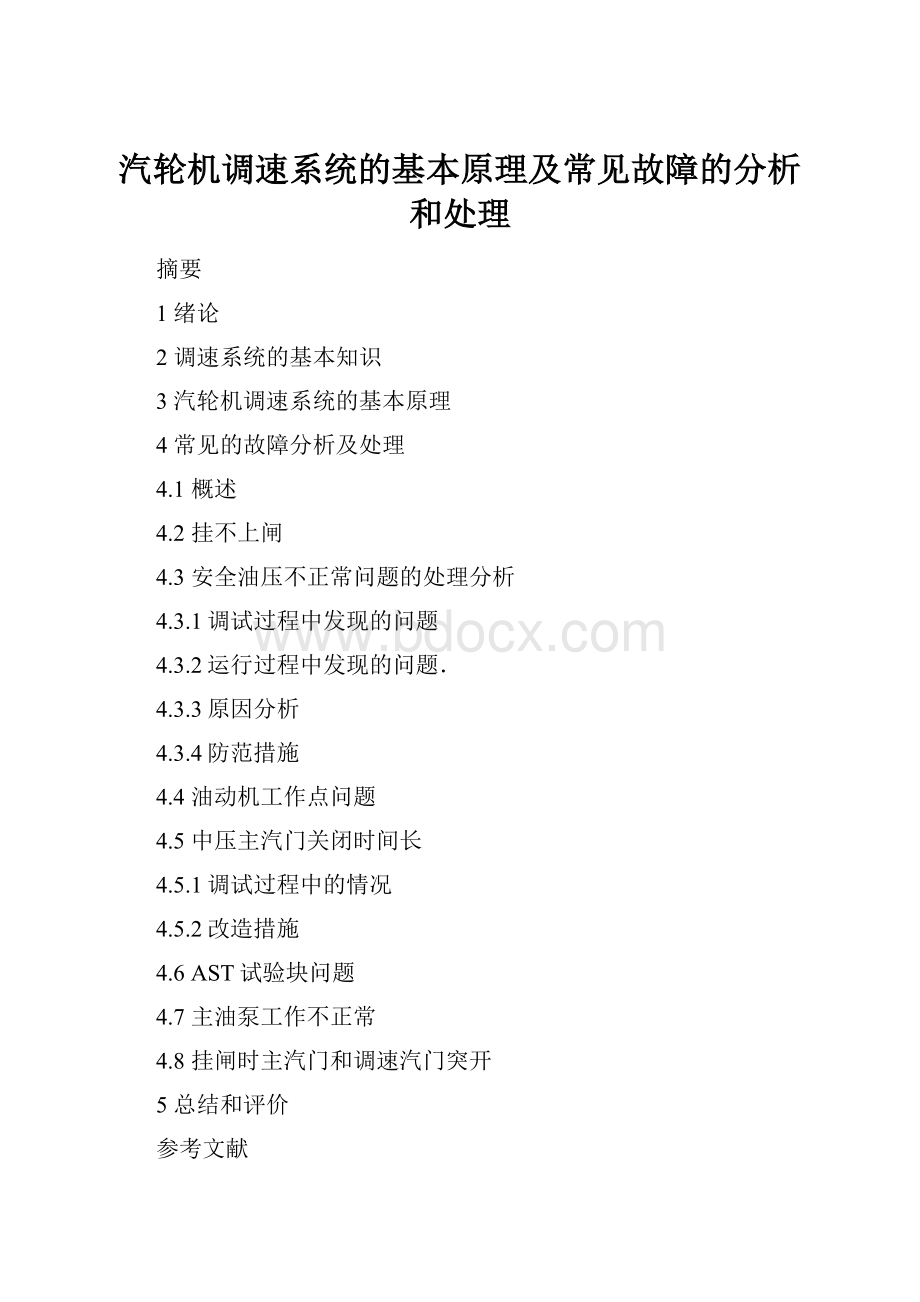
汽轮机调速系统的基本原理及常见故障的分析和处理
摘要
1绪论
2调速系统的基本知识
3汽轮机调速系统的基本原理
4常见的故障分析及处理
4.1概述
4.2挂不上闸
4.3安全油压不正常问题的处理分析
4.3.1调试过程中发现的问题
4.3.2运行过程中发现的问题.
4.3.3原因分析
4.3.4防范措施
4.4油动机工作点问题
4.5中压主汽门关闭时间长
4.5.1调试过程中的情况
4.5.2改造措施
4.6AST试验块问题
4.7主油泵工作不正常
4.8挂闸时主汽门和调速汽门突开
5总结和评价
参考文献
1绪论
调速系统是汽轮机的重要系统,可以说是汽轮机的神经中枢系统,调速系统的设备故障对汽轮机的安全经济运行有者极大的危害,有的甚至严重威胁到机组的安全,所以,本文将结合我们公司的#1汽轮机的调速系统在调试和生产中存在的常见故障进行分析,并结合设备存在的问题,分析提出治理措施,并在实践中修正,以求以理论指导工作实践。
调速系统的常见故障大致有以下几类:
一是部件的结构不合理,导致设备的安全可靠性降低,如活结漏油、部套卡涩等;二是安装或修后调节中易发生的问题,如安全油建立不正常、油动机工作点不合适等;三是系统设计方面的问题,如中压主汽门油动机的安全油排泄不畅,导致汽门关闭时间长等问题。
以上三类问题中,漏油、卡涩、油压不正常、工作点不合适等问题都是比较常见的故障,认真总结其中的规律性的东西,对指导现场的工作具有十分现实的必要性,至于第三类问题,虽然不是常见的故障,但汽门关闭时间长也是常见故障,所以本文也将对其进行简要的分析。
另外,调速系统对油有着较高的要求,油系统的滤网发生堵塞,或破损也是常见的故障,但这类故障在技术上没有很大的难度,因此本文对此将不再阐述。
2调速系统的基本知识
一、调速系统最基本的组成部分
1、调速系统最基本的组成部分包括:
(1)感受元件:
调速器(或调压器)
(2)传动放大机构:
错油门,油动机(3)配汽机构:
调速汽门及传动装置(4)反馈装置
2、调速系统最基本组成部分的作用
(1)感受元件:
在发电机电热负荷变化时,感受到汽轮机的转速变化或抽汽压力变化,并将此变化转变成其他物理量变化。
(2)传动放大机构:
当汽轮机的转速发生变化时,调速器或调压器发出的位移和油压的变化信号值是很小的,而大容量机组中,调速汽门的自重及其受到的蒸汽作用力却比较大,因而用此信号直接操纵调速汽门是不可能的,需将信号加以放大后,再去控制调速汽门,这个任务则由传动放大机构来完成。
(3)配汽机构:
配汽机构包括传动装置和调速汽门,其作用是接受传动放大机构放大后的信号,使调节汽门开度变化,调节汽轮机的进汽量。
(4)反馈装置:
在调节过程中,当油动机活塞因错油门滑阀动作而动作时,又通过一定的装置反过来影响错油门滑阀的动作,使错油门滑阀回到中间位置。
这种油动机对错油门的反作用称为反馈。
反馈是调节系统不可缺少的环节之一,因为只有反馈才能使调节过程较快的稳定下来,不致在调节过程中产生振荡,从而使调节系统具有很大的稳定性。
二、设置调速系统的意义
1、调速系统的基本任务
调速系统的基本任务是:
(1)汽轮机独立运行,当工况发生变化时调节汽轮机的进汽量,使之转速保持在规定范围内;
(2)汽轮机并入电网运行,当电网周波变化时,调整汽轮机负荷,使之保持在规定范围内;
(3)对于带调节抽汽的汽轮机来说,当汽轮机工况发生变化时,调整抽汽压力在规定范围内。
2、汽轮机为什么要设调速系统
汽轮发电机的工作,是由蒸汽作用在汽轮机转子上的作用力矩M汽和发电机转子受到的负载反作用力矩M阻之间的平衡关系所决定的。
当作用力与反作用力相等时,即M汽=M阻,汽轮发电机就处于等速转动的稳定工况。
但外界用户的用电量是在不断变化的,即M阻是在不断变化的,所以汽轮机的进汽量也必须相应的改变,保证M汽=M阻。
否则汽轮机的转速将随外界负荷发生大幅度变化,当外界负荷增加时,转速下降,外界负荷减少时,转速增加。
所以,发出的电能电压与频率忽高忽低,这是绝对不允许的。
为了保证电能质量和机组的运行安全,所有机组都必须装有调速系统,调节汽轮机的进汽量,以适应外界负荷的变化。
3N135汽轮机调速系统的基本原理
调速系统是汽轮机的重要系统,可以说是汽轮机的神经中枢系统,调速系统的设备主要包括三大部分:
液压保安系统、DEH调节和配汽系统、供油系统。
保安系统工作原理如系统图所示。
包括危急遮断器飞锤、复位及遮断装置、试验切换手柄、安全油闭锁阀及其动作电磁阀(OST)、AST跳闸电磁阀及其试验油路、喷油电磁阀和手动阀、安全油泄油活塞、中压主汽门及试验电磁阀等。
调节系统采用新华的电液转换器,输入50~300mA的电流信号,输出控制油压0.1~0.4MPa,控制油压的高低与油动机行程一一对应,以控制4只高压调门油动机、2只中压调门油动机及2只高压主汽门油动机的行程。
安全油压作用于危急继动器,危急继动器动作,控制油压迅速泄掉。
其工作原理图见图1和图2。
图1保安系统原理图复位遮断
安全油去DEH控制系统遮断与复位装置
逆止蝶阀试验手柄
φ1.5主汽门油动机φ2
φ2.4
活动试验电磁阀φ油动机滑阀
φ2.7压力油
φ2φ1.6
φ1.6φ1.2
闭锁阀
图2电液转换器工作原理图
力矩马达50~300mA信号安全油压
控制蝶阀危急继动器
压力油
φ3mm节流孔控制油压
4#1机调速系统故障的分析及治理
4.1概述
山东济宁运河发电有限公司一期工程汽轮机系上海汽轮机有限公司生产的135MW双缸串联双排汽中间再热超高压凝汽式汽轮机,仅生产8台。
保安系统为液压保安系统,与新华公司的DEH-
A低压电调系统相配套。
在调试和生产工程中出现了许多问题,现分别分析如下:
4.2挂不上闸
因工期紧张,汽轮机前箱内管道和部套均在现场组装。
2000年6月1日静态调试时发现,将复位手柄推到复位位置,用手按住不动,挂闸油压只能建立到0.45~0.5MPa(设计应为1.75MPa以上),将试验手柄置试验位置,挂闸,安全油压只有0.6MPa左右(设计应为0.85MPa以上),松开后复位滑阀掉闸,但安全油压能够保持。
检查挂闸油压进油节流孔φ2.4前的压力油为2.2MPa,观察蝶阀的密封情况,无油流喷出。
将进油节流孔取出后,挂闸油压能建立到1.0MPa,但试验手柄置试验位置后即掉闸,这样将无法观察到喷油试验的情况。
后经过多次观察,发现挂闸油压腔室与下面的结合面处有油流出,处理结合面并加垫子,并将安全油压泄油活塞上腔至挂闸油压腔室的节流孔由原来的φ1.6mm扩大到φ2.0mm,问题解决,挂闸油压油压恢复到2.25MPa。
4.3安全油压不正常问题的处理及分析
4.3.1调试过程中发现的问题
挂闸油压建立后,发现安全油压低,只有0.6~0.7MPa左右(后来发现不是安全油压,由于热工将安全油压和危急遮断器试验油压指示油压混淆,致使分析问题更困难,两路油压只有在闭锁阀正常时才是一致的),中压主汽门开启,打闸后安全油压能正常泄压。
但此时,AST电磁阀在失电开启状态,AST带电后,对安全油压无任何影响。
接临时管道,将AST试验块旁路,直接将安全油泄回油,对安全油压仍无影响。
后发现开机盘上安全油压的取样点不对,接临时安全油压表,发现真正的安全油压只有0.2~0.3MPa左右。
而中压主汽门已经开启,装临时阀门将AST电磁阀隔离,压力仍无升高。
观察到中压主汽门试验电磁阀(进口)在失电状态,应该关闭,但阀后管道热,说明有油流通过,失电和带电对安全油压均无改变。
加堵板后,安全油压恢复到1.6MPa,考虑到与DEH接口的问题,最后调整到0.98MPa左右。
在第一次启动后,将安全油压节流孔由原来的φ4mm减少到φ2.7mm,安全油压调整到0.85MPa,以减少安全油流量,改善电液转换器挂闸性能,同时降低远方打闸后的剩余压力。
但打闸时发现,安全油压泄不掉,而AST端子柜上的试验指示油压(约0.7MPa)能泄掉,后来怀疑可能闭锁阀处于闭锁状态,使安全油压和试验指示油压隔离。
但此时,OST电磁阀(在AST试验块上)应为失电泄油状态,不应该闭锁。
OST电磁阀带电后,闭锁滑阀端面上作用的油压为2.1MPa,OST断电后,闭锁阀端面上作用的油压指示消失为0,但仍在闭锁状态。
闭锁所用油压是压力油经节流孔φ1.6产生的,检查发现节流孔孔径为φ4mm。
用φ1.6mm的节流孔更换后,仍不能使闭锁阀恢复正常位置。
重新加工φ1.2节流孔,更换后问题解决。
出现闭锁问题的主要原因是闭锁油压油量太大,OST不能完全泄造成的。
4.3.2运行过程中发现的问题:
7月14日机组交接后,满负荷运行10余天后,安全油压由0.85MPa慢慢降低到0.75MPa左右。
将去AST电磁阀的截止门短暂关闭后又打开,安全油压变成1.0MPa,后又渐渐降低至0.82MPa。
具体做法是:
记录操作前的油压,安全油为0.76Mpa;热工短接门后压力到挂闸(掉闸)信号,手动关闭截止门,表计瞬间下降,迅速开门,安全油压上升至0.99Mpa;要求运行:
注意观察油压变化。
7月21日,发现安全油压力又有所下降,在0.87Mpa左右,继续观察运行。
为了避免机组运行中,现场通过调整溢流阀的方法将其调整到了1.0MPa。
4.3.3原因分析:
a、安全油溢流阀的初始整定时,安全油系统即存在漏点,但可能未引起注意,导致实际整定值即为0.99Mpa,
b、AST存在漏点,当关闭安全油来油时,系统安全油恢复,重开来油门时,漏点部位的杂务被冲走,安全油随之上升。
c、初步分析,仍有泄漏,必要时,进一步试验检查分析。
一可必要时,采取操作机械超速闭锁电磁阀,使系统安全油与危急遮断油门后的安全油隔离,以确认漏点的大致部位,再进一步的分析、处理。
二可在运行中打开前箱,检查安全油溢流阀是否正常。
三是重复上次AST前的手动截门试验,与热工人员一并确认。
d、油质不好,有杂物,需滤油。
4.3.4防范措施:
a、运行中,加强油系统的滤油,保持油系统的清洁。
b、安全油溢流阀再次整定时,应全面检查确认安全油系统是否有漏点。
c、运行中操作手动截门时,应联系热工人员,将可能引起误动的接点暂时短路。
d、手动截门的手轮应调整方向为朝下,正常运行及检修时均应上锁,如需动此门,应经运行人员同意后,开锁操作,并及时恢复和作好记录,
e、主油泵出口油压对安全油压力也应有很大影响,可适当调节主油泵出口管路上的调节门,观察主油泵出口油压对安全油压的影响,
f、确保在同一的压力油起点上整定安全油溢流阀,否则溢流阀的实际整定值将失去参考价值。
g、7月25日,安全油降至0.83Mpa,调整安全油溢流阀,使安全油压升至1.05Mpa。
4.4油动机工作点问题
启动调速油泵后,油动机开启,属于不正常动作,应在控制油建立后,根据控制油信号动作。
可能存在问题:
一是滑阀底部反馈弹簧刚度小,油路封不住;二是控制油不正常,滑阀动作,压力油进入活塞,开启油动机。
检查油路,检查电磁阀动作情况。
实际处理过程为:
调整弹簧,重新整定工作点,使问题得到了解决。
4.5中压主汽门关闭时间长
4.5.1调试过程中的情况
在AST电磁阀跳闸试验中,发现AST电磁阀失电后,安全油压降低到0.2MPa,中压主汽门经1分钟才能关闭到0,左右中压主汽门现象一致。
分析认为,造成以上异常的主要原因是中压主汽门进油逆止蝶阀装反造成的。
主汽门开启的过程是,安全油压达到蝶阀后,作用在蝶阀的背面,使蝶阀的结合面密封。
安全油经过蝶阀阀芯上的φ2mm节流孔进入主汽门油动机安全油管路,油压逐渐建立,推动具有压弹簧的活塞移动,使压力油来的φ5mm节流孔接通油动机下腔,主汽门油动机缓慢开启。
当机组打闸,安全油压失去后,蝶阀密封面迅速打开,将经过φ2mm节流孔过来的安全油泄掉,主汽门迅速关闭。
一般人认为蝶阀是顺着正常油流的方向打开的,故容易装反。
装反后,安全油压建立时,安全油畅通地进入油动机安全油管路,使主汽门迅速打开。
当打闸停机时,蝶阀起到逆止阀的作用,使安全油管路里的安全油只能通过φ2mm节流孔泄掉,油动机滑阀缓慢动作,大大延长了关闭时间。
由此联想到中压主汽门活动试验电磁阀,如果蝶阀装反,当电磁阀大量泄油时,把安全油大量泄掉,使安全油压建立不起来。
如果没有装反,电磁阀只能将经过φ2mm节流孔的安全油泄掉,不会引起安全油压建立不起来。
蝶阀复装后,打闸,中压主汽门能较快关闭。
但关闭时间录波测试显示,中压主汽门ISV1、ISV2关到底的关闭时间分别为0.99秒和1.33秒,是经过0.5左右关闭后(关到油动机行程的25%左右),停顿一段时间再关闭。
人们怀疑主要使由于设计排油管道排油不畅造成的,在关闭时,中压调门在主汽门前面抢先排油,堵塞了主汽门排油途径。
要更换排油管道,工作量大,为了慎重,做试验以确定是否为排油不畅造成:
关闭所有调门和高压主汽门电液转换器输出针阀,挂闸,只开启中压主汽门,然后打闸观察关闭情况,结果毫无改善,这就排除了对排油存在的怀疑。
STC设计人员答应,通过改进设计,增加泄油面积并就地泄安全油,仍能使油动机达到迅速关闭的要求。
第一次启动后停机机会,将中压主汽门油动机进油节流孔由φ5mm减小到φ3mm。
第二次机组启动到3000r/min后,远方打闸停机时对中压主汽门关闭过程录波,结果关闭时间延长到2秒左右。
同时中压主汽门活动试验电磁阀设计逻辑不合理,带电时关闭,失电时开启,不符合“故障安全”原则。
试验发现,就地拔插电磁阀,基本能使油动机顺畅关闭,中间无停顿,主要原因是打闸时安全油压要从4.5m上到9m泄油,产生的静压即达到0.04MPa左右,再加上剩余压力,使安全油压泄油不畅,远方打闸后中压主汽门抖动,而就地泄油能解决此问题。
将电磁阀通径由φ14换成φ16mm,失电常闭。
同时作为跳闸电磁阀使用,从ETS来的跳闸信号直接跳主汽门活动试验阀,15秒后复位。
从油动机到油动遮断阀的安全油,在泄油时是通过球形逆止阀快速泄掉的。
大量的油从油动遮断阀活塞下泄出,不仅延长油动机内安全油压消失时间,而且能使逆止阀的钢球冲到安全油泄油口,阻滞安全油压的顺畅泄出。
做一个顶杆,使钢球只能有3~5mm的活动空间,缓解了其负面影响,录波表明,关闭中停顿现象消失。
油动机滑阀为水平放置,取处油动机滑阀,发现卡涩较严重,磨痕明显。
在滑阀上车6道均压槽,以增加润滑,减小卡涩。
试验中,当左油动机试验电磁阀打开时,安全油压由0.85MPa减小到0.75MPa,当右油动机试验电磁阀打开时,安全油压由0.85MPa减小到0.15MPa,几乎全部泄掉。
检查其安全油进油逆止蝶阀上的节流孔为φ2.1mm,减小到φ1.5mm,同时对蝶阀研磨,导向段打磨,复装后对安全油压的影响基本正常(在主汽门严密性试验中,两试验电磁阀动作后安全油压降低到0.65MPa左右)。
采取以上措施后,6月19日重新对关闭时间录波,远方打闸时主汽门关闭时间由2秒左右减少到0.75秒,就地打闸为0.7~0.8秒。
再缩短关闭时间,必须从设计入手,扩大油动机泄油面积,安全油压就地排回油,STC重新设计试验后到现场更换。
4.5.2改造措施
1.针对油动机安全油回油慢、需返回9米排油、排油面积不足的情况,对主汽门油动机的安全油供排油系统进行了重新设计,使现场的系统得到了优化,增加安全油排油口,在#1机停机小修中实施了更改。
2.门杆试验电磁阀功能恢复到原设计状态,并将电磁阀的通径改回到原设计要求的通径,排油管一并恢复设计。
其控制功能也同步恢复。
3.改造后,请山东电力研究院对主汽门关闭时间,进行了测量。
改造后的试验数据为:
关闭时间为0.4S,达到了动作时间低于0.5S的验收标准。
4.6AST试验块问题
AST电磁阀在试验过程中是装反的,由于现场无设计图纸,无法核对电磁阀方向,由STC提供图纸后更正,但电磁阀活动试验过程中状态指示混乱,将安全油压调整到接近设计值后,仍存在问题。
解体试验块,取下两个φ1.6mm的节流孔,检查发现前面的节流孔没有钻透,直径只有约0.7mm,使中间油压达不到安全油压的一半。
将节流孔重新加工后,试验恢复正常。
4.7主油泵工作不正常
6月11日第一次启动,最高转速达到2500r/min,前箱内声音异常,观察发现主油泵入口油压为0,出口油压只有0.04MPa,打闸停机。
检查注油器花板(起逆止门作用)与密封面的间隙,为0.10mm左右,在制造厂规定范围内,未发现问题,同时进行了研磨。
复装后,开润滑油泵,主油泵入口油压升高到0.22MPa,开机过程中在1200r/min时入口油压达到最低0.03MPa,然后又逐渐升高。
3000r/min定速后,停润滑油泵和调速油泵,主油泵出口油压2.8MPa,入口油压0.28MPa。
出口油压高于设计2.21MPa约0.6MPa,这样超速试验时出口油压将达到3.4MPa左右。
在消缺中,1号注油器(供主油泵用)喷嘴,中心孔保持φ11mm不变,周围4孔堵死,在错位45O位置开4—φ9.5mm孔。
目的是降低注油器出口压力以降低主油泵出口压力。
扩大2号注油器(供轴承用)喷嘴直径,由原来5—φ8.8扩大至5—φ10,从而增加用油量,降低主油泵出口压力。
放大交流油泵至1号注油器节流孔板到φ28mm。
在主油箱内安装阀门,直接将主油泵出口油通过φ42mm管道泄至油箱,以减小主油泵出口压力。
实施以上措施后,再次开机3000r/min时,主油泵出口油压降低到2.7MPa。
主油泵出口油压直接排回油,调整排油阀门后将出口油压降低到2.5MPa。
4.8挂闸时主汽门和调速汽门突开
保安系统挂闸时,电液转换器的危急继动器由于水锤作用使控制油压突升。
经指挥部决定,临时采用动作OPC电磁阀的措施强制关闭主汽门和调门,但机头观察发现,挂闸时主汽门开启保持5~10秒,还未回落,调速汽门即开启,使机组转速升高500~1000r/min,而且随着主汽压力提高,转速升高趋势更加明显。
这是一种极其危险的情况,会使汽机转速突升。
压力油经过φ3mm节流孔后再经力矩马达作用的蝶阀间隙形成控制油压(0.06~0.5MPa)。
安全油压作用在危急继动器活塞上,保持控制油不泄漏。
当挂闸时,安全油压突然建立,推动继动器活塞活动,可能使作用在下腔的控制油压受到迅速冲击,控制油压突然升高。
制造厂提出在危急继动器弹簧座上增加3.5mm垫片,同时减小安全油节流孔,使安全油压建立缓慢,以减小危急继动器的冲击。
采取以上措施,挂闸后发现,GV3和TV2的控制油压0点为0.11MPa左右,此时汽门似开非开。
就地接电流信号发生器,并经调整后,恢复正常。
但跟DEH连接后又恢复原状,确定DEH送来50mA左右的初始电流,热工人员对该电液转换器输入调0,该电液转换器0位恢复,就地和远方挂闸均正常。
经几小时后挂闸,主汽门和调门全部突然开启,转速突然升高,打闸后再挂闸,又重现以上问题。
就地观察,GV1、IV2和TV2的0位又出现异常。
将DEH到电液转换器的接线全部解除后挂闸,恢复正常,确定为DEH问题。
DEH在挂闸时同时发出高于300mA的信号脉冲,使主汽门和调门开启。
经热工检查,电液转换器输入功放全部调0后,再挂闸就不出现问题。
但随着时间的推移,总是有几个调门或主汽门挂闸时全开,挂闸后的0位在似开非开状态。
最后将零点调到负偏置,并在每次挂闸前测量监视,DEH的问题再未出现。
5总结和评价
在静态试验中遇到诸多问题,有的得到了彻底解决,有的尚需进一步治理。
起初的挂闸油压不能正常建立,使我们认为安全油压低是挂闸油压低引起的,但挂闸油压建立后,安全油压仍不能正常建立。
由于中压主汽门进油蝶阀装反,同时试验电磁阀存在无论带电失电均泄漏的缺陷,造成安全油压低;又由于热工将安全油压表计装在遮断试验指示油管路上(起初没有发现),且同时闭锁阀存在异常闭锁,使无法观察到真正的安全油压,误认为试验油压和安全油压是一致的,因为正常是应该是一致的。
AST试验块电磁阀装反,使电磁阀无论带电与否始终处于关闭状态,又掩盖了安全油路真正存在的问题,直到将其旁路掉才将一个问题分解为两个独立的问题。
挂闸时调门和主汽门突开,先是油系统和电气系统都存在问题,后是DEH电气问题。
这些异常错综复杂,互为因果,互相掩盖,大大增加了分析问题的难度。
这些问题,有些是安装工艺问题,有些是加工工艺问题,有的是设计工艺问题。
,但只要认真坚持理论与实践相结合,问题会逐一解决。
参考文献
[1]赵义学主编:
《电厂汽轮机设备及系统》,中国电力出版社1998年
[2]赵永民主编:
《汽轮机设备及运行.》,水利电力出版社1989年
[3]赵鸿逵主编:
《热力设备检修工艺学》,水利电力出版社1993年
[4]罗光华.张家齐主编:
《125MW机组热力设备及运行》下册,北京科学技术出版社1992年
如有侵权请联系告知删除,感谢你们的配合!